Термодинамические характеристики процесса кальциетермического восстановления при различных температурах
Реакция | Т/д характеристика, ккал | Температура, К | ||||
298 | 500 | 800 | 1000 | 1100 | ||
(I) | – ΔHºT – ΔGºT | 132,200 131,394 | 131,869 130,892 | 132,259 130,381 | 131,372 129,907 | 132,463 129,639 |
(II) | – ΔHºT – ΔGºT | 51,450 49,826 | 51,516 48,697 | 51,594 47,008 | 51,447 45,977 | 51,391 45,317 |
(III) | – ΔHºT – ΔGºT | 80,750 81,567 | 80,353 82,195 | 80,665 83,372 | 80,895 84,030 | 81,072 84,322 |
(IV) | – ΔHºT – ΔGºT | 22,250 24,613 | 20,581 26,669 | 18,268 30,944 | 16,445 34,320 | 15,462 36,151 |
(V) | – ΔHºT – ΔGºT | 73,700 74,440 | 72,097 75,366 | 69,862 77,953 | 67,922 80,197 | 66,852 81,468 |
(VI) | – ΔHºT – ΔGºT | 58,500 56,954 | 59,772 55,526 | 62,397 52,428 | 64,450 49,710 | 65,611 48,171 |
Величина теплового эффекта свидетельствует о значительной экзотермичности реакций, а значения энергии Гиббса – о возможности протекания их во всём указанном температурном интервале.
Для получения слитка циркония необходим перегрев продуктов реакции на 200 – 250 °С выше температуры плавления металлического циркония (2125 К). В табл. 9 приведено количество тепла, необходимое для нагрева продуктов реакций (I), (III), (VI) от 298 до 2400 К.
Таблица 9
Тепло, необходимое для расплавления циркония
Реакция | Количество кальция | ![]() |
(I) | Стехиометрическое 5 %-й избыток 10 %-й избыток 15 %-й избыток 20 %-й избыток | 134,714 139,985 145,256 150,527 155,798 |
(III) | Стехиометрическое | 106,516 |
(VI) | Стехиометрическое | 78,319 |
Из сопоставления данных табл. 8 и 9 можно заключить, что полное расплавление и перегрев продуктов на 200 – 250 °С (для хорошего разделения металла и шлака) возможны лишь по реакции (I) в условиях избытка кальция менее 5 %. Однако практически следует учитывать тепловые потери, а также необходимость большого избытка кальция для полноты восстановления. Следовательно, для получения расплава Zr внешний подвод тепла неизбежен.
|
|
В Канаде осуществлен процесс получения сплава циркалой (наиболее распространённый за рубежом в прошлом веке сплав циркалой-2 содержит 1,5 % Sn, 0,1 % Fe, 0,1 % Cr, 0,05 % Ni) при восстановлении ZrF4 кальцием. Процесс протекает в бомбе, куда загружают смесь металлического кальция и фторида циркония. Для обеспечения в конце процесса температуры, достаточной для расплавления металла, производят предварительный нагрев до 850 °С. Реакцию инициируют пропусканием тока через танталовую проволоку, погружённую в шихту. С целью получения сплава в шихту предварительно вводят легирующие добавки. В описанных условиях металл расплавляется, в результате чего компактный слиток сплава получается в аппарате восстановления.
Восстановление хлоридов
Схема аппарата для возгонки тетрахлорида Zr представлена на рис. 11. Реторту из нержавеющей стали, в которой происходит процесс очистки, помещают в шахтную электрическую печь. В печи имеются три независимые зоны нагрева: зона сублимации – 16, зона конденсации – 13 и зона уплотнения затвора – 12. Крышка реторты установлена на жёлобе, заполненном сплавом свинец–сурьма (температура плавления 247 °С) – 11. Сплав можно расплавить при включении верхней зоны нагрева или заморозить (охлаждением воздухом или водой). Расплавленный Рb–Sb-затвор создаёт возможность сброса избыточного давления в реторте. Нормальная рабочая температура крышки и верхней зоны печи не выше 650 °С, а средней и нижней – не выше 900 °С.
|
|
На дно реторты устанавливают контейнеры, изготовленные из сплава инконель (состав сплава инконель X: 72,7 % Ni, 15 % Сr, 7 % Fe, 1 % Nb, 2,5 % Ti, 0,7 % Al, 0,7 % Мn, 0,4 % Si, 0,05 % С). Контейнер представляет собой «этажерку», на которую загружают неочищенный хлорид циркония. Реторту закрывают крышкой, которую погружают в предварительно расплавленный сплав РЬ–Sb. Затем сплав замораживают, реторту эвакуируют, дважды заполняют водородом, нижнюю зону нагревают до 200 ºС, при этом удаляется остаточный SiCl4, а FeCl3 восстанавливается до малолетучего FеСl2. После этого свинцовый затвор расплавляют, температуру нижней зоны повышают до 450 °С, возгоняя ZrCl4. Температуру крышки и стенок поддерживают выше температуры возгонки (чтобы избежать конденсации на них ZrCl4). Тетрахлорид циркония осаждается только на охлаждаемых водой змеевиках – 5, 7. Необходимо обеспечить равенство скорости возгонки и осаждения. По окончании процесса установку охлаждают до комнатной температуры. Аппарат размером 700 мм в диаметре и 1750 мм высотой позволяет очистить за один раз до 200 кг ZrCl4. Цикл длится до 30 ч. Хлорид циркония на змеевике отличается большой плотностью. Большая часть примесей остается на «этажерке».
|
|
Рис. 11. Схема печи рафинирования ZrCl4:
1 – неочищенный хлорид; 2 – место для неочищенного хлорида; 3 – уровень пола; 4 – плотный хлорид; 5 – наружный змеевик; 6 – выхлопной клапан; 7 – внутренний змеевик; 8 – трубка для откачки; 9 – газовый клапан; 10 – нагревательный элемент верхней плиты; 11 – свинцовый затвор; 12 – нагревательный элемент свинцового затвора; 13 – нагревательный элемент средней зоны печи; 14 – стержень для подъёма рафинированного резервуара; 15 – рафинировочный резервуар; 16 – нагревательный элемент нижней зоны печи; 17 – пробки системы охлаждения; 18 – нагревательный элемент нижней зоны печи
|
|
Затем крышку со змеевиком переносят в аппарат для восстановления (рис. 12), по конструкции аналогичный аппарату для очистки. На дне этого аппарата устанавливают никелевый тигель 19 с ~ 20 %-м избытком магния против теоретически необходимого. Над тиглем размещаются экраны 17, препятствующие передаче тепла излучением из одной зоны в другую, а также предотвращающие попадание на поверхность магния случайных брызг сплава Pb–Sb из затвора 12.
Реакцию восстановления хлоридов циркония и гафния можно представить в общем виде:
MeCl4(г) + 2Mg(ж) → Me(тв) + 2MgCl2(ж).
При 827 °С величины ΔH° и ΔG° для реакции восстановления циркония равны –79,3 и –48,0 ккал, для гафния –55,4 и –25,2 ккал соответственно. Реакция восстановления хлорида гафния менее экзотермична, при его восстановлении применяют больший избыток магния (40–65 % для восстановления HfСl4, 20 – 25 % для ZrCl4).
Верхний предел температуры процесса восстановления определяется образованием Fe–Zr-эвтектики с температурой плавления 940 °С. Кроме того, перегрев ведёт к повышению давления пара магния и образованию мелкого пирофорного порошка циркония вследствие протекания реакции в газовой фазе. Поэтому нижняя зона нагрева сосуда восстановления обеспечивает температуру около 825 °С, что несколько выше температуры плавления MgCl2. Сосуд для восстановления закрывают крышкой аппарата очистки со змеевиком с ZrCl4 и после расплавления и замораживания затвора эвакуируют его и заполняют аргоном. Магний в тигле нагревают до 825 °С, а верхнюю зону, где расположена груша ZrCl4, – до 450 – 500 °С, в результате хлорид циркония постепенно испаряется и его пары контактируют с расплавом магния. Скорость процесса можно регулировать скоростью испарения хлорида. Слишком высокая скорость испарения приводит к перегреву реактора. Расплавленный магний находится на поверхности расплава MgCl2, а образующиеся кристаллы циркония опускаются на дно тигля. Стенки и крышка реактора во время процесса восстановления имеют температуру не ниже 450 °С.
Рис. 12. Схема восстановительной печи:
1 – цирконий; 2 – хлорид магния; 3 – магний; 4 – уровень пола; 5 – плотный хлорид; 6 – наружный змеевик; 7 – выхлопной клапан; 8 – внутренний змеевик; 9 – трубка для откачки; 10 – газовый клапан; 11 – нагревательный элемент верхней плиты; 12 – свинцовый затвор; 13 – нагревательный элемент свинцового затвора; 14 – нагревательный элемент средней зоны печи; 15 – реторта; 16 – резервуар для продукта, конденсирующегося из паровой фазы; 17 – экран; 18 – стержень для подъёма рафинированного резервуара; 19 – тигель для восстановления; 20 – пробки системы охлаждения; 21 – нагревательный элемент нижней зоны печи
Процесс возгонки ZrCl4 можно регулировать подачей в змеевик холодного воздуха. Процесс восстановления длится 4 – 5 ч. После этого температура нижней зоны поддерживается в течение одного часа около 920 °С для укрупнения кристаллов циркония. При этом необходим строгий контроль за температурой, так как при 940 °С губка загрязняется железом в местах соприкосновения со стенками тигля вследствие образования эвтектики Fe – Zr. При необходимости температуру снижают, вводя в реторту холодный инертный газ. По окончании восстановления реторту охлаждают, крышку снимают и тигель, содержащий циркониевую губку, MgCl2 и магний, удаляют из реторты.
Возможно совмещение процессов возгонки и восстановления в одном аппарате (рис. 13). При этом если полный цикл раздельных операций очистки и восстановления продолжается 64 ч, то по совмещённому варианту продолжительность цикла 44 ч.
Следующей стадией процесса является отделение губки от MgCl2 и избытка магния. При гидрометаллургическом методе обработки губки металл содержит большое количество кислорода. В настоящее время используют метод вакуумтермической очистки в аппарате, конструкция которого в основном подобна аппарату, представленному на рис. 9. В верхней части реторты помещают перевёрнутый тигель из аппарата восстановления. Затем при температуре выше 712 °С выплавляют основную массу MgCl2, который стекает в резервуар для солей, расположенный в нижней части реактора. Дальнейшее повышение температуры верхней части реактора выше 900 °С обусловливает отгонку магния и остатков MgCl2 в вакууме. Оставшаяся губка содержит обычно не более 0,02 % Mg и 0,04 %. Сl.
Гафниевая губка более пирофорна, чем циркониевая. Прямое извлечение гафния при очистке технического хлорида составляет ~ 94 %, при восстановлении 97 %, при дистилляции – 96 %.
Рис. 13. Схема комбинированного аппарата для очистки и восстановления:
1 – цирконий; 2 – хлорид магния; 3 – магний; 4 – уровень пола; 5 – неочищенный хлорид Zr; 6 – рафинировочный резервуар; 7 – плотный хлорид; 8 – плавающая крышка; 9 – охлаждающие змеевики; 10 – газовый клапан; 11 – трубка для откачки; 12 – выхлопной клапан; 13 – нагревательный элемент верхней плиты; 14 – свинцовый затвор; 15 – нагревательный элемент свинцового затвора; 16 – нагревательный элемент средней зоны; 17 – место для неочищенного хлорида Zr; 18 – реторта; 19 – экран для восстановления; 20 – стержень для подъёма тигля; 21 – тигель для восстановления; 22 – пробки системы охлаждения; 23 – нагревательный элемент нижней зоны
Тетрахлорид циркония может быть восстановлен натрием (табл. 10). С термодинамической точки зрения процесс восстановления тетрахлоридов натрием более благоприятен, чем магнием. Недостатки и преимущества натриетермического метода имеют тот же характер, что и при восстановлении TiCl4.
Таблица 10
Дата добавления: 2019-02-26; просмотров: 269; Мы поможем в написании вашей работы! |
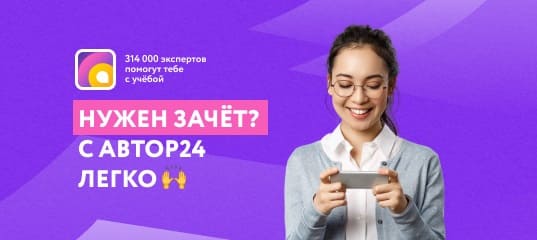
Мы поможем в написании ваших работ!