Коррозионно-стойкие непассивирующиеся
Металлы
В тех случаях, когда обратимый электродный потенциал в заданных условиях коррозии V£5 близок к обратимому потенциалу катодной реакции V0g , коррозионный ток мал и металл обладает высокой коррозионной стойкостью (см. формулу (15.6)).
По этой причине электроположительные металлы Au, Pt, Ag, Си, а также Sn и РЬ, потенциал которых имеет небольшие электроотрицательные значения, обладают коррозионной стойкостью во многих средах.
Так, Au, Pt, Ag стойки к коррозии во всех средах, кроме некоторых концен трированных окисляющих кислот, а Си, Sn, Pb — во влажной атмосфере, морской воде и многих органических кислотах.
Скорости атмосферной коррозии металлов приведены ниже:
Fe Zn Sn Си Ag Au
Кор, мкм/год .... 20,0 3,2 1,2 1,0 0,04 0
Медные сплавы, в состав которых входят электроотрицательные металлы, имеют высокую коррозионную стойкость в условиях равномерной атмосферной и морской коррозии.
Латуни коррозионно-стойки при равномерной коррозии, но склонны к коррозионному растрескиванию во влажной атмосфере (в особенности, при наличии сернистых газов), поэтому после их обработки давлением необходим отжиг для устранения напряжений. При большом содержании цинка латуни подвержены еще одному виду коррозионного разрушения -избирательному поверхностному электрохимическому растворению электроотрицательного цинка.
|
|
15.1.3. Коррозионно-стойкие пассивирующиеся
металлы
Несмотря на большой отрицательный обратимый электродный потенциал металла вследствие большой анодной поляризации Рл в коррозионном элементе устанавливается небольшой коррозионный ток, и металл разрушается с очень малой скоростью (см. формулу (15.6)). Пассивное состояние связывают с образованием на поверхности защитных пленок.
Способностью переходить в пассивное состояние обладают многие промышленные сплавы. Для большинства металлов пассивность наступает в окислительных (кислородсодержащих) средах и даже самопроизвольно на воздухе.
Наибольшей склонностью к самопассивированию на воздухе обладают титан, алюминий и хром. Пассивное состояние в них сохраняются во многих средах, однако оно исчезает в средах, содержащих мало кислорода и много ионов хлора (влажная, плохо аэрируемая почва, морская вода, неокисляющие кислоты).
Титан в пассивированном состоянии по своей коррозионной стойкости уступает только золоту и платине. В отличие от остальных металлов он сохраняет пассивность во влажной атмосфере даже при нагреве, в неокислительных, окислительных и органических кислотах, в морской воде,
476 Глава 15. Материалы, устойчивые к воздействию температуры
|
|
а также в горячих щелочах. Титановые сплавы (см. § 14.1) сохраняют высокую коррозионную стойкость титана.
Алюминий во влажной атмосфере, окислительных и органических кислотах обладает высокой коррозионной стойкостью, что связано с его переходом в пассивное состояние. Однако в щелочах он корродирует с большой скоростью.
Все примеси и легирующие элементы алюминиевых сплавов уменьшают поляризуемость и, тем самым, ухудшают коррозионную стойкость. Наиболее опасны, так как устраняют пассивность, электроположительные металлы. Присутствие железа и меди в десятых долях процента заметно ухудшает коррозионную стойкость алюминия. Сплавы (см. § 13.2), содержащие до 5 % Си, — дуралюмины, высокопрочный сплав с цинком В95, сложные силумины АК8М, жаропрочные сплавы АК4 и другие по коррозионной стойкости значительно уступают чистому алюминию.
Электроотрицательные элементы Si, Mn, Mg не устраняют пассивность алюминия, поэтому простые силумины, не содержащие медь, сохраняют коррозионную стойкость во влажной атмосфере. Марганец оказывает даже положительное влияние, так как, образуя фазу (MnFe)Ale, удаляет железо из твердого раствора и, тем самым, устраняет его вредное действие. Коррозионная стойкость сплава АМц по этой причине даже выше коррозионной стойкости технически чистого алюминия. Магний образует с алюминием анодную фазу Mg2Al3, которая на поверхности сплава быстро растворяется, и поверхность становится однофазной. Это объясняет высокую коррозионную стойкость сплавов АМгб, АМгЮ, которая лишь немного уступает стойкости чистого алюминия.
|
|
Алюминий и его сплавы чувствительны к контактной коррозии. При контакте с более электроположительными металлами (Fe, Ni, Си) алюминий является анодом и разрушается. Алюминиевые сплавы, легированные медью, подвержены МКК. Для защиты от такой коррозии сплавы дополнительно легируют магнием, а листовые полуфабрикаты плакируют чистым алюминием.
15.1.4. Коррозионно-стойкие стали
Коррозионно-стойкие стали являются высоколегированными и содержат не менее 13 % Сг, что обеспечивает образование на поверхности металла пассивирующей защитной пленки.
Их разделяют на классы в зависимости от структуры, которая образуется после высокотемпературного патрона и охлаждения на воздухе (рис. 15.3): мартеноитный, маргенеитип-форри гный (при содоржа-
Рис. 15.3. Зависимость структуры коррозионно-стойких сталей от их химического состава
|
|
нии феррита не менее 10%), ферритный, аустенито-ферритный (при со держании феррита не менее 10 %), аустенитный и аустенитно-мартенеит ный (ГОСТ 5632-72). Суммарное влияние феррито- и аустенитообразую щих элементов характеризуют эквиваленты хрома Сгэкв и никеля Ni)KII:
Сгэкв = Сг + 2Si + 1,5Мо + 5V + 5,5А1 + l,75Nb + l,5Ti + 0,75W; Ni3KB = Ni + 0,5Mn + 30C + 30N + 0,3Cu,
где символы легирующих элементов обозначают их массовые доли в дан мой марке стали, а числа — коэффициенты активности.
В настоящее время разработано несколько групп высокоазотистых коррозионно-стойких сталей с низким содержанием углерода.
Повышение прочности и снижение стоимости коррозионно-стойких сталей наиболее эффективно достигается путем использования азота в ка чостве легирующего элемента.
Азот доступный практически в неограниченном количестве из воз ;уха легирующий элемент — отличается повышенной аустснитообразу к)щей и упрочняющей способностью. Он эффективно заменяет никель и, являясь, как и углерод, элементом внедрения, интенсивно упрочняет паль. Использование азота в качестве легирующего элемента сдержива лось трудностью введения его в сталь ввиду малой (0,045% (мае.)) рас пюримости в жидком железо. Кроме того, азот улетучивается из стали при термической обработке и сварке.
В настоящее время разработаны промышленные способы введения азота в жидкую сталь, что привело к созданию нового перспективного класса высокоазотистых сталей, отличающихся высокими прочностью и коррозионной стойкостью. Для введения азота необходимо большое давление и наличие в стали нитридообразующих элементов (Ti, Nb, V, Сг, Мп). Сталь выплавляют в индукционной печи и раскисляют. После этого ковш с готовой сталью помещают в специальную установку, в которой создают давление газообразного азота до 10 МПа. На поверхности стали молекулы азота диссоциируют, атомарный азот растворяется и диффундирует в жидкую сталь. Процесс кристаллизации идет при высоком давлении, масса получаемых слитков — до 2 т.
Растворимость азота в жидкой стали значительно увеличивает хром — необходимый элемент коррозионно-стойких сталей. Кроме того, хром связывает азот в прочные нитриды CrN и C^N, имеющие высокую (до 1200 °С) термическую стабильность. Оба эти фактора обусловили возможность сверхравновесных (1,0 - 1,3%) концентраций азота именно в коррозионно-стойких сталях. В обычных конструкционных коррозионно-стойких сталях содержание азота составляет 0,15 - 0,25 %.
Аустенитные стали
Это наиболее важный класс коррозионно-стойких сталей по масштабам использования и универсальности применения. По химическому составу эти стали разделяют на хромоникелевые и хромомарганцевые стали (табл. 15.1).
Преимуществами аустенитных сталей кроме коррозионной стойкости являются высокая пластичность и вязкость. Изделия, включая тонкую ленту и фольгу, легко получают всеми способами пластического деформирования; стали имеют хороший комплекс литейных свойств и свариваемость. Исключением является обработка резанием — стали обрабатываются хуже углеродистых и низколегированных из-за высокой пластичности и упрочнения при резании. Сталь 12Х18Н10Е с добавкой 0,18 - 0,36 % Se является автоматной.
К недостаткам аустенитных сталей относят низкие значения предела текучести, а также подверженность опасным видам местной коррозии — коррозионному растрескиванию и МКК.
Структура аустенита обеспечивается при определенном соотношении между феррито- и аустенитообразующими элементами. Так, у хромони-келеных сталей достаточно иметь 9 - 11 % Ni при 17 19% Сг; у хромо-марганцевых сталей из-за пониженной аустенигообра зующей активности .
Таблица 15.1. Химический состав аустенитных сталей, %
Марка стали | С* | Сг | Мп | Ni | N | Прочие элементы |
12Х18Н9 | 0,12 | 17-19 | <2 | 8-10 | - | -- |
12Х18Н10Т | 0,12 | 17-19 | <2 | 9-11 | - | (5C-0f8)Ti |
08Х18Н12Б | 0,08 | 17-19 | < 2 | 11-13 | - | (10C-l,l)Nb |
10Х17Н13МЗТ | 0,10 | 16-18 | <2 | 12-14 | (2-3)Мо (5C-0,7)Ti | |
10Х14АГ15 | 0,10 | 13-15 | 14,5-16,5 | - | 0,15-0,25 | - |
10Х14Г14Н4Т | 0,10 | 13-15 | 13-15 | 2,8-4,5 | - | >5(C-0,02)Ti |
03Х13АГ19 | 0,03 | 12-15 | 19-22 | 1,0 | 0,05-0,10 | - |
*Не более.
марганца необходимо дополнительное легирование никелем (до 4 - 5 %) и азотом (до 0,5%) или одновременно обоими элементами при увеличении содержания хрома до 20 %.
Оптимальной термической обработкой для всех аустенитных сталей является закалка с 1050 — 1150°С в воде (или на воздухе для тонких сечений толщиной 5... 10 мм). После закалки механические свойства характеризуются максимальной пластичностью и вязкостью, невысокими прочностью и твердостью. Механические свойства хромоникелевых сталей следующие: ав = 500 ... 550 МПа, ст0,2 = 150 ... 240 МПа, ё = 40 ... 60 %; KCU = 2 ... 3 МДж/м2, твердость около 200 - 250 НВ. Хромомарганцевые стали несколько прочнее: ав = 600 ... 800 МПа, его,2 = 240 ... 400 МПа.
При холодном деформировании аустенитные стали интенсивно наклёпываются: достаточно 20% деформации, чтобы предел текучести повысился более чем в 3 раза по сравнению с исходным значением. После деформирования на 70 % и выше ав увеличивается в 2 - 3 раза, а сто,2 и 5 6 раз и тем не менее пластичность наклепанных сталей сохраняется на уровне <5 = 8 ... 12 %. При деформировании сталей с неустойчивым ау< тенитом наблюдаются изменения фазового состава: у хромоникелевых сталей образуется мартенсит деформации а' с ОЦК структурой, у хромо-марганцевых два разных мартенсита: а' и е с гексагональной структурой. Количество мартенсита может составить 40-50% (об.), когда сталь деформируют при криогенных температурах (-196°С) с большими цеформациями. Аустенитные стали с устойчивым аустенитом содержат > 15% Ni, при деформировании они наклёпываются без образования мар теней та.
|
После закалки аустенитные стали с однофазной аустенитной структурой проявляют максимальную коррозионную стойкость в большинстве агрессивных сред. Исключение составляют соляно-кислые и серно-кислые растворы с ионами С1_ и SO^ , которые разрушают защитную пассивирующую пленку в особенности при нагреве.
Недостатком аустенитных сталей является восприимчивость к опасным видам местной коррозии — МКК, коррозионному растрескиванию и точечной коррозии.
Причиной МКК является электрохимическая неоднородность пограничных участков по сравнению с самими зернами. Из-за этой неоднородности пограничные участки являются анодами и быстро подвергаются коррозионному разрушению.
В аустенитных сталях, содержащих 17 - 19 % Сг, обедненный хромом слой образуется на границах зерен в интервале 450 — 700 °С. Приэтих температурах диффузионная подвижность атомов углерода велика, а хрома мала. Закаленный аустенит является пересыщенным по отношению к углероду; в нем содержится 0,08 - 0,12% С, а его растворимость при 20 - 25 °С достигает лишь 0,03 %. Нагрев до 450 - 700 °С даже в течение нескольких минут сопровождается выделением избытка углерода в виде МегзСб и появлением обедненного хромом слоя (рис. 15.4).
Для предупреждения МКК аустенитные стали дополнительно легируют титаном или ниобием. Каждый элемент активно связывает углерод в прочный карбид МеС, и для образования карбида МегзСб углерода не остается. Стали, содержащие титан или ниобий, называются стабилизированными, их применяют для сварных конструкций, не опасаясь, что зона термического влияния потеряет стойкость против МКК. При устранении обедненного хромом слоя после повторной закалки или стабилизирующего отжига при 850 °С с выдержкой не менее 3 ч, достаточного для диффузионного выравнивания содержания хрома в этом слое и в зернах, стойкость против МКК восстанавливается.
Рис. 15.4. Схема структуры аусто-нитной стали 12Х18НЮ в состоянии, восприимчивом к МКК:
1 - зерно аустенита; 2 - выделения С г?]('в; 3 обедненный хромом слой
Ayeтенитиыс стали с содержанием не более 0,03 % С не восприимчивы к МКК. Однако даже у них после длительной эксплуатации при 500 (>()()"С теряется стойкость против МКК из за увеличения концентрации примесей на границах аустенитных зерен. Опасным является содержание свыше 0,01 % I», 0,1 % Si, а также 0,001 % В.
Разновидностью МКК является ножевая коррозия сварных соединений, когда основной металл разрушается на узких полосках шириной около 0,1 мм по обе стороны от металла шва. Она связана с растворением карбида МеС в самой горячей зоне основного металла и выделением карбида хрома СггзСб в этой зоне при охлаждении сварного соединения. Понижение содержания углерода в стали затрудняет развитие этого вида коррозии. Лучшей стойкостью против ножевой коррозии обладает сталь 08Х18Н12Б.
Хромомарганцевые стали, содержащие азот, нельзя легировать титаном или ниобием для защиты от МКК. Оба элемента в первую очередь будут взаимодействовать с азотом, образуя нитриды. В этих сталях для повышения стойкости против МКК уменьшают содержание углерода до 0,03%.
Коррозионное растрескивание появляется в результате одновременного действия активной среды и растягивающих напряжений. Коррозионные трещины в металле возникают без заметной макропластической деформации, когда напряжение больше критического (<тКр = 0,5(70^) и в активной среде содержится активатор, разрушающий пассивное состояние металла. Для коррозионно-стойких сталей с хромом активатором являются ионы С1~. Кроме аустенитных сталей типа 12Х18Н10Т коррозионному растрескиванию подвержены мартенситные стали после закалки и низкого отпуска и аустенитно-мартенситные стали после обработки на максимальную прочность. Повышение концентрации никеля в аустенитных сталях увеличивает сопротивление растрескиванию, начиная с 30 - 40 % Ni стали становятся стойкими к этому виду коррозии.
Точечная (питтинг) и щелевая коррозия имеют сходные механизмы коррозионного разрушения: нарушается сплошность защитной пленки и и электролите не хватает кислорода для ее восстановления. Развитию коррозии способствует повышенная (начиная с 0,1 %) концентрация ионов С1~. Типичной средой для развития точечной коррозии является морская иода. Нагрев электролита ускоряет коррозию, ее скорость максимальна при температуре около 80°С и более чем в 100 раз больше скорости равномерной коррозии. В результате разрушения на поверхности металла появляются ямки глубиной и диаметром несколько миллиметров. Струк гурная и химическая неоднородность стали — выпадение карбидов из
II' M.irrpii........... '.."».'
аустенита, образование мартенсита, загрязнение неметаллическими включениями, наклеп и т.д. способствуют коррозии. Шероховатость поверхности (Да > 1,5 мкм) также ускоряет коррозию. Щелевая коррозия развивается в узких зазорах, в местах отслаивания защитных покрытий, под шайбами при слабой затяжке крепежных деталей, в тупиковых зонах из-за неудачной конструкции деталей или ошибок сборки.
В аустенитных сталях стойкость против точечной коррозии повышают дополнительным легированием (2 - 3 %) Мо, уменьшением шероховатости поверхности, повышением структурной и химической однородности.
Особую группу образуют безникелевые стали с аустенитной структурой, содержащие 18 - 24 % Сг и 1,0 - 1,3 % N (05Х18А120, 05Х21А120, 05Х24А120). Эти стали подвергают закалке с 1200 °С, которая обеспечивает практически полное растворение нитридов при сохранении мелкозернистой структуры, и отпуску при 400 °С для уменьшения закалочных напряжений. При закалке достигается максимальное пересыщение азотом аустенита и, как следствие, наибольшее твердорастворное упрочнение. Стали сочетают высокую прочность (ств = 1140... 1250 МПа; сй,2 = 840.. .915 МПа) с высокой пластичностью (<5 = 48... 30%). Но уровню предела текучести эти стали в 3 - 4 раза превосходят хромони-келевую сталь 08Х18Н10. Дополнительно прочностные свойства можно повысить холодным пластическим деформированием со степенью обжатия до 50 %. Упрочнение достигается вследствие наклепа аустенита (без образования мартенсита). Однофазная аустенитная структура (сохраняется при нагреве до 500 °С) и высокая концентрация хрома в твердом растворе обеспечивают высокую коррозионную стойкость этих сталей.
Аустенитно-ферритные стали
Эти стали (078Х22Н6Т, 08Х21Н6М5Т, 08Х18Г8Н2Т) имеют оптимальный комплекс свойств при практически равном содержании аустенита и феррита, которое обеспечивается закалкой с 1000 ... 1100 °С. Эти стали дешевле аустенитных, так как содержат меньше никеля, прочнее их в 1,5 - 2 раза и имеют почти такое же сопротивление коррозии, как сталь 12Х18Н10Т. Во избежание МКК эти стали стабилизируют титаном. Изделия из аустенитно-ферритных сталей рекомендуется эксплуатировать при температурах не выше 350°С во избежание охрупчивания из-за структурных изменений.
Аустенитно-мартенситные стали
Но сравнению с аустенитными эти стали (07Х16Н6; 09Х15Н9Ю, 08Х17Н5МЗ) имеют высокую прочность, которая достигается сложной термической обработкой, включающей закалку для получения аустенита, обработку холодом при 70°С для превращения аустенита в мартенсит и старения мартенсита при 350 - 500°С. Обработка холодом может быть заменена пластическим деформированием, во время которого значительная часть аустенита превращается в мартенсит. Химический состав сталей отличается малым содержанием углерода (< 0,1 %), пониженным количеством никеля (5 - 8 %) и добавками Al, Ti, Си, Мо для упрочнения мартенсита при старении. При 70 - 90 % (об.) мартенсита стали имеют (70,2 = 700 ... 1000 МПа, <тв = 1100 ... 1400 МПа. При таком уровне прочности эти стали особенно склонны к коррозионному растрескиванию. Для защиты от этого вида коррозии старение рекомендуется прервать на стадии образования зон Г - П, не достигая максимума прочности. Особенностью этих сталей является стабилизация аустенита закаленной стали в течение нескольких часов при -20... + 100°С. После стабилизации при обработке холодом образуется меньше мартенсита. Чем больше непревра-щенного аустенита содержится в аустенитно-мартенситных сталях, тем выше их ударная вязкость.
Ферритные стали
Эти стали (08X13, 12X17, 08Х17Т, 15Х25Т, 15X28) не имеют фазового превращения -у^-a и не упрочняются термической обработкой. Они содержат 0,08 - 0,15 % С и 13 - 30 % Сг (табл. 15.2). Чем больше хрома в стали, тем выше ее сопротивление коррозии. Так, стали, содержащие 25 - 28 % Сг, коррозионно-стойки в кипящих растворах 40 %-й и более HNO3. Стали с концентрацией хрома 25 - 28 % в горячих растворах щелочей имеют лучшую стойкость, чем стали типа 12Х18Н10Т. После отжига они характеризуются умеренной прочностью и пластичностью (ств = 400 .. .500 МПа, (70,2 = 250 .. .300 МПа, 6 = 12... 20%), уступая аустенитным сталям по комплексу механических свойств и превосходя их только по сопротивлению коррозионному растрескиванию.
По техническим свойствам ферритные стали хуже аустенитных. Главный их недостаток — резкое охрупчивание после нагрева выше 1000 - 1100°С. Это затрудняет сварку ферритных сталей, так как для частичного уменьшения хрупкости сварные соединения должны подвергаться отжигу при 750 — 800°С. По завершении отжига требуется ускоренное охлаждение, чтобы не допусти п. охрупчивание.
|
Ферри гные слали после высоко температурного нагрева подвержены МКК. Проверка стойкости против МКК предусмотрена только для сталей 08X17Т и 15Х25Т. Перед испытанием их образцы подвергают провоцирующему отжигу при 1080- 1120°С в течение 30 мин (для большинства аустенитных сталей его проводят при 640 - 690°С с выдержкой 60 мин). Склонность к охрупчиванию ферритных сталей ограничивает их применение несмотря на меньшую стоимость по сравнению с аустенитны-ми сталями.
Мартенситные стали
Эти стали (20X13, 30X13, 40X13, 20Х17Н2, 95X18) используют для деталей и инструментов, подвергающихся воздействию слабоагрессивных сред: воды, атмосферы, разбавленных растворов кислот и солей и т.д. Структура отожженных сталей представляет собой легированный феррит с частицами карбида хрома. Отожженные стали имеют удовлетворительную стойкость против коррозии, но их прочность невысока (для 30X13 и 10X13 егв = 500 .. .540 МПа). Прочность увеличивается после закалки и отпуска. Закалку проводят с 1050 - 1100 °С для растворения карбида хрома. Изделия после закалки (нормализации для тонких сечений) подвергают либо низкому (200 - 400 °С), либо высокому (600 - 700°С) отпуску. Максимальное сопротивление коррозии стали имеют после низкого отпуска, пониженное, но тем не менее достаточно высокое — после высокого отпуска. Шлифование и полирование поверхности дополнительно повышают стойкость изделий. Отпуск при 400 - 600°С резко снижает сопротивление коррозии и поэтому не применяется.
После закалки и высокого отпуска стали, содержащие 13 % Сг, имеют пи2 = 500 ... 725 МПа, ств - 700 ... 950 МПа, 6 = 20 ... 14 %, а у наиболее прочной стали 20Х17Н2 ст0,2 = 900 ... 1050 МПа, <тв = 1000 ... 1400 МПа, Л 18 ... 15 %. Сталь 95X18 является износостойкой подшипниковой, после закалки и низкого отпуска она характеризуется высокой твердостью О 59 lIItQ,).
Мартенситные стали после отжига удовлетворительно обрабатываются резанием, горячая обработка давлением и сварка этих сталей за-|руднены из-за образования мартенсита.
1! азотсодержащих сталях мартенситного класса соотношение между ,ivc 1ени тообразующими никелем, углеродом, азотом и ферритообразую-щим хромом требует невысокого (равновесного) содержания азота. Пред tianHHMcM -пой труппы является cia:n. 05Х16Н4ЛВ, содержащая 0,10 0,15 'А N. Для обеспечения мел козернис i ой структуры в нее введен ниобий
(0,08 %), который образует труднорастворимые частицы нитридов и карбидов. Сталь подвергают закалке с 1000°С и отпуску при 400 °С, вызывающему дисперсионное твердение мартенсита за счет выделения мелких и равномерно распределенных частиц нитридов. Нитриды в отличие от карбидов выводят из раствора значительно меньше хрома, поэтому сталь при высокой прочности (<гв = 1550 МПа; <70)2 - 1365 МПа) и повышенной пластичности (6 = 20 %) обладает высокой коррозионной стойкостью.
15.1.5. Коррозионно-стойкие покрытия
Металлические и неметаллические коррозионно-стойкие покрытия являются распространенным средством повышения долговечности изделий при работе в коррозионной среде.
Металлические покрытия по механизму своего влияния делят на катодные и анодные.
Катодные покрытия изготовляют из более электроположительного металла; они экранируют анодные участки металла и повышают электродный потенциал поверхности. Вследствие высокой коррозионной стойкости эти покрытия долговечны, но не выносят механических повреждений. Если есть царапины, то основной металл при наличии покрытия второго катода корродирует быстрее, нежели без покрытия.
Покрытия свинцом или оловом (лужение) для железа и низкоуглеродистой стали являются катодными. Свинец и олово более электроположительные металлы, чем железо в атмосфере воздуха, неорганических и органических неокисляющих кислотах. Луженую сталь применяют в пищевой промышленности, а покрытие свинцом — в химической промышленности.
Анодные покрытия изготовляют из более электроотрицательного металла. Разрушаясь, он предохраняет металл от коррозии. При механических повреждениях такое покрытие выполняет роль дополнительного более электроотрицательного анода, который забирает большую долю коррозионного тока и тем самым защищает основной анод. Анодные покрытия применяют при атмосферной и морской коррозии. Например, анодными для железа и углеродистых сталей являются покрытия цинком или кадмием.
Неметаллические покрытия представляют собой вещества с ионным или молекулярным типом связи, являющимися по своим электрическим свойствам диэлектриками или полупроводниками. Вследствие большого омического сопротивления электрохимическая коррозия в них не развивается (см. формулу (15.6)). Ионным типом связи обладают покрытия
из оксидов, создаваемые на сталях при нагреве на воздухе, или при ано дировании алюминия. Высокомолекулярные соединения входят в состав лаковых покрытий, а также совместно с оксидами в состав красок и эма лей.
Неметаллические высокомолекулярные покрытия во многих случаях легко отслаиваются и разрушаются при относительно небольших нагрузках. В некоторых случаях предпочитают изготовлять детали и элементы конструкций целиком из полимеров и пластмасс, что обеспечивает конструкции долговечность в эксплуатации.
15.2. Жаростойкие материалы
Конструкционные металлические материалы в процессе обработки и эксплуатации при нагреве в коррозионно-активных средах подвергаются химической коррозии и разрушению.
15.2.1. Химическая коррозия металлов
Химическая коррозия развивается в сухих газах или жидких неэлектролитах. В большинстве случаев это кислородсодержащие газы: сухой воздух, углекислый газ, сухой водяной пар и чистый кислород. Известны также сернистая и сероводородная коррозии.
Движущей силой химической коррозии является термодинамическая неустойчивость металлов в газовых средах при определенных давлении, температуре, активности газовой среды.
Способность металла сопротивляться коррозионному воздействию газа при высоких температурах называют жаростойкостью.
Чаще всего поверхность металла окисляется. При невысоких температурах (около 20 - 25 °С) на поверхности металла образуются тонкие оксидные пленки, называемые природными. Несмотря на малую толщину (3 - 10 нм), они обладают очень хорошими защитными свойствами. Эти невидимые глазом плотные пленки покрывают поверхность металла сплошным слоем. Кристаллическая решетка таких оксидов подобна решетке металла. Однако большинство РЗМ окисляется при 20 - 25 °С целиком, и природные оксидные пленки эти металлы от окисления не защищают.
При нагреве растет толщина оксида и изменяется его кристаллическая структура: решетка оксида, по мере удаления от поверхности металла все больше приближается к решетке компактного оксида. Защитные свойства толстых оксидных пленок, образующихся при высоких температурах, определяются способностью оксидного слоя целиком покрывать
поверхность металла и проницаемостью самого оксида для ионов металла и кислорода.
Защитные свойства оксидного слоя характеризуют коэффициент объема ip, равный отношению атомных масс МеО и Me. При <р — 1.. .2,5 оксидный слой является плотным; при <р < 1 образуются рыхлые пленки, не закрывающие доступ кислорода к металлу, а при <р > 2,5 оксидная пленка растрескивается и осыпается под действием напряжений из-за большой разницы удельных объемов оксида и металла. В последнем случае также наблюдается плохая жаростойкость.
Защитные свойства плотной оксидной пленки (у = 1.. .2,5) зависят от диффузионной подвижности ионов металла и кислорода. Недостаток ионов металла или кислорода в узлах решетки оксида, так же как и избыток ионов металла между узлами, занятыми ионами кислорода, ускоряют диффузию и уменьшают защитные свойства оксида. Легирование элементами с большей активностью к кислороду, чем основной металл, сопровождается при окислении накапливанием ионов этих элементов в оксидном слое, уменьшением дефектности кристаллической решетки и повышением защитных свойств оксидной пленки. При достаточно высокой концентрации легирующих элементов меняется даже кристаллическая решетка оксидного слоя. Например, в хромистых сталях начиная с 13 % Сг вместо оксида FeO образуется шпинель МеО ■ МегОз- У жаростойких сталей, содержащих 25 - 30 % Сг, и у самого хрома жаростойкость улучшается при дополнительном легировании 1 % Y.
Скорость окисления оценивают по скорости изменения массы металла (г/(м2-ч)) или толщины оксидной пленки (мкм/ч).
Температурные зависимости скорости окисления металла определяют экспериментально в условиях, максимально приближенных к эксплуатационным. По ним оценивают жаростойкость металла и максимальную рабочую температуру.
Жаростойкость металлов
Сравнительная оценка жаростойкости чистых металлов по скорости окисления на воздухе в интервале допустимых рабочих температур приведена в табл. 15.3.
Очень плохая жаростойкость магния при температурах выше 450 °С связана с образованием рыхлого оксида MgO, у которого коэффициент объема <р — 0,79. В интервале 500 - 600 °С скорость окисления магния лежит в пределах Ю-1 - 101 г/(м2 • ч).
Металлы Nb, Та, Mo, W имеют плотные оксиды, но их защитные свойства ухудшаются при нагреве выше 550°С. Это объясняется том,
Металл |
Mg Nb, Та, Mo, W, Ti, Zr Cu, Fe, Ni, Co |
Л1, Zn, Sn, Pb, Cr, Mn, Be Ag, Au, Pt |
Таблица 15.Я. Жаростойкость чистых метнлло
Жпрсн тойкос гь | Определяющий фак'шр |
Очень плохая | Рыхлые оксиды |
Плохая | Плотные оксиды с плохими |
защитными свойствами | |
Удовлетворительная | Плотные оксиды с |
большой дефектностью | |
Хорошая | Плотные оксиды с хорошими |
защитными свойствами | |
Отличная | Малое химическое сродство |
к кислороду |
что у них ip > 2,5, поэтому возникают большие напряжения, вызывающие растрескивание оксидов. Кроме того, оксид молибдена при нагреве испаряется. Оксиды титана и циркония, образующиеся при нагреве, теряют кислород вследствие его большой растворимости в металле и не защищают от дальнейшего окисления. Это явление называют деградацией оксида. При высоких температурах и длительных выдержках оксид становится даже рыхлым. Для тугоплавких металлов скорости окисления на воздухе в интервале 700 - 800°С лежат в пределах 101 - 103 г/(м2 • ч).
Металлы Си, Fe, Ni, Со (см. табл. 15.3) в интервале 500 - 600 "С окисляются на воздухе со скоростью от 10~3 до Ю-1 г/(м2 -ч), а в интернале 700 - 800 °С — от 101 до 1 г/(м2-ч). Относительно высокие скорости окисления у этих металлов связывают с большой дефектностью образую щихся при нагреве оксидов.
В процессе окисления желе->а и стали на поверхности растут несколько оксидов, у которых химический состав, кристаллическая структура и защитные свойства различны.
107 7. К |
Рис. 15.5. Влияние температуры на скорость окисления Am железа на воздухе |
Температурная зависимость скорости окисления железа на воздухе отражает изменения состава и структуры образующихся на поверхности оксидов (рис. 15.5). До 560"С окисление идет медленнее,
так как на поверхности образуются оксиды FC3O4 и КегОз с хорошими за щитными свойствами. При дальнейшем нагреве единственным защитным оксидом становится FeO с худшими защитными свойствами, чем у КезС>4 и ГегОз- Именно по этой причине предельно допустимая рабочая температура нагрева на воздухе для чистого железа составляет 560 °С. Благодаря легированию эту температуру удается повысить до 1000 — 1200 °С.
Металлы Al, Zn, Sn, Pb, Сг, Mn, Be (см. табл. 15.3) обладают хорошей жаростойкостью. Скорость окисления хрома на воздухе в интервале 400 - 600 °С менее 10~6г/(м2 • ч), а в интервале 700 - 800°С составляет 10~4- 10~3г/(м2 -ч).
Жаростойкость сплавов
Жаростойкость промышленных медных сплавов — латуней и бронз — выше жаростойкости чистой меди. Легирующие элементы в медных сплавах (см. табл. 15.3) имеют большее химическое сродство к кислороду, чем медь, и при достаточном их количестве образуют при нагреве собственные оксиды, обладающие лучшими защитными свойствами, чем Сиг О. Сплавы меди с бериллием, алюминием, марганцем отличаются высокой жаростойкостью; несколько уступают им сплавы меди с цинком, оловом и кремнием.
Титановые и циркониевые сплавы поглощают кислород, поэтому защитные оксиды на поверхности не образуются и жаростойкость титана при легировании не улучшается. Повысить жаростойкость удается лишь применением жаростойких покрытий.
Жаростойкость железа и сталей повышают легированием хромом, алюминием и кремнием. Наибольшее распространение при объемном и поверхностном легировании железа и сталей получил хром, содержание которого доходит до 30 %. С увеличением количества хрома в стали, а также с ростом температуры и выдержки содержание хрома в оксиде возрастает. Легированные оксиды железа заменяются оксидами хрома, что ведет к повышению жаростойкости.
Жаростойкими являются высоколегированные хромистые стали фер-ритного и мартенситного класса, хромоникелевые и хромомарганцевые стали аустенитного класса. Чем больше хрома содержит сталь, тем выше максимальная температура ее применения и больше срок эксплуатации изделий. Жаростойкость определяется главным образом химическим составом стали (т.е. содержанием хрома) и сравнительно мало зависит от ее структуры.
Дополни юлыюо легирование жаростйких с i алой кромпиом (до 2 \\%) и алюминием (до 1 2% и сталях и до I 5% и спламах с высоким >лок гричоским сопротивлением) повышаем температуру эксплуатации.
Низкоуглеродистая сталь при большом содержании хрома ириобро i но г однофазную ферритную структуру. И процессе длительной работы при мысоких температурах кристаллы феррита, растут, что соироножда о гея понижением ударной вязкости. Для предотвращения охрупчивания сталь дополнительно легируют карПидообразующими элементами (например, Ti). Карбиды затрудняют рост зерна феррита. Химический состав и свойства некоторых жаростойких сталей приведены в табл. 15.1.
Таблица 15.4- Химический состав (ГОСТ 5632 72) и механические свойства жаростойких сталей
Марка | Содержание элементов, % |
| ||||
С | С г | N4 | Si | <тв, МНа | 6,% | |
(ЖХ17Т* 15X28* 20X231118** 20Х25Н20С2** | < 0,08 < 0, 15 < U, 2 < 0,2 | 16 - 18 27 29 22 - 25 24 - 27 | 0,7 0,8 17-20 18-21 | 0,8 1 1 2-3 | 400 450 500 600 | 20 20 35 35 |
II римечание. Сплав 08X17Т содержит также 0,4 - 0,8 Ti.
'Свойства приведены в отожженном состоянии. " То же в закаленном.
Следует отметить, что стали 08Х17Т и 15Х25Т ферритного класса (в структуре преобладает феррит) нежаропрочпы, поэтому их используют в изделиях, которые не испытывают больших нагрузок, особенно ударных. Сплавы 20Х23Ш8 и 20Х25Н20С2 аустенитного класса не только жаро стйки, но и жаропрочны. Области применения жаростойких сталей и «плавов указаны в табл. 15.5.
15 жаростойких сталях содержание алюминия и кремния ограничено, 1ак как эти элементы охрупчивают сталь и ухудшают технологические 1 войства при обработке давлением. Этот недостаток можно исключить, если использовать их при поверхностном легировании. Жаростойкие cia ли XI3I01 и Х23Ю5Т, легированные хромом и алюминием, так же как и «плав X20I180, используют как материалы с повышенным электрическим гопротивлонием.
Низкая жаросюйкость тугоплавких металлов Mo, W, Та, ХЬ созда ei большие затруднении при использовании их в качестве жаропрочных маюриалов. Применение вакуума и защитных сред при технологической обработке и эксплуатации тугоплавких металлов вызывает в некоторых
Таблица 15.5. Жаростойкие стали и сплавы, применяемые в электропечах
Марка | Рабочая температура, °С | Назначение | |
Х13Ю4 | 900 | -950 | Электронагреватели печей |
Х23Ю5Т | 1350 | -1400 | То же |
Х20Н80 | 1050 | -1100 | » |
15Х25Т | 800- | 1000 | Малонагруженные детали печей |
20Х23Н18 | 800- | 1000 | Муфели, направляющие, детали вентиляторов, конвейеров и рольгангов печей |
20Х25Н20С2 | 950- | 1050 | Муфели, ролики рольгангов, подовые плиты и другие детали печей, работающие в углеродсодержащей атмосфере |
случаях большие технические трудности. Объемное легирование этих металлов не приводит к повышению жаростойкости, хотя для повышения жаропрочности оно может быть эффективным. Высокой жаростойкости можно добиться, используя жаростойкие тугоплавкие покрытия.
15.3. Жаропрочные материалы 15.3.1. Критерии жаропрочности материалов
Жаропрочностью называется способность материала длительное время сопротивляться деформированию и разрушению, когда рабочие температуры деталей превышают 0,3 tnJl. Многие детали современных паросиловых установок, металлургических печей, двигателей внутреннего сгорания, газовых турбин и других машин нагреваются до высоких температур и несут большие нагрузки.
Решающее значение при выборе материала имеют температура, длительность работы под нагрузкой и действующие напряжения.
Нагрев ослабляет межатомные связи, при высоких температурах уменьшаются модули упругости, временное сопротивление, предел текучести, твердость. Чем ниже tnn основы сплава, тем ниже оказываются его допустимые рабочие температуры (рис. 15.6).
При длительном нагружении при высоких температурах поведение материала определяется диффузионными процессами. Для >тих условий характерны процессы ползучести и релаксации напряжений.
О 400 800 1200 t, С
Рис. 15.7. Кривая ползучести:
Рис. 15.6. Зависимость предела /- неустановившаяся стадия; II - уста-
текучести А1 (/), Си (2), Ti (5), новившаяся стадия; III- стадия разру-
Та (4) и W (5) от температуры шения
Ползучесть представляет собой медленное нарастание пластической деформации под действием напряжений, меньших предела текучести. Типичная зависимость деформации от времени нагружения представлена на рис. 15.7.
Кривая ползучести состоит из трех участков. Стадия / так называемой неустановившейся ползучести отличается постепенным затуханием скорости деформации до определенного постоянного значения. Стадия // — установившейся ползучести — характеризуется постоянной скоростью деформации. На стадии III — стадии разрушения — скорость деформации нарастает до момента разрушения. Как правило, она непродолжительна и для деталей недопустима, так как в этом случае неминуемо быстрое разрушение.
Относительное развитие каждой стадии зависит от температуры и напряжения. При одном и том же напряжении повышение температуры испытания сокращает продолжительность стадии // и ускоряет разрушение (рис. 15.8, а). Аналогично влияет повышение напряжения при неизменной температуре испытания (рис. 15.8,6).
Критериями жаропрочности являются: предел ползучести, предел длительной прочности, сопротивление релаксации.
Пределом ползучести называется напряжение, под действием кого рого материал деформируется на определенную величину за определен нос время при заданной температуре. В обозначении предела ползучести указывают темпера туру, деформацию и время, за которое она возникает.
Например, т'™1,,,,,. = НИ) МПа. означает, что иод действием напряжения
100 МПа за. 100000 ч при 550"С н материале появится пластическая деформация 1 %.
Рис' 15.8. Зависимость ползучести от температуры (а) и напряжений (б):
<1 < <2 < h < U < *5 < U\ ITi < (72 < (Тз < 0-4 < <Ть
Пределом длительной прочности называется напряжение, которое вызывает разрушение материала при заданной температуре за определенное время. В обозначении предела длительной прочности указывают температуру и время до разрушения. Например, ст^[|00 = 130 МПа означает, что при 600°С материал выдержит действие напряжения, равного 130 МПа, в течение 10000 ч.
Ползучесть металлов вызывает релаксацию напряжений в предварительно нагруженных деталях. При высокотемпературных условиях работы постепенно уменьшаются напряжения в болтах и других крепежных деталях, ослабляются натяги и т.п. Деформация нагруженной детали представляет собой сумму упругой и пластической деформации. В начале эксплуатации пластической деформации нет, и напряжение, например, в затянутой шпильке, равно сто = -#<£() (где Е% — модуль упругости при температуре эксплуатации). Появление пластической деформации уменьшает долю упругой деформации до е\, которая меньше eg. Соответственно напряжение уменьшается до о\ = Е%е\. Возникающая пластическая деформация есть не что иное, как деформация ползучести под действием монотонно убывающего напряжения.
Критерием сопротивления релаксации является падение напряжения Дст = сто — оТ за время г при заданной температуре.
Большинство жаропрочных материалов поликристаллические. Деформация ползучести в таких материалах развивается благодаря перемещению дислокаций в зернах, зернограничному скольжению и диффузионному переносу.
Перемещение дислокации при температурах выше 0,3 tnjl происходит двумя путями — скольжением и переползанием. При нагреве имевшиеся вокруг дислокаций скопления атомов легирующих элементов и примесей растворяются, и это облегчает скольжение. Переползание дислокаций
|
4 |
обеспечиваемся их взаимодейс i иием с на кансиями, благодаря лому отдельные участки дислокаций смещаются в сосед нисплоскости кристалла. Матрен ускоряет диффузионный приток вакансий и облегчает переползание.
Рис. 15.9. Схема диффузионной ползучести: заштрихованные области -удлинение зерна под влиянием направленной диффузии вдоль границ зерен |
Зернограничное скольжение представляет собой сдвиг зерен друг относительно друга вдоль общих границ в узкой пограничной области. Скольжение развивается под действием касательных напряжений. Деформация скольжения чем больше, чем мельче зерна.
Диффузионный перенос связан с перемещением вакансий вдоль границ и внутри зерен. Под действием растягивающих напряжений уменьшается энергия образования вакансий. На границе между двумя растянутыми зернами (рис. 15.9) концентрация вакансий увеличивается и они перемещаются в зоны, где их концентрация меньше. Потоку вакансий соответствует встречный поток атомов, поэтому у растянутых границ количество атомов увеличивается и зерна удлиняются. Перенос атомов происходит и по объему зерен, однако вклад объемной диффузии незначителен и играет роль лишь при высоких температурах около 0,9 (пл, а действие зернограничной диффузии существенно уже при 0,4 - 0,6 1пл.
Когда между перемещением дислокаций, зернограничным скольжением и диффузионным переносом нет соответствия, на границах зерен появляются поры и быстро наступает разрушение.
Для обеспечения жаропрочности требуется ограничить подвижность дислокаций и замедлить диффузию. Это достигается повышением прочности межатомных связей, созданием препятствий для перемещения дислокаций внутри зерен и на их границах, увеличением размеров зерен.
Прочность межатомной связи увеличивают легированием, изменени см типа кристаллической решетки, переходом от металлической связи к более прочной ковалентной.
Наиболее целесообразным является легирование твердого раствора более тугоплавкими металлами, чем металл-основа этого раствора. 'Гак, жаропрочные стали с ОЦК решеткой легируют молибденом (до 1 %), а жаропрочные никелевые сплавы с ГЦК решеткой вольфрамом, молибденом, кобальтом (в сумме- до 15 20%).
Эффективность растворного упрочнения небольшая и сохраняется до температур около 0,6 - 0,65 *Пл- Материалы со структурой твердого рас- I твора по жаропрочным свойствам уступают материалам, упрочненным ' дисперсными частицами.
У железа межатомные связи в ГЦК решетке прочнее, чем в ОЦК решетке. В частности, при температуре ~ 911 °С коэффициент самодиф- j фузии железа в ОЦК решетке в 300 раз больше, чем в ГЦК решетке, j Аустенитные стали имеют ГЦК решетку и по жаропрочности немного превосходят жаропрочные стали с ОЦК решеткой.
Выше 1000 °С материалы с ковалентной межатомной связью — графит, керамика на основе SiC, 81зЩ или материалов системы Si - А1 - О - N (сиалоны) по жаропрочным свойствам уступают лишь ряду тугоплавких сплавов, выгодно отличаясь от них меньшей плотностью и стоимостью.
Подвижность дислокаций существенно снижается в многофазной структуре с мелкими частицами упрочняющих фаз. Материалы с многофазной структурой, получаемой термической обработкой, называются дисперсионно-упрочненными.
Эффективность упрочнения определяется свойствами частиц и их распределением. Чем они мельче и чем ближе находятся друг от друга, тем выше жаропрочность.
Многофазная структура с мелкими частицами упрочняющих фаз в сталях получается при помощи закалки и отпуска, а во многих жаропрочных сплавах — после закалки и старения. Для получения оптимальной структуры в жаропрочных сталях и сплавах используют комплексное легирование, и по химическому составу эти материалы сложнее обычных легированных сталей и сплавов.
Упрочняющими фазами служат карбиды и карбонитриды в жаропрочных сталях, 7'-фа-за с ГЦК решеткой в никелевых сплавах, фазы Лавеса и некоторые другие промежуточные фазы в высоколегированных сталях.
Материалы с упрочняющими частицами, инертными по отношению к металлической основе, называются дисперсно-упрочненными. К ним относятся алюминий, упрочненный частицами AI2O3 (САП); никель, упрочненный частицами оксидов ТЬОг или НЮг- Преимуществом дисперсно-упрочненных материалов является устойчивость структуры при продолжительном нагреве. Такие материалы получают порошковой технологией из специально подготовленных порошков. Сущность подготовки заключается в размоле в шаровой мельнице порошков металла и оксида. Во время размола происходит сваривание и разрушение частиц порошков, получается механически легированный порошок. Частицы ною порошка имеют
однородную структуру с равномерным распределением тонких оксидных частиц.
Способы уменьшения зернограничного скольжения: создание крупнозернистой структуры, образование дисперсных частиц вторых (раз на границах зерен, нейтрализация вредных легкоплавких примесей на границах зерен.
Крупнозернистость -— характерная особенность структуры жаропрочных материалов. Чем крупнее зерна, тем меньше протяженность межзеренных границ и слабее зернограничное скольжение и диффузионный перенос. Идеальными в этом отношении являются монокристаллы, у которых совсем нет границ зерен. Однако производство деталей со структурой монокристалла освоено лишь для отдельных деталей, и практически приходится иметь дело с поликристаллическими материалами.
Для упрочнения границ зерен в жаропрочные стали и сплавы вводят малые добавки (0,1 - 0,01 %) легирующих элементов, которые концентрируются на границах. Эти элементы замедляют зернограничное скольжение и нейтрализуют действие вредных примесей. Особенно часто используют бор, церий и другие редкоземельные металлы. Границы зерен в никелевых жаропрочных сплавах упрочняют карбидами, добавляя с этой целью в сплавы около 0,1 % С.
К дополнительным мерам повышения жаропрочности относят: термомеханическую обработку для получения структуры полигонизации; упорядочение твердого раствора металла-основы и создание анизотропной структуры.
Полигонизация повышает сопротивление ползучести, так как мало-уиювые границы в зернах мешают передвижению дислокаций. Однако |»кая обработка эффективна лишь в изделиях простой формы (например, и трубах), когда деформация во всем изделии одинакова.
Применение упорядочения ограничено, не всякий твердый раствор упорядочивается.
Анизотропную структуру в изделиях из жаропрочных сплавов по лучают направленной кристаллизацией или теми же способами, какими получают КМ.
15.3.2. Основные группы жаропрочных материалов
Перлитные, мартенситные и аустенитные жаропрочные стали ис пользуют при 450 — 700°С; по масштабам применения они занимают веду litre место среди жаропрочных материалов. Ниже 450°С вполне пригодны «Лычные конструкционные стали и нет необходимости заменять их жаро прочными.
Жаропрочные сплавы на основе алюминия, магния и титана легче сталей, однако они менее жаропрочны. Используют их при следующих температурах (табл. 15.6): сплавы алюминия до 300 — 350 °С (исключе- j нием являются сплавы САП, которые можно применять до 500 - 550 °С);! сплавы магния до 300 —350°С; сплавы титана до 500- 600°С. Указанные! сплавы, несмотря на более высокую стоимость, применяют там, где из-за повышенных эксплуатационных температур невозможно использовать; обычные сплавы этих металлов и нельзя применять стали из-за более вы-i сокой плотности.
Таблица 15.6. ^Жаропрочность сплавов на основе алюминия, магния, титана
Марка | Содержания легирующих элементов, % | Температура, °C | ||
сплава | рекомендуемая | испытания | ffiooi МПа | |
(применения) | ||||
Сплавы на основе алюминия | ||||
Д20 | 6,ЗСи; 0,6Мп; 0,15Ti | 250-300 | 300 | 80 |
АК4-1 | 2,3Cu; l,6Mg; l.lFe; l.INi; до 0,lTi | 250 - 300 | 300 | 45 |
САП-1 | 6-9 A1203 | 300-500 | 500 | 45 |
АМ5 | 4,9Cu; 0,8Mn; 0,25Ti Сплавы на < | 250 - 300 7снове магния | 300 | 65 |
МА12 | 2,5-3,5Nd;0,5Zr | 150-200 | 200 | ~ 100 |
МЛН | 2,5-4 P3M; 0,7Zr; 0,5Zn | 200 - 250 | 250 | 50 |
МЛ19 | l,6-2,3Nd; 0,6Zn; 0,7Zr; 1,7Y Сплавы на о | 250-300 снове титана | 300 | 50 |
ВТЗ-1 | 6A1; 2,5Mo; 0,5Fe; 0,25Si | 350 - 400 | 400 | 800 |
ВТ6 | 6.25A1; 4V | 400-450 | - | |
ВТ8 | 6.5A1; З.ЗМо; 0,3Si | 450-500 | 500 | 500 |
ВТ9 | 6,5A1; 3,3Mo; 0,25Si; l,6Zr | 500-550 | 550 | 400 |
ВТ18 | 7.5A1; HZr; 0,7Mo; INb; 0,3Si | 550-600 | 600 | 200 |
Сплавы на основе никеля или кобальта жаропрочнее сталей. Первые [рименяют при 700— 1000°С, а вторые не получили широкого распро транения из-за дефицитности.
Тугоплавкие металлы и их (-планы, керамика на опюис SiC и Si:1N.|, графит - это материалы с высокой жаропрочностью, применяемые при температуре выше 1000"С.
Перлитные стали
Перлитные стали предназначены для длительной эксплуатации при ■150- 580°С; используют их главным образом в котлостроении. Критерием жаропрочности для них является предел ползучести с допустимой деформацией 1 % за 104 или 105 ч. Жаропрочность перлитных сталей обеспечивается выбором рационального химического состава и получен ной в результате термической обработки структуры легированного феррита с равномерно распределенными в нем частицами карбидов.
Перлитные жаропрочные стали являются низкоуглеродистыми, содержат от 0,08 до 0,15 % С (иногда концентрацию углерода повышают до 0,2 - 0,3 %) и не более 2 - 3 % карбидообразующих элементов, из которых самые важные — Мо, Сг и V (табл. 15.7) (12Х1МФ, 25Х2М1Ф).
Оптимальной термической обработкой являются нормализация после нагрева до ~ 1000 °С и последующий отпуск при 650 - 750 °С в течение 2 - 3 ч.
Для перлитных жаропрочных сталей особенно важна стабильность исходной структуры н свойств, так как изготовленные из них трубы и другие части теплоэнергетических установок эксплуатируются годами. Н исходном состоянии основная масса молибдена находится в феррите, а ванадий, хром и углерод — в карбидах типа МеС.
В условиях длительной эксплуатации происходит изменение хими ческого состава феррита и карбидов; сфсроидизация и рост карбидных частиц; графитизация — разложение карбидов с выделением свободного графита. Особенно опасна графитизация, так как образование графита приводит к аварийным разрушениям. Наиболее устойчив против графи 1изации карбид МеС, а наименее стоек — карбид Л/е3С. Легирование ванадием и хромом, а также отпуск после нормализации увеличиваю'! к'рмическую устойчивость карбидов и стабилизируют свойства материи
Л а.
Перлитные стали пластичны в холодном состоянии, удовлетворитель по обрабатываются резанием и свариваются. Но теплопроводности и те иловому расширению они близки к обычным конструкционным сталям.
Стали, содержащие 0,12 0,15% С, используют в паросиловых уста нонках для изготовления труб пароперегревателей, паропроводов и др\т их деталей, температура эксплуатации которых не превышает 570 5Ж)"С.
|
Перлитные стали с повышенным содержанием углерода (0,'2Г> О,.40%) но жаропрочности уступают перлитным сталям, содержащим 0,12 0,15 %, и полому для них установлены максимальные температуры длительной эксплуатации, равные 525- 565"С. Из лих сталей изготовляют валы и цельнокованые роторы стационарных и транспортных паровых турбин, плоские пружины и крепежные детали. Перлитные стали широко применяют благодаря невысокой стоимости, технологичности и удовлетворительной жаропрочности.
Мартенситные стали
Мартенситные стали предназначены для изделий, работающих при •150 — 600 °С; от перлитных они отличаются повышенной стойкостью к окислению в атмосфере пара или топочных газов. По своей жаропрочности эти стали немного превосходят перлитные. Критерий жаропрочности мартенситных сталей — предел ползучести с допустимой деформацией 0,1 % за 104 ч или 1 % за 105 ч.
Различают две группы мартенситных сталей:
1) стали с содержанием хрома 10 - 12 %, добавками Mo, V, Nb, W и низким (0,10 - 0,15%) содержанием углерода;
2) сильхромы с содержанием хрома 5-10%, добавками кремния в количестве до 2 - 3 % и повышенным содержанием углерода (до 0,4 %).
Стали первой группы используют в термически обработанном состоянии. Оптимальная термическая обработка заключается в закалке или нормализации после нагрева до 950— 1100 °С (для растворения карбидов) и отпуске при 600 — 740 °С. Структура термически обработанной стали — смесь легированного феррита и мелких карбидов — обеспечивает необходимую жаропрочность, сопротивление коррозии и релаксационную стойкость. Благодаря высокому содержанию легирующих элементов стали глубоко прокаливаются даже при нормализации (до 120 - 200 мм) и поэтому более пригодны для деталей крупных сечений, чем перлитные стали. При высоком содержании хрома (10 - 12 %) и других ферри го-образующих элементов и низком содержании углерода стали становя гея мартенситно-ферритными. Количество неупрочняемого при термической обработке феррита невелико, по жаропрочным свойствам мартенситные и мартенситно-ферритные стали близки. При длительной эксплуатации они могут применяться до 600°С. Мартенситные стали данной группы имеют разнообразное применение в паровых турбинах: из них изготовляют диски, лопатки, бандажи, диафрагмы, роторы, а также трубы и крепежные детали.
Стали второй группы — сильхромы характеризуются повышен ной жаростойкостью в среде горячих выхлопных газов и используются для изготовления клапанов двигателей внутреннего сгорания. Оптимальные свойства сильхромы имеют после обработки на сорбит. Так, сталь 40Х10С2М закаливают после нагрева до 1030 °С и отпускают при 720 — 780 °С. Чем больше содержание хрома и кремния в стали, тем выше ее рабочая температура. Жаропрочность сильхромов позволяет применять их при температурах не выше 600 - 650 °С; при более сложных условиях эксплуатации клапаны мощных двигателей изготовляют из аусте-нитных сталей. Сильхромы не содержат дорогих легирующих элементов и используются не только для клапанов двигателей, но и для крепежных деталей моторов. Технологические свойства сильхромов хуже, чем у перлитных сталей. Особенно затруднена их сварка, требуются подогрев перед сваркой и последующая термическая обработка.
Аустенитные стали
Аустенитные стали по жаропрочности превосходят перлитные и мар-тенситные стали, используют их при температурах выше 600 °С. Основные легирующие элементы — хром и никель. Соотношение между ними и железом выбирают таким, чтобы получить устойчивый аустенит, не склонный к фазовым превращениям. Иногда никель заменяют другими аустенитообразующими элементами — марганцем, азотом. Ферритообра-зующие элементы Mo, Nb, Ti, Al, W и другие вводят в стали для повышения жаропрочности; они образуют карбиды или промежуточные фазы. Аустенитные стали содержат, как правило, ~ 0,1 % С и лишь иногда до 0,4 % С.
Аустенитные жаропрочные стали подразделяют на три группы:
1) однофазные стали, не упрочняемые термической обработкой;
2) стали с карбидным упрочнением;
3) стали с интерметаллидным упрочнением.
Однофазные стали имеют устойчивую структуру однородного аусте-нита с незначительным содержанием карбонитридов титана или ниобия (для предупреждения межкристаллитной коррозии). Такая структура получается после закалки от 1020 — 1100°С. Стали этой группы применяют как жаропрочные в теплоэнергетике (например, 12Х18Н10Т).
Жаропрочность однофазных сталей увеличивают при помощи наклепа, пользуясь тем, что температура рекристаллизации аустенитных
сталей высока (~ 1000"С). Другой путь повышения жаропрочности со здание полигонизованной структуры, ('таль после небольшой пластической деформации (до 20%) нагревают для перераспределения дислокаций и образования малоугловых границ в зернах. Оба вида обработок применимы лишь для деталей наиболее простой формы, например турбинных дисков.
Аустенитные стали с карбидным упрочнением обычно содержат несколько карбидообразующих элементов: W, Mo, Ti, Nb, V, а также В -для обеспечения наивысшей жаропрочности. Из-за высокого содержания ферритообразующих элементов содержание никеля повышают до 14 %. Оптимальная структура получается после закалки от 1100 - 1150°С и старения полученного аустенита при 700 — 800 °С для выделения карбидов.
Аустенитные стали с интерметаллидным упрочнением — самые жаропрочные. Для повышения жаропрочности аустенита стали легируют Сг, Mo, W, добавки Al, Ti, Nb и Та служат для формирования выделений упрочняющей фазы типа №зА1. Их упрочняют закалкой и старением. Например, сталь 10Х1Ш20ТЗР закаливают от 1100 - 1170°С и старят при 700 - 750 °С в течение 15 - 25 ч.
Аустенитные стали охрупчиваются при эксплуатации из-за выделения избыточных фаз по границам зерен и особенно после образования хрупкой ст-фазы в интервале 600 — 750 °С. Чем больше хрома и молибдена содержит сталь, тем больше в ней появляется ст-фазы и тем сильнее охрупчивание. Для растворения образовавшейся «т-фазы проводят дополнительную термическую обработку после некоторого срока службы детали и тем самым устраняют охрупчивание и восстанавливают первоначальные свойства.
Аустенитные стали отличаются большой пластичностью, хорошо свариваются, однако по сравнению с перлитными сталями труднее об рабатываются давлением и резанием.
Жаропрочные никелевые сплавы
Жаропрочные никелевые сплавы содержат, как правило, 10 - 12 % Сг и такие элементы, как W, Мо, V, Со, Al, Ti, В и др.
Mo, W, Со, Сг упрочняют матричный твердый раствор на основе никеля; А1 и Ti вместе с Ni образуют метастабильную 7'-фазу с такой же структурой, как и матричный раствор (ГЦК); углерод в количестве до 0,1 0,15 % формирует дисперсные карбиды на границах зерен.
Термическая обработка сплавов заключается в закалке и старении. Детали нагревают до 1150 - 1250 °С для получения однородного раствора и охлаждают на воздухе. За время охлаждения внутри твердого раствора происходит перераспределение атомов алюминия и титана, образуются малые объемы, обогащенные этими элементами. При старении в этих объемах возникают частицы 7'-фазы, когерентные с матричным твердым раствором. Периоды решеток 7- и 7'-фаз отличаются незначительно (всего на ~ 0,1 %), поэтому полученная метастабильная структура сохраняется при высоких температурах в течение 20000 - 30000 ч.
Частицы 7'-фазы имеют размеры 20 - 40 нм, а ее содержание, в зависимости от легирования, доходит до 20 - 50 %. Переход метастабильной 7'-фазы в стабильную фазу ШзТ1 означает утрату когерентности, укрупнение частиц второй фазы и значительную потерю жаропрочности.
Никелевые жаропрочные сплавы широко применяют благодаря их высокой прочности, коррозионной стойкости и жаропрочности. Помимо основного назначения — изготовления лопаток и других ответственных деталей современных газотурбинных двигателей, эти сплавы применяют для производства штампов и матриц горячего деформирования металлов. Их используют при температурах от 750°С, но не выше 950 - 1000°С. В наиболее жаропрочных сплавах, содержащих около 10 % Сг, недостаток жаростойкости исправляется химико-термической обработкой деталей, в частности алитированием и хромоалитированием. Жаропрочные никелевые сплавы с трудом подвергаются горячему деформированию и резанию. Как и аустенитные стали, они имеют низкую теплопроводность и значительное тепловое расширение.
Дата добавления: 2018-04-05; просмотров: 640; Мы поможем в написании вашей работы! |
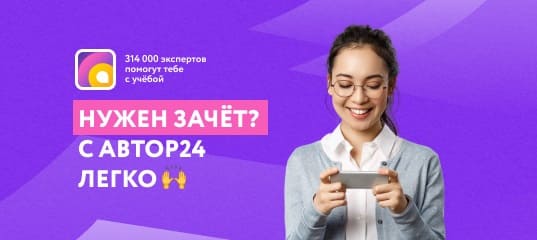
Мы поможем в написании ваших работ!