Легирующие сплавы с редкими металлами
Легирующие сплавы предназначены для введения в состав металлов и сплавов легирующих элементов, улучшающих свойства материала. В качестве легирующих элементов широко применяются редкие металлы. Для лучшего усвоения легирующего элемента его вводят в основной материал в виде вспомогательных сплавов (лигатур). В чёрной металлургии собственно лигатуры отличают от ферросплавов, используемых не только для легирования, но и для раскисления металлов.
Феррониобий
Основными ниобийсодержащими материалами для проведения восстановительной плавки феррониобия являются пирохлоровый концентрат и технический оксид ниобия (V).
Пирохлоровый концентрат состоит из минерала пирохлора, который имеет химический состав (Са, Na)2(Nb, Ti)2O6 (О, ОН, F). Содержание суммы оксидов Nb2O5 и сопутствующего ему Ta2О5 в техническом оксиде ниобия (V), используемом для проведения алюминотермического процесса, должно быть не менее 85 %.
Для получения сплава ниобия с железом заданного состава и улучшения тепловых условий проведения процесса применяют железную руду, которая взаимодействует с алюминием с большим тепловым эффектом.
В промышленных условиях феррониобий получают из технического оксида ниобия (V) в наклоняющемся футерованном реакторе. При этом шихту, содержащую флюсы, постепенно загружают на образующийся расплав продуктов по реакции:
Nb2O5 + Fe2О3 + Al + CaO + MgO → (Nb + Fe) + (A12О3 + CaO + MgO).
|
|
Содержание ниобия в получаемом расплаве достигает 70 %.
В отличие от технического оксида ниобия (V) пирохлоровый концентрат содержит повышенное количество соединений (теплового балласта), на нагрев которых затрачивается тепло. Поэтому восстановительные плавки феррониобия с применением пирохлорового концентрата проводят электропечным способом. Внешний нагрев позволяет исключить загрузку в шихту тепловыделяющих греющих добавок – окислителей.
На первой стадии электропечного процесса на дно реактора загружают железотермитную смесь, состоящую из железной руды, алюминия и извести. Опуская в смесь электроды и зажигая между ними электрическую дугу, инициируют металлотермическую реакцию и выдерживают образуемые продукты в расплавленном состоянии.
На второй стадии на поверхность расплава загружают шихту, состоящую из пирохлорового концентрата, алюминиевого порошка, железной руды и частиц металлического железа. По окончании процесса продукты восстановительной плавки выдерживают в расплавленном состоянии для доосаждения металлических капель в слиток и сливают из реактора в изложницу.
Феррониобий, получаемый при алюминотермическом восстановлении пирохлорового концентрата, содержит: 56 – 62 % (Nb + Та), 10 – 13 % Si, 2 – 6 % Al, 3 – 8 % Ti. Для снижения содержания кремния в получаемом сплаве предложен способ, включающий дополнительную стадию окисления продукта плавки. По этому способу после окончания восстановительного процесса шлак сливают из реактора, а на поверхность расплавленного металла загружают смесь извести и ниобиевого концентрата, после чего барботируют через жидкий металл кислород. В результате продувки расплава кислородом образуется преимущественно оксид кремния (IV), который переходит в шлак. Однако при этом происходит и частичное окисление ниобия.
|
|
Для снижения степени окисления ниобия продувку ведут при небольшой скорости подачи кислорода. В процессе барботирования происходит охлаждение расплава. Поэтому периодически подачу кислорода прекращают во избежание кристаллизации металла.
Рассмотренный технический приём позволяет уменьшить отношение содержания кремния к ниобию в феррониобии до 0,01 при дополнительных потерях ниобия из сплава, составляющих 8 – 10 %.
Ферротитан
При алюминотермическом производстве ферротитана в качестве титансодержащего сырья применяют ильменитовый концентрат с содержанием минерала ильменита (FeTiО3) не менее 96,5 %. Помимо ильменита, в состав шихты для получения ферротитана входят: железная руда, поваренная соль, известь, а также кварцит и ферросилиций. Повышение содержания кремния в алюминотермической шихте способствует увеличению извлечения титана в сплав. Это обусловлено тем, что титан образует с кремнием более прочные соединения, чем с алюминием.
|
|
Шихтование компонентов для проведения восстановительной плавки ферротитана характеризуется следующими особенностями. Во-первых, для улучшения теплового баланса металлотермического процесса ильменитовый концентрат подают на стадию шихтования непосредственно после окислительного обжига с температурой 300 – 450 °С. Во-вторых, операция шихтования совмещена с операцией измельчения металла-восстановителя. Согласно разработанному способу, во вращающуюся смесительную машину с загруженным в неё ильменитовым концентратом под давлением нагнетают жидкий алюминий. Измельчение алюминия происходит в результате истирания между вращающимися слоями концентрата.
Восстановительную плавку титана ведут внепечным способом. Вначале на дно реактора загружают и зажигают запальную часть шихты, состоящую из железной руды, алюминия, ферросилиция, извести.
|
|
На образующийся расплав порциями подают основную часть шихты. По завершении процесса в реактор вводят смесь железной руды, алюминиевого порошка и извести (железотермитный осадитель). При этом образующиеся по реакции
Fe2О3 + 2А1 + СаО → 2Fe + А12О3 + СаО
капли железа, опускаясь в жидком шлаке, коалесцируют с более лёгкими каплями сплава, тем самым облегчая их переход в формирующийся слиток. После выдержки продуктов в расплавленном состоянии для достижения полноты их расслаивания металл сливают в ёмкость с находящимися в ней нагретыми до 100 – 150 °С отходами титановых сплавов для получения ферротитана заданного состава. Шлак, оставшийся в реакторе, сливают в изложницу или используют для довосстановления содержащегося в нём оксида титана (IV).
В получаемом ферротитане содержится 26 – 35 % Ti. Отношение содержаний алюминия и кремния к содержанию титана в сплаве составляет: Al:Ti = 0,07 – 0,4; Si:Ti = 0,012 – 0,28. Шлак восстановительной плавки ферротитана содержит 12 – 16 % ТiО2.
Ферротитан является одним из немногих сплавов, получаемых алюминотермическим способом, в структуре себестоимости которого наибольший удельный вес имеет стоимость восстановителя. В связи с этим в промышленности нашёл применение электропечной способ получения ферротитана, позволяющий уменьшить количество применяемой железной руды (или вообще исключить её из состава основной части шихты), и, следовательно, снизить расход алюминия на её восстановление.
Электропечной процесс начинают с получения на дне реактора жидкой ванны. Для этого в электропечи плавят частицы железа, используют расплав от предыдущей восстановительной плавки или зажигают металлотермическую смесь, состав которой идентичен описанному выше железотермитному осадителю. Затем на поверхности жидкой ванны расплавляют рудную часть шихты, состоящую из ильменитового концентрата и извести, после чего электроды поднимают из расплава и, дозировано загружая основную часть шихты на поверхность расплава, проводят восстановительную плавку. В завершающей стадии процесса для достижения полноты расслаивания металла и шлака используют железотермитный осадитель и выдерживают шлак в электропечи в расплавленном состоянии.
Ферровольфрам
Для получения ферровольфрама алюминотермическим способом используют шеелитовый концентрат с содержанием WO3 не менее 55 %; основным минералом в этом концентрате является шеелит CaWO4.
В состав металлотермической шихты входят также оксиды железа (железная окалина) и частицы железа (отходы гвоздильного производства – «железная обсечка»). Вследствие малого размера частиц шеелитового концентрата (менее 0,05 мм) при проведении восстановительной плавки из реактора может уноситься до 10 % концентрата в виде пыли. С целью уменьшения потерь вольфрама с пылью шихтовые материалы, содержащие 1,5 – 2,6 % влаги, перед плавкой брикетируют и высушивают.
Ферровольфрам получают электропечным способом, так как тепловой эффект протекающих реакций недостаточен для обеспечения полноты расслаивания металла и шлака. Восстановительную плавку проводят в реакторе с угольной футеровкой. Вначале зажигают часть шихты на дне реактора, затем на образующийся расплав дозировано подают остальное её количество. В ходе протекания металлотермического процесса также переплавляют металлические отходы от предыдущих восстановительных плавок, содержащие вольфрам.
После окончания восстановительного процесса со стенок реактора удаляют образовавшиеся настыли (закристаллизовавшийся и неслившийся металл), а на поверхность жидкого шлака небольшими порциями загружают алюминиевый порошок для довосстановления соединений вольфрама.
Слиток сплава неоднороден по составу. Слой сплава с повышенным содержанием таких элементов, как молибден (6 – 10 %), кремний (2,3 – 4,5 %), алюминий (5 – 8 %), отделяют от слитка и подвергают рафинированию с целью снижения содержания в нём кремния и алюминия. В зависимости от получаемой марки в ферровольфраме содержится: 71 – 86 % W; 1,7 – 6 % A1; 0,3 – 7 % Мо.
Грейнал
Одним из комплексных сплавов, применение которого позволяет повысить эффективность легирования стали, является грейнал. В этом сплаве содержится: ≥ 10 % Ti; ≥ 1,5 % Zr; ≥ 1 % В; ≥15 % Аl; ≥ 6 % Si.
Исходными материалами для получения грейнала служат металлсодержащая смесь (ферробор, силикоцирконий, титановые отходы) и алюминотермическая шихта (железная руда, известь и алюминий).
Промышленные плавки грейнала проводят в футерованном реакторе методом металлотермического переплава. По этому способу измельченную металлсодержащую смесь нагревают и помещают на дно реактора. На неё загружают алюминотермическую шихту и сверху инициируют реакцию. Образующееся по реакции расплавленное железо растворяет легирующие элементы с образованием сплава. Слой расплавленного шлака над сплавом металлов предохраняет его от окисления.
При получении грейнала методом металлотермического переплава толщина получаемого слитка не должна превышать 100 мм, так как в противном случае наблюдается ликвация легирующих элементов, т.е. разделение металлов по слоям в соответствии с их плотностями. Увеличить массу слитка грейнала без ухудшения его качества можно за счёт увеличения поверхности расплава при проведении восстановительной плавки в наклоняющемся реакторе с последующим сливом из него металла и шлака.
Изложенные в данном разделе технические приёмы используют также при алюминотермическом получении других ферросплавов и лигатур.
Термитная сварка
Термитная сварка была первым, практически используемым металлотермическим процессом, предложенным Н. Н. Бекетовым.
Металлотермические реакции широко используют для сваривания металлов термитным способом. По этому способу нагрев свариваемых изделий осуществляется за счёт теплового эффекта, сопровождающего горение термитной смеси, состоящей из оксида железа Fe2О3 и алюминия или магния. Вместо оксида железа в состав термитной смеси могут входить оксиды других металлов.
Наибольшее распространение получил железоалюминиевый термит. Температура его возгорания составляет около 1300 °С. Образующиеся по реакции
3Fe3О4 + 8A1 → 9Fe + 4А12О3
железо и шлак нагреваются до 2400 °С. В ряде случаев в состав железного термита входят частицы железа, легирующие присадки и флюсы.
Термитную сварку проводят следующим образом. Соединяемые детали помещают в термитную смесь и изолируют огнеупорным материалом. Затем зажигают запальную смесь и осуществляют металлотермическую реакцию. Образующееся по реакции жидкое железо, сплавляясь с материалом свариваемых изделий, обеспечивает их прочное соединение. Сварку термитом, содержащим алюминий в качестве металла-восстановителя, применяют для соединения стальных и чугунных деталей: стыковки рельсов и труб, заварки трещин и наплавки поверхности при ремонте изделий.
Термит, в состав которого входит магний, используют для соединения телефонных и телеграфных проводов, а также жил кабелей. При этом из термитной смеси изготавливают цилиндрические шашки с осевым каналом для провода и выемкой с торца для запала. Подлежащие сварке концы проводов заводят в шашку и зажигают её. Жидкий металл, образующийся в результате протекания металлотермической реакции, контактирует с проводами и сваривает их. Термит на основе магния может быть использован также для сварки труб небольших диаметров.
Металлотермические смеси применяют и для высокотемпературной пайки изделий. Основными преимуществами этого метода являются высокая экономичность, простота исполнения, возможность производства работ при расположении швов в труднодоступных местах.
Дата добавления: 2019-02-26; просмотров: 213; Мы поможем в написании вашей работы! |
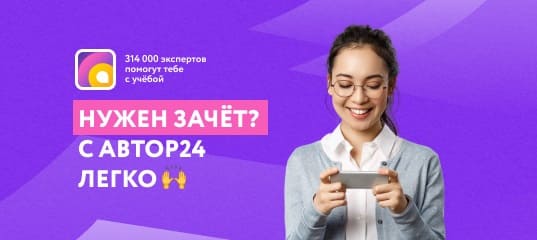
Мы поможем в написании ваших работ!