Расчет режимов обработки и определение технической норы времени
Расчет режимов обработки производится для каждой операции и перехода отдельно. При механической обработке деталей выбор режима резания должен соответствовать частоте вращения, величине подачи, допускаемой прочности механизма коробки передач, крутящему моменту на шпинделе, мощности электропривода с учетом кпд передачи принятого станка.
Выбор режимов необходимо уточнять по паспортным данным принятого станка. Назначение режимов обычно производится по нормативным таблицам в соответствующих справочниках (Краткий справочник металлиста. под ред. Малова и др.) или расчетным путем (Справочник технолога АРП. под ред. Малышева Г.А.) (приложение 2).
Определение технической нормы времени в проекте производится расчетно-аналитическим методом по Справочнику технолога АРП под ред. Малышева Г.А. или по другим справочным литературам по техническому нормированию. (приложение 1).
Расчет режимов обработки и определение технической нормы времени выполняется пооперационно.
Оформление технологического процесса
а) Технологический процесс оформляется в виде маршрутной карты (приложение 2) в соответствии с требованиями Единой системы технологической документации (ЕСТД) по ГОСТ З.1105-74(формы 1 и 1 а). Она полностью и однозначно определяет технологический процесс ремонта детали.
В маршрутную карту должны записываться контрольные операции как пооперационные, после предварительной обработки между операциями перед трудоемкими и ответственными операциями и после них, так и в конце технологического процесса.
|
|
При заполнении маршрутной карты на ремонт детали следует пользоваться указаниями по составлению маршрутной карты на ремонт, а также примером, приведенным в приложении.
б) Указания по составлению операционной карты на ремонт
В операционной карте по каждой операции должны быть все переходы. В переходах необходимо указать размеры по обработке, например, шлифовать шейку с Ø =54,8 мм где Ø =54,6-0,05 на длине l = 51 мм. Операционные карты выполняются по форме, данной в приложении 3.
в) Карта эскизов делается для механических операций по форме данной в приложении 3. Рисунок детали делается в виде эскиза, а для деталей сложной конфигурации допускается прилагать эскиз только тех мест, где ведется ремонт.
Схемы установок и базирования деталей выполняется на карте эскизов согласно приложению 3.
Рекомендации по выполнению «Конструкторской части»
Одним из разделов проекта является «конструкторская часть», где студент должен разработать приспособление для ремонта детали привязанной к теме курсового проекта, то есть приспособление должно обеспечивать установку детали с последующей выверкой для обработки одной или нескольких поверхностей детали на металлорежущих станках или обеспечить установку детали для последующего наращивания отдельных поверхностей сваркой, наплавкой, хромированием и напылением. Так же допускается разработка приспособления для контроля размеров и других параметров детали. Можно разработать приспособление для разборо‑сборочных работ, связанное с данной деталью в узле или агрегате. В этих случаях приспособление называется:
|
|
- приспособление для растачивания отверстия под наружный подшипник в ступице колеса;
- приспособление для наплавки шлиц полуоси;
- приспособление для выпрессовки шестерни коленчатого вала и т.д.
Перед разработкой приспособления студент должен изучить полностью деталь, то есть, какие бывают возможные дефекты на детали и как они устраняются.
Требования по разборке и сборке узла или агрегата.
3.1. Требования к приспособлениям в зависимости от назначения:
а) приспособление для установки детали с последующей механической обработкой на металлорежущих станках:
- жесткость крепления детали
- жесткость конструкции
- возможность выверки детали
|
|
- центровка детали
- минимальные затраты времени и усилия при установке и снятии детали
- технологичность в изготовлении
- легкость конструкции
- удобство пользования
- минимальные затраты на обслуживание и ремонт
б) приспособления обеспечивающие установку детали для последующего наращивания изношенной поверхности:
- быстрота установки и снятия детали
- установка одновременно нескольких деталей
- минимально малый вес конструкции
- фиксация детали в определенное положение
- изменения положения детали без снятия
- технологичность в изготовлении
- простота конструкции
- минимальные затраты на обслуживание
- удобство пользования
в) приспособления для разборно-сборочных работ:
- легкость конструкции
- универсальность
- наименьшие потери сил на трение быстрота установки и снятия минимальные
- усилия на рычаге управления удобство пользования
- жесткость конструкции
- технологичность в изготовлении
3.2. Разработка приспособления производится в следующем порядке:
1. Определяем назначение приспособления, то есть для выполнения какой работы предназначено приспособление.
2. Выполнение эскиза приспособления. Эскиз выполняется в рабочей тетради. Эскиз рекомендуется выполнять следующей последовательности:
|
|
а) Схематическое изображение приспособления.
б) Выведение контуров детали приспособления
в) Выбор соединения деталей
При выборе соединения деталей сначала выбирается базовая деталь. Основные детали приспособления крепятся или устанавливаются на базовой детали. Соединения деталей могут быть: неразъемные и разъемные.
К неразъемным соединениям относится такие соединения:
- сварные
- клееные
- паянные
К разъемным соединениям относятся:
- резьбовые
- клепанные
- шлицевые
- шпоночные
- прессовые
г) Выбор конфигурации и сечения детали.
Здесь за счет выбора конфигурации и сечения деталей приспособления обеспечиваем жесткость детали.
д) Обеспечение жесткость крепления, необходимого усилия.
Здесь жесткости крепления или необходимое усилие обеспечивается за счет применения различных видов резьбы, дополнительного соотношения рычагов.
е) Выбор материалов деталей приспособления.
При выборе материалов надо учитывать следующие рекомендации:
- корпусные детали выполняются из серого чугуна СЧ 20; СЧ 25; СЧ 30; ГОСТ 1412-85 или сваривается из деталей из углеродистой стали Ст 3 ГОСТ 380‑88
- установочные детали (опорные штыри, опорные пластины, опоры, призмы, установочные пальцы и т.д.) с большой износоустойчивостью и твердостью изготавливают из углеродной качественной конструкционной стали Ст 15; Ст 20; Ст 40; Ст 45 ГОСТ 1050-88 или легированной стали Ст 15 Г; Ст 20 Х; Ст 20 Г; Ст 40Х ГОСТ 4543-71.
- направляющие детали, кондукторные втулки лапы съемников изготавливают из инструментальной стали У 10 А; У 12 А ГОСТ 1435-90.
- зажимные детали (клинья, прихваты, губки) изготавливают из углеродистой стали Ст 5 ГОСТ 380~88...
- экцентрики, кулачки зажимов изготавливают из конструкционной стали Ст 15; Ст 20 ГОСТ 1050-88 или инструментальной стали У 7; У 8; У 7 А; У 8 А ГОСТ 1435-90.
- остальные детали изготавливаются из углеродистой стали Ст 3 ГОСТ 380-88.
- отдельные детали для облегчения конструкции могут изготавливаться из алюминиевого сплава АЛ-2; АЛ-4; АЛ-9; АЛ-34 ГОСТ 2685-75.
- детали типа втулок изготавливаются из оловянной бронзы БрОФ 7-0,2 или БрОФ 6,5-0,4 ГОСТ 5017-74.
ж) Для обеспечения легкости вращения и обеспечения точности установки отдельных деталей устанавливаются подшипники качения ГОСТ 520-89.
3. Выполнение сборочного и рабочего чертежей
Сборочный чертеж приспособления выполняется на основании выполненного эскиза приспособления. Сборочный чертеж выполняется по следующему рекомендуемому плану:
а) Определить основной вид приспособления.
б) Определить количество дополнительных проекций приспособления. Количество проекций сборочного чертежа приспособления должно быть достаточным, чтобы можно было прочитать чертеж.
в) Определить необходимые разрезы на проекциях чертежа.
г) Выбрать формат и масштаб.
д) На месте основной проекции сборочного чертежа приспособления начертить в тонких линиях контур детали в масштабе в соотношении по эскизу.
е) В тонких линиях начертить базовую деталь приспособления.
ж) Начертить остальные детали приспособления.
з) Нанести размеры. На сборочном чертеже должны быть габаритные размеры, установочные размеры и присоединительные размеры.
и) Указать характер сопряженных деталей и способы соединения неразъемных соединений (сварные паянные, клееные и т.д.).
к) Указать позиции деталей сборочного чертежа приспособления и выделить стандартные детали.
л) На формате А 4 выполнить спецификацию на сборочный чертеж.
м) Из сборочного чертежа выбрать 4 нестандартные детали для выполнения рабочего чертежа деталей приспособления. Выбор деталей должен быть согласован с руководителем.
н) Выполнить рабочие чертежи. Рекомендуется выполнять рабочие чертежи на форматах А 4.Количество проекций должно быть достаточным, чтобы получить полную информацию о детали. На рабочих чертежах указывают размеры, допуски, класс шероховатости и другие данные.
4. Выполнение пояснительной записки конструкторской части.
Пояснительную записку конструкторской части рекомендуется выполнять по следующему плану:
а) Назначение приспособления, его достоинства.
б) Устройство приспособления. Здесь необходимо дать рисунок приспособления. Описание устройства делается, ссылаясь на рисунок приспособления.
в) Работа приспособления. Описание работы делать, ссылаясь на рисунок.
г) Техника безопасности при пользовании приспособлением.
д) Техническое обслуживание и ремонт приспособления
е) Расчет на прочность отдельных нагруженных соединений детали. Здесь необходимо выполнить проверочный расчет на прочность отдельных нескольких соединений.
Библиографический список
1. Карагодин, В.И. Ремонт автомобилей и двигателей [текст]: Учеб. для студ. сред. проф. учебн. заведений. – М.: Мастерство, 2001. – 496 с. – 50 000 экз. – JSBN5 – 294 – 00043 – 1.
2. Ремонт автомобилей [текст]: Учеб. для автотрасп. техникумов Под ред. С.И. Румянцева. – 2‑е изд., перераб. и доп. – М.: Транспорт, 1988. – 327 с. – 100 000 экз. – JSBN5 – 277 – 00048 ‑ 8.
3. Справочник технолога авторемонтного производства [текст]. Под ред. Г.А. Малышева. – М.: Транспорт, 1977. – 432 с. – 50 000 экз.
4. Технические условия на капитальный ремонт автомобилей ГАЗ-53А [текст]: Министерство автомобильного транспорта и шоссейных дорог РСФСР. – М.: Транспорт, 1968. – 456 с. – 30 000 экз.
5. Технические условия на капитальный ремонт автомобиля ЗИЛ-130 [текст]: Министерство автомобильного транспорта и шоссейных дорог РСФСР. – М.: Транспорт, 1966. – 518 с. – 15 000 экз.
6. Матвеев, В.А. и Пустовалов, И.И. Техническое нормирование ремонтных работ в сельском хозяйстве [текст]: – М.: Колос, 1979. – 288 с. – 80 000 экз.
7. Александров, Л.А. Техническое нормирование на автомобильном транспорте [текст]: – М.: Транспорт, 1967. – 232 с. – 30 000 экз.
8. Клебанов, Б.В. Проектирование производственных участков авторемонтных предприятий [текст]: – М.: Транспорт, 1975. – 176 с. – 30 000 экз.
9. Куликов, В.П. Инженерная графика [текст]: Учебник. – М.: Форум: Инфра-М, 2006. – 368 с. – 4 000 экз. – JSBN5 – 91134 – 011 – 9.
10. Суханов, В.Н. Техническое обслуживание и ремонт автомобилей [текст]: Пособие по курсовому и дипломному проектированию. – М.: Транспорт, 1985. – 224 с. – 30 000 экз.
11. Программа системы трехмерного моделирования компас-график 3D LT V9.
Приложение 1
Выписка
Из «справочника технолога авторемонтного производства»
под редакцией Г.А. Малышева М. Транспорт. 1977 г.
Дата добавления: 2018-11-24; просмотров: 506; Мы поможем в написании вашей работы! |
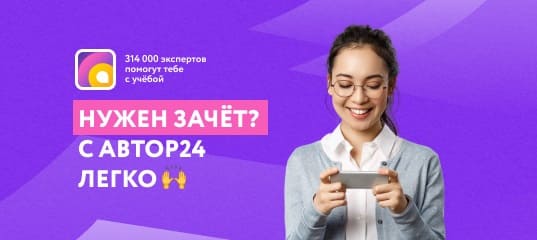
Мы поможем в написании ваших работ!