Техническое нормирование слесарных работ
В авторемонтном производстве слесарные работы применяются при устранении дефектов у изношенных и поврежденных деталей автомобиля. Технологический процесс при выполнении слесарных работ не делится на переходы и приемы. В заводской практике принято только схематически намечать порядок операций.
Примерный перечень дефектов и слесарных операций, применяемых для их устранения:
Забоины и заусенцы на рабочих поверхностях, полученные в результате разборки, и ступенчатый износ – опиливание личным напильником;
Забитость или заваливание резьбы внутренней и наружной – прогонка (калибровка);
Погнутость стержневых деталей (тяг, поводков) – правка на плите молотком;
Забитость или износ цилиндрических и конических отверстий – развертывание цилиндрическими или коническими развертками;
Залом винтов – вывертывание экстрактором;
Срыв внутренней резьбы на базисных деталях, устраняемый постановкой дополнительной ремонтной детали (ДР) – рассверливание резьбы и нарезание новой резьбы под постановку ДР, завертывание ДР, сверление отверстия Ø 3мм под запорный шрифт, отрезание и забивка шрифта, опиливание и зачистка ДР заподлицо с основным материалом детали;
Тот же дефект, но устраняемый заваркой изношенной резьбы – рассверливание резьбы под заварку, зачистка или опиливание наплавленного места, разметка и кернение по шаблону места сверления гнезда под новую резьбу, снятие фаски в гнезде, нарезание резьбы;
|
|
Трещины на базовых деталях, устраняемые заваркой, - сверление на концах трещины отверстий Ø 3-5мм; разделка (расфасовка) крейцмесселем трещин от отверстия до отверстия; заварка трещины, зачистка сварочных швов наждачным кругом или опиливание поверхности напильником;
Трещины на тонкостенных деталях кузова – вырезание и приварка заплаты, зачистка сварочных швов наждачным кругом или опиливание поверхности напильником;
Коррозионное повреждение деталей – вырезание пораженных поверхностей коррозией, приварка ДР; зачистка сварочных швов наждачным кругом.
Для технического нормирования приведенного перечня слесарных работ по устранению дефектов предусмотрены соответствующие нормативные таблицы.
Подготовительно-заключительное время и время на обслуживание рабочего места приведены в разделе нормирования работ по восстановлению автомобильных деталей полимерными материалами (см. табл. IV.3.33. и IV.3.34).
Время на все виды слесарных работ приведено в табл. IV.3.99.- IV.3.114.
Таблица IV.3.99.
Время на установку и снятие одной детали из тисков, мин
Масса детали, кг | Крепление в остальных губках тисков
| Крепление с медными съемными губками | ||||
Крепление и открепление | Перевертывание | Крепление и открепление | Перевертывание | |||
0,5 | 0,14 | 0,05 | 0,19 | 0,08 | ||
1,0 | 0,18 | 0,08 | 0,25 | 0,12 | ||
1,5 | 0,20 | 0,10 | 0,28 | 0,14 | ||
2,0 | 0,22 | 0,11 | 0,31 | 0,17 | ||
2,5 | 0,24 | 0,13 | 0,34 | 0,19 | ||
3,0 | 0,26 | 0,14 | 0,36 | 0,21 | ||
4,0 | 0,28 | 0,16 | 0,40 | 0,24 | ||
5,0 | 0,30 | 0,19 | 0,42 | 0,27 | ||
10,0 | 0,39 | 0,25 | 0,55 | 0,35 |
Примечание. Приведенные нормы времени предусматривают установку детали простой конфигурации без выверки. При креплении детали средней сложности по конфигурации применяют коэффициент К=1,4; сложной конфигурации – К=1,8; установка детали с простой выверкой – К=1,25; то же, со сложной выверкой К=1,50.
Таблица IV.3.100.
Время на зачистку заусенцев или снятие фаски личным напильником, мин
Сталь . Комплекс приемов: 1. Взять напильник. 2. Зачистить кромки напильником. 3. Положить напильник на место.
Зачистка кромки по прямой и ломанной | ||||||
Длина зачищаемой кромки, мм (до) | Характеристика обрабатываемой кромки | |||||
Прямая наружная | Прямая внутренняя | Ломанная наружная | Ломанная внутренняя | |||
20 | 0,32 | 0,35 | 0,38 | 0,42 | ||
30 | 0,36 | 0,40 | 0,43 | 0,47 | ||
50 | 0,43 | 0,47 | 0,51 | 0,56 | ||
70 | 0,50 | 0,55 | 0,60 | 0,66 | ||
100 | 0,54 | 0,59 | 0,64 | 0,70 | ||
200 | 0,68 | 0,75 | 0,81 | 0,89 | ||
Зачистка кромки по цилиндрической поверхности
| ||||||
Диаметр отверстия, мм (до) | Характеристика обрабатываемой кромки | |||||
По внутреннему диаметру | По наружному диаметру | |||||
20 | 0,43 | 0,50 | ||||
40 | 0,57 | 0,85 | ||||
60 | 0,67 | 1,01 | ||||
90 | 0,79 | 1,18 | ||||
130 | 0,91 | 1,36 |
Примечания. 1. Табличные данные предусматривают радиус закругления снимаемой фаски до 0,5мм в удобном для работы положении. При работе в неудобном положении табличные данные следует умножать на коэффициент К=1,1/1,3, 2. При обработке других материалов таблицы данные следует умножать на коэффициенты: для стали – К =0,9; для стали
; для чугуна средней твердости –К=0,8; для медных сплавов – К=0,8; для алюминиевых сплавов –К=0,6. 3. При другой ширине снимаемой фаски используются следующие коэффициенты: для фаски шириной от 0,5 до 1,0мм – К=1,2; для ширины фаски от 1,0 до 1,5мм – К=1,4; для снятия заусенцев по кромке без фаски – К=0,3.
Таблица IV.3.101.
Время на снятие заусенцев после сверления в отверстиях зенковкой вручную, мин
Комплекс приемов:
1. Взять зенковку и вороток.
2. Снять заусенцы в отверстиях.
3. Положить на место зенковку и вороток.
Число зачищаемых отверстий, до | Обрабатываемый материал | ||
Сталь ![]() | Сталь свыше ![]() | Алюминиевые и цветные сплавы | |
1 | 0,10 | 0,11 | 0,08 |
2 | 0,15 | 0,19 | 0,13 |
3 | 0,20 | 0,26 | 0,17 |
4 | 0,25 | 0,32 | 0,22 |
5 | 0,30 | 0,38 | 0,26 |
6 | 0,34 | 0,43 | 0,29 |
8 | 0,43 | 0,54 | 0,36 |
10 | 0,51 | 0,63 | 0,43 |
Примечание. 1. Табличные данные предусматривают снятие заусенцев в отверстиях с образованием фаски до 0,5 мм при диаметре отверстия до 15 мм.
|
|
2. При обработке отверстий ручным шабером табличные данные следует умножать на коэффициент К = 1,6.
3. При обработке отверстий после нарезания резьбы табличные данные следует умножать на коэффициент К = 0,8.
Таблица IV.3.102.
Время на опиливание открытых поверхностей ( ) вручную, мин
Комплекс приемов:
1. Взять напильник и подвести к обрабатываемой поверхности.
2. Опилить поверхность.
3. Очистить от стружки обрабатываемую поверхность и напильник.
4. Положить напильник на место.
Ширина опиливаемой поверхности, см (до) | Припуск на обработку, мм | ||||||
До 0,1 | 0,1-0,2 | 0,2-0,3 | 0,3-0,4 | 0,4-0,5 | 0,5-0,6 | 0,6-0,8 | |
1,0 | 0,09 | 0,150 | 0,200 | 0,245 | 0,290 | 0,330 | 0,410 |
2,0 | 0,070 | 0,115 | 0,155 | 0,190 | 0,225 | 0,260 | 0,320 |
3,0 | 0,077 | 0,130 | 0,175 | 0,220 | 0,225 | 0,295 | 0,360 |
4,0 | 0,084 | 0,140 | 0,185 | 0,230 | 0,270 | 0,310 | 0,380 |
5,0 | 0,089 | 0,145 | 0,195 | 0,240 | 0,280 | 0,320 | 0,400 |
6,0 | 0,094 | 0,155 | 0,210 | 0,255 | 0,295 | 0,345 | 0,420 |
7,0 | 0,098 | 0,161 | 0,220 | 0,270 | 0,320 | 0,360 | 0,440 |
8,0 | 0,102 | 1,169 | 0,230 | 0,280 | 0,340 | 0,380 | 0,460 |
9,0 | 0,105 | 0,173 | 0,235 | 0,290 | 0,345 | 0,390 | 0,480 |
10,0 | 0,108 | 0,180 | 0,240 | 0,300 | 0,350 | 0,400 | 0,500 |
Примечания. 1. Приведенное в таблице время предусматривает опиливание вручную плоских открытых поверхностей длиной более 3,1см, сопрягаемых с одной поверхностью, на верстаке в слесарных тисках при выполнении работы в удобном положении на деталях, изготовленных из углеродистой стали .
2. При измененных условиях обработки вводятся поправочные коэффициенты: для углеродистой стали , для стали хромоникелевой
; для чугуна НВ 140-180-К=0,70; для бронзы НВ 60-80-К=0,60; для меди, латуни средней твердости – К = 0,45
3. При обработке поверхности длиной до 1,0см – К=1,85; 1,1 – 3,0см – К=1,50
4. При обработке в неудобном положении К = 1,26.
Таблица IV.3.103.
Время на зачистку поверхности ( ) наждачным кругом с гибким валом, мин
Комплекс приемов:
1. Взять и включить наждачный круг.
2. Зачистить поверхность.
3. Выключить наждачный круг и отложить его на место.
Ширина зачищаемой поверхности, см | Зачищаемая поверхность, | |||
15 | 30 | 80 | 200 | |
0,5-1,0 | 0,023 | 0,020 | 0,017 | 0,015 |
1,1-1,5 | 0,026 | 0,023 | 0,020 | 0,017 |
1,6-2,0 | 0,029 | 0,025 | 0,022 | 0,019 |
2,1-3,5 | 0,034 | 0,031 | 0,026 | 0,023 |
3,6-4,5 | 0,043 | 0,038 | 0,033 | 0,028 |
Примечания. 1.Приведенное в таблице время рассчитано на зачистку деталей из стали до и величину снимаемого слоя толщиной 0,1 мм.
2. При изменении условий обработки вводятся поправочные коэффициенты: при величине снимаемого слоя до 0,15 мм – К=1,3; до 0,17 мм – К = 1,4; до 0,20 мм – К = 1,6; до 0,25 мм – К=1,9; до 0,3 мм – К = 2,1; до 0,4мм – К = 2,6. при обработке стали применяется коэффициент К = 1,1; чугуна средней твердости – К = 0,7.
3. На включение и выключение наждачного круга с гибким валом следует принимать время, равное 0,7 мин.
Таблица IV.3.104.
Время на обработку поверхностей крейцмейслем (вырубка канавок), мин
Комплекс приемов:
1. Взять крейцмейсель и молоток.
2. Вырубить канавку или паз.
3. Зачистить канавку или паз напильником.
4. Измерить обработанную канавку или паз.
5. Отложить инструмент на верстак.
6. Очистить верстак и тиски от стружки.
Длина вырубаемой канавки, мм | Размеры канавки | |||||||
4 × 2мм | 8 × 4мм | |||||||
Обрабатываемый материал | ||||||||
Сталь σВ=40÷60, кгс/мм | Чугун НВ 100-180, кгс/мм2 | Бронза средней твердости | Баббит средней твердости | Сталь σВ=40÷60, кгс/мм | Чугун НВ 100-180, кгс/мм2 | Бронза средней твердости | Баббит средней твердости | |
50 | 0,335 | 0,226 | 0,177 | 0,158 | 0,460 | 0,310 | 0,243 | 0,210 |
75 | 0,318 | 0,215 | 0,167 | 0,145 | 0,466 | 0,295 | 0,230 | 0,200 |
100 | 0,310 | 0,208 | 0,163 | 0,142 | 0,425 | 0,286 | 0,224 | 0,195 |
125 | 0,292 | 0,198 | 0,155 | 0,134 | 0,403 | 0,271 | 0,212 | 0,184 |
150 | 0,284 | 0,193 | 0,150 | 0,131 | 0,390 | 0,264 | 0,206 | 0,179 |
175 | 0,275 | 0,186 | 0,145 | 0,126 | 0,378 | 0,255 | 0,200 | 0,172 |
200 | 0,271 | 0,183 | 0,143 | 0,124 | 0,372 | 0,251 | 0,197 | 0,170 |
Примечания. 1. Приведенное в таблице время рассчитано на вырубку канавок крейцмейселем вручную на верстаке в слесарных тисках.
2. При изменении условий обработки вводятся поправочные коэффициенты: при обработке на месте (неудобное выполнение работы) – К = 1,1÷1,25; при вырубке канавок на плоских поверхностях – К = 0,8; на цилиндрических внешних поверхностях – К = 1,15; на внутренних цилиндрических (Ø 100мм) разъемных поверхностях – К = 1,0; для прямых канавок – К = 1,00; ломанных канавок – К = 1,15; кривых канавок – К = 1,20.
3. При вырубке канавок с промежуточными размерами время определяется интерполяцией.
Таблица IV.3.105.
Время на разметку отверстий чертилкой через сопрягаемую деталь или через шаблон, мин
Комплекс приемов:
Наметить контур отверстия чертилкой через отверстие сопрягаемой детали или шаблон.
Материал | Первое отверстие | Последующие отверстия | ||||||
Диаметр отверстия, мм (до) | ||||||||
10 | 20 | 30 | 50 | 10 | 20 | 30 | 50 | |
Сталь | 0,12 | 0,15 | 0,17 | 0,19 | 0,10 | 0,12 | 0,14 | 0,16 |
Примечания. 1. Поправочные коэффициенты при размете контура отверстия по шаблону – К=0,7.
2. То же, в неудобных стесненных местах – К=1,1÷1,3
3. То же, на цветных и алюминиевых сплавах – К=0,75.
Таблица IV.3.106.
Время на керновку по разметке или шаблону, мин
Комплекс приемов:
1. Взять кернер и молоток.
2. Кернить.
3. Отложить кернер и молоток на место.
Число намечаемых точек | Кернить по разметке | Кернить по шаблону | ||||||
Сталь σВ = кгс/мм2 | Алюминиевые и цветные сплавы | Сталь σВ = кгс/мм2 | Алюминиевые и цветные сплавы | |||||
30-40 | 41-60 | 61 и выше | 30-40 | 41-60 | 61 и выше | |||
1 | 0,15 | 0,16 | 0,17 | 0,13 | 0,15 | 0,16 | 0,17 | 0,13 |
2 | 0,24 | 0,25 | 0,27 | 0,21 | 0,23 | 0,24 | 0,25 | 0,19 |
3 | 0,32 | 0,34 | 0,36 | 0,27 | 0,29 | 0,30 | 0,32 | 0,24 |
4 | 0,39 | 0,41 | 0,43 | 0,33 | 0,34 | 0,36 | 0,38 | 0,29 |
5 | 0,46 | 0,48 | 0,51 | 0,39 | 0,39 | 0,41 | 0,43 | 0,33 |
6 | 0,52 | 0,55 | 0,58 | 0,45 | 0,44 | 0,46 | 0,48 | 0,37 |
8 | 0,64 | 0,67 | 0,71 | 0,55 | 0,52 | 0,55 | 0,57 | 0,44 |
10 | 0,75 | 0,79 | 0,83 | 0,64 | 0,60 | 0,63 | 0,66 | 0,51 |
Таблица IV.3.107.
Время на сверление отверстий дрелью, мин
Комплекс приемов:
1. Взять дрель, включить и подвести к обрабатываемой детали.
2. Просверлить отверстие.
3. Отложить дрель на место.
4. Очистить от стружки сверло и обрабатываемое отверстие.
Длина просверливаемого отверстия, мм | Диаметр просверливаемого отверстия, мм | |||||||
3 | 4 | 5 | 6 | 7 | 8 | 9 | 10 | |
Сверление электродрелью | ||||||||
3 | 0,190 | 0,182 | 0,167 | 0,180 | 0,190 | 0,210 | 0,220 | 0,230 |
5 | 0,280 | 0,260 | 0,240 | 0,260 | 0,270 | 0,300 | 0,320 | 0,340 |
7 | 0,420 | 0,390 | 0,360 | 0,380 | 0,410 | 0,440 | 0,470 | 0,490 |
10 | 0,570 | 0,550 | 0,500 | 0,510 | 0,540 | 0,590 | 0,620 | 0,650 |
15 | 0,700 | 0,650 | 0,600 | 0,640 | 0,670 | 0,740 | 0,770 | 0,820 |
20 | – | 0,770 | 0,710 | 0,760 | 0,800 | 0,870 | 0,930 | 0,970 |
25 | – | – | 0,830 | 0,850 | 0,890 | 0,970 | 1,030 | 1,080 |
Сверление пневматической дрелью | ||||||||
3 | 0,069 | 0,065 | 0,060 | 0,069 | 0,074 | 0,076 | – | – |
5 | 0,117 | 0,108 | 0,100 | 0,110 | 0,115 | 0,126 | 0,132 | 0,139 |
7 | 0,164 | 0,156 | 0,144 | 0,155 | 0,164 | 0,181 | 0,190 | 0,198 |
10 | 0,240 | 0,223 | 0,206 | 0,223 | 0,232 | 0,258 | 0,276 | 0,292 |
15 | 0,360 | 0,335 | 0,310 | 0,327 | 0,353 | 0,380 | 0,405 | 0,421 |
20 | 0,490 | 0,474 | 0,430 | 0,440 | 0,465 | 0,510 | 0,535 | 0,560 |
25 | 0,600 | 0,560 | 0,515 | 0,550 | 0,575 | 0,635 | 0,660 | 0,710 |
Примечания. 1. Приведенное в таблице время предусматривает сверление отверстий на верстаке в слесарных тисках при удобном положении исполнителя, материал сверла быстрорежущая сталь, обрабатываемый материал сталь σВ = 50 кгс/мм2.
2. При изменении указанных условий применяются следующие коэффициенты: при обработке стали σВ = 40÷60 кгс/мм2 – К = 1; то же стали σВ = 61÷80 кгс/мм2 – К = 1,15; хромоникелевой σВ = 60÷80 кгс/мм2 – К = 1,20; чугуна НВ = 140÷180 – К=0,70; бронзы средней твердости – К=0,60; меди латуни средней твердости – К=0,45; при обработке электродрелью n = 1200 об/мин – К=1,0; то же, n = 2000 об/мин – К = 0,75;при обработке пневмодрелью n = 1400 об/мин – К = 1; то же n = 2000 об/мин – К = 0,75; при обработке сверлами из углеродистой стали – К = 1,20.
3.На включение и выключение дрели принимается время 0,5 мин.
4. Вспомогательное время на установку и снятие детали, смену сверл принимается по табл. IV.3.108.
Таблица IV.3.108.
Время на установку, снятие детали и смену сверла при сверлении отверстий вручную, мин
Характер установки и снятия детали | Масса детали, кг | |||||||
1 | 2 | 3 | 4 | 5 | 6 | 8 | 10 | |
Установка и снятие детали на верстаке без крепления | 0,12 | 0,13 | 0,14 | 0,15 | 0,16 | 0,17 | 0,18 | 0,19 |
Установка с креплением и снятие детали в слесарных тисках | 0,26 | 0,28 | 0,30 | 0,32 | 0,34 | 0,36 | 0,37 | 0,39 |
Установка детали на верстаке с креплением струбцинами и снятие | 0,31 | 0,34 | 0,36 | 0,38 | 0,41 | 0,43 | 0,45 | 0,47 |
Установка детали на верстаке с креплением прижимными планками и снятие | 0,35 | 0,38 | 0,41 | 0,43 | 0,46 | 0,49 | 0,51 | 0,53 |
Продолжение табл. IV.3.108.
Конструкция приспособления | Взять сверло, установить в патрон, вынуть и отложить на место | Взять патрон со сверлом, вставить в конус дрели, вынуть и отложить на место | Взять сверло, вставить в конус дрели, вынуть и отложить на место |
Электродрель | 0,17 | 0,19 | 0,13 |
Пневмодрель | 0,15 | 0,17 | 0,12 |
Таблица IV.3.109.
Время на развертывание отверстий ручной разверткой
при припуске на диаметр 0,15-0,20мм, мин
Комплекс приемов:
1. Взять развертку и вороток.
2. Развернуть отверстие.
3. Очистить развертку от стружки и отложить развертку и вороток на место.
Длина развертывания, мм (до) | Цилиндрическое развертывание | Коническое развертывание | ||||||||
Диаметр развертывания, мм (до) | Наибольший диаметр развертывания, мм (до) | |||||||||
5 | 6 | 10 | 15 | 20 | 5 | 6 | 10 | 15 | 20 | |
3 | 0,30 | 0,28 | 0,33 | 0,39 | 0,44 | 0,42 | 0,39 | 0,46 | – | – |
5 | 0,39 | 0,36 | 0,43 | 0,51 | 0,57 | 0,54 | 0,51 | 0,60 | 0,71 | – |
7 | 0,46 | 0,43 | 0,51 | 0,60 | 0,67 | 0,64 | 0,60 | 0,71 | 0,84 | 0,94 |
10 | 0,55 | 0,51 | 0,61 | 0,71 | 0,80 | 0,77 | 0,71 | 0,85 | 1,00 | 1,12 |
14 | 0,64 | 0,60 | 0,71 | 0,84 | 0,94 | 0,90 | 0,84 | 1,00 | 1,17 | 1,32 |
20 | 0,77 | 0,72 | 0,86 | 1,01 | 1,13 | 1,08 | 1,01 | 1,20 | 1,41 | 1,59 |
25 | 0,87 | 0,81 | 1,00 | 1,18 | 1,32 | 1,22 | 1,14 | 1,40 | 1,65 | 1,85 |
32 | 1,04 | 0,97 | 1,19 | 1,40 | 1,57 | 1,45 | 1,35 | 1,53 | 1,96 | 2,20 |
40 | – | 1,13 | 1,39 | 1,64 | 1,84 | 1,70 | 1,58 | 1,95 | 2,29 | 2,57 |
50 | – | – | 1,63 | 1,91 | 2,15 | – | 1,85 | 2,28 | 2,68 | 3,00 |
Примечания. 1. Табличные данные предусматривают развертывание сквозных отверстий развертками из сталей У10А,У12А, 9ХВС в обрабатываемой стали σВ = 41÷60 кгс/мм2
2. При развертывании отверстий развертками из быстрорежущей стали следует применять коэффициент К = 0,7.
3. Те же, из других материалов или при условиях работы, отличающихся от предусмотренных табличными данными, следует применять коэффициенты:
при припуске на диаметр 0,05-0,1мм – К=0,8:
при обработке стали σВ = 30÷40 кгс/мм2 – К=0,9; то же, стали σВ = 60÷80 кгс/мм2 – К=1,1; то же, чугуна средней твердости К=0,7; то же, бронзы средней твердости – К=0,75; то же, латуни – К = 0,8; то же, алюминиевых сплавов – К=0,65.
при калибровании отверстий – К=0,55;
при развертывании глухого отверстия – К=1,6;
при развертывании соосных отверстий – К=1,25;
при работе в неудобных или стесненных местах – К=1,1÷1,3.
Таблица IV.3.110.
Время нарезания резьбы вручную в отверстиях метчиком
и на стержнях плашками на одно отверстие или стержень, мин
Комплекс приемов:
1. Взять вороток с метчиком (клупп с плашками), смазать маслом и подвести к изделию.
2. Нарезать резьбу в отверстии (на стержне).
3. Отложить метчик и вороток (клупп с плашками) на место.
4. Очистить развертку от стружки метчик (плашку) и обрабатываемую деталь.
Длина нарезаемой резьбы, мм | Диаметр нарезаемого отверстия, мм | |||||||
5 | 6 | 8 | 10 | 12 | 14 | 18 | 20 | |
Шаг нарезаемой резьбы, мм | ||||||||
0,8 | 1,0 | 1,25 | 1,5 | 1,75 | 2,0 | 2,5 | 2,5 | |
Нарезание резьбы в отверстиях | ||||||||
5 | 1,42 | 1,30 | 1,15 | 1,06 | – | – | – | – |
10 | 2,21 | 2,05 | 1,81 | 1,66 | 1,54 | 1,44 | – | – |
15 | 2,90 | 2,68 | 2,37 | 2,18 | 2,02 | 1,89 | 2,07 | 2,28 |
20 | 3,50 | 3,20 | 2,83 | 2,60 | 2,41 | 2,26 | 2,48 | 2,74 |
25 | 4,00 | 3,70 | 3,27 | 3,03 | 2,80 | 2,62 | 2,88 | 3,18 |
30 | – | 4,20 | 3,71 | 3,42 | 3,17 | 2,97 | 3,26 | 3,60 |
35 | – | – | 4,05 | 3,73 | 3,45 | 3,23 | 3,54 | 3,90 |
40 | – | – | 4,42 | 4,07 | 3,77 | 3,53 | 3,88 | 4,28 |
50 | – | – | – | 4,67 | 4,31 | 4,05 | 4,45 | 4,90 |
Нарезание резьбы на стержнях | ||||||||
5 | 0,65 | 0,60 | 0,54 | 0,50 | – | – | – | – |
10 | 1,10 | 1,03 | 0,93 | 0,86 | 0,76 | 0,75 | – | – |
15 | 1,50 | 1,39 | 1,25 | 1,15 | 1,03 | 1,02 | 1,24 | 1,35 |
20 | 1,85 | 1,71 | 1,54 | 1,43 | 1,28 | 1,26 | 1,55 | 1,69 |
25 | 2,20 | 2,03 | 1,83 | 1,69 | 1,52 | 1,50 | 1,85 | 2,02 |
30 | – | 2,37 | 2,14 | 1,98 | 1,78 | 1,76 | 2,17 | 2,37 |
35 | – | – | 2,41 | 2,23 | 2,00 | 1,97 | 2,43 | 2,66 |
40 | – | – | 2,67 | 2,47 | 2,21 | 2,19 | 2,70 | 2,95 |
50 | – | – | – | 2,87 | 2,57 | 2,53 | 3,12 | 3,41 |
Примечания. 1. Табличные данные предусматривают нарезание резьбы вручную на верстаке в слесарных тисках в удобном положении исполнителя.
2. При изменении условий работы табличные данные умножаются на следующие коэффициенты:
При обработке стали углеродистой σВ = 40÷60 кгс/мм2 – К=1,0; то же, σВ = 60÷80 кгс/мм2 – К=1,15; то же, чугуна НВ 140-180кгс/мм2 – К=0,70; то же, бронзы НВ 70-100 кгс/мм2 – К=0,60;
При глухом отверстии – К=1,20;
При неудобном выполнении работы – К=1,1÷1,35;
При калибровании (прогонке) резьбы – К=0,45.
Таблица IV.3.111.
Время на резку заготовок из сортового металла ручной ножовкой, мин.
Комплекс приемов:
1. Отмерить длину отрезаемой заготовки.
2. Взять с верстака ножовку, поднести к заготовке и установить по разметке.
3. Отрезать заготовку.
4. Очистить ножовочное полотно от стружки и положить на верстак.
Пруток диаметром, мм | Обрабатываемый материал | ||||
Площадь сечения, ![]() | Сталь σВ = 40÷60 кгс/мм2 | Сталь σВ = 61÷80 кгс/мм2 | Чугун НВ 170-200 кгс/мм2 | Бронза σВ =25+35 кгс/мм2 | |
5 | 19,63 | 0,25 | 0,34 | 0,20 | 0,15 |
8 | 50,27 | 0,54 | 0,74 | 0,42 | 0,31 |
10 | 78,54 | 0,80 | 1,08 | 0,60 | 0,45 |
12 | 113,10 | 1,08 | 1,40 | 0,82 | 0,62 |
14 | 153,90 | 1,40 | 1,80 | 1,08 | 0,80 |
16 | 201,00 | 1,70 | 2,30 | 1,30 | 1,00 |
18 | 254,50 | 2,05 | 2,80 | 1,60 | 1,20 |
20 | 314,20 | 2,46 | 3,45 | 1,90 | 1,40 |
Примечания. 1.Табличные данные предусматривают удобное выполнение работы в слесарных тисках при длине режущей части ножовочного полотна l=300мм и при резке металла под углом к его геометрической оси.
2. При изменении условий обработки применяются коэффициенты: при длине ножовочного полотна l=200мм – К=1,15; то же, l=250мм – К=1,10.
Таблица IV.3.112.
Время на резку листового материала ручными рычажными ножницами, мин
Комплекс приемов:
1. Взять заготовку и резать по разметке рычажными ножницами.
2. Отложить заготовку и отходы на место.
Длина реза, мм | Толщина нарезаемого материала, (до) | |||||
0,1 | 0,2 | 0,4 | 0,7 | 1,0 | 2,0 | |
До 50 | 0,12 | 0,14 | 0,17 | 0,19 | 0,21 | 0,25 |
75 | 0,14 | 0,16 | 0,20 | 0,23 | 0,25 | 0,30 |
100 | 0,16 | 0,19 | 0,22 | 0,25 | 0,28 | 0,33 |
150 | 0,18 | 0,22 | 0,26 | 0,30 | 0,33 | 0,39 |
250 | 0,23 | 0,27 | 0,32 | 0,37 | 0,40 | 0,48 |
400 | 0,27 | 0,32 | 0,38 | 0,44 | 0,48 | 0,58 |
600 | 0,32 | 0,38 | 0,46 | 0,52 | 0,57 | 0,68 |
800 | 0,36 | 0,43 | 0,51 | 0,58 | 0,64 | 0,76 |
1000 | 0,39 | 0,47 | 0,56 | 0,64 | 0,70 | 0,83 |
1500 | 0,46 | 0,55 | 0,65 | 0,75 | 0,82 | 0,98 |
Примечания.1. Табличные данные предусматривают резку стали σВ = 40÷60 кгс/мм2 прямолинейного профиля.
2. При резке стали других марок или цветных металлов следует применять коэффициенты: при резке стали σВ = 40 кгс/мм2 – К=0,80; при σВ = 61÷80 кгс/мм2 – К=1,20;латуни – К=0,70; алюминиевых сплавов – К=0,60.
3. При резке криволинейного профиля с радиусом кривизны до 250 мм – К=1,40, то же, свыше 250 мм – К=1,20.
4. При резке материала ручными кровельными ножницами – К=1,60.
Таблица IV.3.113.
Время на правку заготовок из листового и круглого пруткового материала, мин
Комплекс приемов:
1. Взять заготовку и положить на плиту.
2. Править заготовку молотком вручную.
3. Проверить правку по плите на просвет или на ровность прилегания.
4. Отложить молоток и заготовку на место.
Из листового материала
Площадь, | Толщина материала, мм (до) | ||||
1,0 | 1,5 | 2,0 | 3,0 | 4,0 | |
0,1 | 0,56 | 0,49 | 0,43 | 0,52 | 0,65 |
0,2 | 0,69 | 0,61 | 0,53 | 0,64 | 0,78 |
0,3 | 0,77 | 0,68 | 0,59 | 0,71 | 0,89 |
0,5 | 0,90 | 0,79 | 0,69 | 0,83 | 1,04 |
1,0 | 1,11 | 0,98 | 0,85 | 1,02 | 1,28 |
3,0 | 1,53 | 1,36 | 1,18 | 1,42 | 1,77 |
5,0 | 1,79 | 1,59 | 1,38 | 1,66 | 2,07 |
10,0 | 2,21 | 1,96 | 1,70 | 2,04 | 2,55 |
15,0 | 2,60 | 2,30 | 2,00 | 2,40 | 3,00 |
20,0 | 2,91 | 2,58 | 2,24 | 2,69 | 3,36 |
25,0 | 3,19 | 2,82 | 2,45 | 2,82 | 3,53 |
30,0 | 3,43 | 3,04 | 2,64 | 3,17 | 3,96 |
35,0 | 3,65 | 3,23 | 2,81 | 3,37 | 4,22 |
40,0 | 3,85 | 3,40 | 2,96 | 3,55 | 4,44 |
50,0 | 4,21 | 3,73 | 3,24 | 3,89 | 4,86 |
Из круглого пруткового материала
Длина прутка, мм (до) | Диаметр прутка, мм | |||||||
2 | 5 | 7 | 10 | 12 | 15 | 20 | 30 | |
0,15 | 0,14 | 0,18 | 0,22 | 0,27 | 0,30 | 0,35 | 0,41 | 0,52 |
0,25 | 0,18 | 0,23 | 0,28 | 0,35 | 0,39 | 0,45 | 0,53 | 0,68 |
0,35 | 0,21 | 0,27 | 0,33 | 0,41 | 0,46 | 0,53 | 0,63 | 0,80 |
0,45 | 0,24 | 0,31 | 0,38 | 0,47 | 0,52 | 0,60 | 0,71 | 0,91 |
0,70 | 0,29 | 0,39 | 0,47 | 0,59 | 0,65 | 0,75 | 0,89 | 1,13 |
0,90 | 0,33 | 0,44 | 0,54 | 0,66 | 0,74 | 0,85 | 1,01 | 1,29 |
1,20 | 0,38 | 0,51 | 0,62 | 0,77 | 0,86 | 0,98 | 1,15 | 1,48 |
Примечания. 1. Табличные данные предусматривают правку заготовок из стали σВ = 60 кгс/мм2, правку листового материала при отношении длины к ширине заготовки не более l : b=1 : 5 без применения измерительных инструментов.
2. При правке заготовок из других материалов следует применять коэффициенты: при правке заготовок из стали σВ = 40 кгс/мм2 – К=0,9; то же, σВ = 80 кгс/мм2 – К=1,2; то же, из латуни – К=0,80; то же, из алюминиевых сплавов – К=0,70.
3. При отношении длины к ширине 1:10 применять коэффициенты – К=1,15; то же, 1:20 – К=1,25; то же, 1:30 – К=1,35; то же, свыше 1:30 – К=1,45.
4. При правке прутков отклонение от оси в одной плоскости не должно превышать 2 мм.
Таблица IV.3.114.
Время на завертывание в гнездо ремонтируемой детали ввертыша (ДР), мин
Комплекс приемов:
1. Взять деталь, гаечный ключ и специальный ключ с нарезкой на конце и контргайкой.
2. Ввернуть специальный ключ во внутреннее отверстие ввертыша и закрепить контргайкой.
3. Завернуть ввертыш в гнездо ремонтируемой детали.
4. Освободить контргайку и вывернуть специальный ключ.
5. Положить на место гаечный и специальный ключ.
Диаметр резьбы, мм (до) | Длина вывертывания, мм (до) | ||||||
6 | 8 | 12 | 18 | 25 | 35 | 50 | |
6 | 0,28 | 0,31 | 0,38 | – | – | – | – |
8 | 0,30 | 0,34 | 0,41 | 0,49 | – | – | – |
10 | 0,32 | 0,37 | 0,44 | 0,53 | 0,61 | – | – |
16 | – | – | 0,51 | 0,61 | 0,71 | 0,82 | – |
20 | – | – | 0,54 | 0,65 | 0,75 | 0,88 | – |
24 | – | – | – | 0,75 | 0,88 | 1,01 | 1,20 |
30 | – | – | – | – | 1,05 | 1,22 | 1,43 |
Примечания. 1. Таблица отражает нормальные условия работы по завертыванию ввертыша (ДР). При других условиях к табличному времени следует применять коэффициенты:
при выполнении работы в неудобном положении – К=1,1÷1,3;
при уплотнении резьбового соединения смазыванием суриком к табличному времени следует добавлять: при резьбовых соединениях диаметром до 20 мм – 0,45 мин, свыше 20мм – 0,75мин.
Время на вывертывание из тела ремонтируемой детали
сломанного винта (шпильки), мин
Комплекс приемов:
1. Взять экстрактор и молоток.
2. Забить экстрактор в просверленное отверстие в сломанном винте.
3. Вывернуть сломанный винт.
4. Сбить с экстрактора сломанный винт.
5. Положить на место экстрактор и молоток.
Время на проведение комплекса приемов определяется по табл. IV.3.114 с учетом коэффициента К=0,90
Приложение 2
Дата добавления: 2018-11-24; просмотров: 2741; Мы поможем в написании вашей работы! |
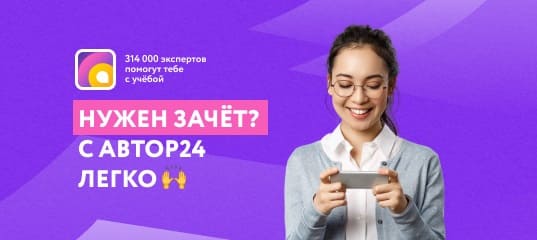
Мы поможем в написании ваших работ!