СБОРКА, ИСПЫТАНИЕ И СДАЧА АВТОМОБИЛЕЙ ИЗ РЕМОНТА 205
изменяют режимы его работы и дорожные условия. При пробеге проверяют также исправность и надежность работы всех систем, механизмов и соединений.
При испытании на стенде дополнительно оценивают основные технические характеристики автомобиля: мощность двигателя; тяговое усилие; расход топлива при различных скоростных и нагрузочных режимах; путь и время разгона до заданной скорости; потери мощности на трение в агрегатах и механизмах; тормозной путь при определенной скорости движения; одновременность и интенсивность действия тормозных механизмов.
После испытания автомобиля пробегом или на стенде все выявленные дефекты устраняют, и автомобиль поступает на окончательную окраску, а затем на склад готовой продукции. По ГОСТ 22581—77* автомобиль, выпускаемый из капитального ремонта, должен отвечать следующим техническим требованиям:
параметры капитально отремонтированных автомобилей и их составных частей (за исключением ресурсных) должны соответствовать установленным для новых автомобилей;
технический ресурс капитально отремонтированного автомобиля должен быть не ниже 80 % ресурса нового автомобиля;
в целях ограничения нагрузочного режима в течение обкаточного периода двигатель автомобиля должен быть оборудован опломбированными ограничительными устройствами.
Сдача автомобилей из ремонта проводится в соответствии с установленной комплектностью. При сдаче из капитального ремонта должна быть приложена следующая документация:
|
|
к автомобилю — паспорт автомобиля, сдававшегося в ремонт с отметкой авторемонтного предприятия о произведенном ремонте, указанием даты выпуска из ремонта, новых номеров шасси и двигателя, паспорт капитально отремонтированных автомобиля и двигателя;
к двигателю — паспорт на отремонтированный двигатель, инструкции по эксплуатации двигателя в обкаточный и гарантийный периоды.
Выдачу из капитального ремонта автомобилей и их составных частей оформляют приемо-сдаточным актом, составленным по специальной форме. При приемке автомобилей и их составных частей представитель заказчика проверяет их внешнее состояние, комплектность, качество сборки и отделки, наличие пломб и т. п. После приема автомобиля из ремонта оформляют приемо-сдаточный акт, который подписывают представители авторемонтного предприятия и заказчика.
В паспорте, который выдают заказчику на каждый отремонтированный автомобиль, фиксируется комплектность, техническое состояние и технические условия, гарантирующие исправную работу автомобиля в течение 12 месяцев со дня выдачи из ремонта. Пробег автомобиля не должен превышать 16 тыс. км, а автобуса 20 тыс. км при условии эксплуатации в соответствии с положением о техническом обслуживании и ремонте подвижного состава автомобильного транспорта и руководством по эксплуатации предприятия-изготовителя.
|
|
Авторемонтное предприятие гарантирует исправную работу отремонтированного автомобиля в целом и всех его составных частей, включая изготовленные или отремонтированные другими предприятиями изделия, кроме шин, аккумуляторов, радиооборудования и электрических ламп.
В течение гарантийного срока все обнаруженные заказчиком неисправности, возникшие по вине авторемонтного предприятия, должны быть устранены в течение трех суток со дня предъявления рекламации.
206
ДВИГАТЕЛЬ И ЕГО СИСТЕМЫ
Контрольные вопросы
1. В чем состоит сущность процесса комплектования деталей?
2. Назовите виды балансировки деталей и узлов.
3. Назовите основные методы обеспечения требуемой точности сборки.
4. Каковы особенности сборки прессовых соединений?
5. Перечислите основные правила сборки резьбовых соединений.
6. В чем состоят особенности сборки шлицевых и шпоночных соединений?
7. Назовите технические требования на сборку соединений с подшипниками качения.
|
|
8. Как осуществляют сборку зубчатых передач?
9. Назовите последовательность сборки автомобильного двигателя.
10. Какова последовательность сборки коробки передач и заднего моста автомобиля?
11. С какой целью выполняют приработку и испытание двигателей после ремонта?
12. Каковы особенности приработки и испытания коробок передач и задних мостов?
13. В чем состоит технологический процесс общей сборки автомобиля?
14. Назовите основные требования, предъявляемые к отремонтированному автомобилю при его испытании.
15. Каков порядок сдачи автомобиля из ремонта?
Глава П. ДВИГАТЕЛЬ И ЕГО СИСТЕМЫ § 43. КРИВОШИПНО-ШАТУННЫИ МЕХАНИЗМ
В кривошинно-шатунном механизме восстановлению подлежат: коленчатый вал, шатуны и маховики.
Восстановление коленчатых валов проводят, если размеры дефектов достигают предельных значений.Основными дефектами коленчатого вала (рис. 141) являются: обломы и трещины /, изгиб 2, износ 7 шатунных и коренных шеек, отверстий 8 и 5 соответственно под болты крепления маховика и под подшипник направляющего конца ведущего вала коробки передач, фланца на торцовой поверхности 4 и по диаметру 3, шпоночных // и маслосгоппых 6 канавок, шеек 10 под шестерню и ступицу шкива, повреждение резьбы 9 под храповик, увеличение длин упорной коренной 12 и шатунных 13 шеек.
|
|
При наличии обломов и трещин, а также при предельном увеличении длины коренной или шатунной шейки вал бракуют. Допустимое увеличение длины упорной коренной шейки компенсируют постановкой упорных шайб ремонтного размера.
Изгиб коленчатого вала (сплошные линии, см. рис. 132) устраняют правкой на прессе в холодном состоянии или наклепом щек.
Рис. 141. Основные дефекты коленчатого вала двигателя
КРИВОШИПНО ШАТУННЫЙ МЕХАНИЗМ
20?
Шатунные и коренные шейки, изношенные в пределах ремонтного размера, шлифуют под ближайший ремонтный размер. Вначале проточкой фасок устраняют повреждения центровых отверстий, затем шлифуют коренные шейки. При шлифовании коренных шеек вал устанавливают в центрах круглошлифовального станка по центровым фаскам, а при шлифовании шатунных шеек — в центросме-сители, совмещая ось вращения шатунной шейки с осью станка. Обработку коленчатого вала начинают со шлифования первой шатунной шейки. При шлифовании последующих шатунных шеек коленчатых валов У-образных двигателей вал поворачивают вокруг оси на необходимый угол, определяемый углом между кривошипами. Все коренные и шатунные шейки шлифуют под один ремонтный размер. Острые кромки фасок масляных каналов притупляют конусным абразивным инструментом, а затем шейки подвергают суперфинишированию.
Если диаметры шатунных или коренных шеек меньше последнего ремонтного размера, то шейки восстанавливают наплавкой под слоем флюса или железне-нием.
Изношенные отверстия 8 (см. рис. 141) под болты развертывают в сборе с маховиком под ремонтный размер, одинаковый для всех отверстий. Изношенное отверстие 5 под подшипник направляющего конца ведущего вала коробки передач восстанавливают постановкой дополнительной ремонтной детали до размера по рабочему чертежу.
Изношенный по торцовой поверхности 4 фланец протачивают до удаления следов износа, уменьшая его биение до допустимых значений и пе допуская до предельной толщины фланца. Износ наружной поверхности 3 фланца по диаметру устраняют накаткой, гальваническим наращиванием или наплавкой с последующей механической обработкой до размера рабочего чертежа.
Изношенные шпоночные // и маслосгонные 6 канавки восстанавливают наплавкой с последующей обработкой до размера чертежа.
При повреждении резьбы 9 под храповик менее двух ниток ее прогоняют гки; размер рабочего чертежа, при срыве двух и более ниток нарезают резьб V ремонтного размера.
После восстановления коленчатого вала проверяют биение средней коренной шейки, посадочного места распределительной шестерни, шейки под сальник, наружного диаметра фланца и отверстия под подшипник, а также радиус кривошипа. Длину первой коренной шейки измеряют специальным приспособлением, базируя его по месту установки шкива коленчатого вала. Размеры коренных и шатунных шеек проверяют предельными скобами.
Восстановление шатунов начинают с проверки' изгиба и скручивания 2 (рис. 142) с использованием индикаторных или оптических устройств. Кроме изгиба и скручивания основными дефектами шатунов являются: износ отверстий в нижней головке 3, в верхней головке под втулку 4 и во втулке 5 верхней головки; уменьшение расстояния / между осями верхней и нижней головок. Шатун и крышку при восстановлении не разукомплектовывают.
Оптическое приспособление для определения изгиба и скручивания снабжено коллиматором 4, излучающим световое пятно с крестообразной тенью 3 (рис. 143). Перед проверкой шатунов определяют точность установки оптической системы с помощью контрольного зеркала 10. Его сдвигают на место зеркала 12, которое крепят к верхней головке шатуна 9. Изображение крестообразной тени 3 с помощью зеркала 5 направляют через отверстие в центре экрана 6 на зеркало 10, которое находится на месте зеркала 12. От зеркала 10 изображение крестообразной тени отражается зеркалом 2 снова на зеркало 10 и от него — в центр экрана
208
ДВИГАТЕЛЬ И-ЕГО СИСТЕМЫ
6. Если центр крестообразной тени не совпадает с центром экрана, положение зеркала 2 регулируют винтами /, добиваясь совпадения центров. Отрегулировав оптическую систему, зеркало 10 передвигают вправо. В верхнюю головку шатуна вставляют держатель с зеркалом 12 и крепят шатун 9 нижней головкой на кронштейн 8, закрепленный на основании 7. Расстояние от центра крестообразной тени 3 до вертикальной линии экрана 6 показывает величину изгиба шатуна, а до горизонтальной линии — скручивания. Шатун правят с помощью рычага 11.
При восстановлении шатунов .предусматривают вначале восстановление геометрических размеров его нижней головки, поверхность которой затем становится базовой при растачивании отверстия во втулке верхней головки шатуна под поршневой палец.
Износ отверстия в нижней головке шатуна устраняют железнением, фрезерованием или шлифованием плоскости разъема шатуна и крышки с последующим растачиванием и хонингованием отверстия до размера рабочего чертежа. При растачивании отверстия в нижней головке шатуна на алмазно-расточном станке базой является шлифованная торцовая поверхность большой головки. После установки шатуна на станке отверстие нижней головки растачивают и снимают фаску. Затем его доводят до требуемых размеров и шероховатости поверхности на верти-кально-хонинговальном станке. В качестве смазочно-охлаждающей жидкости используют смесь керосина (70 % ) и веретенного масла (30 %).
Втулку верхней головки шатуна заменяют новой и растачивают до требуемого диаметра при соответствующей шероховатости поверхности.
После обработки шатуны промывают и продувают сжатым воздухом. Восстановленные шатуны обязательно проверяют. Параметры изгиба, скручивания и расстояние между осями отверстий верхней и нижней головок шатуна измеряют с помощью контрольных приспособлений (см. рис. 143). Диаметры отверстий нижних и верхних головок шатунов измеряют индикаторами-нутромерами и пробками. Более производительными являются пневматические измерительные приборы, основанные на использовании зависимости между размерами отверстия и расходом через него сжатого воздуха. Измерительный прибор регулируют при заданном давлении воздуха с помощью контрольного калибра в виде кольца. При установке
К > И 60 Ш И ПНО - ШАТУННЫЙ МЕХАНИЗМ
209
шатуна на калибр по уровню поплавка в трубке пневматического измерительного прибора определяют диаметр.
Сборку коленчатого вала с маховиком и сцеплением начинают с установки маховика на фланец коленчатого вала и совмещают отверстия в маховике с отверстиями на фланце. Гайки болтов крепления маховика затягивают равномерно крест-накрест, прикладывая заданный момент. Затем индикаторным приспособлением проверяют биение торцовой поверхности маховика относительно оси коленчатого вала. Если биение превышает заданную величину, то узел разукомплектовывают и устанавливают другой маховик. Гайки крепления маховика шплинтуют в обязательном порядке.
В отверстие фланца коленчатого вала запрессовывают подшипник, который должен плотно сидеть в отверстии, а его внутренняя обойма должна легко, без заедания, вращаться от руки. Затем на маховик ставят ведомый и нажимной диски в сборе с кожухом сцепления, центрируют их оправкой по оси коленчатого вала, совмещают отверстия крепления кожуха с отверстиями маховика и завертывают болты с шайбами. Болты крепления кожуха сцепления к маховику затягивают динамометрическим ключом, момент затяжки задан. Затем регулируют высоту рычагов выключения сцепления. Рычаги должны находиться в одной плоскости на необходимом расстоянии от торца маховика. Болты крепления опорных пластин шплинтуют в обязательном порядке.
Собранный с маховиком и сцеплением коленчатый вал балансируют на станке (рис. 144). Для балансировки коленчатый вал 4 в сборе устанавливают на роликовые опоры 3 крайними коренными шейками. Затем надевают технологические балансировочные кольца, масса которых зависит от ремонтного размера шатун-
Д-й
Рис. 144. Станок для динамической балансировки коленчатого вала в сборе с маховиком и
сцеплением:
/ — фиксатор; 2 — дрель; 3 — роликовые опоры; 4 — коленчатый вал; 5 — виброрама; 6 и 8 — лимбы; 7 — муфта; 9 — коллектор; 10 — механический тормоз. Зак. 483
210
ДВИГАТЕЛЬ И ЕГО СИСТЕМЫ
ных шеек коленчатого вала. Закрепив правый конец и освободив левый конец виб-' рорамы 5, включают станок. Вращают лимб 6 коллектора 9 до максимального отклонения стрелки измерительного прибора. Определяют по нему угол расположения балансировочных отверстий для левого конца вала, который устанавливают по лимбу против риски на кронштейне коллектора. Вращая рукой шпиндель станка, совмещают указатель градуированного диска на величину угла, найденного по риске лимба, и устанавливают место сверления балансировочного отверстия.
Для высверливания отверстия в торце маховика используют дрель 2. Глубина отверстия
. 4108 О
Н =--------------- ,
пШ2р
где И — дисбаланс, кг-м; ^ — радиус, на котором сверлят отверстие, м; й — диаметр сверла, м; р — плотность металла, кг/м3, для стали р = 7800 кг/м3.
При балансировке валов отверстия сверлят на расстоянии не менее 20 мм. При необходимости балансируют правый конец вала, предварительно заперев левый конец рамы балансировочного стенда. Балансировать коленчатый вал в сборе с маховиком и сцеплением можно только при определенном значении дисбаланса. При большем значении дисбаланса узел разбирают.
После сверления отверстий у коленчатого вала в сборе с маховиком и сцеплением повторно проверяют его неуравновешенность.
Собранный и отбалансированный коленчатый вал продувают сжатым воздухом для удаления стружки, оставшейся на поверхностях деталей после сверления отверстий в маховике, и снимают технологические балансировочные кольца с шатунных шеек. После устранения неуравновешенности взаимное положение маховика и кожуха сцепления отмечают краской.
ЦИЛИНДРОПОРШНЕВАЯ ГРУППА
Восстановление блоков цилиндров состоит в исключении следующих основных дефектов (рис. 145): трещин и отколов 1\ пробоин 10; износа отверстий 9 под втулки и 6 во втулках под опорные шейки распределительного вала, гнезд 7 вкладышей коренных подшипников, посадочных отверстий 4 и 2 под гильзы, отверстий 5 под толкатели, торцов 8 первого коренного подшипника; повреждении резьбы 3. Для выявления скрытых дефектов блок цилиндров подвергают гидравлическим испытаниям.
Трещины, если они не проходят через поверхность, несущую нагрузку, за- ] варивают или заделывают эпоксидными пастами. Заварку трещин на блоках цилиндров осуществляют способами, описанными выше. Сварной шов зачищают от наплавов металла и окалины заподлицо с плоскостью основного металла шлифовальной машинкой. Пробоины на блоках цилиндров устраняют с помощью эпоксидных составов.
Изношенные отверстия под втулки распределительного вала растачивают под ремонтный размер. При запрессовке ремонтной втулки следят за совпадением отверстий для масла в блоке и втулках. В зависимости от состояния распределительного вала запрессованные втулки растачивают под ремонтный размер или размер по рабочему чертежу. Установив резцы на борштанге расточного станка на необходимый размер, растачивают одновременно все втулки. При этом обеспечивают требуемую шероховатость поверхности. У втулок опорных подшипников распределительного вала следят за точностью диаметра отверстий, отклонением их от
ЦИЛИНДРОПОРШНЕВАЯ ГРУППА
211
круглости, а также за межцентровым расстоянием осей коленчатого и распределительного валов.
Изношенные гнезда вкладышей коренных подшипников коленчатого вала восстанавливают под ремонтный размер или под размер по рабочему чертежу. Снятые крышки коренных подшипников маркируют, а их привалочные плоскости шлифуют или фрезеруют. После установки крышек на место затягивают болты с определенным моментом и растачивают отверстия под коренные вкладыши.
|
Рнс. 145. Основные дефекты блока цилиндров двигателя ЗИЛ-431410 |
Точность обработки и межцентровое расстояние отверстий втулок распределительного вала и коренных подшипников проверяют с помощью приспособления (рис. 146). На скалку 3, вставленную в отверстия коренных опор блока цилиндров, надевают внутреннюю втулку 2 и корпус / приспособления. В корпус / вмонтирован индикатор 4. При точной расточке втулок распределительного вала индикатор 4, касаясь скалки 5, установленной в отверстия втулок, показывает раз-
212
ДбИГАТЁЛЬ И ЕГО СИСТЕМЫ
Вид А
Рис . 146. Приспособление для измерения межцентрового расстояния отверстий коренных подшипников блока цилиндров ., и втулок распределительного вала
мер между осями отверстии под распределительный и коленчатый валы в пределах допустимых отклонений.
Посадочные отверстия поясков под гильзы, имеющие износ выше допустимого, восстанавливают описанными выше методами наращивания металла или постановкой дополнительной ремонтной детали в виде гильзы с последующим растачиванием отверстия. Изношенные отверстия под толкатели развертывают под ремонтный размер, а при большой величине износа восстанавливают постановкой дополнительной ремонтной детали. При запрессовке втулок следят за совпадением отверстий для масла во втулке и блоке. После запрессовки втулки развертывают под размер по рабочему чертежу.
Изношенную торцовую поверхность первой коренной опоры блока цилиндров по длине наплавляют и подвергают механической обработке. Ее можно восстанавливать также эпоксидной смолой. В этом случае механическая обработка не нужна. Поврежденную резьбу восстанавливают установкой ввертыша или заваркой с последующим сверлением отверстия и нарезанием резьбы.
Восстановление гильз цилиндров проводят, если при осмотре на них не обнаружены трещины или сколы и у них отсутствуют скрытые дефекты. Основными дефектами гильз цилиндров (рис. 147) являются: трещины и сколы 4, износы внутренней рабочей поверхности /, а также верхнего 3 и нижнего 2 посадочных поясков в блоке. Для выявления скрытых дефектов гильзу подвергают гидравлическим испытаниям под давлением 0,4 МПа в течение 1...2 мин. На наружной поверхности гильзы не должны быть заметны капли воды.
/ г |
*г~?т;|. >. .^уут! |
Изношенные внутренние поверхности гильзы цилиндров растачивают до ремонтных размеров, а затем хонингуют. Для растачивания гильз цилиндров применяют приспособление (рис. 148, а), которое закрепляют на столе расточного станка. В корпус 5 приспособления вставлена втулка 4, в которой гильзу 3 базируют посадочными поясками. Для предотвращения деформации гильзы при зажиме ее в приспособлении предусмотрены два сферических кольца
ъртт/л штжжж
Дата добавления: 2019-01-14; просмотров: 1531; Мы поможем в написании вашей работы! |
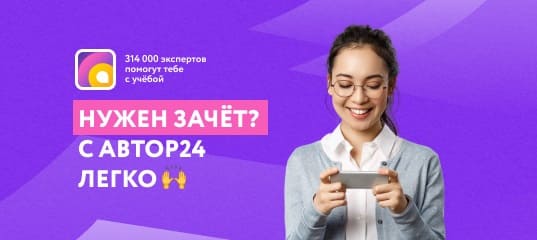
Мы поможем в написании ваших работ!