Механические свойства и коррозионная стойкость металла шва и сварного соединения
Вариант сварки труб | Предел прочности, G в , МПа, не менее | Предел текучести, G т , МПа, не менее | Относительное удлинение, % | Предел прочности, G в , МПа | Угол изгиба, град. | Ударная вязкость | Твердость (макс) НV 10 (НВ) | ||
КСV, Дж/см 2 (при Т° С) | KCU, Дж/см 2 (при Т° С) | ||||||||
Основные электроды | 509 (52) | 392 (40) | 26 | не ниже G в норм. осн. металла | 120 110 (мин) | ³ 39 (-36°) | ³ 45 (-36°) | 238 (205) | |
Целлюлозный + основные эл-ды | 490 (50) | 392 (40) | 24 | 120 110 (мин) | ³ 25 (-36°) | ³ 40 (-36°) | 248* (205) | ||
Стандарт на испытание | |||||||||
| Металл шва: ГОСТ 6996-66 тип II, IV | Сварное соединение: ГОСТ 6996-66 |
| ||||||
тип XII, XIII | тип XXVII XXVIII | тип IX, Х | тип VI, VII | ГОСТ 2299-75 (ГОСТ 9012-59) | |||||
Вариант сварки | Водородно-индуцированное растрескивание (НIС) | Растрескивание под напряжением (SSС) от G т - нормативное | |||||||
СLR | СТR | ||||||||
Основные электроды | 0 | 0 | 0,8 (0,6)** | ||||||
Целлюлозный + основные эл-ды | 0 | 0 | 0,8 (0,6)** | ||||||
Стандарт на испытание | |||||||||
NАСЕ ТМ-02-84 | МСКР-01-85 NАСЕ ТМ-01-77 | ||||||||
Примечание. Для G в и G т в скобках указаны значения в кгс/мм2.
* Для корневого и заполняющего слоев.
** Допускается по согласованию с головной научной организацией.
Дополнительные данные см. Приложение 4.
Таблица 2.5.
Применение сварочных электродов
Назначение | Тип | Марка электрода | Вид покрытия | Диаметр электрода, мм | |||
АWS А 5.1 | ГОСТ 9466-75 | ||||||
Для сварки корневого слоя
| Е7018 | Э50А | Фокс ЕВ50 | Основной | 2,5-3 ,25 | ||
-"- | УОНИ 13/55 | ||||||
Е7016 | -"- | ЛБ-52У | |||||
Е6010 | Э42 | Фокс-Цель | Целлюлозный | 2,5-3,25 | |||
Для сварки* заполняющих, облицовочного слоя | Е7018 | Э50А | Фокс ЕВ50 | Основной | 3,25-4,0 | ||
-"- | УОНИ 13/55 | ||||||
Е7016 | -"- | ЛБ-52У |
______________
* Электроды диаметром 2,5 мм могут применяться для заполняющих слоев при s < 9 мм
2.1.12. Сборка и сварка стыков труб.
2.1.12.1. Длина врезаемых катушек на трубах диаметром 219-406 мм должна быть не менее 1000 мм, на трубах диаметром 219 мм - не менее 500 мм.
2.1.12.2. В местах вырезки (расположения сварного шва) необходимо обследовать металл ультразвуковым прибором для уточнения толщины стенки и выявления дефектов.
В металле труб на расстоянии не менее 50 мм от кромки не должно быть коррозионных каверн, водородных блистеров (расслоений).
2.1.12.3. При проведении РВР необходимо выполнять стыковые сварные соединения без подкладных колец. Врезки в газопровод следует осуществлять с использованием тройников.
2.1.12.4. Перед сборкой (применением) необходимо провести осмотр труб, деталей и арматуры на их соответствие проектным данным и ТУ в части наличия наружных дефектов.
|
|
2.1.12.5. При непосредственном соединении разнотолщинных труб, труб с деталями (тройники, переходы, отводы, днища) концы труб должны иметь механически обработанные кромки.
2.1.12.6. Смещение внутренних кромок стыкуемых труб с одинаковой нормативной толщиной стенок не должно превышать 1,6 мм. Допускается местное смещение внутренних кромок до 2,4 мм на длине не более 100 мм.
Величина внутреннего смещения измеряется специальным шаблоном (рис. 2.1). При необходимости следует делать селекцию труб по диаметрам, могут быть использованы методы см. Приложение 5 или ВСН 006-89 (п.2.11.27).
Рис. 2.1. Схема замеров внутреннего смещения кромок
2.1.12.7. Сварочный зазор между кромками должен быть равным 1,5-3,5 мм. Зазор определяется с помощью универсального шаблона УШС-3.
2.1.12.8. Предварительный подогрев металла должен предусматривать:
- нагрев и выдержку при температуре дегазации Т д;
- охлаждение стыка до температуры начала сварки Т с.
Схема цикла предварительного подогрева концов труб перед сваркой показана на рис. 2.3, 2.4. Значения параметров подогрева Т д и Т с приведены в табл. 2.6, 2.7.
Рис. 2.3. Схема нагрева труб перед сваркой:
B - ширина зоны нагрева
|
|
Рис. 2.4. Цикл предварительного подогрева труб:
Т д - температура дегазации;
Т с - температура сварки
Таблица 2.6.
Параметры предварительного подогрева при дегазации Т д
Толщина металла, мм | Ширина зоны нагрева, мм | Температура подогрева Т д °, С* | Время выдержки, мин |
до 14 | 100-150 | 180-200 | 60 |
15-25 | 150-200 | 200-230 | 90 |
26 и более | 200-230 | 250-280 | 120 |
_______________
* Температура Т д не должна превышать 300° С
Таблица 2.7.
Температура предварительного подогрева при сварке Т с
Эквивалент углерода, С э | Толщина металла, мм | ||||
до 7,5 | 7,5-10 | 11-15 | 16-21 | 22 и более | |
0,35-0,38 | 50 | 60-80 | 90-130 | 140-160 | 170-190 |
2.1.12.9. Перед сборкой необходимо очистить внутреннюю полость труб от снега, воды, грязи и т.д.
Сборку (центровку) труб следует выполнять с помощью центраторов (наружных, внутренних).
2.1.12.10. Концы свариваемых труб газопровода (труб, находившихся в эксплуатации) перед сборкой должны быть зачищены изнутри на глубину до 100 мм от продуктов коррозии с выборкой основного металла до 0,2 мм. Сварка влажных кромок не допускается.
2.1.12.11. Приварка стыка может выполняться в любом пространственном положении. После того, как прихваточные швы выполнили свое назначение, они должны быть либо удалены, либо зашлифованы с обоих концов для возможности их включения в завершающий слой. Бракованные прихватки следует удалить шлифмашинкой.
|
|
Запрещается зажигать дугу вне шва на трубе.
2.1.13. Выполнение сварочных работ.
2.1.13.1. Сварка стыков из стали типа МWX42NS (Приложение 1а) полностью основными электродами (I очередь, подземная и надземная прокладка АГКМ*; критерии качества - табл. 2.11.
_________________
* АГКМ - Астраханское газоконденсатное месторождение
Схема сварки - "снизу-вверх".
Корневой слой - электроды диаметром 2,5-3,25 мм.
Заполняющие слои - диаметр 3,25-4,0 мм.
Облицовочный слой - диаметр 3,25-4,0 мм.
Рекомендуемые значения сварочного тока приведены в табл. 2.8.
Таблица 2.8.
Режимы сварки
Диаметр электрода, мм | Сила тока, А | ||
прихватка, корневой слой | заполняющие слои | облицовочный слой | |
2,5 | 60-90 | - | - |
3,25 | 80-110 | 80-130 | 90-130 |
4,0 | - | 130-180* | 130-180* |
_______________
* Только в случае, если толщина стенки S > 11 мм и диаметр трубы Д > 168,3 мм
2.1.13.2. Сварка стыков труб из стали типа Х42SS с полным проваром корня шва (II очередь, подземная и надземная прокладка АГКМ); критерии качества - табл. 2.12.
Схема сварки - "снизу-вверх".
Корневой слой - электрод основного типа (Е7018) или целлюлозный (Е6010) - диаметр 2,5-3,25 мм.
Заполняющие и облицовочный - электроды основного типа - диаметр 3,25-4,0 мм.
Швы ниточные (стрингерные), валик шириной В = 8-12 мм.
Ориентировочные режимы сварки приведены в табл. 2.9.
При сварке напряженных узлов (приварка арматуры, замыкающие стыки трубопроводов и др.) при выполнении корневого слоя предпочтение следует отдавать электродам основного типа.
Таблица 2.9.
Режимы сварки
Диаметр электрода, мм | Сила тока, А | ||
прихватка, корневой слой | заполняющие слои | облицовочные слои | |
2,5 (Е6010) | 60-90 | - | - |
2,5 (Е7018) | 60-90 | 70-90 | - |
3,25 (Е6010) | 90-110 | - | - |
3,25 (Е7018) | 90-120** | 90-130 | 90-140 |
4,0 (Е7018) | - | 100-140 (III и послед.) | 110-160 |
_____________
* Только для труб Д < 168 мм при толщине стенки s < 9 мм.
** Только в случае Д ³ 168 мм при толщине стенки s ³ 15 мм.
2.1.13.3. Сварку первого (корневого) слоя шва ведут постоянным током обратной или прямой полярности, сварку последующих слоев шва - на постоянном токе обратной полярности. К качеству прихваток предъявляются такие же требования, как и к корневому шву.
2.1.13.4. Длина прихватки должна быть не менее 30 мм, количество прихваток - не менее 3-х для труб диаметром до 219 мм, не менее 5-ти для труб диаметром до 530 мм.
2.1.13.5. Сварку стыка следует осуществлять непрерывно с контролем межслойной температуры. Межслойная температура в момент сварки каждого слоя должна быть не ниже температуры предварительного подогрева (табл. 2.7), но не более 300° С.
2.1.13.6. После сварки каждого слоя шва обязательна зачистка (шлифовка) абразивным инструментом. После окончания сварки поверхность облицовочного слоя шва должна быть очищена от шлака и брызг и проверены шаблоном параметры шва.
2.1.13.7. Ориентировочное число слоев шва приведено в табл. 2.10. Оптимальное число слоев уточняется на стадии проверки процедур сварки.
Таблица 2.10.
Количество слоев шва
Толщина стенки трубы, мм | Минимальное число слоев шва | |
нормальные | стрингерные | |
7 | 3 | 4 |
10 | 3-4 | 6-7 |
16 | 4 | 8 |
21 | 5-6 | 10-12 |
27 | 7-8 |
2.1.13.8. Облицовочный слой должен перекрывать основной металл в каждую сторону от разделки на 2,5-3,5 мм и иметь усиление высотой 1,5-3,0 мм.
2.1.13.9. Сварочные работы (условия сварки) должны быть отражены в исполнительной производственной документации в соответствии с формами Газнадзора, проектной нормативной документацией.
2.1.13.10. Все сварные стыки подвергаются термообработке, требования в соответствии с подразделом 3, разд. II.
2.1.14. Контроль качества сварки.
2.1.14.1. Контроль качества сварки при производстве РВР на газопроводах осуществляется на всех этапах путем 100% операционного контроля, контроля качества сварных соединений физическими методами, аттестацией процедур (технологии) сварки.
2.1.14.2. Операционный контроль включает:
- проверку соответствия труб и сварочных материалов требованиям проекта и технологических условий на их поставку согласно п.п.2.1.4-2.1.8 настоящего раздела;
- контроль квалификации сварщиков (п.п.2.1.11.1; 2.1.11.2; 2.1.11.4 настоящего раздела);
- контроль за соблюдением технологии сборки и сварки стыков труб.
2.1.14.3. Внешнему осмотру подвергаются все стыки после их очистки от шлака, грязи и брызг наплавленного металла; при этом сварные соединения не должны иметь трещин, подрезов глубиной более 0,5 мм, недопустимых смещений, незаплавленных кратеров и выходящих на поверхность пор. Усиление шва должно быть 1,5-3,0 мм, перекрытие кромок 2,5-3,5 мм. Поверхность шва должна быть мелко-чешуйчатой. Переход от наплавленного металла к основному должен быть плавным.
2.1.14.4. Сварные стыки до термической обработки подвергаются 100 % радиографическому контролю. Годными считаются те сварные соединения, величина дефектов в которых не превышает размеров, приведенных в табл. 2.11, 2.12.
После термической обработки сварные стыки подвергаются 100 % ультразвуковому контролю на предмет наличия трещин.
2.1.14.5. Методика контроля качества может быть принята в соответствии с BCH 012-88 "Контроль качества и приемка работ" /14/, ГОСТ 7512-82, ГОСТ 14782-86, Инструкция фирмы "Лавалин", /ч. 15/. Чувствительность при радиографическом контроле должна быть в пределах 2,5-3,0%.
2.1.14.6. Устранение дефектов (пор, свищей, шлаковых включений, непровара) выполняется путем механической обработки (выборки) металла шва с обеспечением стандартной разделки кромок и последующей заваркой электродом основного типа диаметром 2,5-3,25 мм на режимах согласно табл. 2.7, табл. 2.8.
2.1.14.7. Длина ремонтируемого стыка (участка) не должна превышать 1/8 периметра стыка /плюс 30 мм для труб диаметром 60 мм/. Минимальная длина - 70 мм.
Таблица 2.11.
Дата добавления: 2019-11-16; просмотров: 255; Мы поможем в написании вашей работы! |
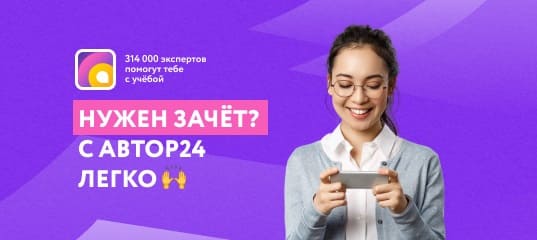
Мы поможем в написании ваших работ!