СПОСОБЫ ВОССТАНОВЛЕНИЯ ДЕТАЛЕЙ
|
Рис . 12$. Распылительная головка аппарата для газопламенного напыления :
/ — смесительная камера ; 2 — канал подачи кислорода ; :1 ~ проволока ; 4 — направляющая втулка ;
5 — канал гюдачн ацетилена ; 6 — канал подачи воздуха : 7 — ацетиленокнслородное пламя ; в —
газометаллнческая струя ; й — поверхность детали
высокая износостойкость покрытия; простота технологического процесса и применяемого оборудования; возможность нанесения покрытий толщиной 0,1 ... 10 мм и более из любых металлов и сплавов. К недостаткам процесса следует отнести пониженную механическую прочность покрытия и сравнительно невысокую прочность сцепления его с поверхностью детали.
В зависимости от вида энергии, используемой в аппаратах для напыления, различают следующие способы напыления: газопламенное, электродуговое, высокочастотное, детонационное и плазменное.
Газопламенное напыление осуществляют при помощи специальных аппаратов. В них металл расплавляется .в ацетиленокислородном пламени 7 и распыли-вается струей сжатого воздуха на поверхность 9 (рис. 123). Напыляемый материал в виде проволоки 3 подается через центральное отверстие направляющей втулки 4 горелки и в зоне пламени 7 с наиболее высокой температурой расплавляется. Проволока подается с постоянной скоростью роликами, приводимыми в движение встроенной в аппарат воздушной турбинкой через червячный редуктор.
|
|
Преимуществами газопламенного напыления являются: небольшое окисление металла; мелкое его распыливание; достаточно высокая прочность покрытия. К недостаткам следует отнести сравнительно невысокую производительность процесса (2 ... 4 кг/ч).
Электродуговое напыление проводится аппаратами, в которых металл плавится электрической дугой, горящей между двумя проволоками 5, а распыливает-ся струей сжатого воздуха 6, подаваемого через сопло 3 (рис. 124).
Основным преимуществом электродугового напыления являются высокая производительность процесса (3...14 кг/ч), простота применяемого оборудования, а также небольшие эксплуатационные затраты. Недостатки электродугового напыления — повышенное окисление металла, значительное выгорание легирующих элементов и пониженная плотность покрытия.
Рис. 124. Схема электродугового напыления:
' — поверхность детали ; 2 —направляющий наконечник : 3 — воздушное сопло ; 4 — ролики механизма подачн ; 5 —проволока ; 6 — окатый воздух
НАПЫЛЕНИЕ МЕТАЛЛА
183
Рис. 125. Распылительная головка аппарата вы- Рнс. 126. Схема детонационного напыления:
сокочастотного напыления: /-электрическая свеча; 2 — кислород: 3 - азот;
|
|
/ — поверхность детали; 2 — газометаллическая 4 — металлический порошок: 5 — ствол; 6 — напы-
струя: 3 — концентратор тока; 4— индуктор, ох- ленный металл; 7 - камера взрыва; 8 — ацетилен
лаждаемый водой; 5 — воздушный канал; 6 — проволока; 7 — ролики механизма подачи; * — направляющая втулка
Высокочастотное напыление основано на использовании принципа индукционного нагрева при плавлении исходного материала покрытия (проволоки). Расплавленный металл напыляется на поверхность 1 детали струей сжатого воздуха. Головка высокочастотного аппарата для напыления (рис. 125) имеет индуктор 4 с электроснабжением от генератора тока высокой частоты и концентратор 3 тока, который обеспечивает плавление проволоки на небольшом участке ее длины.
Преимуществами высокочастотного напыления являются небольшое окисление металла благодаря возможности регулирования температуры его нагрева и достаточно высокая механическая прочность покрытия. К числу недостатков следует отнести сравнительно невысокую производительность процесса, а также сложность и высокую стоимость применяемого оборудования.
Детонационное напыление основано на взрыве смеси газов ацетилена 8 и кислорода 2 (рис. 126).
|
|
При напылении металла в камеру охлаждаемого водой ствола аппарата для напыления подаются в определенном соотношении ацетилен 8 и кислород .2. Струей азота 3 вводится напыляемый порошок 4 с частицами размером 50 ... 100 мкм. Газовую смесь поджигают электрической свечой /. Взрывная волна сообщает частичкам порошка высокую скорость, которая на расстоянии 75 мм от среза ствола достигает 800 м/с.
При ударе о деталь кинетическая энергия порошка переходит в тепловую. Частицы порошка разогреваются до 4000 °С.
После нанесения каждой дозы порошка ствол аппарата продувают азотом для удаления продуктов сгорания. Этот процесс повторяется автоматически с частотой 3—4 раза в секунду. За один цикл на поверхность детали наносится слой металла толщиной до 6 мкм.
Преимуществами этого способа напыления являются: большая производительность процесса (при диаметре ствола 20 ... 25 мм), за 15 с можно нанести покрытие толщиной до 0,3 мм на площади до 5 см2; высокая прочность сцепления покрытия с поверхностью детали; температура на поверхности детали не превышает 200 °С.
К недостаткам процесса следует отнести высокий уровень шума (до 140 дБ), а следовательно, необходимость в специальной звукоизолирующей камере.
|
|
Плазменное напыление — это такой способ нанесения металлического покрытия, при котором для распыливания и переноса металла на поверхность детали используются тепловые и динамические свойства плазменной струи.
184
Дата добавления: 2019-01-14; просмотров: 320; Мы поможем в написании вашей работы! |
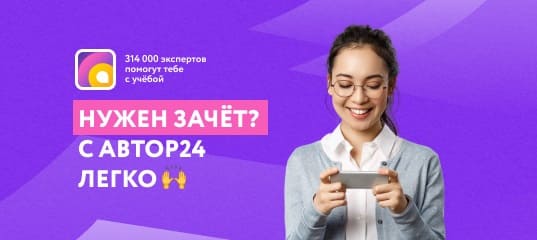
Мы поможем в написании ваших работ!