Технологический процесс изготовления лопастей контактным способом
Контактный способ наиболее примитивен и не требует сложной технологической оснастки. Его широко применяют у нас и за рубежом при изготовлении корпусов судов, кузовов и кабин автомобилей, лопастей градирен, деталей фюзеляжа легких самолетов и вертолетов, лопастей ветряков, лопастей пропеллеров легких самолетов, хвостовых винтов (рис. 4). Рассмотрим технологический процесс изготовления лопасти хвостового винта (контактный метод). Обводы лопасти создаются многослойной обшивкой из стеклоткани, идущей поверх пенопластового заполнения. Оптимальная центровка достигается за счет сочетания специальной укладки слоев в носовой части лопасти, наконечник лопасти крепится на болтах.
Раскроенная по шаблонам стеклоткань предварительно комплектуется в пакеты. На оправку покрытую предварительно антиадгезионной смазкой (ЦИАТИМ-201, КПМС-31 и др.), наносится подслой связующего и укладывается первый слой стеклоткани, затем производится нанесение связующего, обычно холодного отверждения (например, полиэфирного ПН-1) на стеклоткань и т.д.
После укладки слоев нижней обшивки производится укладка обработанного по контуру пенопластового заполнителя (например, ПХВ или ПС), предварительно зашкуренного и покрытого связующим, затем производится укладка слоев стеклоткани верхней обшивки с последующей их пропиткой связующим. Лопасть выдерживается в форме 24 ч. для полного отверждения связующего; производится выемка лопасти, зачистка потеков связующего; проверка качества склеивания, контроля контура лопасти и взвешивание. Затем производится подгонка и установка комлевого узла для стыка лопасти со втулкой. После установки комлевого узла лопасти окрашивают, балансируют и подают в цех окончательной сборки вертолета. Окончательное формование имеет свою специфику, поскольку в связующем отсутствуют летучие вещества, ибо по существу отпадает необходимость в прессовании выложенной заготовки - достаточно контакта каждого укладываемого слоя с предыдущим слоем и некоторого их уплотнения роликом.
|
|
Рис. 4. Схема формования контактным способом:
- формуемое изделие;
- негативная форма.
Достоинства контактного метода:
- простота оснастки, которая сводится к несложной форме (оправке);
- отсутствие необходимости в сложном прессовом и нагревательном оборудовании;
- легкость выкладки на форму полотнищ рулонного материала с жидким связующим.
Эти достоинства позволяют получить таким методом крупногабаритные изделия сложнейших форм.
Недостатки контактного метода:
- нестабильность содержания связующего в стеклопластике и неравномерность его распределения по объему изделия из-за ручного метода нанесения;
- высокое (до 60%) содержание связующего в стеклопластике, приводящее к пониженным механическим свойствам:
;
|
|
- зависимость качества изделия от квалификации формовщика;
- длительность цикла изготовления (24 ч. и более);
- высокая трудоемкость ручной пропитки армирующего материала;
- токсичность компонентов связующего
Технологический процесс изготовления лонжеронов лопасти методом пропитки под давлением
Метод пропитки давлением предусматривает использование пресс-формы и установки для подачи связующего под давлением. Зазор между пуансоном и матрицей соответствует толщине лонжерона. Установка для подачи связующего включает в себя бачок со связующим, компрессорную установку для подачи связующего под давлением и систему управления подачей связующего (рис. 5).
Рис. 5. Схема установки для пропитки под давлением
- На пуансон (оправку), покрытый предварительно антиадгезионной смазкой, в сухом виде укладываются слои стеклоткани или шпон из углеволокна. Раскрой армирующего материала производится по шаблонам.
- Пуансон с набранным пакетом стеклоткани укладывается в пресс-форму и плотно закрывается крышкой. Питательное устройство подсоединяется к установке со связующим, а отсасывающее устройство - к вакуум-насосу. Предварительно дается разрежение для удаления лишних пузырьков воздуха между слоями стеклоткани, затем подается связующее под давлением от 2 до 6 атм и производится пропитка лонжерона. Когда в ловушке-фильтре появится смола, входные и выходные отверстия закрываются и производится полимеризация связующего нагревателями, смонтированными в пресс-форме. После распрессовки и зачистки лонжерона производится контроль качества склейки, контура и подача на сборку лопасти (стабилизатора, крыла). При таком способе пропитки получается изделие высокого качества (точно выдерживается толщина лонжерона, пластик имеет высокие физикомеханические свойства). Процесс пропитки может быть механизирован, а при намотке сухого армирующего материала на оправку и пропитке под давлением исключается контакт рабочих со связующим и стекловолокном, что значительно улучшает условия труда. Недостатком этого метода является дорогостоящая сложная оснастка. Применяется метод пропитки под давлением для изготовления лонжеронов, нервюр, обтекателей и других изделий.
|
|
Дата добавления: 2018-05-01; просмотров: 767; Мы поможем в написании вашей работы! |
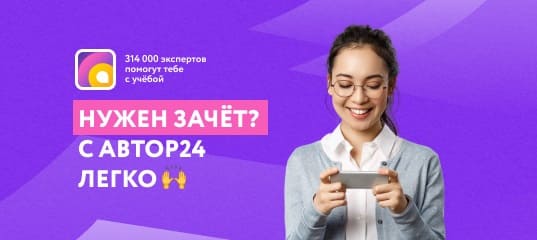
Мы поможем в написании ваших работ!