Стали с высокой технологической пластичностью и свариваемостью
Технологическая пластичность — способность подвергаться горячей и холодной пластической деформации.
В горячем (аустенитном) состоянии большинство сталей обладают высокой пластичностью, что позволяет получать фасонный прокат и поковки без дефектов (трещин, разрывов и т.п.). Более того, горячей обработкой давлением (в сочетании с последующим отжигом) измельчают микроструктуру, устраняют литейные дефекты и, формируя волокна вдоль контура поковок, создают благоприятно ориентированную макроструктуру. В результате этого горячедеформированный металл в отличие от литого имеет примерно в 1,5 раза более высокую конструкционную прочность.
Высокий запас технологической пластичности необходим листовым сталям, предназначенным для холодной штамповки. Холодная штамповка находит широкое применение в автомобилестроении. Более 50 % массы автомобиля составляют детали, изготовленные холодной штамповкой из листа.
Листовая сталь для холодной штамповки должна обладать способностью к глубокой вытяжке и иметь хорошее качество поверхности для последующего нанесения покрытия. Различают четыре категории вытяжки: В Г — весьма глубокая; СВ — сложная; ОСВ — особо сложная; ВОСВ — весьма особо сложная. Способность к вытяжке зависит от многих факторов: химического состава и концентрации углерода, структуры и механических свойств стали. Чем меньше концентрация углерода, тем легче идет технологический процесс вытяжки. Для глубокой вытяжки содержание углерода в стали ограничивают 0,1 %; при 0,2 - 0,3 % С возможны только гибка и незначительная вытяжка, а при 0,35 - 0,45 % С — изгиб большого радиуса.
|
|
Микроструктура стали должна состоять из феррита с небольшим количеством перлита. Выделение по границам зерен структурно свободного (третичного) цементита строго ограничено во избежание разрывов при штамповке. Лучше всего деформируется сталь с мелким зерном, соответствующим 7-8 номеру зернистости по ГОСТ 5639 82. При большем
размере зерна получается шероховатая поверхность в виде так называемой апельсиновой корки, при меньшем — сталь становится слишком жесткой и упругой. Также нежелательна разнозернистая структура, поскольку она способствует неравномерности деформации и образованию трещин.
Контролируемыми параметрами механических свойств стали являются относительное удлинение <5 и отношение аТ/ов. Чем больше 6, ниже <7Т и, следовательно, меньше отношение ат/ав (рекомендуется 0,55.. .0,66), тем выше способность низкоуглеродистых сталей к вытяжке.
Для глубокой, сложной и особо сложной вытяжки используют ма лопрочные <7„ — 280 .. .330 МПа, высокопластичные 6 — 33...45% низ коуглеродистыс стали. Их поставляют в виде тонкого холоднокатаного листа, подвергнутого рекристаллизационному отжигу при 650 — 690°С.
|
|
Широко применяют кипящую сталь 08кп. Способность этой стали хорошо штамповаться обусловлена низким содержанием углерода и почти полным отсутствием кремния, который сильно упрочняет феррит и затрудняет сто деформирование. Из стали 08кп штампуют детали кузова автомобиля, корпуса приборов и другие детали сложного профиля.
Кипящая сталь 08кн обеспечивает только первую категорию вытяж
ки (ВГ). ГОе недостаток склонность к деформационному старению.
('ледствием деформационного старения является образование на поверх
мости изделия после вытяжки полос скольжения — своеобразных складок,
исключающих качественную отделку поверхности. Поэтому отсутствие
склонности листовой стали к деформационному старению является важ
ным показателем ее качества.
Методом контроля склонности стали к деформационному старению служит запись диаграммы кривой растяжения. Кривая растяжения должна быть плавной, со слабым деформационным упрочнением и не иметь площадки или зуба текучести (рис. 10.1). Наличие последних указывает ма ю, что в стали прошло деформационное старение, причиной которого и илистей закрепление дислокаций твердого раствора атомами внедрения азотом и углеродом. В результате происходит упрочнение металла, развивается неоднородная пластическая деформация, приводящая к образца ни ю дефектов на ото поверхности.
|
|
|
1'ис. 10.1. Диаграммы растяжения холоднокатаной отожженной iниш, склонной к деформационному старению (а) и нестареющей ((f)
Для исключения брака в виде полос скольжения применяют нестареющие стали:
кипящую 08Фкп, микролегированную ванадием (0,02 - 0,04 %);
спокойную 08Ю и 10ЮА с присадкой алюминия (0,02 - 0,05 %);
спокойную (08ГСЮФ) с присадками алюминия и ванадия (ванадий и алюминий в этих случаях связывают углерод и остаточный азот в карбиды и нитриды, выводят примеси внедрения из твердого раствора и предупреждают развитие старения).
Основное применение имеет сталь 08Ю, которая допускает все четыре категории вытяжки.
Для штампованных деталей и изделий, которые должны иметь повышенную прочность (например, диски колес), применяют двухфазные стали 12ХМ, 18ХГ2ФТЮДР с ферритно-мартенситной структурой, состоящей из мягкого феррита и прочного мартенсита (20 - 30 %). Получают такую структуру закалкой из межкритического интервала (А\ - А3) после горячей прокатки. В феррите много свободных дислокаций (из-за фазового наклепа при образовании мартенсита), что обеспечивает относительно невысокий предел текучести. Стали достаточно легко штампуются, но при этом сильно упрочняются (после штамповки сгт = 450 .. .600 МПа).
|
|
Свариваемость — способность получения сварного соединения, равнопрочного с основным металлом. Свариваемость металла характеризуется коэффициентом равнопрочности сварного соединения, количеством допускаемых способов и простотой технологии.
Большинство неразъемных соединений получают сваркой плавлением с использованием мощного теплового источника — электрической дуги. При этом основной металл и электрод плавятся, образуя жидкую ванну. Температуры сварочной ванны и примыкающего металла достигают высоких значений. После кратковременного нагрева следует достаточно быстрое охлаждение, т.е. возникает своеобразный термический цикл, который определяет строение сварного шва и околошовной зоны. При сварке углеродистой стали структура околошовной зоны (зоны термического влияния) формируется в соответствии с диаграммой состояния Fc ГезС (рис. 10.2). Шов имеет структуру литого металла, которая образуется в процессе первичной кристаллизации. Из-за направленного отвода теплоты кристаллы здесь приобретают столбчатую форму, вытяну тую перпендикулярно линии сплавления.
Зона термического влияния состоит из четырех участков:
1) участка перегрева с крупным зерном и повышенной хрупкостью. В углеродистых сталях здесь формируется видманштеттова структура, состоящая из сетки феррита и пластинчатого перлита; в легированных
|
-^ '■ "г
1
I
Рис. 10.2. Схима строения с.варно- |
го соединения при сварке стыково- ]
го шва: I
К' кит сплавления; ЗТВ - зона терми- |
ческою влияния; / участок перегрева;
11 участок полной перекристаллизации; I
- I
./ участок частичной нерекристаллиза- _-_Д
ции; 4 зона низкого отжита FrC«Ssi
Таблица 10.1. Структура стали в различных участках зоны термического влияния сварного шва
)М('Р | Сталь | ||
к-тка | низкоуглеродистая | низколегированная | средне- и высоколегированная* |
1 2 •1 | Ф+Н (крупное зерно) Ф+П (мелкое зерно) Ф+П 'Го же | В (крупное зерно) Б (мелкое зерно) Б+Ф Ф+карбиды | М+Аост (крупное зерно) М+Аост (мелкое зерно) М+Ф Продукты отпуска |
*Н высоколегированных аустснитных сталях зона термического влияния сохраняем пру туру аустенита.
с 1 алях возможно образование структур закалки: бейнита, мартенсита или i мсти мартенсита с бейпитом (табл. 10.1). Этот участок предрасположен к и(>ра *ованик> холодных трещин;
2) участка полной перекристаллизации, образующегося после натре и.| выше критической точки Л;\. На этом участке в углеродистых стали \ образуется мелкое; зерно, они имеют повышенный запас пластичности и НЯ1КОСТИ; в легированных сталях здесь также возможно образование i i р\ к тур закалки;
Л) участка неполной перекристаллизации, образующегося после на-i pina стали в межкритическом интервале температур А\ — /1з- После и.и рева углеродистых сталей здесь сохраняется крупное зерно феррита и и шел i.чается перлитная составляющая; в легированных сталях возможно ■ •Г|р;моиание структур неполной закалки;
1) зоны низкою отпуска, испытывающей нагрев ниже- температур ijimniiux превращений (точки Л\). Происходящие на этом участке изменении заиисич от исходной структуры cia.in, которая может не изменять « ш. йены 1 мил 11. рскрис | аллизнцию. если предвари ie.ii,по Пыла проведена
холодная деформация, или отпуск, если металл был предварительно закален.
Ширина характерных участков зоны термического влияния зависит от режима сварки и толщины свариваемого металла. Свариваемость стали тем выше, чем меньше в ней углерода и легирующих элементов. Влияние углерода является определяющим. С увеличением его концентрации усиливается склонность к образованию горячих и холодных трещин.
Горячие трещины образуются непосредственно в сварном шве в процессе кристаллизации, когда металл находится в двухфазном состоянии. Причинами их возникновения являются кристаллизационные усадочные напряжения, а также образование сегрегации примесей (серы, фосфора, кислорода), ослабляющих связи между формирующимися зернами. Склонность к образованию горячих трещин тем выше, чем шире интервал кристаллизации и ниже металлургическое качество стали. Углерод расширяет интервал кристаллизации и усиливает склонность стали к возникновению горячих трещин. Холодные трещины образуются при охлаждении сварного шва ниже 200 - 300 °С преимущественно в зоне термического влияния. Это наиболее распространенный дефект при сварке легированных сталей. Холодные трещины редко встречаются в низкоуглеродистых сталях и особенно в сталях с аустенитной структурой. Причина их образования — внутренние напряжения, возникающие при структурных превращениях (особенно мартенситном) в результате местной закалки (подкалки). Увеличивая объемный эффект мартенситного превращения, углерод способствует появлению холодных трещин.
Для оценки склонности стали к образованию холодных трещин используют значение углеродного эквивалента:
Сэкв = С + Мп/6 + Si/24 + Ni/40 + Сг/5 + Мо/4 + V/14 + Си/13 + Р/2,
где символы легирующих элементов обозначают их массовые доли в дан ной марке стали, а числа — их коэффициенты активности.
Высокой свариваемостью обладают стали, у которых углеродный эквивалент не превышает 0,45... 0,48 %, т.е. содержащие до 0,25% С. В эту группу входят углеродистые стали Ст1 - Ст4, 0,5, 08, 10, 15, 20, 25; низколегированные стали 09Г2(Д), 09Г2С, 14Г2, 15ГФ(Д), 16ГС, 17ГС и др., применяемые для изготовления различных металлоконструкций (трубопроводов, мостов, вагонов, судов), а также стали с карбонитридным упрочнением 14Г2АФ(Д), 15Г2СФ(Д), 16Г2АФ и др., применяемые для изготовления металлоконструкций (мостов, цехов, кранов, резервуаров). Все они содержат небольшие добавки ванадия в сочетании с повышенным содержанием азота (до 0,025 %).
Сварка полуфабрикатов из этих сталей при толщинах до 15 мм не иызываег загрудиений. Сварка при больших толщинах и и термически упрочненном сосгоянии требует подогрева и термической обработки. При (парке полуфабрикатов из углеродистых и низколегированных сталей, со дгржащих более 0,3% С, возникают затруднения из-за возможности за килки и охрупчинания околошовной зоны; сварка полуфабрикатов из нысо ►«хромистых и хромоникелсвых сталей в связи с неизбежными фазовыми превращениями в металле требует специальных технологических ирис мои снижения скорости охлаждения, применения защитных атмосфер и последующей термической обработки.
10.3. Железоуглеродистые сплавы с высокими литейными свойствами
Литейные свойства сплавов оценивают жидкотекучестью, усадкой, а гакже склонностью к образованию пористости, ликвации, горячих и холодных трещин. От литейных свойств зависит не только возможность получения сложной отливки, но и ее конструкционная прочность, так как многие дефекты литой структуры — пористость, ликвационная неодно родное п., микротрещины эффективные концентраторы напряжений.
Литейные свойства сплавов тем выше, чем меньше их температурный интервал кристаллизации. В связи с этим наиболее высокими литейны ми свойствами обладают сплавы, испытывающие эвтектическое превра щение. Из сплавов на основе железа лучшие литейные свойства имеют чуiуны.
10.3.1. Разновидности чугунов
Чу.'унами называются железоуглеродистые сплавы, содержащие бо ,■»•«• 2,1-1% С и затвердевающие с образованием эвтектики. Благодаря ««•метанию высоких литейных свойств, достаточной прочности, износо < 1МИМКТИ, а также относительной дешевизне чугуны получили широкое |м< прос гранение в машиностроении. Их используют для производства ка чп I венных отливок сложной формы при отсутствии жестких требований к I аоари'1 ам и массе деталей.
Н зависимости от того, в какой форме присутствует углерод в сила ппх, различают белые, серые, высокопрочные чугуны, чугуны с вермику лирным графитом и ковкие чугуны1. Высокопрочные чугуны и чугуны с
' Нлншние (ii'jii.ix и серых чугунок определяется цветом ичлома, пачнанис конкою V ломкое.
вермикулярным графитом являются разновидностью серых, но из за по вышенных механических свойств их выделяют в особые группы.
Белыми называются чугуны, в которых весь углерод находится в связанном состоянии в виде цементита. Согласно диаграмме состояния Fe -ГезС белые чугуны подразделяют на доэвтектические, эвтектический и заэвтектические. Из-за большого количества цементита они твердые (450 - 550 НВ), хрупкие и для изготовления деталей машин не используются. Ограниченное применение имеют отбеленные чугуны-отливки из серого чугуна со слоем белого чугуна в виде твердой корки на поверхности. Из них изготовляют прокатные валки, лемехи плугов, тормозные колодки и другие детали, работающие в условиях износа.
В промышленности широко применяют серые, высокопрочные и ковкие чугуны, в которых весь углерод или часть его находится в виде графита. Графит обеспечивает пониженную твердость, хорошую обрабатываемость резанием, а также высокие антифрикционные свойства вследствие низкого коэффициента трения. Вместе с тем включения графита снижают прочность и пластичность, так как нарушают сплошность металлической основы сплава. Серые, высокопрочные и ковкие чугуны различаются условиями образования графитных включений и их формой, что отражается на механических свойствах отливок.
10.3.2. Серые чугуны
Серыми называются чугуны с пластинчатой формой графита.
По химическому составу серые чугуны разделяют на обычные (нелегированные) и легированные. Обычные серые чугуны — сплавы сложного состава, содержащие основные элементы: Fe, С, Si и постоянные примеси: Mn, Р и S. Содержание этих элементов в серых чугунах колеблется в следующих пределах, %: 2,2 - 3,7 С; 1 - 3 Si; 0,2 - 1,1 Mn; 0,02 - 0,3 Р и 0,02 - 0,15 S. В небольших количествах в обычных серых чугунах могут содержаться Сг, Ni и Си, которые попадают из руды. Почти все эти элементы влияют на условия графитизации, количество графитных включений, структуру металлической основы и, как следствие, свойства чугунов.
Углерод оказывает определяющее влияние на качество чугунов, изменяя количество графита и литейные свойства. Чем выше концентрация углерода, тем больше выделений графита и ниже механические свойства чугуна. По этой причине максимальное содержание углерода ограничивается доэвтектической концентрацией. В то же время снижение его содержания отрицательно сказывается на жидкотекучести и, следовательно,
на литейных свойствах чугунов. Нижний предел углерода принимаю'! дли юлегостснных отливок, верхний для тонкостенных.
Кремний обладает сильным графитизирующим действием; способ сiмуст выделению графита в процессе затвердевания чугунов и разложе ник) выделившегося цементита.
Марганец затрудняет графитизацию чугунов, несколько улучшае г их механические свойства, особенно в тонкостенных отливках.
('ера вредная примесь. Она ухудшает механические и литейные свойства чугунов: понижает жидкотекучесть, увеличивает усадку и по нышаст склонность к образованию трещин.
Фосфор в количестве до 0,3% растворяется в феррите. При большей концентрации он образует с железом и углеродом тройную «фосфидную»
• тек тику. Она имеет низкую температуру плавления (950 °С), что у не
личинает жидкотекучесть чугунов, но высокую твердость и хрупкость.
Повышенное содержание фосфора допускается в отливках, от которых
I ребуется высокая износостойкость (до 0,7 Р), а также используемых для
художественного литья (до 1 % Р). В литых чугунных деталях содержа
иие фосфора ограничивают 0,3 %.
Таким образом, степень графитизации в чугунах возрастает с уне личением содержания углерода и кремния. Аналогичное, но более слабое влияние оказывают примеси (или легирующие элементы) меди и никеля. Элементами, затрудняющими графитизацию (отбеливающими), явля имея марганец, сера, хром. Основные элементы, которыми регулируют
• i рук гуру металлической основы серых чугунов, —- углерод и кремний.
Кроме химического состава структура чугуна и его свойства зави ( mi от технологических факторов, главным из которых является скорость охлаждения. С уменьшением скорости охлаждения возрастает количество i рлфита., а с ее увеличением - количество химически связанного углеро i.i При выборе скорости охлаждения принимают во внимание толщину < м'ики отливки. Чем она больше, тем меньше скорость охлаждения и ио.шес протекает процесс графитизации.
II чугунах с высоким содержанием кремния при медленном охлажде нии оишвки первичная кристаллизация происходит в соответствии со ■ ыоильной диаграммой Fe С (см. рис. 4.18); в этом случае графит по и и тек я непосредственно из жидкой фазы. С увеличением скорости охла. *;н'нии создаются условия для первичной кристаллизации в соответствии ( mi' lac I абильной диаграммой Fe Fe.-jC (см. рис. 4.11); из жидкой фазы им .ir.iMc i с я цементит, а графит образуется вследствие его распада при i.i п.пейшем охлаждении. Иногда ледебурит не разлагается и остается в с i |1\к I у ре.
Вторичная кристаллизация преимущественно протекает в соответствии с метастабильной диаграммой, вторичный цементит и цементит перлита могут сохраниться или графитизироваться в зависимости от содержания кремния и скорости охлаждения.
Наглядное представление о влиянии углерода и кремния на степень графитизации чугуна и его структуру дают структурные диаграммы. Структурная диаграмма, приведенная на рис. 10.3, а, справедлива для отливок с толщиной стенки 50 мм. Влияние толщины стенки и состава чугуна (суммарного содержания углерода и кремния) характеризует диаграмма, представленная на рис. 10.3, б.
Поле диаграммы разбито на пять областей. Область / соответствует белому чугуну, имеющему структуру перлит + вторичный цементит + ледебурит; весь углерод здесь связан в виде цементита. В области II находится половинчатый чугун со структурой П + Ц + графит; количество связанного углерода в нем более 0,8 %.
Химический состав серых чугунов отвечает областям 77/, Ша и Шб. По структуре металлической основы серые чугуны разделяют на три вида:
1) серый перлитный со структурой П + графит (рис. 10.4,а). В этом чугуне количество связанного углерода составляет ~ 0,8%;
2) серый ферритно-перлитный со структурой Ф + П + графит. Количество связанного углерода в нем менее 0,8 %;
3) серый ферритный со структурой Ф + графит (рис. 10.4, б). В этом чугуне весь углерод находится в виде графита.
Рис. 10.3. Структурная диаграмма чугунов в зависимости от содержания кремния и углерода (а) и толщины стенки отливки
/~ белый чугун; //- половинчатый чугун; ///, Ша, Шб - серый перлитный, ферритно-перлитный и ферритный чугун соответственно
Рис. 10.4. Микроструктуры серых чугунов. хЗОО:
а - перлитного; б - ферритного
Механические свойства серых чугунов зависят от свойств металлической основы и главным образом от количества, формы и размеров графитных включений. Прочность, твердость и износостойкость чугунов растут с увеличением количества перлита в металлической основе, которая по строению аналогична сталям. Решающее влияние графита обусловлено тем, что его пластинки, прочность которых ничтожно мала, действуют как надрезы или трещины, пронизывающие металлическую основу и ослабляющие ее. При растяжении (наиболее жестком виде нагружения) по концам графитных включений легко формируются очаги разрушения. Но этой причине серые чугуны плохо сопротивляются растяжению, имеют низкие прочность и пластичность. Относительное удлинение при растяжении независимо от структуры основы не превышает 0,5 %. Чем крупнее и прямолинейнее форма графитных включений, тем ниже сопротивление разрыву. И, наоборот, чем мельче и разобщеннее графитные включения, гом меньше их отрицательное влияние.
Значительно слабее влияние графита при изгибе и особенно при сжатии, т.е. при более «мягких» видах нагружения. Статическая прочность серых чугунов при изгибе примерно в 2 раза, а при сжатии — в 4 раза выше, чем при растяжении. Прочность при сжатии и твердость определяются в основном структурой металлической основы чугунов. Они близки к свойствам стали с той же структурой и составом, что и металлическая
основа чугуна.
Более высокая чувствительность чугунов к нормальным напряжениям, чем к касательным, сохраняется при циклических нагрузках. IIpt
этом сопротивление усталости у них, как и у сталей, растет с увеличением статической прочности. Предел выносливости при круговом изгибе ст-1 = (0)45 ■ . .0,58)ств. Наибольшее его значение имеют чугуны с измельченными графитными включениями и перлитной основой.
Для серых чугунов характерно следующее соотношение пределов выносливости при растяжении, изгибе и кручении: ст_\р : о_х : г_! = = 1 : 2 : 1,3. Наиболее высоко сопротивление усталости чугунов сжимающим напряжениям. При пульсирующем цикле сжатия оно в 5 - 6 раз выше, чем при пульсирующем цикле растяжения.
В соответствии с отмеченной особенностью чугуны целесообразнее использовать для деталей, работающих на сжатие. Однако в реальных условиях эксплуатации может возникнуть сложное напряженное состояние. В этом случае работоспособность чугуна лимитируется долей растягивающих напряжений. Поэтому показателем механических свойств серых чугунов, в соответствии с ГОСТ 1412-85, является прочность при статическом растяжении.
Марка серого чугуна состоит из букв СЧ (серый чугун) и цифры, показывающей уменьшенное в 10 раз значение (в мегапаскалях) временного сопротивления при растяжении (табл. 10.2).
Прочность чугуна существенно зависит от толщины стенки отливки. Указанное в марке значение сгв соответствует отливкам с толщиной стенки 15 мм. При увеличении толщины стенки от 15 до 150 мм прочность и твердость чугуна уменьшаются почти в два раза.
Графит, ухудшая механические свойства, в то же время придает чу-гунам ряд ценных свойств. Он измельчает стружку при обработке резанием, оказывает смягчающее действие и, следовательно, повышает износостойкость чугунов, придает им демпфирующую способность. Кроме того, пластинчатый графит обеспечивает малую чувствительность чугунов к дефектам поверхности. Благодаря этому сопротивления усталости чугунных и стальных деталей соизмеримы.
Номенклатура отливок из серого чугуна и их масса разнообразны: от деталей в несколько граммов (поршневые кольца двигателей) до отливок в 100 т и более (станины станков). Выбор марки чугуна для конкретных условий работы определяется совокупностью технологических и механи ческих свойств.
Ферритные серые чугуны СЧ 10, СЧ 15 предназначены для слабо и средненагружснных деталей: крышки, фланцы, маховики, корпуса редукторов, подшипников, насосов, а также суппорты, тормозные барабаны, диски сцепления и пр.
К).П. Желеюуглгродис iне гплним с ныожими ли н'йшлми синие i ними У!)7 Таблица 10.2. Механически»: свойства чугунов
Марка | о-в | С(),2 | 6,% | ПН | Структура |
чугуна | МИ а | металлической оспоны |
Серые чугуны (ГОСТ Ц\2 85)
Ф Ф Ф+П п |
100 150 250 350 |
СЧ 10 |
СЧ 15 |
СЧ 25 |
СЧ 35 |
ВЧ 35 |
ВЧ 45 |
ВЧ 60 |
ВЧ 80 |
ВЧ 100 |
чугу} ЧВГ 30 |
ЧВГ 35 |
ЧВГ 40 |
ЧВГ 45 |
-190 163 210 180 -245 220 - 275
Высокопрочные чугуны (ГОСТ 7293 - 85)
350 | 220 | 22 |
450 | 310 | 10 |
600 | 370 | 3 |
800 | 490 | 2 |
1000 | 700 | 2 |
Ф Ф+П Ф+П II Б |
140- 170 140 - 225 192-227 248-351 270 - 360
Чугуны с вермикулярным графитом (ГОСТ 28384 - 89)
300 | 240 | 3 |
350 | 260 | 2 |
400 | 320 | 1,5 |
450 | 380 | 0,8 |
ф Ф+П Ф+П II Ф+до 10 % II |
130-180 140-190 170 - 220 190 - 250
100-163 100 - 163 110-163 150-207 200 - 269 270-320 |
П+до 20 % Ф |
Ковкие чугуны (ГОСТ 1215 - 19)
КЧ 30 - 6 | 300 | - | 6 |
КЧ 35 - 8 | 350 | - | 8 |
КЧ 37 12 | 370 | - | 12 |
КЧ 45 - 7 | 450 | - | 7 |
КЧ 60 - 3 | 600 | - | 3 |
КЧ 80 - 1,5 | 800 | - | 1,5 |
Ферритно-перлитные серые чугуны СЧ 20, СЧ 25 применяют для лпллей, работающих при повышенных статических и динамических на lpyiKax: блоки цилиндров, картеры двигателя, поршни цилиндров, бара мины сцепления, станины различных станков, зубчатые колеса и другие и 1.1 инк и.
Перлитные серые модифицированные чугуны СЧ 30, СЧ 35 обладают более высокими механическими свойствами главным образом из-за мелких разобщенных графитных включений. Измельчение графитных включений в них достигается путем модифицирования жидкого чугуна ферросилицием или силикокальцием (0,3- 0,6 % от массы шихты). Модифицированные чугуны используют для деталей, работающих при высоких нагрузках или в тяжелых условиях износа: зубчатые колеса, гильзы блоков цилиндров, шпиндели, распределительные валы и пр. Чугуны этих марок обладают наибольшей герметичностью. По этой причине их широко применяют также для корпусов насосов, компрессоров, арматуры тормозной пневматики и гидроприводов.
Для деталей, работающих при повышенных температурах, применяют легированные серые чугуны: жаростойкие (дополнительно содержат Сг, А1), жаропрочные (Сг, Ni, Mo). Применение находят также немагнитные, хромоникелевые чугуны с аустенитной структурой.
Из них изготовляют стойки для магнитов, крышки выключателей и пр.
Отливки из серого чугуна подвергают термической обработке. Используют низкий отжиг (~ 560 °С) для снятия внутренних напряжений и стабилизации размеров, нормализацию или закалку с отпуском для повышения механических свойств и износостойкости. Для повышения износостойкости гильз цилиндров, распределительных валов и других деталей отдельных двигателей автомобилей перлитные чугуны подвергают азотированию.
Высокопрочные чугуны
Высокопрочными называют чугуны, в которых графит имеет шаровидную форму. Их получают модифицированием магнием, который вводят в жидкий чугун в количестве 0,02 - 0,08 %. Ввиду того, что модифицирование чугунов чистым магнием сопровождается сильным пироэффек-том, чистый магний заменяют лигатурами (например, сплавом магния и никеля).
Чугун после модифицирования имеет следующий химический состав, %: 3,0 - 3,6 С; 1,1 - 2,9 Si; 0,3 - 0,7 Мп; до 0,02 S и до 0,1 Р. По структуре металлической основы высокопрочный чугун может быть фер-ритным или перлитным. Ферритный чугун в основном состоит из феррита и шаровидного графита; допускается до 20 % перлита. Структура перлитного чугуна - сорбитообразный или пластинчатый перлит и шаровидный графит; допускается до 20 % феррита (рис. 10.5).
Рис. 10.5. Микроструктура высокопрочного чугуна. хЗОО
Шаровидный графит - менее сильный концентратор напряжений, чем пластинчатый, поэтому он меньше снижает механические свойства металлической основы. Чугуны с шаровидным графитом обладают более высокой прочностью и некоторой пластичностью. Марка высокопрочного чугуна состоит из букв ВЧ и числа, обозначающего уменьшение в К) раз значения временного сопротивления (см. табл. 10.2).
Высокопрочные чугуны применяют в различных отраслях техники, эффективно заменяя сталь во многих изделиях и конструкциях. Из них изготовляют оборудование прокатных станов (прокатные валки массой до 12 т), кузнечно-прессовое оборудование (траверса пресса, шабот ковочного молота); в турбостроении — корпус паровой турбины, лопатки направля ющего аппарата; в дизеле-, тракторо- и автомобилестроении —- коленчатые валы, поршни и многие другие ответственные детали, работающие при высоких циклических нагрузках и в условиях изнашивания.
В некоторых случаях для улучшения механических свойств примени ют термическую обработку отливок: закалку и отпуск при 500-600 °С для повышения прочности; отжиг, способствующий сфероидизации перли i а, для увеличения пластичности.
10.3.4. Чугуны свермикулярным графитом
В чу тунах с вермикулярным графитом структура формируется пои действием комплексного модификатора, содержащего магний и редкоземельные металлы. Графит приобретает шаровидную (до 10%) и верми кулярную в виде мелких топких прожилок форму.
После модифицирования эти 'ivmiu содержат', %: 3,1 3,8 С; 2,0 3,0 Si; 0,2 1,0 Мп; то 0,025 S; 0,08 I'.
Чугуны с вермикулярным графитом производят четырех марок: ЧВГ 30; ЧВГ 35; ЧВГ 40; ЧВГ 45 (табл. 10.2). Число в марке обозначает уменьшенное в 10 раз значение временного сопротивления.
По механическим свойствам чугуны с вермикулярным графитом за нимают промежуточное положение между серыми и высокопрочными чу гунами. Они прочнее серых чугунов, особенно при циклических нагрузках; предел выносливости ст_] составляет 140 МПа у ЧВГ 30 и 190 МИа у ЧВГ 45. Механические свойства этих чугунов в меньшей степени зависят от массы отливок. Они отличаются хорошей теплопроводностью (40 -50 Вт/(м-К)), что обеспечивает их стойкость к теплосменам.
Чугуны с вермикулярным графитом заменяют серые чугуны в отливках, подвергаемых циклическим нагрузкам и частым теплосменам. Из них отливают блоки цилиндров, поршни, гильзы, крышки цилиндров двигателей внутреннего сгорания, а также изложницы и кокили. При введении в состав чугунов до 1,2% Ni и 0,4% Мо они хорошо противостоят изнашиванию и кавитации.
10.3.5. Ковкие чугуны
Ковкими называются чугуны, в которых графит имеет хлопьевидную форму. Их получают отжигом белых доэвтектических чугунов. По этой причине графит ковких чугунов называют углеродом отжига. Такой графит, в отличие от пластинчатого, меньше снижает механические свойства металлической основы, вследствие чего ковкие чугуны по сравнению с серыми обладают более высокой прочностью и пластичностью.
Отливки из белых чугунов, подвергаемые отжигу на ковкие чугуны, изготовляют тонкостенными. Они не должны иметь сечение более 50 мм, иначе в сердцевине при кристаллизации выделяется пластинчатый графит, и чугун становится непригодным для отжига. По этой же причине исходные белые чугуны имеют пониженное содержание углерода и кремния. Их химический состав следующий, %: 2,4 - 2,9 С; 1,0 - 1,6 Si; 0,2 1,0 Мп; до 0,2 S и до 0,18 Р.
По структуре металлической основы, которая определяется режимом отжига, ковкие чугуны бывают ферритными и перлитными (рис. 10.(5).
Отжиг на ферритные чугуны проводят по режиму 1 (рис. 10.7), обеспечивающему графитизацию всех видов цементита белых чугунов. Отливки из такого чугуна загружают в специальные ящики и засыпают песком или стальными стружками для защиты от окисления и медленно (20 - 25 ч) нагревают до температуры несколько ниже эвтектической 950 - 1()()0°С. 15 процессе про ю.тжи i с.тиюй (К) 15 ч) выдержки при
а Рис. 10.6. Микроструктуры ковких чугунов. хЗОО:
а - ферритного; б - перлитного
такой температуре происходит первая стадия графитизации. Она состоит в распаде эвтектического и избыточного вторичного цементита (имеющеюся в небольшом количестве при этой температуре). К концу первой стадии графитизации чугун состоит из аустенита и включений углерода отжига. Затем температуру медленно снижают. При этом происходит промежуточная стадия графитизации — распад выделяющегося вторичного цементита. Вторая стадия графитизации протекает или при весьма медленном охлаждении в эвтектоидном интервале температур, или при длительной выдержке (25 - 30 ч) несколько ниже температуры эвтекто-идного превращения (720 —740°С). В процессе этой выдержки распадается цементит перлита. В результате такого отжига продолжительностью 70 80 ч весь углерод выделяется в свободном состоянии и формируется структура, состоящая из феррита и углерода отжига.
|
г, °С |
Рис. 10.7. Схемы отжига болого чугуна на форритный (/) и перлитный (£) ковкие чугуны |
Перлитный ковкий чугун получают отжигом, который провопят в окислительной среде по режиму 2 (см. рис. 10.7). В этом случае увеличивают продолжи-н'лыюсть первой стадии графитизации, после которой проводят непрерывное охлаждение отливок до 20 °С. Поскольку графитиза-пия цементита перлита практически не происходит, чугун приобретает структуру, состоящую из перлита и углерода отжига.
302 Глава 10. Материалы с особыми технологическими свой г I ними
Отсутствие литейных напряжений, которые полностью снимаются во время отжига, компактная форма и изолированность графитных включений обусловливают высокие механические свойства ковких чугунов. Маркируют ковкие чугуны буквами КЧ и числами, первое из которых указывает уменьшенное в 10 раз значение <тв, второе — значение 6. Из табл. 10.2 следует, что ферритные чугуны имеют более высокую пластичность, а перлитные — более высокие прочность и твердость.
Ковкие чугуны нашли широкое применение в сельскохозяйственном, автомобильном и текстильном машиностроении, в судо-, котло-, вагоно-и дизелестроении. Из них изготовляют детали высокой прочности, работающие в тяжелых условиях износа, способные воспринимать ударные и знакопеременные нагрузки. Большая плотность отливок позволяет делать из ковкого чугуна детали водо- и газопроводных установок, а хорошие литейные свойства исходного белого чугуна — производить отливки сложной формы.
Недостаток ковких чугунов — повышенная по сравнению с остальными чугунами стоимость из-за продолжительного дорогостоящего отжига.
10.4. Медь иее сплавы 10.4.1. Свойства меди
Медь — металл красновато-розового цвета, имеющий кристаллическую ГЦК решетку с периодом а = 0,3608 нм, без полиморфных превращений. Медь менее тугоплавка, чем железо, но имеет большую плотность.
Медь обладает хорошей технологичностью. Она прокатывается в тонкие листы и ленту, из нее получают тонкую проволоку, медь легко полируется, хорошо паяется и сваривается. Примеси кислорода, водорода, свинца и висмута ухудшают свариваемость меди. Применение специальных керамических флюсов улучшает качество сварного шва, приближая его физические и механические свойства к характеристикам основного металла.
Медь характеризуется высокими теплопроводностью и электрической проводимостью, пластичностью и коррозионной стойкостью в атмосферных условиях, пресной и морской воде, едких щелочах, органических кислотах и других агрессивных средах. Однако она взаимодействует с аммиаком, азотной, соляной, горячей концентрированной серной кислотами. Примеси влияют на все эти свойства. По ГОСТ 859-78 в зависимости от содержания примесей различают следующие марки меди: М00 (99,99% Си), МО (99,97% Си), Ml (99,9% Си), М2 (99,7% Си), МЗ (99,5% Си).
Наиболее часто встречающиеся и меди элементы подразделяют на три группы.
1. Растворимые в меди эле
менты Al, Fe, Ni, Sn, Zn, Ag по
вышают прочность и твердость
меди (рис. 10.8) и используются
для легирования сплавов на мед
ной основе.
1 2 Легирующий элемент, % Рис. 10.8. Влияние легирующих элементов на твердость меди |
2. Нерастворимые элемен
ты РЬ и Bi ухудшают механи
ческие свойства меди и однофаз
ных сплавов на ее основе. Обра
зуя легкоплавкие эвтектики (со
ответственно при 326 и 270°С),
располагающиеся по границам зе
рен основной фазы, они вызывают
красноломкость. Причем вредное
влияние висмута обнаруживается при его содержании в тысячных долях процента, поскольку его растворимость ограничивается 0,001 %. Вредное влияние свинца также проявляется при малых его концентрациях (< 0,04%). Висмут, будучи хрупким металлом, охрупчивает медь и ее сплавы. Свинец, обладая низкой прочностью, снижает прочность медных сплавов, однако вследствие хорошей пластичности не вызывает их пхрунчивания. Кроме того, свинец улучшает антифрикционные свойства и обрабатываемость резанием медных сплавов, поэтому его применяют для легирования. 3. Нерастворимые элементы О, S, Se, Те присутствуют и меди и ее сплавах в виде промежуточных фаз (например, СизО, CU2S), которые образуют с медью эвтектики с высокой температурой плавления и не вызывают красноломкости. Кислород при отжиге меди в водороде вызывает «водородную болезнь», которая может привести к разрушению металла при обработке давлением или эксплуатации готовых деталей.
Механические свойства меди в большей степени зависят от ее состоим и я (табл. 10.3) и в меньшей от содержания примесей.
Холодная пластическая деформация (достигающая 90 % и более) увеличивает прочность, твердость, предел упругости меди, но снижает пла-< i ичпость и электрическую проводимость. При пластической деформации m> in икает текстура, вызывающая анизотропию механических свойств меди. Отжиг д-Гя снятия наклепа проводят при 550 — 600°С в восстано-иим'лыюй атмосфере, гак как медь легко окисляется при нагреве. По
Таблица 10.3. Механические свойства технической меди Ml
Состояние | о-в | ^0,2 | 6 | Ф | НВ | KCU, |
МПа | % | МДж/м2 | ||||
Литое | 160 | 35 | 25 | - | 40 | _' |
Деформированное* | 450 | 400 | 3 | 35 | 125 | - |
Отожженное | 220 | 75 | 50 | 75 | 55 | 1,2-1,8 |
'Свойства проволоки, продеформированной на 90 %.
электрической проводимости и теплопроводности медь занимает второе место после серебра. Она применяется для проводников электрического тока и различных теплообменников, водоохлаждаемых изложниц, поддонов, кристаллизаторов. Недостатки меди — невысокая прочность, плохая обрабатываемость резанием и низкая жидкотекучесть.
10.4.2. Общая характеристика и классификациямедных сплавов
Сохраняя положительные качества меди (высокие теплопроводность и электропроводимость, коррозионную стойкость и т.д.), ее сплавы обладают хорошими механическими, технологическими и антифрикционными свойствами. Для легирования медных сплавов в основном используют элементы, растворимые в меди, — Zn, Sn, Al, Be, Si, Mn, Ni. Повышая прочность медных сплавов, легирующие элементы практически не снижают, а некоторые из них (Zn, Sn, Al) увеличивают пластичность. Высокая пластичность — отличительная особенность медных сплавов. Относительное удлинение некоторых однофазных сплавов достигает 65 %. По прочности медные сплавы уступают сталям. Временное сопротивление большинства сплавов меди лежит в интервале 300 - 500 МПа, что соответствует свойствам низкоуглеродистых нелегированных сталей в нормализованном состоянии. И только временное сопротивление наиболее прочных берил-лиевых бронз после закалки и старения находится на уровне среднеугле-родистых легированных сталей, подвергнутых термическому улучшению (ств = 1100... 1200 МПа).
По технологическим свойствам медные сплавы подразделяют на деформируемые (обрабатываемые давлением) и литейные; по способности упрочняться с помощью термической обработки ----- на упрочняемые и не упрочняемые термической обработкой. По химическому составу медные сплавы подразделяют на две основные группы: латуни и бронзы.
Медные сплавы маркируют по химическому составу, используя буквы для обозначения элементов и числа для указания их массовых деталей. I) медных сплавах (так же как в алюминиевых и магниевых) буквенные обо значения отличаются от обозначений, принятых для сталей. Алюминий в них обозначают буквой А; бериллий — Б; железо Ж; кремний К; медь - - М; магний — Мг; мышьяк — Мш; никель — Н; олово О; свинец
С; серебро — Ср; сурьма — Су; фосфор -- Ф; цинк Ц; цирконий Цр; хром — X; марганец — Мц.
Латуни (сплавы меди с цинком) маркируют буквой Л. В деформиру емых латунях, не содержащих кроме меди и цинка других элементов, за буквой Л ставится число, показывающее среднее содержание меди. В мио гокомпонентных латунях после Л ставятся буквы — символы элементов, а затем числа, указывающие содержание меди и каждого легирующего элемента. Например, латунь Л68 содержит 68% Си, латунь Л АН 59-3-2 содержит 59 % Си, 3 % А1; 2 % Ni (остальное Zn). В марках литейных ла гуней указывается содержание цинка, а количество каждого легирующем о элемента ставится непосредственно за буквой, обозначающей его. Например, латунь ЛЦ40МцЗА содержит 40 % Zn, 3 % Mn и 1 % Al.
Бронзы (сплавы меди со всеми элементами, кроме цинка) обозначают буквами Бр, за которыми ставятся буквы и числа. В марках деформируй мых бронз сначала помещают буквы — символы легирующих элементов, а затем числа, указывающие их содержание. Например, БрАЖЭ 4 с одер жит 9% А1, 4% Fe, остальное — Си. В марках литейных бронз после каждой буквы указывается содержание этого легирующего элемента. На пример, БрОбЦбСЗ содержит 6 % Sn, 6 % Zn, 3 % Pb, остальное Си.
Латуни
Медь с цинком образует твердый раствор с предельной концентраци «•и цинка 39% (рис. 10.9, а). При большем содержании цинка образуется i.icK тронное соединение CuZn (/3-фаза) с кристаллической решеткой О ЦК. При 454 - 468°С (штриховая линия на диаграмме) наступает унорядоче ние /3-фазы (/З'-фаза), сопровождающееся значительным повышением ее i верности и хрупкости. В отличие от равновесного состояния /З'-фаза появляется в структуре латуней при содержании цинка около 30%. В и «ответствии с изменением структуры меняются механические свойства латуней (рис. 10.9,6). Когда латунь имеет структуру а-твердого раство 1>а, увеличение содержания цинка вызывает повышение ее прочности и пластичности. Появление/3' фазы сопровождается резким снижением пла i [ичности, прочность продолжает повышаться при увеличении цинка до
![]() |
Си 10 20 30 40 50 Zn, % а
Рис. 10.9. Диаграмма состояния системы Си - Zn (а) и влияние цинка на механические свойства латуней (б)
45 %, пока латунь находится в двухфазном состоянии. Переход латуни в однофазное состояние со структурой /З'-фазы вызывает резкое снижение прочности. Практическое значение имеют латуни, содержащие до 45 % Zn. Сплавы с большим содержанием цинка отличаются высокой хрупкостью. Химический состав некоторых промышленных латуней (ГОСТ 15527-70, ГОСТ 17711-93) и их механические свойства приведены в табл. 10.4, 10.5.
Двойные латуни по структуре подразделяют на две группы:
1) однофазные со структурой отвердого раствора (рис. 10.10, а);
2) двухфазные со структурой а + /3-фаз (рис. 10.10, б).
В связи с высокой пластичностью однофазные латуни хорошо поддаются холодной пластической деформации, которая значительно повышает их прочность и твердость. Рекристаллизационный отжиг проводят при 600-700°С.
Повышение содержания цинка удешевляет латуни, улучшает их обрабатываемость резанием, способность прирабатываться и противостоять износу. Вместе с тем уменьшаются теплопроводность и электрическая проводимость, которые составляют 20 - 50 % от характеристик меди.
Примеси повышают твердость и снижают пластичность латуней. Особенно неблагоприятно действуют свинец и висмут, которые в однофазных латунях вызывают красноломкость. Поэтому однофазные латуни в основном выпускают в виде холоднокатаных полуфабрикатов: полос,
Таблица 1(1.4- Химический состав и механические свойства деформируемых латуней после отжига (ГОСТ 15527-70)
Марка | Си | Прочих | <7B | O"0,2 | 6 | V | KCU, | III) |
латуни | элементов | МДж/м2 | ||||||
% | (мае.) | МПа | % | |||||
Л90 | 88-91 | - | 260 | 120 | 45 | 80 | 1,76 | 53 |
Л68 | 67-70 | - | 320 | 90 | 55 | 70 | 1,68 | 55 |
Л63 | 62-65 | - | 330 | 110 | 50 | 66 | 1,37 | 56 |
Л60 | 59-62 | - | 380 | 160 | 25 | 62 | 0,78 | 77 |
ЛА77-2 | 76-79 | 1,75-2,5 А1 | 400 | 140 | 55 | 58 | - | 60 |
ЛАН59-3-2 | 57-60 | 2,5-3,5 А1 2-3 Ni | 380 | 300 | 50 | — | 0,5 | 75 |
ЛН65-5 | 64-67 | 5-6,5 Ni | 400 | 170 | 65 | - | - | 60 |
ЛЖМц59-1 - 1 | 57-60 | 0,1-0,4 Al 0,6- 1,2 Fe 0,5-0,8 Mn 0,3-0,7 Sn | 450 | 170 | 50 | 58 | 1,18 | 88 |
ЛМц58-2 | 57-60 | 1-2 Mn | 400 | 160 | 40 | 52,5 | - | 85 |
Л070 - 1 | 69-71 | l-l,5Sn | 350 | 100 | 60 | 70 | 0,6 | 60 |
ЛК80-3 | 79-81 | 2,5-4 Si | Si | 200 | 58 | 55 | 0,4 | 100 |
лент, проволоки, листов, из которых изготовляют детали методом глубокой вытяжки (радиаторные трубки, снарядные гильзы, сильфоны, трубопроводы), а также детали, требующие по условиям эксплуатации низкую i нордость (шайбы, втулки, уплотнительные кольца и др.).
В двухфазных латунях вследствие а ^-превращения легкоплавкие жтектики находятся не по границам, а внутри зерен твердого раствора и не влияют на их способность к горячей пластической деформации. И ногда добавляют свинец для улучшения обрабатываемости резанием и понышения антифрикционных свойств. Ввиду невысокой пластичпосги 11 и латуни выпускают в виде горячекатаного полуфабриката: листок, прутков, труб, штамповок. Из них изготовляют втулки, гайки, тройники, штуцеры, токопроводящие детали электрооборудования и др.
Вследствие небольшого температурного интервала кристаллизации двойные латуни обладают пилкой склонностью к дендритной ликнации, высокой жидко текучеегыо, малой рассеянной усадочной пористостью и
Таблица 10.5. Механические свойства и область применения литейных латуней (ГОСТ 17711-93)
Марка | <7В, МПа | 6, % | НВ | Область |
латуни | применения | |||
ЛЦ40С | 215 | 12-20 | 70-80 | Арматура, втулки, сепараторы для подшипников качения |
ЛЦ40МцЗЖ | 390 - 490 | 10-18 | 90-100 | Несложные детали ответственного назначения, гребные винты и лопасти, судовая арматура, работающая при температуре до 300 °С |
ЛЦ38Мц2С2 | 245 - 340 | 10-15 | 80-85 | Антифрикционные втулки, вкладыши, ползуны, |
ЛЦЗОАЗ | 290 - 390 | 12-15 | 80-90 | судовая арматура Коррозионно-стойкие детали |
ЛЦ23А6ЖЗМц2 | 700 | 7 | 160-165 | Детали ответственного назначения, нажимные винты и гайки прокатных станов, венцы червячных колес |
ЛЦ16К4 | 290 - 340 | 15 | 100-110 | Сложные по конфигурации детали, работающие при температуре до 250 °С |
ЛЦ14КЗСЗ | 245 - 290 | 7-15 | 90-100 | Подшипники, втулки |
|
Рис. 10.10. Микроструктуры латуней: а однофатой; б днухфачной (темная /?-фача, cue i лая нг-фа-in) |
Примечание. Максимальные механические свойства обеспечивают литье в кокиль, центробежное литье; минимальные — литье в песчаную форму.
хорошей герметичностью. Но, несмотря на это, они практически не при меняются для фасонных отливок, гак как имеют довольно большую кон центрированную усадочную раковину. Этот недостаток в меньшей степе ни присущ легированным латуням.
Легированные латуни применяют как для деформируемых иолуфа брикатов, так и в виде фасонных отливок. Литейные латуни, как правило, содержат большее количество легирующих элементов.
Для легирования латуней используют Al, Fe, Ni, Sn, Si. Эти элемен ты повышают прочность и коррозионную стойкость латуней. Поэтому легированные латуни широко применяют в речном и морском судострое нии (конденсаторные и манометрические трубки и другие детали).
Практическое применение находят высокомедистые латуни с добавлением алюминия до 4 % (ЛА77-2), которые благодаря однофазной структу ре хорошо обрабатываются давлением. Алюминиевые латуни дополни тельно легируют никелем, железом, марганцем, кремнием, обладающими переменной растворимостью в а-твердом растворе, что позволяет упрочнять эти латуни с помощью закалки и старения. Временное сопротипленив после такой обработки достигает 700 МПа. Хорошая пластичность в закаленном состоянии позволяет дополнительно упрочнять сплавы с по мощью пластического деформирования (перед старением). Обработка по схеме «закалка + пластическая деформация + старение» обеспечивает повышение временного сопротивления до 1000 МПа.
Кремнистые латуни характеризуются высокой прочностью, пластичностью, вязкостью не только при 20-25°С, но и при низких температурах (до —183°С). При легировании латуней для получения однофазной структуры используют небольшие добавки кремния (ЛК80-3). Такие латуни применяют для изготовления арматуры, деталей приборов, в судо- и машиностроении.
Бронзы
Оловянные бронзы
Из диаграммы состояния Си - Sn следует, что предельная растворимость олова в меди соответствует 15,8% (рис. 10.11, а). Сплавы этой системы характеризует склонность к неравновесной кристаллизации, в результате чего в реальных условиях охлаждения значительно сужается область а-твердого раствора, его концентрация практически не меняет ся с понижением температуры, не происходит энтектоидного превращения Л-фазы (см. штриховые линии диаграммы) и при содержании олова
Рис. 10.11. Диаграмма состояния системы Си - Sn (а) и влияние олова на механические свойства бронз (б)
более 6 - 8 % в структуре сплавов присутствует эвтектоид (а + 6), где £-фаза — электронное соединение Cu3iSns со сложной кубической решеткой. Оно обладает высокой твердостью и хрупкостью. Появление <5-фазы в структуре бронз вызывает резкое снижение их вязкости и пластичности (рис. 10.11,6). Поэтому практическое значение имеют бронзы, содержащие только до 10 % Sn.
Двойные оловянные бронзы применяют редко, так как они дороги. Широкий температурный интервал кристаллизации обусловливает у них большую склонность к дендритной ликвации, низкую жидкотекучесть, рассеянную усадочную пористость и поэтому невысокую герметичность отливок.
Оловянные бронзы легируют Zn, Pb, Ni, Р. В бронзы добавляют от 2 до 15 % Zn. В таком количестве цинк полностью растворяется в а-твердом растворе, что способствует повышению механических свойств. Уменьшая интервал кристаллизации оловянных бронз, цинк улучшает их жидкотекучесть, плотность отливок, способность к сварке и пайке. Свинец повышает антифрикционные свойства и улучшает обрабатываемость резанием оловянных бронз. Фосфор, являясь раскислителем оловянных бронз, повышает их жидкотекучесть; износостойкость улучшается благодаря появлению твердых включений фосфида меди Сиз Р. Кроме того, он
увеличивает временное сопротивление, предел упругости и выносливость бронз.
Бронзы хорошо обрабатываются резанием, паяются, хуже свариваются.
Среди медных сплавов оловянные бронзы имеют самую низшую ли нейьую усадку (0,8% при литье в песчаную форму и 1,4% при литье в металлическую форму), поэтому их используют для получения сложных фасонных отливок. Двойные и низколегированные литейные бронзы содержат 10 % Sn. Для удешевления оловянных бронз содержание олова в некоторых стандартизованных литейных бронзах снижено до 3 6 %. Большое количество Zn и РЬ повышает их жидкотекучесть, улучшает плотность отливок, антифрикционные свойства и обрабатываемость резанием. Структура оловянных бронз (БрОЗЦ12С5, Бр04Ц4С17, БрО10Ц2 и др.) полностью удовлетворяет требованиям, предъявляемым к структуре? антифрикционных сплавов. Высокая коррозионная стойкость в атмосферных условиях, пресной и морской воде способствует широкому применению литейных бронз для пароводяной арматуры, работающей под давлением. Рассеянная пористость не мешает этому, поскольку у поверхности отливок имеется зона с мелкозернистой структурой, обладающая высокой плотностью. При усовершенствовании технологии получают отливки, выдерживающие давление до 30 ЗУШа.
Деформируемые бронзы содержат до 6 - 8 % Sn (табл. 10.6). В равновесном состоянии они имеют однофазную структуру (а-твердого раствора (см. рис. 10.12, а). В условиях неравновесной кристаллизации наряду с i вердым раствором может образоваться небольшое количество <5-фазы. Для устранения дендритной ликвации и выравнивания химического со-< лава, а также улучшения обрабатываемости давлением применяют диф-фу»ионный отжиг, который проводят при 700— 750°С. При холодной пластической деформации бронзы подвергают промежуточным отжигам при 550- 700 °С. Деформируемые бронзы характеризуются хорошей ила-« тчностью и более высокой прочностью, чем литейные.
Деформируемые бронзы обладают высокими упругими свойствами и
..... рогивлением усталости. Их используют для изготовления круглых и
пли ких пружин в точной механике, электротехнике, химическом маши-itoi i роении и других областях промышленности.
Алюминиевые бронзы
Алюминиевые бронзы отличаются высокими механическими, анти
knpi»|-|И1>нШ.1МИ и антифрикционными свойствами. Их преимущества не
|н\| оловянными бронзами меньшая стоимость, более высокие меха
ии'М'гкис и некоторые технологические свойства. Например, небольшой
|
Рис. 10.12. Микроструктуры бронз:
а - деформированной однофазной с 5 % Sn после рекристаллизации; б - литой двухфазной с 10 % Sn
интервал кристаллизации обеспечивает алюминиевым бронзам высокую жидкотекучесть, концентрированную усадку и хорошую герметичность отливок, малую склонность к дендритной ликвации. Вместе с тем из-за большой усадки иногда трудно получить сложную фасонную отливку.
Медь с алюминием образует а-твердый раствор (рис. 10.13), концентрация которого при понижении температуры с 1035 до 565 °С увеличивается от 7,4 до 9,4 % А1. При 565 °С /3 — фаза претерпевает эвтектоидное превращение: /3 —* а + 72> гДе 72 — промежуточная фаза переменного состава со сложной кубической решеткой.
При реальных скоростях охлаждения, в отличие от равновесного состояния, эвтектоид появляется в структуре сплавов при содержании 6 -8 % А1. Наличие эвтектоида приводит к резкому снижению пластичности алюминиевых бронз. С увеличением содержания алюминия до 4 -5 % наряду с прочностью и твердостью повышается пластичность, которая затем резко падает, а прочность продолжает расти при увеличении содержания алюминия до 10 - 11 % (рис. 10.13, б).
Однофазные бронзы (БрА5, БрА7), имеющие хорошую пластичность, относятся к деформируемым. Они обладают наилучшим сочетанием прочности (ств = 400.. .450МПа) и пластичности (6 = 60%). Двухфазные бронзы выпускают в виде деформируемого полуфабриката, а также применяют для изготовления фасонных отливок. При наличии большого количества эвтектоида бронзы подвергают не холодной, а горячей обработке давлением. Двухфазные бронзы отличаются высокой прочностью (сгв = 600 МПа) и твердостью (> 100 НВ). Их можно подвергать упрочняющей термической обработке. При быстром охлаждении (закалке) /3-фаза претерпевает не эвтектоидное, а мартенситное превращение.
К недостаткам двойных алюминиевых бронз помимо большой усадки относятся: склонность к газонасыщению и окисляемости во время плавки, образование крупнокристаллической столбчатой структуры, трудность пайки. Эти недостатки уменьшаются при легировании алюминиевых бронз железом, никелем, марганцем.
В а-фазе алюминиевой бронзы растворяется до 4 % железа, при большем содержании образуются включения A^Fe. Дополнительное легирование сплавов никелем и марганцем способствует появлению этих включений при меньшем содержании железа. Железо оказывает модифицирующее действие на структуру алюминиевых бронз, повышает их прочность, твердость и антифрикционные свойства, уменьшает склонность к охруп-чиванию двухфазных бронз из-за замедления эвтектоидного распада /3-фазы и измельчения 72_Фазы> образующейся в результате этого распада. Наилучшей пластичностью алюминиево-железные бронзы (например, БрАЖ9-4) обладают после термической обработки, частично или полностью подавляющей эвтектоидное превращение /?-фазы (нормализация при 600 - 700°С или закалка от 950°С). Отпуск закаленной бронзы при 250-300 °С приводит к распаду /3-фазы с образованием тонкодисперсного эвтектоида (а + 72) и повышению твердости до 175 - 180 НВ.
Никель улучшает технологичность и механические свойства алюми-ниево-железных бронз при обычных и повышенных температурах. Кроме того, он способствует резкому сужению области а-твердого раствора при понижении температуры. Это вызывает у бронз, легированных железом и никелем (БрАЖН 10-4-4), способность к дополнительному
упрочнению после закалки вследствие старения. Например, и отожжен ном (мягком) состоянии БрАЖН 10-4-4 имеет следующие механические свойства: ст„ = 650 МПа; ё = 35%; 140 - 160 НВ. После закалки от !Ж0"С и старения при 400°С в течение 2 ч твердость увеличивается до 100 IIВ. Из алюминиево-железоникелевых бронз изготовляют детали, работающие в тяжелых условиях износа при повышенных температурах (400 - 500°С): седла клапанов, направляющие втулки выпускных клапанов, части насосов и турбин, шестерни и др. Высокими механическими, антикоррозионными и технологическими свойствами обладают нлюминиево-железные бронзы, легированные вместо никеля более дешевым марганцем (БрАЖМцЮ-3-1,5).
Кремнистые бронзы
Кремнистые бронзы характеризуются хорошими механическими, упругими и антифрикционными свойствами.
|
Рис. 10.14. Диаграмма состояния системы Си - Si |
Кремнистые бронзы содержат до 3 % Si и имеют однофазную структуру а-твердого раствора (рис. 10.14). При увеличении содержания кремния более 3 % в структуре сплавов появляется твердая и хрупкая 7-фаза. Однофазная структура твердого раствора обеспечивает кремнистым брон-•»ам высокую пластичность и хорошую обрабатываемость давлением. Они хорошо свариваются и паяются, удовлетворительно обрабатываются резанием. Литейные свойства кремнистых бронз ниже, чем оловянных, алюминиевых бронз и латуней.
Легирование цинком способствует улучшению литейных свойств этих бронз. Добавки марганца и никеля повышают прочность, твердость кремнистых бронз. Никель, обладая переменной растворимостью в а-фазе, позволяет упрочнять никель-кремнистые бронзы путем закалки и старения. После закалки от 800 °С и старения при 500 °С эти бронзы имеют сгв > 700 МПа, ё «8%.
Кремнистые бронзы выпускают в виде ленты, полос, прутков, проволоки. Для фасонных отливок они применяются редко. Их используют вместо более дорогих оловянных бронз при изготовлении антифрикционных деталей (БрКН1 - 3), (БрКМцЗ - 1), а также для замены бериллиевых бронз при производстве пружин, мембран и других деталей приборов, работающих в пресной и морской воде.
Бериллиевые бронзы
Бериллиевые бронзы характеризуются чрезвычайно высокими пределами упругости, временным сопротивлением, твердостью и коррозионной стойкостью в сочетании с повышенными сопротивлениями усталости, ползучести и износу. Двойные бериллиевые бронзы содержат в среднем 2,0
- 2,5 % Be (БрБ2, БрБ2,5). Согласно диаграмме состояния системы Си
- Be (рис. 10.15, а), они имеют структуру, состоящую из а-твердого раствора бериллия в меди и 7-фазы — электронного соединения СиВе с ОЦК решеткой. Концентрация а-твердого раствора значительно уменьшается с понижением температуры (с 2,75 % Be при 870°С до 0,2 % при 300 °С). Это дает возможность подвергать бериллиевые бронзы упрочняющей термической обработке — закалке и искусственному старению.
Изменение механических свойств сплавов меди с бериллием (рис. 10.15, б) показывает, что их временное сопротивление резко увеличивается в интервале 1,5 - 2,0 % Be. При содержании бериллия более 2,0 % временное сопротивление повышается незначительно, а пластичность из-за большого количества твердой и хрупкой 7-фазы становится очень низкой.
Наибольшей пластичностью (6 = 30...40%) бериллиевые бронзы обладают после закалки с 770 - 780 °С. В закаленном состоянии они хорошо деформируются. Пластическая деформация на 40% увеличивает временное сопротивление бронзы БрБ2 почти в два раза (с 450 до 850 МПа). Механические свойства бериллиевых бронз достигают очень высоких значений после закалки и старения. Так, БрБ2 после закалки с 780 "С и старения при 300 —350 °С в течение 2 ч имеет следующие; механические свойства: ст„ = 1250 МПа, aUJ --= 1000 МПа, Ь - 2,5%, твердость 700 ПН,
Рис. 10.15. Диаграмма состояния системы Си - Be (а) и влияние бериллия на механические свойства бронз (б)
К 133 ГПа. Упрочнение происходит благодаря распаду пересыщенного о твердого раствора с образованием метастабильнои 7'-фазы, близкой по составу к 7-фазе. Пластическая деформация закаленной бронзы и последующее старение позволяют увеличить временное сопротивление до ИОО МПа.
Бериллиевые бронзы являются теплостойкими материалами, устой мимо работающими при температурах до 310 - 340°С. При 500°С они имеют приблизительно такое же временное сопротивление, как оловянно фосфористые и алюминиевые бронзы при комнатной температуре. Бериллиевые бронзы обладают высокой теплопроводностью и электрической проводимостью; при ударах не образуют искр. Они хорошо обрабатыванием резанием, свариваются точечной и роликовой сваркой, однако широкий температурный интервал кристаллизации затрудняет их дуговую iпарку.
Бериллиевые бронзы выпускают преимущественно в виде полос, лент, проволоки и других деформированных полуфабрикатов. Вместе с тем из них можно получить качественные фасонные отливки. Из бериллиевых орон i изготовляют детали ответственного назначения: упругие элементы ю'шых приборов (плоские пружины, пружинные контакты, мембраны); нмали, работающие на износ (кулачки, шестерни, червячные передачи); полтинники, работающие при высоких скоростях, больших давлениях и in лишенных температурах.
Основным недостатком бериллиевых бронз является их высокая стоимость. Легирование Mg, Ni, Ti, Со позволяет уменьшить содержание бериллия до 1,7 - 1,9% без заметного снижения механических свойств (БрБНТ1,7и др.).
ИЗНОСОСТОЙКИЕ МАТЕРИАЛЫ
Дата добавления: 2018-04-05; просмотров: 2403; Мы поможем в написании вашей работы! |
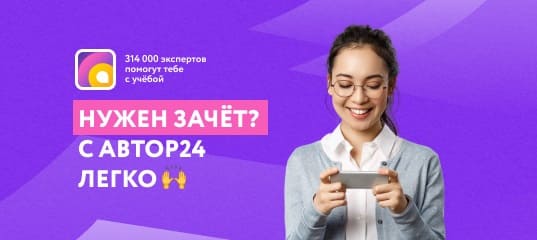
Мы поможем в написании ваших работ!