МЕХАНИЗМЫ ТРАНСМИССИИ. РАМЫ, ПОДВЕСОК, ШИН И РУЛЕВОГО УПРАВЛЕНИЯ
§ 50. КАРДАННАЯ ПЕРЕДАЧА
У крестовин карданных валов в процессе эксплуатации изнашиваются шипы по длине и диаметру. Износ торцов шипов крестовин определяют измерением расстояния между ними. При размере меньше допустимого крестовины бракуют. Износ шипов по диаметру устраняют наплавкой их в углекислом газе с последующим шлифованием до размера по рабочему чертежу.
Карданный вал может иметь следующие повреждения: скручивание трубы вала; изгиб вала; износ отверстий в вилке под подшипник; погнутость щек вилки. Скрученность трубы вала определяют по результатам измерения взаимного углового положения осей поверхностей вилок. При скрученности трубы вала более 3° или при наличии вмятин на трубе ее заменяют новой.
При износе отверстий в вилке под подшипники, обломах или при наличии трещин на вилках они подлежат замене. Изменение размера между щеками вилки устраняют правкой или вилку заменяют. Вилки к трубе приваривают дуговой сваркой под слоем флюса или в углекислом газе.
Погнутость вала определяют измерением радиального биения при установке его в приспособлении по диаметру и торцу в вилках по всей длине. При радиальном биении выше допустимого вал правят на прессе. При невозможности устранить данный дефект трубу заменяют новой.
Сборку карданной передачи автомобиля (ЗИЛ-431410) выполняют в два этапа: вначале собирают узлы, а затем проводят общую сборку передачи.
|
|
Для соединения фланца вилки с крестовиной ввертывают масленку 8 (рис. 175) и предохранительный клапан 7 в крестовину 6. Полученный узел устанавливают двумя шипами в отверстия фланца-вилки / так, чтобы предохранительный клапан 7 был обращен в сторону фланца вилки. На шипы крестовины 6 устанавливают подшипники 5 карданного вала 10 с сальником в сборе и запрессовывают крестовину в отверстия вилки /. Пазы на торце подшипников должны быть параллельны продольной оси вилки. Затем устанавливают опорные пластины 4 подшипников, пластины-замки 3, ввертывают болты крепления 2 и стопорят их, загибая на грани концы пластин-замков 3.
КАРДАННАЯ ПЕРЕДАЧА
241
Рнс . 176. Станок для динамической балансировки карданных калов
При сборке передней 32 и задней 28 крышек с сальником и обоймой сальника в гнездо крышки 32 вставляют уплотнительное кольцо 31 сальника и обойму 30. Затем обойму сальника запрессовывают и кернят в трех точках по окружности.
Для сборки подшипника с передней и задней крышками в заднюю крышку 28 запрессовывают подшипник 29. В подсобранный узел вставляют переднюю крышку 32 в сборе с кольцом 31 сальника и обойму 30 и завальцовывают по окружности, обеспечивая герметичность соединения. При сборке промежуточной опоры 13 карданного вала в заднюю крышку 28 ввертывают масленку 27. В подушку 33 опоры устанавливают подшипник 29 в сборе с крышками, фиксируя его положение и предохраняя от проворачивания скобами 34 крышек. В подсобранный узел закладывают смазку 1-13с и вставляют распорные втулки 26.
|
|
При общей сборке карданных валов 10 и 25 в отверстия вилки 9 вставляют шипы крестовины 6 в сборе с вилкой / и подшипником 5 с сальниками в сборе. Затем аналогично собирают вилку 9 другого конца карданного вала со скользящей вилкой 24 в сборе с крестовиной.
После сборки карданные валы подвергают динамической балансировке на станке (рис. 176). Один конец вала соединяют фланцем-в ил кой с фланцем передней ведущей балки 3, а другой конец опорной шейки скользящей вилки — со шлице-вой втулкой задней бабки /. Затем проверяют легкость вращения карданного вала и фиксатором 7 закрепляют один конец маятниковой рамы 2 станка. Включив станок, вращают лимб выпрямителя 6 против часовой стрелки и доводят показания милливольтметра 5 до максимального значения.
Показание милливольтметра соответствует определенному значению дисбаланса. Шкала милливольтметра градуирована в граммах уравновешивающего груза. Продолжая вращение лимба 6 выпрямителя против часовой стрелки, доводят показание милливольтметра до нулевого значения и останавливают станок.
|
|
По показанию лимба выпрямителя 6 определяют угол смещения дисбаланса и, поворачивая карданный вал, устанавливают это значение на лимбе 4 промежуточного вала. При этом место приварки балансировочной пластины будет расположено вверху вала, а утяжеленная часть — внизу, в плоскости коррекции. Прикрепив балансировочную пластину тонкой проволокой на расстоянии 10 см от сварного шва, включают станок и проверяют сбалансированность конца карданного вала с пластиной.
9 Зак. 483
242 МЕХАНИЗМЫ ТРАНСМИССИИ, РАМЫ, ПОДВЕСОК, ШИН Н РУЛЕВОГО УПРАВЛЕНИЯ
При значении дисбаланса меньше допустимого балансировочные пластины приваривают к поверхности трубы. Затем, освобождая один и закрепляя другой конец маятниковой рамы фиксатором 7 стойки, осуществляют динамическую балансировку другого конца вала.
После динамической балансировки карданного вала на шейку скользящей вилки 24 (см. рис. 175) устанавливают защитную муфту 22 шлицев, гайку 20 распорной втулки, разрезные шайбы 17 и 19, кольцо 18 сальника, резиновый сальник 16 и разрезную шайбу 15. Кольцо сальника и разрезные шайбы вводят в гнездо распорной гайки втулки. Муфту шлицев закрепляют на шейке скользящей вилки проволокой.
|
|
После предварительной сборки и динамической балансировки промежуточного карданного вала на шейку шлицевой втулки // устанавливают передний отражатель 12 сальника, опору 13 промежуточного вала в сборе напрессовывают до упора в буртик. Затем надевают задний отражатель 14 сальника. После заполнения солидолом шлицевой втулки // подбирают скользящую вилку 24 по шлицевой втулке //, обеспечивая свободное движение и совпадение осей болтов стопорных пластин вилок промежуточного вала и скользящей вилки. Установив в выточку шлицевой втулки разрезную шайбу 15 и резиновое кольцо, навертывают до отказа на ее резьбовой конец гайку 20 распорной втулки и стопорят, отгибая ус заднего отражателя сальника в паз гайки. Защитную муфту 22 шлицев передним концом надевают на гайку распорной втулки и закрепляют хомутом 21 и пружинным кольцом 23.
Для отметки взаимного расположения сбалансированного комплекта карданного вала на трубах и скользящих вилках выбиты стрелки.
§ 51. ВЕДУЩИЙ МОСТ
Картер ведущего моста может иметь различные трещины, износ посадочных мест под подшипники и сальники. При наличии трещин картер бракуют. Нарушенные сварные швы после удаления старой сварки восстанавливают дуговой сваркой. Изношенные посадочные места под подшипники восстанавливают любыми видами наплавки. Постановкой дополнительной ремонтной детали в виде кольца восстанавливают диаметр под уплотнительный сальник при его износе.
Картер главной передачи в зависимости от размеров дефектов бракуют или восстанавливают. Характерными дефектами картеров главной передачи являются износ, трещины и обломы отверстий под подшипник конической и цилиндрической шестерен автомобилей (ЗИЛ и КамАЗ), а также повреждение резьбы под гайку подшипника дифференциала.
Трещины и обломы фланца крепления к картеру заднего моста, распространенные менее чем на половину отверстия под болты крепления, устраняют дуговой сваркой. При любых других обломах картер бракуют.
Изношенные отверстия под роликовый подшипник конической шестерни восстанавливают вибродуговой наплавкой с последующей обработкой до размера по рабочему чертежу. Возможно также восстановление постановкой дополнительной ремонтной детали. В этом случае отверстие растачивают, делая углубление под буртик ремонтной детали в виде втулки. В отверстие запрессовывают втулку с буртиком, подрезают ее торец заподлицо с основным металлом и растачивают отверстие до размера по рабочему чертежу.
Отверстия под гнезда подшипников допускают обработку под два ремонтных размера. Также возможно их восстановление вибродуговой наплавкой или галь-
ВЕДУЩИЙ МОСТ
243
Рис. |
|
177. Приспособление для расточки сферической поверхно сти чашки коробки дифференциала
ваническим натиранием с последующей обработкой до размера по рабочему чертежу.
При повреждении резьбы под гайку подшипника дифференциала резьбовое отверстие растачивают и нарезают ремонтную резьбу либо наращивают слой металла вибродуговой наплавкой с последующей расточкой и нарезанием резьбы в соответствии с рабочим чертежом.
Чашки коробки дифференциала при наличии на них трещин бракуют. К основным восстанавливаемым неисправностям относятся: задиры; риски или неравномерный износ торца под шайбу
шестерни полуоси и сферической поверхности под шайбы; износ отверстий под шайбу шестерни полуоси, под стяжные болты и под шипы крестовины, а также шейки под роликовый подшипник.
При задирах, рисках или износе торца под шайбу шестерни полуоси и сферической поверхности под шайбы эти поверхности обрабатывают под ремонтные размеры, компенсируя изменение размеров при сборке шайбами. Расточку сферической поверхности проводят фасонным резцом при установке чашки в приспособлении (рис. 177) токарного станка по планшайбе /. В посадочное отверстие кольца 2 приспособления чашку 5 устанавливают по шейке под роликовый подшипник. Палец 6 при этом должен войти в одно из отверстий под стяжные болты чашки коробки дифференциала. Под болт 4 подкладывают шайбу 3 и закрепляют чашку.
При износе отверстий под стяжные болты и под шипы крестовины сверлят новые отверстия в промежутке между старыми. Затем отверстия под болты зенкуют с двух сторон, а отверстия под шипы крестовины развертывают до размера по рабочему чертежу.
Износ шейки под роликовый подшипник устраняют железнением, хромированием, вибродуговой наплавкой или раздачей с последующей шлифовкой шейки до размера по рабочему чертежу.
Полуоси ведущих мостов могут иметь следующие основные дефекты: погнутость полуоси или фланца; износ конусных отверстий под разжимные втулки и шлицев по толщине. При наличии обломов или трещин, а также скручивания полуось бракуют. Погнутость полуоси определяют после установки ее в центрах при помощи индикаторной головки. Погнутые полуоси правят на прессе. Фланец полуоси, имеющий торцовое биение, протачивают.
Износ конусных отверстий под разжимные втулки устраняют заваркой, предварительно рассверлив их до большего диаметра, с последующим сверлением сквозного отверстия и его зенковкой до необходимого размера по рабочему чертежу. Изношенные по толщине шлицы восстанавливают наплавкой под слоем флю -са с продольным наложением швов. После протачивания диаметров и фрезерования шлиц выполняют необходимую термообработку и доводочные операции.
Ступицы задних колес при наличии трещин на любых поверхностях, кроме ребер, бракуют. Трещины на ребрах устраняют дуговой сваркой. Износы отверстий под подшипники и наружный сальник устраняют вибродуговой наплавкой или постановкой дополнительной ремонтной детали в виде втулки. Резьбу под шпильки крепления полуоси восстанавливают нарезанием ремонтной резьбы или поста-*
Дата добавления: 2019-01-14; просмотров: 318; Мы поможем в написании вашей работы! |
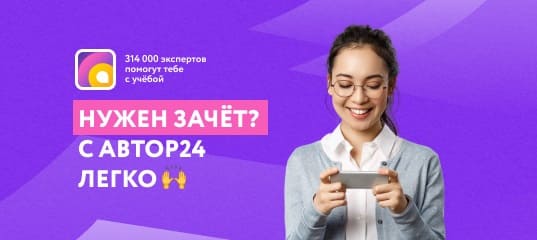
Мы поможем в написании ваших работ!