Термичность восстановления оксидов магнием
Оксид | – ΔΗ298, ккал/моль | Реакция | Термичность, ккал/г |
ВеО СеО2 Cs2O HfO2 La2O3 Li2O Sc2O3 NbO NbO2 Nb2O3 Pr2O3 Rb2O Sm2O3 Ta2O5 ThO2 TiO Ti2O3 TiO2 UO2 U3O8 UO3 VO V2O3 VO2 V2O5 Y2O3 ZrO2 | 147,3 233,0 82,0 271,5 457,0 142,3 407,0 116,0 193,5 463,0 437,0 83 430 499,0 293,0 135,0 375,5 219,0 255,0 845,0 291,0 106,0 300,0 176,0 382,6 441,0 258,5 | BeO + Mg=MgO +Be CeO2 + 2Mg=2MgO +Ce Cs2O + Mg=MgO + 2Cs HfO2 + 2Mg=MgO + Hf La2O3+ 3Mg=3MgO + 2La Li2O + Mg=MgO + 2Li Sc2O3+ 3Mg=MgO + 2Sc NbO + Mg=MgO + Nb NbO2 + 2Mg=2MgO + Nb Nb2O3 + 3Mg=3MgO + 2Nb Pr2O3 + 3Mg=3MgO + 2Pr Rb2O + Mg=MgO + 2Rb Sm2O3 + 3Mg=3MgO + 2Sm Ta2O5 + 5Mg=5MgO + 2Ta ThO2 + 2Mg=2MgO + Th TiO + Mg=MgO + Ti Ti2O3 + 3Mg=3MgO + 2Ti TiO2 + 2Mg=2MgO + Ti UO2 + 2Mg=2MgO + U U3O8 + 8Mg=8MgO + 3U UO3 + 3Mg=3MgO + U VO + Mg=MgO + V V2O3 + 3Mg=3MgO + 2V VO2 + 2Mg=2MgO + V V2O5 + 5Mg=5MgO + 2V Y2O3 + 3Mg=3MgO + 2Y ZrO2 + 2Mg=2MgO + Zr | –67 250 202 64 –63 31 118 210 545 –101 –12 290 5 393 –16 102 260 537 104 295 393 417 593 855 1100 –30 175 |
Металлотермические способы восстановления можно классифицировать по схеме, изображенной на рис. 5. Во внепечном процессе выделяющегося в результате реакции восстановления тепла достаточно для полного (и достаточно быстрого) протекания процесса, расплавления шлака и (или) восстанавливаемого металла. В печных процессах недостающее тепло подводится извне, чаще всего с помощью электронагрева.
Рис. 5. Классификация металлотермических процессов
Между печными и внепечными процессами нельзя провести чёткую границу, так как тепловой баланс определяется их масштабами. Увеличение масштаба плавки всегда ведёт к относительному уменьшению теплопотерь, росту tт.р. Другими факторами, влияющими на характер металлотермического восстановления, являются: состав восстановителя, применяемые добавки, характер получаемого продукта (чистый металл или сплав).
|
|
В тех случаях, когда восстановление проходит при достаточно низкой температуре (давление насыщенного пара компонентов реакции незначительно), реакцию можно осуществлять на воздухе и в открытых аппаратах. Восстановление химически прочных соединений наиболее полно протекает чаще всего при повышенной температуре (1000 °С и выше). При этой температуре, чтобы исключить испарение компонентов смеси, восстановление проводят в герметически закрытых стальных ретортах, заполненных инертным газом.
В настоящее время в технологии редких металлов используют следующие металлотермические процессы:
· кальциетермию: La, Ce, Pr, Nd из хлоридов, Th, V, Y, Sc, Gd, Tb, Dy, Ho, Er, Tm, Lu из фторидов;
· магниетермию: U, V из оксидов, Ti, Zr, Th, Та из хлоридов и U из фторида;
· натриетермию: Та, Nb, Zr из комплексных фторидов, Ti, Zr из хлоридов.
При восстановлении тугоплавких металлов в шихту иногда вводят специальные добавки, образующие с восстанавливаемым металлом сплавы с пониженной температурой плавления. Например, при восстановлении иттрия из YF3 кальцием в шихту вводят магний для образования Y – Mg-сплава, затем магний отгоняется в вакууме. Образование сплавов сопровождается уменьшением термодинамического потенциала системы. Так получают, например, ферротитан и феррованадий, сплавы Ni – Ti; Сu – Ti; Zr – Сr и др.
|
|
Большое значение для качества получаемого продукта имеет выбор исходного соединения для восстановления. При этом следует принимать во внимание, что некоторые оксиды металлов можно восстановить определёнными восстановителями только до промежуточной валентности (так, TiO2 алюминием восстанавливается до устойчивого низшего оксида TiO). При восстановлении хлоридов образуются сравнительно легкоплавкие шлаки, основная масса которых легко отделяется от корольков или губки восстановленного металла в самом реакторе. В некоторых случаях остатки исходных солей и восстановителя (относительно летучих) удаляются из восстановленной губки отгонкой в вакууме. Фториды как исходные материалы для восстановления более дороги, чем хлориды, но менее гигроскопичны.
Некоторые металлотермические процессы проводят в вакууме, что уменьшает возможность протекания в газовой среде вторичной реакции (окисления, образования нитридов и т.п.), снижающей выход и ухудшающей качество восстанавливаемого металла. Однако подобного эффекта можно достичь и без вакуума – при проведении реакции в среде инертного газа.
|
|
Основной особенностью вакуумных металлургических процессов являются высокая скорость и меньшая температура реакции. Как уже указывалось, проведение процесса в вакууме даёт возможность осуществить на практике реакции восстановления, характеризующиеся малым, а подчас и положительным значением ΔG° при условии выведения из сферы реакции (отгонки) образующегося продукта (восстановленного металла или соединения металла-восстановителя). При этом очевидно, что применяемый вакуумный насос должен обеспечивать в аппарате восстановления остаточное давление, меньшее (или, по крайней мере, равное), чем равновесное давление отгоняемого продукта. В противном случае скорость процесса удаления паров из сферы реакции определяется диффузией в остаточном газе, что может привести к скоплению и повышению парциального давления отгоняемых продуктов и остановке реакции восстановления.
Итак, при атмосферном давлении достаточно высокая скорость отгонки восстанавливаемого металла достигается при pMe′ ≥ 1 ат, а в вакууме – при pMe′ ≥ pо.г (где pо.г – остаточное давление газа). Поскольку в вакууме pо.г << 1 ат, a pMe′ экспоненциально возрастает с температурой (уравнение Клаузиуса–Клапейрона), ясно, что достаточная скорость отгонки обеспечивается при более низкой температуре. Обычно pо.г = 10–3 – 10–5 ат, поэтому восстановление проводится при температуре, обеспечивающей рме' по крайней мере на порядок выше pо.г.
|
|
Переход Me'(ж) → Me'(пар) по причинам кинетического характера (ускорение процесса вследствие ускорения отгонки в вакууме) не может не сказаться на термодинамике процесса. Рассмотрим влияние вакуумирования системы на термодинамику процесса восстановления металла Me' из твёрдого окисла Ме'О(тв) с помощью другого твёрдого металла-восстановителя Ме"(тв) при постоянной температуре. При атмосферном давлении:
Ме'О (тв) + Me" (тв) → Me' (ж) + Ме"О (тв).
Реакция характеризуется величиной ΔG°атм. Восстановление в вакууме:
Ме'О (тв) + Me" (тв) → Me' (г) + Me"O (тв) (ΔGвак).
Вычитая одно уравнение из другого, найдём, что изменение энергии Гиббса состояния системы ΔG, соответствующее переходу металла из жидкого состояния в пар, равно ΔGвак – ΔG°атм = ΔG.
Известно, что энергия Гиббса перехода 1 г-атома металла из жидкого состояния в пар при рпар = 1 ат равна нулю, а работа перехода 1 г-атома пара от давления 1 ат к рМе равна:
– RTlnpМе = ΔG
Отсюда
– RTlnpМе = ΔGвак – ΔG°атм
или
ΔGвак = ΔG°атм + 2,3RTlnpМе
Примем ро.г = рМе, тогда
ΔGвак = ΔG°атм + 2,3RTlnpо.г.
Из полученного выражения видно, что энергия Гиббса ΔG° процесса восстановления уменьшается на величину 2,3RTlnpо.г., поскольку po.г << 1 и lnp – отрицательная величина. Величина этого сдвига возрастает с повышением температуры и степени разрежения в системе. Приведём зависимость разности ΔGвак – ΔG°атм от разрежения при Т = 1000 К:
po.г, aт | 10–1 | 10–3 | 10–5 |
ΔGвак – ΔG°атм, ккал | 4,6 | 13,8 | 23,0 |
Абсолютные значения ΔG°восст. оксидов лежат обычно в пределах 30–150 ккал/моль. Отсюда ясна важная роль вакуума как термодинамического фактора. Правда, для практических расчётов целесообразнее принимать рМе ≈ 10 ро.г, что несколько снижает термодинамический эффект вакуумирования.
Продуктом реакции может быть сложное соединение (шлак) состава nMe′O2•mMe"O2 (например, при восстановлении СаО алюминием образуется 3СаО·А12О3). Очевидно, вхождение образующегося оксида в соединение (шлак) снижает его активность, что благоприятно сказывается на протекании реакции восстановления. Однако иногда шлаки могут закрывать поверхность реагирующих веществ, что сильно замедляет реакцию.
Расчёт ΔG°восст. практически возможен лишь в том случае, если компоненты реакции взаимно нерастворимы. При этом условии можно принять значения активности всех конденсированных фаз равными единице (или принять давление их насыщенного пара равным давлению насыщенного пара над чистыми веществами). В случае взаимной растворимости или образования соединений активности конденсированных фаз не равны 1, а данные, учитывающие эти отклонения, для большинства систем отсутствуют. Поэтому термодинамический анализ без учёта явлений, возникающих в реальных системах, даёт лишь приблизительное представление о протекающих процессах. Однако даже приблизительная, полуколичественная оценка часто позволяет сделать определённые выводы о наилучших условиях восстановления или о наиболее перспективном направлении поиска.
МЕТАЛЛЫ-ВОССТАНОВИТЕЛИ
Наиболее широкое применение в качестве восстановителей при проведении металлотермических процессов нашли следующие химически активные металлы: алюминий, магний, кальций, натрий.
Для целого ряда процессов восстановления применяют условно называемый металлический кремний. Однако в технологии редких металлов он практически не применяются.
Способы получения
Алюминий
В промышленности алюминий получают электролизом глинозёма Al2О3, растворённого в расплавленном криолите Na3AlF6 при температуре около 950 °С. Рабочий объём электролизной ванны заполняется расплавленным электролитом, состоящим из 6–8 % глинозёма и 92–94 % криолита (обычно с добавками AlF3 и смеси фторидов калия и магния). Катодом служит подина ванны, анодом – погружённые в электролит угольные электроды. При прохождении тока через электролит на катоде выделяется расплавленный алюминий, который накапливается на подине электролизёра. На аноде выделяется кислород, образующий при взаимодействии с угольным анодом СО и СО2.
Из ванны-электролизёра алюминий извлекают с помощью вакуум-ковша. Расплавленный алюминий разливают в формы.
К глинозёму – основному расходуемому материалу – предъявляются высокие требования по чистоте и размерам частиц. Присутствие в нём оксидов более электроположительных элементов, чем алюминий, ведёт к загрязнению получаемого металла.
Разрабатываются и другие способы получения алюминия. С целью усовершенствования электролитического процесса исследована возможность применения в качестве расходуемого материала хлорида или сульфида алюминия, использования нерасходуемых анодов из сплавов Ni-Fe, Ni-ферриты и др. Оценены перспективы получения алюминия посредством восстановления глинозёма углеродом в доменных печах или метаном в плазменных установках, а также хлорида алюминия марганцем. Изучены реакции диспропорционирования А12S3 и А1Сl3 до металла. Однако промышленное освоение рассмотренных процессов сдерживается рядом нерешённых технологических и аппаратурных проблем, а также отсутствием экономических преимуществ перед существующим способом получения алюминия.
Магний
Основными способами производства металлического магния являются электролитическое и силикотермическое восстановление его соединений.
Электролитический метод получения магния эффективен при крупном масштабе производства, что обусловлено достаточно сложной подготовкой электролита, высокими требованиями к управлению работой электролизёров, относительно большими затратами на утилизацию продуктов электролиза (шлама, хлорсодержащих газов и др.). Экономичное решение этих задач доступно лишь мощному предприятию.
Магний чаще всего получают электролизом МgСl2, находящегося в расплаве хлоридов KCl и NaCl. В качестве исходного сырья применяют обезвоженный карналлит KCl∙MgCl2. Для получения магния используют и шлак титанового производства (процесса восстановления TiСl4 магнием), содержащий в основном MgCl2.
В случае применения карналлита электролит содержит 10 % MgCl2, 75–80 % KCl, 8–13 % NaCl. Состав электролита при использовании шлака, образующегося при получении титановой губки, следующий: 10 % MgCl2, 45–50 % NaCl, 35–40 % KCl. В электролит добавляют также 2–4 % СаСl2, 0,2–0,3 % CaF2.
При электролизе на катодах (сталь) образуется жидкий магний, а на анодах (графит) – газообразный хлор. Плотность расплавленного магния меньше плотности электролита, поэтому капли металла и пузырьки хлора движутся в одном направлении (всплывают). Для устранения их взаимодействия применяли диафрагмы (перегородки), помещённые между катодами и анодами. Создание нового типа магниевого электролизёра – бездиафрагменного позволило резко увеличить единичную мощность аппарата, снизить энергетические затраты, радикально улучшить условия труда и заложить технологические основы для создания непрерывного и автоматизированного процесса.
Силикотермический способ получения магния рационален для маломасштабного производства. Он требует меньших энергетических затрат и капитальных вложений на охрану природы по сравнению с электролитическим процессом. Наиболее распространённым вариантом силикотермического восстановления магния является процесс Magneterm. Исходными веществами для проведения силикотермического процесса являются доломит MgCa(CO3)2, боксит (используемый в качестве флюса) и ферросилиций с содержанием кремния не менее 75 %.
Процесс осуществляют в футерованном графитом аппарате в вакууме при температуре свыше 1600 °С. Шихту нагревают посредством пропускания через неё электрического тока. Образующиеся по реакции 2MgO + Si = 2Mg + SiO2 пары магния поступают в конденсатор, откуда жидкий металл стекает в водоохлаждаемый тигель.
Кальций
В промышленности металлический кальций получают электролизом расплава хлоридов или алюминотермическим восстановлением оксида кальция. Процесс электролиза ведут с применением жидкого катода, в качестве которого используют сплав кальция с медью. Получаемый сплав характеризуется низкой температурой плавления. Его плотность превышает плотность расплавленного электролита, вследствие чего он находится на дне ванны. При температурах дистилляции медь обладает малой упругостью паров и не загрязняет кальций, который отгоняют.
Электролизёр для получения медно-кальциевого сплава представляет собой чугунную ванну, замурованную в кладку из огнеупорного кирпича и соединённую с отрицательным полюсом источника тока. На дне ванны расплавляют электролитную медь или обеднённый медно-кальциевый сплав (катод). В качестве анодов служат пакеты из графитовых блоков.
Электролит содержит 80–85 % СаСl2 и 15–20 % KCl. В процессе электролиза содержание кальция в сплаве повышается до 62–65 %. Хлор, образующийся на анодах, выводится из ванны. Процесс ведут при 680–720 °С: ниже 650 °С электролиз протекает с малым выходом по току, выше 750 °С – резко возрастает растворимость кальция в электролите.
Жидкий сплав кальция с медью извлекают из ванны вакуум-ковшом. Дистилляцию кальция осуществляют в вакууме при температуре около 1200 °С. В процессе дистилляции содержание кальция в сплаве снижается до 30–35 %. По завершении процесса оставшийся сплав направляют на электролиз для использования в качестве жидкого катода. Пары кальция конденсируются в верхней части реторты при 300–700 °С; содержание активного кальция в дистиллированном металле составляет не менее 98 %.
Металлический кальций получают также восстановлением оксида кальция алюминием. Исходными веществами для получения кальция алюминотермическим способом служат обожжённый известняк и алюминиевый порошок, взятые в соотношении СаО:Аl = 3,5:1. Компоненты шихты тщательно перемешивают и подвергают сухому брикетированию. Брикеты укладывают в реторту из высоколегированной хромоникелевой стали. После вакуумирования реторту устанавливают в печь.
Восстановление оксида кальция протекает при 1170–1200 °С в соответствии с уравнением 6СаО + 2Аl = 3СаО∙Аl2О3 + 3Са. В качестве промежуточного продукта может образоваться алюминид кальция состава СаАl3.
Кристаллы кальция, образующиеся в конденсаторе, характеризуются высокой плотностью и прочностью, что делает возможным их прессование. Чистота кальция, получаемого алюминотермическим способом, составляет 98–99 %.
Натрий
Основным промышленным способом получения металлического натрия является электролиз расплава поваренной соли NaCl, содержащего добавки KCl, NaF, СаСl2 и некоторых других компонентов, которые снижают температуру плавления электролита до 575–585 °С. Электролиз поваренной соли без использования добавок привёл бы к большим потерям металла в газовую фазу из-за близости температур кипения натрия и плавления хлорида натрия.
Процесс осуществляют в электролизёрах с катодами, выполненными из железа или меди; аноды изготовлены из графита. Одновременно с натрием в процессе электролиза получают хлор.
Металлический натрий получают также посредством электролиза расплавленного едкого натра NaOH, который значительно дороже NaCl, однако электролитически разлагается при более низкой температуре (320–330 °С), чем поваренная соль.
Кремний
Металлический кремний получают восстановлением оксида SiO2 углеродом (коксом) в электрических или дуговых печах при температуре 1800 °С. При этом чистота получаемого кремния составляет 95–98 %. Чистота технического продукта повышается до 99,9 % специальной кислотной обработкой.
В небольших масштабах кремний получают электролизом расплавов Na2SiF6 или K2SiF6 с добавками хлоридов щелочных металлов, восстановлением водородом чистого SiCl4 при 1200–1300 °С, разложением SiH4 при температуре около 1000 °С.
Дата добавления: 2019-02-26; просмотров: 387; Мы поможем в написании вашей работы! |
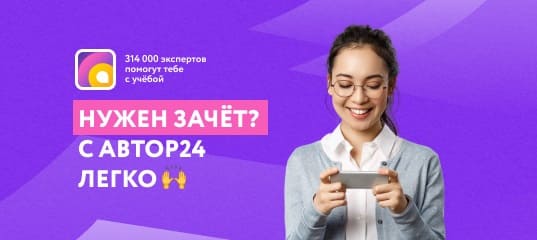
Мы поможем в написании ваших работ!