ПРАКТИЧЕСКОЕ ПРИМЕНЕНИЕ МЕТАЛЛОТЕРМИИ
Получение лития
В настоящее время основной промышленный способ получения металлического лития – электролиз. Однако определённые недостатки этого процесса заставляют искать другие методы получения металла. Описаны лабораторные опыты по металлотермическому восстановлению лития: восстановление гидроксида лития магнием в железной реторте с последующей отгонкой металла. При этом литий содержал много магния и гидрида.
Делались попытки восстановить LiCl кальцием. Получавшийся металл содержал 3–4 % Са.
Для получения лития особой чистоты может быть применён процесс восстановления хромата лития порошкообразным цирконием:
2Li2CrO4 + Zr → 4Li + Zr (CrO4)2.
Реакционною смесь прессуют и загружают в аппарат. Восстановление проводят в вакууме при 450–600 °С. Образовавшийся литий отгоняют при 1000 °С. Выход металла при этом невелик. Чистота получаемого лития обеспечивается малой летучестью остальных компонентов реакции.
В более поздних работах делались попытки применить вакуумное металлотермическое восстановление LiF, LiCl, Li2О магнием, алюминием и кремнием. При этом реакционную смесь в виде брикетов загружают в вакуумную реторту. Остаточное давление в реторте обычно 10–3 мм рт. ст. В качестве продуктов реакции восстановления получается моноалюминат или ортосиликат лития. Для предотвращения связывания лития в моноалюминат в шихту вводят СаО. В этом случае реакция восстановления описывается уравнениями:
|
|
3Li2O + CaO + 2Al → CaO·Al2O3 + 6Li
или
2Li2O + 2CaO + Si → 2CaO·SiO2 + 4Li.
Металл, полученный по второй реакции, содержал 0,01 % Si, 0,01 % Аl и 0,04 % Са; выход лития составлял 81–84 %.
Исследовали процесс восстановления алюмината лития порошком алюминия в вакууме 0,1–0,5 мм рт. ст. при 1150–1200 °С. При этом протекает реакция, которую можно описать уравнением:
3LiAlO2 + Al → 2Al2O3 + 3Li
Выход металлического лития достигал 90 %. Таким способом получают металлический литий высокой чистоты. Анализ зависимости энергии Гиббса соединений, принимающих участие в реакциях восстановления лития, от температуры показывает, что для большинства восстановителей реакцию удаётся осуществить лишь благодаря большой летучести лития (удалению его из сферы реакции и тем самым сдвигу равновесия). Величина ΔG° для соединений лития мало отличается от ΔG° для соединений металлов-восстановителей (Mg, Са). Поэтому литий можно получить лишь вакуумной металлотермией.
Исходными продуктами для металлотермического способа восстановления лития являются карбонат (после его термического разложения до оксида) или гидроксид лития, т.е. продукты большинства схем переработки рудных концентратов. Литий получают достаточно чистым непосредственно из технических солей. Однако этот способ получения металлического лития до настоящего времени находится в стадии лабораторных разработок.
|
|
Большой интерес представляют работы по получению лития непосредственно из сподумена восстановлением ферросилицием или алюминием. Описаны также попытки использовать магний для восстановления сподумена. Восстановление измельчённого сподумена проводят в реторте из жаростойкой стали при 1050–1100 °С и вакууме 0,01–0,02 мм рт. ст. В шихту вводят также известь (СаО). Извлечение Li достигает 85 %. Получающийся литий загрязнен магнием, натрием и калием (которые попадают в конденсируемый металл из извести и исходного сподумена). Прямое восстановление лития из сподумена имеет некоторые преимущества, однако при этом невозможно получить чистый металл. Вакуумная разгонка чернового металла сильно удорожает продукт, сводя на нет выгоды прямого процесса. Кроме того, малое содержание лития в брикетах требует значительного избытка восстановителя.
Получение лития металлотермическим способом имеет следующие преимущества перед электролизом: возможность использования карбоната или гидроксида в качестве исходных соединений и получение лития, свободного от натрия и калия, непосредственно из технических солей.
|
|
Получение бериллия
В настоящее время промышленное получение бериллия в основном осуществляется магниетермическим методом. Хлорид бериллия гораздо менее устойчив, чем оксид (рис. 3, 4), все галогениды восстанавливаются многими более активными металлами, но не водородом. Следует отметить, что BeO относится к наиболее устойчивым оксидам, что определяет его использование для изготовления тиглей для плавки различных металлов (при этом расплав не загрязняется кислородом). Восстановление кальцием не применяют из-за образования устойчивого соединения CaBe13.
В промышленном производстве бериллия используют в основном фторид, отличающийся сравнительно высокой температурой плавления и кипения. При этом осуществляют реакцию:
BeF2 + Mg → MgF2 + Be.
Изменение энергии Гиббса данной реакции равно: 298 К ΔG, кДж/моль – 157,5; 1000 К − 138,6; 2000 К − 34,8.
Реакцию получения бериллия проводят в тиглях из плотного графита с графитовой крышкой. Поскольку ВеF2 токсичен и гигроскопичен, тонкого измельчения перед загрузкой в тигель не производят. Поэтому сначала реакция протекает медленно. Обычно процесс осуществляют в индукционной печи. Физические свойства реагентов и продуктов реакции представлены в табл. 5.
|
|
Таблица 5
Физические свойства BeF 2 , MgF 2 , Be и Mg
Свойство | BeF2 | MgF, | Be | Mg |
Температура, ºС: плавления кипения | 787 1327 | 1240 2230 | 1283 2970 | 660 1107 |
Плотность, г /см3 | 2,0 | 3,1 | 1,85 | 1,74 |
Растворимость при комнатной температуре, г/ 100 г воды | 50 | 0,012 | Не растворим | Не растворим |
BeF2 должен быть высокой чистоты, поскольку в процессе восстановления примеси практически не удаляются. Его получают разложением фторбериллата аммония, который, в свою очередь, получают растворением гидроксида бериллия в бифториде аммония. В измельчённом состоянии BeF2 реагирует с магнием с достаточной скоростью уже при 900 °С, однако обычно в конце процесса поддерживается температура 1300 °С для расплавления бериллия и ВеF2.
При проведении реакции со стехиометрическим соотношением компонентов не удаётся получить хорошее разделение продуктов реакции, поэтому в шихту обычно вводят значительный избыток BeF2. Хорошие результаты достигаются при введении в смесь магния в количестве всего 75 % от стехиометрического. Применение шихты, содержащей более 85 % стехиометрически необходимого количества магния, делает невозможным отделение металла от шлака. Большой избыток ВеF2 обеспечивает быстрое измельчение шлака. В шлаке фторид магния находится в виде довольно крупных игольчатых кристаллов, каждый из которых заключён в плёнку BeF2. В процессе мокрого измельчения плёнка ВеF2 растворяется, шлак растрескивается, частицы металлического бериллия высвобождаются. Избыточный BeF2 делает шлак более легкоплавким и текучим, растворяет ВеО, снижает равновесное количество магния в реакционной смеси и частично связывает MgF2. Основная часть металла в конце процесса плавает в виде линзы на поверхности шлака и удаляется после охлаждения тигля до 1200 °С.
Описаны установки периодического действия с графитовым тиглем диаметром 610 мм. Загрузка представляет собой шихту, состоящую из 118 кг ВеF2 и 43,5 кг магния (гранулы BeF2, полученные разложением фторбериллата аммония в печи непрерывного действия, и кубики магния с длиной ребра 25 мм). Продолжительность цикла 3,5 ч. По окончании реакции жидкотекучее содержимое тигля выливают в графитовый тигель-приёмник. После охлаждения содержимое приёмника загружают в шаровую мельницу для выщелачивания горячей водой. Раствор BeF2 направляют на повторное использование. Нерастворимый MgF2 отделяют от раствора в отстойнике. Мелкие кристаллы бериллия, захваченные фторидом магния, растворяют в плавиковой кислоте. После окончания этой операции MgF2 отфильтровывают, промывают и направляют в отвал. Общее извлечение бериллия составляет 96–97 %.
Полученный таким способом бериллий содержит около 3 % примесей (0,2–0,5 % металлических примесей, кроме магния; 0,02 % С; 0,1 % ВеО; 1,5 % Mg в виде металла и фторида). Последующая вакуумная переплавка позволяет получить бериллий с содержанием не более 0,03–0,05 % Mg.
Для получения ВеF2 технический оксид или гидроксид бериллия можно растворять в плавиковой кислоте. Затем в раствор вводят NH4F для образования фторбериллата аммония. Это соединение хорошо растворимо, кристаллизуется без кристаллизационной воды и не подвержено гидролизу. Степень его диссоциации в растворе настолько мала, что рН раствора может изменяться в широких пределах без осаждения гидроксида бериллия. Поэтому содержащиеся в растворе примеси можно осадить и сравнительно легко удалить, что обеспечивает хорошую очистку раствора. Для очистки можно использовать также сорбционные и экстракционные методы. Очищенный раствор упаривают до выпадения кристаллов. Соль отделяют и сушат, а затем подвергают термическому разложению. Диссоциация начинается при температуре около 125 °С, однако разложение ниже точки плавления приводит к образованию пористой и рыхлой, гидролизующейся на воздухе массы. Поэтому разложение проводят при температуре около 900 °С.
Восстановление фторида бериллия натрием не получило распространения ввиду того, что натрий разрушает графит и обладает низкой температурой кипения (880 °С). Хлорид бериллия также менее удобен для металлотермического восстановления, так как его температура кипения 488 °С. Наиболее изучена в лабораторных условиях реакция:
2Na(пар) + BeCl2(пар) → Be(тв) + 2NaCl(ж)
Промышленному осуществлению этой реакции мешают большие трудности в подборе конструкционных материалов.
Дата добавления: 2019-02-26; просмотров: 441; Мы поможем в написании вашей работы! |
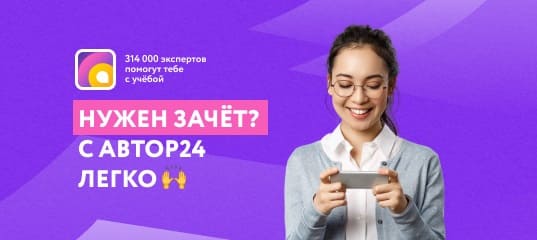
Мы поможем в написании ваших работ!