Технология приготовления травяной муки и резки
Травяную муку и резку приготавливают на высокотемпературных агрегатах типа АВМ. Приготовление травяной муки и резки включает следующие последовательно выполняемые операции: скашивание растительного сырья с измельчением и погрузкой в транспортное средство; перевозку его к пункту сушки и выгрузку в питатель сушильного агрегата; высушивание сырья до кондиционной влажности (14…16 % для травяной резки и 10…12% для травяной муки); прессование травяной муки в гранулы или брикеты; охлаждение травяной муки; закладку кормов на хранение.
Высокотемпературная сушка позволяет заготовлять из трав корма (травяную резку и муку), не уступающие по питательности многим зерновым концентратам и превосходящие их по ценности белка, содержанию минеральных веществ, витаминов и другим элементам; сократить до минимума потери питательных и биологически активных веществ растительного сырья; увеличить примерно в 1,3…1,5 раза выход кормовых единиц с 1га; получать высококачественный корм независимо от складывающихся погодных условий; организовать заготовку кормов на промышленной основе. Благодаря высокому содержанию в травяной муке и резке каротина (в 5…8 раз больше, чем в сене) уменьшаются расходы ферм на приобретение дорогостоящих препаратов витамина А. Муку можно использовать также для повышения питательной ценности комбикормов и снижения в них удельного веса концентратов (зерна).
|
|
Вместе с тем при производстве кормов искусственной сушки велик расход топлива: в зависимости от влажности исходного сырья на 1000кг травяной муки требуется 118…474 кг жидкого топлива. Это обстоятельство ограничивает производство витаминной травяной муки.
Для получения высококачественной травяной муки исходное сырье должно быть высокого качества. В 1кг сухого вещества зеленой массы должно содержаться 250…300мг каротина, 20…21 % сырого протеина и 21…22 % сырой клетчатки. Травяную муку для свиней и птицы целесообразно готовить из свежескошенных трав, муку или резку для жвачных животных - из провяленных. В первом случае траву скашивают с измельчением и грузят в транспортные средства, во втором - выполняются кошение с обязательным плющением, провяливание, подбор с измельчением и погрузка. Дальнейшие операции обеих технологий аналогичны: транспортировка зеленой массы к сушилкам, взвешивание, разгрузка, сушка, гранулирование муки или брикетирование резки, взвешивание и складирование готовой продукции.
При уборке и измельчении зеленой массы необходимо соблюдать следующие агротехнические требования. В измельченной массе частицы длиной до 30мм должны составлять не менее 80%, а длиной до 100мм - не более 2%. Максимальная длина частиц - 100мм. Между скашиванием и сушкой допускается разрыв не более 2ч (для первого варианта технологии).
|
|
Свежескошенные бобовые травы сушатся очень неравномерно (листья пересыхают, стебли остаются влажными), из-за чего наблюдаются большие потери наиболее ценной лиственной фракции. Поэтому бобовые травы убирают с обязательным плющением и провяливают. При провяливании трава теряет некоторое количество питательных веществ и витаминов, поэтому процесс продолжают лишь до влажности растений 60…65%. Длительность этого процесса зависит от погодных условий и вида сырья, но не должна превышать 4ч. Благоприятны для провяливания трав условия, когда количество осадков в сутки не превышает 0,5мм, относительная влажность воздуха не более 85%, температура не ниже 13°С. Для ускорения провяливания, а значит, и снижения потерь питательных веществ зеленую массу ворошат в прокосах. При выпадении осадков в период уборки трав работу организуют по первому варианту технологии. Следует помнить, что скошенная трава, пролежавшая навалом 5…6 ч, непригодна для приготовления муки и резки.
Измельченная масса не должна содержать посторонних предметов (камни, металл и т. д.). Не рекомендуется нагревать траву в процессе сушки более чем до 70°С, иначе резко ухудшается ее переваримость. Необходимо стремиться к верхнему пределу влажности, установленной ГОСТом для готового продукта. В этом случае снижаются затраты энергии и потери питательных веществ.
|
|
Сокращению затрат топлива и повышению производительности сушилок способствует также двухфазный способ приготовления травяной резки. Вначале траву сушат до влажности 23…25% в сушилке, а затем досушивают до кондиционной влажности (15%) в хранилищах активным вентилированием. Это позволяет на 10..12% снизить расход топлива и на 15…20% повысить пропускную способность сушилки. Температура сушильного агента на выходе из сушилки при этом устанавливается на 15…20°С ниже, чем при сушке травы до кондиционной влажности.
Температура закладываемой на хранение готовой продукции не должна превышать температуру окружающего воздуха более чем на 8°С.
Согласно требованиям пожарной безопасности, резку до загрузки в хранилища необходимо выдерживать в прицепах вместимостью 12м3 не менее 10ч, 40м3 - не менее 12, а травяную муку- в промежуточных помещениях около 12 ч. Однако в прицепы поступает травяная резка температурой 40…45°С, при выдержке температура ее снижается незначительно и происходят большие потери каротина. Поэтому резку лучше охлаждать в специально оборудованных прицепах активным вентилированием до тех пор, пока разность температур верхних ее слоев и окружающего воздуха будет не более 8°С. Вентилирование обычно продолжается 15…20 мин. Кроме того, при продувке воздухом выявляются возможные очаги пожара. Охлажденную резку загружают в хранилища.
|
|
Травяную муку, предназначенную для хранения более трех месяцев, рекомендуется гранулировать на оборудовании типа ОГМ-0,8Б, ОГМ-1,5А с одновременным введением антиоксидантов (стабилизаторов) и хранить в бумажных мешках. При быстром охлаждении гранул, и особенно брикетов, на их поверхности образуется твердая корка, которая замедляет отдачу влаги и охлаждение внутренних слоев. При закладке такого корма на хранение поверхность брикетов нагревается и отпотевает за счет тепла и влаги внутренних слоев, корм плесневеет, может разогреться и «загореться». Поэтому брикеты и гранулы, приготовленные в холодную погоду, необходимо дополнительно охлаждать в вентилируемых бункерах или контейнерах. Лучше всего гранулированная мука сохраняется в комплектном оборудовании в среде инертных газов типа ОЗВ-1 и ОХК-1 (первое исполнение). В зависимости от качества корм искусственной сушки подразделяют на три класса с соответствующими свойствами.
В состав технологических комплексов приготовления травяной муки входят агрегаты высокотемпературной сушки травы, оборудование для гранулирования и брикетирования травяной муки и сечки, для накопления и временного хранения гранулированных кормов, а также для длительного их хранения. Для высокотемпературной сушки трав разработаны агрегаты типа АВМ-0.65Р (АВМ-0.65РЖ, АВМ-0.65РГ, АВМ-0,65РТ), типа ABM-1,5Б (ABM-1,5БЖ, АВМ-1.5БГ, АВМ-1,5РТ) вместо выпускавшихся раньше АВМ-0,65 и АВМ-1,5А. Проведены испытания агрегатов АВМ-3 и АВМ-5. Для гранулирования травяной муки предназначено оборудование ОГМ-0,8Б (вместо ОГМ-0.8А), ОГМ-1.5А (вместо ОГМ-1,5), а также ОПК-2А (вместо ОПК-2); для накопления и кратковременного (до суток) хранения гранулированных кормов - оборудование ОНК-1,5 и ОНК-1-80, для длительного хранения - ОЗВ-1 и ОХК-1.
4.2 Устройство агрегата для сушки кормов АВМ-0,65РЖ
Агрегаты типа АВМ-0.65Р (Рисунок 14) состоят из следующих основных узлов: питателя зеленой массы 4; подающего транспортера 3; теплогенератора 6; сушильного барабана 7; системы отвода сухой массы 1; дробилки 8; системы отвода муки 9; системы рециркуляции 2; шкафа управления 5. Агрегат разработан в трех исполнениях (в зависимости от используемого топлива): АВМ-0,65РЖ - с топкой, работающей на жидком топливе; АВМ-0.65РГ - на природном газе; АВМ-0.65РТ - на каменном угле.
Рисунок -14 Общий вид агрегата АВМ-0,65РЖ: 1-система отвода сухой массы; 2-система рециркуляции теплоносителя; 3-подающий транспортер; 4-питатель зеленой массы; 5-шкаф управления; 6-теплогенератор; 7-сушильный барабан; 8-дробилка; 9-система отвода муки; 10-циклоны.
Технологическая схема приготовления травяной муки АВМ-0,65РЖ представлена на рисунке 15. Перегруженная из транспортных средств трава подается конвейером 8 к битерам 9, 10; они выравнивают поток и направляют массу на транспортер 11, который подает ее в сушильный барабан 13. Жидкое топливо сжигается в топке 4. Перемешиваясь с воздухом и отработанным сушильным агентом, засасываемыми вентилятором 19 циклона системы отвода сухой массы 18, газы образуют теплоноситель, температура которого 500…900°С.
При вращении барабана 13 зеленая масса ворошится и омывается теплоносителем. Высохшая масса транспортируется в циклон 18, где отделяется от теплоносителя и через шлюзовой затвор 34 поступает в дробилку 29 для измельчения. Из дробилки мука отсасывается в циклоны 22, 25. Здесь она отделяется от воздуха и через шлюзовые затворы 21, 26 шнеком 20 подается в загрузочные горловины.
Рисунок-15 Технологическая схема агрегата АВМ-0.65РЖ:1-вентилятор; 2-форсунка; 3-камера сгорания; 4-топка теплогенератора; 5-битер; 6-гидравлические цилиндры; 7-лоток; 8-конвейер; 9-отбивной битер; 10-битер; 11-выгрузная горловина; 12-транспортер подающий; 13-барабан сушильный; 14-система рециркуляции; 15, 16 и 17-заслонки; 18-циклон сухой массы; 19-вентилятор; 20-шнек; 21-шлюзовой затвор; 22-циклон муки; 23, 24-вентиляторы; 25-циклон муки; 26- шлюзовой затвор; 27-заслонка дробилки; 28-решето дробилки; 29-дробилка; 30, 31, 32 и 33-заслонки пневмосепаратора; 34-шлюзовой затвор; 35-отборщик тяжелых частиц.
Теплоноситель температурой 110…120°С через выхлопную трубу вентилятором 19 циклона системы отвода сухой массы выбрасывается в атмосферу. При температуре отработанного теплоносителя 50…80°С включается система рециркуляции 14. Для этого необходимо частично закрыть заслонку 17, одновременно открывается заслонка 16, так как заслонки соединены.
В систему рециркуляции подается 25…30% отработанного теплоносителя. На транспортер поступает 30% тепла, а остальное - в теплогенератор. При невысокой влажности кормов в систему рециркуляции рекомендуется подавать до 60% отработанного теплоносителя. Регулировка проводится заслонкой 15.
Сушка и измельчение фуражного зерна аналогичны процессу приготовления травяной муки, но начальная температура не должна превышать 140…220°С, а температура отработанного теплоносителя - 90°С. Кроме того, необходимо трубопроводом соединить циклон 22 с вентилятором 24 циклона 25. В местах соединения лотка с конвейером устанавливают уплотнения.
Дата добавления: 2019-02-13; просмотров: 1700; Мы поможем в написании вашей работы! |
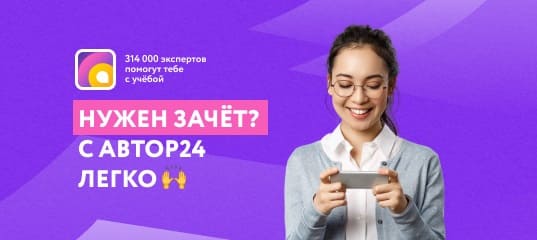
Мы поможем в написании ваших работ!