НАЗНАЧЕНИЕ И КОНСТРУКЦИЯ ДЕТАЛИ
В процессе проектирования студент должен ознакомиться с конструкцией детали, ее назначением и условиями работы в узле или механизме. Все эти вопросы должны быть изложены в соответствующем разделе пояснительной записки.
Для технически грамотного и обоснованного изложения это необходимо изучить чертежи общих видов узлов и дать описание назначения самой детали, основных ее поверхностей и влияния их взаимного расположения, точности и шероховатости поверхности на качество работы механизма, для которого изготовляется деталь. Если назначение детали исследует описать назначение ее поверхностей. Говоря о поверхностях, необходимо присваивать каждой из них буквенное значения, например плоскость Аили торец Б. Эти же обозначения должны быть найдены на соответствующие поверхности на чертеже. Далее следует определить отклонения на размеры и поверхности, отсутствующие на чертеже (на свободные размеры, неуказанные отклонения формы и расположения), для последующей записи их в технологические карты.
Из описания назначения и конструкции детали должно быть ясно какие поверхности и размеры имеют основное, решающее для служебного назначения детали и какие — второстепенное.
В том разделе следует привести также данные о материале детали: химический состав, механические свойства до и после термической обработки. Эти данные сводятся в таблицы 1.1 и 1.2.
|
|
Таблица 1.1 Химический состав стали 45 (ГОСТ 1050-74)
С | Sl | Mn | S | P | Ni | Cr |
Не более | ||||||
0,40 – 0,50 | 0,17 – 0,37 | 0,50 – 0,80 | 0,045 | 0,045 | 0,30 | 0,30 |
Таблица 1.2 Механические свойства стали 45
sт, МПа | sвр, МПа | d5,% | y, % | aн, Дж/см2 | НВ ( не более) | ||
горячекатаной | отожженной | ||||||
Не менее | |||||||
360 | 610 | 16 | 40 | 50 | 241 | 197 |
Кроме того, необходимо высказать свои соображения относительно правильности выбора материала для данных условий работы детали в узле, целесообразности его замены другими марками и какими именно.
АНАЛИЗ ТЕХНОЛОГИЧНОСТИ КОНСТРУКЦИИ ДЕТАЛИ
В процессе курсового проектирования, так же как и в производственных условиях, любая конструкция (машина, узел, деталь) должна быть самым тщательным образом проанализирована. Цель такого анализа – выявление недостатков конструкции по сведениям, содержащимся в чертежах и технических требованиях, а также возможное улучшение технологичности рассматриваемой конструкции.
Технологический контроль чертежей сводится к тщательному их изучению. Рабочие чертежи обрабатываемых деталей должны содержать все необходимые сведения, дающие полное представление о детали, т. е. все проекции, разрезы и сечения, совершенно четко и однозначно объясняющие ее конфигурацию, и возможные способы получения заготовки На чертеже должны быть указаны все размеры с необходимыми отклонениями, требуемая шероховатость обрабатываемых поверхностей, допускаемые отклонения от правильных геометрических форм, а также взаимного положения поверхностей. Чертеж должен содержать все необходимые сведения о материале детали, термической обработке, применяемых защитных и декоративных покрытиях, массе детали и др. Таким образом, технологический контроль – важная стадия проектирования технологических процессов, он способствует выяснению и уточнению приведенных выше факторов.
|
|
Технологический анализ конструкции обеспечивает улучшение технико-экономических показателей разрабатываемого технологического процесса. Поэтому технологический анализ – один из важнейших этапов технологической разработки, в том числе и курсового проектирования.
Основные задачи, решаемые при анализе технологичности конструкции обрабатываемой детали, сводятся к возможному уменьшению трудоемкости и металлоемкости, возможности обработки детали высокопроизводительными методами.
Анализ технологичности целесообразно проводить в определенной последовательности.
|
|
1 На основании изучения условий работы узла изделия, а также учитывая заданную годовую программу, проанализировать возможность упрощения конструкции детали, замены сварной, армированной или сборной конструкцией, а также возможность целесообразность замены материала.
2 Установить возможность применения высокопроизводительных методов обработки.
3 Проанализировать конструктивные элементы детали в технологическом отношении, используя при этом рекомендации по Технологичности конструкций, приведенные в справочной литературе [I], [2], [б], [151, [32]. Выявить труднодоступные для обработки места.
4 Определить возможность совмещения технологических и измерительных баз при выдерживании размеров, оговоренных допусками, необходимость дополнительных технологических операций для получения заданной точности и шероховатости обработанных поверхностей.
5 Увязать указанные на чертежах допускаемые отклонения размеров, шероховатости и пространственные отклонения геометрической формы и взаимного расположения поверхностей с геометрическими погрешностями станков.
6 Определить возможность непосредственного измерения заданных на чертеже размеров.
|
|
7 Определить поверхности, которые могут быть использованыпри базировании, возможность введения искусственных баз.
8 Определить необходимость дополнительных технологических операций, вызванных специфическими требованиями (например, допустимыми отклонениями в массе детали), и возможность изменения этих требований.
9 Проанализировать возможность выбора рационального метода получения заготовки, учитывая экономические факторы.
10 Предусмотреть в конструкциях деталей, подвергающихся термической обработке, конструктивные элементы, уменьшающие коробление деталей в процессе нагрева и охлаждения, и определить, правильно ли выбраны материалы с учетом термической обработки [32], [33].
С целью упрощения анализа технологичности можно дать частные рекомендации для некоторых классификационных групп деталей.
Для корпусных деталей определяют:
а) допускает ли конструкция обработку плоскостей на проход и что мешает такому виду обработки?
б) можно ли обрабатывать отверстия одновременно на многошпиндельных станках с учетом расстояний между осями этих отверстий?
в) позволяет ли форма отверстий растачивать их на проход с одной или двух сторон?
г) есть ли свободный доступ инструмента к обрабатываемым поверхностям?
д) нужна ли подрезка торцов ступиц с внутренних сторон отливки и можно ли ее устранить?
е) есть ли глухие отверстия и можно ли заменить их сквозными?
ж) имеются ли обрабатываемые плоскости, расположенные под тупыми и острыми углами, и можно ли заменить их плоскостями, расположенными параллельно или перпендикулярно друг к другу?
з) имеются ли отверстия, расположенные не под прямым углом к плоскости входа И выхода, и возможно ли изменение этих элементов?
и) достаточна ли жесткость детали, не ограничит ли она режимы резания?
к) имеются ли в конструкции детали достаточные по размерам и расстоянию базовые поверхности, если нет, то каким образом следует выбрать вспомогательные базы?
л) нет ли в конструкции внутренней резьбы большого диаметра и возможно ли заменить ее другими конструктивными элементами?
м) насколько прост способ получения заготовки (отливки), правильно ли выбраны элементы конструкции, обусловливающие получение заготовки?
Для валов указывают:
а) можно ли обрабатывать поверхности проходными резцами?
б) убывают ли к концам диаметральные размеры шеек вала?
в) можно ли уменьшить диаметры больших фланцев или буртов или исключить их вообще, и как это повлияет на коэффициент использования металла?
г) можно ли заменить закрытые шпоночные канавки открытыми, которые обрабатываются гораздо производительнее дисковыми фрезами?
д) имеют ли поперечные канавки форму и размеры, пригодные для обработки на гидрокопировальных станках?
е) допускает ли жесткость вала получение высокой точности обработки жесткости вала считается недостаточной, если для получения точности 6…9-го квалитетов соотношение его длины l к диаметру d свыше 10...12 для валов, изготовляемых по более низким квалитетам, это отношение может быть равно 15; при многорезцовой обработке это отношение следует уменьшить до 10?
Следует помнить, что технология обработки гладких валов в значительной мере отличается от технологии изготовления ступенчатых валов простотой и экономичностью, поэтому необходимо проанализировать возможность замены ступенчатого вала гладким.
Зубчатые колеса – массовые детали машиностроения, поэтому вопросы технологичности приобретают для них особенно значение. При анализе технологичности конструкции колес следует определить возможность высокопроизводительных методов формообразования зубчатого венца с применением пластического деформирования в горячем и холодном состоянии.
Конструкция зубчатого колеса должна характеризоваться следующими признаками:
а) простой формой центрального отверстия, так как сложные отверстия значительно обработку, вызывая необходимость применения револьверных станков и полуавтоматов;
б) простой конфигурацией наружного контура зубчатого колеса (так как наиболее технологичными являются зубчатые колеса плоской формы без выступающих ступиц);
в) расположенными с одной стороны ступицами, так как в противном случае обработка по одной детали на зубофрезерных станках вызывает увеличение количества этих станков на 25 – 30 %;
г) симметричным расположением перемычки между ступицей и венцом для зубчатых колес, подлежали термической обработке как по отношению к венцу, так и по отношению к ступице. Нарушение этого условия приводит к значительным односторонним искажениям при термической обработке;
д) правильной формой и размерами канавок для выхода
инструментов;
е) возможностью многорезцовой обработки в зависимости от соотношения диаметров венцов и расстояний между ними.
После проведенного анализа технологичности все предложения по изменению конструкции детали должны быть систематизированы в расчетно-пояснительной записке, ряд этих предложений но согласованию с руководителем проекта может быть внесен в конструкцию детали.
Пример 1.1. Деталь – корпус ступицы (рис. 1.1) – изготовляется из ковкого чугуна КЧ 37 12 литьем, поэтому конфигурация наружного контура и внутренних поверхностей не вызывает значительных трудностей, при получении заготовки. Тем не менее даже при этом формовка должна производиться сприменением стержней, формирующих как внутренние полости, так и карманы и ребра с боковых сторон, особенно нетехнологично литое отверстие шириной 10 мм. Эти элементы определяются конструктивными соображениями, и изменить их, по-видимому, затруднительно.
То же самое относится и к внутренним обрабатываемым поверхностям (0120 М7 и 0150 М7). Эта отверстия должны быть выполнены в пределах указанных отклонений и с точностью до 0,04 мм. Единственным способом достижения указанной точности является окончательная расточка отверстий на алмазно-расточных станках При этом в какой то мере нарушается точность их взаимного расположения относительно наружного диаметра (0165^6), так как именно этот диаметр будет использован в качестве установочной базы. Этим и обусловливается второй пункт технических требований относительно необходимости окончательной обработки конструктивных баз после запрессовки колец подшипников.
Нетехнологичны в данной конструкции цековки Æ30 мм, так как здесь не предусмотрен свободный доступ инструмента. Поэтому необходимо применять инструменты с удлинителями кроме того наружным диаметром эти цековки совпадают с наружным диаметром детали, что приводит к образованию острых кромок и необходимости введения слесарно-зачистных операций ручной обработки.
В остальном деталь достаточно технологична, допускает применение высокопроизводительных режимов обработки, имеет хорошие базовые поверхности для первоначальных операцией довольно проста по конструкции. Расположение крепежных отверстий как резьбовых, так и гладких допускает много инструментальную обработку. Поверхности вращения могут быть обработаны на многошпиндельных станках.
Рисунок 1.1 Корпус ступицы.
Пример 1.2. Деталь корпус редуктора (рисунок 1.2) – представляет собой отливку коробчатой формы из серого чугуна СЧ 20. Отливка довольно проста по конфигурации, но требует применения стержневой формовки для образования внутренних полостей. Кроме того, в опоке должен быть предусмотренсложный разъем ввиду наличия у детали выступов на боковой поверхности. Следует заметить, что толщина стенок отливки неоправданно завышена, так как наибольший габаритный размер детали не превышает 250 мм и минимальная толщине стенок для таких отливок составляет 3...5, а на чертеже – 10 мм. Следовательно условию минимальной металлоемкости эта деталь уже не удовлетворяет.
С точки зрения механической обработки деталь имеет следующие недостатки в отношении технологичности. Форма и расположение отверстий Æ95H7 и Æ62Js7 удобны для обработки с одной стороны отливки. Два других отверстия, лежащих на оси II 62Js7 и Æ40Js7 не могут быть обработаны на проход с той же стороны, что и отверстия по оси I.
Таким образом, обработка этих групп отверстий может вестись только с двух сторон одновременно или с перестановкой детали на разных операциях. В последнем случае затруднительно обеспечить требование относительно параллельности осейIиIIв пределах 0,03 мм.
Значительные трудности вызывает обработка крепежных отверстий, так как они расположены близко относительно друг друга (в большинстве случаев на расстоянии менее 25 мм), и одновременная их обработка на многошпиндельных станках невозможна. Ряд крепежных отверстий расположен внутри отливки в труднодоступных для инструмента местах, что затрудняет процесс обработки Нетехнологичны цековки Æ20 мм, так как их обработку возможно производить только с обратной стороны съемными зенковками, которые надеваются на оправку после того, как она пропущена в отверстие. При обработке шпинделем станка производится давление на инструмент. При этом инструмент вытягивается вверх. Эти цековки можно довольно просто заменить платиками под головки винтов. Платики можно будет фрезеровать напроход совместно с обработкой наружных поверхностей.
Затруднительна и обработка поверхности С, так как она расположена внутри детали и, следовательно, к ней нет свободного доступа и выхода инструмента Сказанное выше справедливо для массового и крупносерийного производства.
Остальные обрабатываемые поверхности с точки зрения обеспечения точности и шероховатости не представляют технологических трудностей, позволяют вести обработку напроход и дают возможность обрабатывать несколько деталей одновременно высокопроизводительными методами.
Рисунок 1.2 Корпус редуктора
Пример 1.3. Деталь – ведомая шестерня (рис 1.3) – изготовлена из легированной стали 20ХНР и проходит термическую обработку, что имеет большое значение в отношении короблений, возможных при нагревании и охлаждении детали. В этом смысле перемычка, связывающая тело зубчатого венца и ступицу, расположена неудачно, так как при термической обработке возникнут односторонние искажения. Зубчатый венец уменьшится в размерах и вызовет сжатие ступицы с левого торца Таким образом, отверстие приобретет коническую форму, что скажется на характере искажения зубчатого венца. Поэтому перемычку между венцом и ступицей следует в осевом сечении расположить наклонно, как это указано на чертеже пунктиром. Такое конструктивное изменение приведет к меньшим искажениям при термической обработке деталь, по-видимому, не обладает достаточной жесткостью для применения методов пластического формообразования зубчатого венца, а также протягивания шлицевого отверстия в ступице, и некоторое усиление ступицы с этой целью не приведет к значительному увеличению заготовки. Вывод о недостаточной жесткости следует проверить расчетом.
С точки зрения механической обработки зубчатые колеса вообще нетехнологичны, так как операция нарезания зубьев со снятием стружки производится в основном малопроизводительными методами.
При конструировании деталей должны учитываться вопросы повышения производительности зубообработки. Так, например, наличие выступа относительно зубчатого венца на левом торце неизбежно приведет к тому, что при одновременной обработке двух деталей зубофрезерованием между ними придется установить прокладку в виде кольца, что увеличит длину резания и, следовательно, снизит производительность процесса. Это приведет также к тому, что на нижнем торце верхней детали при зубофрезеровании образуются заусенцы, которые нужно будет снять. Возможно, эти факторы могли быть учтены при конструировании детали, и технологичность ее была бы значительно улучшена.
Положительным следует считать наличие в отверстии двух фасок, наружный диаметр которых больше наружною диаметра шлицевого отверстия. Это позволяет протягивать шлицевые отверстия после изготовления фасок, а торцы обрабатывать на многорезцовом станке, в этом случае резцы для подрезки торцов не будут доходить до шлицевого отверстия, что обеспечивает хорошие условия резания (не на прерывистой поверхности) и, следовательно, высокую точность.
Рисунок 1.3 Ведомая шестерня.
Глава 2. ПРЕДВАРИТЕЛЬНАЯ ПРОРАБОТКА ПРОЕКТНЫХ РЕШЕНИЙ
_______________________________________________________________
ВЫБОР ТИПА ПРОИЗВОДСТВА
Тип производства по ГОСТ 31108-74 характеризуется коэффициентом закрепления операций Кзо, который показывает всех различных технологических операций, выполняемых подлежащих выполнению подразделением в течение месяца, к числу рабочих мест:
где åПо – суммарное число различных операций; Ря – явочное число рабочих подразделения, выполняющих различные операции.
ГОСТ 14004-74, принимаются следующие коэффициенты закрепления операций: для массового производства ; для крупносерийного производства
Практическое значение Кз.о. для массового производства может быть 0,1…1,0.
Коэффициент закрепления операций должен в производственных условиях определяться для планового периода, равного месяцу.
Так как в заданиях курсовых проектов регламентируется готовая программа изготовления какой-то конкретной детали, то условие планового периода, равного одному месяцу, здесь необходимо.
Если заданием на курсовое проектирование предусматривается внесение изменений в существующий на производстве технологический процесс, то вычисление коэффициента закрепления операций для этого процесса сведется к проверке правильности расчетов режимов резания, норм времени, фактических коэффициентов загрузки оборудования и др. При этом тип и организационная форма производства заранее известны и мало вероятно, чтобы вычисленные значения коэффициента закрепления операций противоречили установленному типу производства.
При самостоятельной разработке студентом технологического процесса необходимо этот процесс расчленить на технологические операции и переходы по обработке элементарных поверхностей, определить основное время выполнения каждого перехода и штучное или штучно-калькуляционное время для каждой операции. На данном этапе проектирования нормирование переходов и операций можно выполнить, пользуясь приближенными формулами (приложение 1).
Порядок расчета коэффициента закрепления операций приведен в расчетном формуляре (приложение 8.3). На основании исходных данных рассчитывается годовая программа. Располагая штучным или штучно-калькуляционным временем, затраченным на каждую операцию, определяют количество станков;
где N – годовая программа, шт.; Тшт(ш–к) – штучное или штучно- калькуляционное время, мин; Fд – действительный годовой фонд времени, ч; ηз.н. – нормативный коэффициент загрузки оборудования.
Средние значения нормативного коэффициента загрузки оборудования по отделению или участку цеха при двухсменной работе следует принимать: для мелкосерийного производства – 0,8...0,9; серийного – 0,75...0,85; массового и крупносерийного – 0,65...0,75.
Так как на данном этапе тип производства еще не известен, можно принять усредненные значения нормативного коэффициента загрузки оборудования порядка 0,75...0,8. Это не приведет к большим погрешностям в расчетах, а фактические значения коэффициента загрузки оборудования будут определяться после детальной разработки технологического процесса.
После расчета и записи в графы таблицы прил. 83 по всем операциям значений Тщт (ш–к), mp – устанавливают принятое число рабочих мест Р, округляя до ближайшего большего целого числа полученное значение mp.
Далее по каждой операции вычисляют значение фактического коэффициента загрузки рабочего места по формуле и записывают эти значения в графы таблицы.
Если ηз.ф. операции оказывается выше нормативного, следует для данной операции количество станков. Если же на каких-то операциях ηзф значительно ниже нормативного, следует проанализировать возможность дозагрузки рабочего места другими, примерно равноценными по трудоемкости, операциями. количество операций на данном рабочем месте может быть увеличено, а в графу Отаблицы будет записано скорректированное значение.
Количество операций, выполняемых на рабочем месте, определяется по формуле .
После заполнения всех граф таблицы подсчитывают суммарные значения для О и Р, определяют Кз.о. и тип производства.
Пример 2.1. Рассчитать коэффициент закрепления операций для технологического процесса, состоящего из трех операций протяжной, Тшт=1 мин; сварной, Тшт=2,4 мин; зубофрезерной, Тшт.=8 мин. Годовая программа станочная, выпуск запасных частей, – 60 000 деталей. Расчетное количество станков составит:
для первой операции – 0,33;
второй – 79;
третьей – 2,65.
Принятое количество станков:
для первой операции – 1;
второй – 1;
третьей – 3.
Практический коэффициент загрузки оборудования:
дня первой операции – 33;
второй – 0,79;
третьей – 0,88.
Коэффициент закрепления операций:
Т.е. производство будет массовым.
Если в нашем примере все операции имели бы фактический коэффициент загрузки оборудования примерно 0,25, количество операций, которые могли бы выполняться на каждом рабочем месте, О = 0,75/0,25 = 3 и коэффициент закрепления операций:
Производство будет крупносерийным.
Действительный фонд времени работы оборудования на год (в часах) можно определить по следующим данным:
Календарному числу дней – 365; количеству выходных дней – 104; праздничных дней – 8; предпраздничных дней, сокращенных на 1час – 6; рабочих суббот – 1; числу смен работы оборудования – в продолжительности рабочего дня – 8,2 ч; потерям времени на проведение ремонтов, обслуживания, настройки и подналадки оборудования (в процентах) П:
Дата добавления: 2018-05-12; просмотров: 2146; Мы поможем в написании вашей работы! |
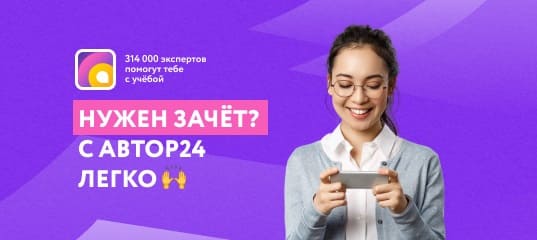
Мы поможем в написании ваших работ!