КОМПЛЕКТОВАНИЕ ДЕТАЛЕЙ. СБОРКА И ИСПЫТАНИЕ АВТОМОБИЛ Ей
Коробку передач собирают из отдельных узлов. На специальных постах собирают следующие основные узлы: ведущий промежуточный и ведомый валы; крышку коробки передач; механизм управления; блок зубчатых колес заднего хода.
При общей сборке узлов коробки передач особое внимание обращают на правильность монтажа подшипниковых узлов, сборку сопряжений, служащих для переключения передач. Кроме того, следят за обеспечением требуемого бокового зазора между зубьями колес и осевых зазоров блока зубчатых колес промежуточного вала, ведомого вала и блокирующих колец синхронизаторов. Передвижные зубчатые колеса ведомого вала и синхронизаторы должны перемещаться вдоль шлицев без заеданий.
Собранные коробки передач подвергают испытанию.
Задний мост также собирают из узлов: картера заднего моста с трубами полуосей, сальниками и пробками; конической шестерни с картером подшипников; дифференциала с цилиндрическим (коническим) зубчатым колесом; конического зубчатого колеса с валом цилиндрической (конической) шестерни, редуктора; ступицы с тормозным барабаном, опорного диска заднего тормоза, регулировочного рычага и колесного цилиндра.
Особое внимание при сборке уделяют конической гипоидной зубчатой передаче. Качество зацепления зубьев определяется боковым зазором между зубьями, уровнем шума, размером и расположением пятна контакта.
При сборке дифференциала коробки сателлитов ориентируют между собой. Проверяют биение тыльной части конического зубчатого колеса, боковой зазор в зацеплении зубьев зубчатой пары полуосей и сателлитов и плавность вращения зубчатой пары полуосей.
|
|
После сборки задний мост прирабатывают и испытывают на специальном стенде.
ПРИРАБОТКА И ИСПЫТАНИЕ АГРЕГАТОВ
Приработка и испытание завершают ремонт агрегатов. Целью приработки является подготовка трущихся поверхностей деталей к восприятию эксплуатационных нагрузок. В процессе приработки происходит выравнивание микро- и макронеровностей на сопряженных поверхностях деталей. Это приводит к снижению давления на рабочих поверхностях деталей и, следовательно, их изнашивания.
Целью испытания агрегатов является выявление возможных дефектов, а также определение технико-экономических характеристик агрегатов в соответствии с техническими условиями на ремонт.
Приработку и испытание двигателей проводят в два этапа. На первом этапе детали двигателя прирабатываются на стенде, а на втором в условиях эксплуатации в течение 1000 км пробега.
Стендовая приработка подразделяется на три этапа: холодную приработку, горячую приработку на режиме холостого хода и приработку под нагрузкой. Для приработки и испытания двигателя 2 применяют специальные стенды (рис. 138), в которых в качестве нагрузочного устройства служит асинхронный электродвигатель 10. Электродвигатель 10 может работать в режиме генератора.
|
|
При холодной приработке коленчатый вал двигателя приводится во вращение от электродвигателя стенда. Холодная приработка позволяет подготовить поверхности трения к восприятию нагрузок, которые имеют место в работающем двигателе. Продолжительность холодной приработки составляет 35... 40 мин. Частоту
ПРИРАБОТКА И ИСПЫТАНИЕ АГРЕГАТОВ
201
Рис. 138. Стенд для приработки и испытания двигателей:
1 — бак с охлаждающей жидкостью; 2 —двигатель; 3 — кран системы охлаждения; 4 — краник перекрытия жидкого топлива; 5 — край газообразного топлива; 6 — предохранительная решетка карданной передачи; 7 — водяной реостат; 8 — рукоятка управления реостатом; 9 — кнопка управления электродвигателем; 10 — электродвигатель; // — тахометр; 12 — пульт; 13 — рычаг коробки передач; 14 — тяга управления дроссельной заслонкой карбюратора; 15 — педаль сцепления; 16 — кран перекрытия воды из водопровода
вращения коленчатого вала 400 ... 1000 мин-1 контролируют по тахометру // пульта 12.
|
|
После холодной приработки двигатель пускают и проводят горячую приработку на режиме холостого хода в течение 30 ... 40 мин при постепенном повышении частоты вращения вала от 1000 до 2000 мин-1. При горячей приработке под нагрузкой, которая создается асинхронным электродвигателем 10, работающим в генераторном режиме при нагрузке на водяной реостат 7, происходит окончательная подготовка всех сопряжений двигателя к восприятию эксплуатационных нагрузок.
В процессе приработки под нагрузкой скоростной режим работы двигателя постепенно повышается до близкого к эксплуатационному режиму. Продолжительность горячей приработки составляет 50 ... 60 мин. После окончания процесса приработки в течение 5 ... 10 мин проводится приемка отремонтированного двигателя.
В процессе приработки и испытания двигателя выявляют дефекты, подлежащие устранению, измеряют давление в смазочной системе, величину прорыва газов в картер и другие параметры, характеризующие качество ремонта. Измеряют одну точку внешней характеристики двигателя: при определенной частоте вращения определяют развиваемый момент.
В процессе испытания двигателя необходимо поддерживать температуру охлаждающей воды, поступающей из бака /, и масла в заданных пределах. С этой целью испытательные стенды оборудуют устройствами для автоматического регулирования температурного режима двигателя.
|
|
202 КОМПЛЕКТОВАНИЕ ДЕТАЛЕЙ, СБОРКА И ИСПЫТАНИЕ АВТОМОБИЛЕЙ |
Рис. 139. Стенл для испытания коробок передач с электрическим тормозом
Приработка и испытание коробок передач заключаются в проверке работы зубчатых пар на всех передачах, легкости переключения передач и отсутствии самопроизвольного выключения зубчатой пары. При испытании контролируют также уровень шума зубчатой пары (он должен быть равномерным, без стуков), температуру нагрепа смазочного материала (не выше 70°С) и герметичность уплотнений.
Испытание проводят на всех передачах без нагрузки, а затем при постоянной нагрузке с частотой вращения ведущего вала 1000 ... 1400 мин-1.
Для испытания коробок передач используют стенды с электрическим тормозом или с замкнутым силовым контуром. В первом типе стендов в качестве нагрузочного устройства используется асинхронный электродвигатель 5 (рис. 139). Электродвигатель / через муфту 2 и вал с промежуточной опорой приводит во вращение ведущий вал испытуемой коробки передач 3. Ведомый вал испытуемой коробки через карданный вал соединен с ведомым валом коробки передач 4 стенда. Коробка передач стенда служит для изменения частоты вращения вала ротора асинхронного двигателя, который выполняет роль тормоза. Асинхронный электродвигатель 5 установлен балансирно на двух опорах и соединен рычагом с
Рис. 140. Схема стенда для испытания коробок передач с замкнутым силовым контуром:
' —испытуемая коробка передач; 2 — коробка передач стенда; 3 — правый редуктор; 4 — торсиои; 5--указатель величины закручивания торсиона; 6 — рукоятка; 7 — механизм закручивания торсио-
На; 5 - левый редуктор
Дата добавления: 2019-01-14; просмотров: 676; Мы поможем в написании вашей работы! |
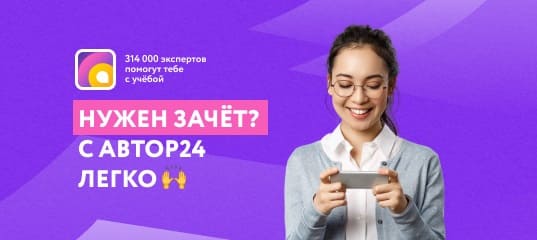
Мы поможем в написании ваших работ!