КОМПЛЕКТОВАНИЕ ДЕТАЛЕЙ, СБОРКА И ИСПЫТАНИЕ АВТОМОБИЛЕЙ
стия конусной разверткой или притиркой поверхностей пастой. После притирки поверхности должны быть ровными и иметь матовый цвет. Чтобы конусное соединение работало надежно, оно должно собираться с натягом.
Резьбовые соединения являются самыми распространенными и составляют около 1/3 общего числа соединений деталей.
При сборке резьбовых соединений выполняют следующие требования:
обеспечивают соосность болтов (шпилек) и резьбовых отверстий и необходимую плотность посадки в резьбе;
исключают перекосы торцов гайки или головки болта относительно поверхности сопрягаемой детали, так как перекосы являются основной причиной обрыва болтов и шпилек;
строго соблюдают порядок и постоянство усилия затяжки группы гаек крепления деталей.
Шлицевые соединения в автомобилях могут быть прямобочными, эвольвент-ными и треугольными. Наибольшее распространение получили прямобочные шлицевые соединения, при сборке которых центрирование охватывающей детали может быть выполнено по наружному диаметру выступов охватываемой детали (вала), по внутреннему диаметру впадин вала и по боковым сторонам шлиц.
При центрировании детали по наружному диаметру выступов вала последний шлифуют по наружному диаметру шлиц, а отверстие охватывающей детали протягивают. При центрировании детали по внутреннему диаметру впадин вала шлифуют отверстие в охватывающей детали. Это шлицевое соединение наименее технологично и поэтому не экономично. Шлнцевое соединение при центрировании детали по боковым сторонам шлиц применяют только в том случае, если на валу более десяти шлицев.
|
|
При механической обработке не всегда удается обеспечить точность сопрягаемых поверхностей. При сборке приходится подбирать по шлицам вала охватываемую деталь (например, шестерню).
После сборки шлицевого соединения нужно проверить детали на биение при помощи индикатора, установив вал в центрах. В случае подвижной посадки шестерни проверяют ее перемещение по шлицам вала. Оно должно быть свободным, без заеданий и боковой качки.
Шпоночные соединения двух видов используют в автомобилях: с призматической и сегментной шпонкой.
При сборке шпоночных соединений особое внимание необходимо обратить на точность подгонки шпонок по боковым поверхностям и зазору по наружной поверхности. При неточной подгонке возрастает давление в шпоночном соединении, что приводит к смятию боковых сторон шпонок и шпоночных пазов в деталях. В результате в шпоночном соединении возникает зазор, который разрушает соединение.
Сборку соединений с подшипниками качения необходимо проводить с соблюдением следующих правил.
|
|
В сборочном узле с вращающимся валом и неподвижным корпусом внутреннее кольцо подшипника должно иметь посадку с натягом, а наружное — с зазором. При неподвижном вале и вращающемся корпусе внутреннее кольцо устанавливают с зазором, а наружное — с натягом. Зазор необходим для удобства демонтажа подшипника и возможности провертывания кольца, что обеспечивает более ровный износ кольца и посадочной поверхности детали.
При запрессовке подшипника качения размер его колец изменяется: диаметр внутреннего кольца увеличивается, а наружного уменьшается. Эти изменения при-
СБОРКА УЗЛОВ И АГРЕГАТОВ
!97
водят к уменьшению зазора в подшипнике, а следовательно, к повышению износа колец и шариков.
При установке в узле двух или нескольких подшипников необходимо обеспечить самоцентрирование неподвижных колец в радиальном и осевом направлениях. Это позволит компенсировать возможные неточности обработки, сборки и температурные деформации деталей. Несоблюдение этого правила может привести к перекосам подшипников и заклиниванию шариков (роликов).
При запрессовке подшипников необходимо пользоваться оправками и следить, чтобы усилие запрессовки передавалось на запрессовываемое кольцо.
|
|
Регулировку радиального зазора в коническом роликовом подшипнике осуществляют смещением наружного или внутреннего кольца в осевом направлении регулировочным винтом или гайкой или подбором соответствующего комплекта прокладок. Срок службы подшипников качения в значительной степени зависит от их смазывания и степени предохранения от грязи и пыли. После сборки подшипников устанавливают сальники и прокладки, задерживающие смазочный материал и предохраняющие подшипник от попадания в рабочую зону пыли и влаги. Неправильно установленный зазор в коническом роликовом подшипнике может вызвать преждевременный его износ.
Зубчатые передачи с цилиндрической зубчатой парой после установки колес на валы проверяют. Правильность зацепления определяют по боковому зазору и пятну контакта. Боковой зазор измеряют при помощи индикаторного приспособления путем поворота на некоторый угол одного зубчатого колеса при неподвижном другом. Боковой зазор должен соответствовать требованиям технических условий на сборку сопряжения. Расположение пятна контакта проверяют по отпечатку краски.
|
|
Правильность сборки передач с конической или- гипоидной зубчатой парой оценивают по пятну контакта зубьев, зазору и уровню шума.
Правильность расположения пятна контакта достигается путем взаимного перемещения зубчатых колес вдоль оси вращения. Боковой зазор измеряют с помощью индикаторного приспособления, которое закрепляют на картере. Регулируют зазор перемещением зубчатых колес и установкой прокладок. Уровень шума проверяют на стенде, он не должен превышать 50 ... 70 дБ.
СБОРКА УЗЛОВ И АГРЕГАТОВ
Двигатель собирают из узлов. Перед общей сборкой двигателя собирают основные его узлы: поршень с шатуном; головку цилиндров; коленчатый вал с маховиком и сцеплением; водяной насос; масляный фильтр; насос-форсунки; топливный насос; масляный насос и др.
Общую сборку двигателя проводят на поворотном стенде. На стенд устанавливают предварительно промытый блок цилиндров в сборе с картером сцепления и гильзами. Сняв крышки коренных подшипников, в них и в гнезда блока вставляют вкладыши. Смазав вкладыши, в блок цилиндров укладывают коленчатый вал в сборе с маховиком, сцеплением, зубчатым колесом и упорными шайбами.
Осевой зазор между торцом коренной шейки коленчатого вала и упорной шайбой регулируют путем подбора шайбы по толщине. Этот зазор должен составлять 0,075 ... 0,285 мм. Болты крышек коренных подшипников затягивают в определенной последовательности динамометрическим ключом, момент затяжки 110 ... 130 Н- м (для карбюраторных двигателей). После этого коленчатый вал должен свободно проворачиваться за маховик, момент не должен превышать ПО Н-м. Тугое
148
Дата добавления: 2019-01-14; просмотров: 392; Мы поможем в написании вашей работы! |
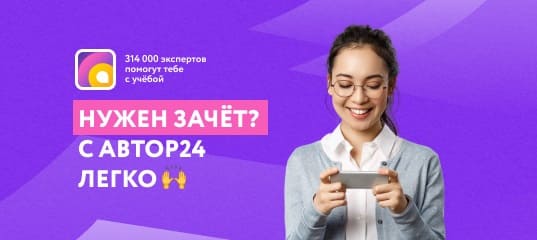
Мы поможем в написании ваших работ!