Закаливаемость и прокаливаемость сталей
Закаливаемость и прокаливаемость — важнейшие характеристики сталей. Закаливаемость определяется твердостью поверхности закаленной детали и зависит главным образом от содержания углерода в стали. При закалке различных деталей поверхность их, как правило, охлаждается со скоростью, большей икр, следовательно, на поверхности образуется мартенсит, обладающий высокой твердостью.
При закалке любых деталей даже в самых сильных охладителях невозможно добиться одинаковой скорости охлаждения поверхности и сердцевины детали. Следовательно, если скорость охлаждения сердцевины при закалке будет меньше vKp, то деталь не прокалится насквозь, т.е. там не образуется мартенсит.
Прокаливаемостью называют способность стали закаливаться на определенную глубину. С помощью термокинетических диаграмм можно не только анализировать эту способность стали, но и определять ее, если известны кривые охлаждения закаливаемой детали в различных точках. Этот прием показан на рис. 6.18, где на термокинетическую диаграмму стали 45 нанесены кривые охлаждения в воде детали типа вала в точках, расположенных на поверхности (1) на расстоянии 0,5Л от поверхности (2) и в центре (5) вала. Эти кривые получают экспериментальным или расчетным путем. В данном случае кривые расположились так, что при указанных условиях охлаждения на поверхности и на расстоянии 0,5Л от нее будет образовываться только мартенситная структура, а в центре вала — смесь перлита с бейнитом.
|
|
Иногда на термокинетических диаграммах указывают значенкя твердости стали после охлаждения с той или иной скоростью. И лом случае
можно построить график изменения твердости по сечению цилиндрического образца данной стали. Такие графики, но полученные экспериментальным путем, приведены в справочниках и характеризуют прокаливаемость сталей.
Рис. 6.30. Изменение твердости по длине J образца после торцовой закалки: /- твердость полумартенси гной зоны; 1 - сталь с низкой прока-ливаемостью; 2 - сталь с высокой прокаливаемостью |
Условились при оценке прокаливае-мости закаленными считать слои, в которых содержится не менее 50 % мартенсита (полумартенситная зона). Установлено, что легирование стали любыми элементами, кроме кобальта, увеличивает прокаливаемость, так как при этом повышается устойчивость переохлажденного аустенита. Для экспериментального определения прокаливаемости менее трудоемким оказался способ торцо-
вой закалки (ГОСТ 5657-69). Цилиндрический образец, диаметром 0,025 м и длиной 0,1 м, нагретый до температуры закалки, охлаждают струей воды только с торца на специальной установке. После охлаждения измеряют твердость по образующей цилиндра и строят график изменения твердости по длине образца (рис. 6.30). Оригинальным в этом способе является то, что каждая точка поверхности стандартного образца охлаждается с различной и вполне определенной скоростью. Сопоставление двух кривых на рис. 6.30 наглядно показывает, что сталь, характеризуемая кривой 2, имеет более высокую прокали-иаемость, чем сталь, у которой твердость изменяется в соответствии с кривой 1. Прокаливаемость стали одной и той же марки в зависимости щ изменений химического состава, размера зерна аустенита (температуры нагрева), размера и формы детали и т.д. колеблется в значительных пределах. В связи с этим в справочниках прокаливаемость стали каждой марки характеризуется не кривой, а полосой прокаливаемости.
|
|
Отпуск закаленных сталей
Нагрев закаленных сталей до температур, не превышающих А\, на и,1 паю г отпуском.
К результате закалки чаще всего получают структуру мартенсита
с некоторым количеством остаточного аустенита, иногда структуру
сорбита, троостита или Пей и и та.
Рис. в.32. Изменение содержания углерода • мартенсите при отпуске до 100*С |
Изменение структуры мартенситно-аустенитной стали при отпуске
|
|
При отпуске происходит несколько процессов. Основной — распад мартенсита, состоящий в выделении углерода в виде карбидов. Кроме того, распадается остаточный аустенит, совершаются карбидное превращение и коагуляция карбидов, уменьшаются несовершенства кристаллического строения Q-твердого раствора и остаточные напряжения.
Фазовые превращения при отпуске принято разделять на три превращения в зависимости от изменения удельного объема стали. Распад мартенсита и карбидное превращение вызывают уменьшение объема, а распад аустенита — его увеличение.
На рис. 6.31 схематично показано изменение длины закаленного образца углеродистой стали при отпуске, в которой было значительное количество остаточного аустенита. В сталях, не содержащих легирующих элементов, первое превращение происходит в интервале температур 80 - 200 °С, второе при 200 - 260 °С, третье при 260 - 380 °С (см. рис. 6.31,
/ - ш).
I. Из мартенсита выделяется часть углерода в виде метастабильно-го е-карбида, имеющего гексагональную решетку и химический состав, близкий к Fe2C. Дисперсные кристаллы е-карбида когерентны с решеткой мартенсита. Обеднение твердого раствора углеродом происходит неравномерно: наряду с участками мартенсита, обедненного углеродом (вблизи карбидов), сохраняются участки с исходным содержанием углерода. Первое превращение идет с очень малой скоростью и без нагрева. Уменьшение количества растворенного углерода снижает тетрагональность мартенсита — длина образца уменьшается.
|
|
|
|
80 200 260 380 Рис. 6.31. Изменение длины цилиндрического образца стали с содержанием углерода Польши О,в % при отпуске (схема) |
Содержание углерода в мартенсите в интервале температур первого превращения зависит от исходного количества углерода (рис. 6.32), тогда как при более высоком нагреве оно определяется лишь температурой.
II. Одновременно происходит несколько процессов: продолжается распад мартенсита, распадается остаточный аустенит и начинается карбидное превращение. Распад мартенсита распространяется на весь объем, концентрационная неоднородность твердого раствора исчезает; в мартенсите остается около 0,2 % растворенного углерода. Распад остаточного аустенита происходит по механизму бейнитной реакции: образуется смесь кристаллов низкоуглеродистого мартенсита и дисперсных карбидов. При температурах около 250 °С начинается превращение е-карбида в цементит; при этом когерентность решеток твердого раствора и карбида нарушается.
Если в закаленной стали было много остаточного аустенита, то уменьшение плотности при распаде будет большим, чем ее увеличение, вследствие выделения углерода из мартенсита. В этом случае (см. рис. 6.31) длина закаленного образца возрастает.
III. Завершаются распад мартенсита и карбидное превращение. Из мартенсита выделяется весь пересыщающий углерод в виде карбидов, тетрагональность решетки а-твердого раствора устраняется — мартенсит переходит в феррит. После отпуска при 380 —400 °С в структуре стали обнаруживается только карбид цементитного типа. Оба указанные процесса вызывают увеличение плотности стали — длина образца уменьшается
(см. рис. 6.31).
Ферритно-карбидная смесь, образовавшаяся в конце третьего превращения, весьма дисперсна и имеет примерно такую же твердость, как тро-остит (ее называют трооститом отпуска). Структуру стали, образовавшуюся при температурах первого и второго превращений, называют отпущенным мартенситом.
При более высоких нагревах в углеродистых сталях происходят изменения структуры, не связанные с фазовыми превращениями: изменяются форма, размер карбидов и структура феррита.
В интервале температур третьего превращения цементит имеет форму тонких пластин. С повышением температуры происходит коагуляция: кристаллы цементита укрупняются (более мелкие кристаллы распадаются, а более крупные растут); при этом форма кристаллов постепенно приближается к сфероидальной. Коагуляция и сфероидизация карбидов происходят с заметной скоростью начиная с температур 350-400°С. Скорость этих процессов увеличивается при повышении температуры.
Изменения структуры феррита обнаруживаются начиная с температуры около 400°С: уменьшается плотность дислокаций, которая очень нолика н мартенсите до отпуска; постепенно устраняются границы между пластинчатыми кристаллами феррита, в результате чего зерна феррита
укрупняются и их форма приближается к равноосной. Таким образом, с повышением температуры отпуска постепенно снимается фазовый наклеп, возникший при мартенситном превращении.
Ферритно-карбидную смесь, которая образуется после отпуска при 450 — 650°С, называют сорбитом отпуска. После отпуска при температуре, близкой к температуре А\, образуется грубая ферритно-карбидная смесь — зернистый перлит.
Дата добавления: 2018-04-05; просмотров: 658; Мы поможем в написании вашей работы! |
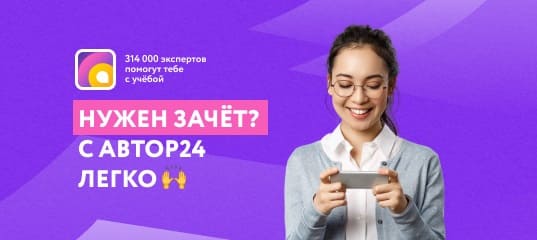
Мы поможем в написании ваших работ!