Основные технические характеристики станков марок СН-6 и НШБ-2
соответственно:
Диаметр наматываемого баллона, мм............. ......... 200-650 10-360
Зональный угол намотки, град....................... .............. 7~90 10-90
Число оборотов шпинделя, об/мин................. 1,5— 20 2 -- 2 5
На станке марки СН-6 (рис. 2.46) перед началом намотки оправку закрепляют в опорных узлах на секторах в расчетном положении (первая зона намотки). Синхронное вращение правого и левого секторов обеспечивается разрезными шестернями (безлюфтовая передача). Главное движение осуществляется двигателем постоянного тока, а скорость главного движения регулируется сменными шестернями, расположенными в передней бабке. Скорость полярного вращения задается управляемым двигателем постоянного тока с редуктором. Намотка одной зоны осуществляется за один оборот оправки вокруг своей оси. Поэтому скорость полярного вращения и передаточное число редуктора подбирают так, чтобы за один оборот
Рис. 2.46.Схема зональной намотки сферической оболочки на станке СН-6:
/ - шпулярник с пропиточно-натяжным трактом; 2 — сферическая оправка с намотанной зоной; 3 - вращающиеся сектора; 4 - опора для оси оправки; 5 ~ электромеханический привод станка; 6 - корпус станка; 7 - двигатель полярного вращения; 8 - коллектор привода; со - главное движение оправки; ωпол - полярное вращение оправки; со - зональное движение (изменение зонального угла намотки у)
13* |
195
2.8. Формообразование намоткой
|
|
главного движения оправка сместилась на расстояние, равное или меньшее ширины наматываемой ленты.
Перестановку оправки для намотки следующей зоны осуществляют вручную по угловым рискам, нанесенным на секторах. Положение оси оправки относительно оси главного движения может изменяться в диапазоне от 10° до 80°.
Для намотки силовой и герметизирующей оболочек торо-вых сосудов применяют малогабаритный торонамоточный станок марки СНТ-2 (рис. 2.47). Станок предназначен для радиальной и спиральной намоток оболочек торовой формы, имеющих круговое, эллиптическое или произвольное сечение. Диаметр изготавливаемых изделий 300...500 мм, диаметр сечения 60... 100 мм. Габаритные размеры станка 1200x800x1000 мм, масса станка 100 кг.
|
Рис. 2.47.Схема намотки торовых оболочек на станке СНТ-2: 1 — композитная оболочка; 2 — намоточная головка; 3 — съемная катушка с препрегом; 4 — система направляющих роликов и устройство торможения; 5 — песчаная оправка |
Станок имеет разъемную вращающуюся с постоянной угловой скоростью головку, центр которой совпадает с центром меридианального сечения торовой оправки. Намоточная головка выполнена в виде разъемного зубчатого кольца, на котором установлено несколько катушек с пре-прегом. С катушек лента пре-прега (или прядь волокон) сматывается на торовую оправку, образуя слой композита под углом +р или -р к меридиану оболочки. Кроме того, на силовом кольце крепятся фрикционное устройство для торможения ленты, система направляющих роликов, измеритель натяжения нитей индукционного типа и ролик — раскладчик наполнителя. Количество оборотов намоточной головки фиксируется при помощи электромеханического счетчика. Скорость вращения головки изменяется дискретно в пределах от 12 до 36 об/мин, что соответствует скорости намотки
|
|
1. ТЕХНОЛОГИЯ КОНСТРУКЦИЙ ИЗ ПОЛИМЕРНЫХ КОМПОЗИЦИЙ
1...12 м/мин. Расчетные углы намотки устанавливаются с помощью двух гитар сменных шестерен и червячно-кулачкового механизма, создающего ускоренное или замедленное вращение червячного колеса, а следовательно, и оправки в нужный момент времени. Станок обеспечивает укладку нитей под углами армирования Р с точностью ±2°...2,5°.
Технологические оправки
Во всех случаях изготовления изделий намоткой применяют специальную технологическую оснастку — оправку. Конструкция оправки должна отвечать следующим требованиям: соответствовать геометрии и форме внутренней конфигурации изделия; обладать достаточной прочностью при сжимающих нагрузках; не прогибаться под собственной массой; не проскальзывать на валу; легко удаляться после отверждения изделия; предусматривать установку закладных элементов; иметь гладкую и ровную поверхность.
|
|
В соответствии с конструктивным оформлением оправки подразделяют на цельные, разборные и разрушаемые. Возможно применение и комбинированных оправок, включающих в себя элементы одноразового и многоразового использования.
Цельные оправки. Такие оправки применяют в серийном производстве при формовании изделий, из которых оправку можно извлечь полностью (цилиндры, конусы, полусферы и т.п.). В этих случаях извлечение оправки из изделия не представляет принципиальных трудностей, если на ее поверхность предварительно нанесено антиадгезионное покрытие. Для обеспечения демонтажа поверхность цилиндрических оправок выполняют с небольшим технологическим конусом (1:100...1:200). Цельные оправки изготавливают из сталей и алюминиевых сплавов. Выбор материала оправки определяется размером изделий, их точностью и масштабом производства. Извлекают оправку вручную (если она небольшая), либо с помощью специальных станков — кабестанов (в случае больших изделий). Применение неразборных многоразовых оправок целесообразно до диаметра изделий 500 мм.
|
|
Разборные оправки. Их используются при формовании изделий, из которых цельные оправки извлечь нельзя (цилиндрические оболочки с днищами, сферические оболочки с боль-
196
197
Формообразование намоткой
шими полюсными отверстиями). Для изготовления таких конструкций применяют разборные металлические оправки (рис. 2.48).
|
А-А
Рис.2.48. Конструктивная схема металлической оправки: / - разборные части оправки, формирующие днища сосудов; 2 -цилиндрическая часть оправки; 3 - вал; 4 - гайки для сборки частей днищ; 5 — гайки крепления оправки на валу
Разборная оправка разделена на три части, соответствующие профилированным днищам и цилиндрической части оболочки; каждая из них разрезана по образующей на тринадцать секторов, один из которых плоский. Части оправки, формирующие днища, устанавливаются в посадочных местах вала, а затем после установки секторов цилиндрической части всю оправку закрепляют гайками. Для демонтажа оправки достаточно извлечь вал и плоские секторы в каждой части, после чего остальные секторы можно свободно удалить из отверж-денной оболочки через ее полюсные отверстия.
Разборная оправка обеспечивает точность и жесткость конструкции, является оправкой многоразового использования, сравнительно легко удаляется из готового изделия. Однако конструкция этой оправки сложная и процесс изготовления ее дороже по сравнению с другими типами оправок.
Разборные многоразовые оправки целесообразно использовать при изготовлении не менее 25 изделий диаметром от 500 до 1500 мм.
Разрушаемые оправки применяют в тех случаях, когда контур изделия замкнутый или близок к такому (сферичес-
1. ТЕХНОЛОГИЯ КОНСТРУКЦИЙ ИЗ ПОЛИМЕРНЫХ КОМПОЗИЦИЙ
кие, овалоидные, торовые оболочки с малыми полюсными (ч нерстиями). Для их изготовления можно использовать такие материалы, как гипс, эвтектические соли и легкоплавкие металлы, песок, связанный раствором поливинилового спирта в иоде, парафиновосковую смесь. Такие оправки получают ме-iодами литья или прессования в специальных пресс-формах, поверхность которых покрыта кремнийорганической или графитовой смазкой. Их недостаток заключается в том, что они дают усадку, которая часто бывает неравномерной, а это приводит к нарушению точности размеров и геометрической формы готовых изделий. Удаляются такие оправки механическим разрушением, вымыванием, выплавлением, растворением В соответствующих жидкостях при нормальной или повышенной температурах.
Наиболее широко на практике применяют песчано-поли-мерные или аренальные (в Древнем Риме — круглая или овальная посыпанная песком площадка) оправки.
В качестве примера приведем конструктивную схему (рис. 2.49) и процесс изготовления удаляемых песчаных оправок торовой формы. Оправка состоит из двух половинок, в одну из которых впрессована втулка с уплотнительным кольцом. Эти детали, а также штуцер являются элементами заправочного узла торового сосуда. Штуцер размещают во внутренней полости оправки и фиксируют в нужном положении с помощью разжимной цанги и винта. Конус служит для определения места расположения штуцера, раздвигания нитей и вытаскивания штуцера из оправки после окончания намотки.
Половинки торовых оправок изготавливают из смеси кварцевого песка и водного раствора поливинилового спирта в алюминиевых пресс-формах. На 1 в.ч. ПВС марки "Совиол" берут 8 в.ч. воды и 55...57 в.ч. однородного песка. Смесь размешивают до равномерного состава и появления мелких пузырьков воздуха во всей массе. Такая смесь обладает достаточной текучестью и легко заполняет замкнутый объем торовой пресс-формы. Термообработку песчаных оправок любой формы проводят при температуре 393 К в течение 1 ч.
Изготовленные половинки совмещают и обматывают технологической лентой шириной 20 мм из растворимой в воде
198
199
|
1. ТЕХНОЛОГИЯ КОНСТРУКЦИЙ ИЗ ПОЛИМЕРНЫХ КОМПОЗИЦИЙ |
цесса изготовления таких изделий, точности выдерживания его важнейших технологических параметров. |
2.8. Формообразование намоткой
ПВС'-пленки марки ПВС-Э с целью прочного скрепления половинок между собой и предохранения поверхности герметизирующей оболочки от прилипания к ней отдельных песчинок. Изготовленные таким способом оправки являются жесткими и прочными (асж = 9 МПа), имеют малую усадку, твердую и гладкую поверхность, безопасны при изготовлении и дешевы.
Рис. 2.49.Конструктивная схема вымываемой песчаной оправки торовой формы с закладными элементами штуцера оболочки и цанговым устройством для извлечения штуцера из оправки после намотки однонаправленного КМ: /, 10 — верхняя и нижняя половины торовой оправки; 2 — поверхностный слой из пленки ПВС-Э; 3 — схема укладки ленты, вырезанной из пленки ПВС-Э; 4 — штуцер; 5 - втулка; 6 — разжимная цанга; 7 - раздвижной конус; 8 — фторопластовое уплотнение; 9 — установочный винт
Песчаную оправку и пленку ПВС-Э удаляют из готового изделия путем вымывания горячей водой (Т= 333 К). В течение 20...30 мин оправка распадается на мелкие части и удаляется через штуцер наружу, одновременно растворяется и вымывается водой технологическая пленка ПВСЭ.
Общая технологическая схема изготовления песчано-поли-мерных оправок показана на рис. 2.50.
Далее будут приведены примеры конструкторских решений оправок для намотки конкретных изделий.
Дата добавления: 2018-05-02; просмотров: 1308; Мы поможем в написании вашей работы! |
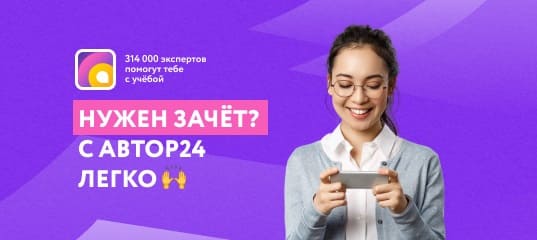
Мы поможем в написании ваших работ!