Уравнения для расчёта изменения энергии Гиббса
реакций восстановления TiCl4 металлами
Реакция | Уравнение энергии Гиббса, кал. |
½TiCl4 +2Na → 2NaCl + ½Ti | – 110200 + 28T |
½TiCl4+Ca → CaCl2 +½Ti | – 94200 + 15,9T |
½TiCl4 + Mg → MgCl2 + ½Ti | – 66800 + 22Т |
½TiС14 + 2/3 Аl → 2/3 АlCl3 + ½Ti | – 9600 + 12,37Т |
В промышленности широкое распространение получили процессы восстановления TiCl4 магнием и натрием. Для восстановления TiCl4 алюминием требуется более высокая температура. Этот процесс осложнен также образованием сплава Ti–Al.
Способ магниетермического восстановления TiCl4 – основной в технологии титана. Достаточно сказать, что при проектировании всех заводов в СССР был принят этот способ производства металлического титана. Приемлемый для промышленного производства способ получения титана магниетермическим восстановлением впервые был предложен Кроллем (США) в 1940 г., причём первый аппарат Кролля был рассчитан на получение менее 300 г металла за цикл. Советский Союз по производству титана вышел на одно из первых мест в мире. Были созданы аппараты, позволяющие за один цикл получать 1,5–2 т титановой губки («Редмет-500», «Редмет-501»). В настоящее время масштаб плавки значительно увеличен (более 5 т Ti).
Для реакции
TiCl4 + 2Mg → 2MgCl2 + Ti
выражение для константы имеет вид
При избытке магния рMg = const и Кр определяется температурой проведения реакции. Зная рMg и рассчитывая K р реакции по уравнению, легко определить равновесное давление пара TiCl4, или иными словами – полноту протекания процесса.
|
|
Так, принимая для 800 °С ΔG° ≈ 80 ккал, имеем .
При избытке магния (800 °С)
pMg = 0,04 ат; .
В реакционной системе, кроме основной реакции восстановления, могут протекать и другие реакции:
A. | 2TiCl4 + Mg → MgCl2 + 2TiCl3; | (I) |
TiCl4 + Mg → MgCl2 + TiCl2; | (II) | |
TiCl4 + 2Mg → 2MgCl2 + Ti; | (III) | |
2TiCl3 + Mg → 2TiCl2 + MgCl2; | (IV) | |
2/3TiCl3 + Mg → 2/3Ti + MgCl2; | (V) | |
TiCl2 + Mg → MgCl2 + Ti; | (VI) | |
Б. | TiCl4 + Ti → 2TiCl2; | (VII) |
2TiCl4 + 2TiCl2 → 4TiCl3; | (VIII) | |
2TiCl4 + 2/3Ti → 8/3TiCl3; | (IX) | |
2TiCl3 + Ti → 3TiCl2; | (X) | |
В. | 2TiCl4 + 2Mg → 2MgCl + 2TiCl3; | (XI) |
2TiCl4 + 2MgCl → 2MgCl2 + 2TiCl3; | (XII) | |
2TiCl3 + 2Mg → 2MgCl + 2TiCl2; | (XIII) | |
2TiCl3 + 2MgCl → 2MgCl2 + 2TiCl2; | (XIV) | |
TiCl2 + 2MgCl → 2MgCl2 + Ti. | (XV) |
Все возможные реакции разбиты на три группы: А – основные реакции – восстановление TiCl4 магнием до TiCl3, TiCl2, Ti, а также реакции довосстановления низших хлоридов; Б – вторичные реакции – взаимодействие TiCl4 с продуктами основных реакций, реакции диспропорционирования низших хлоридов; В – реакции с образованием субхлорида магния и его участием в качестве восстановителя.
При взаимодействии в конденсированных фазах термодинамически вероятны реакции (I – VI), а также (XI – ХIII). Из вторичных процессов наиболее вероятна реакция (VII). Реакции (VIII) и (IX) характеризуются малой убылью энергии Гиббса, однако протекание их возможно, поскольку TiCl3 обладает высоким давлением насыщенного пара и может удаляться из сферы реакции.
|
|
В газовой фазе наиболее вероятны реакции первичного образования низших хлоридов TiCl2 и TiСl3; возможны также и вторичные реакции их образования.
Все реакции с участием субхлорида магния в качестве восстановителя характеризуются большой убылью энергии Гиббса, что может способствовать протеканию реакций его образования. В настоящее время реакторы восстановления в промышленных условиях имеют диаметры от 850 – 1000 до 1300 – 1500 мм при высоте от 1800 – 2000 до 3000 мм. Наиболее употребляемые материалы для их изготовления – малоуглеродистые, хромоникелевые стали, а также биметаллы (материал, состоящий из двух слоёв – чёрная сталь и сплав, устойчивый к воздействию хлоридов).
Обычно используют два типа реакторов: с вставным реакционным стаканом и без стакана (тигля). Реакционный стакан предохраняет корпус реактора от проплавления и облегчает удаление реакционной массы, однако зазор между стенками стакана и аппарата резко ухудшает теплоотвод, уменьшает полезный объём аппарата. Вакуумируют реактор и подают в него TiCl4 и аргон через центральную трубу на крышке, MgCl2 сливают с помощью сифона или патрубков, расположенных сбоку или в центре днища. На рис. 6 приведена схема промышленного аппарата без стакана (тигля). Тепло от реактора отводят, как правило, охлаждая зону преимущественного протекания реакции воздухом. Охлаждающий воздух подают в нескольких точках по окружности печи. Вентиляторы включают и подают охлаждающий воздух с помощью автоматической системы.
|
|
Рис. 6. Схема бестигельного аппарата для металлотермического получения губчатого титана: 1 – аппарат восстановления; 2 – печь
Разнообразие возможных реакций определяет сложность установления истинного механизма протекания процесса восстановления. В настоящее время наибольшее распространение получило следующее описание процесса. Реакция происходит между жидким магнием и TiCl4 на поверхности губки, растущей у стенок аппарата, выше первоначального уровня восстановителя (выше поверхности расплавленного магния). Таким образом, первоначально титановая губка образуется в точках соприкосновения расплава восстановителя и стенок реакционного сосуда или вставного реакционного стакана.
|
|
Магний капиллярными силами по порам поднимается к поверхности губки и покрывает её поверхность плёнкой. Процесс носит автокаталитический характер. Катализатором служит активная (не перекрытая хлористым магнием) поверхность губки. Предполагается, что молекулы ТiСl4 проходят через стадию активированной адсорбции.
Образующийся по реакции хлористый магний опускается под слой расплавленного магния (плотность MgCl2 1,68 г/cм3, Мg 1,57 г/cм3). Схематично рост губки в аппарате восстановления TiCl4 представлен на рис. 7.
Рис. 7. Схема восстановления TiCl4 магнием:
а – начало процесса, б – конец процесса;
1 – бачок с TiCl4, 2 – электропечь; 3 – место появления титановой губки,
4 – аппарат восстановления; 5 – летка для выпуска расплава МgСl2
Плотность титана больше плотности MgCl2, и часть титана опускается на дно.
При высокой температуре TiCl4 реагирует с материалом реактора – железом. При этом получаются низшие хлориды и титаниты железа:
Fe + 2TiCl4 → FeCl2 + 2TiCl3;
Fe + TiCl4 → FeCl2 + TiCl2;
Fe + 2TiCl2 → FeTi + TiCl4;
Fe + 4TiCl3 → FeTi + 3TiCl4;
3Ti + 2FeCl2 → 2FeTi + TiCl4.
Побочные реакции загрязняют губку железом и низшими хлоридами. Часть низших хлоридов растворяется в хлористом магнии и довосстанавливается до титана магнием, также растворённым в MgCl2. Однако значительная часть образовавшихся низших хлоридов остаётся на поверхности губки, крышке и боковых стенках реактора. При демонтаже реактора низшие хлориды взаимодействуют с влагой воздуха и разлагаются с образованием оксида титана и НСl. Происходит также реакция диспропорционирования с образованием тонкодисперсного порошка металлического титана и паров TiCl4. Мелкодисперсный титан пирофорен и при выборке губки часто загорается. Пары TiCl4 портят вакуумное масло и насосы.
Большинство исследователей считают, что реакции в газовой фазе не имеют места или протекают в особых условиях (пониженные концентрации, начало процесса и т.п.).
В настоящее время из двух вариантов процесса: с догрузкой восстановителя и с единовременной загрузкой – предпочтение отдается последнему (т.е. весь необходимый магний загружается в твёрдом виде на дно реактора или реакционного стакана)
Представляет интерес разработка процесса восстановления TiCl4 магнием в условиях одновременной подачи исходных реагентов: магния и TiCl4. При этом могут создаться более благоприятные условия для реагирования.
Рассмотрим более подробно современный способ производства титана. Реакционный стакан и реактор перед проведением процесса тщательно очищают (механическим способом, травлением соляной кислотой, металлическими щётками и обдувкой). Магний загружают в виде чушек, слитков или в расплавленном состоянии. Твёрдый магний перед загрузкой очищают от поверхностных плёнок и шлаковых включений травлением в 0,5-1 %-м растворе НСl с последующей промывкой водой. Загрузка в реактор проводится в «сухих комнатах». Для загрузки расплава применяют специальный вакуумный тигель – дозатор. Реактор перед установкой в печь восстановления вакуумируют и проверяют на герметичность, затем заполняют сухим инертным газом. В печи реактор разогревается до 400 – 600 °С с одновременным вакуумированием. Затем его снова заполняют аргоном и разогревают до 650 – 760 °С. При этой температуре давление инертного газа в реакторе снижают до 0,05 – 0,1 ат и подают TiCl4.
Вначале процесс восстановления протекает медленно – до появления на стенках реактора первых частиц титана (катализатор). После этого процесс вступает в основную стадию. В процессе восстановления периодически производится слив MgCl2. В конце процесса восстановления после прекращения подачи TiCl4 для довосстановления низших хлоридов и более полного отделения MgCl2 делают 30 – 60-минутную выдержку при 900 °С, после чего проводят последний слив MgCl2. Затем в аппарат подают аргон и охлаждают в печи до 800 °С (если реактор изготовлен из нержавеющей стали) или до 600 °С (из малоуглеродистой стали), чтобы избежать окисления поверхности реактора на воздухе. Дальнейшее охлаждение аппарата до 20 – 40 °С проводят на специальном стенде с орошением его поверхности водой или обдувкой.
Реакционная масса состоит из 45 – 60 % губчатого титана, 15 – 35 % MgCl2 и 25 – 35 % Mg. Содержимое аппарата восстановления высверливается на станке или удаляется с помощью отбойного молотка.
Предложено несколько режимов подачи TiCl4 в аппарат, однако лучшие показатели получены для режима стабильной максимально возможной скорости подачи в течение всего процесса. На рис. 8 показана схема автоматического регулирования процесса восстановления TiCl4.
|

Рис. 8. Схема автоматического регулирования процесса восстановления TiCl4:
1 – пульт программирования и сигнализация; 2 – расходомер TiCl4 с регулирующим клапаном 2а; 3 – термощупы для измерения температуры в зоне реакции с многопозиционным потенциометром 3а; 4 – вентилятор охлаждения печи с исполнительным механизмом переключения шиберов воздушного коллектора 4а; 5 – тензовесы с весомером 5а и клапаном 5б пневмоцилиндра привода устройства для слива хлористого магния, 6 – приборы регулирования давления аргона и TiCl4 в реакторе: 7 – термопара с потенциометром 7а для измерения температуры в нижней зоне реактора, 8, 9 – вольт-амперметры
Титановую губку можно отделить от MgCl2 и магния дистилляцией в вакууме гидрометаллургическим способом и по комбинированной схеме. В настоящее время предпочтение отдают дистилляционному методу сепарации губки. Дистилляция исключает возможность окисления порошка титана и поглощения водорода, неизбежных при гидрометаллургической обработке. Отгонка магния и MgCl2 в вакууме основана на высоком давлении насыщенного пара этих веществ при повышенной температуре (табл. 6).
Таблица 6
Давление насыщенного пара магния и MgCI2, мм рт.ст.
t, °С | Mg | MgCl2 | t, °С | Mg | MgCl2 |
700 750 800 850 | 5 12 25 45 | – 1,9 2,2 3,8 | 900 1000 1107 1412 | 80 250 760 – | 8,0 80 150 760 |
Отгонку можно осуществлять как в аппарате восстановления, так и в отдельном аппарате. Аппарат для сепарации схематично показан на рис. 9. Головка реторты, подвергающаяся нагреванию в печи (куда помещают реакционный стакан в перевёрнутом виде), изготовляется из нержавеющей стали толщиной 13 мм; нижняя часть реторты, заключенная в охлаждаемую водой рубашку, – из малоуглеродистой стали. Реакционный стакан (тигель) аппарата восстановления устанавливают на подставке в опрокинутом положении.
Рис. 9. Реактор для вакуумной сепарации титановой губки:
1 – водоохлаждаемый кожух; 2 – опорная колонна; 3 – печь; 4 – тигель;
5 – реторта; 6 – резервуар для солей; 7 – экраны; 8 – к вакуум-насосу
В том случае, если реакционную массу предварительно выбирают из реактора, куски несепарированной губки загружают в перфорированную корзину, по оси которой проходит также перфорированная труба, что облегчает испарение примесей. Примерные размеры корзины: диаметр 420 мм, высота 610 мм, загрузка 100 кг губки.
Перед началом отгонки корзину устанавливают на решётчатой опорной плите и поднимают в верхнюю часть реторты из нержавеющей стали. Для предотвращения нагрева сконденсированных продуктов теплоизлучением из верхней зоны посредине реторты устанавливают стальные отражательные экраны. Верхняя часть реторты нагревается вакуумной электропечью, в зоне нагревателей которой создаётся вакуум. Это делается для предохранения от смятия стенок реторты при нагреве (поскольку реторта перед сепарацией вакуумируется и при нагреве её верхней части возможно её смятие, если не создать контрвакуума в печи). До включения обогрева в реторте вакуум составляет 3·10–7 мм рт. ст., а в вакуумной печи – 2·10–4 мм рт. ст. В процессе нагрева вакуум в реторте обычно составляет 2·10–6 мм рт. ст. Температура верхней части реторты поддерживается 925 °С. Процесс длится 48 ч. Время остывания реторты около 20 ч. Во время остывания производят откачку аппарата, а затем реторту заполняют сухим аргоном или гелием. Разгрузку аппарата производят при продувке реторты сухим аргоном.
Очищенную губку измельчают на щёковой дробилке и просеивают через грохот с размером ячеек 12 – 13 мм. Средний расход энергии на дистилляцию 4,6 квт/ч на 1 кг рафинированной губки. Проведение процесса сепарации в отдельном аппарате сопряжено с соприкосновением губки с воздухом и частичным окислением. Для повышения качества металла разработаны процессы сепарации в аппарате восстановления. Получаемая титановая губка содержит обычно: 0,03 – 0,15 % О; 0,01 – 0,04 % N; 0,02 – 0,15 % Fe; около 0,002 – 0,005 % Н; 0,02 – 0,12 % Сl; 0,01 – 0,05 % Si; 0,01 – 0,03 % С; около 0,01 % Аl; 0,01 % Ni и др. Твёрдость губки по Бриннеллю колеблется от 90 – 100 до 160 – 180 кгс/мм2, а в отдельных случаях до 200 – 220 кгс/мм2.
Обычно центральная часть блока губки получается наиболее качественной, гарниссажная (прилегающая к стенкам реактора) губка и губка низов содержат больше примесей и более тверды.
Стоимость энергии и трудовые затраты на переделе восстановления и очистки титана составляют примерно 25 % стоимости получаемой титановой губки, стоимость исходного ТiСl4 – около 30 % стоимости губки.
В настоящее время ведутся работы по созданию непрерывного процесса получения титана магниетермическим методом. Главное осложнение при осуществлении непрерывного процесса – трудность непрерывного вывода продуктов реакции из реакторов из-за приваривания титана к стенкам.
Можно осуществить подачу жидкого восстановителя в реактор, вдувая его с помощью аргона. ТiСl4 подаётся в парообразном виде. Возможна подача обоих компонентов реакции в виде пара. Иногда жидкий восстановитель подаётся в виде капель, которые реагируют с TiCl4, образуя гранулы реакционной массы, выводящиеся из зоны реакции.
По одному из способов жидкий магний нагревают в испарителе до 1043 °С (при этом давление его насыщенного пара достигает 400 мм рт. ст). Аргон, нагретый до 800 °С и с высокой скоростью пропускаемый через испарительную камеру, подаёт в реактор пары магния сверху. Расплавленный магний имеет постоянную поверхность, что при постоянной температуре позволяет регулировать скорость испарения количеством пропускаемого аргона. ТiСl4 поступает из испарительной камеры, обогреваемой газовой горелкой, в трубопровод, конденсируется, во второй испаритель, где мгновенно испаряется и с высокой скоростью через сопло, направленное вниз, поступает в реактор. Продукты реакции поступают в зону охлаждения и затем в циклон.
По другому методу капли жидкого восстановителя подаются в кипящий TiCl4, находящийся всё время во вращении для предотвращения приваривания частиц титана к стенкам реактора. При этом состав гранул, опускающихся на дно реактора по мере увеличения содержания титана, следующий: 79 % MgCl2, 1 % Mg , 19 – 20 % Ti, 0,5 – 1,5 % низших соединений титана. Наилучшее использование магния достигается при диаметре капель 2 – 5 мм.
В настоящее время можно считать решённой проблему непрерывного ввода в реактор восстановителя и TiCl4, однако, обеспечение непрерывного вывода продуктов реакции ещё требует детальной проработки.
3.4.2. Восстановление TiCl4 натрием
До 1955 г. магниетермический способ восстановления ТiСl4 был единственным промышленным способом, получившим широкое распространение. Главным недостатком этого способа является его периодичность.
Применение натрия даёт возможность снизить температуру восстановления. В этих условиях непрерывный процесс представляется более осуществимым. Если процесс восстановления магнием достигает заметной скорости при температуре выше 750 °С, то в случае натриетермического восстановления процесс идёт с заметной скоростью уже при 200 °С, а приемлемая для промышленных целей скорость достигается при температуре 500 – 700 °С. При такой температуре можно избежать сваривания титана со стенками реактора, что является главным препятствием к осуществлению непрерывного процесса.
Восстановление ТiСl4 натрием можно в принципе осуществить по трём вариантам:
· при температуре ниже точки плавления NaCl (800 °С);
· в интервале 800 – 880 °С – ниже температуры кипения металлического натрия;
· выше температуры кипения натрия (в газовой фазе).
Третий вариант связан с трудностями, главная из которых – зарастание впускного отверстия форсунок для подачи парообразного металла продуктами реакции. В этих условиях получается мелкодисперсный титан, который трудно отделить от хлорида металла-восстановителя. Аналогичные трудности возникают, если использовать в качестве восстановителя парообразный магний.
Второй вариант неудобен из-за очень узкого интервала рабочей температуры. Реакция восстановления экзотермична, поэтому трудно предотвратить местные перегревы.
Первый вариант представляет наибольший интерес. Получающаяся в результате реакции смесь легче поддаётся гидрометаллургической обработке, чем реакционная масса после восстановления магнием. Обладающий низкой температурой кипения натрий легко отогнать из реакционной массы в вакууме или же его можно перевести в раствор выщелачиванием аммиачной водой. Коэффициент использования натрия в процессе восстановления значительно выше, чем при работе с магнием, поэтому содержание металла-восстановителя в реакционной массе меньше.
Более низкая температура плавления натрия облегчает очистку и подачу восстановителя в жидком виде в реактор:
TiCl4 + 4Na → Ti + 4NaCl – 209 800 кал;
TiCl4 + 2Mg → Ti + 2MgCl2 – 123 400 кал.
Количество тепла, выделяющегося при натриетермическом восстановлении (750 кал на 1 г шихты), выше, чем в случае использования магния (в расчёте на единицу массы восстановленного титана), что приводит к необходимости отвода тепла и препятствует ведению процесса с высокой скоростью. Объём образующихся продуктов реакции больше объёма продуктов магниевого процесса. Все это снижает удельную производительность реакторов при восстановлении натрием (по сравнению с магниетермией).
Расход энергии при электролитическом получении натрия составляет 14 кВт∙ч/кг, а магния – 20 кВт∙ч/кг. Однако расход натрия при восстановлении TiCl4 больше, чем магния, поэтому и расход энергии на восстановитель в этом случае на 25 % выше. Кроме того, 90 % MgCl2, получающегося при восстановлении, используют для электролиза и возврата металла-восстановителя, что значительно снижает стоимость магния. NaCl – весьма дешёвый продукт, поэтому его возвращение на электролиз не может существенно сказаться на стоимости восстановителя. Однако замена вакуумной сепарации губки после магниетермического восстановления не требующим больших капитальных затрат выщелачиванием сказывается на стоимости получаемого титана и в ряде случаев делает натриетермический процесс более выгодным. В настоящее время в Англии и США работают заводы, использующие натриетермию. На некоторых заводах процесс восстановления осуществляется по непрерывной схеме.
По одному из способов восстановление идёт при температуре, близкой к температуре плавления NaCl. В закрытый реактор, наполовину заполненный твёрдым NaCl, подают TiCl4 и жидкий натрий (с избытком 1 % сверх стехиометрического). Образующаяся реакционная масса, состоящая из NaCl и титана, непрерывно перемешивается и постепенно выводится из реактора и затем охлаждается. Получающийся губчатый титан имеет чистоту 99,5 %. Низкая температура реакции обусловливает образование мелкого порошка титана. С целью укрупнения кристаллов реакционную массу перед выпуском нагревают несколько выше 800 °С и выдерживают при этой температуре непродолжительное время. При этом порошок превращается в губку. Перед выщелачиванием NaCl значительная часть его обычно выплавляется с возвратом на электролиз. Оставшаяся реакционная масса выщелачивается.
По другому способу ТiСl4 восстанавливается амальгамой натрия, которая получается в результате электролиза расплава NaCl с ртутным катодом. Титан отделяется от ртути отгонкой в вакууме. Металлический натрий в амальгаме дешевле и более чист.
Присутствие в реакционной массе низших хлоридов вредно из-за возможности их гидролиза:
6TiCl2 + 6H2O → 4TiCl3 + 2Ti(OH)3 + 3H2;
TiCl3 + 3H2O → Ti(OH)2 + 3HCl.
Поэтому выщелачивание целесообразно вести подкисленным раствором (0,5 % кислоты):
TiCl3 + 3HNO3 → Ti(NO3)3 + 3HCl;
2TiCl3 + 3H2SO4 → Ti2(SO4)3 + 6HCl.
При этом образуются растворимые соли, удаляющиеся при выщелачивании, и губка не загрязняется кислородом.
Полученную титановую губку сушат при температуре несколько выше 100 °С. Для предотвращения окисления необходима герметизация сушильных аппаратов. При строгом соблюдении условий выщелачивания титановый порошок можно прессовать в электроды для переплавки в дуговых печах без дополнительной дегазации.
3.4.3. Восстановление Т i О2 кальцием
Порошкообразный титан можно получить восстановлением диоксида титана кальцием по реакции:
TiO2 + 2Ca → Ti + 2CaO – 25,4 ккал.
Температура процесса 1000 °С. При этом разница в сродстве кальция к кислороду (ΔGº = – 124 ккал) и титана к кислороду (ΔGº = – 118 ккал) составляет всего 6 ккал. Поэтому для обеспечения быстрого протекания реакции надо создать большой избыток восстановителя (25 – 50 %) над теоретически необходимым количеством. Выделяющегося тепла недостаточно для поддержания необходимой температуры. При температуре процесса кальций находится в жидком состоянии, а давление его насыщенного пара высокое (11 мм рт. ст. при 1000 °С), что обеспечивает хороший контакт восстановителя с ТiO2. Последний загружают в реактор в виде порошка, кальций – в виде мелких кусочков или стружки. К кальцию предъявляют высокие требования по чистоте, так как он может поглощать из воздуха азот и углекислоту, которые переходят в восстановленный титан. Перед восстановлением кальций обычно очищают дистилляцией.
Восстановление проводят в герметическом реакторе (бомбе) из нержавеющей стали. Реактор после загрузки шихты и откачки воздуха заполняют аргоном. Во избежание повышения давления при разогреве во время реакции к реактору через открытый патрубок присоединяют резиновый буферный баллон с аргоном. Крышка реактора должна обогреваться, чтобы предотвратить конденсацию на ней паров кальция. Чтобы обеспечить контакт между компонентами, шихту брикетируют. Реактор выдерживают около часа в печи при 1000 – 1100 °С. Затем его удаляют из печи и после остывания выгружают застывший солевой плав. Для отделения порошка титана от СаО и избытка кальция реакционную массу обрабатывают большим количеством Н2О и затем слабой кислотой. Получающийся мелкий порошок титана (2 – 3 мкм) в процессе выщелачивания заметно окисляется. Более крупные кристаллы титана (100 мкм) получают, добавляя в шихту СаСl2 (в количестве, равном по массе образующейся СаО). При 1000 °С СаО частично растворяется в расплаве СаСl2 и прослойка твёрдой СаО, мешающая росту кристаллов титана, не образуется. Кроме того, в расплаве СаСl2 частично растворяются металлический кальций (при 1000 °С около 25 %) и ТiO2. Реакция восстановления при этом протекает в растворе:
TiO2 + 2CaCl2 → TiCl4 + 2CaO;
TiCl4 + 2Ca → Ti + 2CaCl2.
Получающийся металл загрязнён кислородом.
3.4.4. Восстановление Т i О2 гидридом кальция
В промышленности получил применение процесс восстановления диоксида титана гидридом кальция с получением гидрида титана:
TiO2 + 2CaH2 → TiH2 + 2CaO + H2
с последующим разложением гидрида титана на водород и титан.
Гидрид кальция получают прокаливанием кусков металлического кальция в чистом сухом водороде при 400 – 600 °С. Он представляет собой хрупкое солеподобное соединение ионного типа, легко измельчающееся в порошок. СаН2 легко разлагается водой:
CaH2 + 2H2O → Ca(OH)2 + 2H2,
поэтому при шихтовании с ТiO2 следует принимать меры, предотвращающие попадание влаги. Для уменьшения скорости разложения гидрид не следует измельчать до мелкого порошка.
Получающийся порошкообразный гидрид титана (3 – 5 мкм) вследствие большой коррозионной стойкости по сравнению с чистым металлом окисляется при промывке и сушке в меньшей степени.
Восстановление производят в реторте из стали при температуре 1100 °С. После эвакуации реторту заполняют водородом. Спёк, состоящий из смеси порошка гидрида титана и СаО, вымывают водой из реторты, в которой происходило восстановление. СаО выщелачивают слабым раствором HCl. Титановый порошок отфильтровывают, сушат, прессуют в брикеты и подвергают спеканию в печи с индукционным нагревом при 1400 – 1450 °С и давлении 10–3 мм рт. ст.
В отмытом порошке гидрида титана содержится около 0,5 % кислорода в виде плёнок оксидов. Однако при спекании в вакууме брикетов, спрессованных из порошка гидрида титана, происходит, по-видимому, частичное восстановление плёнок оксидов выделяющимся в результате диссоциации гидрида атомарным водородом. Получающийся компактный металл содержит меньшее по сравнению с исходным порошком гидрида количество кислорода и следы водорода.
Получение циркония и гафния
Технологические приёмы получения металлических циркония и гафния практически не отличаются друг от друга. Энергетические характеристики их соединений, используемых в металлотермических процессах, чрезвычайно близки (табл. 7).
Таблица 7
Энергия Гиббса ΔGº298 и теплота образования Δ H º298 соединений циркония и гафния (в расчёте на один атом окислителя)
Соединение | – ΔGº298, ккал | – ΔHº298, ккал | Соединение | – ΔGº298, ккал | – ΔHº298, ккал |
НfO2 | 126,2 | 133,1 | HfСl4 | 58,4 | 62,5 |
ZrO2 | 123,9 | 130,8 | ZrF3 | 111,0 | 117,0 |
ZrCl2 | 67,0 | 72,8 | ZrF2 | 109,5 | 116,7 |
ZrCl3 | 64,3 | 69,3 | ZrF4 | 106,2 | 111,2 |
ZrCl4 | 52,3 | 57,7 | HfF4 | 103,3 | 108,8 |
Специфика получения циркония и гафния в сравнении с титаном обусловлена некоторыми различиями в химическом поведении и агрегатном состоянии их соединений.
Восстановление оксидов
Диоксид циркония восстанавливают кальцием, процесс начинается при 700 °С и проходит полностью при 1000 °С. При повышении температуры > 1100 °С наблюдается спекание зёрен, и получаемый порошок обладает меньшей пирофорностью. Избыток кальция сверх теоретически необходимого по реакции
ZrO2 + 2Ca → 2CaO + Zr
составляет 10 – 50 %.
Процесс осуществляют в герметически закрытом реакторе, в который послойно загружается ZrO2 (крупностью 0,175 мм) и кальций в виде стружки (2×5×20 мм). Добавка СаСl2 может быть меньше, чем в случае восстановления титана, так как порошок циркония обладает большей коррозионной стойкостью и окисляется в меньшей степени, несмотря на мелкозернистость. Процесс следует проводить в вакууме либо в атмосфере инертного газа.
Восстановление ZrO2 гидридом кальция протекает в тех же условиях, что и восстановление титана.
Восстановление фторидов
Фториды имеют преимущество перед хлоридами вследствие их малой гигроскопичности. В настоящее время в промышленных масштабах производят тетрафторид циркония ZrF4 и фторцирконат калия K2ZrF6. Фториды циркония и гафния могут быть восстановлены натрием, кальцием, магнием и алюминием. Использование в качестве восстановителя кальция и магния приводит к образованию нерастворимых фторидов, в то время как NaF легко удаляется из реакционной смеси в результате обработки водой.
Теплоты реакции восстановления:
K2ZrF6 + 4Na → Zr + 4NaF + 2KF
не хватает для самопроизвольного протекания процесса, поэтому для поддержания температуры реакции (800 – 900 °С) необходим внешний подогрев.
Схема аппарата для натриетермического восстановления фторцирконата калия представлена на рис. 10.
В толстостенный тигель вставлен реакционный стакан из нержавеющей стали. Готовят расплав, состоящий из смеси 90 кг K2ZrF6, 16,5 кг КСl и 16,5 кг NaCl. KCl и NaCl добавляют для снижения температуры плавления смеси. Застывший расплав измельчают (до 1 мм) и засыпают в бункер. В реакционный стакан заливают расплавленный натрий, повышают температуру до 800 °С и из бункера подают смесь K2ZrF6 + KCl + NaCl. Фторцирконат падает на поверхность расплавленного натрия, и образующиеся кристаллы металлического циркония опускаются на дно стакана. Жидкий натрий и расплавленные хлориды защищают образующийся металл от контакта с газом (обычно во время реакции аппарат заполняется водородом). В дальнейшем реакционную массу измельчают и выщелачивают водой. В результате реакции восстановления образуется большое количество солей, что приводит к формированию мелких кристаллов порошка циркония и его загрязнению кислородом. Содержание циркония в таком порошке 98 – 99 %. Порошок используют в основном в военном деле (для различных взрывчатых и воспламеняющихся смесей), в пиротехнике и в электровакуумной технике (в качестве геттера). Мелкие порошки редких металлов (Ti, Zr и др.) применяют в качестве добавок в напалм (зажигательное вязкое вещество на основе бензина или керосина в смеси с загустителем – порошком алюминиевых солей нафтеновой или пальмитиновой кислот). Добавление порошков Mg, Ti, Zr и неорганических окислителей повышает температуру горения до 1600 °С и выше.
Рис. 10. Схема аппарата для натриетермического восстановления
фторцирконата калия:
1 – тигель, 2 – реакционный стакан; 3 – бункер, 4 – бачок с расплавленным натрием;
5 – печь
Представляет большой интерес получение слитка циркония непосредственно в печи для восстановления. В этом плане более перспективным представляется восстановление фторидов из-за более низкого давления насыщенного пара при высокой температуре и меньшей склонности к гидролизу.
Металлический кальций является самым эффективным восстановителем для тетрафторида и низших фторидов циркония. Учитывая возможность стадийного протекания процесса кальциетермического восстановления с образованием в качестве промежуточных продуктов низших фторидов циркония, можно предположить протекание следующих реакций:
ZrF4 + 2Ca → Zr + 2CaF2; | (I) |
ZrF4 + ½Ca → ZrF3 + ½CaF2; | (II) |
ZrF3 + 3/2Ca → Zr + 3/2CaF2; | (III) |
ZrF3 + ½Ca → ZrF2 + ½CaF2; | (IV) |
ZrF4 + Ca → ZrF2 + CaF2; | (V) |
ZrF2 + Ca → Zr + CaF2. | (VI) |
Значения теплового эффекта и энергии Гиббса реакций (I) – (VI) для интервала 298 – 1100 К представлены в табл. 8.
Таблица 8
Дата добавления: 2019-02-26; просмотров: 698; Мы поможем в написании вашей работы! |
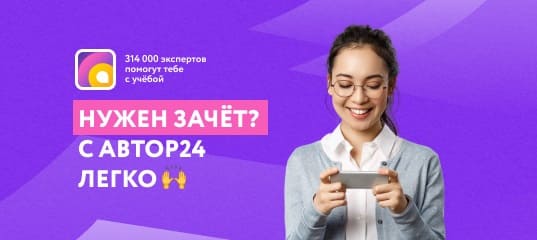
Мы поможем в написании ваших работ!