Изоляция деталей при хромировании?
Участки детали, не подлежащие хромированию, а также подвески, за исключением мест контактов, должны быть изолированы.
Пористое хромирование?
Пористое хромирование. Плотные осадки хрома неудовлетворительно смачиваются маслами. Если детали работают при смазке, не исключающей возникновения кратковременного сухого трения, то применять плотное хромирование не рекомендуется. В этом случае применяют пористое хромирование (канальчатое, точечное). Сначала деталь хромируют, а затем производят дехромирование (анодное травление). Активно растворяются участки, расположенные вдоль сетки трещин, и пассивно - гладкие участки поверхности. Глубина пор 0,03...0,06 мм контактов, должны быть изолированы. Для изоляции применяют лаки (цапонлак, эмалит, перхлорвиниловый и др.), липкие ленты, фольгу и другие материалы.
Подслой при декоративном хромирован?
Блестящий хром недостаточно плотен, трещиноват. Это вынуждает коррозионно-стойкие покрытия получать с подслоями меди и никеля. Например: автомобиль "Волга" - медь (2...3 мкм), никель (5...10 мкм); хром (1...2 мкм); представительские автомобили - никель, медь, никель, хром.
Какие детали можно ремонтировать хромированием?
Декоративное хромирование.
Применяется для бамперов, декоративных решеток, штабиков (закрывают стыки панелей), молдингов (облицовка на радиаторе), дверных ручек и т.д
Из каких материалов готовят электролит для железнения? Тип электролита?
|
|
Электролиты. Наиболее полно требованиям производства удовлетворяют горячие хлористые электролиты простейшего состава (без добавок). Исходными материалами для его приготовления являются хлористое (двухвалентное) железо РеСЬ • 4Н2О и соляная кислота НСl. В промышленности электролит готовят путем травления стальных стружек в соляной кислоте.
Какой электролит применяется для получения твердых покрытий при железнении? Предельная толщина покрытия?
Малоконцентрированный электролит (РеС12 - 200. ..220 г/л) при температуре 60...80°С и плотности тока 30... 5 0 А/дм2 обеспечивает получение плотных и гладких покрытий высокой твердости 4500.. .6500 МПа (450...650 кгс/мм2), толщиной 0,8. ..1,5 мм.
Какой электролит применяется для получения мягких покрытий при железненни? Предельная толщина покрытия?
Высококонцентрированный электролит (600...680 г/л) при высокой температуре (75...95°С) и невысокой плотности тока обеспечивает получение мягких твердостью 200...2000 МПа и вязких покрытий толщиной 2...3 мм и более. В этом электролите могут быть получены и твердые покрытия до 6000 МПа, но покрытия более шероховатые, чем из электролитов с меньшей концентрацией железа.
|
|
Область применения мягких покрытий при железнении?
Мягкие покрытия (НВ 120...300) применяют для наращивания неответственных поверхностей (например, наружной поверхности бронзовых втулок); для покрытия пластинок из твердого сплава для облегчения припайки к инструментам; изготовления медножелезных электродов; для ремонта ответственных поверхностей деталей с последующей химико-термической обработкой или хромированием.
Область применения твердых покрытий при железнении?
Детали вращения - клапаны, толкатели, вал рулевой сошки, валы и оси насосов (водяного, масляного, гидроусилителя), шкворень, вал педали сцепления, вал коробки передач, ведущая коническая шестерня, распределительный вал, разжимной кулак тормозов и др.
Детали сложной конфигурации - чашка коробки дифференциала, поворотный кулак, крестовины, коленчатые валы (в основном, гнезда подшипников шариковых и роликовых).
Чем руководствуется технолог при выборе твердости покрытия (при железнении)?
Следует помнить, что оптимальная твердость поверхности детали, обеспечивающая высокую износостойкость, во многом зависит от материала сопряженной детали (определяется опытным путем): В условиях недостаточной смазки предпочтительно применять пористые железные покрытия.
|
|
Сравните технико-экономические показатели железнения и хромирования?
Чем отличаются технологические процессы железненя и хромирований?
Особенности технологического процесса (в сравнении с хромированием)При подготовке деталей к осаждению твердого железа основное отличие в особенностях анодного травления (электрохимической подготовке). Дело в том, что после анодного травления в процесса промывки деталей и переносе их в ванну электролиза железо успевает несколько окислиться (в течение 3 с пребывания на воздухе образуется окисный слой толщиной 14А), что снижает прочность сцепления электролитического железа с деталью. На этот период необходимо пассивировать поверхность детали.
Дата добавления: 2018-02-28; просмотров: 885; Мы поможем в написании вашей работы! |
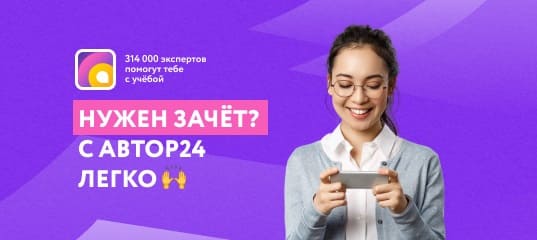
Мы поможем в написании ваших работ!