Термически упрочненных сплавов для упругих
Элементов приборов
Сплав | Содержание элементов*, % | ""0,002 | £-105 | ||||
Be | Ni | Ti | Al | Cr | МПа | ||
БрБ2 БрБНТ1,9 36НХТЮ | 1,8-2,1 1,85-2,1 | 0,2-0,5 0,2-0,4 35-37 | 0,1-0,25 2,7-3,2 | 0,9-1,2 | 11,5-13 | 600 650 800 | 1,28 1,25 2,2 |
* По ГОСТ 18175-78.
Разработаны способы термомеханической обработки бериллиевых бронз, при которой сплавы подвергают холодной пластической деформации в закаленном состоянии. Это приводит к более значительному росту предела упругости при старении и сильному снижению упругого последействия. Так, сплав БрБНТ1,9, деформированный на 50 % в закаленном состоянии, после старения при 350 °С в течение 0,25 ч имеет предел упругости ао,оо2 = Ю00 МПа.
Железоникелевые сплавы (ГОСТ 10994-74) менее дефицитны и дешевле бериллиевых бронз. Они имеют примерно тот же предел упругости, но обладают более высоким модулем упругости, что снижает допустимые упругие деформации элемента.
Сплав 36НХТЮ, применяемый для упругих элементов, является сплавом на железной основе. Высокое содержание никеля и хрома обеспечивает получение аустенитной структуры и способствует высокой коррозионной стойкости. Аустенитная структура придает сплаву хорошие технологические свойства в отношении обрабатываемости давлением и свариваемости. Титан и алюминий образуют с никелем и железом фазы переменной растворимости в аустените, что позволяет упрочнять сплав термической обработкой.
После закалки с 925 - 950 °С сплав приобретает однофазную структуру. В процессе искусственного старения из аустенита выделяется промежуточная метастабильная 7'-фаза, упрочняющая сплав. После старения при 700 °С в течение 2 ч сплав 36ХНТЮ имеет предел упругости о'о^ог = 800 МПа (см. табл. 12.1). Дополнительное легирование молибденом в количестве 8 % (36НХТЮМ8) после термической обработки позволяет получить предел упругости <7о,оо2 = 950 МПа. Применение термомеханической обработки для сплава 36ХНТЮ повышает предел упругости Д° ^0,002 = НЮ МПа.
|
|
Среди сплавов на основе Al, Mg и пластмасс лишь отдельные i рун пы имеют такие свойства, которые указаны в табл. 13.1. Эти материалы предназначены главным образом для изготовления мало- и средненагру-женных деталей.
Материалы с высокой удельной прочностью (сплавы титана и бериллия, композиционные материалы) предназначены в основном для изготовления высоконагруженных деталей. При этом бериллий и его сплавы, а также композиционные материалы, армированные борным и углеродным волокнами, обладают высокой удельной жесткостью.
13.2. Алюминий и его сплавы 13.2.1. Свойства алюминия
Алюминий — металл серебристо-белого цвета. Он не имеет полиморфных превращений и кристаллизуется в решетке ГЦК с периодом а - 0,4041 нм.
|
|
Алюминий обладает малой плотностью, хорошими теплопроводностью и электрической проводимостью (см. § 1.2), высокой пластичностью и коррозионной стойкостью. Примеси ухудшают все эти свойства алюминия.
Постоянные примеси алюминия — Fe, Si, Си, Zn, Ti. В зависимости от содержания примесей первичный алюминий подразделяют на три класса: особой чистоты А999 (< 0,001 % примесей), высокой чистоты А995, А99, А97, А95 (0,005 - 0,05% примесей) и технической чистоты А85, А8 и др. (0,15 - 1 % примесей). Технический алюминий, выпускаемый в виде деформируемого полуфабриката (листы, профили, прутки и др.), маркируют АЛО и АД1. Механические свойства алюминия зависят от его чистоты и состояния. Увеличение содержания примесей и пластическая деформация повышают прочность и твердость алюминия (табл. 13.2).
Ввиду низкой прочности алюминий применяют для ненагруженных деталей и элементов конструкций, когда от материала требуется легкость, свариваемость, пластичность. Так, из него изготовляют рамы, двери, трубопроводы, фольгу, цистерны для перевозки нефти и нефтепродуктов, посуду и др. Благодаря высокой теплопроводности его используют для различных теплообменников, в промышленных и бытовых холодильниках. Высокая электрическая проводимость алюминия способствует его широкому применению для конденсаторов, проводов, кабелей, шин и т.п.
|
|
Следует также отметить высокую отражательную способность алюминия, в связи с чем его используют в прожекторах, рефлекторах, экранах
Таблица 13.2. Механические свойства алюминия
Марка | Сумма примесей, % | Состояние | О-в, МПа | ff0,2, МПа | 5,% | нв |
А 995 | 0,005 | Литое | 50 | - | 45 | 15 |
А5 | 0,5 | VI | 75 | - | 29 | 20 |
АО | 1 | V) Деформированное и | 90 | 25 | 25 | |
отожженное* | 90 | 30 | 30 | 25 | ||
Деформиро- | ||||||
ванное | 140 | 100 | 12 | 32 |
* Отжиг алюминия для снятия наклепа проводят при 350 —
400°С.
телевизоров. Алюминий имеет малое эффективное поперечное сечение за хвата нейтронов, он хорошо обрабатывается давлением, сваривается газо-ной и контактной сваркой, но плохо обрабатывается резанием. Алюминий имеет большую усадку при затвердевании (6 %). Высокие теплота плавления и теплоемкость способствуют медленному остыванию алюминия из жидкого состояния, что дает возможность улучшать отливки из алюминия и его сплавов путем модифицирования, рафинирования и других технологических операций.
|
|
13.2.2. Общая характеристика алюминиевых сплавов
Алюминиевые сплавы характеризуются высокой удельной прочностью, способностью сопротивляться инерционным и динамическим на-1 рузкам, хорошей технологичностью. Временное сопротивление алюминиевых сплавов достигает 500-700 МПа при плотности не более 2,850 г/см3 По удельной прочности некоторые алюминиевые сплавы ((Тп/(рд) = 23 км^ приближаются или соответствуют высокопрочным сталям (<гъ/(рд) = = 27 км). Большинство алюминиевых сплавов имеют хорошую корро 1Ионную стойкость (за исключением сплавов с медью), высокие теилопро водность и электрическую проводимость, хорошие технологические свой < гва (обрабатываются давлением, свариваются точечной сваркой, а специ »льныс сваркой плавлением, в основном хорошо обрабатываются реза иисм).
Рис. 13.1. Диаграмма состояния алюминий - легирующий элемент (схема):
Рис. 13.2. Влияние легирующих элементов на температуру рекристаллизации алюминия |
А - деформируемые сплавы; В - литейные сплавы; /, // - сплавы, неупрочняемые и упрочняемые термической обработкой соответственно
Основными легирующими элементами алюминиевых сплавов являются Си, Mg, Si, Mn, Zn; реже — Li, Ni, Ti. Многие легирующие элементы образуют с алюминием твердые растворы ограниченной переменной растворимости и промежуточные фазы СиА1г, Mg2Si и др. (рис. 13.1). Это дает возможность подвергать сплавы упрочняющей термической обработке, состоящей из закалки на пересыщенный твердый раствор и естественного или искусственного старения.
Легирующие элементы, особенно переходные, повышают температуру рекристаллизации алюминия (рис. 13.2.). При кристаллизации они образуют с алюминием пересыщенные твердые растворы. В процессе гомогенизации и горячей обработки давлением происходит распад твердых растворов с образованием тонкодисперсных частиц интерметаллидных фаз, препятствующих прохождению процессов рекристаллизации и упрочняющих сплавы. Это явление получило название структурного упрочнения, а применительно к прессованным полуфабрикатам — пресс-эффекта. По этой причине некоторые алюминиевые сплавы имеют температуру рекристаллизации выше температуры закалки. Для снятия остаточных напряжений в нагартованных полуфабрикатах (деталях), полученных холодной обработкой давлением, а также в фасонных отливках проводят низкий отжиг. Температура отжига находится в пределах 150 - 300 °С.
Конструкционная прочность алюминиевых сплавов зависит от примесей Fe и Si. Они образуют в сплавах нерастворимые в твердом растворе фазы: Fe.\l;t, о(Л1, Fo, Si), /?(Л1, IV, Si) и др. Независимо от формы
(пластинчатой, игольчатой и т.д.) кристаллы этих фаз снижают иластич пость, вязкость разрушения, сопротивление развитию трещин. Легирова ние сплавов марганцем уменьшает вредное влияние примесей, гак как он связывает их в четверную а-фазу (Al, Fe, Si, Mn), кристаллизующуюся в компактной форме. Однако более эффективным способом повышения конструкционной прочности является снижение содержания примесей с 0,5 - 0,7% (ГОСТ 4784-74) до 0,1 - 0,3% (чистый сплав), а, иногда и до сотых долей процента (сплав повышенной чистоты). В первом случае к марке сплава добавляют букву "ч", например Д16ч, во втором буквы "пч", например В95пч. Особенно значительно повышаются характеристи ки пластичности и вязкости разрушения в направлении, перпендикуляр ном пластическому деформированию. Например, ударная вязкость сплава Д16ч после естественного старения более чем в два раза, а относи тельное удлинение в 1,5 раза выше, чем у сплава Д16 после той же обработки. Так, КХс = 43...46МПа- м1/2 для сплава Д16ч и 35 - ЗбМПа- м1/'2 для сплава Д16. Сплавы повышенной чистоты используют для ответствен ных нагруженных деталей, например, для силовых элементов консгрук ции пассажирских и транспортных самолетов.
Алюминиевые сплавы классифицируют по технологии изготовления, способности к упрочнению термической обработкой и свойствам (рис. 13.3).
13.2.3. Деформируемыеалюминиевые сплавы
К сплавам, неупрочняемым термической обработкой, относятся сила вы АМц и АМг (табл. 13.3). Сплавы отличаются высокой пластичностью, хорошей свариваемостью и высокой коррозионной стойкостью.
Сплавы типа АМц относятся к системе Al-Mn (рис. 13.4, а). Струк i.vpa сплавов типа АМц состоит из а-твердого раствора и вторичных вы мелений фазы МпА1б, переходящих в твердый раствор при повышении к'мпературы. В присутствии железа вместо МпА1б образуется сложная 1 ройная фаза (Мп, Ге)А1б, практически нерастворимая в алюминии, по ному сплавы типа АМц не упрочняются термической обработкой. М отожженном состоянии они обладают высокой пластичностью и низкой прочностью. Пластическая деформация упрочняет эти сплавы почти в '2 раза.
Сплавы чипа АМг относятся к системе Al-Mg (рис. 13.4,6). Мат нии образуем с алюминием а-твердый раствор, концентрация которою при повышении клшературы увеличивается от 1,4 до 17,4 % в резульгам-рлепюрения фазы Mg^Al^. Однако сплавы, содержащие до 7% Mg, дайн
|
|
|
Al 0,05 1 2 Mn, % Al 10 20 Mg, % Л1 10 20 Cu, "'
а б в
Рис. 13.4. Диаграммысостояния:
а А1 Мп; б - к\ - Mg; е А1 Си
очень незначительное упрочнение при термической обработке. Вследствие этого сплавы типа АМг, как и АМц, упрочняют с помощью пластической деформации и используют в нагартованном (ЛмгН — 80 % наклепа) и по-лунагартованном (АмгП — 40 % наклепа) состояниях.
Однако применение наклепа ограничено из-за резкого снижения пластичности сплавов, поэтому их используют в отожженном (мягком -АМгМ) состоянии. Сплавы типа АМц и АМг отжигают при 350-420 °С. При повышении содержания магния временное сопротивление возрастает от 110 МПа (AMrl) до 340 МПа (АМгб) при соответствующем снижении относительного удлинения с 28 до 20 %. Легирование магнием, кроме то го, вызывает склонность к окислению во время планки, разливки и кри сталлизации, что приводит к появлению в структуре оксидных пленок и снижению механических свойств. Поэтому сплавы с высоким содержанием магния (АМгб, АМгЮ) для устранения склонности к окислению легируют бериллием. Укрупнение зерна, вызванное бериллием, устраняется добавкой титана или циркония.
Сплавы тина АМц и АМг применяют для изделий, получаемых глубокой вытяжкой, сваркой, от которых требуется высокая коррозионная стойкость (трубопроводы для бензина и масла, сварные баки), а также для заклепок, переборок, корпусов и мачт судов, лифтов, узлов подъемных кранов, рам вагонов, кузовов автомобилей и др.
К сплавам, упрочняемым термической обработкой, относятся главным образом сплавы нормальной прочности и высокопрочные. Типичны ми представителями являются дуралюмины (маркируют буквой Д). Они характеризуются хорошим сочетанием прочности и пластичности и щ носятся к сплавам системы Al-Cu Mg. Согласно диаграмме гостяния
AI Си (рис. 13.4, в), медь с алюминием образуют твердый раствор, максимальная концентрация меди в котором 5,65 % при эвтектической температуре. С понижением температуры растворимость меди уменьшается, достигая 0,1% при 20 °С. Из твердого раствора при этом выделяется 0-фаза (CuAl2), содержащая ~ 54,1 % Си. Она имеет объемно-центрированную тетрагональную кристаллическую решетку и обладает сравнительно высокой твердостью (530 HV). В сплавах, дополнительно легированных магнием, помимо в образуется еще .У-фаБа (CuMgA^) с ромбической кристаллической решеткой (564 HV). На рис. 13.5
показано влияние соотношения в- и 5-фаз на прочность. Чем больше медисодержится в сплаве, тем большее количество 0-фазы будет в его структуре (Д1).
Увеличение содержания магния приводит к росту количества S-фазы и повышению прочности сплавов (Д16). Разница в свойствах особенно значительна после упрочняющей термической обработки (см. табл. 13.3), состоящей из закалки и естественного старения. При закалке сплавы Д16 и Д18 нагревают до 495 - 505 °С, а Д1 — до 500 - 510 °С, затем охлажда ют в воде при 40 °С. После закалки структура состоит из пересыщенного iверного раствора и нерастворимых фаз, образуемых примесями. При естественном старении происходит образование зон Г - П, богатых медью и магнием. Старение продолжается 5 - 7 сут. Длительность старения шачительно сокращается при увеличении температуры до 40 °С и осо Пенно 100°С. Более высокие значения <тв и (70,2 прессованных прутков объясняются пресс-эффектом. Для упрочнения дуралюминов, как прави ло, применяют закалку с естественным старением, так как в этом случае i плавы обладают лучшей пластичностью и менее чувствительны к кон центраторам напряжений.
Искусственному старению (190°С, 10 ч) подвергают лишь детали, ис пользуемые для работы при повышенных температурах (до 200 °С). Воль шое практическое значение имеет начальный, или «инкубационный», не риод старения (20 60 мин), когда сплав сохраняет высокую пластичность
и низкую твердость. Это позволяет проводить такие технологические операции, как клепка, правка и др. Для проведения подобных операций естественно состаренные сплавы и детали из них можно подвергнуть обработке «на возврат», которая состоит в кратковременной выдержке сплава (1-2 мин) при 230-300 °С. Во время нагрева рассасываются зоны Г - П и восстанавливается пластичность, свойственная сплавам непосредственно после закалки. Однако применение обработки «на возврат» ограничено тем, что у тонкостенных изделий снижается коррозионная стойкость, а у толстостенных за короткое время выдержки не успевает восстанавливаться пластичность по всему сечению. Увеличение выдержки приводит к искусственному старению сплава на поверхности изделия, что вызывает снижение пластичности.
Дуралюмины широко применяют в авиации. Из сплава Д1, например, изготовляют лопасти воздушных винтов; из Д16 — шпангоуты, нервюры, тяги управления и др. Кроме того, их используют для строительных конструкций, кузовов грузовых автомобилей, обсадных труб и др. Сплав Д18 — один из основных заклепочных алюминиевых сплавов. Заклепки из сплава Д18 ставят в конструкцию после закалки и естественного старения.
Ковочные алюминиевые сплавы маркируют буквами АК. Они обладают хорошей пластичностью и стойки к образованию трещин при горячей пластической деформации. По химическому составу сплавы близки к дуралюминам, отличаясь более высоким содержанием кремния. Поэтому в их структуре вместо фазы S присутствуют кремнийсодержащие фазы — четверная фаза (Al, Си, Mg, Si) и /J-фаза (Mg2Si). Ковку и штамповку сплавов ведут при 450 - 475 °С. Их применяют после закалки и искусственного старения. Сплавы с пониженным содержанием меди (АК6) отличаются лучшей технологической пластичностью, но меньшей прочностью (<тв = 360 МПа). Их используют для средненагруженных деталей сложной формы: большие и малые крыльчатки, фитинги, качалки, крепежные детали. Сплавы с повышенным содержанием меди (АК8) хуже обрабатываются давлением, но более прочны и применяются для высоко-нагруженных деталей несложной формы: подмоторные рамы, пояса лонжеронов и др.
Высокопрочные алюмининиевые сплавы маркируют буквой В. Они отличаются высоким временным сопротивлением (600 - 700 МПа) и близким к нему по значению пределом текучести. Высокопрочные сплавы принадлежат к системе Al-Zn-Mg-Cu и содержат добавки марганца и хрома или циркония. Эти элементы, увеличивая неустойчивость твердого раствора, ускоряют его распад, усиливают эффект старения сплава, вызывают пресс-эффект. Цинк, магний и медь образуют Л/-, .V- и '/'-фазы, обладающие переменной растворимостью в алюминии: соответственно MgZnj,
CuMgAl'j и Mg3Zii3Al2. При 480°С эти фазы переходят в твердый раствор, который фиксируется закалкой. При искусственном старении ироис ходит распад пересыщенного твердого раствора с образованием тонкодисперсных частиц метастабильных М'-, Т'- и S'-фаз, вызывающих максимальное упрочнение сплавов. Наибольшее упрочнение вызывают закалка (165 - 475°С) и старение (140°С, 16 ч). После такой обработки сплав И95пч имеет ав = 560 ... 600 МПа; ст0,2 = 480 .. .550 МПа; ё = 9... 12%; К и = ЗОМПа-м1/2; КСТ = 30кДж/м2; твердость — 150 НВ. Подобные сплавы, отличающиеся более высоким содержанием цинка, магния и меди, обладают повышенной прочностью. Так, сплав В96 имеет аъ = 700 МПа; ап2 = 650 МПа; S = 7 %; 190 НВ. Однако после указанной термической обработки сплавы имеют низкие пластичность и вязкость разрушения.
Для повышения этих характеристик сплавы подвергают двухступенчатому смягчающему старению при 100- 120°С, 3 - 10 ч (первая ступень) и 160 - 170°С, 10-30 ч (вторая ступень). Столь высокие температуры и большие выдержки второй ступени старения приводят к образованию и коагуляции стабильных фаз М, S и Т. Предварительное зонное старение (первая ступень) способствует их равномерному распределению, поскольку в сплавах этой системы стабильные фазы образуются из зон Г - П. По-(vie смягчающего старения сплав В95пч имеет ав - 590 .. .540 МПа; ап.г = ■ПО... 470 МПа; 6= 10... 13; КХс = 36 МПа-м1/2; КСТ = 75 кДж/м2.
Сплавы применяют для высоконагруженных деталей конструкций, работающих в основном в условиях напряжения сжатия (обшивка, стрин-к-ры, шпангоуты, лонжероны самолетов).
13.2.4. Литейные алюминиевые сплавы
Химический состав и механические свойства некоторых промышленных литейных сплавов приведены в табл. 13.4. Для литейных алюминиевых сплавов наиболее распространена классификация по химическому составу (Al Si, Al - Си и Al - Mg).
Лучшими литейными свойствами обладают сплавы Al - Si (силумины). Высокая жидкотекучесть, малая усадка, отсутствие или низкая склонность к образованию горячих трещин и хорошая герметичность си туминон объясняются наличием большого количества эвтектики в структуре этих сплавов. В двойных сплавах Al - Si эвтектика состоит из гвер мою раствора и кристаллов практически чистого кремния (рис. 13.6, а), и легированных (АК9ч и др.) помимо двойной имеются тройные и более (.южные )В К'км ики.
|
Плотность большинства силуминов 2650 кг/м3, т.е. меньше плотно сти чистого алюминия (2700 кг/м3). Они хорошо свариваются.
Механические свойства зависят от химического состава, технологии изготовления (модифицирования, способа литья и т.д.), а также терми ческой обработки (см. табл. 13.4). В двойных силуминах с увеличением содержания кремния до эвтектического состава снижается пластичность и повышается прочность. Появление в структуре сплавов крупных кристаллов первичного кремния вызывает снижение прочности и пластичности (рис. 13.7). Несмотря на увеличение растворимости кремния в алюминии от 0,05% при 200°С до 1,65% при эвтектической температуре, двойные < плавы не упрочняются термической обработкой. Это объясняется выг.о кой скоростью распада твердого раствора, который частично происходит уже при закалке, а также большой склонностью к коагуляции стабильных иыделений кремния. Единственным способом повышения механических ( 1юйств этих сплавов является измельчение структуры путем модифици
рования.
Силумины обычно модифицируют натрием, который в виде хлор и г гых и фтористых солей вводят в жидкий сплав в количестве 2 3 % от массы сплава. Помимо модифицирующего действия натрий сдвигает :>н н-ктическую точку в системе Al - Si в сторону больших содержаний крем пия (рис. 13.8). Благодаря этому эвтектический по составу сплав (ЛК12) становится доэвтектическим. В его структуре помимо мелкокристалли ческой эвтектики появляются первичные кристаллы мягкой пластичной фазы твердого раствора (рис. 13.6, б). Все это приводит к увеличению пластичности и прочности (см. рис. 13.7, табл. 13.4).
0 20 40 60 80 100 Рис. 13.8. Диаграмма состояния Al- Si |
Рис. 13.7. Зависимость механических свойств для модифицированного (штриховые линии) и немоди-фицированного (сплошные линии) силумина от содержания кремния
Модифицируют как двойные, так и легированные силумины, содержащие более 5 - 6 % Si. Для легирования силуминов часто используют Mg, Си, Mn, Ti; реже — Ni, Zr, Сг и др. Растворяясь в алюминии, они повышают прочность и твердость силуминов. Кроме того, медь улучшает обрабатываемость резанием, титан оказывает модифицирующее действие. Медь и магний, обладая переменной растворимостью в алюминии, способствуют упрочнению силуминов при термической обработке, как правило, состоящей из закалки и искусственного старения. Температура закалки различных силуминов находится в пределах 515 - 535°С, температура старения — в интервале 150 - 180 °С. Грубокристаллическая структура литейных сплавов требует больших выдержек при нагреве под закалку (5 - 10 ч) и при старении (10 - 20 ч). Переходные металлы, например, Mn, Ti, Zr, способствуют получению пересыщенных твердых растворов при кристаллизации в условиях больших скоростей охлаждения, что вызывает некоторое упрочнение сплавов при старении без предварительной закалки.
Из легированных силуминов средней прочности наибольшее применение в промышленности нашли сплавы с добавками магния (АК7ч), магния и марганца (АК9ч). Наибольшее упрочнение вызывает метастабильная /З'-фаза (Mg2Si).
Легированные силумины применяют для средних и крупных литых деталей ответственного назначения: корпусов компрессора, картеров, головок цилиндров. Высокопрочный сплав ЛК8М, разработанный и МВТУ
им. Н.Э. Баумана, предназначен для литья иод давлением. Сплав облака ет хорошими литейными свойствами, обрабатываемостью резанием, сна риваемостыо и коррозионной стойкостью. Марганец и титан, а также большая скорость кристаллизации при литье под давлением способе гну ют получению метастабильной структуры при отливке деталей. Это да ет возможность упрочнять отливки путем искусственного старения без предварительной закалки. Упрочнение вызывают в- и /3-фазы (CuAl'2 и \lg2Si). Наилучшим является старение при 175°С в течение 8 ч, когда выделяются метастабильные в1- и /З'-фазы; при этом ст„ увеличивается на 30 - 40 МПа, НВ - на 18.
При изготовлении деталей другими методами литья сплав АК8М подвергают полной упрочняющей термической обработке — закалке от 515 ± 5°С и старению при 175 °С.
Сплав АК8М применяют для литья под давлением нагруженных до-талей, например блоков цилиндров, головок блоков и других деталей ан томобильных двигателей.
Сплавы системы А1 - Си (АМ4,5; АМ5) характеризуются высокой прочностью при обычных и повышенных температурах; они хорошо об рабатываются резанием и свариваются. Вместе с тем из-за отсутствия ■жтектики сплавы обладают плохими литейными свойствами, имеют низ кую герметичность. Как и деформируемые сплавы этой системы, они имеют структуру твердого раствора, но отличаются пбвышенным содер жанием меди (см. рис. 13.4, в). Эвтектика в данной системе (в отличие от силуминов) образуется при высоком содержании меди (33%), поэтому имеет большое количество твердой и хрупкой #-фазы (СиА1г), вызываю щей хрупкость эвтектических сплавов.
Литейные и механические свойства сплавов системы А1 Си улучша игтея в результате легирования титаном и марганцем (АМ5). Марганец, образуя пересыщенный твердый раствор при кристаллизации из жидко ю состояния, способствует значительному упрочнению сплава. Во время нагрева сплава под закалку наряду с растворением 0-фазы из твердого раствора выпадают мелкодисперсные частицы фазы А^гМпгСи, увели чивающие прочность при обычных и повышенных температурах. Напри мер, после закалки сплав АМ5 имеет следующие механические свойств;»: пп = 320 МПа; ст0,2 = 180 МПа; 6 = 9%; 80 НВ. При последующем и с кусственном старении происходит дальнейшее упрочнение сплава, вызы маемое уже 0-фазой, так предел текучести увеличивается почти на 40%, достигая 250 МПа. Сплавы системы А1 - Си используют для деталей, работающих при температурах до 300°С.
('плавы системы Al Mg (АМт, АМгШ) обладают высокой коррози онной стойкостью, прочностью, вязкостью и хорошей обрабатываемостью
резанием. Они не содержат в структуре эвтектики по той же причине, что и сплавы системы А1 - Си, и характеризуются невысокими литейными свойствами, пониженной герметичностью и, кроме того, повышенной чувствительностью к примесям Fe, Si, которые образуют в этих сплавах нерастворимые фазы, снижающие пластичность сплавов.
Для того чтобы предотвратить окисление, плавку и разливку двойных сплавов алюминия с магнием АМг необходимо вести под защитными флюсами. Легирование двойных сплавов Be, Ti, Zr не только устраняет их склонность к окислению и росту зерна, но и тормозит естественное старение, вызывающее снижение пластичности и вязкости сплавов. Наилучшие механические свойства сплавы системы Al - Mg приобретают после закалки от 530 °С, когда весь магний находится в твердом растворе.
Сплавы системы Al - Mg применяют для изготовления деталей, работающих в условиях высокой влажности, в судо-, самолето- и ракетостроении. Из них делают детали приборов, вилки шасси и хвостового оперения, штурвалы и др.
Глава 15
Дата добавления: 2018-04-05; просмотров: 648; Мы поможем в написании вашей работы! |
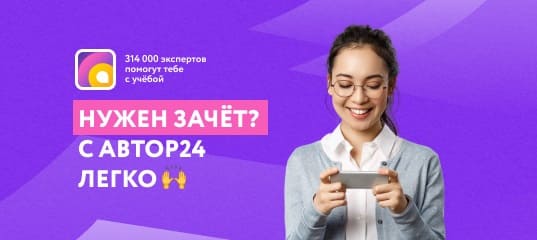
Мы поможем в написании ваших работ!