Технологические параметры процессов намотки
Всвязи с тем, что материал наматываемых изделий формируется во время их намотки, его физико-механические свойства в значительной степени зависят от технологического про-
200
Рис. 2.50. Технологическая схема изготовления песчано-полимерной оправки
Основными параметрами, определяющими свойства ПКМ, и соответствии с законом аддитивности, являются характеристики компонентов и объемное содержание νB волокон в композите:
σК = νB σВ + (1 - νB) σ*СВ
Здесь σК , σВ , σ*СВ — прочности компонентов, волокон и связующего соответственно.
Из уравнения видно, что с увеличением коэффициента армирования νB предел прочности однонаправленного КМ линейно возрастает. Однако эксперименты показывают, что существует оптимальное значение коэффициента νB°пт (рис. 2.51), при котором σК достигает своего максимума (σКмах) при растяжении. Так, для однонаправленных стеклопластиков νBопт = 0,70...0,72, а для органо- и углепластиков νBопт = 0,60...0,65.
Это объясняется тем, что предельные значения коэффициента армирования зависят от геометрии упаковок волокон. Так, для круглых волокон в зависимости от схемы их упаковки (см.
201
2.8 Формообразование намоткой
рис. 2.51) предельные значения νBопт = 0,907 (гексагональная укладка), νBопт = 0,785 (тетрагональная укладка). Другое ограничение связано с выбором минимального значения толщины δmin прослойки связующего между волокнами, которое приближенно оценивают следующим образом:
|
|
δmin> dв/ (εсв/εв – 1)
где εсв,εв— относительные деформации волокна и связующего соответственно.
Рис. 2.51. Качественная зависимость прочности ПКМ от коэффициента армирования:
1 — теоретический предел прочности ПКМ; 2 - практический предел прочности ПКМ
Объемное содержание волокон в ПКМ всегда меньше массового содержания вследствие наличия пор и воздушных включений в материале. Соотношение между объемным и массовым содержанием волокон определяется выражением
νBоб = νBмас/ (νBмас +(1 - νBмас)ρсв/ ρв)
где ρсв, ρв — плотности связующего и волокна соответственно.
202
1. ТЕХНОЛОГИЯ КОНСТРУКЦИЙ ИЗ ПОЛИМЕРНЫХ КОМПОЗИЦИЙ
Очевидно, что соотношение между объемным и массовым содержанием в системе наполнитель—связующее в основном определяется технологией изготовления. И в первую очередь оно зависит от следующих факторов: натяжения армирующего наполнителя, его вида; вязкости и температуры связующего и температуры разогрева препрега; скорости намотки.
При способе "мокрой" намотки все эти параметры необходимо контролировать в ходе технологического процесса изготовления изделия. При способе "сухой" намотки процессы получения намоточного материала и изготовления силовой оболочки разделены, и параметрами, подлежащими обязательному контролю, являются технологическое натяжение ленты, скорость намотки и температура разогрева препрега. В этом случае остальные параметры отслеживаются в процессе получения ленты-препрега. Преимущества метода "сухой" намотки заключаются в возможности обеспечения качественного контроля и выдерживания оптимальных значений перечисленных выше технологических параметров при изготовлении намоточного материала.
|
|
Натяжение армирующего наполнителя. Выбору технологического натяжения пряди нитей или ленты препрега при намотке уделяют большое значение.
1. Натяжение должно создавать нормальное давление на
оправку с целью уплотнения материала в процессе формования
изделия. Нормальное давление можно рассчитать, используя
формулу
РH = (qл/tлR).sin2β,
где qл — растяжение ленты; tл — ширина ленты; R — радиус оправки; β — угол намотки.
Зная давление, можно определить, достаточное ли оно для уплотнения материала, с одной стороны, и не вызовет ли оно прогиб оправки или ее разрушение, с другой.
|
|
2. Натяжение должно обеспечивать получение высоких ме
ханических характеристик материала за счет одновременного
включения всех нитей (волокон) в работу. Наиболее значитель
но натяжение нитей влияет на предел прочности однонаправ
ленных КМ. Многочисленные эксперименты показывают, что
203
2.8. Формообразование намоткой
для однонаправленных стеклопластиков оптимальным является натяжение нити qH = (0,05...0,15) qраз для органопластиков qH = (0,25...0,36) <7раз, а для однонаправленных углепластиков qH = (0,02...0,07) qpaз, где qpaз — разрушающая нагрузка на ленту.
3. Натяжение должно обеспечивать равномерное содержание связующего в материале по толщине, особенно при намотке толстостенных изделий. В этом случае натяжение наполнителя программируют так, чтобы натяжение сначала увеличилось, а затем уменьшилось при достижении заданной толщины стенки изделия.
4. Натяжение должно снижать начальный уровень несовершенства арматуры (искривления). Необходимое натяжение создается в намоточно-пропиточном (нитепроводном) тракте от шпулярника до наматываемого изделия. Нитепроводные тракты являются важнейшим элементом намоточного станка.
Основные принципы построения нитетрактов следующие: нитетракт должен быть (по возможности) коротким; конструкция элементов нитетракта должна обеспечивать
|
|
минимальное травмирование волокон и не способствовать их
пушению.
Для выполнения этих требований необходимо, чтобы количество перегибов армирующего материала и касаний им элементов нитетракта было минимальным; нити перед пропиткой были отделены одна от другой (рис. 2.52, а— г); радиусы перегибов составляли не менее 10... 15 мм; в местах касаний ленты деталей нитетракта не было защемлений.
Кроме того, нитетракт должен быть удобен при заправке арматурой и при обрыве нитей в процессе намотки; коэффициент усиления натяжения тракта должен быть близок к постоянному; все элементы нитепроводного тракта, контактирующие с арматурой, должны иметь полированную или хромированную поверхность и высокую стойкость к истиранию (эффективно применение керамики и фторопласта).
В схеме нитепроводного тракта нельзя четко выделить зону создания натяжения, так как все элементы и узлы тракта в той или иной степени влияют на уровень натяжения. Однако в тракте есть элементы, регулирующие уровень натяжения, которые называют натяжителями. Некоторые схемы устройства натяжителей нитей, прядей нитей, лент показаны на рис. 2.53.
1. ТЕХНОЛОГИИ КОНСТРУКЦИЙ ИЗ ПОЛИМЕРНЫХ КОМПОЗИЦИЙ
Все устройства имеют механические регуляторы натяжения — тормозные механизмы или нажимные грузики.
Механические натяжители обеспечивают разнонатянутость арматуры в пределах +0,2 кг.
Рис. 2.52.Схема формирования ленты перед протяжкой:
а — прямым стержнем; 6— изогнутым стержнем с прямыми плечиками;
в — кольцом; г — гребенкой; / — линия, параллельная оси оправки
Параметры процесса пропитки наполнителя. Как известно, для каждого вида армирующего волокнистого наполнителя существует оптимальное с точки зрения прочности формируемого композиционного материала, процентное содержание его в единице объема. Для большей части применяемых при намотке наполнителей оптимальное содержание составляет примерно 50...70%.
204
205
|
2.8. Формообразование намоткой |
Рис. 2.53.Схемы устройств натяжения пряди нитей или ленты
Изменение этого технологического параметра неизбежно приводит к снижению прочности материала. В свою очередь объемное содержание армирующих нитей в изделии зависит от многих параметров процесса получения намоточной ленты-вязкости полимерного связующего, скорости протягивания нитей через пропиточную ванну, количества и плотности упа-
1. ТЕХНОЛОГИЯ КОНСТРУКЦИЙ ИЗ ПОЛИМЕРНЫХ КОМПОЗИЦИЙ
ковки одновременно пропитываемых волокон, а также их спо-собности к смачиванию данным типом связующего.
Вязкость связующего на практике определяют с помощью простых вискозиметров типа ВЗ-4 и измеряют ее в секундах. Согласно измерениям по ВЗ-4, вязкость — это время, за которое вытекает 100 мл связующего из конической воронки, имеющей диаметр выходного сечения 4 мм. Чем меньше вязкость связующего во время соприкосновения с армирующими волок-Нами, тем лучше пропитка намоточного материала, тоньше его слой на каждом волокне и, следовательно, выше объемное содержание наполнителя в КМ и конечная прочность этого материала. С целью уменьшения вязкости связующего в него юбавляют растворитель типа ацетоноспиртовой смеси, родст-Венный высокомолекулярный полимер или дополнительно подогревают его.
Следует заметить, что подогрев связующего во время пропитки нужно осуществлять кратковременно и до определенных и-мператур, так как это может привести к ускорению реакции полимеризации и к еще большему увеличению его вязкости. С целью уменьшения наноса связующего на протягиваемую через него ленту на выходе из пропиточной ванны устанавливают отжимные валки или острые скребки, снимающие излишки связующего с верхней и нижней сторон намоточной ленты.
При способе "мокрой" намотки содержание наполнителя В композиционном материале может изменяться по толщине изделия: уменьшаться по мере удаления слоя от поверхности технологической оправки. Это происходит вследствие того, что сжимающие силы в материале, возникающие от технологического натяжения наматываемой ленты, суммируются пропорционально нарастанию толщины стенки изготавливаемого изделия, и жидкое связующее выдавливается, мигрируя от нижних слоев к верхним. Получившееся в результате этого процесса соотношение между содержанием наполнителя и связующего фиксируется при отверждении, что приводит к неодновременности включения слоев в работу при нагружении эксплуатационными силами.
При "сухом" способе намотки фиксация этого важнейшего технологического параметра происходит уже при подсушке намоточной ленты в нагревательной камере, обеспечивающей
206
207
2.8. Формообразование намоткой
удаление растворителя и частичную полимеризацию термореактивного связующего. Поэтому при такой технологии изготовления изделий выдавливания связующего из нижних слоев в верхние почти не происходит.
В процессе непрерывной намотки изделий и производстве препрегов используют в основном два способа пропитки: пропитка окунанием арматуры в ванночку (рис. 2.54, а); пропитка на вращающемся барабане, так называемый "типографский" способ (рис. 2.54, б).
Рис. 2.54.Два способа пропитки наполнителя:
а - пропитка окунанием; б - пропитка на вращающемся барабане; / — нити, сматываемые со шпулярника; 2 — направляющие ролики; 3 — механизм подачи пропитанной ленты на оправку; 4 — устройство формирования ленты из пряди; 5— валики, регулирующие угол охвата лентой барабана; 6 - барабан
Вторая схема более предпочтительна, поскольку упрощает обслуживание и позволяет перейти на нагрев связующего не во всем объеме ванночки, а только в зоне пропитки, что существенно снижает температуру связующего в ванночке и резко увеличивает его жизнеспособность.
В соответствии с первым способом связующее нагревается во всем объеме ванночки, поэтому жизнеспособность связующего, например ЭДТ-10, не превышает двух часов. Большим недостатком этого способа является необходимость введения системы термостатирования связующего, регулирования и закачки теплоносителя (глицерина, масла, воды) с обеспечением герметичности. Нарушение герметичности приводит к попаданию теплоносителя в связующее и необратимому браку изделий.
208
1. ТЕХНОЛОГИЯ КОНСТРУКЦИЙ ИЗ ПОЛИМЕРНЫХ КОМПОЗИЦИЙ
При пропитке окунанием перемешивание связующего в ii.ii точке происходит за счет движения ленты, при барабанной пропитке — вследствие вращения барабана, что повышает ин-тенсивность перемешивания, выравнивает температуру связую-щего и улучшает качество пропитки. Тем не менее оба метода
не позволяют существенно повысить жизнеспособность связующего.
Этого недостатка лишен радиационный метод нагрева пенты и связующего в зоне пропитки при барабанном способе. Простым подбором расстояния от инфракрасного нагревателя до зоны пропитки обеспечивается нужная температура в этой юне. За счет того, что нагреву подвергается локальный участок, шачительно снижается потребляемая мощность. Однако и этот Способ имеет два недостатка: трудность организации контроля и регулирования температуры связующего в зоне нагрева и пропитки; зависимость качества прогрева от скорости движения ленты (пропитки).
Однако резкое уменьшение температуры связующего во всем объеме ванночки, увеличение живучести и, как следствие, времени межоперационных промывок нитетракта, а также снижение требований по температуре к доливаемому связующему в процессе его расходования делают этот способ наиболее перспективным.
Переработка связующего при повышенных температурах, приводящая к сгусткообразованию и преждевременному частичному отверждению связующего, выражающемуся в быстром нарастании вязкости, предъявляет определенные требования к ванночкам. Это, прежде всего, отсутствие застойных зон, где массообмен затруднен и "старое" связующее может стать центром нарастания вязкости во всем объеме.
209 |
Для непрерывного процесса намотки необходимо, чтобы ванночки были быстросъемными, причем в комплекте нитетракта их должно быть не менее двух. Ванночка и узлы, остающиеся на тракте, должны быть скомпонованы таким образом, чтобы все участки были доступны к промывке растворителями. Особенно это относится ко всякого рода втулкам, подшипникам, пробкам и узлам трения, в которые не исключено попадание связующего. Выполнение конструктором этих
14-243
2.8. Формообразование намоткой
2. ТЕХНОЛОГИЯ КОНСТРУКЦИЙ ИЗ ПОЛИМЕРНЫХ КОМПОЗИЦИЙ
14* |
условий существенно облегчит эксплуатацию оборудования и повысит надежность процесса намотки.
Дата добавления: 2018-05-02; просмотров: 2813; Мы поможем в написании вашей работы! |
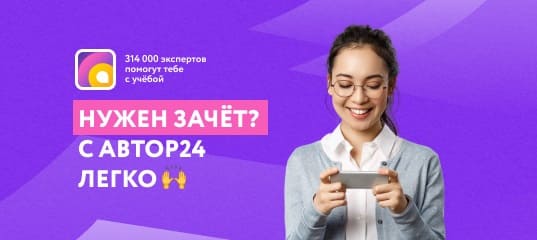
Мы поможем в написании ваших работ!