Технологический процесс изготовления хвостовых отсеков лопасти
Хвостовые отсеки состоят из сотовых заполнителей (фольга А1Т Δ-0.04 мм), вклеенных (клей ВК-8) между нервюрами и обшивками из стеклопластика. Обшивка хвостовых отсеков изготавливается из двух слоев стеклоткани АСТТ(σ)С1. на связующем ЭФ-32-301, которая усиливается специальными накладками тоже из стеклоткани (рис. 10). Стеклоткань, пропитанная связующим, раскраивается по шаблонам и укладывается на цулагу, покрытую предварительно антиадгезионной смазкой, так чтобы основа ткани была параллельна хорде. Усилительные накладки в районе нервюр раскраиваются под углом ±45. Собранные обшивки накрываются верхней цулагой и герметизируются баллонной тканью 500, кромки которой склеиваются клеем 88. Вакуумные трубки соединяются через штуцер со шлангом вакуум-насоса РВН-20, затем собранный пакет устанавливается в термошкаф и производится прессование обшивки под вакуумом Р = 0,6÷0,8 кгс/см при температуре 160±5°С в течение 1 ч. с момента достижения заданной температуры в клеевом соединении. Затем обшивки охлаждаются под вакуумом до температуры 40÷50°С, отключается вакуум-насос и производится распрессовка, зачистка и контроль качества склеивания обшивок. Нервюры изготавливаются из двух слоев стеклоткани, пропитанной связующим ЭФ-32-301, на оправках аналогичным способом.
Сборка и склеивание хвостовых отсеков производится на клее ВК-3 в специальных приспособлениях. Приспособление пружинного-вакуумного типа состоит из “ложного” лонжерона-оправки, обработанного по ШКС лонжерона и боковых металлических вкладышей, выполненных по ШВК нервюр. Давление создается специальными тарированными пружинами и струбцинами на нервюры и стрингер и вакуумным мешком на соты. Обшивка, нервюры и стрингер предварительно зашкуриваются и покрываются клеепленкой ВК-3; сотовый
|
|
блок, изготовленный методом растяжения, обезжиривается в бензине, затем по торцам сот наносится клей ВК-3 методом окунания или механизированно (на автомате УНК-2) [29].
После сборки отсека в приспособлении, производится загрузка отсеков в термошкаф, дается давление вакуума Р=0,6÷0,8 кгс/см2 на соты и Р=6 кгс/см2 на нервюры и стрингер. Отсек выдерживается при температуре 165±5°С в течение 1 ч. Температура контролируется термопарами, установленными на обшивку в разных точках. После охлаждения, распрессовки и зачистки отсек проверяется на непроклей, по контуру, взвешивается и сортируется по партиям.
Результаты взвешивания заносятся в весовой журнал, что дает возможность легко комплектовать хвостовые отсеки для сборки взаимозаменяемых лопастей.
Рис. 10. Схема прессования обшивки при помощи вакуума:
|
|
- стол;
- термопара;
- электронагреватель;
- теплоизолятор;
- клей № 88;
- баллонная ткань 500;
- трубка 10x8;
- мановакуумметр;
- форвакуумный бачок;
- вакуум-насос РВН-20
Технологический процесс изготовления противообледенительной системы лопасти вертолета автоклавным способом
Автоклавный способ прессования применяется для выклейки и приклейки пакетов электрической антиобледенительной системы на лопасти вертолетов, для прессования лонжеронов из стеклопластиков несущих и хвостовых винтов и других изделий сложной конфигурации и большой длины (до 20 м) (рис. 11).
Рис. 11. Схема запрессовки носка лопасти в автоклаве:
- прижимная рамка;
- форма;
- чехол;
- склеиваемый пакет;
- автоклав.
Рассмотрим процесс приклейки антиобледенительной системы лопасти вертолета. Противообледенительная система представляет собой пакет из нескольких слоев стеклоткани с вклеенным между ними электронагревательным элементом. Пакет приклеивается клеем ВК-3 горячего отверждения на лопасть в автоклаве. Автоклав имеет в длину 16 м, диаметр рабочего пространства 540 мм, рабочее давление 10 кгс/см2, максимальная температура нагрева 300°С. Давление в автоклаве регулируется электроконтактными манометрами ЭКМ-1. Регистрация процесса регулирования давления в автоклаве осуществляется самопишущим электрическим манометром типа МСТМ на бумажном диске, температура контролируется измерением температуры воздуха термопарами в шести точках, расположенных по длине автоклава. Регулирование температуры осуществляется электронным потенциометром ЭПП-09 с записью на бумагу. Секции нагревательного элемента рассчитаны таким образом, что при регулировании температуры прибором обеспечивается перепад температур по всей длине автоклава в пределах ±5°С. Несмотря на ряд существенных преимуществ этот метод склеивания получил широкое распространение лишь в опытном производстве. Причина этого в том, что срок службы вакуумных мешков при высокой температуре очень незначителен и, кроме того, на нагрев и охлаждение автоклава затрачивается много времени, что удлиняет цикл сборки.
|
|
Предварительно электронагревательный пакет выклеивают на оправке по форме носка лонжерона лопасти, затем на клеепленке ВК-3 приклеивают на лонжерон. Поверх пакета укладывают цулагу, покрытую предварительно антиадгезионной смазкой. В качестве цулаг (прокладок) обычно используют листовой авиаль АВАТ толщиной 0,3-0,4 мм, закаленный и состаренный. Применение прокладок из нержавеющей листовой стали нецелесообразно в связи с высокой пластичностью материала, такие прокладки легко деформируются от неровностей прижима и переносят эти неровности на поверхности изделия.
|
|
На цулагу навертывается слой дренажной сухой некондиционной стеклоткани. Затем прокладываются вакуумные трубки. Для этого обычно используют трубки медные диаметром 8-10 мм; отверстия в трубках диаметром 1,5-2 мм просверливаются в шахматном порядке с шагом 50-100 мм. Сверху трубки снова обматывают дренажной сухой стеклотканью, и весь пакет укладывают в мешок из ткани 500, заклеивают клеем 88 и дают вакуум 0,8-0,9 кг/см2, затем сборку устанавливают в автоклав.
В автоклаве производят прессование пакета антиобледенительной системы под давлением 4-6 кгс/см2 при температуре 160±5°С в течение 1 ч. Давление обеспечивается смесью воздуха и азота во избежание загорания ткани 500. После охлаждения, распрессовки и зачистки пакет электросистемы лопасти проверяют на качество склейки, контролируют контур по шаблону и проверяют электрические параметры: сопротивление изоляции и на пробой согласно ТУ на лопасть.
Сборка и склеивание лопасти
Лонжерон, собранный с наконечником и приклеенный противообледенительной системой, поступает на участок окончательной сборки (рис. 12). Здесь его зашкуривают, наносят подслой клея и прикатывают клеевую пленку в районе приклейки хвостовых отсеков. Скомплектованные хвостовые отсеки подгоняют по задней стенке лонжерона, зашкуривают и наносят подслой клея в районе склейки обшивки хвостового отсека с лонжероном. Затем на лонжерон, установленный в стапеле второго перехода, устанавливают хвостовые отсеки и межотсечные резиновые вкладыши. Производят запрессовку прижимами стапеля хвостовых отсеков к лонжерону, давление по боковым стенкам лонжерона Р=6 кгс/см2, по задней стенке лонжерона Р=0,8-0,6 кгс/см2 во избежание смятия хвостового отсека. Присоединяют термопары и производят нагрев и выдержку в зоне склейки до температуры отверждения клея.
После запрессовки лопасть вынимают из стапеля и производят внестапельные работы: зачищают от подтеков клея и подают на контроль склейки, контроль по контуру, закрутки и другим геометрическим параметрам. Затем производят установку балансировочных бобышек, концевого и комлевого обтекателя, проверку электросистемы на пробой и сопротивление электроизоляции, производят окраску лопастей и балансировку для определения статического момента МСТ продольной и поперечной центровки zц.т. и xц.т. каждой лопасти. После этого заполняется формуляр на комплект лопастей, и лопасти передаются для установки на вертолет.
Рис. 12. Технологический процесс изготовления стеклопластиковой лопасти
Дата добавления: 2018-05-01; просмотров: 1155; Мы поможем в написании вашей работы! |
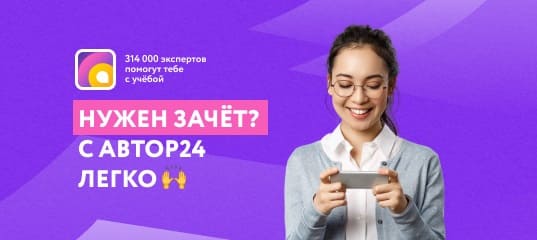
Мы поможем в написании ваших работ!