Рафинирование металлов-восстановителей
Содержание примесей в металлах, получаемых методами металлотермии, определяется их содержанием в исходных материалах, в том числе, в восстановителях. В связи с этим требования, предъявляемые к чистоте металла-восстановителя, должны соотноситься с количеством примесей в восстанавливаемом соединении, а также с ограничениями содержания примесей в получаемом металле. Например, в соответствии с нормативами, разработанными на алюминиевый порошок, используемый при восстановлении металлов из рудных концентратов, в зависимости от марки алюминиевого порошка содержание основного компонента в нём может изменяться от 83 до 96,9 %, а суммарное содержание примесей составлять от 3 до 14%.
Значительно более высокие требования к металлам-восстановителям по содержанию примесей предъявляют при получении продуктов из индивидуальных соединений, что делает необходимым их рафинирование. Рассмотрим основные технологические приёмы, применяемые для рафинирования металлов-восстановителей.
Распространённым способом очистки кальция, магния и натрия является вакуумная дистилляция. Этот метод основан на различии давления паров рафинируемого металла и примесей. Он пригоден как для отгонки из металла более летучих примесей, так и для возгонки самого металла. В последнем случае в остатке будут концентрироваться менее летучие примеси.
В результате вакуумной дистилляции получают кальций с содержанием не менее 99,5 % Са, магний с содержанием 99,99 % Mg. Чистота металлов может быть повышена, если их подвергнуть повторной дистилляции
|
|
Для получения особо чистого алюминия применяют дистилляцию через субфторид алюминия. Метод основан на протекании обратимой реакции:
АlF3 + 2Аl 3AlF.
Образующийся по реакции газообразный субфторид алюминия переносится в конденсатор, где распадается с образованием чистого алюминия. В оптимальных условиях этим способом может быть получен металл с содержанием 99,999–99,9999 % Al.
К другой группе процессов относится электролитическое рафинирование алюминия и магния. Сущность этого метода заключается в анодном растворении алюминия или магния из сплавов, содержащих исходные металлы, и выделении чистых металлов на катоде. При этом более электроположительные элементы накапливаются в анодном сплаве, не растворяясь в электролите, а менее электроположительные переходят в электролит, не разряжаясь на катоде.
В результате электролитического рафинирования могут быть получены алюминий с содержанием 99,995–99,999 % Al и магний, по чистоте не уступающий дистиллированному металлу.
Для рафинирования магния широко применяют его переплав с флюсами, содержащими хлорид магния. В состав флюсов входят также хлориды и фториды щелочных и щёлочноземельных металлов. Хлорид магния взаимодействует с такими примесями, как натрий и калий, переводя их в солевой расплав, который наряду с этим адсорбирует из металла неметаллические примеси.
|
|
С целью очистки магния от металлических примесей и кремния применяют контактирование расплавленного металла с хлоридами титана и циркония или с такими металлами, как марганец, титан, цирконий. В результате протекания реакций в системе образуются интерметаллиды активных металлов и примесей, которые малорастворимы в магнии и выводятся из него.
Разработаны и другие способы рафинирования рассматриваемых металлов. Например, жидкий алюминий продувают хлором; при этом образующиеся газообразные хлориды обволакивают и выносят на поверхность металла частицы неметаллических примесей. Для глубокой очистки металлов применяют метод зонной кристаллизации, основанный на различии в распределении примесей между жидкой и твёрдой фазами металла, и др.
Измельчение
С целью улучшения контакта между компонентами шихты, повышения однородности её состава металлы-восстановители используют в металлотермических процессах в измельчённом виде. Уменьшение размера частиц металла-восстановителя способствует повышению плотности шихты и, следовательно, позволяет увеличить количество металлотермической смеси, загружаемой в аппарат.
|
|
Вместе с тем уменьшение размера частиц активных металлов приводит к увеличению степени их поверхностного окисления, имеющего место в процессе измельчения, при хранении и шихтовке. Оксидная плёнка на поверхности металла-восстановителя обусловливает снижение скорости протекания металлотермической реакции и способствует увеличению степени загрязнения получаемого металла кислородом. При этом, чем более химически активен металл-восстановитель по отношению к кислороду, тем больше критический размер частиц, до которого его целесообразно измельчать. Поэтому, если алюминий обычно используют в металлотермических процессах в виде порошка, то магний или кальций, как правило, в виде гранул или стружки.
В практике металлотермических процессов применяют различные способы измельчения химически активных металлов. Рассмотрим наиболее характерные из них.
Методы измельчения металлов-восстановителей можно разделить на две основные группы: механическое измельчение и диспергирование расплавов. Диспергирование расплавленных металлов используют для получения их порошков и гранул.
|
|
Широкое распространение получил способ распыления расплава металлов газом с помощью форсунок. По этому способу расплавленный металл под давлением подают в распыливающую форсунку. На выходе из форсунки струя металла разбивается на мелкие капли потоком воздуха или инертного газа. Капли быстро кристаллизуются и охлаждаются. Полученный порошок пневмотранспортом подаётся на рассеивание по фракциям. Размер образующихся частиц металла зависит от вязкости, поверхностного натяжения расплава и энергии газового потока. С целью уменьшения окисления металла в случае проведения процесса диспергирования на воздухе на поверхность расплава загружают флюсы, состоящие из смеси KCl, NaCl, CaF2.
Описанный способ является типичным в производстве порошка алюминия. Согласно техническим условиям на алюминиевый порошок, используемый при получении ферросплавов, его гранулометрический состав должен удовлетворять следующим требованиям:
Фракция, мм | 0,1 | 0,1–1,0 | 1,0–3,0 |
Содержание, % | |||
I сорт | 20 | 70 | 15 |
II сорт | 25 | 65 | 20 |
Процесс распыления расплава осуществляют и под действием центробежных сил при сливе струи металла во вращающийся с большой скоростью перфорированный стакан или на дисковое устройство. На размер образующихся капель влияют скорость вращения и размер отверстий в стакане. Наиболее чистые порошки алюминия и магния получают в результате центробежного распыления металла из оплавляемых вращающихся цилиндрических заготовок в инертной среде или высоком вакууме.
Разработан способ получения гранул магния посредством центробежного дробления струи расплава с введением в него солевой добавки для исключения возгорания металла. Для достижения необходимого качества гранулированного магния требуется точная дозировка металла и солевой добавки. Чрезмерное уменьшение солевой составляющей приводит к появлению недопустимого количества частиц игловидной формы, которые образуются из капель металла, не защищённых солевой оболочкой. При транспортировке гранул с помощью пневмонасоса происходит истирание хрупкой солевой оболочки, что делает возможным частичное отделение её от магния.
Помимо магния, в виде гранул получают и кальций. Размеры применяемых в металлотермических процессах гранул кальция составляют 3–4 мм.
Рассмотрим далее механические способы измельчения твёрдых металлов-восстановителей.
Магний и кальций достаточно хорошо обрабатываются резанием. Поэтому при проведении ряда металлотермических процессов они используются в виде стружки различных типов и размеров. Стружку металлов-восстановителей готовят на токарных и фрезерных станках; во избежание её окисления операцию осуществляют в инертной атмосфере. Натрий является пластичным металлом, в связи с чем его нарезают на кусочки специальными ножницами. Для измельчения магния и кальция применяют также операции дробления и помола в мельницах.
Известен следующий способ измельчения магния. Магний, полученный после дистилляции, дробят молотом. Полученные куски разрезают на гильотинных ножницах и измельчают в мельницах. Измельчённый продукт пропускают через сито для отсева пыли. Ситовый анализ частиц магния следующий:
Размер отверстия сита, мм | 2 | 0,84 | 0,59 | 0,42 | 0,25 |
Количество продукта, прошедшего через сито, % | 90–99 | 25–55 | 10–35 | 2–15 | 0–1 |
Такой магниевый порошок имеет насыпную массу около 0,22 г/см3, а после утряски – 0,25 г/см3.
Измельчение кальция осуществляют во вращающейся молотковой дробилке. Механическими способами получают и мелкодисперсные порошки магния и кальция. Например, магний размером частиц 220 мкм образуется в результате царапания компактного металла стальной щёткой в виде ленты. При этом царапающую ленту укрепляют на вращающемся барабане, а пластину магния прижимают к ней и придают пластине возвратно-поступательное движение. Порошок магния размером частиц 90 мкм получают на фрезерных станках специальной конструкции. Известен способ получения кальция с размером частиц около 250 мкм, заключающийся в виброистирании кусков металла в модифицированной шаровой мельнице в атмосфере аргона.
Физические свойства
Условия проведения металлотермических реакций в значительной степени определяются физическими свойствами металлов-восстановителей. В частности, теплопроводность металлотермических шихт и, следовательно, характер их нагрева в печи восстановления зависят от теплопроводности металлов-восстановителей. Переход металлов-восстановителей в расплав интенсифицирует протекание металлотермической реакции, а их испарение является существенным фактором, влияющим как на скорость горения металлотермической смеси, так и на условия расслаивания металла и шлака. Плотность металлов-восстановителей обусловливает количество шихты, загружаемой в аппарат восстановления.
К основным физическим свойствам металлов-восстановителей, которые необходимо учитывать при анализе металлотермических реакций, относятся следующие:
Al | Mg | Са | Na | |
Плотность при 20 °С, г/см3 | 2,70 | 1,74 | 1,54 | 0,97 |
Плотность расплавленного металла, г/см3 | 2,38 | 1,59 | 1,36 | 0,93 |
Коэффициент теплопроводности при 20 °С, Вт/(м∙К) | 238 | 167 | 125 | 128 |
Вязкость расплавленного металла, мПа∙с | 1,24 | 1,32 | 1,22 | 0,68 |
Температуры фазовых переходов и термодинамические параметры металлов-восстановителей и некоторых их соединений, представляющих интерес в металлотермии, показаны в табл. 3 и 4.
Таблица 3
Температура ( t ) и энтальпии (Δ H ) фазовых превращений
Дата добавления: 2019-02-26; просмотров: 213; Мы поможем в написании вашей работы! |
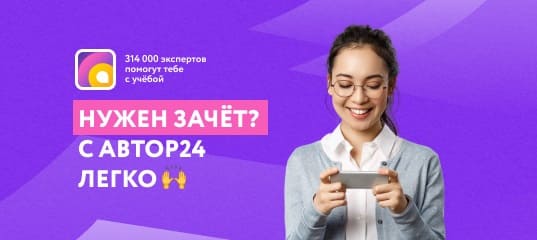
Мы поможем в написании ваших работ!