Классификация конструкционных материалов
Перечень конструкционных материалов, применяемых в машино- и приборостроении, велик, и классифицировать их можно по разным признакам. Большинство из них, например, стали, чугуны, сплавы на основе меди и легких металлов, являются универсальными. Они обладают многочисленными достоинствами и используются в различных деталях и конструкциях.
Наряду с универсальными применяют конструкционные материалы определенного функционального назначения: жаропрочные, материалы с высокими упругими свойствами, износостойкие, коррозионно- и жаростой кие.
Предлагаемая классификация подразделяет конструкционные мате риалы по свойствам, определяющим выбор материала для конкретных деталей и конструкций. Каждая группа материалов оценивается соответствующими критериями, обеспечивающими работоспособность в эксплуатации. Универсальные материалы рассматриваются в нескольких группах, если возможность применения их определяется различными критериями.
В соответствии с выбранным принципом классификации все конструкционные материалы подразделяют на следующие группы.
1. Материалы, обеспечивающие жесткость, статическую и циклическую прочность (стали).
2. Материалы с особыми технологическими свойствами.
3. Износостойкие материалы.
4. Материалы с высокими упругими свойствами.
5. Материалы с малой плотностью.
6. Материалы с высокой удельной прочностью.
7. Материалы, устойчивые к воздействию температуры и рабочей среды.
|
|
Глава 9
СТАЛИ, ОБЕСПЕЧИВАЮЩИЕ ЖЕСТКОСТЬ, СТАТИЧЕСКУЮ И ЦИКЛИЧЕСКУЮ ПРОЧНОСТЬ
Детали машин и приборов, передающих нагрузку, должны обладать жесткостью и прочностью, достаточными для ограничения упругой и пластической деформации, при гарантированной надежности и долговечности. Из многообразия материалов в наибольшей степени этим требованиям удовлетворяют сплавы на основе железа —■ чугуны и особенно стали. Стали обладают высоким, наследуемым от железа, модулем упругости (£ = 210ГПа).
Высокую жесткость стали сочетают с достаточной статической и циклической прочностью, значение которой можно регулировать в широком диапазоне изменением концентрации углерода, легирующих элементов и технологии термической и химико-термической обработки.
Кроме комплекса этих важных для работоспособности деталей свойств стали могут обладать и рядом других ценных качеств, делающих их универсальным материалом. При соответствующем легировании и технологии термической обработки сталь становится либо износостойкой, либо коррозионно-стойкой, либо жаростойкой и жаропрочной, а также приобретает особые магнитные, тепловые или упругие свойства. Сталям свойственны также хорошие технологические свойства. К тому же они сравнительно недороги.
|
|
Благодаря этим достоинствам стали — основной металлический материал промышленности. Разработано около 2000 марок сталей и сплавов на основе железа.
Классификация конструкционных сталей
Стали классифицируют по химическому составу, качеству, степени раскисления, структуре, прочности и назначению.
По химическому составу стали классифицируют на углеродистые и легированные. В зависимости от концентрации углерода те и другие подразделяют на низкоуглеродистые (< 0,3 % С), среднеуглеродистые (0,3 -
0,7 % С) и высокоуглеродистые (> 0, 7 % С). Легированные стали в зависимости от введенных элементов подразделяют на хромистые, марганцовистые, хромоникелевые, марганцевые и многие другие. По количеству введенных элементов их разделяют на низко-, средне- и высоколегированные. В низколегированных сталях количество легирующих элементов не превышает 5 %, в среднелегированных содержится от 5 до 10 %, в высоколегированных — более 10 %.
По качеству стали классифицируют на стали обыкновенного качества, качественные, высококачественные и особовысококачественные.
|
|
Под качеством стали понимают совокупность свойств, определяемых металлургическим процессом ее производства. Однородность химического состава, строения и свойств стали, а также ее технологичность во многом зависят от содержания газов (кислорода, водорода, азота) и вредных примесей — серы и фосфора. Газы являются скрытыми, количественно трудно определяемыми примесями, поэтому нормы содержания вредных примесей служат основными показателями для разделения сталей по качеству. Стали обыкновенного качества содержат до 0,050 % S и 0,040 % Р, качественные — не более 0,04 % S и 0,035 % Р, высококачественные — не более 0,025 % S и 0,025 % Р, особо высококачественные — не более 0,015 % S и 0,025 % Р.
По степени раскисления и характеру затвердевания стали классифицируют на спокойные, полуспокойные и кипящие.
Раскисление — процесс удаления из жидкого металла кислорода, проводимый для предотвращения хрупкого разрушения стали при горячей деформации.
Спокойные стали раскисляют марганцем, кремнием и алюминием. Они содержат мало кислорода и затвердевают спокойно без газовыделения. Кипящие стали раскисляют только марганцем. Перед разливкой в них содержится повышенное количество кислорода, который при затвердевании, частично взаимодействуя с углеродом, удаляется в виде СО. Выделение пузырей СО создает впечатление кипения стали, с чем и связано ее название. Кипящие стали дешевы, их производят низкоуглеродистыми и практически без кремния (Si< 0,07%), но с повышенным количеством газообразных примесей.
|
|
Полуспокойные стали по степени раскисления занимают промежуточное положение между спокойными и кипящими.
При классификации стали по структуре учитывают особенности ее строения в отожженном и нормализованном состояниях. По структуре в отожженном (равновесном) состоянии конструкционные стали разделяют на четыре класса: доэвтектоидные, имеющие в структуре избыточный
феррит; эвтекгпоидные, структура которых состоит из перлита; ayemv-
ншпные и ферритные.
Углеродистые стали могут быть первых двух классов, легированные — всех классов. Стали аустенитного класса образуются при введении большого количества (правее точки 6, см. рис. 4.19) элементов Ni, Мп, расширяющих 7-область; стали ферритного класса — при введении элементов Сг, Si, V, W и др., расширяющих а-область (см. рис. 4.20).
По структуре после нормализации стали подразделяют на следующие основные классы: перлитный, мартенситный, аустенитный, ферритный.
Стали перлитного класса имеют невысокую устойчивость переохлажденного аустенита (рис. 9.1, а). При охлаждении на воздухе они приобретают структуру перлита, сорбита или троостита, в которой могут присутствовать также избыточные феррит или карбиды. К этому классу относятся углеродистые и низколегированные стали. Это большая группа дешевых, широко применяемых сталей.
Стали мартенситного класса отличаются высокой устойчивостью переохлажденного аустенита (рис. 9.1,6); при охлаждении на воздухе они закаливаются на мартенсит. К этому классу относятся средне- или высоколегированные стали.
Стали аустенитного класса из-за повышенного количества никеля или марганца (обычно в сочетании с хромом) имеют интервал мартенситного превращения ниже 0°С и сохраняют аустенит при 20 — 25 °С (рис. 9.1, в). Распад аустенита в перлитной и промежуточной областях отсутствует.
Структурный класс аустенитных и ферритных сталей совпадает по классификации как в отожженном, так и нормализованном состояниях.
а б Рис. 9.1. Схемы изотермического распада аустенита сталей перлитного (а), мартенситного (б) и аустенитного (в) классов |
По прочности, оцениваемой временным сопротивлением, конструкционные стали с некоторой условностью можно разделить на стали нормальной (средней) прочности (сгв < 1000 МПа), повышенной прочности (сгв < 1500 МПа) и высокопрочные (ств > 1500 МПа).
2\\
|
|
Гиг. 0.2. Влияние углерода на мсхпии'кч-кис свойства горяче-кйтммых г талей |
I пи а и же структура характерна и для сталей в горячекатаном состоянии без тер-ммчггкой обработки. |
Но назначению конструкционные стали подразделяю! на машиностроительные, предназначенные для изготовления деталей машин и механизмов, и строительные, используемые для металлоконструкций и со-
оружении.
9.2. Влияние углерода и постоянных примесей на свойства сталей
Стали — сложные по составу железо-углеродистые сплавы. Кроме железа и углерода — основных компонентов, а также возможных легирующих элементов стали содержат некоторое количество постоянных и случайных примесей, влияющих на их свойства.
Углерод, концентрация которого в конструкционных сталях достигает 0,8 %, оказывает определяющее влияние на их свойства. Степень его влияния зависит от структурного состояния стали, ее термической обработки.
После отжига углеродистые конструкционные стали имеют феррит-но-перлитную структуру, состоящую из двух фаз — феррита и цементита . Количество цементита, который отличается высокой твердостью и хрупкостью, увеличивается пропорционально концентрации углерода. В связи с этим, по мере повышения содержания углерода, возрастают прочность и твердость, но снижаются пластичность и вязкость (рис. 9.2).
Кроме того, углерод заметно повышает верхний порог хладноломкости, расширяя тем самым температурный интервал перехода стали в хрупкое состояние (рис. 9.3). Каждая 0,1 % С повышает верхнюю границу этого перехода примерно на 20 °С. При 0,4% С порог хладноломкости равен 0°С, при большей концентрации углерода эта температура достигает 20 °С; такие стали менее надежны в работе.
Влияние углерода еще более значительно при неравновесной структуре стали. После закалки на мартенсит временное сопротивление сталей
интенсивно возрастет по мерс увеличения содержания углерода и достигает максиму ма при 0,4 % С. При низком отпуске механические свойства сталей полностью определяются концентрацией углерода в твердом растворе.
Рис. 9.3. Влияние содержания углерода на хладноломкость сталей |
Углерод изменяет технологические свойства стали. При увеличении его содержания снижается способность сталей деформироваться в горячем и особенно в холодном состояниях, затрудняется свариваемость.
Постоянные примеси в стали: Mn, Si, S, Р, а также газы Ог, N2, Щ.
Марганец — полезная примесь; вводится в сталь для раскисления и остается в ней в количестве 0,3 - 0,8%. Марганец уменьшает вредное влияние серы и кислорода.
Кремний — полезная примесь; вводится в сталь в качестве активного раскислителя и остается в ней в количестве до 0,4%, оказывая упрочня ющее действие.
Сера — вредная примесь, вызывающая красноломкость стали хрупкость при горячей обработке давлением. В стали она находится в виде сульфидов. Красноломкость связана с наличием сульфидов FeS, кото рые образуют с железом эвтектику, отличающуюся низкой температурой плавления (988°С) и располагающуюся по границам зерен. При горячей деформации границы зерен оплавляются, и сталь хрупко разрушается.
От красноломкости сталь предохраняет марганец, который связывает серу в сульфид MnS, исключающий образование легкоплавкой эвтектики.
Устраняя красноломкость, сульфид MnS, так же как и другие неметаллические включения (оксиды, нитриды и т.п.), служат концентратора ми напряжений, снижают пластичность и вязкость сталей. Содержание серы в стали строго ограничивают. Положительное влияние серы про является лишь в улучшении обрабатываемости резанием.
Фосфор — вредная примесь. Он растворяется в феррите, упрочняет его, но вызывает хладноломкость — снижение вязкости по мере пониже ния температуры. Сильное охрупчивающее действие фосфора вы ража ется в повышении порога хладноломкости (рис. 9.4). Каждая 0,01 % 1' повышает порог хладноломкости на 25 °С. Хрупкость стали, вызываемая фосфором, тем выше, чем больше в ней углерода.
кси. мдж/м2 Фосфор — крайне нежелательная при-
месь в конструкционных сталях. Современные методы выплавки и переплавки не обеспечивают его полного удаления, поэтому основной путь его снижения — повышение качества шихты.
Кислород, азот и водород — вредные
скрытые примеси. Их влияние наиболее
-80 -40 о г, °с сильно проявляется в снижении пластич-
Рис. 9.4. Влияние фосфора ности и повышении склонности стали к
на хладноломкость стали: хрупкому разрушению.
1 - 0,008 % Р; 2 - 0,06 % Р v .
Кислород и азот растворяются в феррите в ничтожно малом количестве и загрязняют сталь неметаллическими включениями (оксидами, нитридами). Кислородные включении способствуют красно- и хладноломкости, снижают прочность. Повышенное содержание азота вызывает деформационное старение. Атомы азота в хо-лоднодеформированной стали скапливаются на дислокациях, образуя атмосферы Коттрелла, которые блокируют дислокации. Сталь упрочняется, становится малопластичной. Старение особенно нежелательно для листовой стали (< 0,1% С), предназначенной для холодной штамповки. Последствия старения — разрывы при штамповке или образование на поверхности листов полос скольжения, затрудняющих их отделку1.
Водород находится в твердом растворе или скапливается в порах и на дислокациях. Хрупкость, обусловленная водородом, проявляется тем резче, чем выше прочность материала и меньше его растворимость в кристаллической решетке. Наиболее сильное охрупчивание наблюдается в закаленных сталях с мартенситной структурой и совсем отсутствует в аустенитных сталях.
Повышенное содержание водорода при выплавке стали может приводить к флокенам. Флокенами называют внутренние надрывы, образующиеся в результате высоких давлений, которые развивает водород, выделяющийся при охлаждении в поры вследствие понижения растворимости. Флокены в изломе имеют вид белых пятен, а на поверхности — мелких
Для устранения хрупкости листы перед штамповкой подвергают волнообразному и и ибу со слабым обжатием. При этой операции дислокации, отрываясь от окружающих их атмосфер, приобретают подвижное ть. Пластичность временно носе i ананлинаекя, и ciajn, хорошо iirniMlive i ся.
79
трещин. Этот дефект обычно встречается в крупных поковках хром и стых и хромоникелевых сталей. Для его предупреждения стали после горячей деформации медленно охлаждают или длительно выдерживают при 250°С. При этих условиях водород, имеющий большую скорость диффу зии, не скапливается в порах, а удаляется из стали.
Наводороживание и охрупчивание стали возможны при травлении в кислотах, нанесении гальванических покрытий и работе в водородсодер-жащих газовых средах.
Случайные примеси — элементы, попадающие в сталь из вторичного сырья или руд отдельных месторождений. Из скрапа в стали попадает сурьма, олово и ряд других цветных металлов. Стали, выплавленные из уральских руд, содержат медь, из керченских — мышьяк. Случайные примеси в большинстве случаев оказывают отрицательное влияние на вязкость и пластичность сталей.
9.3. Углеродистые стали
На долю углеродистых сталей приходится 80 % от общего объема. Это объясняется тем, что углеродистые стали дешевы и сочетают удовлетворительные механические свойства с хорошей обрабатываемостью резанием и давлением. При одинаковом содержании углерода по обрабатываемости резанием и давлением они значительно превосходят легированные стали. Однако углеродистые стали менее технологичны при термической обработке. Из-за высокой критической скорости закалки углеродистые стали охлаждают в воде, что вызывает значительные деформации и коробление деталей. Кроме того, для получения одинаковой прочности с легированными сталями их следует подвергать отпуску при более низкой температуре, поэтому они сохраняют более высокие закалочные напряжения, снижающие конструкционную прочность.
Главный недостаток углеродистых сталей — небольшая прокаливае-мость (до 12 мм), что существенно ограничивает размер деталей, упрочняемых термической обработкой. Крупные детали изготовляют из сталей без термического упрочнения — в горячекатаном или нормализованном состояниях, что требует увеличения металлоемкости конструкций.
По статической прочности углеродистые стали относятся преимущественно к сталям нормальной прочности. Углеродистые конструкционные стали выпускаю! двух видов: обыкновенного качества и качественные.
Дата добавления: 2018-04-05; просмотров: 1151; Мы поможем в написании вашей работы! |
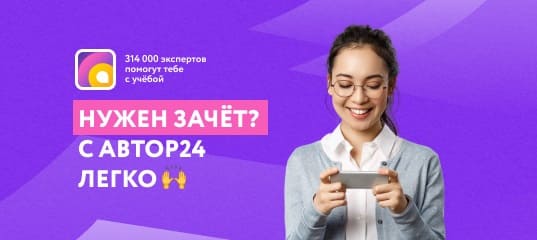
Мы поможем в написании ваших работ!