Kaк производится раскисление металла шва при сварке и плавке в средне CO2?
Таким образом, при сварке в среде СО2 необходимо предусматривать меры по раскислению наплавленного металла. В основном в качестве раскислителей используют кремний (0,6...1,0 %) и марганец (1...2 %), включаемые в состав электродной проволоки. Раскисление окислов железа идет по реакциям:FeO+Mn->MnO+Fe, 2FeO+Si->SiO2+2Fe. Образующиеся в процессе раскисления окислы кремния и марганца всплывают и скапливаются на поверхности сварочной ванны в виде шлак
Номенклатура ремонтируемых деталей в среде СО2?
Механизированную наплавку, в основном, применяют для восстановления деталей диаметром 10... 30 мм, а также, для наплавки глубоких отверстий, когда трудно применить другие способы. Многие детали, восстанавливаемые наплавкой под флюсом, могут, быть отремонтированы наплавкой в среде углекислого газа (резьбы, шейки под сальники, под подшипники).
Углекислый газ сварочный (ГОСТ, свойства, хранение)?
Углекислый газ СО2 поставляется в сжиженном состоянии в баллонах типа А вместимостью 40л под давлением 5,0... 5,5 МПа (заливается 25 кг жидкой углекислоты, при испарении обеспечивается отбор 20... 25 дм3/мин газа для сварки). Баллоны с углекислотой окрашивают в черный цвет с желтой надписью "СО2 сварочный". Сварочная углекислота высшего сорта имеет чистоту 99,8 % и первого - 99,5 %. После дополнительной очистки можно использовать и пищевую углекислоту. Для удаления -примесей воздуха рекомендуется перед сваркой выпускать первые порции газа в атмосферу (СО2 примерно в 1,5 раза тяжелее воздуха). А затем для снижения влажности углекислого газа устанавливают баллоны вентилем вниз. После отстаивания в течение 10... 15 мин осторожно открывают вентиль и выпускают из баллона влагу. Часть влаги задерживается в углекислоте в виде водяных паров, ухудшая при сварке качество шва. При выходе из баллона от резкого расширения происходит снижение температуры углекислого газа, и влага, конденсируясь в редукторе, забивает каналы. Чтобы предотвратить замерзание влаги, между баллоном и редуктором устанавливают электрический подогреватель (36В). Окончательное удаление влаги после редуктора производиться в осушителе (лучше использовать сели-кагель марки ШСМ - микропористый S1O2; прокаленный при температуре 300°С в течение 2ч) редуктор РК-53 понижает давление газа до рабочего давления 0,1.. .0,4Мпа. Одного баллона газа по опыту ремонтных предприятий хватает на 60.. .70 часов работы.
|
|
Почему сварку а среде СО2 можно применять для ремонта тонколистовых деталей?
Очень широкое распространение получила полуавтоматическая дуговая сварка в среде при ремонте кузовов, кабин, рам, т.е. при ремонте тонколистовых деталей. Почему? Углекислый газ обладает парниковым эффектом, тепловой к.п.д. дуги повышается с 0,28 (ручная сварка плавящимся электродом) до 0,70. Поэтому силу тока можно снизить до 60...100А (при ручной сварке 180...240А), что позволяет варить тонколистовую сталь кузовов.
|
|
162. Электролиз подчиняется законам Фарадея: Q = Clr, объясните формулу?
Положительные свойства хромирования?
Высокая твердость, низкий коэффициент трения и химическая стойкость электролитического хрома способствуют его высокой износостойкости. При правильно выбранных условиях нанесения и эксплуатации хромового покрытия износостойкость стальных деталей возрастает в результате хромирования примерно в три-пять раз больше.
Отрицательные свойства хромирования?
Отрицательные стороны хромирования:
- гладкий хром имеет плохую смачиваемость (повышается пористым хромированием на период приработки деталей);
- осадки хрома характеризуются высокими внутренними напряжениями. Усталостная прочность стали в результате понижается (при толщине слоя хрома 0,2 мм на 30...40%). Хромированные детали, работающие при знакопеременных нагрузках,' целесообразно подвергать термической обработке при температуре 150..200°С. При этом из хрома удаляется до 2/3 содержащегося в нем водорода и уменьшается хрупкость покрытия. Для более полного удаления водорода температура нагрева должна быть повышена до 400...500°С;
- низкий к.п.д. хромовых ванн (12... 15%);
- возможность восстановления деталей с относительно небольшим износом (менее 0,3...0,4 мм). Если деталь воспринимает ударные нагрузки, то толщина хромирования не более 0,05...0,08 мм;
- сложность подготовительных работ.
Дата добавления: 2018-02-28; просмотров: 594; Мы поможем в написании вашей работы! |
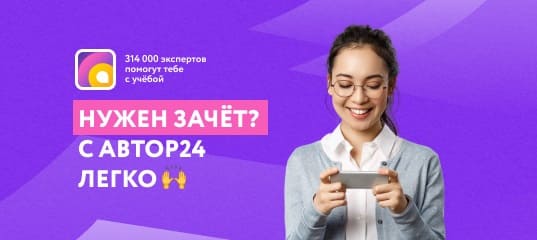
Мы поможем в написании ваших работ!