Сфероидизирующии отжиг инструментальных сталей (сферойдизация)
Инструментальные стали для режущего, измерительного инструмента и для инструмента, деформирующего металл в холодном состоянии, содержат углерод в количестве от 0,7 до 2 %. Высокое содержание углерода обусловливает высокую твердость инструментальных сталей, что затрудняет их обработку резанием. Для снижения твердости такие стали отжигают. Для заэвтектоидных сталей сфероидизирующии отжиг, кроме того, подготовляет структуру к закалке.
Наименьшую твердость имеют стали со структурой зернистого пер лита, когда цементит перлита имеет округлую форму. Отсюда и название отжига — «сфероидизация».
|
Рис. 6.26. Микроструктура эвтектоид-ной углеродистой стали после сфероиди-чирующего отжига. Зернистый перлит. хГ.ОО |
Зернистый перлит (рис. 6.26) в инструментальных сталях обычно по лучают путем нагрева сталей до температуры 750 — 770° С (немного выше, чем Ас\) и последующего медленного охлаждения или изотермической ныдержки при субкритической температуре 650 — 680°С. При нагреве до температуры, лишь немного превышающей критическую, даже в доэвтек тидных сталях сохраняются нераспавшиеся мелкие карбидные частицы, которые при охлаждении или изотермической выдержке выполняют роль центров кристаллизации сфероидального цементита.
В заэвтектоидных сталях требуется сфероидизировать не только эв-тектоидный цементит, но и цементит вторичный (избыточный), который при нарушениях режима обработки давлением выделяется в виде сплошных оболочек аустенитных зерен (на шлифе — сетка). Этот заэвтектоид-ный цементит сфероидизируется труднее, чем цементит перлита, поэтому заэвтектоидные стали предварительно нагревают выше температуры Асст) Для распада цементита и охлаждают на воздухе. Такая обработка вызывает измельчение цементита и разрыв сетки цементита на границах зерен, что облегчает сфероидизацию при вторичном нагреве.
|
|
Низко-, средне- и высоколегированные инструментальные стали сфе-роидизируют аналогичным образом, однако чаще вместо непрерывного охлаждения от температуры нагрева используют субкритические изотермические выдержки.
Нормализация сталей
Нормализации, как и перекристаллизационному отжигу, чаще всего подвергают конструкционные стали после горячей обработки давлением и фасонного литья. Нормализация отличается от отжига в основном условиями охлаждения; после нагрева до температуры на 50 - 70 °С выше Ас$ сталь охлаждают на спокойном воздухе.
Нормализация — более экономичная термическая операция, чем отжиг, так как меньше времени затрачивается на охлаждение стали. Кроме того, нормализация, обеспечивая полную перекристаллизацию структуры, приводит к получению более высокой прочности стали, так как при ускорении охлаждения распад аустенита происходит при более низких температурах.
|
|
Легированные конструкционные стали с повышенной устойчивостью переохлажденного аустенита после нормализации приобретают высокую твердость, затрудняющую последующую обработку резанием. В связи с этим после нормализации проводят отпуск при температурах, обеспечивающих получение требуемой твердости (650 — 750 °С в зависимости от состава стали).
После нормализации углеродистых и низколегированных сталей, так же как и после отжига, образуется ферритно-перлитная структура, однако имеются и существенные структурные отличия (рис. 6.27). При ускоренном охлаждении, характерном для нормализации, доэвтектоидный феррит при прохождении температурного интервала Аг$ — Аг\ выделяется на границах зерен аустенита; поэтому кристаллы феррита образую! сплошные или разорванные! оболочки вокруг зерен аустенита ферришую соку.
Рис. 6.27. Микроструктура стали (0,4 % С) после отжига (а) и после нормализации (б). х500
Нормализация позволяет несколько уменьшить анизотропию свойств, вызванную наличием в горячедеформированной стали вытянутых неме таллических включений. При ускоренном охлаждении (но сравнению с отжигом) возникает больше самопроизвольно образующихся центров кри сталлизащш, поэтому строчечность структуры менее резко выражена. Это дополнительное преимущество данного вида обработки.
|
|
Свойства нормализованных горячекатаных полуфабрикатов суще ственно зависят от сечения: чем меньше сечение, тем быстрее произойдет охлаждение на спокойном воздухе и тем выше будет прочность стали.
6.6.3. Особенностизакалки сталей
В большинстве случаев при закалке желательно получить структуру наивысшей твердости, т.е. мартенсит, при последующем отпуске которо го можно понизить твердость и повысить пластичность стали. При равной твердости структуры, полученные при отпуске мартенсита, имеют луч шие механические свойства, чем структуры, полученные непосредственно в результате распада аустенита, за исключением нижнего бейнита.
В зависимости от температуры нагрева закалку называют полной и неполной. При полной закалке сталь переводят в однофазное аустепит мое состояние, т.е. нагревают выше критических температур 1с,( или Лс.ст, при неполной — до межкритических температур между Лс\ и
|
|
Лс-л {Асст) (рис. 6.28, а).
Дожтектоидные стали, как правило, подвергают полной закалке, при пом оптимальной температурой нагрева является температура Лс\ I I (1И) . . . Г>0"С). Такая температура обеспечивает получение при nai реве
Рис. 6.28. Оптимальные температуры нагрева под закалку доэвтектоидных и заэвтектоидных (а), а также высоколегированных ледебуритных сталей (б)
мелкозернистого аустенита и соответственно после охлаждения — мелкокристаллического мартенсита. Недогрев до температуры Ас?, приводит к сохранению в структуре кристаллов доэвтектоидного феррита, что при некотором уменьшении прочности обеспечивает повышенную пластичность закаленной стали.
Заэвтектоидные стали подвергают неполной закалке. Оптимальная температура нагрева углеродистых и низколегированных сталей при этом — температура Ас\ + (30 ... 50 °С).
После закалки заэвтектоидная сталь приобретает структуру, состоящую из мартенсита и цементита. Кристаллы цементита тверже кристаллов мартенсита, поэтому при неполной закалке заэвтектоидные стали имеют более высокую твердость, чем при полной. Так как сталь предварительно подвергалась сфероидизирующему отжигу, избыточные карбиды округлой формы не вызывают снижения вязкости. Высоколегированные инструментальные стали ледебуритного класса (рис. 6.28, б) для повышения теплостойкости1 нагревают при закалке до очень высоких температур (область 1), близких к эвтектической. При этом происходит распад всех вторичных карбидов, аустенит обогащается не только углеродом, но и легирующими элементами, содержащимися в карбидах. В результате получается высоколегированный, а следовательно, и теплостойкий мартенсит.
Теплостойкость — способность легиронаиных сталей сохраним, имсикуы i мерность при иai репе до 500 — 600 °0.
Если высоколегированные инструментальные стали используют но как теплостойкие, а только как износостойкие, температуру закалки понижают (см. рис. 6.28, область 2), сохраняя некоторое количество вторичных карбидов нерастворенными. При такой закалке температура нагрева достаточно высокая (900 — 1000 °С). Это связано с влиянием легирующих элементов на критические температуры стали (см. гл. 4) и с малой скоростью диффузии легирующих элементов в твердом растворе.
Для получения мартенситной структуры необходимо переохладить аустенит до температуры мартенситного превращения; следовательно, скорость охлаждения должна превышать критическую скорость икр (см.
рис. 6.18).
Для углеродистых сталей икр составляет 400 — 1400 °С/с. Для того чтобы переохладить аустенит таких сталей до температуры мартенситного превращения, необходимо прибегать к очень резкому охлаждению, которое достигается погружением закаливаемых деталей в холодную воду либо воду с добавками соли или едкого натра (табл. 6.2).
При охлаждении на поверхности стальной детали не должна образоваться паровая пленка, препятствующая теплообмену с закалочной средой.
Таблица 6.2. Относительная охлаждающая способность закалочных сред
Температура, °С | Относительная | ||
Охлаждаю- | охлаж- | пузырь- | интенсивность |
щая среда | дающей | кового | охлаждения в |
среды | кипения | середине интервала пузырькового кипения | |
Вода | 20 | 400 - 100 | 1 |
40 | 350- 100 | 0,7 | |
80 | 250 - 100 | 0,2 | |
10 %-й раствор | |||
в воде: | |||
NaCl | 20 | 650 - 100 | 3 |
NaOll | 20 | 650 - 100 | 2,5 |
Масло ми- | |||
неральное | 20 200 | 501) 250 | 0,3 |
Лучшей является стадия пузырькового кипения охлаждающей жидкости. Чем больше температурный интервал этой стадии, тем интенсивнее охлаждает закалочная среда.
Лучше пользоваться добавками едкого натра, так как щелочная среда не вызывает последующей коррозии стальных деталей. Многие легированные стали приобретают мартенситную структуру при охлаждении в холодных или подогретых маслах, а высоколегированные стали закаливаются на мартенсит даже при охлаждении на воздухе.
Охлаждение при закалке наиболее просто осуществляется погружением закаливаемой детали в жидкую среду (воду или масло), имеющую температуру 20 - 25 °С. Однако в некоторых случаях для уменьшения деформации (коробления) деталей или для предотвращения образования трещин условия охлаждения усложняют.
Коробление и растрескивание вызываются значительными остаточными напряжениями, возникающими при закалке. Основной источник напряжений — увеличение объема при превращении аустенита в мартенсит. Модуль упругости в температурном интервале мартенситного превращения достаточно велик, поэтому возникающие из-за объемных изменений напряжения релаксируют с малой скоростью. Значительные макроскопические напряжения возникают из-за неодновременности превращения по сечению, а также в закаливаемых деталях сложной формы. Остаточные напряжения уменьшаются при условии одновременного превращения
|
по сечению и понижения скорости охлаждения в интервале температур Мн-Мк. В практике термической обработки сталей широкое использование нашли следующие способы охлаждения, позволяющие значительно уменьшить величину остаточных напряжений: закалка в двух средах и ступенчатая закалка.
Рис. 6.29. Способы охлаждения при закалке сталей: / - непрерывное охлаждение; 2 -закалка в двух средах; 3 - ступенчатая закалка; 4 ~ изотермическая закалка |
Закалка в двух средах. Схема обработки показана на рис. 6.29. После нагрева под закалку деталь погружают на определенное время в воду, в результате чего достигается быстрое прохождение температурного интервала минимальной устойчивости аустенита, а затем переносят в более мягкую охлаждающую среду, обычно в масло.
Ступенчатая закалка.При ступенчатой закалке деталь, nai р«м ун> до температуры закалки, переносят в жидкую среду, имеющую юмпера туру на 50— 100°С выше мартенситной точки Мн закаливаемой стали, и выдерживают небольшое время, необходимое для выравнивания темпера туры по сечению, а затем окончательно охлаждают на спокойном воздухе
(см. рис. 6.29).
Получение мартенсита при таком способе охлаждения возможно только в легированных сталях с достаточно высокой устойчивостью переохла жденного аустенита в интервале температур перлитного превращения.
К ступенчатой закалке прибегают обычно при термической обработке инструментов небольшого сечения из низко- и среднелегированных сталей. Достоинство указанного способа охлаждения состоит также в возможно сти правки инструментов в специальных приспособлениях при охлажде нии после изотермической выдержки.
Изотермическая закалка. В некоторых случаях после закалки на мартенсит и последующего отпуска не удается получить достаточной прочности и вязкости, тогда применяют изотермическую закалку на нижний бейнит, обладающий высокой вязкостью и прочностью.
При изотермической закалке нагретую деталь переносят в ванну с расплавленными солями, имеющую температуру на 50- 100°С выше мар тенситной точки М„, выдерживают при этой температуре до завершс ния превращения аустенита в бейнит и затем охлаждают на воздухе (см.
рис. 6.29).
Изотермическая закалка, так же как и ступенчатая, применима голь ко к сталям с достаточной устойчивостью переохлажденного аустенита.
Для предотвращения коробления изделий, таких, как ножовки, пилы, бритвы, их охлаждают заневоленными, например, в массивных медных или стальных плитах; скорость охлаждения в этих условиях оказывается меньшей, чем в маслах.
Обработка холодом1. Охлаждение закаленных деталей до темпе ратуры, меньшей 20 — 25°С, называют обработкой холодом.
Обработке холодом подвергают закаленные легированные стали, дли которых температура конца мартенситного превращения Мк значительно ниже 20-25 °С. Вследствие этого, после охлаждения до этой температуры, наряду с мартенситом в структуре оказывается значительное количество остаточного аустенита. Остаточный аустенит понижает твердость зака ленной стали и может вызвать нестабильность размеров готовых деталей.
Предложена ме i алломедом Л II. I уля'-вмм н I9'!7 I.
|
так как, будучи нестабильной фазой, способен к распаду при низкой температуре с малой скоростью. Для стабилизации размером закаленных изделий и повышения их твердости проводится охлаждение до температуры Мк, в процессе которого аустенит превращается в мартенсит. Температура Мк легированных сталей изменяется в широких пределах, поэтому при обработке холодом их охлаждают до температур от -40 до -196°С (температуры жидкого азота).
Остаточный аустенит в процессе выдержки при 20 - 25 °С несколько стабилизируется, поэтому обработку холодом следует проводить сразу после закалки.
Обработке холодом подвергают измерительные инструменты, детали подшипников качения, цементированные детали из легированных сталей и ряд других изделий.
Дата добавления: 2018-04-05; просмотров: 598; Мы поможем в написании вашей работы! |
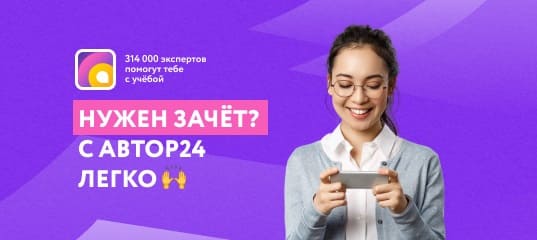
Мы поможем в написании ваших работ!