ПРИМЕНЕНИЕ СТАНКОВ С ЧИСЛОВЫМ ПРОГРАММНЫМ УПРАВЛЕНИЕМ
Станки с программным управлением (ЧПУ) сочетают точность специализированных станков и имеют более высокую производительность, чем станки общего назначения (в 2...5 раз). Однако станки с ЧПУ значительно сложнее обычных, стоимость их пока еще довольно высока и превышает стоимость универсальных станков в 1,2...8 раз. Тем не менее производство станков с ЧПУ благодаря их существенным преимуществам непрерывно увеличивается, следовательно, и стоимость их будет постепенно снижаться.
Область применения станков с ЧПУ достаточно широка как по характеру технологических операций, так и по типам производств, для которых они предназначаются. По последнему признаку созданы и успешно используются станки с ЧПУ как для единичного и мелкосерийного, так и для крупносерийного и массового производства. Так, в настоящее время уже определились следующие возможности использования станков по типам производства:
1) станки с ЧПУ токарной группы применяются в массовом, серийном и единичном производстве;
2) фрезерные, сверлильные и расточные станки с ЧПУ – в серийном и единичном производстве;
3) шлифовальные станки с ЧПУ – в серийном производстве. Данные по возможности использования каждой из моделей
станков с ЧПУ в условиях определенного типа производства приводятся в паспортах станков. Для наиболее распространенных отечественных моделей станков с ЧПУ технические характеристики и оптовые цены приводятся в работе [5].
|
|
В моделях станка для обозначения степени автоматизации добавляется буква Ф с цифрой: Ф1 – станки с цифровой индикацией и преднабором координаты; Ф2 – станки с позиционными и прямоугольными системами; ФЗ – станки с контурными системами; Ф4 – станки с универсальной системой для позиционной и контурной обработки.
К основным условиям целесообразности применения станков с ЧПУ можно отнести следующее:
1) обработку отверстий сложной геометрической формы, требующих применения нескольких последовательно работающих инструментов, а также обработку групп отверстий на сверлильных и расточных станках. Эти виды обработки могут быть выполнены на станках с ЧПУ без изготовления специальной оснастки (кондукторов, копиров и др.), которая обычно применяется на универсальных станках;
2) необходимость построения процесса по принципу концентрации операций, т. е. сосредоточения возможно большего числа однотипных видов обработки на одном рабочем месте;
3) необходимость уменьшения доли вспомогательного времени, которое затрачивается в рассматриваемой операции на приемы, связанные с изменением режимов резания, переходом с обработки одной поверхности на другую, сменой режущего инструмента и прочего, что обычно имеет место при последовательной обработке нескольких поверхностей на универсальных станках;
|
|
4) обработку нескольких аналогичных деталей на одном станке, что имеет место в условиях серийного производства. В этом случае применением станков с ЧПУ можно сократить время на переналадку оборудования;
5) возможность сокращения числа операторов введением многостаночного обслуживания.
Работа по составлению технологической документации о применении станков с ЧПУ включает следующие этапы:
1) составление технологического процесса механической обработки детали и выявление операций, на которых применение станков с ЧПУ принципиально возможно и, по всей вероятности, целесообразно;
2) выбор станка с ЧПУ, который можно было бы применить на намеченных операциях;
3) технологическую разработку чертежа детали (операционного эскиза) для выполнения намеченной операции на станке с ЧПУ;
4) составление расчетно-технологической карты команд и перемещений исполнительных органов станка с ЧПУ;
5) технико-экономическое обоснование применения станка с ЧПУ.
Технологический процесс механической обработки с перспективой применения станков с ЧПУ в отношении последовательности операций обработки, состава операций, расчета режимов резания, выбора моделей станков в принципе подчиняется тем же правилам, что и для станков с иным управлением, т.е. первоначально может быть составлен технологический процесс с ориентацией на обычные станки. Далее анализируются те операции, на которых применение станков с ЧПУ может быть целесообразно. Операции должны быть проанализированы по элементам вспомогательного времени и высказаны соображения о возможности уменьшения вспомогательного времени при переходе на обработку на станке с ЧПУ. Эти соображения на данном этапе могут рассматриваться как предварительные, так как окончательно о выигрыше во времени можно судить только тогда, когда выбран совершенно определенный станок с ЧПУ и операция обработки детали на нем пронормирована с учетом характеристики станка.
|
|
Нормирование операции на станке с ЧПУ может быть выполнено только после переработки чертежа или операционного эскиза таким образом, чтобы он был бы пригоден для составления расчетно-технологической карты команд и перемещений исполнительных органов станка.
|
|
Когда операция пронормирована, необходимо на основании технико-экономического расчета по методике, изложенной в работе [5], показать целесообразность применения станка с ЧПУ вместо, например, универсального станка.
Технологическая переработка чертежа или операционного эскиза для операции, на которую предполагается запроектировать станок с ПУ, ведется различными способами в зависимости от типа и модели станка и характера выполняемой операции. Методические указания по выполнению этой работы изложены в специальной и справочной литературе [9], [27], [30]. Данные, необходимые для выполнения этой работы, содержатся также в технических характеристиках станков с ЧПУ.
Расчетно-технологическая карта составляется на основании подробной разработки операции технологического процесса и переработанного чертежа В карте последовательно указываются все команды для осуществления запроектированной на станке с ЧПУ обработки, скорости и направления перемещения органов станка.
В дальнейшем на основании расчетно-технологической карты данные карты преобразуются в систему команд программоносителя, предусмотренного данным станком. Указания по составлению расчетно-технологических карт также приводятся в литературе [9], [30].
Глава 4. ТЕХНОЛОГИЧЕСКИЕ РАСЧЕТЫ И ДОКУМЕНТАЦИЯ
_________________________________________________________________
РАСЧЕТ РЕЖИМОВ РЕЗАНИЯ
Расчет режимов резания по таблицам. Расчет ведется одновременно с заполнением операционных или маршрутных карт технологического процесса. Совмещение этих работ исключает необходимость дублирования одних и тех же сведений в различных документах, так как в операционных (или маршрутных для серийного производства) картах должны быть записаны данные по оборудованию, способу обработки, характеристике обрабатываемой детали и другие, которые используются для расчетов режимов резания и не должны вторично записываться как исходные данные для выполнения расчета. Элементом, в значительной мере поясняющим ряд исходных данных для расчета режимов резания, является операционный эскиз.
Расчет должен выполняться в той форме и последовательности, которые, дополняя технологическую карту, позволяют сократить время, необходимое для выполнения самого расчета, и свести его в такую систему, которая дает возможность легко проверить отдельные элементы произведенного расчета. С этой целью расчет режимов резания, так же как и другие расчеты в курсовом проекте, предлагается вести в виде карт расчета (расчетных формуляров).
В приложении приведен ряд формуляров для расчета элементов режима резания и основного времени. Они не являются обязательными по форме, так как их построение зависит от конкретных рекомендаций справочной литературы, которой пользовался проектант при расчетах, но порядок выполнения расчетов, предлагаемый в них, в основном будет именно таким, так как это определяется последовательностью расчета режимов резания вообще.
Приведенные формуляры расчетов составлены на основании общемашиностроительных нормативов режимов резания [18]...[21]. Однако не исключено использование и другой справочной литературы, поэтому во всех случаях составления формуляра расчета или даже расчета в произвольной форме после заголовка расчета необходимо дать ссылку на источник, на основании которого выполнен расчет.
Одноинструментная обработка на токарных станках. Все исходные данные для расчета по операции содержатся в операционной карте и эскизе, поэтому здесь должны быть приведены только дополнительные сведения по режущему инструменту. Ход расчета ясен из формуляра и не требует дополнительных пояс нений. Период стойкости резца в расчете не используется и приводится только в сводной таблице по режимам резания. Выбирается период стойкости по таблицам с учетом организационных факторов, как, например, удобные для обслуживания станочного парка сроки смены режущего инструмента.
Расчетное значение частоты вращения, так же как и рас четную величину подачи, согласовывают со значением, приведенным в паспорте станка, выбирая ближайшее меньшее число.
Если в справочниках или каталогах станков не указаны все значения частоты вращения шпинделей, подач и чисел двойных ходов, то принимают во внимание следующее.
Частоты вращения шпинделей металлорежущих станков в РФ нормализованы, поэтому полученные расчетом значения округляются до ближайших, имеющихся в нормальных рядах. Числа двойных ходов в минуту и подачи выбираются из этих рядов. Каждый из таких рядов построен по закону геометрической прогрессии.
В справочниках по металлорежущим станкам указываются обычно числа nmах и nmin оборотов шпинделей, двойных ходов и подач.
Из определения геометрической прогрессии следует, что nmах= nmin∙jm-1.
где m – общее число ступеней скорости соответствующего элемента станка – шпинделя токарного или фрезерного станка, стола продольно-строгального станка и др.; j – знаменатель ряда.
Отсюда можно определить любую из четырех величин – nmax, nmin, j или m, если известны или выбраны значения всех остальных.
Чаще всего необходимо для построения ряда по известным nmax, nmin и mопределить j. В станкостроении принято семь нормализованных гео-метрических рядов соответственно следующим значениям знаменателя j: 1,06; 1,12; 1,26; 1,41; 1,58; 1,78; 2. В современных станках чаще всего применяются средние значения знаменателя j: 1,26; 1,41 или 1,58; другие значения j, особенно меньше 1,26, используются реже.
В тех случаях, когда ряды частоты вращения подач или двойных ходов построены на вышеуказанных нормализованных значениях знаменателя, можно воспользоваться следующей методикой для определения значения j и принятого значения частоты вращения, подачи или двойных ходов. Изформулы для nmax следует jm-1 = nmax/nmin.
Значения нормализованных знаменателей рядов j, возведенные в степень, приведены в прил. 13. Пользуясь таблицей, можно легко определить значение j на основании заданных в технической характеристике станка nmax, nmin и m.
Для этого вычисляем частное nmax/nmin и в строке таблицы, соответ-ствующей степени m – 1, находим то числовое значение jm-1, которое равно или близко вычисленному. В головке графы, в которой приводится это число, указано соответствующее данному ряду значение j.
Затем делим расчетное значение частоты вращения двойных ходов или подачи на минимальное и получаем расчетное значение j в степени x.
В той же графе таблицы для найденного ранее значения j выбираем ближайшее меньшее число, соответствующее вычислен ному jx = nрасч./ nmin. Умножив затем найденное в таблице значение jx на nmin, получим принятые частоту вращения, число двойных ходов или подачу.
Пример 4.3.Станок 1А730: nmax = 710 мин-1; nmin = 56 мин-1; m = 12;
nрасч=250 мин-1 Найти nприн; jm-1 = nmax/nmin; m-1 = 11; j11 = 710/56 = 12.7.
По таблице находим j11 = 12,64, что соответствует j = 1,26.
jx = nрасч/ nmin = 250/56 = 4,5
В графе таблицы, соответствующей j = 1,26, находим ближайшее меньшее значение jx = 4,00. Тогда nприн = 56 ∙ 4,00 = 224 мин-1.
Иногда из-за конструктивных особенностей станков в результате таких вычислений не удается получить нормализованные значения знаменателя j. В этих случаях j удобно определить с помощью таблиц чисел в дробных показателях степеней (прил.12) по формуле:
j = ( nmax/nmin)1/m-1
Подсчитанную по формулам эффективную мощность резания Nэ(кВт) сопоставляют с паспортными данными выбранного станка.
Необходимая мощность на приводе станка:
Nпр = Nэ/h,
где h – КПД станка; h берется по паспорту станка (в среднем h = 0,80...0,85).
При сопоставлении расчетной мощности резания с мощностью станка принимается во внимание мощность на шпинделе, допускаемая прочностью слабых звеньев кинематической цепи станка.
Многоинструментная обработка на одношпиндельных токарных станках.Первоначальные данные по всем инструментам наладки, так же как и данные по мощности резания, целесообразно оформить в виде таблицы. В первой части таблицы записываются элементы, определяющие длину рабочего хода каждого суппорта. Все элементы до lдоп определяются по таблицам справочников по расчету режимов резания. lдоп – дополнительная длина хода, вызванная в ряде случаев особенностями наладки и конфигурации детали, например величина, на которую необходимо отвести суппорты (инструменты) для того, чтобы можно было свободно извлечь обрабатываемую деталь из рабочей зоны. Для сложных наладок эту величину лучше всего определить графически.
Формуляр построен исходя из предположения, что лимитирующим производительность обработки суппортом является продольный суппорт. В том случае, когда лимитирующим суп портом является поперечный, его данные по табличному и пас портному значениям подачи следует записать в первую строку расчета вслед за определением длины рабочего хода. Затем, так же как и в приведенном случае, определяются расчетное и паспортное значения подачи для не лимитирующего суппорта.
Далее весь ход расчета понятен из формуляра и не требует дополнительных пояснений.
В графы таблиц формуляра 8.8.2, обведенные жирными линиями, записывается значение (в данном случае Lpx), общее для всех строк (инструментов). Запись делается только один раз в средней строке.
Многоинструментная обработка на многошпиндельных полуавтоматах последовательного действия.Пример формуляра не приводится. Расчет ведется так же и в такой же последовательности, как и для многоинструментной обработки на одно шпиндельных станках [18], для каждого из шпинделей много шпиндельного станка. Далее определяется лимитирующий шпиндель и производится корректирование (уменьшение) числа оборотов шпинделя и подач на не лимитирующих позициях с учетом установленного машинного времени работы станка.
Одноинструментная обработка на сверлильных станках.После-довательность и ход расчета достаточно ясны из формуляра и не требуют дополнительных пояснений. В некоторых случаях может оказаться необходимым в качестве исходных данных поместить в формуляре дополнительные, кроме тех, что указаны в технологических картах, сведения по инструменту.
Многоинструментная обработка на сверлильных станках с одной многошпиндельной головкой.В данном случае имеется в виду использование вертикально-сверлильных станков для специальных наладок (2С150, 2С170) или многошпиндельных вертикально-сверлильных станков с колокольной головкой (2150М, 2170М).
Расчет, так же как и для многоинструментной обработки на токарных станках, целесообразно выполнить в виде таблицы. Таблица содержит столько горизонтальных строк, сколько раз личных инструментов имеется в многошпиндельной головке. Инструменты обозначаются на эскизе операционной карты, но мерами, которые записываются в таблицу. Порядок расчета определяется последовательностью граф таблицы, и сущность рас чета сводится к заполнению граф для каждого инструмента в последовательности, определяемой построением таблицы. Нормативные данные по подачам, скоростям резания, усилиям и мощности, а также поправочные коэффициенты приведены в справочниках, например [18]. Там же даются необходимые пояснения, а формулы для расчета остальных величин приводятся внизу таблицы. Следует иметь в виду, что передаточное отношение в головке между шпинделем станка и шпинделями инструментов может быть либо задано заранее, если, например, используется нормализованная или уже спроектированная многошпиндельная головка, либо выбирается произвольно, исходя из наибольшего приближения скоростей резания инструментальных шпинделей к расчетным.
Осевая сила резания при обработке отверстий проверяется только для сверл. Мощность резания при обработке отверстий должна соответствовать мощности станка только для сверл (из быстрорежущей стали и оснащенных пластинками твердого сплава) и для зенкеров, оснащенных пластинками твердого сплава.
Дата добавления: 2018-05-12; просмотров: 486; Мы поможем в написании вашей работы! |
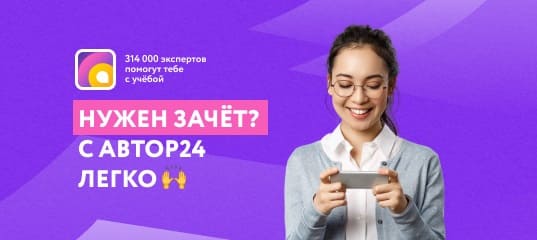
Мы поможем в написании ваших работ!