КОНСТРУКЦИОННАЯ ПРОЧНОСТЬ МАТЕРИАЛОВ
Общие требования, предъявляемые к конструкционным материалам
Конструкционными называют материалы, предназначенные для из-)товления деталей машин, приборов, инженерных конструкций, подвер-«ощиеся механическим нагрузкам. Детали машин и приборов характе-изуются большим разнообразием форм, размеров, условий эксплуатации, ни работают при статических, циклических и ударных нагрузках, при изких и высоких температурах, в контакте с различными средами. Эти акторы определяют требования к конструкционным материалам, основ-ые из которых — эксплуатационные, технологические и экономические.
Эксплуатационные требования имеют первостепенное значение. Для эго чтобы обеспечить работоспособность конкретных машин и приборов, атериал должен иметь высокую конструкционную прочность.
Конструкционной прочностью называется комплекс механических юйств, обеспечивающих надежную и длительную работу материала в словиях эксплуатации.
Механические свойства, определяющие конструкционную прочность
выбор конструкционного материала, будут рассмотрены в следующем
араграфе. Требуемые значения механических свойств материала для
энкретного изделия зависят не только от силовых факторов, но и от воз-
зйствия на него рабочей среды и температуры.
Среда — жидкая, газообразная, ионизированная, радиационная, в коброй работает материал, оказывает существенное и преимущественно грицателыюе влияние на ею механические свойства, снижая рабогоспо-)Г>||ост1» деталей. I! частости, рабочая среда может вызывать поврежде-ие повсрхиосiи вследствие коррозионного растрескивания, окисления и
|
|
образования окалины, а также изменение химического состава ионерхнос1 ною слоя в результате насыщения нежелательными элементами (например), водородом, вызывающим охрупчивание). Кроме того, возможны разбухание и местное разрушение магериала под действием ионизационного и радиационного облучения. Для того чтобы противостоять рабочей среде, материал должен обладать не только механическими, но и определенными физико-химическими свойствами: стойкостью к электрохимической коррозии, жаростойкостью (окалиностойкостью), радиационной стойкостью, влагостойкостью, способностью работать в условиях вакуума и др.
Температурный диапазон работы современных материалов очень широк от -269 до 1000 °С, а в отдельных случаях до 2500 °С. Для обеспечения работоспособности при высокой температуре от материала требуется жаропрочность, а при низкой температуре — хладостойкость.
В некоторых случаях важно также требование определенных магнитных, электрических, тепловых свойств, высокой стабильности размеров деталей (особенно высокоточных деталей приборов).
|
|
Технологические требования (технологичность материала) направлены на обеспечение наименьшей трудоемкости изготовления деталей и конструкций. Технологичность материала оценивается обрабатываемостью резанием, давлением, свариваемостью, способностью к литью, а ижже прокаливаемостыо, склонностью к деформации и короблению при термической обработке. Технологичность материала имеет важное значение, так как от нее зависят производительность и качество изготовления деталей.
Экономические требования сводятся к тому, чтобы материал имел невысокую стоимость и был доступным. Стали и сплавы по возможности должны содержать минимальное количество легирующих элементов. Использование материалов, содержащих легирующие элементы, должно быть обосновано повышением эксплуатационных свойств деталей.
Экономические требования, так же как и технологические, приобретают особое значение при массовом масштабе производства.
Таким образом, качественный конструкционный материал должен удовлетворять комплексу требований.
8.2. Конструкционная прочность материалов и критерии ее оценки
|
|
Конструкционная прочность — комплексная характеристика, включающая сочетание критериев прочности, жесткости, надежности и долго вечноеiи.
Критерии прочности материала выбирают в зависимости от условий его работы. При статических нагрузках критериями прочности являются временное сопротивление сгв и предел текучести (70,2 (ат), характеризующие сопротивление материала пластической деформации^ Поскольку при работе большинства деталей пластическая деформация недопустима, то их несущую способность, как правило, определяют по пределу текучести. Для приближенной оценки статической прочности используют твердость НВ (для сталей справедливо эмпирическое соотношение ав = НВ/3,4).
Большинство деталей машин испытывает длительные циклические нагрузки. Критерий их прочности — предел выносливости <тд (при симметричном круговом изгибе c_i).
По значениям выбранных критериев прочности рассчитывают допустимые рабочие напряжения. При этом, чем больше прочность материала, тем выше допустимые рабочие напряжения и меньше размеры и масса детали.
Однако повышение уровня прочности материала и, как следствие, рабочих напряжений сопровождается увеличением упругих деформаций
|
|
£упр = <f/E,
где Е — модуль нормальной упругости.
Для ограничения упругой деформации материал должен обладать высоким модулем упругости (или сдвига), являющимся критерием его жесткости. Именно критерии жесткости, а не прочности обусловливают размеры станин станков, корпусов редукторов и других деталей, от которых требуется сохранение точных размеров и формы.
Возможно и противоположное требование. Для пружин, мембран и других чувствительных упругих элементов приборов, наоборот, важно обеспечить большие упругие перемещения. Поскольку £^р = аупр/Е, то от материала требуются высокий предел упругости и низкий модуль упругости.
Для материалов, используемых в авиационной и ракетной технике, важна эффективность материала по массе. Она оценивается удельными характеристиками: удельной прочностью ав/(рд) (где р — плотность материала; д — ускорение свободного падения) и удельной жесткостью Е/{Рд).
Характеристики (Т„ и ао,7 используют также для оценки прочности деталей при кра i конре.менных циклических перегрузках и при малом числе циклон (< 10' ).
Таким образом, в качестве критериев конструкционной прочности выбирают те характеристики, которые наиболее полно отражают прочность в условиях эксплуатации.
Кроме стандартных механических характеристик <тв и его,2> характеризующих металлургическое и технологическое качество материала, для оценки конструкционной прочности необходимы характеристики прочности при рабочих температурах и в эксплуатационных средах.
Например, для расчета на прочность вала, работающего во влажной атмосфере при 250°С, необходимы егв и сгп,2) Е ПРИ так°й температуре, а также er_i, определенный во влажной среде и при нагреве.
Надежность — свойство материала противостоять хрупкому разрушению. Хрупкое разрушение вызывает внезапный отказ деталей в условиях эксплуатации. Оно считается наиболее опасным из-за протекания с большой скоростью при напряжениях ниже расчетных, а также возможных аварийных последствий*
Для предупреждения хрупкого разрушения конструкционные материалы должны обладать достаточной пластичностью (6, ф) и ударной вязкостью (KCU). Однако эти параметры надежности, определенные на небольших лабораторных образцах без учета условий эксплуатации конкретной детали, достаточно показательны лишь для мягких малопрочных материалов. Между тем стремление к уменьшению металлоемкости конструкций ведет к более широкому применению высокопрочных и, как правило, менее пластичных материалов с повышенной склонностью к хрупкому разрушению. Необходимо также учитывать то, что в условиях эксплуатации действуют факторы, дополнительно снижающие их пластичность, вязкость и увеличивающие опасность хрупкого разрушения. Это концентраторы напряжений (надрезы), понижение температуры, динамические нагрузки, увеличение размеров деталей (масштабный фактор).
Чтобы избежать внезапных поломок в условиях эксплуатации, необходимо учитывать трещиностойкость материала. Трещиностойкость — группа параметров надежности, характеризующих способность материала тормозить развитие трещины.
Количественная оценка трещиностойкости основывается на линейной механике разрушения. В соответствии с ней очагами разрушения высокопрочных материалов служат небольшие трещины эксплуатационного или технологического происхождения (могут возникать при сварке, термической обработке), а также трещиноподобные дефекты (неметаллические
И зне<■ in» немало анарий из-за хрупкого разрушения корпусов судов, ферм мое гон, i руоонроиодон и ;ipyi их конструкций.
|
слючения, скопления дислокаций и т.п.). Трещины являются острыми щцентраторами напряжений, местные (локальные) напряжения в верши-! которых могут во много раз превышать средние расчетные напряжения ■ис. 8.1).
Для трещины длиной / и радиусом г (см. рис. 8.1) напряжение в ршине
^ах = 2асрЧ///;. (8.1)
энцентрация напряжений тем больше, чем длиннее трещина и острее ее ршина.
Для пластичных материалов опасность таких дефектов невелика. В зультате перемещения дислокаций у вершины трещины протекает мест-я пластическая деформация, которая вызывает релаксацию (снижение) кальных напряжений и их выравнивание. К тому же увеличение плот-сти дислокаций и вакансий в вершине трещины сопровождается ее заилением, и дефект перестает играть роль острого концентратора на-яжений.
Хрупкие материалы, наоборот, чрезвычайно чувствительны к надре-л. В силу того, что дислокации заблокированы и пластическая дефор-ция невозможна, при увеличении средних напряжений локальные на-яжения <7™ах повышаются настолько, что вызывают разрыв межатом-х связей и развитие трещины. Рост трещины не тормозится, как в астичных материалах, а наоборот, ускоряется. После достижения неко-эой критической длины наступает самопроизвольный лавинообразный :т трещины, вызывающий хрупкое разрушение.
Так как высокопрочные материалы обладают определенной пластич-:тью, то для них реальную опасность представляют трещины не любых 1меров, а только критической длины /кр. Подрастание трещины до /кр шозится в них местной пластической деформацией. Но при определен-1 сочетании рабочего напряжения и длины дефекта равновесное пологие трещины нарушается, и происходит самопроизвольное разрушение. Оценку надежности высокопрочных материалов по размеру допусти-о дефекта (меньше критического) проводят по критериям Ж. Ирвина, предложено два критерия трещиностойкости, из которых наибольшее [менение имеет критерий К — коэффициент интенсивности напряже-i в вершине трещины. Он определяет растягивающие напряжения <ту юбой точке (рис. 8.2) впереди вершины трещины:
(Ту = К/у/Ъгх. (К.2)
Рис. 8.2. Зависимость напряжения от расстояния до вершины трещины |
Рис. 8.1. Концентрация напряжений вблизи эллиптической трещины
Знаменатель дроби обращается в единицу при х и 0,16, поэтому К численно равен ау на расстоянии ~ 0,16 мм от вершины трещины.
Критерий К для наиболее жесткого нагружения (плоская деформация растяжением) обозначают К\, а при достижении критического значения, когда стабильная трещина переходит в нестабильную, — К\с. Критерий К\с показывает, какого значения (интенсивности) достигает напряжение вблизи вершины трещины в момент разрушения. Он связывает приложенное среднее напряжение с критической длиной трещины:
К\с - crcpV/a7dKp, (8.3)
где a — безразмерный коэффициент, характеризующий геометрию трещины.
Из соотношения (8.3) следует, что единица измерения К\с —
МПа-м1/2.
Значение К\с определяют экспериментально на образцах с надрезом и с заранее созданной на дне этого надреза усталостной трещиной (рис. 8.3). Для расчета К\с при нагружении образца фиксируют усилие в момент подрастания трещины на некоторую длину и перехода ее к нестабильному распространению.
Значение К\с зависит от степени пластической деформации у вершины трещины (ее затуплении) и характеризует сопротивление развитию вязкой трещины. По этой причине критерий К\с называют вязкостью разрушения. Чем значение К\с больше, тем выше сопротивление материала вязкому разрушению и его надежность. Кроме качествен ной характеристики надежности, К\с дополняет параметры ctq2 и Ь" при
|
<кр ' * кр
Рис. 8.3. Образец для определения критерия К\с |
Рис. 8.4. Зависимость критического напряжения <т от размера дефекта / для двух материалов (/ и //) с разным значением К1с (КЦ > К(с)
асчетах на прочность деталей из высокопрочных материалов (сталей с в > 1200 МПа, титановых сплавов с ав > 800 МПа и алюминиевых спла-ов с ав > 450 МПа). Этот критерий позволяет определить безопасный азмер трещины при известном рабочем напряжении или, наоборот, бе-эпасное напряжение при известном размере дефекта. Например, при ра-очем напряжении ар (рис. 8.4) трещина длиной / будет безопасной для атериала II и вызовет разрушение в материале /, имеющем меньшее тачение К1с (К{с < #//).
Для оценки надежности материала используют также следующие па-аметры: ударную вязкость КСУ1ялн КСТ2, температурный порог хлад-эломкости t$Q3. Однако это качественные, непригодные для расчета на рочность, параметры.
Параметром KCV оценивают пригодность материала для сосудов да-тения, трубопроводов и других конструкций повышенной надежности.
Параметр КСТ, определяемый на образцах с трещиной усталости у :нования надреза, более показателен. Он характеризует работу развития зещины при ударном изгибе и оценивает способность материала тормо-[ть начавшееся разрушение. Если материал имеет КСТ = 0, то это начает, что процесс его разрушения идет без затраты работы. Такой гтериал хрупок, эксплуатационно ненадежен. И, наоборот, чем больше
Ударная вязкость, определенная на образце с V-образным концентратором при мнатной температуре.
То же на образце с усталостной трещиной. ' Температура, соответствующая равным долям (50 %) хрупких и шпикучастке») '■рушения в изломе при определении ударной вязкости.
параметр КСТ, определенный при рабочей температуре, тем выше надежность материала н условиях эксплуатации. Так же как и К\с, КС'1 учитывают при выборе материала для конструкций особо ответственного назначения (летательных аппаратов, роторов турбин и т.п.).
Порот хладноломкости характеризует влияние снижения температуры на склонность материала к хрупкому разрушению. Его определяют но результатам ударных испытаний образцов с надрезом при понижающейся температуре. Сочетание при таких испытаниях ударного нагруже-ния, надреза и низких температур — основных факторов, способствующих охрупчиванию, важно для оценки поведения материала при экстремаль пых условиях эксплуатации.
О пригодности материала для работы при заданной температуре; судят по температурному запасу вязкости, равному разности температуры эксплуатации и 150- При этом, чем ниже температура перехода в хрупкое состояние по отношению к рабочей температуре, тем больше температурный запас вязкости и выше гарантия от хрупкого разрушения.
На рис. 8.5 показан случай, когда ударная вязкость двух сталей при температуре эксплуатации, равной 20°С, одинакова. Однако переход в хрупкое состояние стали 1 (мелкозернистой) заканчивается при — 40 °С, а стали 2 (крупнозернистой) при 0°С. По сравнению с температурой эксплуатации температурный запас вязкости у стали 1 составит 60 °С, а у стали 2 лишь 20°С. Сталь 1 более надежна в работе, так как возможное понижение температуры эксплуатации относительно расчетной при наличии трещин и ударной нагрузки не вызовет в ней хрупкого разрушения.
Долговечность — свойство материала сопротивляться развитию по-i тененного разрушения (постепенного отказа)1, обеспечивая работоспособность деталей в течение заданного времени (ресурса). Причины по-и'ри работоспособности (постепенного отказа) разнообразны: развитие
|
Рис.. 8.5. Зависимость ударной вязко
стиот температуры испытания мел
козернистой (1) и крупнозернистой (S)
стали (0,22 % С):
<-- ► температурный запас вязкости
Постепенный отказ потеря материалом работоспособности, при наступлении
кишрой дг|али заменяю т без угрозы аварийных последствий.
процессов усталости, изнашивания, ползучести, коррозии, радиационного разбухания и др. Эти процессы вызывают постепенное накопление необратимых повреждений в материале и его разрушение. Обеспечение долговечности материала означает уменьшение до требуемых значений скорости его разрушения.
Для большинства деталей машин (более 80 %) долговечность определяется сопротивлением материала усталостным разрушениям (цикличе-:кой долговечностью) или сопротивлением изнашиванию (износостойко-:тью).
Циклическая долговечность характеризует работоспособность материала в условиях многократно повторяющихся циклов напряжений. Она гем выше, чем ниже скорость зарождения и скорость развития трещины усталости.
Износостойкость характеризует сопротивление материала разруше-iHio поверхности путем отделения его частиц под воздействием силы тремя. Износостойкость оценивают величиной, обратной скорости изнашивания.
Долговечность деталей, работающих при высоких температурах (детали энергетических установок, реактивных двигателей), определяется :коростью ползучести — скоростью развития пластической деформации 1ри постоянном (ниже предела текучести) напряжении. Ограничение ско->ости ползучести достигается применением жаропрочных материалов.
Долговечность деталей, работающих в атмосфере нагретых сухих га-ов или жидких электролитов, зависит соответственно от скорости хи-1ической или электрохимической коррозии. Работоспособность в таких редах сохраняют жаростойкие и коррозионно-стойкие материалы.
Таким образом, работоспособность материала детали в условиях экс-[луатации характеризуют следующие критерии конструкционной прочно-ти:
1) критерии прочности <тв, сто,2> ^-Ь которые при заданном запасе :рочности определяют допустимые рабочие напряжения, массу и размеры ;еталей;
2) модули упругости Е, G, которые при заданной геометрии детали пределяют величину упругих деформаций, т.е. ее жесткость;
3) пластичность 6, ф, ударная вязкость КСТ, KCV, KCU, вязкость азрушения К\с, порог хладноломкости <50, которые оценивают надеж-ость материала в эксплуатации;
4) циклическая долговечность, скорости изнашивания, ползучести, оррозии, определяющие долговечность материала.
Дата добавления: 2018-04-05; просмотров: 737; Мы поможем в написании вашей работы! |
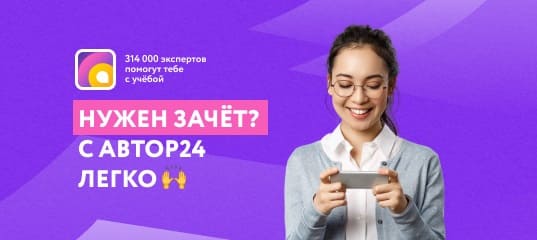
Мы поможем в написании ваших работ!