Форма и порядок выполнения самостоятельной работы. (Ход работы)
1) Изучить и законспектировать основные свойства, значение хлорметанов в промышленности, технологию получения хлорметанов по учебнику Капкин В.Д. (стр. 245-247)
2) Начертить схему процесса получения хлорметана (Капкин В.Д. стр. 246), соблюдая правила ГОСТ.
Технологическая схема процесса получения хлорметанов:
1 — реактор; 2 — циклон; 3 —колонка нейтрализации; 4 — кипятильник; 5 — холодильник; 6—8 — скрубберы; 9 — компрессор; 10, 12, 13— ректификационные колонны; 11— дефлегматор
Описание процесса
Хлор и метан подают в реактор в соотношении от 1:2 до 3,88:1 в зависимости от того, какое хлорпроизводное желательно получить.
Метан и хлор поступают в реактор 1 с псевдоожиженным слоем катализатора. Реактор выполнен на хромоникелевой стали. Хлорирование ведут при 350 °С и атмосферном давлении, время контакта 0,1—20 с. Реакционная смесь проходит систему пылеулавливания (циклон 2) и поступает на нейтрализацию в колонну 3, где отпариваются кислые газы. После этой колонны продукты реакции промывают водой в скруббере 6; при этом получается товарная соляная кислота. Далее газы нейтрализуют раствором щелочи в скруббере 7 и осушают серной кислотой в скруббере 8.
Нейтрализованные газы, содержащие в основном метан и метилхлорид, компримируют и возвращают в реактор 1 на хлорирование. Конденсат после отпаривания кислых газов поступает на ректификацию в колонны 10, 12 и 13, в которых последовательно выделяют метиленхлорид, хлороформ и тетрахлорид углерода.
|
|
Для удаления инертных примесей часть реакционного газа после компрессора 9 и скруббера 6 выводят в атмосферу (на схеме не показано). Расход основного сырья на 1 т готового продукта составляет 133 кг метана и 1784 кг хлора.
3) Подготовиться к защите работы
4. Критерии оценивания самостоятельных работ
1) Провести опрос по изученному материалу
2) Проверить правильность, лаконичность и грамотность конспектов.
3) Проверить знание технологической схемы и соблюдение стандартов при изображении этих схем.
5. Литература
1) Капкин В.Д., Савинецкая Г.А., Чапурин В.И. Технология органического синтеза.- М.;Химия, 1984, 398с.
2) Лебедев Н.Н. Химия и технология основного органического синтеза.- М.;Химия, 1998, 592с.
Самостоятельная работа № 7
1. Тема : Получение винилхлорида, технологическая схема
2. Цель работы:
Изучить способы получения винилхлорида, оценить их достоинства и недостатки, научиться изображать технологическую схему получения винилхлорида комбинированным методом с соблюдением всех требований ГОСТ.
Форма и порядок выполнения самостоятельной работы. (Ход работы)
1) Изучить и законспектировать основные способы получения винилхлорида по учебнику Капкин В.Д. (стр. 253-256)
|
|
2) Начертить схему процесса получения винилхлорида комбинированным методом (Капкин В.Д. стр. 255), соблюдая правила ГОСТ.
Технологическая схема процесса получения винилхлорида комбинированным методом:
1,2 — реакторы; 3 — конденсатор; 4 — сепаратор; 5, 7 — сборники; 6 — закалочная колонна; 8, 10, 11, 16—18 — ректификационные колонны; 9 — кипятильник; 12 — емкость; 13 — насос; 14 — печь; 15 — закалочная колонна; 19 — скруббер
Описание процесса
Синтез 1,2-дихлорэтана прямым жидкофазным хлорированием этилена проходит в реакторе 1, а окислительное хлорирование этилена — в реакторе 2. Этилен подают примерно в равных количествах в оба реактора. В реактор 1 (стальной полый аппарат) одновременно подают хлор в количестве, обеспечивающем избыток этилена 1—3%. В колонне сохраняют постоянный уровень жидкости, в которой растворен катализатор FeС13. Тепло реакции отводится за счет испарения паров дихлорэтана-1,2 и конденсации их в конденсаторе 3. Непрореагировавшие газы после улавливания паров дихлорэтана-1,2 направляют на абсорбцию. 1,2-Дихлорэтан-сырец промывают кислотой, щелочью, водой в аппарате 5 (на схеме указан один аппарат) для удаления остатков катализатора и направляют в колонну азеотропной осушки 8. В реактор оксихлорирования 2 (стальной аппарат), одновременно с этиленом подают воздух с небольшим избытком .(~5%) и хлороводород.
|
|
Процесс проводят при 0,3—0,5 МПа и 210—250 °С. В качестве катализатора используют хлориды меди, нанесенные на носитель. Тепло реакции отводится за счет испарения водного конденсата, подаваемого во встроенные в реактор змеевики. Реакционные газы, состоящие из паров 1,2-дихлорэтана, воды, непрореагировавших этилена, кислорода, хлороводорода и инертных примесей, направляют в закалочную колонну 6, орошаемую водой. В аппарате улавливаются следы пыли катализатора и хлороводорода. Затем газы поступают в конденсатор 3. Сконденсированная жидкость разделяется на 1,2-дихлорэтан-сырец и водный слой. Непрореагировавшие газы после абсорбции возвращают на оксихлорирование. Водный слой возвращается в закалочный аппарат, а 1,2-дихлорэтан-сырец подается на промывку щелочью и водой в аппарат 7 (на схеме указан один аппарат) для удаления хлораля. Отмытый 1,2-дихлорэтан-сырец поступает также в колонну азеотропной осушки 8. Здесь 1,2-дихлорэтан обезвоживается и направляется на двухступенчатую ректификацию. В колонне 10 из него выделяются низкокипящие примеси, во второй колонне 11 выделяется 1,2-дихлорэтан-ректификат со степенью чистоты 99,95%, собираемой в емкость 12. Дегидрохлорирование 1,2-дихлорэтана проводят в трубчатой печи 14 при давлении 1,5—2 МПа и 500 °С. Степень конверсии 1,2-дихлорэтана за один проход составляет 50—70%.
|
|
Продукты дегидрохлорирования из печи 14 поступают в закалочную колонну 15 для охлаждения и выделения из них смолистых продуктов. Далее продукты пиролиза поступают в колонну 16, где выделяется чистый хлороводород, который возвращается на стадию оксихлорирования. Кубовую жидкость колонны 16, состоящую из винилхлорида, 1,2-дихлорэтана, следов хлороводорода и ацетилена, подают в колонну 17 для выделения винилхлорида. Кубовый продукт колонны 17— 1,2-дихлорэтан — возвращают в колонну азеотропной осушки 8. Винилхлорид направляют в колонну 18 для отделения от следов хлороводорода и ацетилена, затем в скруббер 19, заполненный твердым гидроксидом натрия. Полученный винилхлорид содержит 99,9% основного вещества.
3) Подготовиться к защите работы
4. Критерии оценивания самостоятельных работ
1) Провести опрос по изученному материалу
2) Проверить правильность, лаконичность и грамотность конспектов.
3) Проверить знание технологической схемы и соблюдение стандартов при изображении этих схем.
5. Литература
1) Капкин В.Д., Савинецкая Г.А., Чапурин В.И. Технология органического синтеза.- М.;Химия, 1984, 398с.
2) Лебедев Н.Н. Химия и технология основного органического синтеза.- М.;Химия, 1998, 592с.
Самостоятельная работа № 8
1. Тема : Хлорирование по функциональным группам
2. Цель работы:
Освоить химизм хлорирования кислород- и азотосодержащих соединений, изучить показатели процессов.
3. Форма и порядок выполнения самостоятельной работы. (Ход работы)
1) Изучить основные закономерности хлорирования кислород- и азотосодержащих соединений.
2) Законспектировать основные показатели технологии хлорирования по функциональным группам по учебнику Лебедев Н.Н. (стр. 131-136)
Рис. 46. Реакционный узел для получения хлораля:
1, 2 — реакционные колонны; 3 — промывная колонна
Описание процесса
При непрерывном синтезе ведут процесс в каскаде из двух барботажных колонн с противотоком газа и жидкости. В первую колонну 1, где охлаждением поддерживают температуру 55— 65 °С, подают спирт и смесь хлора с HCI после второй ступени. Жидкость, содержащая смесь хлорацетальдегидов, их ацеталей и полуацеталей, перетекает во вторую колонну, работающую при 90°С, куда подают хлор и воду. Назначение воды — гидролиз ацеталей, что обеспечивает более полное использование спирта. Продукт, получаемый после второй колонны, представляет собой смесь хлоральгидрата, полуацеталя хлораля и соответствующих производных дихлорацетальдегида. Его обрабатывают концентрированной серной кислотой, разрушая гидраты и ацетали с образованием свободного хлораля.
4. Критерии оценивания самостоятельных работ
1) Провести опрос по изученному материалу
2) Проверить правильность, лаконичность и грамотность конспектов.
5. Литература
1) Капкин В.Д., Савинецкая Г.А., Чапурин В.И. Технология органического синтеза.- М.;Химия, 1984, 398с.
2) Лебедев Н.Н. Химия и технология основного органического синтеза.- М.;Химия, 1998, 592с.
Самостоятельная работа № 9
1. Тема : Получение α-оксидов
2. Цель работы:
Изучить основы технологии получения пропиленоксида, эпихлоргидрина, технологическую схему получения эпихлоргидрина
3. Форма и порядок выполнения самостоятельной работы. (Ход работы)
1) Изучить и законспектировать свойства и способы получения α-оксидов по учебнику Лебедев Н.Н. (стр. 166-168)
2) Начертить схему процесса получения эпихлоргидина (Лебедев Н.Н. стр. 168), соблюдая правила ГОСТ.
Технологическая схема получения эпихлоргидрина:
1 — реактор, 2 — холодильники-конденсаторы; 3 — сепаратор; 4 — колонна отгонки легкой фракции; 5 — колонна отделения тяжелой фракции; 6— кипятильники
Описание процесса
В реактор 1 подают водные растворы Са(OH)2 и дихлоргидрина глинерпна, а в куб дают острый пар, служащий для обогрева и отгонки продуктов. На тарелках происходит реакция омыления с образованием эпихлоргидрина и побочного продукта — глицерина. Последний стекает в куб колонны, откуда водный раствор СаС12 и избыток щелочи выводят на очистку. Летучие продукты вместе с водяным паром конденсируются в холодильнике-конденсаторе 2 и конденсат разделяется в сепараторе 3 на две фазы: водную, содержащую 6 % растворенного эпихлоргидрина, и органическую, на 85—90% состоящую из эпихлоргидрина с примесью воды, трихлорпропана, непрореагировавшего дихлоргидрина глицерина и летучих веществ — аллилхлорида и 2,8-дихлорпропилена. Водную фазу возвращают на орошение реактора /, а органическую отводят на разделение.
Вначале в колонне 4 отгоняют воду вместе с летучими веществами, которые являются отходами производства. Кубовую жидкость этой колонны направляют на дистилляцию в колонну 5, где эпихлоргидрин отгоняется от более тяжелых продуктов, собирающихся в кубе. Эту смесь непрореагировавшего хлоргидрина и трихлорпропана дополнительно разделяют, возвращая хлоргидрин на гидролиз и получая трихлорпропан в качестве товарного продукта (его наиболее рационально перерабатывать в тетрахлорэтилен и СС14 путем хлоролиза). С верха колонны 5 отбирают 98—99 %-й эпихлоргидрин, который дополнительно очищают до 99,5 %-й концентрации путем ректификации (на схеме не изображено).
При процессах щелочного дегидрохлорирования с образованием хлоролефинов реакционный узел выполняют аналогично рассмотренному. При получении пропиленоксида, полностью смешивающегося с водой, в холодильнике 2 осуществляют частичную конденсацию паров, а сепаратор 3 служит для разделения конденсата и паров. Конденсат возвращают на орошение реактора 1, а пары, состоящие главным образом из пропиленоксида, направляют на ректификацию.
3) Подготовиться к защите работы
4. Критерии оценивания самостоятельных работ
1) Провести опрос по изученному материалу
2) Проверить правильность, лаконичность и грамотность конспектов.
3) Проверить знание технологической схемы и соблюдение стандартов при изображении этих схем.
5. Литература
1) Капкин В.Д., Савинецкая Г.А., Чапурин В.И. Технология органического синтеза.- М.;Химия, 1984, 398с.
2) Лебедев Н.Н. Химия и технология основного органического синтеза.- М.;Химия, 1998, 592с.
Самостоятельная работа № 10
1. Тема : Гидратация ацетилена, реакционные узлы
2. Цель работы:
Изучить основы технологии гидратации ацетилена с ртутнымм катализатором и с нертутными катализаторами, реакционные узлы.
3. Форма и порядок выполнения самостоятельной работы. (Ход работы)
1) Изучить и законспектировать химизм, условия процесса гидратации ацетилена по учебнику Лебедев Н.Н. (стр. 184-187)
2) Начертить схему реакционных узлов для гидратации ацетилена (Лебедев Н.Н. стр. 185), соблюдая правила ГОСТ.
Реакционные узлы для гидратации ацетилена:
а — жидкофазный процесс с ртутным катализатором; б — газофазный процесс с гетерогенным нертутным катализатором
Описание процесса
Схема реакционного узла жидкофазной гидратации ацетилена изображена на рис. а. Реактором служит пустотелая колонна, футерованная кислотоупорными плитками и имеющая в верхней расширенной части слой насадки, играющей роль брызгоуловителя. Реактор заполнен катализаторной жидкостью описанного состава, через которую барботирует ацетилен, вводимый в низ колонны. Реактор не имеет поверхностей теплообмена и работает при 90°С автотермически: выделяющееся тепло отводится за счет испарения воды, которая конденсируется в обратном холодильнике и возвращается в реактор. Часть катализаторного раствора непрерывно отводят на регенерацию и заменяют регенерированным раствором. Из газофазовой смеси, выходящей из реакционного узла, абсорбируют водой ацетальдегид, возвращают ацетилен на реакцию, а водный раствор ацетальдегида подвергают ректификации.
Газофазную гидратацию ацетилена проводят в колонном аппарате с несколькими сплошными слоями катализатора (см. рис. б). Предварительно нагретую смесь водяных паров и ацетилена вводят в верхнюю часть реактора, а снизу отводят реакционные газы на конденсацию и разделение. Аппарат не имеет поверхностей теплообмена — съем выделяющегося тепла осуществляют за счет испарения водного конденсата, вбрызгиваемого в пространство между слоями катализатора. Они разделены, кроме того, колпачковыми тарелками, препятствующими попаданию брызг в последующие слои катализатора.
Кроме сравнительно низкого выхода ацетальдегида, существенным недостатком газофазного процесса является небольшой срок службы катализатора — его приходится регенерировать каждые 100 ч. С учетом этого общий срок службы катализатора составляет всего 2500 ч.
3) Подготовиться к защите работы
4. Критерии оценивания самостоятельных работ
1) Провести опрос по изученному материалу
2) Проверить правильность, лаконичность и грамотность конспектов.
3) Проверить знание схем реакционных узлов и соблюдение стандартов при изображении этих схем.
5. Литература
1) Капкин В.Д., Савинецкая Г.А., Чапурин В.И. Технология органического синтеза.- М.;Химия, 1984, 398с.
2) Лебедев Н.Н. Химия и технология основного органического синтеза.- М.;Химия, 1998, 592с.
Самостоятельная работа № 11
1. Тема : Жидкофазные процессы этерификации, реакционные узлы
2. Цель работы:
Освоить технологию жидкофазного синтеза эфиров карбоновых кислот, химизм и условия процесса, изучить состав реакционной массы.
3. Форма и порядок выполнения самостоятельной работы. (Ход работы)
1) Изучить и законспектировать свойства получаемых эфиров карбоновых кислот, условия процесса получения, технологию по учебнику Лебедев Н.Н. (стр. 199-204)
2) Начертить реакционные узлы для жидкофазных процессов этерификации (Лебедев Н.Н. стр. 203), соблюдая правила ГОСТ.
Реакционные узлы для жидкофазных процессов этерификации, совмещенных с отгонкой азеотропной смеси:
а—куб с конденсатором; б — куб с дефлегмирующей колонной ; в — куб с ректификационной колонной; г — реактор типа тарельчатой колонны
Описание процесса
Процесс этерификации, совмещенный с отгонкой, можно осуществлять периодическим или непрерывным способом; наибольшее применение имеет последний. Основные варианты оформления реакционных узлов непрерывной этерификации изображены на рисунке.
Первые три имеют реакторы-эфиризаторы (кубы) достаточно большой емкости, обогреваемые паром через рубашку или змеевики. Жидкость в реакторе находится в состоянии кипения
(или испарения из нее летучего компонента), и при непрерывной подаче исходных веществ и отгонке летучего продукта протекает химическое превращение. Узлы а, б и в различаются лишь эффективностью систем разделения: в первой имеется только обратный конденсатор, во второй дефлегмирующая колонка, в третьей ректификационная колонна с собственным кипятильником, что позволяет увеличить флегмовое число и эффективность разделения. Соответственно этому, каждую из этих схем целесообразно применять при большом, среднем или малом различии в летучестях кубовой жидкости, остающейся в реакторе, и отгона, удаляемого из реакционной массы. Эти три схемы пригодны в тех же случаях и для периодических процессов этерификации, причем схемы изображены для систем, в которых эфир остается в кубе, а летучим компонентом является азеотропная смесь воды и эфира, которая разделяется в сепараторах на два слоя (воду выводят из системы).
При непрерывной этерификации (схемы а, б и в) кубы будут работать удовлетворительно лишь при высокой скорости химической реакции, иначе полнота превращения или производительность реактора будут слишком низкими. Поэтому для непрерывных процессов часто применяют последовательность (каскад) эфиризаторов с перетоком кубовой жидкости из одного реактора в другой, но с соответствующей разделительной системой при каждом эфиризаторе.
Другое решение состоит в применении эфиризатора типа тарельчатой колонны (схема г). Каждая тарелка, имеющая слой жидкости высотой 0,5—1,0 м, играет роль отдельного реактора, причем жидкость перетекает по колонне сверху вниз и
находится на каждой тарелке в состоянии кипения, что обеспечивает совмещение химической реакции с ректификацией. Катализатор и менее летучий реагент (обычно кислота) подают на одну из верхних тарелок, а второй реагент — в определенное место по высоте колонны, соответствующее летучести реагента, причем жидкость и пар движутся противотоком. Такой узел особенно пригоден для сравнительно медленных химических реакций (обычных при этерификации с невысокой концентрацией катализатора) и при небольшом различии в летучести отгона и кубового остатка.
3) Подготовиться к защите работы
4. Критерии оценивания самостоятельных работ
1) Провести опрос по изученному материалу
2) Проверить правильность, лаконичность и грамотность конспектов.
3) Проверить знание технологической схемы и соблюдение стандартов при изображении этих схем.
5. Литература
1) Капкин В.Д., Савинецкая Г.А., Чапурин В.И. Технология органического синтеза.- М.;Химия, 1984, 398с.
2) Лебедев Н.Н. Химия и технология основного органического синтеза.- М.;Химия, 1998, 592с.
Самостоятельная работа № 12
1. Тема : Алкилирование изопарафинов олефинами
2. Цель работы:
Освоить технологию получения алкилата при алкилировании изопарафинов олефинами в присутствии серной кислоты, как катализатора
3. Форма и порядок выполнения самостоятельной работы. (Ход работы)
1) Изучить и законспектировать технологию, условия процесса алкилирования изобутана бутеном по учебнику Капкин В.Д. (стр. 132-135)
2) Начертить технологическую схему алкилирования изобутана бутеном в присутствии серной кислоты (Капкин В.Д. стр. 133), соблюдая правила ГОСТ.
3) Подготовиться к защите работы
Технологическая схема алкилирования изобутана бутеном:
1 — алкилатор; 2 — сепаратор-ресивер; 3 —дроссельный вентиль; 4 — компрессор- 5 —холодильник-конденсатор; 6 — депропанизатор; 7 —насос; 8, 10 — сепараторы- 9 — нейтрализатор; 11— промежуточная емкость; 12— каплеотбойник; 13— дебутанизатор
Описание процесса
Свежая и циркулирующая серная кислота и жидкий изобутан поступают в первую секцию каскадного алкилатора 1. Олефиновое сырье параллельными потоками подают в каждую секцию реактора.
Теплота реакции отводится за счет частичного испарения избыточного изобутана, пары которого поступают в емкость 2, служащую одновременно ресивером и сепаратором. Отсюда газ непрерывно забирается компрессором 4, сжимается до 0,6 Мпа и при этом давлении конденсируется в водяном холодильнике 5. В дроссельном вентиле 3 давление снижается до рабочего (~0,2 МПа), при этом часть изобутана испаряется и разделяется в емкости 2. Жидкий изобутан вновь поступает в алкилатор. В процессе работы в изобутане постепенно накапливается пропан, образующийся в результате деструкции углеводородов и присутствующий в исходных углеводородных фракциях. Поэтому в изобутановый холодильный цикл включен депропанизатор — ректификационная колонна 6, в которую отводят часть циркулирующего изобутана после холодильника 5.
Продукт, выходящий из последней секции алкилатора, представляет собой смесь избыточного изобутана, н-бутенов, углеводородов С5—С7, октанов и более высокомолекулярных углеводородов. Эта смесь проходит дополнительный сепаратор 8, где происходит отделение остатков серной кислоты. Часть кислоты возвращают в алкилатор 1, а часть отводят из системы на регенерацию, а вместо нее подают свежую. Углеводородный слой из сепаратора 8 нейтрализуют 10%-ным водным раствором щелочи в аппарате 9, а полученную при этом эмульсию разделяют в сепараторе 10. Нейтрализованная смесь стекает в емкость 11, откуда поступает в ректификационную колонну (дебутанизатор) 13. В эту же колонну подают и свежую изобутановую фракцию. Ректификацию ведут под давлением 0,6 МПа. Часть изобутана возвращается на орошение колонны 13, а остальное количество после дросселирования поступает в емкость 2. Из куба колонны 13 алкилат-сырец направляют на ступенчатую ректификацию (на схеме не показано); вначале отгоняют низшие углеводороды, затем алкилат, в кубе последней колонны содержится тяжелый остаток из углеводородов С9 и выше.
4. Критерии оценивания самостоятельных работ
1) Провести опрос по изученному материалу
2) Проверить правильность, лаконичность и грамотность конспектов.
3) Проверить знание технологической схемы и соблюдение стандартов при изображении этой схемы.
5. Литература
1) Капкин В.Д., Савинецкая Г.А., Чапурин В.И. Технология органического синтеза.- М.;Химия, 1984, 398с.
2) Лебедев Н.Н. Химия и технология основного органического синтеза.- М.;Химия, 1998, 592с.
Самостоятельная работа № 13
1. Тема : Алкилирование бензола этиленом и пропиленом
2. Цель работы:
Освоить технологию алкилирования бензола этиленом, пропиленом, изучить химизм, условия, целевые и побочные продукты реакции
3. Форма и порядок выполнения самостоятельной работы. (Ход работы)
1) Изучить и законспектировать технологию, условия процесса алкилирования бензола по учебнику Капкин В.Д. (стр. 135-137)
2) Начертить технологическую схему алкилирования бензола этиленом в присутствии хлорида алюминия (Капкин В.Д. стр. 135), соблюдая правила ГОСТ.
Технологическая схема алкилирования бензола этиленом:
1 — мешалка; 2 — абсорбционная колонна; 3—насос; 4 — сепаратор; 5, 9, 13 — холодильники; 6—емкость; 7 - алкилатор; 8,10, 16— отстойники; 11—колонна разложения- катализаторного комплекса; 12 — деалкилатор; 14 — нейтрализатор; 15— скруббер
Описание процесса
Процесс проводят в алкилаторе 7 — колонне, эмалированной или футерованной графитовой плиткой для защиты от коррозии. Основное количество выделяющегося тепла отводят путем испарения некоторой части исходного бензола. Алкилирование ведут в присутствии жидкого катализаторного комплекса, содержащего 10—12% хлорида алюминия, 50—60% бензола и 25—30% полиалкил бензолов. Для образования хлороводорода, который является промотором реакции, в катализаторный комплекс добавляют воду (2% от количества хлорида алюминия), а также дихлорэтан или этилхлорид, при разложении которых выделяется хлороводород.
Катализаторный комплекс, приготовленный в аппарате 1, подают в емкость 6, в которую поступают свежий осушенный бензол и полиалкилбензолы из абсорбционной колонны 2 и отстойника 8. Далее всю эту смесь направляют в алкилатор 7, куда снизу через распылитель подают олефиновую фракцию.
Газы, выходящие из алкилатора, охлаждаются в холодильнике 5 и поступают в сепаратор 4, где выделяется бензол, возвращаемый в алкилатор. Пары бензола, не отделенные в сепараторе, поглощаются полиалкилбензолами в колонне 2.
Продукты алкилирования отделяются в отстойниках 8 и 10 от катализаторного комплекса и через сепаратор 4 поступают в колонну 11, где остатки комплекса разлагаются водой. Далее алкилат промывают щелочью (в нейтрализаторе 14) и водой (в скруббере 15) и через отстойник 16 направляют на ректификацию. Высококипящие полиалкилбензолы из отстойника 10 периодически выводят на деалкилирование (при 200—260 °С) в аппарат 12, а продукты деалкилирования возвращают в алкилатор. Они имеют следующий состав: 62—63% бензола, 28— 29% этилбензола и 7,2—7,3% полиалкилбензолов.
Для выделения этилбензола из алкилата отгоняют бензол при атмосферном давлении (при этом одновременно удаляются следы влаги). От кубовой жидкости при пониженном давлении (26,6 кПа) отгоняют широкую фракцию (смесь этил- и полиалкилбензолов). В следующей колонне при остаточном давлении 6,65 кПа отделяют полиалкилбензолы от смол. Широкую фракцию разгоняют в вакуумной колонне при остаточном давлении 56—60 кПа. Товарный этилбензол перегоняется в пределах 135,5—136,2°С.
3) Подготовиться к защите работы
4. Критерии оценивания самостоятельных работ
1) Провести опрос по изученному материалу
2) Проверить правильность, лаконичность и грамотность конспектов.
3) Проверить знание технологической схемы и соблюдение стандартов при изображении этой схемы.
5. Литература
1) Капкин В.Д., Савинецкая Г.А., Чапурин В.И. Технология органического синтеза.- М.;Химия, 1984, 398с.
2) Лебедев Н.Н. Химия и технология основного органического синтеза.- М.;Химия, 1998, 592с.
Самостоятельная работа № 14
1. Тема : Технология сульфатирования, реакционные узлы
2. Цель работы:
Освоить технологию получения ПАВ сульфатированием серной кислотой спиртов и олефинов, условия, состав реакционной массы.
3. Форма и порядок выполнения самостоятельной работы. (Ход работы)
1) Изучить и законспектировать технологию, условия процесса сульфатирования спиртов и олефинов по учебнику Лебедев Н.Н. (стр. 308-313)
2) Начертить технологическую схему производства моющего средства на основе алкилсульфата, реакторы для процессов сульфатирования и сульфирования (Лебедев Н.Н. стр. 312, 313), соблюдая правила ГОСТ.
Реакторы для процессов сульфатирования и сульфирования:
а — аппарат с реакционной тарелкой (стакан), б — реактор с турбинной мешалкой; в — аппарат с вращающимся внутренним барабаном; а—пленочный реактор
Описание процесса
Разные варианты оформления реакционного узла при сульфатировании спиртов триоксидом серы изображены на рис. (б, в, г).
В одном из них применяют каскад из двух-трех реакторов с турбинными мешалками, охлаждающими змеевиками и рубашками (б). Внутри реактора благодаря цилиндрическому кожуху создается высокотурбулентный вертикальный поток смеси, обеспечивающий интенсивную циркуляцию и теплоотвод. При этом жидкость движется последовательно через все реакторы каскада, а разбавленный воздухом SO3 подают параллельно в каждый из них.
В другом типе реактора (в) имеются кожух с охлаждающей рубашкой и внутренний вращающийся барабан; на его внешней поверхности есть штыри, способствующие лучшему перемешиванию и турбулизации потока реагентов, движущихся снизу вверх в узком кольцевом пространстве между кожухом и барабаном. Эта конструкция достаточно сложная, и сейчас применяют главным образом пленочные реакторы. Они бывают (г) одно- и многотрубные (типа кожухотрубных теплообменников с пленкой жидкости, стекающей по трубам, и с охлаждением рассолом или водой, циркулирующими в межтрубном пространстве). Органический реагент вводят сверху через специальные дозирующие устройства, что обеспечивает на стенках образование равномерно стекающей пленки жидкости. Разбавленный воздухом SО3 подают тоже сверху, прямотоком к жидкости, причем, чтобы SО3 не попадал в верхнюю часть реактора, туда вводят воздух, а разбавленный SО3 подают через специальные трубы, опущенные в реакционное пространство.
3) Подготовиться к защите работы
4. Критерии оценивания самостоятельных работ
1) Провести опрос по изученному материалу
2) Проверить правильность, лаконичность и грамотность конспектов.
3) Проверить знание технологической схемы и соблюдение стандартов при изображении этой схемы.
5. Литература
1) Капкин В.Д., Савинецкая Г.А., Чапурин В.И. Технология органического синтеза.- М.;Химия, 1984, 398с.
2) Лебедев Н.Н. Химия и технология основного органического синтеза.- М.;Химия, 1998, 592с.
Самостоятельная работа № 15
1. Тема : Гидрирование по функциональным группам, узлы для жидкофазного гидрирования
2. Цель работы:
Освоить технологию гидрирования кислородсодержащих, азотосодержащих соединений, изучить технологию жидкофазного гидрирования, реакционные узлы.
3. Форма и порядок выполнения самостоятельной работы. (Ход работы)
1) Изучить и законспектировать технологию, условия процесса гидрирования по функциональным группам, технологию жидкофазного гидрирования по учебнику Лебедев Н.Н. (стр. 483-500)
2) Начертить реакционные узлы для жидкофазного гидрирования (Лебедев Н.Н. стр. 499), соблюдая правила ГОСТ.
Реакционные узлы для жидкофазного гидрирования:
а- колонна периодического действия с выносным охлаждением для процесса с суспендированным катализатором; б — каскад колонн непрерывного действия с внутренним охлаждением для процесса с суспендированным катализатором; в — колонна непрерывного действия с внутренним охлаждением для процесса со стационарным катализатором; г — колонна непрерывного действия с охлаждением холодным водородом для процесса со стационарным катализатором
Описание процесса
На рис. а показан реакционный узел периодического действия для работы с суспендированным катализатором. Реакционная колонна, рассчитанная на соответствующее давление, примерно на 3/4 заполнена жидкой реакционной массой, через которую барботирует водород, подаваемый снизу через распределительное устройство. Верхняя часть колонны расширена и играет роль брызгоуловителя (там имеются полки или слой насадки из колец Рашига). Отвод реакционного тепла осуществляют путем принудительной циркуляции жидкости через выносной холодильник. Водород подают в колонну в значительном избытке, чтобы турбулизовать движение жидкости и поддержать катализатор в суспендированном состоянии. Непрореагировавший водород выходит из колонны сверху и обычно нахватывает с собой пары реагентов и воды, выделяющейся при гидрировании. Его охлаждают, отделяют от конденсата и возвращают циркуляционным компрессором в колонну гидрирования. По окончании операции заполняют реактор новой порцией реагента с катализатором, нагревают жидкость паром до требуемой температуры и начинают циркуляцию водорода.
О завершении процесса судят по данным анализа реакционной массы.
Рассмотренный реактор не пригоден для непрерывного процесса, поскольку он работает в режиме полного смешения. При непрерывных подводе исходного вещества и отводе образующегося продукта производительность аппарата и полнота завершения реакции окажутся неудовлетворительными.
По этой причине для непрерывного процесса с суспендированным катализатором приходится использовать каскад из двух или более последовательных колонн (рис. 6). В этой схеме исходный реагент подают только в первую колонну, и жидкость перетекает из одного аппарата в другой. Чтобы избежать излишнего перемешивания реакционной массы, здесь лучше применить внутреннее охлаждение и прямоток жидкости и газа, подаваемых в нижнюю часть колонн и выводимых сверху. В зависимости от рабочей температуры хладагентом может служить вода или йодный конденсат. В последнем случае на установке генерируется пар, используемый для производственных нужд.
При работе со стационарным слоем катализатора только в редких случаях слабоэкзотермических реакций можно использовать адиабатические аппараты с одним сплошным слоем катализатора. Чаще катализатор укладывают в специальные корзины с перфорированным дном; в пространстве между корзинами находятся охлаждающие змеевики (рис. б) или вводится холодный водород (рис. г), аккумулирующий реакционное тепло. В этих случаях каждый слой катализатора работает в адиабатическом режиме, и реагенты, проходя через слой, разогреваются, после чего перед следующим слоем катализатора происходит охлаждение смеси. Направление потоков жидкости и водорода может в принципе быть трех вариантов: противоток жидкости с верха колонны и газа с низа; прямоток жидкости и газа снизу вверх; прямоток, наоборот, сверху вниз. Во втором случае, изображенном на рис. в, реактор работает с затоплением слоя катализатора, что ведет к значительному увеличению его гидравлического сопротивления. Если оба реагента подают с верха колонны, насадка катализатора только орошается жидкостью (рис. г) и гидравлическое сопротивление становится небольшим.
3) Подготовиться к защите работы
4. Критерии оценивания самостоятельных работ
1) Провести опрос по изученному материалу
2) Проверить правильность, лаконичность и грамотность конспектов.
3) Проверить знание технологических узлов и соблюдение стандартов при их изображении.
5. Литература
1) Капкин В.Д., Савинецкая Г.А., Чапурин В.И. Технология органического синтеза.- М.;Химия, 1984, 398с.
2) Лебедев Н.Н. Химия и технология основного органического синтеза.- М.;Химия, 1998, 592с.
Самостоятельная работа № 16
1. Тема : Термическое дегидрирование н-парафинов
2. Цель работы:
Освоить технологию дегидрирования н-парафинов при повышенных температурах, условия процесса, целевые и побочные продукты
3. Форма и порядок выполнения самостоятельной работы. (Ход работы)
1) Изучить и законспектировать технологию, условия процесса дегидрирования н-парафинов при повышенных температурах по учебнику Капкин В.Д. (стр. 94-96)
2) Начертить печь градиентного типа для термического дегидрирования н-парафинов (Капкин В.Д. стр. 96).
Печь градиентного типа:
1—каркас; 2 — беспламенные панельные горелки; 3 — смотровые окна; 4 —радиантные трубы; 5 —потолок; 6 — подвеска для труб; 7 — конвекционная камера; 8 —трубная решетка
Описание процесса
Основными реакторами для термического дегидрирования углеводородов являются двухкамерные трубчатые печи с панельными беспламенными горелками, так называемые печи градиентного типа. В каркас печи 1, выложенный из огнеупорного кирпича, вмонтированы беспламенные панельные горелки 2 для сжигания топлива. Трубы, по которым проходит углеводородное сырье, образуют конвекционную камеру 7. В ней происходит предварительный подогрев сырья за счет конвективной теплопередачи. Дегидрирование протекает в радиантных трубах 4, причем теплопередача идет за счет излучения тепла от нагретого топочного газа и от огнеупорной кладки печи. Продукты реакции из печи направляют на закалку водой (с целью прекращения процесса), а затем на охлаждение и промывку.
3) Подготовиться к защите работы
Дата добавления: 2019-07-15; просмотров: 380; Мы поможем в написании вашей работы! |
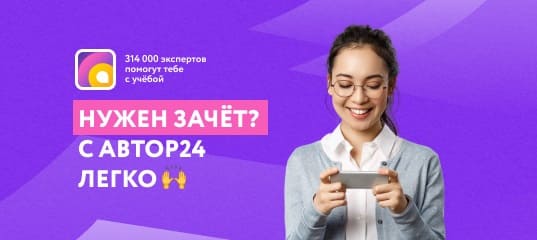
Мы поможем в написании ваших работ!