СПОСОБЫ ВОССТАНОВЛЕНИЯ ДЕТАЛЕЙ
|
Рис. 127. Схема плазмотрона для напыления металлического порошка:
/ — порошковый дозатор; 2 — катод; 3 — изоляционная прокладка; 4 — анод (сопло); 5 — азот; 6 — поверхность детали; 7 — охлаждающая вода; 8 — плазмообразующнй газ
В качестве напыляемого материала исполь
зуется металлический порошок, который вво
дится в сопло плазмотрона из дозатора /, опре
деляющего расход порошка в единицу времени
■ им I 5 (рис. 127). Попадая в струю плазмы, металли-
[| ческий порошок расплавляется и, увлекаемый
Щ скоростным напором струи, наносится на по-
до / верхность 6 детали.
&^Жм&: Напыление проводится при следующем ре-
жиме: сила тока 350 ... 400 А, напряжение 60 ... 70 В, расход плазмообразующего газа 30 ... 35 л/мин, расход порошка 5 ... 8 кг/ч, расстояние от поверхности детали 125 ... 150 мм.
Этот способ напыления является наиболее перспективным. К его преимуществам следует отнести: высокую производительность процесса (до 12 кг ч напыляемого металла); высокую прочность сцепления покрытия с поверхностью детали (до 50 МПа); полную автоматизацию управления процессом; возможность нанесения покрытий из любых металлов и сплавов.
Технологический процесс восстановления деталей напылением включает в себя три основные операции: подготовку поверхности детали к нанесению покрытия; напыление; обработку деталей после напыления. Перед напылением деталь проходит дробеструйную обработку, которая придает поверхности детали наибольшую шероховатость для повышения прочности сцепления покрытия с деталью.
|
|
Нанесение покрытия на поверхность деталей осуществляют на переоборудованных токарных станках или в специальных камерах. Детали устанавливают в патроне станка, а аппарат для напыления на его суппорт. После нанесения покрытия детали медленно охлаждают до температуры окружающей среды, а затем обрабатывают до требуемого размера.
НАНЕСЕНИЕ ГАЛЬВАНИЧЕСКИХ И ХИМИЧЕСКИХ ПОКРЫТИЙ
Гальванические и химические покрытия наносят для компенсации износа поверхности детали, а также как антикоррозионные или декоративные покрытия. Из гальванических способов наиболее широко применяют хромирование, желез-нение, никелирование, цинкование и меднение, из химических — оксидирование и фосфатирование.
Гальванические покрытия получают из электролитов, в качестве которых служат водные растворы солей тех металлов, которые необходимо нанести на детали. Катодом при этом служит деталь, а анодом — металлическая пластина. При прохождении тока через электролит на катоде (детали) будет осаждаться металл, а анод будет растворяться.
|
|
Технологический процесс нанесения покрытий на детали заключается в подготовке деталей к нанесению покрытия, нанесении покрытия и обработке деталей после покрытия.
НАНЕСЕНИЕ ГАЛЬВАНИЧЕСКИХ И ХИМИЧЕСКИХ ПОКРЫТИИ
185
Подготовка деталей к нанесению покрытия включает следующие операции:
механическую обработку с целью придания поверхностям детали правильной геометрической формы;
очистку деталей от окислов путем обработки полировальными кругами с пастой;
предварительное обезжиривание деталей растворителями;
монтаж деталей на подвесное приспособление для последующего погружения их в ванну с электролитом и обеспечения надежного электрического контакта с токоподводящей штангой;
изоляцию поверхностей детали, которые не подлежат покрытию кислотостойкими материалами (лаком, пленками и т.п.);
обезжиривание наращиваемых поверхностей электрохимической обработкой в щелочных растворах или протиркой венской известью;
промывку деталей в горячей и холодной воде с целью удаления щелочи и контроля качества обезжиривания (вода должна смачивать обезжиренную поверхность);
активацию (анодную обработку) поверхности детали с целью удаления тончайших окисных пленок. Перед хромированием активацию производят в ванне для хромирования. Детали выдерживают под током на аноде 30 ... 40 с, а затем переключают на катод для наращивания металла. При железнении активацию производят в ванне с 30%-ным раствором серной кислоты, затем промывают в холодной и горячей воде.
|
|
После активации детали металл наращивают в гальванических ваннах.
Обработка деталей после нанесения покрытия включает следующие операции:
промывку деталей в холодной и горячей воде от остатков электролита;
нейтрализацию в содовом растворе;
демонтаж с подвесного приспособления;
удаление изоляции;
механическую обработку до требуемого размера.
Хромирование деталей проводят в электролите, который представляет собой водный раствор хромового ангидрида и серной кислоты. Анодом при этом служат пластины из свинца.Концентрация хромового ангидрида в электролите может изменяться в пределах 150 ... 400 г/л, а концентрация серной кислоты должна быть в 100 раз меньше.
Режим хромирования определяется двумя параметрами — плотностью йк тока и температурой ^электролита. Изменяя соотношение этих параметров, можно получить три вида хромовых покрытий, отличающихся своими свойствами: матовые (серые); блестящие и молочные (зоны /—3, рис. 128).
|
|
Блестящие хромовые покрытия имеют высокую твердость и износостойкость, а также красивый внешний вид. Молочные покрытия имеют небольшую твердость, пластичны, обладают высокой износостойкостью и антикоррозионными свойствами. Матовые покрытия отличаются высокой твердостью и хрупкостью, но имеют пониженную износостойкость.
Хромирование получило широкое применение при восстановлении деталей: для компенсации износа деталей; в качестве антикоррозионного и декоративного покрытия. Хромовое покрытие получается высокой твердости и износостойкости, которая в 2—3 раза превышает износостойкость закаленной стали 45.
К числу недостатков хромирования следует отнести: сравнительно низкую производительность процесса (не более 0,03 м,м/ч) вследствие малых значений электрохимического эквивалента 10,324 г/(А-ч)] и выхода металла по току (12 ...
186
Дата добавления: 2019-01-14; просмотров: 325; Мы поможем в написании вашей работы! |
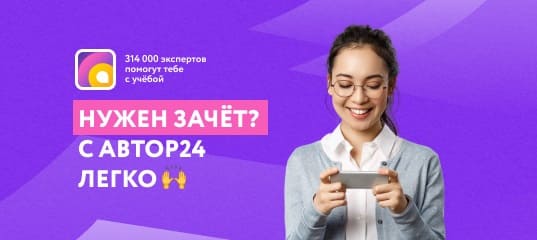
Мы поможем в написании ваших работ!