ТЕХНИЧЕСКОЕ НОРМИРОВАНИЕ СТАНОЧНЫХ РАБОТ
К станочным часто встречающимся на авторемонтных предприятиях работам относятся: токарные, сверлильные, фрезерные и шлифовальные. Для всех станочных работ техническая норма времени:
где tш.к – штучно-калькуляционное время;
t0 – основное (машинное) время – расчетом на основании рекомендуемых режимов обработки или данных для их определения и расчетных данных, вытекающих из размеров обрабатываемых деталей;
t в.у – вспомогательное время на установку и снятие детали, мин;
tв.п – вспомогательное время, связанное с переходом;
t о.р.м – время обслуживания рабочего места;
T п.з – подготовительно-заключительное время, мин;
Все нормы времени, кроме основного, при нормирования станочных работ принимаются из нормативных таблиц.
Основное (машинное) время t0 для всех видов обработки определяется из формулы:
где l – длина обрабатываемой поверхности, мм;
у - величина врезания и выхода инструмента;
n – частота вращения детали, вытекает из скорости резания, об/мин;
S – подача на один оборот детали, мм/об;
i – число ходов.
Значения величины у, V и S определяют для каждого вида обработки по методикам, изложенным ниже.
Определение элементов технической нормы времени
Для токарных работ
Величина врезания и выход резца:
y = y 1 + y 2 + y 3,
где y 1 – величина врезания резца, равная мм;
t – глубина резания, мм;
φ – главный угол резца в плане, градус;
|
|
y 2 – перебег резца при обтачивании на проход (y 2 = 2-3 мм);
y 3 – взятие пробной стружки (y 3 = 2-3 мм).
Глубину резания выбирают исходя из того, чтобы весь припуск снять за один проход, если не надо оставлять часть его на чистовую обработку. Глубиной резания при прорезании канавок или отрезании является ширина резца b =0,6 d0,5 , где d - диаметр отрезаемой детали.
При нарезании резьбы глубина резания определяется числом проходов, которое равно 6-9.
Подачи выбирают по нормативам согласно табл. IV.3.47-IV.3.53. При нарезании резьбы резцом подача равняется шагу резьбы.
Скорость резания определяется по эмпирическим зависимостям
где Сυ – коэффициент, зависящий от условий работы и механических качеств обрабатываемого материала и металла инструмента;
К – поправочный коэффициент, характеризующий конкретные условия работы;
t – глубина резания, мм;
S – подача, мм/об.
Поправочные коэффициенты на скорость резания применяются в зависимости от обрабатываемого материала, стойкости резца, марки твердого сплава, главного угла в плане резца φ, при растачивании, при обтачивании и подрезании торцовых поверхностей (табл. IV.3.54-IV.3.55).
При нарезании резьбы резцами в упор расчет скорости резания производится по формуле
|
|
где d – внешний диаметр резьбы, мм;
f к – размер проточки для выхода резца, мм;
τ – время на отвод резца и на переключение на обратный ход, мин; τ = 0,03-0,04 мин;
S – шаг резьбы, мм.
После определения скорости резания рассчитывают частоту вращения шпинделя и основное время на точение. Подготовительно-заключительное время, вспомогательное время и время обслуживания рабочего места принимают по нормативным табл. IV.3.56-IV.3.62.
Таблица IV.3.47
Подачи при грубом продольном обтачивании проходными резцами
при глубине резания до 5 мм, мм/об
Диаметр обрабатываемой детали d , мм | Подача | Диаметр обрабатываемой детали d , мм | Подача | Диаметр обрабатываемой детали d , мм | Подача |
10 – 18 18 – 30 | До 0,25 0,20 – 0,50 | 30 – 50 50 – 80 | 0,40 – 0,80 0,60 – 1,20 | 80 – 100 100 – 180 | 1,00 – 1,60 1,40 – 2,00 |
Примечание. Большие значения подач следует брать при обработке мягких сталей при работе в центрах соотношением < 6 или в патроне при
< 2; меньшие – при обработке твердой стали и чугуна. При обтачивании закаленных сталей рекомендуются следующие значения подач; при твердости HRC 49 – 0,1 – 0,3 мм/об и HRC 58 – 0,05 –0,15 мм/об.
|
|
Таблица IV.3.48
Подачи при получистом продольном обтачивании незакаленных сталей, мм/об
Класс шероховатости поверхности | Радиус при вершине резца, мм | Подача | Класс шероховатости поверхности | Радиус при вершине резца, мм | Подача | Класс шероховатости поверхности | Радиус при вершине резца, мм | Подача |
4 | 0,5 1,0 2,0 | 0,54 – 0,46 0,65 – 0,57 0,69 – 0,67 | 5 | 0,5 1,0 2,0 | 0,29 – 0,23 0,40 – 0,31 0,52 – 0,44 | 6 | 0,5 1,0 2,0 | 0,15 – 0,11 0,21 – 0,16 0,28 – 0,21 |
Таблица IV.3.49
Подачи при грубом растачивании отверстий проходными расточными резцами, мм/об
Глубина резания t, мм | Диаметр круглого сечения, резца, мм | |||||
10 | 12 | 16 | 20 | 25 | 30 | |
Вылет резца, мм | ||||||
50 | 60 | 80 | 100 | 125 | 150 | |
2 3 | Сталь, стальное литье и алюминиевые сплавы | |||||
0,08 – | 0,10 0,08 | 0,8 – 0,20 0,12 | 0,15 – 0,40 0,10 – 0,25 | 0,25 – 0,70 0,15 – 0,40 | 0,50 – 1,00 1,20 – 0,50 | |
2 3 | Чугуны и медные сплавы | |||||
0,08 – 0,12 < 0.08 | 0,12 – 0,2 0,8 – 0,12 | 0,25 – 0,40 0,15 – 0,25 | 0,50 – 0,80 0,30 – 0,50 | 0,90 – 1,5 0,50 – 1,8 | – 0,9 – 0,70 |
Примечание. Большие значения подач принимаются при обработке мягких металлов, меньшие – для твердых.
Таблица IV.3.50
Подачи при получистовом растачивании отверстий, мм/об
Глубина резания t, мм | Класс шероховатости поверхности
| Диаметр растачиваемого отверстия, мм | ||||||
До 30 | 31 – 50 | 51 - 80 | 81 – 120 | 121 – 180 | ||||
До 2 | 4 5 | 0,04 – 0,08 | 0,06 – 0,1 | 0,08 – 0,13 | 0,10 – 0,15 | 0,12 – 0,18 |
Примечание. Меньшие значения подач принимаются при обработке стали и стального литья, большие – при обработке чугунов и при малых глубинах резания.
Таблица IV.3.51
Подачи при глубоком торцевом обтачивании и подрезании проходными отогнутыми и подрезными резцами на токарных станках, мм/об
Диаметр обрабатываемой детали d , мм | Глубина резания t ,мм | Диаметр обрабатываемой детали d , мм | Глубина резания t ,мм | ||
2 | 3 | 2 | 3 | ||
Подача | Подача | ||||
10 – 18 19 – 30 31 - 50 | 0,18 – 0,30 0,25 – 45 0,90 – 0,80 | 0,15 – 0,25 0,20 – 0,35 0,35 – 0,70 | 51 – 80 81 – 120 121 - 180 | 0,50 – 1,00 0,80 – 1,20 0,90 – 1,30 | 0,45 – 0,90 0,70 – 1,10 0,80 – 1,20 |
Таблица IV.3.52
Подачи при получистовом торцевом обтачивании и подрезании проходными,
отогнутыми и подрезными резцами на токарных станках, мм/об
Глубина резания t, мм | Класс шероховатости поверхности | Диаметр обрабатываемой детали d , мм | ||||
До 30 | 31 - 50 | 51 - 80 | 81 - 120 | 121 – 180 | ||
До 2 | 4 | 0,08 – 0,13 | 0,10 – 0,15 | 0,13 – 0,2 | 0,18 – 0,25 | 0,20 – 0,30 |
Примечание. Меньшие значения подач принимаются при обработке стали и стального литья, большие – при обработке чугунов и при малых глубинах резания.
Таблица IV.3.53
Подачи при прорезании канавок и отрезании, мм/об
Диаметр обрабатываемой детали d , мм | Ширина резца, мм | Сталь и стальное литье | Чугун | |||
Предел прочности σ B, кг/мм2 | Твердость HB | |||||
50 | 51 - 80 | 81 - 120 | До 180 | 181 – 260 | ||
До 18 19 – 30 31 – 50 51 – 80 81 - 120 | 2 3 3 – 4 4 – 5 5 – 7 | 0,07 – 0,09 0,09 – 0,11 0,11 – 0,13 0,13 – 0,16 0,16 – 0,18 | 0,05 – 0,07 0,07 – 0,09 0,09 – 0,11 0,11 – 0,13 0,13 – 0,15 | 0,04 – 0,06 0,06 – 0,07 0,07 – 0,09 0,09 – 0,11 0,11 – 0,13 | 0,09 – 0,12 0,12 – 0,15 0,15 – 0,18 0,18 – 0,22 0,22 – 0,25 | 0,07 – 0,10 0,10 – 0,12 0,12 – 0,15 0,15 – 0,18 0,18 – 0,20 |
Примечания. 1. Большие значения подач следует принимать для больших диаметров и мягких металлов, меньшие – для меньших диаметров и твердых металлов.
2. При требовании шероховатостей поверхности классов 4–6 и при работе с ручной подачей табличные значения подач следует уменьшать на 30–40%.
По мере углубления резца к центру приблизительно на 0,5 радиуса обрабатываемой детали следует подачу уменьшать до 0,5 первоначальной величины для предотвращения отжима отрезаемой детали.
Таблица IV.3.54
Значения коэффициента Сυ и показателей степени xυ и yυ
Материал резца и его марка | Обрабатываемый металл и его механические свойства | Характер обработки | Сυ | xυ | yυ |
Твердый сплав Т15К6 Твердый сплав Т15К6 | Сталь углеродистая, стальное литье σВ = 75 кгс/мм2 (без охлаждения) Чугун серый 190 HB | Получистовая S≤0,3 мм Грубая S>0,3 мм Получистовая S≤0,4 мм Грубая S>0,4 мм | 170 141 77 68 | 0,18 0,18 0,13 0,20 | 0,20 0,35 0,20 0,40 |
Таблица IV.3.55
Поправочные коэффициенты на скорость резания, Кр
В зависимости от обрабатываемого материала
Наименование обрабатываемого материала | Механические качества | Кр | |
Твердость HB | Прочность стали σВ, кгс/мм2 | ||
Углеродистые, легированные стали и стальное литье | 116 – 146 146 – 174 174 – 203 203 – 230 230 – 260 260 – 288 288 – 317 | 40 – 50 50 – 60 60 – 70 70 – 80 80 – 90 90 – 100 100 – 110 | 2,15 1,60 1,25 1,00 0,84 0,73 0,62 |
Серый чугун и медные сплавы | 140 – 160 160 – 180 180 – 200 200 – 220 220 – 240 240 – 260 | – – – – – – | 1,50 1,20 1,00 0,85 0,72 0,63 |
В зависимости от стойкости резца Т
Обрабатываемый материал | Стойкость резца Т, мин | ||||||||||
20 | 30 | 45 | 60 | 75 | 90 | 120 | 150 | 180 | 240 | 360 | |
Незакаленная сталь | 1,33 | 1,24 | 1,15 | 1,08 | 1,04 | 1,00 | 0,94 | 0,91 | 0,87 | 0,82 | 0,76 |
В зависимости от марки твердого сплава
Марка твердого сплава | Т5К10 | Т15К6 | Т30К4 | ВК8 | ВК6 | ВК3 |
Кр | 0,65 | 1,0 | 1,5 | 1,0 | 1,2 | 1,5 |
В зависимости от главного угла в плане φ0
Обрабатываемый материал | Главный угол в плане φ0 | ||||||
10 | 20 | 30 | 45 | 60 | 70 | 80 | |
Углеродистые, легированные стали и стальное литье Серый чугун и медные сплавы | 1,55 – | 1,30 – | 1,13 1,20 | 1,00 1,00 | 0,92 0,88 | 0,86 0,83 | 0,81 0,73 |
При растачивании отверстий проходными расточными резцами
(коэффициент при наружном продольном точении принят равным единице)
Диаметр отверстия, мм | До 75 | 76 - 150 | 151 - 250 | Свыше 250 |
Коэффициент | 0,80 | 0,90 | 0,95 | 1,00 |
При обтачивании и подрезании торцовых поверхностей
Тип резца | Значение (d2 – d1)/d2 | ||||
0,3 | 0,5 | 0,7 | 0,8 | 0,9 | |
Проходной Подрезной | 1,03 0,65 | 1,04 0,67 | 1,07 0,70 | 1,10 0,73 | 1,18 0,93 |
Таблица IV.3.56
Вспомогательное время, связанное с переходом, при нарезании
резьбы на токарных станках (время на один ход), мин
Характер обработки | Диаметр резьбы, мм (до) | Высота центра станка, мм | |||
До 200 | 300 | ||||
Нарезание резьбы резцом | С автоматическим обратным перемещением каретки суппорта | Без промера С промером: резьбовым микрометром резьбовой скобой | – 50 50 | 0,12 0,40 0,24 | 0,15 0,43 0,27 |
С ручным обратным перемещением каретки | Без промера С промером: резьбовым микрометром резьбовой скобой | – 50 59 | 0,18 0,45 0,30 | 0,22 0,49 0,34 |
Таблица IV.3.57
Подготовительно – заключительное время при работе на токарных станках, мин
Способ установки детали | Высота центров станка, мм | |||||
до 200 | 300 | |||||
Кол-во устанавливаемых инструментов | ||||||
2 | 4 | 6 | 2 | 4 | 6 | |
На наладку станка, инструментов и приспособлений | ||||||
В центрах или на шпиндельной оправке | 7 | 9 | 12 | 8 | 10 | 14 |
В патроне самоцентрирующем, цанговом или пневматическом | 8 | 10 | 12 | 12 | 14 | 16 |
То же, с поджатием центром задней бабки | 10 | 12 | 13 | 13 | 15 | 18 |
На дополнительные приемы | ||||||
Установка упора | 1,5 | 2,0 | ||||
Установка люнета с регулировкой | 2,7 | 3,8 | ||||
Установка подачи по ходовому винту для нарезания резьбы рычагом коробки передач | 1,0 | 1,0 | ||||
Смещение задней бабки для обточки конуса | 2,5 | 3,0 | ||||
Поворот суппорта на угол для обточки конуса | 1,0 | 1,0 | ||||
Расточка сырых кулачков | 6,0 | 8,0 | ||||
На получение инструментов и приспособлений до начала и сдачу их после окончания работы | 8 | 9 |
Таблица IV.3.58
Вспомогательное время на установку и снятие детали
при работе на токарных станках, мин
Способ установки детали вручную | Масса детали, кг | |||||||
0,5 | 1,0 | 3,0 | 5,0 | 8,0 | 12,0 | 20,0 | ||
В трехкулачковом патроне с ручным зажимом | Без выверки С выверкой по мелку С выверкой индикатором | 0,22 0,42 1,15 | 0,25 0,45 1,25 | 0,29 0,54 1,29 | 0,34 0,64 1,44 | 0,38 0,72 1,68 | 0,46 0,84 1,96 | 0,56 1,00 2,36 |
То же, с пневмати- ческим зажимом | Без выверки С выверкой по мелку | 0,11 0,32 | 0,12 0,34 | 0,13 0,38 | 0,14 0,44 | 0,16 0,50 | 0,19 0,57 | 0,24 0,70 |
То же, с ручным зажимом | С поджатием центром задней бабки | 0,29 | 0,32 | 0,35 | 0,39 | 0,43 | 0,48 | 0,53 |
То же, с ручным зажимом | С поджатием центром задней бабки и неподвижным люнетом | 0,41 | 0,46 | 0,54 | 0,58 | 0,62 | 0,69 | 0,79 |
То же, с ручным зажимом | С неподвижным люнетом, длина детали: до 400 мм 400–1000 мм | 0,30 – | 0,33 – | – 0,36 | – 0,41 | – 0,45 | – 0,50 | – 0,56 |
В центрах | Без надевания хомутика С надеванием хомутика | 0,17 0,25 | 0,18 0,27 | 0,20 0,30 | 0,24 0,34 | 0,26 0,40 | 0,29 0,48 | 0,34 0,60 |
В центрах с ведущим передним центром | – | 0,18 | 0,19 | 0,22 | 0,26 | – | – | – |
В центре с неподвижным люнетом | Без надевания хомутика, при длине детали: 400 мм 1200 мм 2500 мм | 0,32 – – | 0,34 – – | – 0,37 – | – 0,41 – | – 0,43 0,47 | – 0,45 0,52 | – 0,52 0,59 |
В центре с неподвижным люнетом | С надеванием хомутика, при длине детали: 400 мм 1200 мм 2500 мм | 0,43 – – | 0,46 – – | – 0,48 – | – 0,51 – | – 0,57 0,62 | – 0,64 0,71 | – 0,78 0,85 |
Таблица IV.3.59
Вспомогательное время, связанное с переходом при продольном обтачивании
и растачивании на токарных станках (время на один ход), мин
Характер обработки | Измерительный инструмент | Обрабаты-ваемый диаметр | Высота центров станка, мм | ||||
До 200 | 300 | ||||||
Обрабатываемая длина, мм (до) | |||||||
200 | 500 | 200 | 500 | ||||
Грубое обтачивание или растачивание | Резцом, установленным на размер С установкой резца по упору или лимбу грубо То же, с точностью 0,2 мм С предварительным промером То же | – – – Кронциркуль Линейка, кронциркуль | – – – До 100 100 – 300 | 0,10 0,15 0,17 0,36 0,42 | 0,12 0,17 0,19 0,38 0,44 | 0,12 0,18 0,20 0,40 0,46 | 0,16 0,22 0,24 0,44 0,50 |
Обтачивание или растачивание по 4-му и 5-му классам точности | Со взятием одной пробной стружки | Штангенциркуль Скоба или штихмас | До 100 100 – 200 До 100 100 - 300 | 0,38 0,41 0,34 0,37 | 0,40 0,43 0,36 0,39 | 0,44 0,47 0,40 0,43 | 0,48 0,51 0,44 0,47 |
Обтачивание или растачивание по 3-му классу точности | Со взятием двух пробных стружек | Микрометр Скоба Калибр- пробка | До 100 ›› 100 ›› 50 50 - 100 | 0,81 0,57 0,51 0,55 | 0,83 0,59 0,53 0,57 | 0,89 0,65 0,59 0,63 | 0,93 0,69 0,63 0,67 |
Повернуть головку | Четырехрезцовую | – | – | 0,12 | 0,15 |
Таблица IV.3.60
Вспомогательное время, связанное с переходом при поперечном обтачивании
на токарных станках (время на один ход), мин
Характер обработки | Измерительный инструмент | Обрабаты-ваемый диаметр | Высота центров станка, мм | |||||
До 200 | 300 | |||||||
Обрабатываемая длина, мм (до) | ||||||||
200 | 500 | 200 | 500 | |||||
Поперечное обтачивание отрезка, протачивание наружных канавок | Резцом, установленным на размер С установкой резца по упору, грубо С установкой резца по лимбу с точностью 0,2 мм С предварительным промером Со взятием одной пробной стружки | – – – Линейка, шаблон То же Штангенциркуль То же | – – – – До 300 До 100 100 - 200 | 0,08 0,13 0,15 0,25 0,32 0,36 0,39 | 0,10 0,15 0,17 0,27 0,34 0,38 0,41 | 0,12
0,18
0,20
0,31
0,40 0,44 0,47 | 0,16 0,22 0,24 0,35 0,44 0,48 0,51 | |
Протачивание внутренних канавок | Без установки резца на размер С установкой резца на размер | – – | – – | 0,15 0,29 | – – | 0,20 0,36 | – – | |
Внутренняя подрезка дна и уступа | – | – | 0,12 | – | 0,16 | – | ||
Таблица IV.3.61
Вспомогательное время, связанное с переходом на дополнительные приемы работы,
не вошедшие в комплексы таблиц, мин
Наименование приемов работы | Высота центров станка | ||
До 200 | 300 | ||
Изменить частоту вращения или изменить величину подачи Установить инструмент и снять | Одним рычагом Двумя рычагами Проходной или подрезной резец с креплением одним болтом двумя болтами Фасонный или резьбовой с креплением: одним болтом двумя болтами Сверло, зенкер, развертку | 0,04 0,06 0,60 0,70 0,90 1,00 0,12 | 0,05 0,08 0,70 0,80 1,00 1,20 0,14 |
Повернуть верхнюю часть суппорта на угол | 0,06 | 0,07 | |
Смазать деталь, развертку или метчик | 0,03 | 0,04 | |
Закрепить или открепить каретку от продольного перемещения: рукояткой ключом | 0,04 0,08 | 0,05 0,10 | |
Таблица IV.3.62
Время на обслуживание рабочего места, (для всех станочных работ), % оперативного
Характер затрат времени | Высота центров станка, мм | |
До 200 | 300 | |
Организационное и техническое обслуживание рабочего места и естественные надобности исполнителя Проведение физпаузы (где она введена) | 6 3 | 7 3 |
Дата добавления: 2018-11-24; просмотров: 1190; Мы поможем в написании вашей работы! |
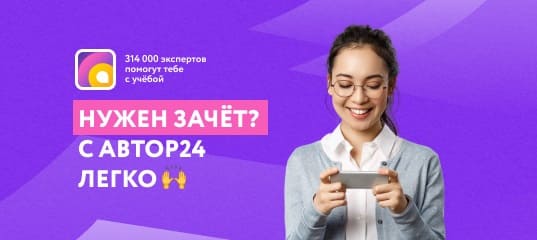
Мы поможем в написании ваших работ!