Особенности конструирования деталей с учетом технологии прессования
Основные принципы конструирования изделий, получаемых методом прессования, помогают избежать ошибок на стадии проектирования, если учитываются технологические возможности метода формования.
При конструировании детали следует учитывать, что на ее конечную форму и качество оказывают влияние:
геометрическая форма детали (габаритные размеры, толщина стенок, наличие выступов, отверстий, арматуры, их взаимное расположение и т.д.);
171
2.7. Формообразование прессованием в формах
технология изготовления деталей (температурные и временные режимы процесса изготовления, применяемые давления, режимы охлаждения и т.д.);
ориентация материала при заполнении формы и время ее заполнения.
Влияние формы детали на конечные размеры. Детали из термореактивных композиций, имеющие Т-образное поперечное сечение, коробятся с утягиванием к основанию полки Т-образного сечения, так как вследствие разного охлаждения внутренняя часть охлаждается медленнее, чем наружная, что и вызывает соответствующую усадку (рис. 2.28, а).
Детали, имеющие подковообразное сечение (рис. 2.28, б), деформируются в сторону разгибания (эффект остаточного пружинения). Наличие пазов и вырезов на поверхности детали влияет на протекание усадочных процессов, приводящих к овальности деталей и искажению формы паза (рис. 2.28, в).
■ Рис.2.28. Влияние формы деталей на конечные размеры:
а — усадка; б— остаточное пружение; в — искажения формы; — по чертежу;
----- фактическое
|
|
Арматура отрицательно влияет на точность детали; размер детали оказывается тем больше, чем больше число армирующих вставок он пересекает. После извлечения из формы деталь имеет изогнутость, обращенную выпуклостью в ту сторону, где температура формы была больше. Отклонения от геометрической формы плоских поверхностей непосредственно зависят от площади детали.
Технологические уклоны, радиусы. Прессовый уклон (конусность) должен иметь направление и величину, обеспечивающие нормальный разъем пресс-формы, извлечение оформляющих элементов и изделия из пресс-формы. Уклон для несопрягае-мых размеров назначают в диапазоне значений от 1,5 до 3°.
2. ТЕХНОЛОГИЯ КОНСТРУКЦИЙ ИЗ ПОЛИМЕРНЫХ КОМПОЗИЦИЙ
Уклоны внутренних поверхностей и отверстий следует делать большими, чем уклоны по наружному контуру деталей. При назначении уклонов крупногабаритных и сложнопрофильных деталей необходимо учитывать силы, возникающие при извлечении их из формы и предел прочности материала детали при сжатии. Поэтому детали из материалов с низкими пределами прочности при сжатии должны иметь увеличенные уклоны.
|
|
При конструировании прессуемых деталей рекомендуется избегать поднутрений, препятствующих извлечению детали из формы. При наличии поднутрений требуются дополнительные плоскости разъема форм, что приводит к последующей зачистке деталей.
Острые углы у прессованных деталей не рекомендуются, их можно сохранять только на гранях, примыкающих к плоскости разъема пресс-формы. Радиусы скруглений должны составлять не менее 1,5...3,0 мм.
Оформление стенок деталей. В силу особенностей физико-механических процессов при прессовании стенки детали должны иметь равномерную толщину. В случаях, когда по условиям прочности толщина стенок не может быть одинаковой, рекомендуется избегать резких переходов от одного сечения в другое.
Разнотолщинность деталей допускается не более 2:1 при прямом прессовании и не более 2,5:1 — при литьевом.
Толщину стенки сложных сечений, за исключением отдельных случаев, не рекомендуется назначать свыше 10... 12 мм. Минимальные значения толщины стенки определяют исходя из прочностного расчета детали. Для ее уменьшения предусматривают ребра жесткости.
Толщина ребра жесткости не должна превышать толщину стенки детали или ее элемента, к которому они примыкают. Оптимальная толщина ребер жесткости должна быть не более 0,6...0,8 толщины сопрягаемой стенки.
|
|
Ребра жесткости рекомендуется располагать на прямых участках элементов детали.
При конструировании ребристых панелей, днищ и крышек с плоской поверхностью необходимо стремиться к диагональному, диаметральному или шахматному расположению ребер, причем форма их сечения должна быть постоянной по всей длине.
172
173
2.7. Формообразование прессованием в формах
Оформление резьб. В деталях, получаемых прессованием, резьбы можно оформлять в процессе формования армированием и механической обработкой. Наиболее технологичны резьбы, получаемые непосредственно формованием.
Силовые резьбы, а также резьбы на деталях, которые подвергаются частой сборке и разборке, рекомендуется армировать металлом. Наиболее прочной является метрическая резьба с шагом 1,5 мм.
Резьбу малого диаметра (менее 2,5 мм) не рекомендуется использовать так же, как и мелкую резьбу с шагом менее 0,5 мм.
Оформление отверстий. Отверстия в прессуемых деталях можно получить:
полным оформлением в пресс-форме;
частичным оформлением в пресс-форме с последующим сверлением;
сверлением и другими способами.
|
|
Отверстия в деталях по форме должны быть простыми. Сквозные отверстия являются более технологичными, чем глухие.
Перемычку между соседними отверстиями или отверстием и краем детали назначают не менее диаметра отверстия для термопластичных композитов, а для термореактивных выбирают по табл. 2.6.
Таблица 2.6 Размеры перемычек между отверстиями или от отверстия до края детали
Размер отверстия, мм | Перемычка между отверстиями, мм | Перемычка от края изделия до отверстия, мм |
Свыше 3 до 4 | 2,5 | 3,5 |
4 до 5 | 3,0 | 4,0 |
6 до 8 | 4,0 | 5,0 |
10 до 12 | 5,0 | 6,0 |
12 до 14 | 6,0 | 7,0 |
14 до 30 | 8,0 | 9,0 |
30 до 50 | 10,0 | 11,0 |
Максимальное отношение глубины вертикального отверстия к диаметру зависит от метода прессования и диаметра отверстия. Для диаметров от 3 до 50 мм это отношение находится в диапазоне (2,5...5,0) для прямого прессования и в
2. ТЕХНОЛОГИЯ КОНСТРУКЦИЙ ИЗ ПОЛИМЕРНЫХ КОМПОЗИЦИЙ
диапазоне (5,0... 15) — для литьевого прессования. Максимальная длина горизонтальных отверстий не должна превышать двойного диаметра.
2.8. Формообразование намоткой
Получение конструкций методом намотки явилось в 60-х годах подлинным прогрессом в технологии производства изделий из ПКМ. Это закономерно, поскольку метод намотки позволил получить высокопрочные материалы в конструкциях аэрокосмической и ракетной техники и заключал в себе огромные возможности совершенствования, многие из которых сегодня реализованы.
Намотка — технологический процесс, при котором непрерывный армирующий наполнитель в виде нитей, лент, жгутов, тканей, пленок пропитывается полимерным связующим, подается на оправку, имеющую конфигурацию внутренней поверхности изделия и укладывается по ее поверхности в заданном направлении. После получения необходимой схемы армирования, заданной толщины и структуры материала производится отверждение изделия тем или иным способом и удаление оправки. Иногда оправка может быть элементом наматываемой конструкции, например, герметизирующей оболочкой.
Методом намотки изготавливают изделия, имеющие форму тел вращения: баллоны давления, баки, корпуса ракетных двигателей, головные части, отсеки ракет, транспортно-пусковые контейнеры, корпуса подводных аппаратов, стволы орудий и корпуса снарядов, жидконаливные цистерны, трубопроводные магистрали, коробчатые шпангоуты, воздухозаборники самолетов, лопасти винтов вертолетов, различные профили, пространственно изогнутые трубы и т.д.
Основным элементом перечисленных конструкций является тонкостенная силовая оболочка. Геометрически она образована вращением двух плоских кривых вокруг неподвижной оси, лежащей в плоскости этих кривых. Расстояние между кривыми называют толщиной оболочки hоб, а среднюю кривую y = f (r) - образующей или меридианом (рис. 2.29, а).
Структура материала оболочки создается в результате набора (намотки) n-го количества слоев, которые образуют узор
174
175
2.8. Формообразование намоткой
--------------------------- г——~~---------------------- ■ :------------------------------------------------------------
намотки или схему армирования оболочки. При этом основным элементом намотки является форма витка нитей, укладываемого на поверхность. В зависимости от формы витка различают спиральную и планарную (плоскостную) намотки.
Рис.2.29. Геометрическое представление оболочки вращения: а — основные геометрические формы; б — геометрические параметры и положение нити на поверхности вращения общего вида; г — радиус полюсного отверстия
Спиральный виток представляет собой замкнутую (или разомкнутую) пространственную кривую. Главная разновидность спирали — геодезическая кривая или линия, которая определяется уравнением Клеро (рис. 2.29, б):
r∙sin β = R sin βo = const,
где β =f(r) — текущий угол намотки; R ~ максимальный радиус вращения; βo — расчетный угол намотки.
Геодезическая линия - это кратчайшее расстояние между двумя точками на поверхности, например прямая линия на плоскости, винтовая линия на цилиндре, окружность большого диаметра на сфере, все меридианы оболочек вращения.
При планарной намотке (например, при намотке по меридианам и широтам) форма витка нитей представляет собой плоскую замкнутую кривую.
Технология изготовления изделий из КМ методом намотки имеет ряд преимуществ по сравнению с другими известными методами переработки композитов в изделия. Важнейшими из этих преимуществ являются, во-первых, возможность наиболее
176
2. ТЕХНОЛОГИЯ КОНСТРУКЦИЙ ИЗ ПОЛИМЕРНЫХ КОМПОЗИЦИЙ
полной реализации в изделиях высокой прочности на растяжение волокон, составляющих намоточный материал, а во-вторых, возможность обеспечения высокой степени автоматизации подобного технологичсеского процесса изготовления изделий на станках с программным управлением.
Наиболее эффективна укладка волокон и нитей в направлении действия главных напряжений, появляющихся в материале вследствие действия силовых нагрузок, а также, если эти волокна одинаково натянуты и прочно склеены между собой. Одинаково натянутыми волокна оказываются лишь при намотке нитей на тела, имеющие выпуклую поверхность типа цилиндра, сферы, овалоида, изотензоида, тора и других им подобных, называемых телами вращения. Поэтому технология намотки изделий композиционными материалами и является наиболее применимой для этого класса изделий.
Дата добавления: 2018-05-02; просмотров: 750; Мы поможем в написании вашей работы! |
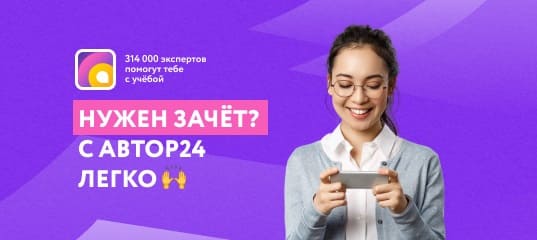
Мы поможем в написании ваших работ!