Легированные стали нормальной и повышенной статической прочности
Из сталей нормальной и повышенной прочности наибольшее применение в машино- и приборостроении имеют низкоуглеродистые (цементуемые) и среднеуглеродистые (улучшаемые) стали, содержащие, как правило, в сумме не более 5 % легирующих элементов.
Низкоуглеродистые (0,1 - 0,3 % С) легированные стали (табл. 9.7) используют в состоянии наибольшего упрочнения, т.е. после закалки и низкого отпуска со структурой (в зависимости от состава стали) низкоуглеродистого мартенсита или бейнита. Повышенные прочностные свойства сочетаются у них с хорошей пластичностью, вязкостью, малой чувствительностью к надрезам и высоким сопротивлением развитию вязкой трещины.
Таблица 9.7. Содержание элементов в легированных конструкционных сталях (ГОСТ 4543-71),%
Марка | с | Мп | Сг | Ni | Мо | Прочие |
стали | ||||||
Низкоуглеродистые стали | ||||||
15Х | 0,12-0,18 | - | 0,7-1 | - | - | - |
15ХГМ | 0,23-0,29 | 0,9-1,2 | 0,9-1,2 | - | 0,2-0,3 | ~ |
зохгт | 0,24-0,32 | 0,8-1,1 | 1-1,3 | - | - | 0,03-0,09 Ti |
20ХНЗА | 0,17-0,24 | - | 0,6-0,9 | 2,75-3,15 | — | |
12Х2Н4А | 0,09-0,15 | - | 1,25-1,65 | 3,25-3,65 | — | |
18Х2Н4МА | 0,14-0,2 | - | 1,35-1,65 4-4,4 0,3-0,4 | |||
Среднеуглеродистые стали | ||||||
■nix | 0,36-0,44 | - | 0,8-1,1 | - | - | - |
40ХГТР | 0,38-0,45 | 0,7-1 | 0,8-1,1 | - | — | 0,03-0,09 Ti |
зохгса* | 0,28-0,34 | 0,8-1,1 | 0,8-1,1 | — | ||
10ХН2МА | 0,37-0,44 | - | 0,6-0,9 | 1,25-1,65 | 0,15-0,25 | ~ |
ЗКХНЗМФА | 0,33-0,4 | - | 1,2-1,5 | 3-3,5 | 0,35-0,45 | 0,1 -0,18 V |
:шЧ'2МЮЛ | 0,35-0,42 | - | 1,35-1,65 | - | 0,15-0,25 | 0,7- 1,1 А1 |
"I............
и высококачественных сталей |
Истли 1 ак же содержи кя 0,!) 1,'JTtSi |
Примечания: 1. Концентрации марганца и кремния как постоянных тмесеи in- укачаны. 2. Сера и фосфор находится в пределах норм для качественных
|
Таблица 9.8. Режимы термической обработки и механические: свойства низкоуглеродистых сталей
Температура, | Механические свойства | |||||||
Марка | °С | (не менее) | ||||||
стали | закалки | отпуска | Тв | "0,2 | 6 | Ф | KCU, | |
I | II | МПа | % | МДж/м2 | ||||
15Х | 880 | 770 - 820 | 180 | 700 | 500 | 12 | 45 | 0,7 |
15ХФ | 880 | 760-810 | 180 | 750 | 550 | 13 | 50 | 0,8 |
ЗОХГТ | 880 | 850 | 200 | 1500 | 1300 | 9 | 40 | 0,6 |
25ХГМ | 860 | - | 200 | 1200 | 1100 | 10 | 45 | 0,8 |
12ХНЗА | 860 | 760-810 | 180 | 950 | 700 | 11 | 55 | 0,9 |
12Х2Н4А | 860 | 760 - 800 | 180 | 1150 | 950 | 10 | 50 | 0,9 |
18Х2Н4МА | 950 | 860 | 200 | 1150 | 850 | 12 | 50 | 1 |
Функциональное назначение низкоуглеродистых сталей — цементуемые (нитроцементуемые) детали (зубчатые колеса, кулачки и т.п.), работающие в условиях трения. После насыщения поверхности углеродом, закалки и низкого отпуска низкоуглеродистые стали наряду с твердой поверхностью (58 - 63 HRC) имеют достаточно прочную и вязкую сердцевину, устойчивую к воздействию циклических и ударных нагрузок. Работоспособность цементованных деталей зависит от свойств поверхностного слоя и сердцевины. При одних и тех же свойствах цементованного слоя работоспособность деталей повышается по мере увеличения предела текучести и твердости сердцевины. При недостаточном уровне этих свойств под цементованным слоем происходит пластическая деформация, которая вызывает его преждевременное разрушение.
|
|
Благоприятное сочетание прочности, пластичности и вязкости, а также высокая хладостойкость (порог хладноломкости лежит в области отрицательных температур) обусловливают применение низкоуглеродистых сталей и без поверхностного упрочнения. Механические свойства таких сталей (без поверхностного упрочнения) после двойной закалки и низко го отпуска, т.е. термической обработки цементуемых деталей, приведены в табл. 9.8. При использовании этих сталей для деталей, от которых не требуется износостойкая поверхность, проводят однократную закалку по режиму I и низкий отпуск. Псе стали, кроме 18X211 1МЛ, приведенные в табл. 9.8, относятся к перлитному классу.
Хромистые стали 15Х, 20Х, а также содержащие дополнительно вакаций (1Г>ХФ) или бор (20ХР), образуют группу дешевых сталей нормальной прочности. Для уменьшения коробления их закаливают не в воде, а в ма г;н'. II результате они приобретают структуру троостита или бейнита и упрочняются несколько меньше (см. табл. 9.8). Стали этой группы применяют для небольших деталей (сечением не более 25 мм), работающих при средних нагрузках.
|
|
К труппе сталей повышенной прочности относятся комплексно-легированные, а также экономно-легированные стали с повышенным содержанием углерода (0,25 - 0,30 %).
Хромой и келевые стали 12ХНЗА, 20ХНЗА, 12Х2Н4А, 20Х2Н4А применяют для крупных деталей ответственного назначения. После закалки N масле эти стали в сечениях до 100 мм имеют структуру низкоуглеро-дмстого мартенсита в смеси с нижним бейнитом, которая обеспечивает io'ieiaiiHc высокой прочности и вязкости.
Хромоникельмолибденовая (хромоникельвольфрамовая) сталь
18Х2Н4МА (18Х2Н4ВА) наиболее высоколегирована и имеет высокие механические свойства.
И этой стали отсутствует перлитное превращение, а температурный интервал бейнитного превращения практически сливается с мартенсит-ИЫм, поэтому при любом, даже очень медленном охлаждении получается струк тура мартенсита (или смеси мартенсита и бейнита). Отжиг для нее неприменим. II качестве смягчающей операции проводят высокий отпуск ИИ сорбит.
|
|
(/таль 18Х2Н4МА относится к мар-
ижсипншу классу, закаливается на
HOiayxe и прокаливается практически
И любом сечении. Ее применяют для
крупных деталей особо ответственного
мши,пения, (/таль 18Х2Н4МА
Рис. 9.9. Влияние температуры отпуска на механические гпойстпа стали 18Х2Н4ПА |
(IHX2H 1ПЛ) из за присутствия молиб-,UMia (вольфрама) слабо ра.зупрочняет-< и при отпуске (рис. 9.9). Ее исполь-»уич ia к же в улучшенном состоянии при больших статических и ударных it a i ру 1клх.
ЦелоеI л I нами срецне.'нч иронанных • тлей,содержащих II 1'Л Ni, являю!
ся высокая стоимость и усложненный цикл химико-термической обработки. В присутствии легирующих элементов точка Мк для высокоуглеродистого цементованного слоя смешается значительно ниже 0°С, поэтому после закалки в нем сохраняется до 60 % остаточного аустенита. Стали необходимо обрабатывать холодом для того, чтобы вызвать превращение остаточного аустенита в мартенсит и обеспечить высокую твердость поверхности.
Хромомарганцевые стали с титаном (18ХГТ, ЗОХГТ) и молибденом (25ХГМ) относятся к экономно-легированным и предназначены для замены хромоникелевых сталей. Вместо никеля они содержат марганец; титан и молибден введены для измельчения зерна и снижения чувствительности к перегреву. Прокаливаемость сталей составляет 35 - 60 мм. В таких сечениях по прочности и твердости они превосходят хромоникелевые стали, но уступают им по вязкости. Эти стали применяют для деталей крупносерийного и массового производства (зубчатых колес автомобилей).
Среднеуглеродистые (0,3-0,5% С) легированные стали (см. табл. 9.7) приобретают высокие механические свойства после термического улучшения — закалки и высокого отпуска (500 — 650°С) на структуру сорбита. Улучшение этих сталей в отличие от нормализации обеспечивает повышенный предел текучести в сочетании с хорошей пластичностью и вязкостью, высоким сопротивлением развитию трещины. Кроме того, улучшение заметно снижает порог хладноломкости, который в этих сталях, в отличие от низкоуглеродистых, лежит при более высоких температурах.
Улучшаемые легированные стали применяют для большой группы деталей машин, работающих не только при статических, но и в условиях циклических и ударных нагрузок (валы, штоки, шатуны и др.), концентрации напряжений, а в некоторых случаях и при пониженных температурах. При выборе стали кроме предела текучести, вязкости, чувствительности к надрезу важное значение имеют верхний Ц0 и нижний Ц0 пороги хладноломкости, сопротивление усталости.
Высокие механические свойства при улучшении возможны лишь при обеспечении требуемой прокаливаемости, которая служит важнейшей характеристикой при выборе этих сталей. Кроме прокаливаемости в сталях важно получить мелкое зерно и не допустить развития отпускной хрупкости.
Механические свойства улучшаемых сталей определяются температурой отпуска, так как в зависимости от легирования разупрочнение одних сталей при отпуске идет быстрее, других — медленнее. Однако при обработке на одинаковую прочность (например, полученную подбором
температуры отпуска) стандартные механические свойства, определяемые при растяжении, поручаются достаточно близкими (табл. 9.9). Различие состоит в параметрах надежности, которые более чувствительны к изменению структуры и состава стали.
Таблица 9.9. Термическая обработка и механические свойства улучшаемых легированных сталей
Марка | Температура закал- | Отпуск | О-в | СО,2 | 6 | Ф | кси, МДж/м2 | в ^50 | и *50 | |
t, °С | Среда | МПа | % | о | С | |||||
не менее | ||||||||||
ки, °С |
| |||||||||
40Х | 860 | 500 | Вода, масло | 1000 | 800 | 10 | 45 | 0,6 | 0 | -100 |
50Х | 830 | 520 | То же | 1100 | 900 | 9 | 40 | 0,4 | 20 | 60 |
ЗОХГСА | 880 | 540 | 5, | 1100 | 850 | 10 | 45 | 0,5 | 20 | 60 |
40ХН | 820 | 500 | 55 | 1000 | 800 | 11 | 45 | 0,7 | -30 | 100 |
40ХН2МА | 850 | 620 | 3) | 1100 | 950 | 12 | 50 | 0,8 | -40 | 120 |
38ХНЗМА | 850 | 600 | Воздух | 1200 | 1100 | 12 | 50 | 0,8 | -60 | -140 |
Хромистые стали 40Х, 45Х, 50Х (см. табл. 9.7) относятся к дешевым конструкционным материалам. С увеличением содержания углерода возрастает прочность, но снижаются пластичность и вязкость, повышается порог хладноломкости этих сталей (см. табл. 9.9). Хромистые стали склонны к отпускной хрупкости, устранение которой требует быстрого охлаждения от температуры высокого отпуска. Стали прокаливаются на глубину 15 - 25 мм, их применяют для производства деталей небольшого сечения. Причем стали 45Х, 50Х из-за невысокой вязкости рекомендуются для изделий, работающих без значительных динамических нагрузок.
Хромокремнемарганцевые стали ЗОХГСА, 35ХГСА содержат по 1 % Сг, Мп и Si и называются хромансилями. Это дешевые стали, сочетающие хорошие технологические и механические свойства. Хромансили свариваются всеми видами сварки, хорошо штампуются, удовлетворительно обрабатываются резанием, прокаливаются в деталях сечением 30 - 40 мм. Их широко применяют в автомобилестроении (валы, сварные конструкции, детали рулевого управления).
Хромоникелевые стали 10ХН, 15ХН, 50ХН обеспечивают высокий комплекс механических с вой с i в в деталях сечением -10 50 мм. Из-за
присутствия никеля эти стали, в отличие от хромистых, имеют более высокий температурный запас вязкости и меньшую склонность к хрупкому разрушению.
Хромоникельмолибденовые (хромоникельвольфрамовые) стали 40ХН2МА, 38ХНЗМА, 38ХНЗМФА, а также 18Х2Н4МА (18Х2Н4ВА) относятся к глубокопрокаливающимся сталям, предназначенным для деталей с поперечным сечением 100 мм и более. Их комплексное легирование обусловлено тем, что применение чисто хромоникелевых сталей нецелесообразно, так как они имеют сильно выраженную склонность к отпускной хрупкости. Для ее устранения в деталях большого сечения недостаточно быстрого охлаждения от температуры высокого отпуска. Поэтому хромо-никелевые стали легируют молибденом (вольфрамом).
Стали относятся к мартенситному классу, закаливаются на воздухе, обладают малой склонностью к хрупкому разрушению, хорошо работают при динамических нагрузках и в условиях пониженных температур. Кроме того, стали слабо разупрочняются при нагреве и могут применяться при температурах до 300 - 400 °С. Они предназначены для деталей наиболее ответственного назначения (валы и роторы турбин, тяжелонагру-женные детали компрессорных машин, редукторов).
Недостатки этой группы сталей: высокая стоимость, пониженная обрабатываемость резанием, склонность к образованию флокенов.
Легированные высокопрочные стали
В лучших низко- и среднеуглеродистых сталях после типичной для них термической обработки прочность, оцениваемая временным сопротивлением, ограничивается значениями ниже 1500 МПа. При ств > 1500 МПа эти стали имеют высокую чувствительность к концентраторам напряжений и эксплуатационно ненадежны.
Развитие техники, стремление к созданию машин наименьшей массы требуют применения высокопрочных сталей, имеющих ав > 1500 МПа. Для предупреждения хрупкого разрушения таким сталям необходим определенный запас вязкости (KCUne менее 0,2 МДж/м2). Кроме того, расчет рабочих напряжений в деталях из этих сталей необходимо вести не только по значению сто,2) но и по предельно допустимому размеру дефекта с использованием критерия К\с. При использовании высокопрочных сталей важно также соблюдение определенных требований к конструированию деталей и технологии обработки их поверхности. При проектировании необходимо избегать конструктивных концентраторов напряжений, а при изготовлении не допускать на поверхности глубоких рисок, царапин, обеспечивать минимальную ее шероховатость.
Высокопрочное состояние в сочетании с достаточно высоким сопротивлением хрупкому разрушению может быть получено при использовании: 1) среднеуглеродистых комплексно-легированных сталей после низкого отпуска или термомеханической обработки; 2) мартенситно-стареющих сталей; 3) метастабильных аустенитных сталей.
Срсднсуглеродистпые комплексно-легированные низко отпущенные стали. После закалки и низкого отпуска уровень прочности стали определяется содержанием углерода и практически не зависит от присутствия Легирующих элементов. Увеличение содержания углерода до 0,4% повы-Шыч временное сопротивление до 2400 МПа, но углеродистая сталь имеет Полностью хрупкое разрушение. Необходимый запас вязкости при такой ИЛИ несколько меньшей прочности достигается совокупностью мероприятий, главные из которых направлены на подбор рационального состава СТ*-'1И, получение мелкого зерна, обязательного для высокопрочного состояния, повышение металлургического качества металла.
Повышение вязкости достигается прежде всего легированием никелем (1,Г) 3 %). Чем больше его количество, тем ниже порог хладноломкости ■ больше допустимый уровень прочности. Вместе с ним вводят небольшое количество кремния, молибдена, вольфрама, ванадия. Эти элементы, МПрудняя разупрочнение маргенсита при отпуске, позволяют несколько ■опыеить температуру отпуска и тем самым полнее снять закалочные на-■ряжения. Карбидообразующие элементы необходимы также для полу-ЧИния мелкого зерна. Хром и марганец вводят для обеспечения нужной (рокалииаемости.
К распространенным высокопрочным сталям относятся ЗОХГСНА, 40ХГСНЗВА, ШХН2СМЛ, 30Х2ГСН2ВМ, 30Х5МСФА. Характерные ме-яа-нические свойства двух сталей, определенные на образцах с трещиной (»илчгния приведены в скобках) и без нее, приведены ниже:
ЗОХГСНА 40ХГСНЗВА
1850(1670)2000(1200)
1650(1570) 1850(1560)
/\ '/................................................................... 13/15 11/12
i . '/................................................................... 50/53 43/45
КСГ, МЛж/м2................................................. 0,55/0,62 0,45/0,5
К,, , МПлм"'............................................... 60/65 45/60
Прим <■ ч а м и г. Н мисли irjif снойстна после )акалки с <)()0"С и ни uni о 1,111 \- < ка при 2 Г> П " (', п шимпш i еле после ичо термической чакалии
13
В самолетостроении широко применяют сталь ЗОХГСНЛ, которая представляет собой хромансиль, улучшенную введением 1,6% Ni. Ее используют для силовых сварных конструкций, деталей фюзеляжа, шасси и т.п. При аъ до 1650 МПа сталь подвергают изотермической закалке, поскольку по сравнению с низкоотпущенным состоянием она обеспечивает меньшую чувствительность к надрезам и более высокое сопротивление разрушению.
Среднеуглеродистые стали, упрочненные термомеханической обработкой. Термомеханическая обработка (ТМО) совмещает два способа упрочнения — пластическую деформацию аустенита и закалку — в единый технологический процесс. Такое комбинированное воздействие применительно к среднеуглеродистым легированным сталям (ЗОХГСА, 40ХН, 40ХН2МА, 38ХНЗМА и др.) обеспечивает высокую прочность (на образцах небольшого размера <тв = 2000 ... 2800 МПа) при достаточном запасе пластичности и вязкости.
В зависимости от условий деформации аустенита — выше или ниже температуры рекристаллизации — различают соответственно высокотемпературную (ВТМО) и низкотемпературную (НТМО) термомеханическую обработку.
|
Рис. 9.10. Схема термомеханической обработки стали: а - ВТМО; б- НТМО (заштрихованная зона - интервал температур рекристаллизации) |
При ВТМО (рис. 9.10, а) сталь деформируют при температуре выше температуры Аз и сразу закаливают с тем, чтобы не допустить развития рекристаллизации аустенита. При НТМО (рис. 9.10, б) деформация проводится в области повышенной устойчивости аустенита (400-600 °С). Рекристаллизация при этих температурах не происходит, однако необходимо избегать образования бейнитных структур.
ТМО обоих видов заканчивается низким отпуском при 100 - 200"С. При ТМО повышается весь комплекс механических свойств и особенно пластичность и вязкость, что наиболее важно для высокопрочного состояния. По сравнению с обычной обработкой прирост прочности при ТМО составляет 200 - 500 МПа, т.е. 10 - 20 %. Характеристики пластичности и вязкости повышаются в 1,5 - 2 раза.
Улучшение комплекса механических свойств обусловлено формированием специфического структурного состояния. Деформация создает в ау-стените высокую плотность дислокаций, образующих из-за процесса поли-гонизации устойчивую ячеистую субструктуру, которая наследуется мартенситом при закалке. При этом субграницы тормозят движение дислокаций и локализируют деформацию внутри зерна; в результате прочность повышается. В то же время субграницы ведут себя как полупроницаемые барьеры. Они допускают прорыв дислокаций, их передачу из мест скоплений в соседние субзерна. Это вызывает пластическую релаксацию локальных напряжении и служит причиной повышенных пластичности и вязкости.
Наибольшее упрочнение (сгв < 2800 МПа) достигается при НТМО. Однако ее проведение технологически более сложно, чем ВТМО. Она требует мощных деформирующих средств, так как для получения высокой прочности необходимы большие степени обжатия (50 - 90 %), а аустенит в области температур 400 - 600 °С не столь пластичен. Ее можно применять для изделий небольшого сечения и простой формы (лист, лента, прутки). Кроме того, НТМО пригодна для легированных сталей с большой устойчивостью переохлажденного аустенита.
ВТМО обеспечивает меньшее упрочнение1 (<тв < 2400 МПа), но более высокие пластичность и вязкость. Она уменьшает также чувствительность к трещине {К\с возрастает на 20 - 50%), снижает порог хладноломкости, повышает сопротивление усталости и затрудняет разупрочнение при отпуске, что связано с устойчивостью ячеистых дислокационных структур мартенсита. Особенно эффективна ВТМО для чистого вакуу-мированного металла. Кроме того, ВТМО более технологична, так как аустенит выше точки Аз пластичен и стабилен. При деформации не требуются большие степени обжатия; предельное упрочнение достигается при деформации на 20 - 40 %. Для ВТМО пригодны любые конструкционные сiал и.
')к> обусловлено тем, чт при высокой м-ммературе трудно избежать частичной рек рис I ал л и за и и и ну с I см и та.
Область ВТМО расширяет явление обратимости эффекта упрочнения. Оно состоит в том, что свойства, полученные при ВТМО, наследуются после повторной закалки. Это позволяет закладывать определенный ресурс свойств в стальные полуфабрикаты в тонких сечениях (ленты, листы, трубы), подвергая их ВТМО на металлургическом заводе.
Улучшить свойства среднеуглеродистых легированных сталей можно холодной пластической деформацией низкоотпущенного мартенсита. Небольшая деформация (5 - 20 %) увеличивает временное сопротивление и особенно предел текучести сталей.
Наиболее высокая прочность (<тв ~ 3000 МПа) получена сочетанием ВТМО с последующей холодной пластической деформацией низкоотпу-щенных среднеуглеродистых сталей.
Мартенситно-стареющие стали. Это особый класс высокопрочных материалов, превосходящих по конструкционной прочности и технологичности рассмотренные выше среднеуглеродистые стали.
Их основа — безуглеродистые (< 0,03 % С) сплавы железа с 8 - 25 % Ni, легированные Со, Mo, Ti, А1, Сг и другими элементами (табл. 9.10).
Таблица 9.10. Химический состав и механические свойства мартенситно-стареющих сталей
Марка стали | Содержание элементов, % | <тв | СО,2 | к1с | 8 | ф | KCU | КСТ |
МПа | МПа-м1/2 | % | МДж/м2 | |||||
03Н18К9М5Т 03Н12К15М10 03Х11Н10М2Т | 18 Ni; 9Со; 5Мо; 0,9 Ti 12 Ni; 15 Со; 10 Мо 11 Сг; 10 Ni; 2 Мо; 0,9 Ti; 0,2 А1 | 2100 2500 1600 | 1900 2400 1550 | 75-85 90- 105 | 8 6 8 | 50 30 50 | 0,5 0,3 0,5 | 0,20 0,2 |
Высокая прочность этих сталей достигается совмещением двух механизмов упрочнения: мартенситного -у —> а-превращения и старения мартенсита. Небольшой вклад вносит также легирование твердого раствора.
Никель стабилизирует 7-твердый раствор, сильно снижая темпера-ТУРУ 7 ~* а-превращения (см. рис. 4.19), которое даже при невысоких скоростях охлаждения протекает по мартенситному механизму.
Мартенситно-стареющие стали закаливают от 800 ■- 860"С на нозду хе. При нагреве легирующие элементы Ti, Be, Al, Си, Мо, обладающие ограниченной и переменной растворимос'1 ыо в IV,», переходя г в 7 расiвор
и при охлаждении не выделяются. Закалка фиксирует пересыщенный же лезоникелевый мартенсит. Благсжаря высокому содержанию никеля, ко балы а и малой концентрации углерода дислокации в нем обладают высокой подвижностью. Поэтому железоникелевый мартенсит при прочно сти ств = 900 ... 1000 МПа имеет высокую пластичность (й = 18... 20%, гр = 75 .. .85 %), вязкость (KCU = 2 .. .3 МДж/м2) и малую способность к упрочнению при холодной деформации. Последнее позволяет деформиро вать закаленные стали с большими степенями обжатия.
Основное упрочнение достигается при старении (480 - 520°С), ко 1 да из мартенсита выделяются мелкодисперсные частицы вторичных фаз (МзТл, NiAl, Fe2Mo, N13M0 и др.), когерентно связанные с матрицей. Наибольшее упрочнение при старении вызывают Ti и А1, меньшее -- Си и Мо. Для мартенситно-стареющих сталей характерен высокий предел текуче сти (см. табл. 9.10) и более высокий, чем у лучших пружинных сплавов, предел упругости (сто,002 = 1300 МПа), низкий порог хладноломкости.
При прочности аъ = 2000 МПа и более стали разрушаются вязко, хотя сопротивление распространению трещины у них невелико (КСТ « % 0,2 МДж/м2). Малая чувствительность к надрезам, высокое сопроти вление хрупкому разрушению обеспечивают высокую конструкционную прочность изделий в широком диапазоне температур от криогенных до 150 - 500 °С. При содержании Сг около 12 % стали являются коррозионно-
с тйкими.
Другое важное достоинство этого класса сталей — высокая техноло
Iичцость.
Они обладают неограниченной прокаливаемостью, хорошо сварива и) н:я, до старения легко деформируются и обрабатываются резанием. При iep.u и ческой обработке практически не происходит коробления и исключе
но обезуглероживание.
Стали со стареющим мартенситом, несмотря на высокую стоимость, применяют для наиболее ответственных деталей в авиации, ракетной тех пике, судостроении и как пружинный материал в приборостроении.
Мстпасгпабильные аустенитные стали (трипстали) — особый класс
высокопрочных материалов повышенной пластичности. Они относятся к
высоколегированным сталям. Их состав ориентировочно, согласно мар
кировкс, можно выразить в виде 25Н25М4Г, 30Х9Н8М4Г2С2. Его иодби
1>;мо1 таким образом, чтобы после закалки от температуры 1000- 1100°С
• 1Л.Ш имели усюйчивую аусгенитную структуру (Мн лежит ниже 0°).
\\ (лениiпая структура обладаем высокой вязкостью, но низким преде
юм м'кучесли. Для упрочнении cia.in подвергают специальной тепловой
olipadn 1 кс пластической деформации с большими пенсиями обжатия
|
|
А"1с, мш м*2 (50-80%) при температуре 400 -
600 1400 2200 (Тод,МПа Рис. 9.11. Вязкость разрушения высокопрочных сталей: 1 - метастабильных аустенит-ных; 2 - мартенситнб-старею-щих; 3 - хромоникелевых |
600°С, лежащей ниже температуры рекристаллизации. При этом деформационное упрочнение (наклеп) совмещается с карбидным упрочнением, развивающимся в результате деформационного старения. Насыщенная дислокационная структура, создаваемая пластической деформацией, дополнительно стабилизируется выделяющимися дисперсными частицами карбидов. В результате деформационно-термического упрочнения предел текучести повышается до 1800 МПа. При этом сталям свойственны высокая пластичность (> 20 %) и трещиностойкость. Значения 8 к К\с у этих сталей больше, чем у других высокопрочных сталей (рис. 9.11). Высокая пластичность и вязкость разрушения обусловлены развитием мартенситного превращения в процессе деформирования. Дело в том, что при тепловой обработке аустенит обедняется углеродом и легирующими элементами и становится менее устойчивым (метастабильным). Благодаря этому повторная пластическая деформация вызывает превращение метастабильного аустенита в мартенсит деформации. Механизм повышения пластичности и вязкости разрушения связан с «залечиванием» — локальным упрочнением аустенита в участках пластического течения (в том числе и у вершин движущейся трещины). Образующийся в таких участках мартенсит деформации упрочняет их настолько, что они перестают быть слабыми участками, и деформация распространяется на соседние участки.
Применение метастабильных аустенитных сталей ограничивается сложностью деформационно-термического упрочнения. Для высоких степеней деформации при низких температурах требуются мощные деформирующие средства. Области применения сталей: детали авиаконструкций, броневой лист, проволока тросов и др.
На рис. 9.12 показаны области значений прочности и пластичности высокопрочных сталей различных классов. Видно, что наибольшей прочностью обладают среднеуглеродистые стали после термомеханической
Рис. 9.12. Соотношение между пределом текучести и пластичностью высокопрочных сталей:
1 - среднеуглеродистых, упрочненных ТМО; 2 - мартенситно-стареющих; 3- среднеуглеродистых легированных без ТМО; 4 -
метастабильных аустенитных ,,0|_______ I_____ I_____ I_____ i щ
О 20 40 60 8, %
обработки, а наибольшей пластичностью при одинаковой прочности метастабильные аустенитные стали.
Легированные стали с повышенной циклической прочностью
Циклическая прочность стали определяет работоспособность большой группы ответственных деталей машин — валов, осей, шатунов, штоков, валов-шестерен и др. Основой выбора стали для таких деталей служит предел выносливости &-\. Наряду с а-\ используют и такие параметры статической прочности, как <тв, <то,2- Это допустимо, так как для большой группы сталей установлена тесная корреляционная связь между циклической и статической прочностью, характеризуемая коэффициентом выносливости кв = <Т_1/сгв.
Кроме значений c_i, ав, сто,2 ПРИ выборе марки стали учитывают ударную вязкость, сопротивление износу, прокаливаемость. Высокая циклическая прочность стали достигается в том случае, если она оказывает высокое сопротивление зарождению трещин усталости и их развитию. Механизм зарождения усталостной трещины связан с развитием и накоплением в поверхностном слое микропластической деформации. Он основан на движении дислокаций, возможность перемещения которых при напряжениях ниже предела текучести обусловлена анизотропией кристаллов и их случайной ориентацией. В отдельных кристаллах при небольших средних напряжениях могут возникать напряжения, достаточные для перемещения слабозакрепленных дислокаций. Кроме того, для тонких поверхностных слоев (в 1 - 2 зерна) характерно низкое напряжение работы источников дислокаций Франка — Рида. По этим причинам в мягких (отожженных) металлах уже на ранней стадии нагружения (1-5% от общего числа циклов до разрушения) наблюдаются ранняя микропластическая деформация и повреждение тонких поверхностных слоев. Микро-ила.стическая деформация проявляется в образовании на поверхности линий сдвига (скольжения), плотность которых растет с увеличением числа
Рис. 9.14. Профиль поверхности алюминия после циклического нагружения |
1_ 1
Рис. 9.13. Схема расположения линий скольжения в экструзиях (/) и интрузиях (2)
циклов. По мере выхода дислокаций на поверхность усиливается ее повреждение в виде возникающих ступенек. Линии скольжения расширяются в полосы и постепенно перерождаются в экструзии и интрузии (рис. 9.13). Экструзия — это выдавливание, а интрузия — углубление полос скольжения. Экструзии и интрузии формируют пикообразный рельеф поверхности, состоящий из выступов и острых впадин (рис. 9.14). Впадины — места концентрации деформации и, как следствие, вакансий, дислокаций. Из-за их высокой плотности здесь возникают микропоры, рыхлоты, которые сливаясь, образуют субмикротрещины. Развитие и объединение субмикротрещин ведет, в свою очередь, к образованию микротрещин.
При напряжениях, меньших предела выносливости, микротрещины остаются в наружном слое толщиной не более размера зерна, поскольку границы зерен — барьеры для их распространения. При напряжениях выше предела выносливости микротрещины преодолевают границы зерен, сливаются, образуя магистральную трещину усталости. Трещина усталости растет прерывисто — скачками, связанными с местной пластической деформацией (наклепом) металла у ее вершины. Для распространения трещины на некоторую длину необходимо, чтобы у ее вершины была исчерпана пластичность. По этой причине у пластичных металлов сопротивление распространению трещины усталости много выше, чем ее зарождению. Увеличению сопротивления зарождению трещины усталости способствует структурное состояние, препятствующее движению дислокаций и их выходу на поверхность. Наиболее эффективно его создают поверхностным упрочнением.
Циклическая прочность зависит от большого числа факторов, из которых решающее значение имеют структура и напряженное состояние поверхностного слоя, качество поверхности и воздействие коррозионной среды. Наличие на поверхности остаточных напряжений сжатия затрудняет образование и развитие трещин усталости и, как следствие, способствует увеличению предела выносливости. Резко отрицательное влияние оказывают напряжения растяжения и многочисленные концентраторы напряжений:
конструктивные — изменение формы сечения детали: галтели, отверстия, канавки, проточки и т.п.;
технологические — микронеровности поверхности, риски и другие следы механической обработки;
металлургические — внутренние дефекты в виде пор, раковин, неметаллических включений (оксидов, сульфидов, силикатов и др.).
Влияние концентраторов напряжений оценивают эффективным коэффициентом концентрации напряжений Ка = cr_i/<7_iK, под которым понимают отношение предела выносливости гладкого образца o_i к пределу выносливости такого же образца с концентратором напряжений а~\.
Предел выносливости снижается с увеличением размеров деталей (масштабный фактор) и особенно интенсивно под влиянием коррозионной среды, вызывающей повреждение поверхности в виде углублений, сетки трещин и других концентраторов напряжений.
Совместное влияние различных факторов на предел выносливости в расчетах оценивается коэффициентом {Ка)а — c_i/(cr_i)fl, показывающим, во сколько раз предел выносливости гладкого образца диаметром К) мм больше предела выносливости детали:
{Кв)а = (Ка/еа + 1/0 - 1)1//Зу„р, (9.1)
i де еа — масштабный фактор, характеризующий уменьшение несущей способности детали при увеличении ее поперечного размера; /3 — коэффициент, учитывающий влияние шероховатости поверхности (в коррозион пых средах заменяется на/Зкорр); /Зупр — коэффициент, характеризующий >ффективность поверхностного упрочнения.
Из соотношения (9.^следует, что влияние факторов на несущую способность детали тем слабее, чем ближе к единице значение коэффициентов K„JEa и /3 и больше коэффициент поверхностного упрочнения /3ynp.
В соответствии с закономерностями усталостного разрушения изменение предела выносливости стали с ростом ее статической прочности
Аналогичное соотношение спр»пгллими и для касательных напряжений.
|
Рис. 9.15. Зависимость предела выносливости при изгибе от временного сопротивления средне-углеродистых сталей с различной структурой
200 600 1000 1400 ств,МПа
подчиняется сложной зависимости (рис. 9.15), учитывающей влияние не только прочности, но и пластичности стали. Снижение пластичности стали обусловливает замедление роста предела выносливости (см. рис. 9.15) при повышении прочности выше 1200 МПа.
Для деталей, работающих при циклических нагрузках, преимущественно применяют стали нормальной и повышенной статической прочности. Из них предпочтение отдают улучшаемым сталям: углеродистым Ст5, 35, 40, 45, 50, 55 и низколегированным 40Х, 50Х, 40ХН, 50ХН, 40ХН2МА, 35ХГСА, 38ХНЗМА, обрабатываемым на структуру сорбита. В отдельных случаях углеродистые стали из-за низкой прокаливаемости применяют в нормализованном состоянии с ферритно-перлитной структурой.
Для улучшаемых сталей, имеющих невысокую твердость (< 350 НВ), характерны раннее пластическое течение и повреждение тонких (5 -10 мкм) поверхностных слоев. Субмикроскопические трещины усталости у них возникают на ранней стадии, составляющей 3 - 10 % от общего времени до разрушения. Остальное время приходится на их развитие.
Характерная особенность улучшаемых сталей — высокая надежность, обусловленная низкой скоростью роста трещины усталости (СРТУ). Причиной низкой СРТУ, кроме высокой пластичности сталей, является также развитая субструктура ферритной фазы сорбита, которая формируется при высоком отпуске в результате процесса полигонизации.
Дислокации образуют в феррите малоподвижные субграницы, которые дополнительно блокируются карбидными частицами. При наличии таких внутренних барьеров трещина вынуждена ветвиться, развиваться зигзагообразно, что увеличивает энергию ее образования и время развития. В результате улучшаемые стали имеют достаточно низкую скорость роста усталостной [ретины.
Кроме высокой надежности важное достоинство улучшаемых сталей — малая чувствительность к качеству поверхности и случайным ударным нагрузкам. В связи с этим выносливость улучшаемых сталей относительно слабо снижается при наличии на поверхности деталей острых концентраторов напряжений (резьбы, шпоночных канавок, мелких отверстий, галтелей малого радиуса и т.п.).
Недостаток улучшаемых сталей — невысокий предел выносливости, значение которого растет по мере увеличения статической прочности стали (см. рис. 9.15). При этом до значений <тв < 1200 МПа зависимость между <тв и сг_1 сохраняется линейной, а коэффициент выносливости А;в = <7_i/crB имеет максимальное значение, равное 0,5.
Рассчитывать детали из улучшаемых сталей по <r_i не всегда целесообразно из-за низких допустимых рабочих напряжений, что определяет слишком большие размеры деталей. Нередко расчет ведут по ограниченному пределу выносливости (сграб > <т-\). Это допустимо, так как высокая надежность улучшаемых сталей позволяет своевременно выявить трещину и заменить деталь без аварийных последствий. Наиболее низкий предел выносливости имеют среднеуглеродистые стали (Ст5, 35, 40, 45, 50, 55, 40Х и др.), применяемые в нормализованном состоянии с ферритно-перлитной структурой (см. рис. 9.15). В таком состоянии эти стали используют при ограничении стоимости деталей или при больших вибрационных нагрузках, когда от материала требуется высокая демпфирующая способность.
Стали повышенной прочности (ств = 1300 ... 1500 МПа) и твердости (К) - 50 HRC) со структурой троостита (см. рис. 9.15) относятся к ма-1сриалам функционального назначения — рессорно-пружинным сталям. Циклические нагрузки в них вызывают слабое деформационное упрочнение поверхности и развитие ее усталостной повреждаемости. Усталостное разрушение в этих сталях, как правило, инициируют поверхностные концентраторы напряжений: риски, царапины, обезуглероженные участки и l.ii. Повышенная чувствительность к надрезам служит причиной более сметного разброса значений cr_i (см. рис. 9.15), замедления их роста с увеличением статической прочности и, как следствие, снижения коэффициента выносливости до 0,4. Для того чтобы обеспечить более высокую циклическую прочность этих сталей, необходимо уменьшить их чувстви-М'.п.ность к концентраторам напряжений.
Твердые (> 50 HRC) высокопрочные стали с мартенситной структурой обладают особо высокой чувствительностью к концентраторам напряжений, что нейтрализует их основное свойство высокое сопротивление образованию трещин ус ia:n>c i и. По этой причине увеличение их
статической прочности не сопровождается повышением выносливости (см. рис. 9.15). Более того, при ав > 2000 МПа начинается снижение сг_ь а коэффициент выносливости уменьшается до 0,3* Таким образом, потенциальные свойства высокопрочных сталей при циклических нагрузках не реализуются. Особенно сильно это проявляется не в образцах, а в реальных деталях вследствие резкого увеличения эффективного коэффициента концентрации напряжений (Ка)д (см. формулу 9.1). Его увеличение связано с интенсивным ростом коэффициента Ка по мере повышения статической прочности стали и снижением коэффициентов еа и /3, характеризующих соответственно влияние масштабного фактора и шероховатости поверхности. Вследствие высоких значений (Kff)a несущая способность деталей из легированных высокопрочных сталей может быть ниже, чем из простых углеродистых сталей.
Вместо объемно-упрочненных высокопрочных сталей применяют средне- и низкоуглеродистые стали, подвергнутые поверхностному упрочнению. Его проводят следующими технологическими методами: 1) закалкой с индукционным нагревом; 2) химико-термической обработкой — цементацией (нитроцементацией), азотированием; 3) поверхностным пластическим деформированием (ППД): обкаткой роликами, обдувкой дробью и др.; 4) комбинированными методами, включающими химико-термическую обработку и ППД.
Благоприятное влияние технологических методов обусловлено действием двух факторов — повышением сопротивления пластической деформации поверхностного слоя и созданием в нем остаточных напряжений сжатия.
Влияние этих факторов особенно значительно для деталей машин, работающих на изгиб, кручение, т.е. когда напряжения максимальны на поверхности (валы, оси, зубчатые колеса и др.). Упрочненный поверхностный слой в виде жесткой оболочки затрудняет выход дислокаций на поверхность и тем самым препятствует развитию на ней повреждений и образованию трещин усталости. Этому же способствуют и остаточные напряжения сжатия. Суммируясь с напряжениями от внешней нагрузки, они уменьшают на поверхности неблагоприятные напряжения растяжения.
Степень влияния остаточных напряжений сжатия растет с увеличением предела текучести поверхностного слоя — того предельного значения, которое они могут достигать в нем. При этом растет не только возможный уровень остаточных напряжений, но и их стабильность в процессе
Высокие значения ka ss 0,5 при мартенситной структуре могут сохраняться лишь для среднеуглеродистых сталей, упрочненных термомеханической обработкой (штри ховая линия на рис. 9.15).
циклического нагружения. При мартенситной высокопрочной структуре остаточные напряжения в поверхностном слое возрастают настолько, что напряжения растяжения от внешней нагрузки уменьшаются и очаг разрушения смещается в подповерхностный слой, нейтрализуя тем самым поверхностные концентраторы напряжений. Таким образом, формирование высоких остаточных напряжений сжатия — важная составная часть технологии изготовления деталей машин с повышенным сопротивлением усталости.
Эффективность технологических методов количественно оценивается коэффициентом упрочнения /Зупр, показывающим, во сколько раз снижается эффективный коэффициент концентрации напряжений (Ка)ц и увеличивается предел выносливости конкретной детали. Влияние способа поверхностного упрочнения на /?уПр показано в табл. 9.11.
Видно, что эффективность технологических методов тем значительнее, чем острее концентратор напряжений (выше Ка).
Таблица 9.11. Повышение предела выносливости валов приповерхностном упрочнении
Вид | <тв, МПа (сердцевины) | Коэффициент упрочнения валов /Зупр | ||
поверхностной обработки | гладких (Ка = 1) | с малой концентрацией напряжений (Я„<1,5) | с большой концентрацией напряжений (К, = 1,8...2) | |
Индукционная закалка с нагревом ТВЧ | 600 - 800 800-1000 | 1,5-1,7 1,3-1,5 | 1,6-1,8 | 2,4-2,8 |
Азотирование | 900-1200 | 1,1-1,3 | 1,5-1,7 | 1,7-2,1 |
Цементация | 400 - 600 700 - 800 1000 - 1200 | 1,8-2 1,4-1,5 1,2-1,3 | 3 2 | - |
Дробеструйный наклеп | 600-1500 | 1,1-1,3 | 1,5-1,6 | 1,7-2,1 |
Накатка роликом | 1,1 1,3 | 1,3-1,5 | 1,6- 2 |
|
Выбор метода поверхностного упрочнения детали зависит от условий ее эксплуатации, формы, размеров, марки выбранной стали и других факторов.
Закалку с индукционным нагревом ТВЧ широко используют в массовом производстве для повышения долговечности осей, пальцев, валов и других деталей цилиндрической формы. На структуру мелкопластинчатого мартенсита и высокую твердость (50 - 60 HRC) обрабатывают слои толщиной 1-3 мм. Вследствие фазовых превращений, вызывающих увеличение удельного объема поверхностного слоя, в нем формируются остаточные напряжения сжатия, которые на поверхности составляют 300 - 600 МПа. Предел выносливости гладких валов увеличивается в 1,3 - 1,7 раза (см. табл. 9.11).
Обладая высокой производительностью, метод поверхностной закалки в то же время мало эффективен для деталей сложной формы, для которых возможно только местное упрочнение. В местах обрыва закаленного слоя, не охватывающего галтели, выточки и другие концентраторы, возникают высокие остаточные напряжения растяжения, снижающие выносливость. Этого недостатка не наблюдается при химико-термической обработке, обеспечивающей равномерное упрочнение, более высокую выносливость и одновременно износостойкость поверхности. Поверхностные слои приобретают высокую твердость: 700 - 900 HV (59 - 63 HRC) после цементации (нитроцементации) и 800 - 1000 HV после азотирования, а также высокие остаточные напряжения сжатия, смещающие очаг усталостного разрушения под поверхность. Предел выносливости гладких валов увеличивается в 1,1 - 2 раза, а при наличии концентраторов напряжений в 3 раза и более (см. табл. 9.11).
Наиболее напряженные детали (зубчатые колеса, вал-шестерни и др.) подвергают цементации, применяя для их изготовления низкоуглеродистые стали (см. табл. 9.7). После насыщения углеродом, закалки и низкого отпуска эти стали при высокой поверхностной твердости сохраняют вязкую сердцевину, способную воспринимать ударные нагрузки. Достоинство цементации — возможность получить упрочненные слои большой толщины (0,8-2 мм и более), выдерживающие высокие удельные нагрузки. Однако максимальной циклической прочности отвечают слои меньшей толщины (0,4 - 0,8 мм), когда остаточные напряжения сжатия высоки у поверхности, а очаг разрушения находится неглубоко от нее. С увеличением толщины слоя остаточные напряжения и предел выносливости снижаются, очаг разрушения смещается в глубь слоя — на границу с сердцевиной. По этой причине циклическая прочность цементированных деталей зависит не только от свойств поверхностного слоя, по и от свойств
сердцевины, увеличиваясь по мере повышения ее прочности и твердости, достигая максимального значения при <тв = 1200 ... 1400 МПа и 43 45 HRC. Такие свойства характерны для хромоникелевых и хромоникель-молибденовых сталей 12ХНЗА, 12Х2Н4А, 20Х2Н4А, 18Х2Н4МА, а также сталей с повышенным содержанием углерода 25ХГМ, ЗОХГТ и т.д. (см.
табл. 9.7).
Азотированию подвергают легированные стали 38Х2МЮА, 40Х, 40ХН2МА, 18Х2Н4МА и другие, для упрочнения сердцевины которых проводят термическое улучшение. Их выносливость определяется режимом азотирования и возрастает по мере увеличения толщины упрочненного слоя. Вследствие небольшой толщины слоя (0,3 - 0,6 мм), ограничивающей допустимые нагрузки, а также большой длительности процесса азотирование применяют реже, чем цементацию. Ему отдают предпочтение в тех случаях, когда нежелательна деформация деталей при упрочнении или требуется повышение коррозионной стойкости и высокая износостойкость поверхности.
В отличие от азотирования цементация вызывает сильную деформацию деталей, для устранения которой шлифованием приходится удалять слои толщиной 0,10 - 0,25 мм, т.е. слои с остаточными напряжениями сжатия. В результате остаточные напряжения сжатия снижаются; во многих случаях формируются напряжения растяжения. В связи с этим цементованные детали после шлифования упрочняют обкаткой роликами или обдувкой дробью. Обкатку роликами применяют для поверхностного наклепа деталей цилиндрической формы, обдувку дробью (диаметром 0,6 - 3,0 мм), отличающуюся большой универсальностью и производительностью, — для деталей любой конфигурации.
Комбинированное упрочнение характеризуется высокой эффективностью, поскольку ППД дополнительно увеличивает твердость поверхностных слоев (на 10 - 20 %) и формирует в них высокие остаточные напряжения сжатия. В итоге предел выносливости цементованных деталей увеличивается в 1,5 - 2 раза. ППД эффективно также для деталей, закаленных с нагревом ТВЧ, особенно при обрыве упрочненного слоя у концентратора.
Рис. 9.16. Зависимость предела выносливости углеродистых сталей от временного сопротивления при испытании в различных средах:/ на ночдухе; 2 в пресной воде; .V в морской поде
В коррозионных средах сопротивление усталости рассмотренных выше некоррозионно-стойких сталей резко снижается и не зависит от их статической прочности (рис. 9.16). Такие стали применяют с поверхностным покрытием из цинка, кадмия, хрома или никеля. Широко используют также специальные коррозионно-стойкие стали, которые рассмотрены в гл. 15.
Дата добавления: 2018-04-05; просмотров: 1522; Мы поможем в написании вашей работы! |
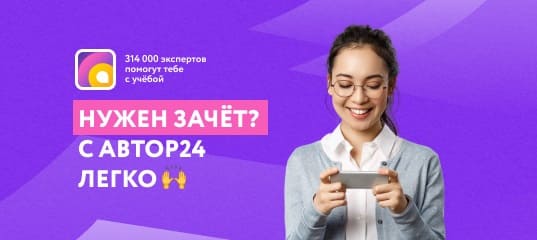
Мы поможем в написании ваших работ!