Основные технологические процессы
Внастоящее время известно множество технологических процессов переработки ПКМ в изделия различных размеров, конфигурации и целевого назначения. Основные технологические процессы формования, применяемые в производстве изделий из ПКМ, а также рекомендуемые виды армирующих наполнителей и связующих для этих процессов приведены в табл. 2.1. Технологические процессы, применяемые в производстве полуфабрикатов, таких как различные типы препрегов, углерод-углеродные каркасы, стренги, описаны в гл. 1.
125
124
2.2. Общая характеристика технологических процессов
2. ТЕХНОЛОГИЯ КОНСТРУКЦИЙ ИЗ ПОЛИМЕРНЫХ КОМПОЗИЦИЙ
Табл. 2.1
Основные технологические процессы формообразования изделий из ПКМ
Окончание табл. 2.1
Технологический процесс | Рекомендуемые компоненты ПКМ | |
Тип армирующего наполнителя | Тип связующего | |
Предварительное формование заготовок и | Короткие рубленые | Водные растворы |
матов | волокна, | этилового спирта, |
нитевидные | четыреххлористый | |
кристаллы | углерод, полимерные связующие, органические | |
жидкости |
Каждый технологический процесс имеет свои особенности, преимущества и недостатки. Кроме того, каждый процесс обусловлен предельными технологическими возможностями формообразования изделий, параметрами процесса (давление, температура, скорости формования и т.п.), геометрии, формы степенью автоматизации и реализации исходной прочности компонентов и т.д. Эти предельные возможности, с одной стороны, заложены в самом методе формообразования, а с другой стороны, ограничены параметрами технологического оборудования и оснастки.
|
|
Рассмотрим общую характеристику технологических процессов формообразования изделий из ПКМ (см. табл. 2.1).
Контактное формование. Процесс КФ заключается в послойной укладке заготовок из волокнистого наполнителя на форму вручную, напылением или с помощью специальных выкладочных центров. Пропитку заготовок можно осуществлять как на форме, так и предварительно с последующим удалением пузырьков воздуха из межслойного пространства. Этим способом можно изготавливать изделия практически любых размеров, но достаточно простой конфигурации. В США этот метод называют "метод ведра и щетки" (busket and brush).
Методом прессования получают детали и узлы разнообразного назначения, формы и размеров, обладающие высокой механической прочностью и жесткостью. Существует две разновидности метода прессования: прямое и литьевое. Прямое горячее прессование рационально применять для изготовления деталей средней сложности, больших габаритов и массы; ли-
|
|
126 127
2.2. Обшая характеристика технологических процессов
тьевое - для изготовления тонкостенных деталей сложной конфигурации.
Формование эластичной диафрагмой. Процесс заключается в том, что изделие вакуумируется в резиновом мешке и формуется под действием равномерного давления воздуха или смеси газов (в автоклаве), которое распределяется по всей поверхности изделия. Этот способ применяют для получения качественных изделий с высокими упругопрочностными характеристиками, поскольку процесс отверждения происходит при повышенных температурах, а внешнее давление уменьшает пористость и улучшает пропитку материала. К недостаткам способа относятся большие трудозатраты, энергозатраты, а также проблемы, связанные с выпуском крупносерийных партий изделий.
|
|
Формообразование давлением. Процесс осуществляется вакуумной пропиткой или пропиткой под давлением связующего сухого армирующего материала, заложенного в форму. Эти способы формования применимы в основном для изготовления изделий, имеющих простую симметричную форму — днища, конуса, кожуха, иолупатрубки. Кроме того, трудность изготовления форм больших размеров, высокая стоимость оборудования ограничивают размеры изделий, изготавливаемых этим способом.
Прессование в формах открытого и закрытого типов. Способ контактного формования имеет ряд недостатков, которые проявляются в условиях серийного производства. К ним относятся: значительный разброс показателей физико-механических свойств изделий, длительность процесса формования, тяжелые условия труда.
Однако применение способа КФ для производства крупногабаритных изделий в небольших количествах считают экономически целесообразным, так как не требуется сложной и дорогостоящей технологической оснастки и оборудования. К недостаткам этих способов относятся сравнительно низкие уп-ругопрочностные характеристики материалов (особенно при литьевом прессовании) вследствие хаотичного расположения коротких волокон, армирующих материал, а также необходимость использования дорогостоящих пресс-форм.
|
|
2. ТЕХНОЛОГИЯ КОНСТРУКЦИЙ ИЗ ПОЛИМЕРНЫХ КОМПОЗИЦИЙ
Намотка. Процесс заключается в укладке нити, жгута, ленты или ткани на вращающуюся или неподвижную оправку и отверждении изделия на оправке. Существует множество способов укладки: спиральная намотка, закатка, продольно-поперечная, по геодезическим линиям, хордовая, обмотка неподвижной оправки и т.д. Совершенство процесса изготовления изделий методом намотки определяет возможность его автоматизации и механизации. Намоткой изготавливают трубы, резервуары, обечайки, различные пустотелые профили, используя достаточно простую технологическую оснастку. При намотке однонаправленных лент, жгутов, нитей получают изделия с максимальными физико-механическими показателями. Для изготовления наиболее ответственных изделий осуществляют намотку сухих препрегов ("сухая" намотка). При этом, как правило, используют связующие горячего отверждения.
К недостаткам этого метода следует отнести неравномерность распределения связующего по толщине стенки намоточного изделия и определенные трудности при съеме изделий с оправки (особенно при длине оправки более 2 м).
Пултрузия. В технологическом процессе ориентация волокон в профилях различных сечений осуществляется методом протяжки, согласно которому собранные в жгут волокна с нанесенным связующим протягивают через клинообразную нагретую фильеру, где происходит уплотнение и отверждение материала. Поскольку при этом исключается выдержка матет риала под давлением, то в процессе пултрузии используют, как правило, расплавы смол, не содержащие растворителей (эпоксидные, полиэфирные). В соответствии с этим методом можно формовать различные профили из непрерывных нитей или жгутов и получать изделия с максимальными значениями прочности при растяжении и изгибе вдоль оси протяжки. Для улучшения пропитки и смачивания жгута обычно используют две фильеры (формообразующую и калибровочную), расположенные после ванны со связующим.
Предварительное формование заготовок и матов. Независимо от выбранных способов процессы предварительного формования заготовок и матов можно считать примерно одинаковыми, различие состоит лишь в подготовке материалов (до формования) и сложности получаемых изделий. Этим способом полу-
128
9-243
129
2.3. Контактное формование
2. ТЕХНОЛОГИЯ КОНСТРУКЦИЙ ИЗ ПОЛИМЕРНЫХ КОМПОЗИЦИЙ
чают предварительно отформованные заготовки, близкие по форме к детали, а также маты, которые в дальнейшем перерабатываются в изделия.
2.3. Контактное формование
В настоящее время около 30 % всех изделий из ПКМ,например корпуса лодок, яхт, элементы кузовов автомобилей, мебель, панели, ванны, водяные горки и другие, производят способами контактного формования.
Технологический процесс КФ заключается в том, что на подготовленную поверхность открытой формы укладывают вручную (или с помощью автомата) либо напыляют армирующий наполнитель, затем пропитывают его связующим, уплотняют и отверждают. Рассмотрим особенности способов КФ.
Ручная выкладка
При КФ используют открытую форму без применения давления. Форма может быть позитивной или негативной в зависимости от требуемой гладкости внутренней или внешней поверхности изделия.
Рис.2.3. Элементы конструкции формы и изделия при формовании ручной укладкой: / — форма; 2 — разделительная пленка; 3 — наружный смоляной слой; 4 — стекловолокно; 5 — ручной валик; 6 — смола в смеси с катализатором |
Негативная форма точно воспроизводит наружный контурформуемогоизделия,а позитивная — внутренний контур. Типовые способы укладки материала на негативную и позитивную формы показаны на рис. 2.3 и 2.4. Характерная особенность этого способа — получение точных размеров и гладкости только той' поверхности изделия, которая непосредственно прилегает к форме в процессе изготовления.
Для получения формы можно использовать любой материал, обладающий доста-
|
Рис.2.4. Типовой способ укладки волокнистого материала на позитивной форме: / - форма; 2 — слои волокнистого материала; 3 — деревянный брус, к которому прикрепляется стеклоткань
точной жесткостью и обеспечивающий получение необходимой геометрии изделия в процессе изготовления. Основное условие заключается в том, чтобы материал формы не подвергался химическому воздействию смолы и не оказывал вредного влияния на скорость отверждения последней.
Для изготовления формы можно применять дерево, фанеру, гипс, бетон, металлы. Цветные металлы можно использовать только в облуженном или хромированном состоянии, так как они чувствительны к действию некоторых катализаторов, входящих в связующие, и оказывают отрицательное воздействие на скорость отверждения. При использовании связующего горячего отверждения формование изделий происходит на формах, изготовленных из стеклопластика, песочно-полимерных смесей, алюминия.
Пористые материалы обычно гигроскопичны. Об этом нужно помнить, так как присутствие влаги замедляет отверждение связующего. Гипс и бетон необходимо предварительно высушивать при нагревании. Дерево, фанера также должны быть тщательно высушены. Кроме того, в формах из пористого материала необходимо заполнить и изолировать поры поверхности формы парафином, воском, фунтом, шпаклевкой независимо от наличия разделительной пленки или смазки. Если связующее хотя бы в отдельных местах пройдет сквозь разделительную пленку, то может произойти прилипание отформованного изделия к форме и ее отверждение.
При подготовке формы неообходимо реализовать следующие требования:
геометрия формы должна соответствовать геометрии изделия с учетом усадки материала и допуска на размеры;
130
9*
131
2.3. Контактное формование
поверхность формы должна быть такой, чтобы отформованное изделие можно было извлекать без больших усилий.
возможность обеспечения контроля равномерности и полноты нанесения наружных покрытий, а также качества пропитки армирующего материала по цвету формы.
Первой стадией при получении любого изделия в открытой форме является нанесение на ее поверхность антиадгезионного покрытия. На практике применяют различные типы антиадгезионных покрытий (табл. 2.2).
Таблица 2.2 Типы антиадгезионных покрытий
Тип покрытия | Форма при нанесении | Особенности покрытий |
Парафин | Пастообразная или | Глянцевая поверхность, |
жидкая | воспроизводит все детали формы; большие партии изделий | |
Поливиниловый | Жидкая, напыляемая | Водорастворимое, |
спирт (ПВС) | одноразового использования, смывается с изделия и формы, превосходный антиадгезионный материал; позволяет получить легко окрашиваемую поверхность | |
Фторированные | Жидкая, напыляемая | Низкий коэффициент |
углеводороды: | трения | |
силаны | Не дают хорошего глянца | |
силоксаны | Дорогие | |
Прокладочные | Бумага с покрытием, | Одноразового |
бумаги и | целлофан, пленка из | использования |
антиадгезионные | ПВС | Формование плоских |
пленки | листов | |
Внутренние | Жидкая (проникает в | Глянцевая поверхность; |
антиадгезионные | наружный смоляной: | сохраняет форму всех |
смазки | слой) | деталей, отпадает необходимость в парафинировании формы; позволяет получать легко окрашиваемую поверхность |
2. ТЕХНОЛОГИЯ КОНСТРУКЦИЙ ИЗ ПОЛИМЕРНЫХ КОМПОЗИЦИЙ
Выбор и эффективность разделительных покрытий определяются тремя факторами:
1) типом материала применяемой формы и связующего, которое может быть холодного или горячего отверждения;
2) степенью глянцевитости готовой поверхности изделия, наличием или отсутствием вторичных отделочных операций (например, окрашивания);
3) периодом времени, требуемого для сушки пленки разделительного слоя, по отношению к общему времени цикла формования.
При КФ положительные результаты можно получить при использовании не одного, а двух антиадгезионных материалов, например парафина и ПВС.
После каждого цикла формования нужно всегда полировать формы чистой салфеткой. Дополнительный слой парафина следует наносить после каждых 1-5 или более циклов в зависимости от типа парафина и условий формования. Периодически (через каждые 10...20 деталей) форму необходимо чистить для удаления всех остатков парафина и смолы. Тщательная подготовка формы — один из основных этапов цикла формования.
Для получения наружного смоляного слоя (гелькоата) обычно используют полиэфирную смолу, содержащую минеральные наполнители и пигменты, но без армирующих добавок. Эту композицию наносят на поверхность формы, а затем в процессе формования она попадает на формуемое изделие, образуя наружный слой. Тем самым обеспечивается образование декоративной глянцевой окрашенной поверхности с хорошими защитными свойствами, практически без последующей отделки.
Гелькоат (жидкое пальто) представляет собой желеобразное покрытие, которое наносят на поверхность из пульверизатора, кистью или малярным валиком. При выкладке волокнистых материалов на гелькоат необходимо обеспечить хорошую адгезию, для этого гелькоат должен оставаться гибким и незагрязненным. Для устранения воздушных включений между слоями следует тщательно разгладить первый выкладываемый слой, так как из-за наличия даже небольших воздушных включений на поверхности формируемого изделия могут возникать вздутия.
После правильной подготовки формы и нанесения наружного смоляного слоя приступают к укладке армирующих мате-
132
133
2.3. Контактное формование
риалов и их пропитке. Все типы армирующих материалов -маты из рубленой стеклопряжи, ткани и тканый ровинг -поступают на производство в виде больших рулонов различной ширины. Лист нужной длины вырубают из рулона, а затем, при необходимости, обрезают его по шаблону с помощью универсального бритвенного ножа, больших ножниц или электрической машины для резки тканей, аналогичной применяемым в швейной промышленности.
Затем тщательно смешивают заранее отмеренные количества смолы и катализатора. Композицию можно наносить на волокно как вне формы, так и внутри нее. Для полного удаления воздуха и обеспечения равномерности пропитки смолу в первую очередь наносят на участки волокна в верхней части формы. Для уплотнения материала и удаления пузырьков воздуха используют щетки, резиновые и зубчатые валики (рис.2.5). Как уже отмечалось, смесь катализатора со смолой можно наносить на волокно распылителем, который автоматически дозирует и смешивает компоненты.
Рис.2.5. Валики, применяемые для обкатки волокнистого материала |
Особое внимание следует уделить нанесению первого слоя (часто это "кожица" из тонкой вуали или мата с развесом 229 г/м2), чтобы не допустить образования воздушных пузырь-
2. ТЕХНОЛОГИЯ КОНСТРУКЦИЙ ИЗ ПОЛИМЕРНЫХ КОМПОЗИЦИЙ
ков между армирующим волокном и наружным смоляным слоем (гелькоатом). После этого уже можно наносить необходимое число слоев мата и (или) тканого ровинга до получения расчетной суммарной толщины (и, следовательно, прочности). Слои мата и тканого ровинга следует чередовать для обеспечения хорошей межслойной прочности сцепления, предотвращения появления воздушных включений и получения максимальной прочности. Во всех случаях основной задачей на данной стадии производства является наиболее полное вытеснение воздуха, задержанного слоями наполнителя.
В зависимости от типа армирующего материала в изделиях, полученных способом контактного формования, содержание волокна в материале составляет 35...50 %.
При формовании изделий на основе термореактивных связующих после завершения процесса выкладки изделие остается на форме до тех пор, пока не закончится отверждение связующего. На этой стадии трогать формуемое изделие не следует. Отверждение можно ускорить за счет нагревания самой формы. После извлечения изделия из формы оно еще должно "дозреть" в течение некоторого времени при комнатной температуре для окончательного отверждения.
Следует иметь в виду, что выкладка в открытую форму может быть одной из подготовительных операций, за которой обязательно следует самостоятельная операция формования — вакуумного, прессового, автоклавного и др.
При использовании ТКМ, в отличие от термореактивных, можно совмещать выкладку с формованием готового изделия. Смысл совмещенного процесса заключается в последовательном приформовывании каждого последующего слоя с одновременной его монолитизацией вплоть до достижения заданной толщины листа. Схемы выкладочных устройств в процессе роликовой и прессовой выкладки термопластичных полуфабрикатов представлены на рис. 2.6.
Технологические особенности формования термопластов обусловлены состоянием связующего и свойствами полуфабриката в процессе выкладки: отсутствием липкости при нормальной температуре и ограниченными драпировочными возможностями, особенно при выкладке пакета по поверхности сложной формы. В случае нелипкости волоконного полуфаб-
134
135
2.3. Контактное формование
2. ТЕХНОЛОГИЯ КОНСТРУКЦИЙ ИЗ ПОЛИМЕРНЫХ КОМПОЗИЦИЙ
риката требуется для приваривания каждого последующего слоя к предыдущему применять инструмент, нагретый до температуры, превышающей температуру плавления термопластичного связующего. Так как драпировочные возможности ограничены, при формовании сложных по форме деталей на оснастке следует предусматривать плавные переходы с радиусом кривизны не менее 10 мм.
Рис.2.6. Схема выкладочных устройств при роликовой (а) и прессовой (б) выкладке термопластичных полуфабрикатов:
1 — нагревательное устройство; 2 — полуфабрикат; 3 — антиадгезионная разделительная пленка; 4 - прикаточный ролик; 5 - металлическая лента; 6 — нагретый инструмент; 7 - холодный инструмент; 8 - направляющие ролики; 9 — пакет; 10 - теплоизолирующая подложка; // — стол; Р — сила нагружения ролика; Q - натяжение полуфабриката
Напыление
Поскольку метод напыления представляет собой фактически механизированный вариант формования ручной выкладкой, к нему полностью можно отнести все рекомендации, касающиеся подготовки формы, нанесения разделительных слоев и гелькоата.
Схема напыления рубленого короткого волокна с наружным смешением компонентов связующего показана на рис. 2.7.
Измельченное волокно и смола одновременно вводятся в открытую форму или на нее. Ровинг волокна проходит через рубильное устройство и вдувается в поток смолы, который направляется в форму распылительной системой с наружным (случай 1) или внутренним (случай 2) смешением компонентов.
136
Рис.2.7. Безвоздушная система напыления с двумя емкостями:
1 — ровинг; 2 — смола с катализатором; 3 — рубильное устройство; 4 —
смола с ускорителем; 5 — уплотненный слой; 6 — валик; 7 — форма
1. Первая распылительная головка впрыскивает смолу,
предварительно смешанную с катализатором, или только ката
лизатор, в то время как вторая головка впрыскивает заранее
полученную смесь смолы с ускорителем.
2. Смола и катализатор подаются в смесительную каме
ру распылителя позади единственной распылительной го
ловки.
В обоих случаях полимерная композиция предварительно покрывает волокно, и объединенный поток равномерно распыляется в форме в соответствии с заданной схемой.
После введения в форму смеси смолы с волокном образовавшийся слой прикатывают вручную для удаления воздуха, уплотнения волокон и получения гладкой поверхности.
В состав установки для напыления входят устройства для подачи смолы и катализатора по шлангам к распылителю, включающие насосы, нагнетательные бачки; рубильное устройство для армирующего материала; распылительное устройство; регуляторы подачи воздуха и измерительные приборы.
При массовом производстве изделий методами ручной укладки и напылением обычно применяют роботы. Преимущество робота состоит в том, что его применение при формовании напылением позволяет выполнить жесткие требования по охране здоровья и безопасности труда на производстве. Схема трехкоординатного роботизированного автомата для напыления показана на рис. 2.8.
137
2.3. Контактное формование
2. ТЕХНОЛОГИЯ КОНСТРУКЦИЙ ИЗ ПОЛИМЕРНЫХ КОМПОЗИЦИЙ
риката требуется для приваривания каждого последующего слоя к предыдущему применять инструмент, нагретый до температуры, превышающей температуру плавления термопластичного связующего. Так как драпировочные возможности ограничены, при формовании сложных по форме деталей на оснастке следует предусматривать плавные переходы с радиусом кривизны не менее 10 мм.
Рис.2.6. Схема выкладочных устройств при роликовой (а) и прессовой (б) выкладке термопластичных полуфабрикатов:
1 — нагревательное устройство; 2 — полуфабрикат; 3 — антиадгезионная разделительная пленка; 4 — прикаточный ролик; 5 — металлическая лента; 6— нагретый инструмент; 7— холодный инструмент; 8— направляющие ролики; 9 — пакет; 10 — теплоизолирующая подложка; 11 — стол; Р — сила нагружения ролика; Q — натяжение полуфабриката
Напыление
Поскольку метод напыления представляет собой фактически механизированный вариант формования ручной выкладкой, к нему полностью можно отнести все рекомендации, касающиеся подготовки формы, нанесения разделительных слоев и гелькоата.
Схема напыления рубленого короткого волокна с наружным смешением компонентов связующего показана на рис. 2.7.
Измельченное волокно и смола одновременно вводятся в открытую форму или на нее. Ровинг волокна проходит через рубильное устройство и вдувается в поток смолы, который направляется в форму распылительной системой с наружным (случай 1) или внутренним (случай 2) смешением компонентов.
Рис.2.7. Безвоздушная система напыления с двумя емкостями:
/ — ровинг; 2 — смола с катализатором; 3 — рубильное устройство; 4 —
смола с ускорителем; 5 - уплотненный слой; 6 - валик; 7 - форма
1. Первая распылительная головка впрыскивает смолу,
предварительно смешанную с катализатором, или только ката
лизатор, в то время как вторая головка впрыскивает заранее
полученную смесь смолы с ускорителем.
2. Смола и катализатор подаются в смесительную каме
ру распылителя позади единственной распылительной го
ловки.
В обоих случаях полимерная композиция предварительно покрывает волокно, и объединенный поток равномерно распыляется в форме в соответствии с заданной схемой.
После введения в форму смеси смолы с волокном образовавшийся слой прикатывают вручную для удаления воздуха, уплотнения волокон и получения гладкой поверхности.
В состав установки для напыления входят устройства для подачи смолы и катализатора по шлангам к распылителю, включающие насосы, нагнетательные бачки; рубильное устройство для армирующего материала; распылительное устройство; регуляторы подачи воздуха и измерительные приборы.
При массовом производстве изделий методами ручной укладки и напылением обычно применяют роботы. Преимущество робота состоит в том, что его применение при формовании напылением позволяет выполнить жесткие требования по охране здоровья и безопасности труда на производстве. Схема трехкоординатного роботизированного автомата для напыления показана на рис. 2.8.
136
137
Рис.2.8. Трехкоординатный роботизированный автомат для напыления: 1 — привод продольного перемещения; 2 — форма; 3 — распылительное сопло; 4 — поворотная головка; 5 — подача волокна; 6 — привод вертикального перемещения; 7— привод поперечного перемещения; 8 — кабель; 9 — подача смолы; 10 — ленточные программные носители
Автоматизированная выкладка
Для получения открытых оболочек сложной формы с произвольной образующей используют технологию автоматизированной выкладки препрега, которая состоит в укладке препрега по заданным в схеме армирования направлениям на оправку. Автоматизированную выкладку препрега осуществляют в соответствии с программой перемещения головки выкладочного станка. Выкладку проводят в направлениях, обеспечивающих равновесие укладываемого препрега на оправке и не являющихся геодезическими. Для устранения неплотного прилегания слоев укладываемого препрега выкладку обычно сопровождают прикаткой препрега нежесткими роликами. При выкладке препрега достаточно большой ширины необходимо рационально раскраивать полуфабрикат с целью повышения коэффициента использования материала.
138
2. ТЕХНОЛОГИЯ КОНСТРУКЦИЙ ИЗ ПОЛИМЕРНЫХ КОМПОЗИЦИЙ
Препрег из однонаправленной ленты может выкладываться автоматом без образования складок только по линейчатым поверхностям, образуемым движением прямой линии по произвольным траекториям. Если поверхность изделия нельзя аппроксимировать линейчатыми поверхностями, то при выкладке используют однонаправленный препрег минимальной ширины или тканый препрег полотняного плетения.
Рис.2.9. Схема автоматизированной выкладки препрегом оболочки двойной кривизны:
/ - оправка; 2 — головка; 3 — устройство обрезки; 4 — рама; 5 — бобина с препрегом; 6 — разделительная пленка; 7 - нагреватель; 8 - суппорт; 9 - каретка; I...V - степени подвижности станка
Схема автоматизированной выкладки препрегом оболочки двойной кривизны показана на рис. 2.9. Подогрев укладываемого препрега повышает его деформативность в плоскости
139
2.4. Формование с эластичной диафрагмой
армирования, и при определенной ширине ленты удается выкладывать однонаправленный препрег на пологие поверхности двойной кривизны.
2.4. Формование с эластичной диафрагмой
Процессы формования в эластичном мешке заключаются в выкладке заготовок на плоскую или криволинейную форму и последующем формообразовании за счет разности давлений внутри и снаружи мешка по всей формуемой поверхности. Формующее давление может приближаться к атмосферному, когда внутри мешка создается разряжение (вакуумный метод), или превышать его, если формование осуществляется в автоклаве под давлением сжатых газов на заготовку, вакуумирован-ную внутри эластичного мешка (вакуумно-автоклавный метод). Рассмотрим эти методы подробнее.
Вакуумный метод
Вакуумное формование применяют для изготовления изделий с различными габаритными размерами.
Приложенное внешнее давление, воздействуя на материал заготовки через эластичную диафрагму, должно выполнить следующие функции:
уплотнить последовательные слои армирующего материала, выложенные на форме;
обеспечить качественную глубокую пропитку волокна связующим;
выдавить из пустот летучие побочные продукты реакции и пузырьки воздуха;
выдавить избыток смолы из слоев материала.
Поэтому в качестве матрицы выбирают связующие холодного или горячего отверждения, при полимеризации не выделяющие побочных газообразных продуктов, которые могут создать в материале значительно большее противодавление, чем давление формования, и вызвать тем самым расслоение материала детали.
2. ТЕХНОЛОГИЯ КОНСТРУКЦИЙ ИЗ ПОЛИМЕРНЫХ КОМПОЗИЦИЙ
В последние годы в качестве матрицы используют термопластичные связующие типа полисульфон, полиамид, поликап-роамид и другие.
Вследствие невысокого давления формования существенно ограничивается выбор армирующих материалов. В основном это стекловолокнистые материалы, так как их плотность и прочность сравнительно мало зависят от давления прессования. Тем не менее возможно применение любых волокнистых материалов.
Схемы вакуумного формования на внутренней (позитивной) и внешней (негативной) формах представлены на рис. 2.10.
К дйкуумному
Рис. 2.10.Схема установки прессования композитов вакуумным методом: а — с внутренней формой; б — с наружной формой; / — резиновый чехол; 2 — форма; 3 - заготовка; 4 - цулага или целлофан; 5 — основание; 6 - прижим
Выбор материала для формы обусловлен объемом производства изделий, габаритами и формой изделия, тепловыми характеристиками материала формы. При использовании термореактивных связующих горячего отверждения и термопластичных связующих формы изготавливают в основном из металлов и реже из гипса и слоистых пластиков. Для связующих холодного отверждения в случае небольшой партии изделий (5-10 формовок) применяют деревянные формы. Алюминиевые формы относят к наименее дорогой оснастке, но они менее долговечны, чем стальные, и обладают большим относительным линейным удлинением Д/ при изменении температуры оснастки, что отражается на точности изделий (табл. 2.3).
140
141
2.4. Формование с эластичной диафрагмой
Таблица 2.3
Дата добавления: 2018-05-02; просмотров: 1194; Мы поможем в написании вашей работы! |
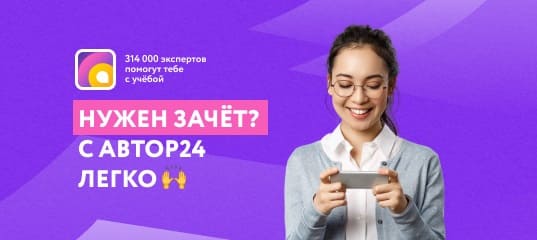
Мы поможем в написании ваших работ!