УЗЛЫ И ПРИБОРЫ СИСТЕМЫ ПИТАНИЯ
229
корпуса устраняют притиркой на плите, припиливанием или шабровкой по краске. Изношенные отверстия под оси развертывают под больший ремонтный размер. В зависимости от конструкции корпуса изношенные отверстия под оси можно восстанавливать рассверливанием, установкой бронзовых втулок с внутренним диаметром отверстия под ось номинального размера.
Сборку карбюратора проводят в последовательности, обратной разборке, с помощью тех же приспособлений, что и разборку.
При сборке карбюратора необходимо следить за сохранностью и правильной установкой прокладок. После окончательной сборки винты крепления заслонок кернят во избежание самоотвертывания.
Дизель
Топливоподкачивающий насос разбирают и ремонтируют только в случае, если он не обеспечивает требуемых характеристик. Разбирают топливоподкачивающий насос в специальном приспособлении.
Следует помнить, что поршень и корпус топливоподкачивающего насоса, а также поршень и цилиндр ручного насоса раскомплектованию не подлежат. Дета-. ли и узлы насоса необходимо рассматривать во взаимосвязи с деталями, с которыми они работают в паре. Детали, имеющие трещины, обломы, срыв резьбы в отверстиях, не ремонтируют. Допускается восстанавливать резьбу в отверстиях под болты крепления топливопроводов с помощью стальных резьбовых ввертышей на эпоксидном клее или спиральных резьбовых вставок.
|
|
Значения зазоров в насосах приведены в табл. 13.
На поршне топливного насоса выработка от штока толкателя не должна превышать 0,25 мм. Клапан насоса с торцовой поверхностью седла должен обеспечивать герметичность соединения.
Особое внимание обращают на состояние узла шток—втулка насоса, так как от величины износа в сопряжении зависит переток топлива в полость кулачкового вала. Зазор в сопряжении проверяют, не извлекая втулки из корпуса насоса, по времени падения давления воздуха от 0,5 до 0,4 МПа в аккумуляторе объемом 30 см3, подключенном через кран к сети сжатого воздуха. Схема установки представлена на рис. 166.
Корпус / насоса устанавливают в приспособление, заполняют аккумулятор 4 сжатым воздухом до давления 0,55 МПа, обеспечивая герметичность. Отключают
Значения зазоров между элементами топливоподкачивающего и ручного насосов, мм
Наименование зазора | Номинальный | Допустимый | Наименование зазора | Номинальный | Допустимый |
Топливоподкачивающий насос Между корпусом и поршнем Между корпусом и толкателем Между осью ролика и толкателем поршня | 0,006...0,03 0,07...0,093 0,025...0,06 | 0,18 0,2 0,15 | Между штоком и втулкой Между роликом толкателя и осью ролика Ручной насос Между цилиндром и поршнем | 0,012...0,014 0,025...0,06 0...0.022 | 0,2 0,05 |
I
|
|
230
ДВИГАТЕЛЬ И ЕГО СИСТЕМЫ
|
Рис. 166. Схема установки испытания пары шток — втулка: / — корпус насоса; 2 — ограничитель перемещения штока; 3 — соединитель для подвода воздуха к корпусу насоса; 4 — воздушный аккумулятор: 5 — манометр; 6—9 — краны; 10 — масловлагоотделитель; / — в атмосферу; // — из системы; /// — к насосу |
аккумулятор от сети сжатого воздуха и фиксируют время, в течение которого произойдет падение давления воздуха в аккумуляторе от 0,5доО,4МПа. Полученное время сравнивают с аналогичным временем, полученным для эталонной прецизионной пары, имеющей зазор в сопряжении 0,012 ... 0,014 мм. Пара подлежит замене или ремонту, если плотность испытуемой пары меньше эталонной. Если узел шток—втулка заменяют, то поверхность резьбы и торец в корпусе клея. Новую втулку штока устанавливают в корпус Очищенные контактирующие поверхности корпуса |
насоса очищают от остатков
насоса на эпоксидном клее.
насоса и втулки обезжиривают бензином или ацетоном перед нанесением клея.
После затяжки втулки штока (момент 10 Н-м) проверяют легкость перемещения
штока в ней. При неудовлетворительной подвижности штока уменьшают момент
|
|
затяжки.
После сборки измеряют подачу насоса. Последовательность проверки топ-ливоподкачивающего насоса подробно изложена выше.
Ручной насос проверяют на стенде на герметичность. Воздух подводят под поршень при давлении 0,2 ... 0,3 МПа в течение 5 ... 6 с предварительным смачиванием подпоршневой полости дизельным топливом.
Форсунки имеют следующие дефекты: поломки и трещины любого размера; засорение и износ сопловых отверстий; заедание иглы и износ ее уплотнительной части; износ сопряженных с пружиной деталей и усадку пружины; износ торца корпуса форсунки; разрушение сетки фильтра в штуцере форсунки; наличие рисок и следов коррозии на торцовых поверхностях сопрягаемых деталей (простав-ка, корпус распылителя, корпус форсунки).
Детали, имеющие поломки и трещины любого размера, ремонту не подлежат.
Перед разборкой и дефектовкой форсунку (см. рис. 51) тщательно промывают в дизельном топливе и насухо вытирают. Разбирать форсунку следует в специальном приспособлении, исключающем поврежденные корпуса. Следует помнить, что корпус и игла распылителя раскомплектованию не подлежат. Предельно допустимый зазор между корпусом и иглой распылителя 0,006 мм. Не следует допускать увеличения хода иглы распылителя, т. е. размера между торцами иглы и распылителя более 0,4 мм. Измерения проводят в приспособлении, оснащенном индикаторной головкой с ценой деления 0,01 мм. Диаметр сопловых отверстий распылителя не должен превышать 0,38 мм.
|
|
Неудовлетворительная работа форсунок вызывается уменьшением давления начала впрыскивания топлива. Это объясняется износом сопряженных с пружиной деталей и усадкой пружины, в связи с чем высота проставки форсунки не должна быть менее8,89 мм при номинальном размере8,9 ...9 мм. При обнаруже-
Дата добавления: 2019-01-14; просмотров: 362; Мы поможем в написании вашей работы! |
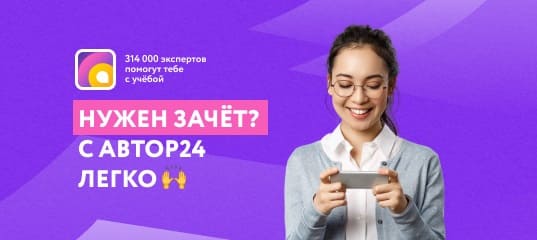
Мы поможем в написании ваших работ!