Техническая документация металлорежущих станков. Транспортирование, установка на фундамент металлорежущих станков
Испытания станков. Виды испытаний.
Испытание и приемка станков после изготовления (а также после ремонта) проводятся в соответствии с техническими условиями, указанными в рабочей документации. Специально выделяются испытания станка на заводе-изготовителе и заводе-за-казчике. В процессе испытания выполняют проверку внешнего вида; испытание оборудования на холостом ходу и под нагрузкой; проверку геометрической точности, жесткости и виброустойчивости; проверку обработанных деталей на соответствие техническим условиям. Все испытания станка на соответствие нормам (точности, жесткости и др.) можно проводить только после выполнения требований, предъявляемых к первоначальному пуску станка.
Первоначальный пуск. Подключить заземление станка к общей цеховой системе заземления, затем станок к электросети, причем напряжение сети должно соответствовать напряжению электрооборудования станка. Ознакомившись с назначением рукояток управления, проверяют вручную работу всех механизмов. Должны быть выполнены все относящиеся к пуску указания, изложенные в Руководстве по эксплуатации конкретной модели станка в разделах «Система смазки» и «Электрооборудование». При отсутствии давления в системе смазки и отсутствии масла в контрольных точках работа на станке недопустима.
После подключения станка к сети проверяют работу электродвигателя (без подключения рабочих органов станка) и смазочную систему (по манометру). Только после этого можно опробовать работу всех механизмов станка на холостом ходу. При испытании оборудования на холостом ходу проверяют механизмы главного движения последовательно на всех режимах (частота вращения шпинделя, двойных ходов ползуна и др.). На максимальной скорости вращения шпинделя станок работает до 2 ч — до стабилизации температуры всех его механизмов, которая не должна быть выше указанной в технической документации: для подшипников качения — 80 °С, подшипников скольжения — 70 °С, других механизмов — 50 °С, для масла гидросистем — 60 °С.
|
|
Во время испытаний станка непрерывно наблюдают за взаимодействием всех механизмов, безотказностью средств автоматики. Особое внимание уделяют проверке работы станочных узлов, подачи СОЖ, функционирования гидравлических и пневматических систем. Одновременно станок проверяют на плавность переключения и вращения маховиков, на отсутствие сильного шума, вибраций. После изготовления деталей-образцов проверяют их точность и шероховатость, результаты фиксируют в протоколах. Проверку геометрической точности и жесткости станков выполняют согласно техническим условиям, составленным в соответствии с действующими ГОСТами на данный тип испытываемого станка.
|
|
Проверка установки. Прежде всего, определяют расположение станков и другого технологического оборудования относительно колонн и чистого пола цеха в горизонтальной и вертикальной плоскостях с помощью рулетки. Точность взаимного расположения станков и устройств в продольном направлении проверяют по штанге конвейера или транспортным планкам (рис. 15.2), а взаимного расположения оборудования по высоте — контрольной линейкой 2, уложенной на поверхности соседних станков 3. На линейку устанавливают уровень 1 с ценой деления 0,01 мм. Допустимая погрешность установки оборудования по высоте в продольном и поперечном направлениях 0,04...0,05 мм на длине 1 м.
Проверка установки и испытания станков
При монтаже оборудования сблокированных линий с жесткой транспортной связью обеспечивают определенные перепады по высоте между верхними плоскостями базовой 6 и промежуточных 4 и 8 планок. Эти перепады составляют при заходе заготовки на базовую планку 0,1 мм, а при сходе с нее — 0,25 мм. Перепады проверяют щупом, определяя зазоры между линейкой 5, приложенной к промежуточной планке 4, и базовой планкой 6 с одной стороны и между линейкой 7, приложенной к базовой планке 6, и промежуточной планкой 8 с другой.
|
|
При монтаже сблокированных линий также проверяют правильность расположения штанги (ленты) и направляющих привода конвейера (рис. 15.3). Щупом толщиной 0,1 мм измеряют зазор между штангой 2 и направляющими роликами 1 при ручном перемещении штанги, отсоединенной от каретки 3 привода 6 конвейера. Одновременно проверяют параллельность штанги 2 относительно направляющих 5 предварительно выверенного привода 6. Для этой проверки используют стойку с индикатором 4, установленную на направляющих привода 6 и перемещаемую на длину хода каретки, при этом измерительный наконечник индикатора касается поверхности штанги.
Дата добавления: 2018-08-06; просмотров: 1398; Мы поможем в написании вашей работы! |
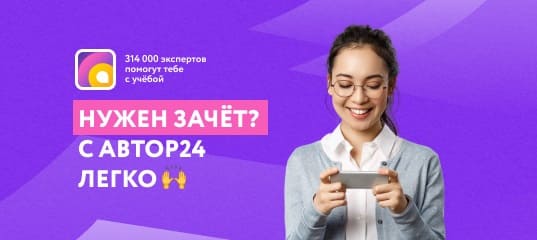
Мы поможем в написании ваших работ!