Основное время (с) для нарезания зубчатого венца
TО = 60 ∙ R/n + TО.П.,
где ТОП– время опускания и подъема салазок (берется из технической характеристики станка).
При выполнении курсового проекта формулу для v можно с достаточной точностью использовать также для станков 5120 и 5А130.
Наружное круглое шлифование с продольной подачей. Формуляр прост и не требует особых пояснений, последовательность расчета одинакова во всех справочниках, с той лишь разницей, что коэффициентами может учитываться большее или меньшее число факторов. В приведенном примере, составленном на основании вышеуказанных общемашиностроительных нормативов, кроме прочих факторов, учитывается состояние шлифовального станка поправочным коэффициентом kT, который определяется из справочных таблиц исходя из срока эксплуатации станка.
Формуляр составляется одновременно с заполнением операционной карты, поэтому в качестве исходных не приводятся те данные, которые записываются непосредственно в операционную карту.
Рассчитанная мощность резания при шлифовании сопоставляется с допустимой при бесприжоговом шлифовании мощностью.
Наружное круглое шлифование с радиальной подачей. Расчет ведется в той же последовательности, что и с продольной подачей, но несколько проще. Вместо ширины шлифовального круга при определении предельно допустимой мощности исходя из режима бесприжогового шлифования в расчет принимается ширина шлифования, т. е. ширина контакта круга с изделием
|
|
Подобным же образом составляется расчетный формуляр и для бесцентрового шлифования с радиальной подачей. При шлифовании на бесцентрово-шлифовальных станках срок эксплуатации станка не принимается во внимание и коэффициент, зависящий от точности и жесткости станка, независима от срока эксплуатации принимается равным единице.
Бесцентровое шлифование с продольной подачей. Формуляр составляется аналогично рассмотренным выше способом шлифования. В отличие от рассмотренных случаев здесь принимается во внимание число проходов. Несмотря на то, что распределение общего припуска (удвоенной глубины шлифования – 2t) по проходам не является фактором, определяющим основное технологическое время, а учитывается только при настройке станка, его следует определять именно в расчетном формуляре, так как в операционных картах эти данные не указываются.
Для ряда сравнительно простых технологических операций составление расчетных формуляров не имеет смысла, так как достаточные для определения режимов резания и нормирования процесса данные содержатся в технологических картах. К числу таких операций относятся, например, зубозакругление и снятие фасок на торцах зубчатых колес, некоторые виды зубообработки, для которых устанавливается время обработки на один зуб, слесарная обработка, когда ее невозможно избежать, и др.
|
|
РАСЧЕТ ТЕХНИЧЕСКОЙ НОРМЫ ВРЕМЕНИ
Технические нормы времени в условиях массового и серийного производств устанавливаются расчетно-аналитическим методом.
В серийном производстве определяется норма штучно-калькуляционного времени Тшк:
Тшк= Тпз/n + Тшт,
в массовом производстве определяется норма штучного времени Тшт:
Тшт=ТО + Тв + Тоб + Тот,
где Тпз – подготовительно-заключительное время, мин; n – количество деталей в настроечной партии, шт.; ТО – основное время, мин; ТВ – вспомогательное время, мин. Вспомогательное время состоит из затрат времени на отдельные приемы: Тв = Тус + ТЗО + Туп + Тиз; Тус – время на установку и снятие де тали, мин; ТЗО – время на закрепление и открепление детали, мин; Туп – время на приемы управления, мин; Тиз – время на измерение детали, мин; Тоб – время на обслуживание рабочего места, мин. Время на обслуживание рабочего места Тоб в массовом производстве и при шлифовании в серийном производстве слагается из времени на организационное обслуживание Торг и времени на техническое обслуживание рабочего места: Тоб = Ттех + Торг; Тот – время перерывов на отдых и личные надобности, мин.
|
|
Основное время ТО вычисляется на основании принятых ре жимов резания по формулам, содержащимся в литературе по ре жимам резания [18]...[22]. Нормативы на отдельные элементы вспомогательного времени для массового производства приведены в прил. 5 и литературе [22].
Нормативы вспомогательного времени, приведенные в прил. 5, можно в учебных целях использовать и для нормирования вспомогательного времени в серийном производстве, применяя коэффициент k в крупносерийном – 1,5, а в среднесерийном производстве – 1,85. Основанием для этого служат результаты анализа структуры штучно-калькуляционного времени в основных типах производства [11].
В массовом производстве время на техническое обслуживание рабочего места Ттех определяется по следующим формулам:
· для токарных, фрезерных и сверлильных операций Ттех = ТО ∙ tсм/Т,
· для шлифовальных операций Ттех = ТО ∙ tп/Т,
· для остальных операций Ттех = ТО ∙ Птех/Т,
где ТО – основное время, мин; tсм – время на смену инструментов и подналадку станка, мин; tn – время на одну правку шлифовального круга, мин; Птех – затраты на техническое обслуживание рабочего места в процентах от основного; Т – период стойкости при работе одним инструментом или расчетный период стойкости лимитирующего инструмента при много-инструментной обработке, мин.
|
|
Нормативные значения времени tсм, tп, Птех приведены в прил. 5.
Время на организационное обслуживание рабочего места Торг в массовом производстве для всех операций определяется в процентах от оперативного времени (их значения приведены в прил. 5).
Эти же нормативы можно в учебных целях использовать и для определения Ттех и Торг при нормировании шлифовальных операций в серийном производстве.
В серийном производстве для всех остальных операций Тоб и Тот по отдельности не определяются. В нормативах дается сумма этих двух составляющих в процентах от оперативного времени.
Оперативное время Топ = ТО + Тв, а общее время на обслуживание рабочего места и отдых в серийном производстве:
ТОБ ОТ = ТопПоб/100,
Время перерывов на отдых и личные надобности при нормировании работ в массовом производстве ТОТ = ТО ∙ Пот/100, где Пот – затраты времени на отдых в процентном отношении к оперативному. Соответствующие значения Пот приведены в прил. 5 для массового производства, а для нормирования шлифовальных работ в серийном производстве в прил. 6.
Приведенные выше формулы для определения штучного и штучно-калькуляционного времени можно представить в виде:
Тшт = То+Тус+Тзо+Туп+Тиз+Ттех+Торг+Тот,
в серийном производстве для всех операций, кроме шлифовальных,
Тшк = Тпз/n+То+( Тус+Тзо+Туп+Тиз) ∙ к+Тоб от,
для шлифовальных операций
Тшк = Тпз/n+То+( Тус+Тзо+Туп+Тиз) ∙ к+Ттех+Торг+Тот,
Рассчитанное по нормативам вспомогательное время в массовом производстве умножается на приведенные ниже коэффициенты, зависящие от такта работы поточной линии:
такт работы, мин 0,5 1 2 4 8
коэффициент кп 0,81 0,9 1 1,11 1,23
Результаты определения Тшт или Тшк следует записать в табл. 4.20.
Таблица 4.20. Сводная таблица технических норм времени по операциям мин.
Номер и наименование операции | То | Тв | Топ | Тоб | Тот | Тшт | Тпз | n | Тшк | |||
Тус+Тзо | Туп | Тиз | Ттех | Торг | ||||||||
Пример 4.4. Рассчитать норму штучного времени для токарной операции, выполняемой на многорезцовом полуавтомате в центрах. Производство поточное, массовое. Масса детали 2 кг. Размеры детали Æ75×250 мм, наибольшая Длина обрабатываемой ступени 160 мм. Точность обработки – 10-й квалитет; 100 % деталей контролируется скобой односторонней Резцы проходные и подрезные – 4 шт. сечением 25×25 мм. Расчетная стойкость лимитирующего инструмента 150 мин. Основное время – 2 мин.
Расчет ведем по формуле для массового производства.
По прил. 5 Тус+Тзо = 0,085 мин. Время на включение станка кнопкой равно 0,01 мин. Время на перемещение каретки суппорта в продольном направлении на длину 100 мм по прил. 5 равно 0,04 мин, тогда Туп=0,01+ 0,04 = 0,05 мин
Время на измерение детали односторонней скобой по прил. 5 Тиз=0,07 мин. Вспомогательное время Тв = 0,085 + 0,05 + 0,07 = 0,205 мин.
Оперативное время:
Топ=2 + 0,205=2,205 мин,
Время на обслуживание (техническое) рабочего места- по прил. 5.17 tсм=2,5 мин на один резец, а на смену четырех резцов – 10 мин:
Ттех = 2 ∙ 10/150 » 0,133 мин,
Время на организационное обслуживание рабочего места: по прил. 5 составляет 1,7 % оперативного времени, тогда:
Торг = 2,205 ∙ 1,7/100 = 0,037 мин,
Время перерывов на отдых (по прил. 5) Пот = 6 % оперативного времени, тогда:
Тот = 2,205 ∙ 6/100=0,132 мин,
Штучное время Тшт =2 + 0,085 + 0,05 + 0,07 + 0,133 + 0,037 + 0,132 = 2,507 мин.
Пример 4.5. Рассчитать норму штучно-калькуляционного времени для операции фрезерования плоскости 200×100 мм высотой 50-0,1 торцевой фрезой на вертикально-фрезерном станке с длиной стола 750 мм. Масса детали 12 кг. Производство среднесерийное, размер партии деталей 100 шт.; 20 % деталей контролируется штангенциркулем с установкой его на размер в процессе измерения. Деталь устанавливается в тисках с пневмозажимом. Основное время равно 1,2 мин.
Расчет Тшк ведем по формуле для серийного производства.
Определяем состав подготовительно-заключительного времени: установка тисков с креплением четырьмя болтами – 14 мин; установка фрезы – 2 мин; получение инструмента и приспособлений до начала работы и сдачи их после завершения работы (по прил. 5) – 7 мин: Тпз = 14 + 2 + 7=23 мин,
Время на установку и снятие детали, закрепление ее и открепление (по прил. 5) Тус + Тзо=0,136 мин.
Время на приемы управления (по прил. 5): включить и выключить станок кнопкой – 0,01 мин; подвести деталь к фрезе в продольном направлении – 0,03 мин, переместить стол в обратном (продольном) направлении на 300 мм – 0,11 мин; тогда Туп = 0,01 + 0,03 + 0,11 = 0,15 мин.
Время, затраченное на измерение (по прил 5) детали, равно 0,18 мин; при 20 % контролируемых деталей (табл. 4.21), получим:
Тпз = 0,18 ∙ 20/100 =0,036 мин,
Поправочный коэффициент на вспомогательное время при среднесерийном производстве k=1,85. Вспомогательное время Оперативное время Топ = 1,2 + 0,59 = 1,79 мин.
Таблица 4.21. Число контрольных измерений деталей на операции [22].
Наименование операции | Точность измерения | Контролируемый размер, мм | Число контролируемых измерений (в % от общего числа деталей) при способе достижения размеров обработки | ||
Обеспечивающемся конструктивными размерами инструмента | Работой инструментом, установленным на размер | Работой с пробным промером | |||
1 | 2 | 3 | 4 | 5 | 6 |
Точение, растачивание, круглое шлифование, наружное и внутреннее | 11…12 квалитет | 50 | 20 | 25 | 60 |
200 | 25 | 30 | 70 | ||
Свыше 200 | 30 | 40 | 80 | ||
30 | 40 | 100 | |||
6..8 квалитет | 50 | 40 | 50 | 100 | |
200 | 50 | 60 | 100 | ||
Свыше 200 | |||||
Бесцентровое шлифование | 11..12 квалитет | 100 | 1 | ||
6..8 квалитет | 2 | ||||
Хонингование и суперфиниш | 100 | ||||
Плоское шлифование | 0,01 мм | 200 | 100 | ||
0,05мм | 50 | 80 | |||
200 | 90 | ||||
Свыше 200 | 100 | ||||
0,1 мм | 50 | 70 | |||
200 | 80 | ||||
Свыше 200 | 90 | ||||
0,2 мм | 50 | 40 | |||
200 | 60 | ||||
Свыше 200 | 80 |
лоское фрезерование | До 0,1 мм | 50 | 10 | ||
200 | 20 | ||||
Свыше 200 | 30 | ||||
Сверление | 10 | 1 | |||
25 | 2 | ||||
50 | 3 | ||||
Свыше 50 | 4 | ||||
Накатывание резьбы | 10 | 1 | |||
25 | 2 | ||||
50 | 3 | ||||
Нарезание резьбы плашками, метчиками и головками | 10 | 10 | |||
25 | 20 | ||||
50 | 30 | ||||
Свыше 50 | 40 | ||||
Фрезерование резьбы | 100 | 20 | |||
Шлифование резьбы | 50 | 100 |
Время на обслуживание рабочего места и отдых (по прил. 5) составляет 6 % оперативного времени, тогда:
ТОБ ОТ = 1,79 ∙ 6/100 = 0,1 мин,
Штучно-калькуляционное время:
Тшк = 23/100 + 1,2 + (0,136 + 0,15 + 0,036) ∙ 1,85 + 0,1 = 2,12 мин.
Настоящей методикой нормирования станочных работ рекомендуется пользоваться при отсутствии нормативной литературы [22], [23].
ПРИЛОЖЕНИЯ
___________________________________________________________________
Дата добавления: 2018-05-12; просмотров: 500; Мы поможем в написании вашей работы! |
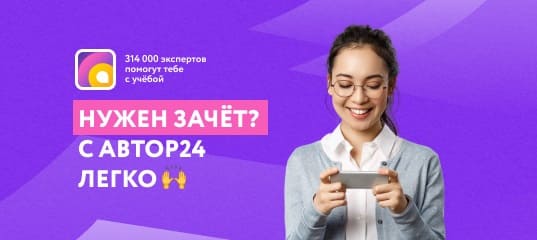
Мы поможем в написании ваших работ!