Классификация механизмов запирания машин ЛПД.
В машинах для литья под давлением применяют механизмы запирания гидравлического, пневморычажного, гидроклинового типа.В гидравлическом механизме запирания усилениезапирания передаёться на подвижную плиту гидроцилиндром,в пневморычажном – системой рычагов,а в клиновом предварительно осуществляеться закрытие пресс-формы гидроцилиндром,после чего шарнирные части механизма запираються клином.
Рис.2-5 Схема гидравлического запирания устройства
1 неподвижная плита
2 подвижная плита
3 неподвижная плита
4 направляющая
5 шток гидроцилиндра
6 гидроцилиндр
В гидравлическом механизме запирающее усилие создаёться тоько гидравлическим цилиндром большого диаметра.К преимуществам его относяться простота наладки по высоте формы,отсутствие перекосов подвижной плиты,а следовательно получение более более точной отливки. Недостаток:большой расход рабочей рабочей жидкости.
Рис.2-6 Пневморычажная система
Запирающее усилие создаёться гидравлическим цилиндром и системой рычагов, увеличивающих жёсткость. Приемщества:меньший объёмнеобходимой рабочей жидкости;быстроходность;жёсткость и надёжность запирания формы;простота эксплуатации.Недостатки:меньшая точность изделия вследствие температурных перекосов плит,сложность настройки по высоте формы,малое усилие обратного хода.
|
|
Рис.2-7 Гидрокленовое запирающее устройство
1 привод
2 клин
3 гидроцилиндр,который управляет клином
4 штанины направляющие
Приемщества:простота наладки на различный размер форм,отсутствие перекоса подвижной плиты,а следовательно получение точной отливки. К недостаткам относиться их сложность из-за большой массы машины,а также сложность изготовления клинового запора и быстрого его изнашивания. Клиновые запирающие механизмы используют на машинах большой мощности
Автоматизированные установки для приготовления и нанесения суспензии и песка, используемых в керамической оболочке форм для литья по выплавляемым моделям.
Рис.1 – Схема установки для нанесения суспензии.
1-трубопровод. 2-дозаторы, 3- мешалка, 4- лопастная мешалка, 5-трубопровод для выпуска готовой продукции, 6-устр-во для дозирования сыпучих материалов, 8-бункер.
Рис.2-Схема агрегата для нанесения суспензии на блоки.
1-блок моделей. 2-трубопровод для подачи суспензии, 3- конвейер, 4-подвеска, 5- изгиб трассы конвейера, 6- устройство для нанесения песка, 7- датчик уровня, 8-емкость с суспензией, 9- мешалка, 10суспензия.
Схема изготовления отливки по газифицируемой модели
|
|
а)модель выжигаемая.
б)форма подготовленная
в)начало заливки
г)отливка с элементами ЛПС
Эту технологию можно отнести к группе способов получения отливок в неразъемных формах по разовой модели как литье по выплавляемым моделям. Модель удаляется (газифицируется) не до заливки, а в процессе заливки формы металлом, который, замещая испаряющуюся модель, занимает освободившееся пространство в полости формы.Современные варианты технологического процесса заключаются в следующем.
Разовые пенополистирольные модели изготавливают либо засыпкой в специальные металлические пресс-формы (массовое и крупносерийное производство) суспензионного полистирола в виде подвспененных гранул, либо механической обработкой нормализованных пенополистирольных плит (мелкосерийное, единичное производство). Сложные модели делают по частям. Отдельные части и литниковую систему соединяют в единый блок склеиванием или сваркой.Собранную модель окрашивают слоем огнеупорной краски и сушат на воздухе. В итоге получается огнеупорная газопроницаемая оболочка, прочно связанная с пенополистирольной моделью (а).
Готовую модель устанавливают в специальную опоку-контейнер, засыпают зернистым огнеупорным наполнителем без связующего, уплотняют его вибрацией, закрывают металлической крышкой с отверстиями, нагружают и устанавливают литниковую чашу (б).
|
|
Приготовленную форму заливают жидким металлом (в). Температура газификации пенополистирола близка к 560°С, поэтому под действием теплоты заливаемого расплава модель газифицируется. При этом полость формы постепенно освобождается и заполняется металлом.
После затвердевания и охлаждения отливки опоку-контейнер переворачивают, наполнитель отделяется от отливки и высыпается, после чего отливка направляется на финишные операции(г). В случае использования обычных формовочных смесей форму выбивают на выбивных решетках.
Главная особенность способа (применение неразъемной формы) определяет основное его преимущество для качества готовых отливок – повышение точности отливок благодаря сокращению числа частей формы, стержней, а, следовательно, и возможных искажений конфигурации и размеров отливок, связанных с изготовлением и сборкой этих элементов формы.
В настоящее время литье по газифицируемым моделям чаще всего используется со следующими целями:
- изготовление средних и крупных массивных отливок в условиях опытного и мелкосерийного производства;
- изготовление сложных отливок из черных и цветных сплавов массой до 50 кг с повышенной точностью размеров в условиях серийного и крупносерийного производства. К таким отливкам можно отнести, например, отливку типа «блок цилиндров» для автомобильного двигателя.
|
|
Билет № 21
1 Устройство гидравлического запирающего механизма машин ЛПД
1- гидравлический цилиндр
4- подвижная плита
Механизм запирания форм . Конструкция механизма запирания современных машин должна обеспечивать надежность запирания полуформ, свободный доступ к пресс-форме, достаточный ход открытия пресс-формы, возможность регулирования хода открытия Для установки пресс-форм, различных по высоте, достаточное усилие для размыкания пресс-форм и выталкивания отливки. Применяют четыре основных типа механизма запирания: гидравлический, гидрорычажный, комбинированный (гидроклинорычажные и гидроклиновые). В гидравлическом механизме запирающее усилие создается гидравлическим цилиндром большого диаметра. Достоинствами механизма являются простота наладки пресс-форм по высоте, отсутствие перекосов подвижной плиты и следовательно, получение более точных размеров отливки. Недостатки: большой расход сжимаемой жидкости, что требует увеличение вместимости бака гидроагрегата, и быстрый износ уплотняющих манжет, приводящий к утечке рабочей жидкости.
21(51) 2 Оборудование для выплавления модельного состава.
Для приготовления модельного состава используют установку, состоящую из плавильного и мазеприготовительного агрегатов. Плавильный агрегат состоит из двух блоков – верхнего 1 и нижнего 2. 1-ый с крышкой, открывающейся с помощью рычажного механизма, служит для плавки возврата модельного состава и свежих материалов. Расплавляемый материал загружают на трубы,внутри которых,а также между стенками бака циркулирует горячая вода с темп. 80 гр..Нагрев и циркуляцию воды обеспечивает насосная станция 9.Расплавленный состав стекает между трубами через фильтр в нижний бак и оттуда с помощью центробежного насоса 3 по трубопроводу 4 попадает в бак 5.Установка 6 для приготовления модельного состава состоит из двух поршневых мешалок и бака готовой пасты.Готовая паста сжатым воздухом выжимается из мешалки в бак,откуда поршневым насосом7 по трубопроводу8 попадается к автоматам для изготовления модельных звеньев.
21(81) 3 Оборудование для предварительного вспенивания гранул полистирола и изготовления моделей в пресс-формах.
1. Предварительное вспенивание гранул полистирола.
Сырьем для производства является полистирол вспенивающийся (EPS). В состоянии поставки он представляет собой шарики диаметром 0,4-1,6 мм. Целью предварительного вспенивания является увеличение диаметра шариков в 30-40 раз. Это достигается путем нагрева гранул паром в специальном вспенивателе. Пар производится парогенератором и накапливается в ресивере. Под воздействием пара гранулы размягчаются и находящийся в них газ изопентан раздувает их. Чем больше длится нагрев и чем больше подается во вспениватель пара, тем больше увеличиваются шарики и соответственно легче становится объемный вес вспененного полистирола. Таким образом на этом этапе закладывается плотность будущего пенопласта. Поэтому этот процесс очень важен, т.к. в дальнейшем изменить плотность и соответственно марку пенопласта уже будет нельзя. Процесс вспенивания ведется непрерывно. Из вспенивателя гранулы попадают в сушилку, где из них удаляется излишняя влага, затем с помощью пневмотранспортера гранулы перемещаются в специальный бункер вылежки. В этом бункере предварительно вспененные гранулы должны вылежаться в течении 12-48 часов. За это время происходит стабилизация гранул - они становятся прочными и упругими и готовыми для дальнейшей формовки. Этот процесс является общим для изготовления любых изделий из вспененного полистирола. Предварительно вспененные гранулы полистирола являются полуфабрикатом для дальнейшей формовки изделий.
2. Формовка изделий.
Этот процесс также основан на свойстве вспенивающегося полистирола увеличиваться в объеме при нагреве. Предварительно вспененные гранулы помещаются в плотно закрывающиеся пресс-формы. Затем в пресс-форму подается пар, под воздействием которого происходит дальнейший рост гранул. Но поскольку гранулы находятся в замкнутом пространстве, то с увеличением их объема происходит их деформация и склеивание между собой в цельное изделие. Какое это будет изделие - зависит от того в какую пресс-форму мы загрузили гранулы. Затем подача пара прекращается и происходит процесс охлаждения изделия с помощью воды либо вакуума, после чего форму открывают и извлекают готовое изделие.
3. В случае производства листового пенопласта на 2-м этапе формуется блок пенопласта. Он чаще всего имеет размеры 2000 х 1000 х 500 мм. И на 3-м этапе его разрезают на специальном резательном столе разогретыми нихромовыми нитями на листы нужной толщины и размеров. Также путем компьютерной резки можно вырезать из такого блока различные декоративные элементы.
Билет № 22
1 Устройство рычажного запирающего механизма машин
1-опорная плита
2-подвижная плита
3-неподвижная плита
4-направляющие
5-рычажная система
В гидрорычажном механизмезапирающее усилие создается гидравлическим цилиндром и системой рычагов. Достоинствами механизма являются меньший объем необходимой рабочей жидкости по сравнению с гидравлическим запором; быстроходность, но с необходимым замедлением движения плиты 3 при закрывании пресс-формы; надежность запирания пресс-формы; нежесткие требования к гидроаппаратуре. К недостаткам этого механизма относятся меньшая размерная точность изделия за счет температурных перекосов плит, сложность настройки пресс-формы по высоте, малое усилие обратного хода.
22(52) 2 Автоматические линии для изготовления керамических форм для способа литья по выплавляемым моделям.
22(82) 3 Изготовление литейных моделей из пенополистирола
Среди последних промышленных способов получения отливок, созданных во второй половине прошлого века, литье по газифицируемым моделям уверенно расширяет свои объемы .Жидкий металл не заливается в пустую полость литейной формы, а замещает пенопластовую модель в форме, чтобы там затвердеть в качестве отливки. В ЛГМ-процессе качество пенополистироловой (ППС) модели служит главным определяющим фактором, а понимание этого - ключом к организации производства качественных точных отливок с меньшими трудовыми и материальными затратами. ЛГМ формовка состоит из засыпки контейнерной опоки сухим песком с виброуплотнением. При этом все другие операции на литейном участке ЛГМ (кроме касающихся изготовления моделей и указанной простой операции формовки) аналогичны таким практически для всех литейных цехов, включая шихтовку, плавку, заливку металла, очистку отливок, т. п., и обычно выполняются на стандартном общелитейном оборудовании. Для производства ППС моделей имеется четыре основных способа, выбор каждого из них зависит, прежде всего, от серийности и размера отливок. Исключительно низкая твердость и легкость обработки ППС плотностью 20…30 кг/м3 как конструкционного материала литейных моделей в сочетании с кратко рассмотренными ниже указанными четырьмя способами объясняет высокую гибкость ЛГМ-процесса, пригодного как для ремонтного, так и для массового литья. Простой и легкодоступный способ изготовления модели на простейшем оборудовании – вырезание из блочного ППС нагретой проволокой. При получении единичной отливки, например, отливки детали для ремонта дорогостоящей или уникальной машины, этот способ является почти единственно приемлемым по экономическим и технологическим соображениям. Модель необходимой детали с учетом усадки металла весом от десятков грамм до нескольких тонн можно вырезать из ППСплит по шаблонам. Если деталь пространственно-объемная, то модель изготавливается из частей и собирается в целое. Сборку частей осуществляют склеиванием или расплавлением стыка тепловым ножом, контур детали или его частей прорисовывают на плоскостях ППС плиты гелевой ручкой или фломастером. При необходимости изготовления нескольких моделей одной и той же детали с целью повторяемости размеров целесообразно изготовление шаблонов из плотного картона толщиной 1…1,5 мм, которые сверху и снизу ППС плиты закрепляют тонкими гвоздями или специальными кнопками. При изготовлении модели детали с элементами зубчатой передачи по картонным шаблонам необходимо их точное взаимное ориентирование в разных плоскостях. Для этого шаблоны могут иметь средства совмещения типа шип-паз и. Исходный полистирол рекомендуемой марки и размеров гранул можно подвспенивать на подвспенивателях конструкции ФТИМС или на автоматических подвспенивателях. Последние такие конструкции, разработанные конструкторами института, позволяют в полуавтоматическом режиме получать подвспененные гранулы полистирола заданной плотности от 15 до 50 кг/м3 и размеров диаметром от 0,5 до 3 мм.
Билет № 23
Дата добавления: 2020-04-08; просмотров: 458; Мы поможем в написании вашей работы! |
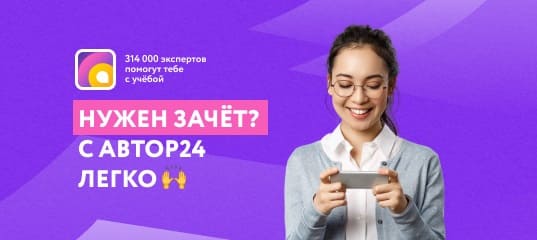
Мы поможем в написании ваших работ!