Оборудование для литья погружением.
Типы кристаллизаторов для непрерывного литья и их конструкция.
Вертикальный кристаллизатор установки непрерывного литья труб.
1 – наружная часть кристаллизатора; 2 – внутренняя часть кристаллизатора; 3 – раструбная часть кристаллизатора; 4 – входной патрубок; 5 – выходной патрубок.
Наружная часть кристаллизатора – цилиндрическая и раструбная. Патрубки входной и выходной соединены с резиновыми шлангами, что позволяет ему свободно двигаться. Толщина стенки до 50 мм. Установка располагается на 2-м этаже.
Кристаллизатор для горизонтального непрерывного литья трубчатых заготовок и профилей.
1 – раздаточная печь; 2 – водоохлаждаемая рубашка кристаллизатора; 3 – вкладки кристаллизатора (графитовый); 4 – графитовый стержень; 5 – отливка.
Кристаллизатор устанавливают в стенке раздаточной печи. Состоит из 2х частей водоохлаждаемой графитовой рубашки, где циркулирует охлаждающая жидкость и графитовой вставки, образующей внутреннюю поверхность.
В зазор между стержнем и графитовой вставкой заливаем металл.
Перед началом литья в кристаллизатор вводят затравку, которая вытягивает отливку.
Билет № 14
14. Кокильные линии.
Схема типовой автоматической линии получения отливок в облицованных кокилях:
1 — бункер с песчано-смоляной смесью, 2 — четырехпозиционный карусельный формовочный агрегат, 3 — манипулятор съема полуформ с моделей, 4 — приводной рольганг участка простановки стержней, 5 — манипулятор сборки полуформ, 6 — заливочный двухпозиционный агрегат, 7 — агрегат раскрытия кокилей и выбивки отливок, 8 — печь для предварительного (перед началом работы линии) подогрева кокилей, 9 — камера очистки кокилей от остатков облицовки, 10 — камера охлаждения кокилей, 11 — кантователь.
|
|
Автоматизация литья выжиманием.
Литье выжиманием является разновидностью литья в кокиль, Оно предназначено для изготовления крупногабаритных отливок (2500х1400 мм) панельного типа с толщиной стенок 2—3 мм. Для этой цели используют металлические полуформы, которые крепят на специализированных литейно-выжимных машинах с односторонним или двухсторонним сближением полуформ. Отличительной особенностью этого способа литья является принудительное заполнение полости формы широким потоком расплава при сближении полуформ. В литейной форме отсутствуют элементы обычной литниковой системы.
Жидкий металл поднимается сплошным потоком по створам. Сечение потока металла во много раз больше сечения будущей отливки. По мере того как жидкий металл поднимается вверх, на обеих створах образуются корочки застывающего металла. К концу выжимания отливка уже состоит из двух таких корочек, образующих внутреннюю и внешнюю поверхности детали, и из очень тонкой прослойки между ними, заполненной металлом в твердожидком состоянии. Как только створы окончательно сомкнутся, эта прослойка полностью застывает, соединив в одно целое ранее полученные корочки. Образуется тонкостенная отливка. Так как структура металла в этих условиях мелкокристаллическая, отливки получаются очень прочными. Литейная форма, образуемая створами, заполняется со скоростью 40-60 см/сек, вместо обычных 3-5 см/сек.
|
|
Такая высокая скорость помогает быстрой очистке металла. Пузырьки газов и легкие шлаки, соприкасаясь со струйками жидкого металла, обладающими различной скоростью, приходят по законам гидравлики во вращательное движение и приобретают силу, сдвигающую их от стенок формы к центру металлического потока, то есть в зону больших скоростей. Отсюда они вместе с избытком жидкого металла выносятся за пределы литейной формы. Отливки получаются плотными и чистыми.
Машина литья выжиманием с угловым перемещением.
1 – электрический электродвигатель; 2 – муфта сцепления; 3 – редуктор;
|
|
4 – рычажный механизм; 5 – створка подвижная; 6,7,12,14 – упор;
8 – нагревательный элемент; 9 – щека боковая; 10 – нагреватель; 11 – вал
13 – промежуточная плита; 15 – кронштейн; 16 – основная плита; 17 – винт упорный; 18 – станина.
Машина литья выжиманием с плоско-параллельным перемещением.
1 – станина; 2 – гидроцилиндр перемещения траверсы; 3 – гидроцилиндр протяжки; 4 – гидроцилиндр для фиксирования формы; 5 – формодержатель; 6 – полуформа; 7 – основание формы; 8 – блок стержней; 9 – боковая уплотнительная щека; 10 – механизм поворота этой щеки; 11 – привод поворота щеки; 12 – траверса; 13 – следящий золотник; 14 – направляющая траверса; 15 – втулка для центрирования; 17 – гидроцилиндр для протяжки.
Дата добавления: 2020-04-08; просмотров: 216; Мы поможем в написании вашей работы! |
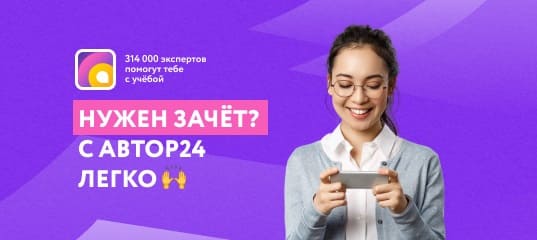
Мы поможем в написании ваших работ!