Установки полу непрерывного вертикального литья труб.
1 – водоохлаждаемый стержень
2 – литниковая система
3 – кристаллизатор водоохлаждаемый
4 – ковш с жидким металлом
5 – разборный стержень с кольцевым выступом, который играет роль затравки
6 – стол
7 – колонны
8 – привод стола
При непрерывном литье труб устанавливается стержень, который формирует внутреннюю поверхность трубы. Чтобы стержень не заклинивал, он имеет конусность 0,3-0,50.
Перед началом заливки стол устанавливают в верхнее положение. В кристаллизатор помещают стержень, устанавливают затравку. Жидкий чугун заливают из ковша через ЛПС (лоток + чаша). В дне чаши имеются питатели, через которые расплав попадает в зазор между чашей и стержнем. Вытягивание трубы начинается, когда уровень жидкого металла поднимается в кристаллизаторе на высоту < 30 мм всего кристаллизатора.
Подача жидкого металла не прекращается, начинается вытягивание. Для устранения схватывания металла со стенками кристаллизатора, он осуществляет поступательные движения вверх-вниз. Вверх – с ускорением, вниз – со скоростью вытягивания, т.е. возвратно-поступательное движение.
После завершения манипулятор снимает трубу и укладывает на стеллаж. Стол поднимается в верхнее исходное положение и цикл повторяется.
Установка полу непрерывного вертикального литья труб.
1 – заливочный ковш; 2 – кристаллизатор; 3 – механизм поворота кристаллизатора; 4 – поддон; 5 – кантователь.
|
|
Билет № 15
Автоматизированные литейные комплексы литья в кокиль
а) восьмипозиционная карусельная машина
1- дозатор жидкого металла
2- кокиль
3-манипулятор
4-магазин (наполнитель) стержней
5- конвейер для горячих отливок
6- манипулятор для извлечения отливок
7- коробка для отходов и литниковых систем
8- обрезной пресс для отливок
9- монорельс
б) комплекс из 2-х однопозиционных машин
1- дозатор
2- кокильная машина
3- тара для отливок
4- манипулятор
5- пульт управления
Общая характеристика процесса изготовления многослойной оболочковой формы по выплавляемым моделям
а) запрессовка модельного состава в пресс форму
Модель или звено модели (2) изготавливают в пресс форме (1). Полость пресс формы имеет размеры увеличенные на величину усадки. Модель изготавливают из материалов, которые имеют не высокую температуру плавления = 80 ° С и материалов, которые не размягчаются; предел текучести 30 ° С. Используют парафин, стеарин, воск. Аналогично изготавливают формы из выплавляемых и выжигаемых материалов.
б) сборка блоков выплавляемых моделей
Готовые звенья собирают в блоки (3), но которые изготавливают из выплавляемых моделей, модель стояка и питателя
|
|
в) нанесение суспензии
Вода и огнеупорные материалы
г) обсыпка
Нанесение сухого зернистого слоя суспензии кварцевый песок
д) сушка воздухом
Каждый слой покрытия высушивается отдельно, количество слоёв от 3-х до 10.
е) удаление модели
Выплавление модельного состава с использованием горячей воды (80-90 ° С)
ж) засыпка огнеупорным материалом
формирование оболочковой формы в опоке неким фиксирующим материалом
з) прокалка засыпанных материалов
Прокалку проводят перед заливкой. Выгорают остатки модельного состава
и) заливка жидкого металла
Заполнение оболочкой формы жидким металлом. На одном стояке через питатели несколько отливок
Дата добавления: 2020-04-08; просмотров: 86; Мы поможем в написании вашей работы! |
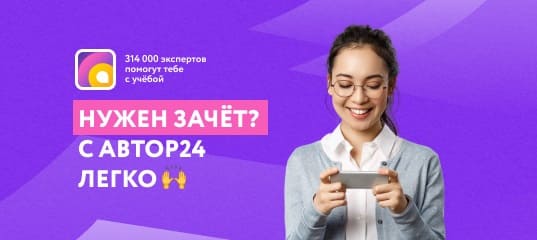
Мы поможем в написании ваших работ!