Расчет размера партии обрабатываемых деталей
где: Nг – годовая производственная программа
Кр – маршрутный коэффициент ремонта
P – количество одноименных деталей на автомобиле ДРГ - дни работы в году
ДРГ – дни работы в году
Выбор установочных баз
Основные установочные базы почти всегда подвергаются износу, поэтому использовать их при ремонте деталей можно только в крайних случаях, когда отсутствуют вспомогательные базы или трудно создать новые базы и нет неизношенных обработанных поверхностей, с помощью которых можно было бы установить ремонтируемую деталь на станке или в приспособлении. Принятие решения о выборе базовой поверхности является сложной задачей, зависящей от типа детали, номенклатуры изношенных поверхностей, степени и вида износа, от способов ремонта и т.д.
Базировать можно по центровым отверстиям или на оправке, по наружной цилиндрической поверхности в призме, по двум плоскостям и т.д. Если технологические базовые поверхности детали нарушены или отсутствуют, то необходимо в первую очередь обрабатывать их.
Наибольшей точности при механической обработке можно достичь лишь в том случае, если вся обработка детали ведется на одной базе (с одной установки), например в центрах. При обработке детали на ряде станков желательно использовать, по мере возможности, одни и те же установочные поверхности, предусмотренные заводом-изготовителем. При выборе установочных баз нужно, чтобы технологический процесс обеспечил технические требования на прямолинейность, параллельность, перпендикулярность осей и поверхностей обрабатываемой детали.
|
|
Подбор необходимого оборудования, приспособлений, инструмента
При подборе оборудования, приспособлений и инструмента для каждой технологической операции должны быть учтены:
2.7.1. Размер программы ремонтируемых деталей.
2.7.2. Габаритные размеры детали, размеры и расположение обрабатываемых поверхностей»
2.7.3. Возможности обеспечения выполнения технических требований, предъявляемых к обрабатываемой детали в отношении точности её размеров, формы и качества обработанных поверхностей.
2.7.4. Уменьшение затрат времени на обработку.
2.7.5. Наиболее полная загрузка оборудования.
2.7.6. Наименьшая себестоимость обработки детали.
Перечень (с краткой технической характеристикой) наиболее распространенного оборудования, применяемого в авторемонтном производстве, приведен в приложении 1. Приспособления для каждой технологической операции подбираются из числа описанных в литературе по ремонту автомобилей. Так же допускается самим устанавливать подбор приспособления исходя от сложности детали, от содержания выполняемой операции. Например, для развертки втулок под шкворень поворотной цапфы. Необходимо приспособление для развертки втулок поворотной цапфы на вертикально-сверлильном станке.
|
|
Приспособление, разрабатываемое в конструкторской части курсового проекта, необходимо включить в маршрутную карту ремонта детали. При выборе приспособления необходимо учитывать установочную базу детали, точность и качество обработки поверхностей, снижение вспомогательного времени, улучшение условий труда.
При разработке технологического процесса ремонта деталей режущий инструмент нужно подбирать с учетом твердости материала обрабатываемой детали, вида обработки, точности и качества (шероховатости) поверхности ремонтируемой детали.
При подборе режущего инструмента указывается название инструмента и материал режущей части (сверло Р 9, машинная развертка Р 9, проходной резец ВК 8 и т.д.).
При подборе режущего инструмента рекомендуется пользоваться каталогом режущих инструментов металлорежущих станков или учебником «Технология металлов».
Многие режущие инструменты изготавливаются из инструментальных сталей ( смотрите «Методику выполнения конструкторской части курсового проекта»). В настоящее время режущие части инструментов выполняются из тугоплавких сплавов (ВК8; Т15К6 и т.д.).
|
|
Подбор мерительного инструмента производится исходя из точности обрабатываемой поверхности. Например: после токарной и фрезерной работы используются штангенциркули (штангенциркуль 0-125), после шлифования микрометры (микрометр 50-75, нутромер 75+100). Или же можно подбирать предельные скобы, проходные и непроходные, пробки проходные и непроходные, пробки резьбовые проходные и непроходные, кольца резьбовые проходные и непроходные с указанием размеров и отклонений.
Составление плана технологических операций.
План технологических операций составляется для дальнейшей разработки маршрутной карты на устранение группы дефектов детали, причем операции должны располагаться в рациональной последовательности, т.е. нужно, чтобы последующие операции не влияли на качество поверхностей, подученных при предыдущих операциях, не ухудшали их, а также не нарушали взаимное расположение отдельных поверхностей детали и их осей. Для этого нужно использовать ранее разработанные схемы технологических процессов устранения каждого дефекта в отдельности.
|
|
Пример составления ранее разработанного плана технологических операций на ремонт поворотной цапфы автомобиля ЗИЛ-130 на основе схем технологических процессов устранения дефектов этой детали.
План технологических операций на ремонт поворотной цапфы
№ | Наименование операций | Оборудование | Приспособления | Инструмент | |
рабочий | мерительный | ||||
1. | Токарная (выправить центровые отверстия) | Токарно-винторезный станок 16К20 | – | Шабер | Индикатор часового типа, цена деления 0,01 мм |
2. | Токарная (проточить изношенную резьбу) | Токарно-винторезный станок 16К20 | Поводковый патрон с поводком, центрами | Проходной резец Т15К6 | Штангенциркуль с пластинками 0-150 мм |
3. | Сварочная (наплавить шейку под резьбу) | Установка для вибродуговой наплавки | – | – | – |
4. | Шлифовальная (шлифовать шейку) | Кругло- шлифовальный станок ЗБ 151 | – | Шлифовальный круг Д-150мм Э60СМ2К | Микрометры 25-50 мм 50-75 мм |
5. | Гальваническая (подготовка и хромирование шеек) | Ванны для обезжиривания, хромирования, электропечь | Подвеска для хромирования | Кисть для изоляции | – |
6. | Токарная (проточить шейку и нарезать резьбу) | Токарно-винторезный станок 16К20 | Поводковый патрон с поводком, центрами | Проходной прямой резец с пластинкой Т15К6, прямой резьбовой резец Р18 | Штангенциркуль 0-150 мм |
7. | Фрезерная (фрезеровать лыску) | Горизонтально- фрезерный станок 6Н82 | Кронштейн, домкрат | Цилиндрическая фреза Д=90 мм, ширина=50 мм с пластинками Т15К6 | Штангенциркуль 0-150 мм |
8. | Шлифовальная (шлифовать шейку) | Кругло- шлифовальный станок ЗБ 151 | Поводковый патрон с поводком | Шлифовальный круг Д =150мм Э60СМ2К | Предельные скобы Ø55 – 0,012 – 0,032 Ø40 – 0,010 – 0,027 |
9. | Слесарная (впрессовывать втулки, запрессовать и раздать втулки) | Гидравлический пресс Г АРО208 | – | Оправка для выпрессовки, запрессовки, раздачи | – |
10. | Сверлильная (отвернуть втулки) | Вертикальный сверлильный станок 2А150 | Кондуктор | Цилиндрическая машинная развертка Д=38-0,025 Д=38-0,060 | Предельная пробка – 0,02 – 0,02 |
11. | Слесарная (прогнать резьбу) | – | Тиски | Плашка М36х2 - кл.1 | Резьбовое кольцо М36х2 - кл.1 |
Затем следует определить переходы по каждой операции, места обработки, размеры обработки по диаметру и длине, способы контроля операционного и в конце технологического процесса.
Дата добавления: 2018-11-24; просмотров: 511; Мы поможем в написании вашей работы! |
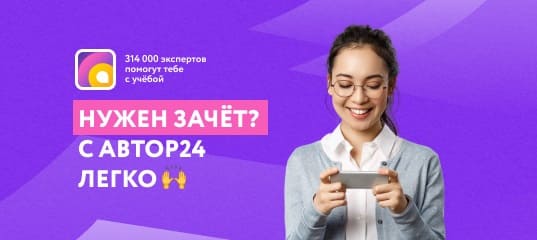
Мы поможем в написании ваших работ!