Определение элементов технической нормы времени
Для фрезерных работ
Величина врезания и перебега фрезы ,
где – величина врезания фрезы, мм;
– величина перебега фрезы, равная (0,03÷0,05) D мм;
D – диаметр фрезы, мм.
Для фрезерования цилиндрической фрезой ;
Для фрезерования торцовой фрезой ,
где t – глубина фрезерования, мм;
В – ширина фрезерования, мм.
Подача в минуту
,
где – подача на один оборот фрезы, мм/об;
– подача на один зуб, мм/зуб;
n – частота вращения фрезы, об/мин;
z – число зубьев фрезы.
Подачи при фрезеровании приводятся в табл. IV.3.76.- IV.3.80. скорость резания для всех видов фрезерной обработки определяют по эмпирической зависимости:
м/мин,
где А – постоянная величина, зависящая от обрабатываемого материала, типа фрезы, подачи на один зуб и т.п. (табл.IV.3.81.)
D – Диаметр фрезы, мм;
Т – стойкость фрезы, мм;
t – глубина резания, мм;
– подача на один зуб, мм/зуб;
где z – число зубьев фрезы;
– показатели степени (табл.IV.3.81.)
После определения скорости резания рассчитывают обороты фрезы в минуту, минутную подачу и основное время фрезерования.
Поправочные коэффициенты на скорость резания, подготовительно-заключительное время, вспомогательное время и время обслуживания рабочего места приведены в табл. IV.3.82.- IV.3.87.
Таблица IV.3.76.
Подача на один зуб мм/зуб, при фрезеровании плоскостей
цилиндрическими фрезами из быстрорежущей стали
(черновая обработка)
Диаметр
фрезы D, мм | Число зубьев фрезы, z | Глубина резания t, мм | |||
до 3 | 3-5 | ||||
Подача при фрезеровании стали | |||||
60 | 16 | 0,08-0,04 | 0,05-0,03 | ||
8 | 0,15-0,08 | 0,12-0,07 | |||
75 | 18 | 0,08-0,04 | 0,05-0,03 | ||
8 | 0,20-0,10 | 0,15-0,08 | |||
90 | 20 | 0,12-0,06 | 0,08-0,05 | ||
8 | 0,30-0,10 | 0,20-0,10 | |||
110 | 10 | – | 0,20-0,10 | ||
130 | 10 | – | 0,30-0,15 | ||
150 | 12 | – | 0,30-0,15 | ||
Подача при фрезеровании чугуна | |||||
60 | 16 | 0,12-0,08 | 0,08-0,05 | ||
8 | 0,25-0,15 | 0,20-0,10 | |||
75 | 18 | 0,12-0,06 | 0,08-0,15 | ||
8 | 0,30-0,15 | 0,25-0,15 | |||
90 | 20 | 0,18-0,10 | 0,12-0,06 | ||
8 | 0,40-0,20 | 0,30-0,15 | |||
110 | 10 | – | 0,30-0,15 | ||
130 | 10 | – | 0,40-0,25 | ||
150 | 12 | – | 0,40-0,25 |
Примечание. При чистовой обработке с фрезерованием в один ход после чернового с глубиной резания до 2 мм подача рекомендуется мм и при фрезеровании в один ход без предварительного чернового с глубиной резания до 4 мм
мм.
Таблица IV.3.77.
Подача на один зуб , мм/зуб, при фрезеровании пазов
концевыми фрезами из быстрорежущей стали (фрезерование стали)
Диаметр фрезы D, мм | Число зубьев фрезы z | Ширина паза t = D мм | Глубина паза В, мм | ||
5 | 10 | 15 | |||
6 | 6 | 6 | 0,01-0,005 | 0,006-0,003 | – |
10 | 6 | 10 | 0,015-0,01 | 0,008-0,004 | 0,005-0,003 |
16 | 5 | 16 | 0,025-0,015 | 0,015-0,010 | 0,01-0,005 |
20 | 5 | 20 | – | 0,03-0,02 | 0,025-0,015 |
25 | 5 | 25 | – | 0,05-0,03 | 0,04-0,02 |
30 | 6 | 30 | – | 0,05-0,03 | 0,04-0,02 |
|
|
Таблица IV.3.78.
Подача на один зуб , мм/зуб, при фрезеровании торцовыми фрезами
из быстрорежущей стали (черновая обработка)
Диаметр фрезы D, мм | Число зубьев z | Глубина резания t, мм | |
до 3 | 3-5 | ||
Подача при фрезеровании стали | |||
60 | 16 | 0,10-0,06 | 0,08-0,05 |
10 | 0,15-0,08 | 0,12-0,06 | |
75 | 18 | 0,10-0,06 | 0,08-0,05 |
10 | 0,15-0,08 | 0,12-0,06 | |
90 | 20 | 0,10-0,06 | 0,08-0,05 |
12 | 0,15-0,08 | 0,12-0,06 | |
110 | 12 | 0,15-0,08 | 0,12-0,06 |
150 | 16 | 0,12-0,07 | 0,10-0,06 |
200 | 20 | 0,12-0,07 | 0,10-0,06 |
Подача при фрезеровании чугуна | |||
60 | 16 | 0,20-0,10 | 0,15-0,08 |
10 | 0,25-0,15 | 0,20-0,12 | |
75 | 18 | 0,20-0,10 | 0,15-0,08 |
10 | 0,25-0,15 | 0,20-0,12 | |
90 | 20 | 0,20-0,10 | 0,15-0,08 |
12 | 0,25-0,15 | 0,20-0,12 | |
110 | 12 | 0,25-0,15 | 0,20-0,12 |
150 | 16 | 0,20-0,12 | 0,15-0,10 |
200 | 20 | 0,20-0,12 | 0,15-0,10 |
300 | 30 | 0,20-0,12 | 0,15-0,10 |
Примечание. При получистовой обработке с фрезерованием в один ход после чернового с глубиной резания до 2 мм подача рекомендуется мм и при фрезеровании в один ход без предварительного чернового с глубиной резания до 2 мм
мм
Таблица IV.3.79.
Подача на один зуб SZ, мм/зуб, при фрезеровании боковых плоскостей,
и уступов дисковыми фрезами из быстрорежущей стали
Диаметр фрезы D, мм | Число зубьев
фрезы z | Ширина фрезерования В, мм | Глубина резания t, мм | |||||
до 5 | 5-10 | 10-20 | 20-40 | |||||
Подача при фрезеровании стали | ||||||||
75 | 18 | 4-10 | 0,12-0,08 | 0,12-0,08 | 0,10-0,05 | – | ||
12 | 4-10 | 0,20-0,12 | 0,20-0,012 | 0,15-0,10 | – | |||
90 | 20 | 4-10 | 0,12-0,08 | 0,12-0,08 | 0,10-0,05 | – | ||
12 | 4-10 | 0,20-0,12 | 0,20-0,12 | 0,15-0,10 | – | |||
110 | 22 | 4-10 | 0,15-0,08 | 0,02-0,08 | 0,10-0,05 | – | ||
14 | 4-10 | 0,20-0,12 | 0,20-0,12 | 0,15-0,10 | 0,12-0,08 | |||
150 | 28 | 6-15 | – | 0,15-0,10 | 0,12-0,08 | 0,08-0,05 | ||
14 | 6-15 | – | 0,25-0,15 | 0,20-0,10 | 0,15-0,10 | |||
200 | 18 | 6-15 | – | 0,25-0,15 | 0,20-0,10 | 0,15-0,08 | ||
Подача при фрезеровании чугуна | ||||||||
75 | 18 | 4-10 | 0,20-0,12 | 0,15-0,10 | 0,12-0,08 | – | ||
12 | 4-10 | 0,30-0,20 | 0,25-0,15 | 0,20-0,15 | – | |||
90 | 20 | 4-10 | 0,20-0,12 | 0,15-0,10 | 0,12-0,08 | – | ||
12 | 4-10 | 0,30-0,20 | 0,25-0,15 | 0,20-0,15 | – | |||
110 | 22 | 4-10 | 0,20-0,12 | 0,15-0,10 | 0,12-0,08 | – | ||
14 | 4-10 | 0,30-0,20 | 0,30-0,20 | 0,25-0,15 | 0,20-0,10 | |||
150 | 28 | 6-15 | – | 0,20-0,12 | 0,15-0,12 | 0,12-0,08 | ||
14 | 6-15 | – | 0,40-0,20 | 0,30-0,15 | 0,25-0,15 | |||
200 | 18 | 6-15 | – | 0,40-0,30 | 0,30-0,15 | 0,20-0,10 |
Таблица IV.3.80.
Подача на один зуб SZ, мм/зуб, при фрезеровании пазов
дисковыми фрезами из быстрорежущей стали
Диаметр фрезы D, мм | Число зубьев фрезы z | Ширина фрезерования В, мм | Глубина резания t, мм | |||||
До 5 | 5-10 | 10-15 | 15-20 | |||||
Подача при фрезеровании стали
| ||||||||
60 | 16 | 6-12 | 0,08-0,05 | 0,06-0,03 | 0,05-0,03 | – | ||
18 | 6-12 | 0,08-0,05 | 0,06-0,06 | 0,05-0,03 | – | |||
75 | 12 | 10-20 | 0,12-0,08 | 0,10-0,06 | 0,08-0,05 | – | ||
20 | 10-20 | 0,08-0,05 | 0,06-0,03 | 0,06-0,03 | – | |||
90 | 12 | 10-20 | 0,12-0,08 | 0,10-0,06 | 0,08-0,05 | – | ||
22 | 10-20 | 0,10-0,05 | 0,08-0,04 | 0,06-0,03 | – | |||
110 | 14 | 12-24 | 0,12-0,08 | 0,10-0,05 | 0,08-0,04 | 0,06-0,03 | ||
15 | 14 | 18-30 | – | 0,12-0,06 | 0,10-0,05 | 0,08-0,04 | ||
200 | 18 | 20-40 | – | 0,15-0,08 | 0,12-0,06 | 0,08-0,04 | ||
Подача при фрезеровании чугуна | ||||||||
60 | 16 | 6-12 | 0,12-0,08 | 0,10-0,06 | 0,08-0,05 | – | ||
18 | 6-12 | 0,12-0,08 | 0,10-0,06 | 0,08-0,05 | – | |||
75 | 12 | 10-20 | 0,18-0,12 | 0,15-0,10 | 0,12-0,08 | – | ||
20 | 10-20 | 0,12-0,08 | 0,10-0,05 | 0,08-0,05 | – | |||
90 | 12 | 10-20 | 0,08-0,12 | 0,15-0,10 | 0,12-0,08 | – | ||
22 | 10-20 | 0,12-0,08 | 0,10-0,05 | 0,08-0,05 | – | |||
110 | 14 | 12-24 | 0,08-0,12 | 0,15-0,08 | 0,12-0,06 | 0,10-0,05 | ||
15 | 14 | 18-30 | – | 0,18-0,10 | 0,15-0,08 | 0,12-0,06 | ||
200 | 18 | 20-40 | – | 0,20-0,10 | 0,18-0,10 | 0,15-0,08 |
Таблица IV.3.81.
Значение А и показателей степени для определения скорости резания
Тип фрезы из быстро-режущей ста- ли | Обрабатываемые материалы | Величина SZ, мм/зуб | А | ![]() | m | ![]() | ![]() | ![]() | ![]() |
Цилиндри-ческая | Углеродистая сталь, с охлаждением | > 0,1 | 21,2 | 0,45 | 0,33 | 0,3 | 0,4 | 0,1 | 0,1 |
≤ 0,1 | 33 | 0,45 | 0,33 | 0,3 | 0,2 | 0,1 | 0,1 | ||
Чугун серый, НВ 190 без охлаждения | > 0,15 | 13,5 | 0,7 | 0,25 | 0,5 | 0,6 | 0,3 | 0,3 | |
≤ 0,15 | 28,8 | 0,7 | 0,25 | 0,5 | 0,2 | 0,3 | 0,3 | ||
Торцовая | Углеродистая сталь, с охлаждением | > 0,1 | 24,6 | 0,25 | 0,2 | 0,1 | 0,4 | 0,15 | 0,1 |
≤ 0,1 | 38,8 | 0,25 | 0,2 | 0,1 | 0,2 | 0,15 | 0,1 | ||
Чугун серый, НВ 190 без охлаждения | – | 21,0 | 0,2 | 0,15 | 0,1 | 0,4 | 0,1 | 0,1 | |
Дисковая | Углеродистая сталь, ![]() | – | 41 | 0,25 | 0,2 | 0,3 | 0,2 | 0,1 | 0,1 |
Чугун серый, НВ 190 без охлаждения | – | 36 | 0,2 | 0,15 | 0,5 | 0,4 | 0,1 | 0,1 | |
Концевая | Углеродистая сталь, ![]() | – | 29,4 | 0,45 | 0,33 | 0,3 | 0,2 | 0,1 | 0,1 |
Чугун серый, НВ 190 без охлаждения | – | 36 | 0,70 | 0,25 | 0,5 | 0,2 | 0,3 | 0,3 |
Таблица IV.3.82.
Поправочные коэффициенты на скорость резания
в зависимости от обрабатываемого материала
Наименование | Твердость, НВ | Прочность стали, ![]() | Коэффициент |
Углеродистые стали | 107-138 | 40-50 | 1,1 |
138-169 | 50-60 | 1,25 | |
169-200 | 60-70 | 1,10 | |
200-231 | 70-80 | 0,80 | |
Хромистые, хромоникелевые, хромованадиевые, хромомолибденовые, хромоникелемолибденовые, хромовольфрамовые, никелевые стали | 146-174 | 50-60 | 1,0 |
174-203 | 60-70 | 0,85 | |
203-230 | 70-80 | 0,75 | |
230-260 | 80-90 | 0,63 | |
260-288 | 90-100 | 0,40 | |
288-317 | 100-110 | 0,35 | |
317-345 | 110-120 | 0,28 | |
– | 120-130 | 0,24 | |
Чугун серый | 140-160 | – | 1,20 |
160-180 | – | 1,10 | |
180-200 | – | 1,0 | |
200-220 | – | 0,90 | |
220-240 | – | 0,80 | |
240-260 | – | 0,75 | |
Чугун ковкий | 120-140 | – | 1,40 |
140-160 | – | 1,20 | |
160-180 | – | 1,10 | |
180-200 | – | 1,00 |
Таблица IV.3.83.
Подготовительно-заключительное время при работе
на фрезерных станках, мин
Способ установки детали | Количество устанавли-ваемых фрез | Длина стола станка, км | ||
750 | 1250 | 1800 | ||
На столе с креплением болтами с планками в тисках или в приспособлении, устанавливаемом вручную | 1-2 | 14 | 16 | 18 |
3-4 | 16 | 18 | 20 | |
В приспособлении, устанавливаемом подъемником, в центрах, в патроне с делительной головкой или делительным приспособлением | 1-2 | 17 | 19 | 21 |
3-4 | 19 | 21 | 23 | |
Добавлять, мин, в случаях: | ||||
Установки двух стоек поддерживающих хобот установки зубчатых колес для нарезания спиралей | – | 2 | 2 | 2 |
Установки вертикальной фрезерной головки | – | 10 | 12 | 14 |
Поворота стола на угол | – | 1 | 1 | 1 |
Установки одного упора | – | 2 | 2,5 | 3 |
Получения исполнителем работы, инструмента и приспособлений | – | 7 | 7 | 10 |
Таблица IV.3.84.
Вспомогательное время на установку и снятие детали
при работе на фрезерных станках, мин
Способ установки детали | Количество устанав-ливаемых деталей | Масса детали, кг (до) | |||||
1,0 | 3,0 | 5,0 | 8,0 | 12,0 | 20,0 | ||
На столе с креплением болтами с планками по обработанной поверхности | 1 | 0,8 | 0,95 | 1,0 | 1,2 | 1,35 | 1,6 |
2 | 1,5 | 1,7 | 1,9 | 2,2 | 2,5 | 3,0 | |
На угольнике с креплением болтами с планками с простой выверкой | 1 | 0,85 | 1,05 | 1,3 | 1,5 | 1,7 | 2,1 |
В тисках с эксцентриковым зажимом без выверки | 1 | 0,19 | 0,21 | 0,25 | 0,29 | 0,34 | 0,39 |
2 | 0,27 | 0,33 | 0,39 | 0,48 | – | – | |
То же, с выверкой | 1 | 0,39 | 0,43 | 0,48 | 0,56 | 0,64 | 0,79 |
В тисках с винтовым зажимом с креплением рукояткой или ключом без выверки | 1 | 0,27 | 0,29 | 0,32 | 0,36 | 0,41 | 0,46 |
2 | 0,35 | 0,40 | 0,45 | 0,55 | – | – | |
То же, с выверкой | 1 | 0,47 | 0,51 | 0,55 | 0,63 | 0,71 | 0,80 |
В тисках с винтовым зажимом с креплением воротком без выверки | 1 | 0,23 | 0,25 | 0,28 | 0,30 | – | – |
2 | 0,31 | 0,36 | 0,41 | 0,49 | – | – | |
То же, с выверкой | 1 | 0,45 | 0,50 | 0,54 | 0,62 | – | – |
В центрах без надевания хомутика | 1 | 0,26 | 0,34 | 0,43 | 0,48 | 0,55 | 0,60 |
То же, с надеванием хомутика | 2 | 0,35 | 0,44 | 0,55 | 0,60 | 0,75 | 0,85 |
На гладкой или шлицевой центровой оправке при свободном надевании детали от руки | 1 | 0,35 | 0,44 | 0,55 | 0,60 | 0,75 | 0,85 |
То же, при надевании с помощью молотка | 2 | 0,38 | 0,48 | 0,56 | 0,67 | 0,78 | 0,86 |
То же, при надевании с помощью пресса | 3 | 0,49 | 0,60 | 0,75 | 0,85 | 1,00 | 1,20 |
На центровой оправке с гайкой с шайбой простой | 1 | 0,65 | 0,75 | 0,85 | 0,95 | 1,05 | 1,10 |
То же, с шайбой быстросъемной | 2 | 0,49 | 0,60 | 0,65 | 0,75 | 0,85 | 0,90 |
Установка на оправу каждой последующей детали (свыше одной) | 1 | 0,09 | 0,10 | 0,12 | – | – | – |
В самоцентрирующем патроне | 2 | 0,18 | 0,18 | 0,22 | 0,26 | 0,32 | 0,39 |
То же с поджатием центром задней бабки | 2 | 0,34 | 0,39 | 0,45 | 0,50 | 0,55 | 0,60 |
В специальном приспособлении с базированием по одной или двум плоскостям или с одним-двумя упорами, или с креплением поворотной или скользящей планкой с зажимом рукояткой эксцентрика | 1 | 0,14 | 0,18 | 0,19 | 0,22 | 0,23 | 0,26 |
На каждый последующий зажим | 1 | 0,05 | 0,05 | 006 | 0,06 | 0,08 | 0,08 |
То же, с креплением накидной крышкой с зажимом рукояткой эксцентрика | 2 | 0,18 | 0,22 | 0,24 | 0,27 | 0,29 | 0,35 |
На каждый последующий зажим | 1 | 0,09 | 0,11 | 0,11 | 0,11 | 0,14 | 0,14 |
То же с креплением накидной крышкой с зажимом гайкой (гаечным ключом) | 2 | 0,33 | 0,40 | 0,47 | 0,51 | 0,55 | 0,63 |
На каждый последующий зажим | 1 | 0,16 | 0,16 | 0,21 | 0,23 | 0,26 | 0,29 |
Таблица IV.3.85.
Вспомогательное время на установку и снятие детали при работе
на фрезерных станках пневмо- или электроталью, мин
Способ установки детали на столе станка | Масса детали, кг (до) | ||||||
30 | 50 | 80 | 120 | 200 | 300 | 500 | |
На столе с креплением болтами с планками по обработанной поверхности | 2,8 | 3,0 | 3,3 | 3,6 | 4,0 | 4,4 | 5,3 |
На угольнике с креплением болтами с планками с простой выверкой | 5,5 | 6,0 | 7,0 | – | – | – | – |
На столе в тисках с эксцентриковым зажимом без выверки | 2,3 | 2,5 | 2,8 | 3,1 | 3,5 | 3,9 | 4,8 |
То же, с выверкой | 2,8 | 3,0 | 3,3 | 3,6 | 4,0 | 4,4 | 5,3 |
Дополнительное время на очистку приспособления от стружки, мин
Способ очистки | Без выступов и впадин | С выступами и впадинами | Коробчатое | ||||||
Размеры очищаемой поверхности, см | |||||||||
10∙10 | 20∙30 | 30∙50 | 10∙10 | 20∙30 | 30∙50 | 10∙10 | 20∙30 | 30∙50 | |
Сжатым воздухом | 0,06 | 0,07 | 0,08 | 0,08 | 0,09 | 0,11 | 0,10 | 0,12 | 0,14 |
Щеткой или тряпкой | 0,06 | 0,08 | 0,10 | 0,08 | 0,11 | 0,13 | 0,10 | 0,15 | 0,17 |
Таблица IV.3.86.
Вспомогательное время, связанное с переходом при фрезеровании плоскостей (время на ход), мин
Характер работы | Длина станка, мм | |||||||
750 | 1250 | 1800 | ||||||
Длина обрабатываемой поверхности, мм (до) | ||||||||
100 | 200 | 100 | 200 | 300 | 100 | 200 | 300 | |
Фрезой установленной на размер | 0,12 | 0,17 | 0,15 | 0,21 | 0,26 | 0,18 | 0,26 | 0,24 |
С установкой фрезы на размер в одной плоскости: | ||||||||
по упору | 0,28 | 0,33 | 0,33 | 0,39 | 0,44 | 0,40 | 0,48 | 0,56 |
по разметке | 0,46 | 0,51 | 0,55 | 0,61 | 0,66 | 0,67 | 0,75 | 0,83 |
по лимбу | 0,30 | 0,35 | 0,36 | 0,42 | 0,47 | 0,43 | 0,51 | 0,59 |
по шаблону приспособления и щупу | 0,38 | 0,43 | 0,44 | 0,50 | 0,53 | 0,53 | 0,61 | 0,69 |
С установкой фрезы на размер в двух плоскостях: | ||||||||
по упору | 0,41 | 0,46 | 0,47 | 0,53 | 0,58 | 0,57 | 0,65 | 0,73 |
по разметке | 0,66 | 0,71 | 0,77 | 0,83 | 0,88 | 0,94 | 1,02 | 1,10 |
по лимбу | 0,45 | 0,50 | 0,53 | 0,59 | 0,64 | 0,63 | 0,71 | 0,79 |
по шаблону приспособления и щупу | 0,61 | 0,66 | 0,69 | 0,75 | 0,80 | 0,83 | 0,91 | 0,99 |
С взятием одной пробной стружки с измерением линейкой или шаблоном: | ||||||||
при размере 100мм | 0,53 | 0,58 | 0,64 | 0,70 | 0,75 | 0,76 | 0,84 | 0,92 |
при размере 300мм | 0,55 | 0,60 | 0,66 | 0,72 | 0,77 | 0,78 | 0,86 | 0,94 |
То же, с измерением штангенциркулем: | ||||||||
при размере 100мм | 0,58 | 0,63 | 0,69 | 0,75 | 0,80 | 0,81 | 0,89 | 0,97 |
при размере 300мм | 0,67 | 0,72 | 0,78 | 0,84 | 0,89 | 0,90 | 0,98 | 1,06 |
С взятием двух пробных стружек с измерением линейкой или шаблоном; | ||||||||
при размере 100мм | 0,85 | 0,90 | 1,00 | 1,06 | 1,11 | 1,17 | 1,25 | 1,33 |
при размере 300мм | 0,91 | 0,96 | 1,06 | 1,12 | 1,17 | 1,23 | 1,31 | 1,39 |
То же, с измерением штангенциркулем: | ||||||||
при размере 100мм | 1,07 | 1,12 | 1,22 | 1,28 | 1,33 | 1,39 | 1,47 | 1,55 |
при размере 300мм | 1,37 | 1,42 | 1,52 | 1,58 | 1,63 | 1,69 | 1,77 | 1,85 |
Примечание. К вспомогательному времени, связанному с переходом при перемещении стола вручную, добавляется время, равное 0,05 мин на каждые 100 мм хода стола, сверх указанных в таблице.
Таблица IV.3.87.
Вспомогательное время на дополнительные приемы работы,
связанные с переходом, мин
Наименование приемов работы | Длина стола станка, мм | ||
750 | 1250 | 1800 | |
Изменить частоту вращения шпинделя: | |||
одним рычагом | 0,04 | 0,04 | 0,05 |
двумя рычагами | 0,06 | 0,06 | 0,08 |
Изменить величину подачи: | |||
одним рычагом | 0,03 | 0,03 | 0,04 |
двумя рычагами | 0,05 | 0,05 | 0,06 |
Повернуть делительную головку или делительное приспособление на одну позицию | 0,04 | 0,04 | 0,04 |
Повернуть приспособление с рабочей позиции на загрузочную | – | 0,09 | 0,09 |
Поставить щиток ограждения от стружки и снять | 0,16 | 0,18 | 0,20 |
Примечание. Время обслуживания рабочего места см. в табл.IV.3.62
Дата добавления: 2018-11-24; просмотров: 375; Мы поможем в написании вашей работы! |
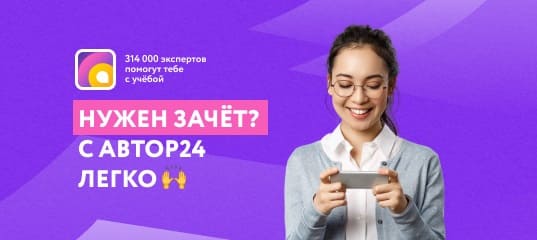
Мы поможем в написании ваших работ!