Выбор режима сварки (ручной электродуговой)?
Ответы на вопросы.
- Понятия о надежности изделий.
Надежность- свойство объекта сохранять во времени в установленных пределах значения всех параметров, характеризующих способность выполнять требуемые функции в заданных режимах и условиях применения, технического обслуживания, хранения и транспортирования.
- Понятия о долговечности изделий.
Долговечность- свойство автомобиля сохранять работоспособное состояние до наступления предельного состояния при установленной системе технического обслуживания и ремонта.
- В чем заключается сущность ремонта деталей?
Сущность ремонта автомобилей (агрегатов, узлов)заключается в экономически целесообразной реализации остаточной долговечности деталей по прочности.
- С какай долговечностью детали ремонтируются и заменяются на новые?
По прочностным свойствам детали автомобиля (или рабочие поверхности деталей) делятся на 2 вида: долговечные (70...75 %) и ограниченно долговечные (остальные). Долговечные, в свою очередь, делятся на 2 группы: первая имеет срок службы, близкий к пробегу до КР (капитального ремонта), вторая - выше нормативного. Ограниченно долговечные детали при КР, как правило, не ремонтируют (заменяют на новые). Учитывая быстрое старение пластмасс, резиновых деталей, обивочных материалов (2,5...3 года), повторное их использование не целесообразно. Не ремонтируют также неразборные узлы (например, свечи зажигания). Долговечные детали могут быть восстановлены несколько раз. Например, коленчатый вал двигателя ЗИЛ-130 имеет 8 ремонтных размеров; ГАЗ-53, ГАЗ-24 - 6 ремонтных размеров; автомобилей ВАЗ - 4 ремонтных размера. В случае необходимости шейки коленчатого вала можно наплавить (есть и другие методы восстановления).
|
|
- Причины низкого качества ремонта?
В советское время не удалось добиться высокого качества ремонта автомобилей (агрегатов, узлов) из-за отсутствия конкуренции между ремонтными предприятиями. Низкому уровню качества способствует и широко распространенный на специализированных предприятиях обезличенный метод ремонта(детали и сборочные единицы не сохраняют при ремонте принадлежность к определенному объекту):
- нарушается приработанность высокоресурсных сопряжений;
- обезличивание деталей - одна из причин большого числа выполняемых КР за срок службы агрегата, что, в конечном счете, приводит к значительному росту затрат на поддержание его работоспособности в процессе эксплуатации;
- полная неопределенность в ресурсах элементов вновь собранных агрегатов; отказ может наступить в любой момент и повлечь за собой значительные потери.
|
|
- Какую минимальную долговечность должны иметь агрегаты после кап. ремонта?
Действующие нормативы требуют, чтобы долговечность отремонтированных автомобилей, агрегатов, узлов была выше 80 % от долговечности, установленной автозаводом.
- Основные отличия АРП от машиностроительного?
1) большой объем разборочных, моечных и очистных работ (15 %);
2) наличие нескольких маршрутов технологии ремонта для одной и той же детали;
3) нестабильность исходного сырья - ремфонда;
4) наличие сложных дефектовочных работ;
5) большой удельный вес высококвалифицированного труда;
6) для управления производством приходится пользоваться информацией в несколько раз большей, чем на автомобилестроительном заводе, которая зачастую носит вероятностный характер (нестабильность ремфонда, нестабильность поступления и т.п.).
- Комплектность двигателей и грузовых автомобилей, принимаемых на кап. ремонт?
Первая комплектность установлена для автомобилей-тягачей, пассажирских; силовых агрегатов в сборе, дизельных и бензиновых двигателей. До 1976 года бензиновые двигатели сдавались в ремонт первой и второй комплектности (без приборов питания, электрооборудования и других навесных механизмов). До сих пор есть АРП, ремонтирующие двигатели второй комплектности. Грузовые автомобили сдаются в ремонт первой и второй комплектности. Автомобили первой комплектности - с кузовами, кабинами, платформами, со всеми составными частями, включая запасное колесо, без комплекта инструментов. Второй комплектности - без платформы, кузовов, специального оборудования и деталей их крепления на шасси. Кабины грузовых автомобилей также имеют две комплектности. В ГОСТе установлена комплектность для 43 агрегатов и узлов.
|
|
- Какие документы нужно иметь для сдачи в кап. ремонт двигателей и автомобилей?
технический паспорт автомобиля; паспорта и карточки на баллоны; паспорта на ранее отремонтированные автомобили и двигатели.
- С какими дефектами не принимается в кап. рем. грузовой автомобиль?
- грузовые - если кабина в сочетании с рамой подлежат списанию;
- автобусы, легковые - если кузов подлежит списанию.
При приемке автомобилей в КР относят к категории подлежащих списанию:
рамы - при наличии на любой из продольных балок (лонжеронов) одного и более из пере численных дефектов:
- двух и более трещин, включая заваренные;
- более одной накладки, приваренных внахлестку;
|
|
- более трех вставок, приваренных встык, или вставок общей длиной свыше 1500 мм;
- деформации, не поддающейся устранению правкой;
- С какими дефектами не принимается в кап. рем. легковой автомобиль?
кузова легковых автомобилей и грузопассажирских - при наличии двух и более из пере численных дефектов, являющихся следствием коррозионного разрушения:
- глубокая коррозия всего основания;
- разрушение основания по всему периметру;
- коррозия передней панели боковины, захватывающая стойку ветрового окна и часть пола;
- разрушение основания центральных стоек, захватывающее части пола;
- глубокая коррозия задней поперечины.
- С какими дефектами не принимается в кап. рем. автобус?
Кузова автобусов - при наличии более 60 % негодных ферм, шпангоутов и облицовки (шпангоуты - поперечные дуги в кузове, фермы - поперечины в основании кузова).
- Сущность процесса очистки детали?
Жировые отложенияпо химическим свойствам разделяют на 2 основных группы: омыляемые и неомыляемые. К омыляемым относят жиры органического происхождения. При действии на эти жиры щелочного раствора образуется мыло, легко растворимое в воде. К неомыляемым жирам относятся масла минерального происхождения. Они растворяются в керосине и бензине. Со щелочами образуют эмульсии в виде мельчайших капелек. Добавляя к щелочным растворам эмульгаторы, можно собрать отдельные жировые капельки и осадить их из раствора.
- Трехстадийная очистка (на примере ремонта грузового автомобиля)?
1) Наружная мойка автомобиля, агрегатов.
2) Очистка подразобранного автомобиля. С автомобиля снимаются:
а) платформа; б)кабина; в) колеса; г) приборы питания и электрооборудования (очистка на участках ремонта приборов питания и электрооборудования).
3) Разборка на агрегаты.
4) Очистка подразобранных агрегатов.
5) Разборка агрегатов.
6) Очистка деталей.
7) Дополнительная очистка некоторых деталей:
а) очистка от нагара; б) накипи; в) консистентных смазок; г) смолистых отложений; д) коррозии; е) очистка масляных каналов; ж) удаление старой краски.
- Две стадии моющего действия СМС?
Механизм действия Моющего раствора сложен и состоит из двух стадий:
1) смачивать поверхности и переводить во взвешенное состояние частицы загрязнений в виде эмульсии или суспензии;
2) процесс стабилизации;
Процесс смачиванияпри моющем действии имеет вид коллоидного растворения (солюбилизации), т.е. самопроизвольного перехода нерастворимых частиц в раствор. ПАВ (поверхностно-активные вещества, добавляемые к щелочи) создают в растворе особые комплексы, состоящие из многих тысяч атомов, молекул и ионов (мицеллы).
Процесс стабилизациисложен и заключается в придании дисперсным системам агрегативной устойчивости. Стабилизация достигается вводом в раствор стабилизаторов (диспергаторы, эмульгаторы, пенообразователи). Под их действием мицеллы оседают на дно моечной машины.
- Недостатки NaOH при очистке детали?
1) разрушает детали из легких сплавов;
2) коррозия деталей из тонколистовой стали;
3) слабые стабилизирующие свойства;
4) нельзя мыть одновременно черные и цветные металлы;
5) оказывает вредное воздействие на человека (разъедает кожу, особенно опасно попадание в глаза). Спецодежда рабочего: резиновые сапоги, резиновые перчатки, очки, брезентовая одежда. Повышенные требования к вентиляции, чтобы пары щелочного раствора не попадали в воздух.
- Для каких целей применяется каустическая сода в ремонтной практике?
В настоящее время щелочныемоющие средства (каустическая сода NаОН, кальцинированная сода Nа2СОЗ, и др.) применяются в ремонтной практике редко, в основном, для снятия старой краски с кузовов, кабин, рам.
- Положительные стороны СМС?
1) нетоксичные, негорючие, пожаробезопасные и хорошо растворяются в воде;
2) по моющей способности значительно превосходят растворы щелочей (30 %);
3) растворы СМС допускают одновременную очистку деталей из черных, цветных и легких металлов и сплавов.
4) детали после очистки СМС не нуждаются в антикоррозионной обработке. Антикоррозионная защита поверхности обеспечивается силикатами, входящими в состав СМС.
- Положительные и отрицательные стороны РЭС?
РЭС обычно состоят из базового растворителя (керосин, уайт-спирит, хлорированные углеводороды и др.), сорастворителей, ПАВ и небольшого количества воды. РЭС способны быстро (10...30 мин.) очищать сильно загрязненные детали двигателей при комнатных (15...25 градусах), или умеренных температурах (40...50 градусов). Это обеспечивает их большие преимущества по сравнению с СМС, которые требуют нагрева (70...100 градусов), а очистку производят значительно медленнее (в 2...10 раз). Однако РЭС обладают определенной токсичностью или пожароопасностью. Для работы с РЭС можно использовать ванны с герметизированной крышкой и оборудованные местной вентиляцией.
- Механические способы очистки деталей от нагара?
Очищают: выпускные патрубки, клапаны, головки цилиндров, поршни, пружины клапанов.
Наиболее простой способ - применяют металлические щетки (капроновые или из малоуглеродистой стали). Для медных деталей — из латунной проволоки. Диаметр проволоки - 0,3...1,0 мм. Используют электрические или пневматические машинки, п=1500...3000 мин"1.Дробеструйная очистка. Используют металлический песок (чугун) - дробь ДЧК, ДСК, ДСЛ (размер 0,3...1,0 мм). В аппарат АД-3 загружается 15 кг песка, давление воздуха — 0.5...0.7 МПа . Производительность - 1...2 м/ч. Отверстия, каналы необходимо заглушать и тщательно промывать после очистки.
Галтовочные барабаны. Качественную очистку мелких деталей (клапанов, нормалей и др.) можно осуществить во вращающихся барабанах с жидким наполнителем (СМС). Барабан загружают на 75 % объема, п=16...18 мин "' . Загружают иногда фарфоровую крошку (1/3), грануляция - 6...15 мм. Для очистки мелких деталей могут применяться установки шнекового типа.Виброабразивная очистка. Контейнеру сообщается колебательное движение. Оптимальная частота колебаний — 2500...2700 Гц при амплитуде 1,5...2 мм. Эффект создает взаимодействие механической энергии и физико-химических свойств моющего раствора (СМС + синтетическая или фарфоровая крошка). Установка ОМ-3025 имеет дебалансовый вибратор (вращаются два маховика; прикрепленные грузы создают центробежную силу Fц, встряхивающую контейнер с нужной частотой). Ёмкость контейнера — 100л. Производительность за 1 час: 200 клапанов, 300 клапанных пружин, 15 трубопроводов (впускных или выпускных), 400 кг метизов (метизы очищаются без абразива).
- Химико-термическая очистка (в расплаве солей) деталей от нагара?
Химико-термическая очистка. Этот способ по производительности и качеству очистки от нагара и других загрязнений превосходит все другие. ГОСНИТИ рекомендует соляную ванну: NaOH — 60...65 %, NaNO3 — 30...35 %, NaCl — 5 %, t = 400±10 градусов, т = 5...10 мин. Установка ОМ-4265 имеет 4 камеры, расположенные в линию (имеется на Семипалатинском АРЗ).Перед погружением в расплав солей детали выдерживают 1 ...2 минуты над поверхностью для удаления влаги. Загрязнения на деталях сгорают, поэтому над поверхностью видны языки пламени, черный дым. Прекращение их — очистка закончена.Затем детали попадают в камеру с проточной водой, происходит бурное паровыделение (т=5...6 мин.).
Третья камера с кислотным раствором служит для нейтрализации щелочи, оставшейся после промывки, удаления окислов и осветления. Cталь/чугун: 50 % ингибированная НС1, t=50...60 градусов, т = 5...6 мин. Затем промывка в 4-й камере: Na2CO3 — 3...5 г/л, Na3PO4 — 2г/л, t = 80...90 град., т = 5...6 мин. Если очищается сталь + А1, то состав раствора в 3-й камере: Н3РО4 — 85 г/л, СЮ3 — 125 г/л, t=85...95 град, т=5...6 мин. Если А1 сплав: 10 % HNO3, t=20 град, т = 5...6 мин. Соляная ваннавмещает 1т расплава. Разогревается от 20 град, до 400 град. ± 10 град, в течение 6 часов. В конце рабочей недели температуру снижают до 250 град, (недостатком этого способа очистки являются большие затраты энергии). В одной тонне расплава можно очистить 30...40 т. деталей.
- Очистка системы смазки двигателей?
Технологический процесс:
1) выварка блоков, коленвалов, шатунов в щелочном растворе 1...3 часа. Происходит размягчение смолистых отложений;
2) очистка каналов ершами (проволочными, волосяными);
3) промывка пульсирующей струей моечного раствора, р=0.15...0.2 МПа . Используются установки ОМ-3600, АКТБ-160 и др.
- Очистка системы охлаждения двигателей (чугунные блоки)?
Очистка системы охлаждения двигателей (удаление накипи).В состав накипи входят карбонаты и сульфаты Са и Mg и силикаты (SiO2). Наиболее эффективным является способ удаления накипи в кислотных растворах.
Для черных металловиспользуется раствор ингибированной соляной кислоты. Очистка производится прокачкой (циркуляцией) или погружением блоков в раствор. Погружением: 10... 15 % НС1, t = 40...60 градусов, т = 20...30 мин.
Затем производится нейтрализация кислоты в щелочной ванне: Nа2СО3 -10г/л, NaNO2 (ингибитор) — 3...5 г/л, t = 60...70 градусов, т = 5...7 мин. Для ускорения очистки — прокачка (также двойная): р = 0.1 МПа , т = 3...10 мин.
Сложность изготовления: ванна винипластовая, фарфорованный насос (для перекачки кислот), трубы полистироловые, штуцеры из оргстекла.
- Очистка системы охлаждения двигателей (алюминиевые блоки)?
Для очистки блоков цилиндров из алюминиевых сплавовприменяется раствор фосфорной кислоты - 100 г/л и хромового ангидрида - 50 г/л, t = 60...70 градусов. При большом отложении накипи блоки на 2 часа погружают в 5 % раствор азотной кислоты при t = 20 градусов.
- Очистка радиаторов?
Для очистки радиаторовиспользуется установка М-2024 (ГАЗ, ЗИЛ, МАЗ). Применяется NaOH - 100 г/л или контакт Петрова - 500 г/л, t = 70...80 градусов. Затем - споласкивание. При большом загрязнении отпаивают бачки и производят шомполирование.
- Очистка топливных баков?
Очистка топливных баков. Очистка и дегазация баков производится паром (р=0.2...0.4 МПа , t=120...140 град.) или горячей водой. Бак считается взрывобезопасным, если на внутренней поверхности нет следов топлива, а концентрация паров нефтепродуктов меньше 0,3 мг/л воздуха. Используется установка М-2030 Гипроавтотранса или пароводоструйный очиститель ОМ-3360 или водоструйный ОМ-5179 и ОМ-5181 ГОСНИТИ. Концентрация паров определяется прибором УГ-2.
- Применение ультразвуковых колебаний для очистки?
Широкое внедрение УЗ-очистки ограничивается из-за сравнительной дороговизны и сложности УЗ-генераторов. Поэтому применение УЗ рентабельно пока для обработки сложных и дорогостоящих узлов, деталей. Под воздействием УЗ-колебаний жидкость постоянно испытывает сжимающие и растягивающие усилия. Многие жидкости легко "переносят" большие всесторонние сжатия, однако они очень чувствительны к растягивающим усилиям (фаза разрежения). Жидкость как бы "разорвана" и в ней образуется множество мельчайших полостей (пузырьков). В момент захлопывания кавитационного пузырька образуется ударная волна, которая создает давление в сотни атмосфер. Ударная мощность - 2...5 Вт/см2 при частоте 8...12 кГц. Всякая установка состоит из трех основных элементов: УЗ-генератора (источника электрических колебаний), преобразователя электрических колебаний в упругие механические магнитострикционного типа, ванны для очистки.
- Недостатки моечных машин струйного типа?
Недостатки:
1) недостаточное качество очистки деталей сложной формы от смолистых отложений ( картер двигателя, кожух маховика, узлы и детали системы смазки и др.);
2) необходимость подводить тепло (как правило, это пар) для поддержания температуры 80...85 градусов Цельсия. Контактируя с холодной деталью, и при разбрызгивании струи, моющий раствор быстро охлаждается. При температуре 60 градусов моющая способность уменьшается в 1,5...2,0 раза;
3) применение более эффективных растворителей для удаления АСО возможно только в ваннах (охрана труда!).
- Положительные и отрицательные стороны моечных машин ванного типа?
Положительные стороны:простота конструкции, низкая энергоемкость, доступность и удобство обслуживания, возможность использования разнообразных моющих средств, высокая эффективность очистки труднодоступных поверхностей. Широко используются подобные установки и в других странах (например, типа Rewel в Англии). Общий недостаток всех очистных машин ванного типа - в конструкции требуются специальные механизмы для создания давления. В струйных машинах этот недостаток отсутствует, (давление обеспечивается подбором насоса и диаметра сопел).
- Способы создания давления в моечных машин ванного типа?
1) в установке ОМ-7627, предназначенной для очистки двигателей в сборе, активация производится сжатым воздухом. Двигатель выдерживается в растворе с температурой 85...95 градусов Цельсия в течение 40...50 минут, после чего в картерные полости двигателя на 15...20 минут подаётся сжатый воздух (0.3...0.4 МПа). Общее содержание загрязнений на внутренних поверхностях снижается в 4...7 раз. Применение сжатого воздуха целесообразно, если его энергия используется направленно, а не рассредоточивается по всему объему раствора;
2) в моечной установке ММЧ-1 для активации раствора используется лопастной винт с одновременным вращением деталей поворотным столом;
3) на ряде ремонтных заводов применяются ванны с качающейся платформой (есть и на БАРЗ);
4) широко применяются ванны с вращающейся крестовиной, к шипам которой подвешиваются люльки с деталями, агрегатами, автомобилями. На некоторых крестовинах ("мальтийский крест") люльки могут смещаться вдоль шипов, что удлиняет контакт деталей, агрегатов с раствором (движение люлек происходит тогда по эллипсу).
- Перечислите основные положения организации разборочных работ?
Основные положения, которые необходимо соблюдать при организации производственного процесса:
1) высокое качество очистки автомобилей, агрегатов, поступающих на посты разборки;
2) полная разборка агрегатов и узлов. Ряд узлов, сопряжений на предприятиях не разъединяют, например, ступицы и кольца роликовых подшипников, ступицы и тормозные барабаны, тормозные диски и кронштейны осей тормозных колодок, регулируемые рычаги, ведомую коническую и цилиндрическую шестерни и др. - в итоге затрудняется дефектовка деталей этих сопряжений и снижается качество ремонта;
3) сохранность деталей при разборке - первостепенное значение в экономике АРЗ (теряется до 4% от стоимости деталей). Результат некачественной разборки - срыв резьбы, забитость торцов валов, погнутость деталей, трещины и обломы специфичность разборки (загрязнение, коррозия) психологически затрудняет исполнителя свыкнуться с необходимостью не портить детали при разборке;
4) обоснованное нормирование. Отсутствие обоснованной нормы времени на расчленённые операции. Пользуются на предприятиях, в основном, укрупнёнными нормами;
5) научная организация разборки агрегатов:
- высокий уровень технического оснащения оказывает влияние на организацию работы, условия труда и его трудоёмкость;
- поточный метод производства. Сосредоточение одноименных технологических операций на определенных постах позволяет сократить количество применяемых инструментов (~ 35 %), повышается интенсивность использования технологической оснастки (~ 50 %). Специализация плюс техническое оснащение позволяют повысить производительность труда на 20 %. На предприятиях с годовой программой 1...4 тыс. приведённых КР применяются многопредметные поточные линии;
- комплексная механизация основных и вспомогательных работ;
- наличие специальной оборотной тары резко сокращает время на погрузо-разгрузочные работы;
- обеспечение складирования возле рабочих мест;
- рациональная организация рабочих мест;
6) Качество ремонтируемой продукции зависит не только от технических, технологических и организационных мероприятий, но и от системы взаимосвязей «человек—производство». Установлено, что к концу смены большинство показателей функций, характеризующих состояние организма, резко ухудшаются. Например у рабочих разборочного цеха продолжительность зрительно - двигательной реакции в конце рабочего дня увеличивается на 40 %, скрытый период рече-двигательной реакции - на 24 %, энергозатраты - на 25 %, тремор (дрожание пальцев) — на 45 %. Всё это говорит о развитии значительного утомления исполнителей в процессе работы, вследствие чего нарушается динамический стереотип (система условных и безусловных рефлексов, выработанных в ходе тренировки, обучения и обеспечивающая точное и быстрое выполнение работы), что приводит к снижению эффективности труда и ухудшению качества продукции. Исследования показали, что наибольший удельный вес среди рекламационных изделий имеют те, которые изготавливают после обеденного перерыва и особенно в конце смены.
- Как обеспечить сохранность деталей при разборке?
Повышение производительности труда и сохранность деталей при разборке резьбовых соединений достигаются путем широкого применения механизированного инструмента (гайковертов, отверток). Следует учитывать крутящий момент, необходимый для отвёртывания гайки (болта), диаметр резьбы, а также положительные и отрицательные особенности электрического, гидравлического и пневматического инструмента.
- Механизация разборочных работ?
Механизация разборочных работ.Разборочные работы на АРП занимают значительный удельный вес (~11 %) от общей трудоёмкости ремонта. Этот вид работ трудно поддаётся механизации, а тем более автоматизации.
На крупных ремонтных предприятиях применяют поточно-механизированный способ разборки автомобилей. В этом случае используют тяговые или несущие конвейеры, кантователи рам с мостом (с перевёрнутой рамы удобно снимать мосты с рессорами и др. сборочные единицы). Конвейеры оснащают гидравлическими установками с силовыми головками и комплектами съёмников для каждого поста разборки. В значительной- степени снижается трудоёмкость и повышается производительность труда при использовании многоместных стендов для разборки коробок передач, компрессоров и др. Некоторые составные части автомобилей, например, сцепление, рулевые механизмы разбираются на одноместных стендах и приспособлениях с применением механизированных приводов и инструментов.
- Какие задачи должна решать инженерная служба для снижения утомляемости рабочих в разборо-моечном цехе?
Инженерная службадолжна выполнить работы:
1) по нормализации параметров воздушной среды производственных помещений (температура - 21 градус Цельсия, влажность - 60 %, скорость перемещения). В воздух не должны попадать пары бензина, керосина, ацетона, щелочи, а также СО, свинец и др.;
2) работы по снижению уровня производственного шума;
3) работы по улучшению освещённости рабочих мест (75 лк);
4) работы по организации и оснащенности рабочих мест и участков. Необходимо, насколько позволяет существующая технология исключить во время работы позу "стоя" и обеспечить позу "сидя"; позу "нагнувшись" исключить полностью. Необходимо сокращать до предела переходы исполнителей при выполнении операций и перемещении груза вручную. Необходимо обеспечить чистоту рабочих мест, правильный цветовой интерьер, звуковой (музыкальный) фон. Чистота моечных работ должна быть такая, чтобы в дефектовочном отделении можно было работать в белых халатах.
- Особенности контроля деталей на ремонтном предприятии?
Контроль деталей на АРП имеет следующие особенности:
1) в процессе эксплуатации возникают дефекты деталей, которые при изготовлении не встречаются (усталостные трещины, коррозия, выкрашивание металла):
2) количество негодных деталей, выявляемых при дефектовке, в сотни раз больше, чем при изготовлении деталей. Брак при изготовлении — редкое явление;
3) по контролируемым параметрам (те, которые изменяются в процессе эксплуатации ) де-фектуют 100 % деталей. Выборочный контроль недопустим ! ;
4) применяемые в ремонтном производстве предельные размеры деталей не укладываются в систему допусков и посадок ГОСТ;
5) при существующих размерах ремонтных предприятий средства контроля должны быть высокопроизводительными, однако, автоматизация контрольных операций в настоящее время нерентабельна (применяют иногда автоматы для сортировки иголок подшипников и др.).
- Организация дефектовочных работ?
Требования к помещениютакие же, как к лабораторным помещениям. Столы для контролеров должнй быть просторными, металлическими, покрытыми износостойким пластиком. К ним д.б. подведены транспортеры, рольганги, склизы, по которым легко перемещать оборотную тару с деталями. Для крупных деталей желательно предусматривать отдельные посты и для прохождения по участку иметь самостоятельные пути. Так как детали, требующие ремонта, сортируют по маршрутам, то на участке организуется рабочее место для учета выхода деталей, оснащенное ЭВМ. На деталях, годных без ремонта, ставится кислотное клеймо годности (или электрофорезным и др. способами). Детали, требующие ремонта, помечают зеленой (желтой) нитрокраской в тех местах, где замечены дефекты. Забракованные детали маркируют красной масляной краской. Для каждого наименования детали д.б. эталонный образец. Эталоны смазывают техническим вазелином и хранят в специальной яркоокрашенной таре.
- Основные обязанности дефектовщика?
Задача контроля - рассортировать детали на три группы. Совокупность методов и приемов, позволяющих выявить дефекты деталей, носит название дефектоскопии(визуальные методы и методы структуроскопии). Визуальныйметод называют обычно дефектовкой,под которой понимают совокупность приемов для определения наружныхдефектов.При визуальном методе пользуются измерительными инструментами, шаблонами, лупой и др.
- Какие коэффициенты подсчитывают в производственном отделе по дефектовочным ведомостям?
Важное, значение имеет учет результатов работы участка. Заполняются дефектовочные ведомости (по агрегатам), в которых напечатан перечень деталей и их заводские индексы. В результате обработки данных можно получить коэффициенты годности, восстановления (ремонта) и сменности: Kr=nr/N; KB=nB/N; KCM=nCM/N. На основании коэффициентов осуществляется планирование производственной деятельно-сти (ремонт деталей, покупка или изготовление новых деталей). Детали, требующие восстановления, дефектовщик раскладывает по маршрутам ремонта.
- Причины появления усталостных трещин?
Усталостный износ (разрушение металла)- определение условное и обобщенное. Сюда относят поломки деталей под действием знакопеременных или циклических нагрузок, а также так называемый осповидный износ. Можно отметить три стадии в процессе усталостного разрушения деталей: межкристаллитное скольжение, приводящее к упрочнению; зарождение усталостной трещины и ее развитие под действием концентрации напряжений до размеров, приводящих к разрушению детали. На предел выносливости материала оказывает влияние конструктивные факторы (резкие переходы от одного сечения к другому, выточки, канавки, отверстия и т. п.). Технологические (чистота обработки поверхности, остаточные напряжения, влияние покрытий и т. п.). Эксплуатационные (отклонения в соосности опор валов, вызывающих дополнительные напряжения в валу и перегрузку опор; увеличение зазоров, царапин, следы схватывания трущихся поверхностей, налипшие материалы и др.).
- Магнитная дефектоскопия деталей?
Магнитная структуроскопия. Если в детали имеется трещина, она вызывает местное искажение магнитных силовых линий, которые будут видны, если поверхность детали облить магнитной суспензией из магнитной пудры Fe2O3 (прокаленный крокус) и дизельного топлива (1:30...1:50). На кромках трещины появятся магнитные полюса и частички магнитной пудры притянутся к ним. Дефект обнаруживают в приложенном (J=(6...8)d) , А или остаточном магнитном поле (J=(20...25)d), А ; U= 4... 12 В, J до 7000 А (подбирают опытным путем). Магнитоэлектрический дефектоскоп для контроля коленчатых валов МЭД-2 : 0тах=90 мм, Lmax=900 мм, Jmax= 4500 A, U=220 В, t =1,5...2 мин. При обнаружении поперечной трещины на шейке коленвала (магнитные силовые лиши должны пересекать ее) - деталь бракуют. Продольные же трещины с углом к оси вала 20° можно устранить шлифованием под ремонтные размеры. Детали после магнитной структуроскопии необходимо размагнитить, чтобы не скапливали* продукты износа. Два способа размагничивания:
1)деталь проносят внутри соленоида, через который проходит переменный ток (удаляютor торца соленоида на расстояние не менее 0,5 м); 2) деталь помещают в поле электромагнита, который питается переменным током v =1гц; затем силу тока при помощи реостата уменьшают до нуля. Коленвал считается размагниченным, если на хвостовике не удерживается мягкая железная проволока D=1мм и длиной 20 мм.
- Люминесцентный способ структуроскопии деталей?
Люминесцентный дефектоскоп. ЛДА-3 состоит из камер пропитки, мойки, сушки, опыления проявляющим порошком (силикагель - микропористый SiCh) и осмотра в ультрафиолетовых лучах. Детали обезжиривают ацетоном или бензином Б-70 (в керосине нельзя). Затем погружают на 10... 15 мин в флюоресцирующую жидкость. Один из составов: трансформаторное или вазелиновое масло - 0,25 л; керосин - 0,5 л, бензин - 0,25 л, краситель ("дефектоль") - 0,25 г/л. После сушки горячим сжатым воздухом деталь освещают ртутно-кварцевой лампой (ПРК-7, ПРК-4 - переносная) со светофильтром. Трещина дает яркое свечение желто-зеленого цвета.
- Ультразвуковой дефектоскоп?
Ультразвуковой дефектоскоп. Можно выявить границы: воздух - металл; инородные включения - металл. Для ремонтного производства рекомендуется дефектоскоп УЗД-7Н (импульсный метод). Задающий генератор вырабатывает эл. колебания, которые управляют генератором импульсов и схемой развертки луча. Если в шпильке есть трещина глубиной более 2 мм, на экране появится третий импульс (кроме прямого и отраженного).
- Сущность маршрутной технологии ремонта деталей?
Детали, требующие ремонта, имеют, как правило, не один дефект. Так, коленчатый вал ГАЗ-53 (см. "Технические условия на КР ГАЗ-53А") может иметь 14 дефектов. Сочетания (группы) дефектов появляются с определенной вероятностью (изучают на каждом АРП, так как условия эксплуатации автомобилей разные). Под маршрутом ремонтапонимают такое сочетание дефектов на детали, которое определяется их естественной взаимосвязью, единством технологического маршрута и экономической целесообразностью восстановления.
- Преимущества маршрутной технологии ремонта деталей?
- повышается качество восстановления деталей;
- имеется возможность планирования работы по ремонту деталей;
- имеется полная ясность по объему ремонтных работ на складе;
- упрощается процесс нормирования работ и оформление рабочих нарядов (в наряде заранее все расписано, указывается только фамилия исполнителя).
- Основные дефекты гильзы двигателя и причины их появления?
- Основные дефекты шатуна причины их появления?
- Основные дефекты коленчатого вала причины их появления?
- Основные дефекты блока цилиндров причины их появления?
- Основной признак, по которому деталь подлежит выбраковке?
Основной признак, по которому деталь подлежит выбраковке — это развитие в ней дефектов, приводящих к потери прочности и тем самым к исчерпанию долговечности. Поэтому дефекты целесообразно разделить на 2 группы:
- дефекты, приводящие к потере прочности;
- дефекты, приводящие к потере износостойкости;
Для обеспечения высокого качества ремонта автомобилей и агрегатов применять такие способы ремонта деталей второй группы, в результате которых срок службы деталей, как по износостойкости, так и по прочности будет равен оптимальному сроку службы отремонтированного автомобиля или агрегата, т. е. близкий к сроку службы нового автомобиля (не менее 80 %). Ремонт деталей с пониженным ресурсом по износостойкости и прочности вызовет дополнительные расходы на текущие ремонты отремонтированного автомобиля и снизит срок службы такого автомобиля.
- Ремонт деталей индивидуальным методом?
Ремонт деталей индивидуальным методом. При этом методе изношенную поверхность основной, более сложной и дорогой детали ремонтируют механической обработкой до устранения дефекта. Сопряженную, более простую в изготовлении или более дешевую деталь изготовляют новой конструкции и подгоняют к основной детали. При этом размеры деталей получаются произвольными и отличными от номинальных. Сохраняется при этом лишь характер соединения и посадки. Например:сорвана резьба под шпильку головки цилиндров. Резьба ремонтируется (увеличивается диаметр), а шпилька изготовляется новой конструкции (ступенчатой). Метод применим в мастерских, гаражах; на ремзаводах необходимо восстанавливать
взаимозаменяемость.
- Способ ремонтных размеров?
Восстановление деталей обработкой под ремонтный размер. При этом способе одну из изношенных деталей сопряжения подвергают механической обработке, придавая ей заданный ремонтный размер и устраняя при этом искажения геометрической формы и дефекты поверхности (риски, задиры), обеспечивают предписанную чертежом шероховатость. Другую деталь сопряжения заменяют новой указанного ремонтного размера или восстановленной под этот ремонтный размер. Рем. размеры устанавливают в зависимости от величины и характера износа и необходимого припуска на обработку. Принцип взаимозаменяемости в этом случае сохраняется только в пределах одного ремонтного размера.
- Восстановление деталей способом ДРД?
ДРД применяют для компенсации износа рабочих поверхностей деталей. Этим способом восстанавливают изношенные посадочные отверстия под подшипники в картерах КП, задних мостах, ступицах колес, изношенные резьбовые поверхности, цилиндры двигателя (запрессовка "сухой" гильзы) и т.д. Обычно ДРД изготавливают из одного и того же материала. Посадочные отверстия в чугунных деталях могут восстанавливаться стальными втулками-пластинами (толщина стенок не менее 2,0...2,5 мм, для чугунных - вдвое толще). Сопрягаемые поверхности обрабатывают по допускам посадки H7/J6 второго класса точности с шероховатостью Ra =1,25...0,32 мкм. При запрессовке втулок сопрягаемые поверхности целесообразно смазывать машинным маслом для облегчения запрессовки. После постановки и закрепления ДРД (иногда применяют сварку, клеевые композиции, стопорные штифты, винты и др.) производят их окончательную механическую обработку до требуемых размеров.
- Восстановление деталей способом замены части детали?
Отрезается изношенная часть детали, изготавливается новая часть и присоединяется чаще всего стыковой или точечной сваркой. Стыковая сварка (или трением) применяется при ремонте полуосей (приваривается шлицевая часть), клапанов, карданных валов, хомутов задних рессор, тяг и др. деталей. Точечная сварка применяется при ремонте кабин, кузовов, оперения. Привариваются также отломанные ушки и фланцы к чугунным корпусным деталям (изготовляют литьем), сферическое гнездо под рычаг переключения передач. Некоторые предприятия ремонтируют шестерни (например, блок шестерен заднего хода) путем замены венца (срезают изношенный, напрессовывают новый и приваривают).
- Восстановление деталей способом изменения положения рабочих поверхностей?
Примеры: шпоночный паз можно нарезать у многих деталей под углом 45°, 60°, 90°, 180° к изношенному. Венец маховика при износе зубьев спрессовывают, разворачивают изношенной частью зубьев в сторону, противоположную от зацепления с шестерней стартера, и снова напрессовывают (у ВАЗ нагревают до 250°С).
На фланцах полуосей сверлят новые отверстия под болтовые соединения между изношенными отверстиями. Шестерни, имеющие односторонний износ, разворачивают (например, в колесных редукторах).
- Исправления коробления базовых деталей (на примере блока цилиндров)?
Рассмотрим на примере восстановления соосности постелей коренных подшипников блока цилиндров двигателя. У 70 % двигателей ЗИЛ-130, поступающих в КР на московские АРП, эта несоосность превышает предельно допустимую (0,07...0,14). Несоосность за пределами допуска проявляет себя уже при сборке двигателя: после нормированной затяжки крышек коренных подшипников коленчатый вал с трудом проворачивается. В небольших мастерских соосность восстанавливают, помещая под вкладыши металлическую фольгу. При КР необходимо восстановить номинальную соосность. Причины появления несоосности за пределами допустимой:
1) внутренние напряжения в блоке цилиндров после отливки (остаточные напряжения у ЗИЛ - 75...147 МПа ); необходима термическая обработка или длительная выдержка блока до механической обработки;
2) динамическая несоосность (появляется в эксплуатации при перегрузке автомобиля : деформируются крышки и постели).
Определяют несоосность при помощи индикаторных приспособлений. Не восстановленная соосность значительно сокращает ресурс работы двигателя - до 30 % (нагружается только часть поверхности вкладышей: происходит выкрашивание; а также возникают вибрации коленвала).
Способы ремонта:
1) Наиболее простым способом восстановления изношенных гнезд под вкладыши коренных подшипников блока цилиндров является растачивание их под увеличенный размер вкладышей ремонтного размера ("утолщенные" вкладыш). Пример: двигатель ЯМЗ-740 (КамАЗ) - все вкладыши и номинального и пяти ремонтных размеров выпускаются в двух вариантах: тонкие и утолщенные (для восстановления соосности).
2) фрезерование (шлифование) торцов крышек коренных подшипников по плоскости разъема на 0,3...0,4 мм и последующее растачивание гнезд до номинального размера при условии сохранения допустимого размера от оси отверстия гнезд до верхней плоскости блока цилиндров. Снятие металла резцом (с пластиной ВК6М) должно ' происходить за счет крышки . Этот метод применяют даже автоколонны;
3) наплавка посадочных мест (применяют на Барнаульском, Майминском АРЗ). Блоки из серого чугуна наплавляют твердым припоем (латунью) или никелевым электродом; алюминиевые блоки (ГАЗ-53) - в среде аргона прутком из силумина.
- Применение синтетических алмазов при ремонте автомобилей?
Алмазное шлифованиеприменяют также в качестве чистового шлифования закаленных сталей, хромовых и железных гальванических покрытий, для заточки и доводки режущих инструментов.Обработка синтетических материалов. Тонкое (алмазное) точениезначительно более рентабельно, чем шлифование. С его помощью можно обеспечить шероховатость поверхности, отвечающую как монтажным, так и эксплуатационным требованиям. Прибегать к шлифованию допускается в исключительных случаях (круги из электрокорунда или карбида кремния на керамической связке; диаметр круга - 300...400 мм, ширина - 35...60 мм).Алмазное выглаживание производитсяс целью повышения усталостной прочности отремонтированных деталей (наплавленных, с гальваническими покрытиями). Выглаживание производится державкой с впаянным алмазом (R=0,8...3,0 мм). Усилие- 100...400 Н к детали; Vдет = 150...300 м/мин; 8=0,03...0,08 мм/об.
Качество зависит от инструмента, радиального усилия, числа проходов, подачи и окружной скорости.
- Сущность ремонта деталей давлением?
Сущностьданного метода состоит в том, что металл под давлением по законам пластичности перемещения с малоответственных мест детали к изношенным поверхностям и тем самым компенсируется износ. Метод экономичен (10...15 % от стоимости новой детали). Не подлежатвосстановлению давлением детали, изготовленные из непластических материалов, детали с малыми запасами прочности и детали сложной конфигурации.
- Какие факторы влияют на технологию пластических деформаций (перечислить)?
Натехнологию пластической деформации оказывают влияние:
- конструкция детали;
- вид термической обработки изношенной детали;
- структура (однородность, величина зерна);
- температура нагрева;
- скорость деформации;
- имеющееся оборудование.
- Влияние температуры при ремонте деталей давлением?
Сопротивление деформации стали в холодном состоянии больше в 10... 15 раз. Желательно, чтобы температура не была высокой (уменьшается влияние на размеры и структуру детали). Кроме того, при высокой температуре возможно коробление из-за термических напряжений. Важно избегать образования окалины (для углеродистых сталей начало - 675...700°С) и обезуглероживания поверхности слоев (снижается износостойкость, а также усталостная прочность). Пластичность повышается при t > 350°С. Должны быть определенные границы температуры: начала и конца обработки.
- Восстановления деталей осадкой?
Осадку применяют для увеличения наружного диаметра сплошных и внутреннего диаметра полых деталей, а в отдельных случаях при восстановлении деталей типа втулок достигают изменения обоих диаметров одновременно за счет уменьшения высоты. Ремонтируют:втулки из цветных металлов (шкворневые, шатунные), клапаны, толкатели, полуоси, шлицы сошки руля, вилки карданных сочленений, ступицы ведомых дисков сцепления и др.
- Восстановления деталей вдавливанием (примеры)?
Сущность восстановления шлицев вдавливаниемзаключается в том, что материал детали при помощи инструмента клинообразной формы выдавливается из средней части шлица в сторону изношенных боковых поверхностей, что обеспечивает увеличение его ширины до 1 мм на каждую сторону. Инструмент устанавливают по середине шлица и перемещают его вдоль последнего. Шлицевые поверхности подвергают, как правило, вдавливанию в холодном состоянии и в зависимости от твердости сплава они в дальнейшем могут подвергаться термической обработке.
- Восстановления деталей раздачей?
Гидротермическая раздача(ГТР) относится к числу высокоэффективных и недорогих способов восстановления пустотельных деталей типа поршневых пальцев. Способ заключается в том, что изношенный поршневой палец нагревают в индукторе ТВЧ до температуры 1063...1103К, затем быстро охлаждают, пропуская поток воды через внутреннюю полость детали. В результате происходит увеличение наружного диаметра (0,1...0,3 мм) с одновременной закалкой. Этот способ позволяет производить 4...6 краткое восстановление пальцев. Механическая обработка: черновое шлифование - шлифование торцов (если при раздаче пальцы жестко фиксируются в осевом направлении, то эта операция отпадает) - снимают и полируют наружные и внутренние фаски - чистовое шлифование - полирование на доводочном станке - контроль.
- Использование электрогидравлического эффекта для восстановления поршневых пальцев?
Поршневой палец (карбюраторных двигателей: с толщиной стенок 4...5 мм) ставят в полиэтиленовый технологический патрон разового действия, который служит для направления электрического разряда по оси детали. Для увеличения эффективности процесса в полость ножки патрона устанавливают специальный взрывающийся проводник (алюминиевая проволока диаметром 0,7 мм). В полость пальца подают техническую воду. Высоковольтный импульс конденсаторной батареи (37...40 кв, 6 мкф) проходит через шаровой разрядник на положительный электрод, проводник и отрицательный электрод. В результате электрогидравлического взрыва возникает ударная волна, которая раздает поршневой палец. При указанном режиме удается достичь остаточной деформации по наружному диаметру, равной 0,12 мм для пальцев из стали 45. Мах износ у поршневых пальцев ЗИЛ-130 — 0,025 мм, припуск на шлифование — 0,05 мм.
- Восстановление поршневых пальцев термопластическим методом?
- Восстановление деталей обжатием?
Обжатиепримеряют для восстановления внутренних размеров полых деталей в результате уменьшения наружных размеров.
Восстанавливают: втулки, сепараторы роликовых подшипников при износе стенок окон под ролики; конусные отверстия (проушины) рулевой сушки; рычаги поворотных цапф, продольных рулевых тяг; отверстия в поворотных цапфах, внутреннюю поверхность цилиндров амортизаторов, гильзы цилиндров двигателей и др. Матрица штампа состоит из трех частей: приемной, обжимающей и калибрующей. Внутреннюю поверхность матрицы для уменьшения сил трения обрабатывают до высокой степени чистоты. Внутренний диаметр втулки после ее обжатия пуансоном обрабатывают, а наружный диаметр наращивают на требуемый размер одним из способов, например, гальваническим.
- Недостатки правки под прессом?
Недостатки правки под прессом:
1) снижение усталостной прочности на 15...40 %;
2) снижение несущей способности детали, т.е. способности детали противостоять воз-
действию внешней силы в направлении, противоположном направлению правки.
3) Исследования показали, что многие ответственные детали (коленвалы, шатуны) после некоторого периода эксплуатации возвращаются в прежнее положение. Нестабильность правки можно объяснить объемной неоднородностью остаточной деформации и асимметричным распределением остаточных напряжений на участке детали, за счет которого произошла правка.
- Стабилизация правки?
Стабилизация правки:
1) перегибают деталь при правке в противоположную сторону, а затем повторной правкой выдерживают деталь после правки длительное время;
2) выдерживают деталь после правки длительное время;
3) термофиксация правки (отпуск при температуре 400...450 градусов, выдержка в зависимости от размеров детали 0,5...! час и медленное охлаждение). Если такой нагрев осуществить нельзя (из-за уменьшения механических свойств закаленных деталей), то нагревают до 180...200 градусов с выдержкой в печи 5...6 часов;
4) чеканка — состоит в том, что на поверхностях деталей, имеющих после правки напряжение растяжения, создается наклепом напряжение сжатия.
- Правка шатунов?
Деформация — изгиб и скручивание. Причины: неправильная сборка, заклинивание поршней, неправильная правка. Индикаторы устанавливают на нуль по эталонному шатуну. Параллельность осей на автозаводе получают одновременной расточкой верхних и нижних головок. Промышленность выпускает для контроля и правки шатунов индикаторное приспособление. К приспособлению прилагаются рычаги для правки. Нижнюю головку шатуна крепят в слесарных тисках и рычагами правят шатуны, контролируя правку индикаторами. Схема технологического процесса: 1)проверка;
2) двойная правка;
3) термофиксация (400...500 градусов, время выдержки 0,5...1 ч.)
Если проверяемые шатуны надеваются на технологические пальцы, править их не нужно.
- Ротационная обработка?
В ремонтном производстве нашли широкое использование совмещенные методы обработки восстанавливаемых поверхностей деталей: наплавка, железнение; расточка и раскатывание, расточка и калибрование и др.
Режим обработки: усилие прижатия шариков (роликов) - 50...200 кгс; скорость движения - 150...450 м/мин; продольная подача - 0,06...0,08 мм/об; припуск на раскатку - 0,03...0,06 мм; глубина наклепанного слоя — 0,05...0,15 мм; числа проходов- 1...3. Ротационная обработка может также производиться непрерывным вибрационным и ударным способом.
После ротационного упрочнения уменьшается шероховатость поверхности до Ra = 0,32...0,16 мкм, твердость обработанной поверхности увеличивается на 30...80 %, а усталостная прочность деталей повышается на 50... 100 %.
- Ремонт рессор термомеханической обработкой?
Восстановление рессор методом высокотемпературной термомеханической обработки
Сущность метода заключается в пластической деформации металла при температуре выше верхней критической точки АСЗ с немедленным охлаждением, чтобы предотвратить развитие рекристаллизации. После отпуск.
Технология(для стали СТ55С2 и 50ХГА):
1) нагрев — 950...970 градусов; 900...920 градусов;
2) прокатка со степенью обжатия 15%;
3) закалка в масле;
4) отпуск (300, 400 градусов- 1 час, 460 градусов - 30 минут).
Механическая прочность превышает прочность новых листов (если нет усталостных трещин). Повышение прочности происходит в результате измельчения структуры, увеличения плотности дефектов кристаллической решетки (дислокаций) и выделения в мартенсите большого количества включений, препятствующих движению и перераспределению дислокаций.
- Какие детали изготавливают из серого чугуна (сч)?
Из серого чугуна (СЧ-15, СЧ-18, СЧ-21, СЧ-24) изготовляют: гильзы цилиндров, тормозные барабаны, ведущие диски сцепления, картеры и крышки коробок передач, блоки цилиндров двигателя и компрессора, маховики, картеры сцеплений, главный и колесные тормозные цилиндры, впускные и выпускные трубопроводы, корпусы жидкостных и масляных насосов и др. детали.
- Структурные изменения в сч при сварке?
Структурные изменения прирасплавлении чугуна весь углерод (свободный графит)
переходит в связанное состояние, в цементит (Fe3C). При охлаждении часть Fe3C распадается на железо (Fe) и графит (С). При наличии кремния (Si) и углерода до 4% практически весь Fe3C переходит в графит, а при наличии кремния менее 0,8% распад цементита почти полностью приостанавливается. Этим определяется химический состав присадочных продуктов «А» и «Б» для газовой сварки. После сварки для графитизации должно быть очень медленное охлаждение детали (вместе с печью, в термостате и др. приемы: помещают в сухой песок, накрывают листами асбеста).
- Что способствует распаду Fe3C в процессе сварки детали из сч?
При охлаждении часть Fe3C распадается на железо (Fe) и графит (С). При наличии кремния (Si) и углерода до 4% практически весь Fe3C переходит в графит, а при наличии кремния менее 0,8% распад цементита почти полностью приостанавливается. Этим определяется химический состав присадочных продуктов «А» и «Б» для газовой сварки.
- Почему детали из сч ремонтируют сваркой в горизонтальном положении?
Вследствие жидко текучести чугуна сварку с образованием большой ванночки расплавленного металла можно производить только в нижнем положении.
- Почему сварщику рекомендуют сваривать детали из сч с образованием большой (2 см) ванночки расплавленного металла?
Чугун быстро переходит из жидкого состояния в твердое (у стали, есть промежуточное состояние - пластичное, у чугуна - нет). Если имеющиеся в металле газы не успевают выделиться из него, то шов получается пористым (газовыделение происходит вследствие окисления углерода с образованием его окиси). Вывод: сварку чугуна ведут с образованием большой ванночки расплавленного металла, минимум 2 см3.
- Почему в процессе сварки деталей из сч могут возникать трещины?
Чугун склонен к значительным усадкам. При быстром охлаждении компоненты чугуна, имеющие различную усадку и плотность, вызывают в металле внутренние напряжения (образуются трещины Вывод: необходимо деталь медленно охлаждать).
- Почему сварщику рекомендуется медленно охлаждать детали из сч?
При быстром охлаждении компоненты чугуна, имеющие различную усадку и плотность, вызывают в металле внутренние напряжения (образуются трещины Вывод: необходимо деталь медленно охлаждать).
- Почему чугунный блок цилиндров рекомендуется варить с предварительным нагревом? До какой температуры?
Горячая сварка является радикальным способом предотвращения отбеливания шва и около шовной зоны, образования пор и трещин, может обеспечить прочность шва, равноценную прочности основного металла. И хотя процесс трудоемкий и дорогостоящий, без него порой не обойтись, особенно при сварке картерных, сложных по конфигурации деталей. Рассмотрим подготовку к сварке, на примере, картера сцепления (сколы лапок крепления). Картер нагревают предварительно в электропечи до температуры 200...250°С в течении 20...25 минут, затем доводят температуру картера до 600...650°С с выдержкой при этой температуре в течении 20...25 минут. Установив нагретый картер на сварочный стол, его закрывают теплоизоляционной чехлом, оставив открытыми лишь места, подлежащие сварке. Во время сварки температура картера не должна снижаться ниже 400°С. Заваренный картер снова помещают в печь и нагревают до 600...650°С. Охлаждение производят вместе с печью. Наплывы металла начищают заподлицо с основным металлом.
- Как испытывается блок цилиндров после ремонта трещины сваркой?
При ремонте трещины на впускном трубопроводе (требуется обеспечить герметичность) шов должен выступать над поверхностью детали на 1,0...1,5 мм. После визуального осмотра очищенного шва производится гидравлическое испытание шва под давлением* 0,3...0,4 МПа.
- Флюсы для газовой сварки деталей из сч?
Выпускается несколько марок:
1) бура (Na2B4O7) — 100%;
2) бура — 56%, Na2CO3 — 22%, К2СО3—22%;
3) бура — 50%, NaHCO3 — 47%, SiO2—3% и тд.
- Какие прутки применяют для газовой сварки деталей из сч? Их заменители?
Хим. состав прутка «Б»: С — З...3,5%; Si — 3,5...4%; Мn — 0,5...0,8%; Ni не более 0,04%; Si не более 0,05%; Р — 0,3...0,5%. Для горячей сварки (деталь, например блок цилиндров, подогревается в электропечи до 600...650°С) применяют пруток марки «А» (отличается от прутка «Б» меньшим содержанием кремния — 3,0...3,4%). Примерно таким же хим. составом обладают компрессорные кольца поршней, которые иногда используют в транспортных предприятиях как заменители прутков «А» и «B» Для сварки чугунов применяют присадочные прутки марок «А» и «Б», а также прутки НЧ-1, НЧ-2 диаметром 4,6,8,10,12 мм. Отличаются от «А» и «Б» наличием титана (0,03...0,06%). Например, при сварке картера сцепления (см. 8.3.9.) применяют присадочный чугунный прут диаметром 6мм.Для износостойкой наплавки применяют прутки «БЧ» и «ХЧ» (Сг -— 1,2...2,0%). Для горячей сварки можно использовать порошковую проволоку ППЧ-3 (С — 4,5...5,0%; Si — 3,3...4,0%;А1 — 0,1...0,3%; Ti—0,1...0,3%).
- Технологический процесс сварки-пайки тонкой стенки водяной рубашки чугунного блока цилиндров?
При заварке тещины в тонкой стенке рубашки охлаждения двигателя может быть применена высокотемпературная пайка припоями на основе меди (ПМЦ-54,Л-2 и др.). Трудность пайки чугуна связана, прежде всего, с наличием в нем графита или цементита. Поэтому рекомендуется фторидно-боридные флюсы ПВ-209 и ПВ-284, растворяющие графит и обеспечивающие хорошее смачивание припоем соединяемых кромок изделия (иногда графит удаляют выжиганием окислительным пламенем). Пайка чугуна должна производиться при 897...900°С, так как при дальнейшем повышении температуры начинается отбеливание чугуна
- Как подготовить флюс для сварки деталей из сч? Как внести флюс в зону сварки?
Флюс вносят погружением в него, нагретого прутка. Флюсы перед погружением рекомендуется прокалить (400°С).
- Прутки для износостойкой наплавки чугунных деталей?
Для износостойкой наплавки применяют прутки «БЧ» и «ХЧ» (Сr - 1,2...2,0%).! Для горячей сварки можно использовать порошковую проволоку ППЧ-3 (С - 4,5...5,0%; Si - 3,3...4,0%;А1 - 0,1...0,3%; Ti-0,1...0,3%).
- Подготовка трещин на деталях из сч к сварке?
1) При обнаружении трещин следует произвести засверловку их концов (диаметр сверла 3мм);
2) удаление дефектных участков производится механическими способами: фрезерованием, /сверловкой, вырубкой зубилом и т. п.;
3) поверхность детали, прилегающая к месту сварки, на 10...20. мм вокруг него зачищается абразивным кругом или щеткой до металлического блеска;
4)разделка кромок трещин и других дефектных участков производится путем снятия фасок вдоль края. При трещине стенки до 15 мм делается V- образная разделка кромок с общим углам 60...70°С при толщине свыше 15 мм двухсторонняя Х- образная разделка с тем же углом перекрытия.
- Перечислите основные виды электродов для сварки деталей из сч?
Железно-никелевый электрод ЖНБ-1 (Fe - 45%; Ni - 55%; С - 0,07%; Мп - 1,5%; Si - 0,7%; покрытие -У ОНИ-13/45) используется для заварки отдельных небольших дефектов деталейиз серого и высокопрочного чугуна и в ряде других случаев
Медно-никелевые электроды(МНЧ-1, МНЧ-2). Для изготовления электрода используются медно-никелевые сплавы — монельметалл и константан, НМЖМЦ 28-2,5-1,5 содержит 65...75% Ni, 27...30% Си, 2...3% Fe b 1,2...1,8% Mn (МНЧ-1); сплав МНМЦ 40-1,5 — 60% Ni и 40% Си (МНЧ-2). Электроды Электрод марки ОЗЧ-1 с медным(красная медь М-2, М-3) стержнем диаметром 4...5 мм и покрытием У ОНИ-13/45 содержит медь и железный порошок в равных соотношениях Более эффективно применение для сварки чугуна электрода ЦЧ-2 со стержнем из стальной малоуглеродистой проволоки Св-08 или Св-08А.
- Область применения чугунных электродов, пример: ОМЧ-1?
Для горячей сварки чугуна с нагревом до 600...650°С используются чугунные электроды (ОМЧ-1, ВЧ-3 и др. Например: электрод ОМЧ-1 (стержень — пруток из чугуна «Б»); толщина покрытия - 1 мм: мрамор или мел - 25% (для ионизации); полевой шпат - 25% (шлакообразование); графит — 41% (обеспечивает распад цементита); ферромарганец — 9% (раскислитель) и жидкое стекло к сумме сухих компонентов - 30...35% (связующее).
- Область применения стальных электродов для сварки деталей из сч?
Электроды, предназначенные для сварки углеродистых и низколегированных сталей, могут быть применены для сварки неответственных поверхностей чугунных деталей, т.е. не несущих нагрузку (например: рубашка охлаждения блока цилиндров). В этом случае неизбежно в металле шва образуется высокоуглеродистая сталь, которая при охлаждении чугуна без предварительного нагрева будет закалена, в результате чего может образоваться трещина.
- Комбинированные электроды (ОЗЧ-1, ЩЗЧ-1П) для сварки деталей из чугуна?
Электрод марки ОЗЧ-1 с медным (красная медь М-2, М-3) стержнем диаметром 4...5 мм и покрытием УОНИ-13/45 содержит медь и железный порошок в равных соотношениях. Электроды ОЗЧ получили наиболее широкое применение при холодной сварке чугуна. При сварке чугуна медно-железным электродом не следует допускать сильного разогрева основного металла. Ток должен быть минимально возможным, шов — коротким в разброс с перерывом для охлаждения свариваемой детали. Медно-железный шов можно перековывать в горячем состоянии, чтобы уменьшить уровень сварочных напряжений. Проковка позволяет снизить вероятность образования трещин в около шовной зоне. При сварке медно-железным электродом получается/неоднородный металл шва. Причина " неоднородности: наличие мягкой сердцевины и твердых включений карбида железа. Это затрудняет механическую обработку. Несколько лучшие результаты дает электрод АНЧ-1 с сердечником из стали марки Св-04х 18 Н9 и медной оболочкой (покрытие — основное «Б»).
- Никелевые электроды (МНЧ-1, МНЧ-2) для сварки деталей из чугуна?
Медно-никелевые электроды (МНЧ-1, МНЧ-2). Для изготовления электрода используются медно-никелевые сплавы — монельметалл и константан, НМЖМЦ 28-2,5-1,5 содержит 65...75% Ni, 27...30% Си, 2...3% Fe b 1,2...1,8% Mn (МНЧ-1); сплав МНМЦ 40-1,5 — 60% Ni и 40% Си (МНЧ-2). Электроды МНЧ-1 и МНЧ-2 имеют основное покрытие «Б». Медно-никелевые электроды практически не дают твердых карбидных составляющих, поскольку, ни медь, ни никель не образуют с углеродом химического соединения. Частичное расплавление основного металла большого практически значения не имеет, так как и медь, и никель являются графитизаторами чугуна и, проникая в расплавленный металл, положительно влияют на него. К тому же медь и никель, обладающие неограниченной растворимостью, способствует надежному сплавлению с чугуном. Недостатки: высокая стоимость электродов и большая усадка расплавленного металла при кристаллизации (могут быть Горячие трещины). По этой причине сварку медно-никелевыми электродами не рекомендуется для заварки трещин. В горячем состоянии наплавленный металл необходимо проковывать ударами легкого молотка. Валики наносятся короткими участками при возвратно-поступательном движении электрода с перерывами для охлаждения.
- Какие детали автомобилей изготавливают из ковкого чугуна (кч)?
Из ковкого чугуна (ферритного класса) КЧ-35, КЧ-37 в отечественном автомобилестроении изготавливают:
картеры редукторов, рулевых механизмов; коробки сателлитов, ступицы колес, кронштейны рессор, подвески, педали, тормозные колодки, крышки редукторов и коробок передач, корпусы буксирных приборов и др.
- Структурные изменения в кч при сварке?
Если КЧ сваривать обычным методом, т.е. нагревая кромки деталей до температуры плавления, то углерод отжига растворяется в металле и при охлаждении не успевает выделиться. Происходит отбеливание чугуна, которое можно устранить только повторным отжигом, это экономически не выгодно в условиях ремонтных предприятий.
- Какой припой рекомендуется при ремонте трещин на деталях из кч?
Удовлетворительные результаты без отжига получаются при пайке деталей из КЧ медно-цинковыми припоями, например:
ПМЦ-54; температура плавления — 885°С. Кромки подогреваются до температуры 850...900°C ни в коем случае не расплавляются.
- Почему рекомендуется пайка трещин на деталях из кч вместо газовой сварки?
Удовлетворительные результаты без отжига получаются при пайке деталей из КЧ медно-цинковыми припоями, например:
ПМЦ-54; температура плавления — 885°С. Кромки подогреваются до температуры 850...900°C ни в коем случае не расплавляются.
- Флюсы для сварки-пайки деталей из ковкого чугуна?
флюсы: 1) Na3B4O7 (бура)-50%, НВО3 (борная кислота) - 50%; 2) Na3B4O7 - 70%, NaCI - 20%,
НВО3 - 10%. Пламя слегка окисленное, чтобы обеспечить выжигание углерода из поверхностного
слоя металла. При этом образуются пары, в которые проникает расплавленный припой, и создаются
условия для прочного сцепления его с деталью. Получаемые соединения обладают высокой пластичностью и прочностью: бв= 35. ..40 кгс/мм2, относительное удлинение ψ=8...15%. Сложные детали
рекомендуется подогревать до 600...650°С.
- Электродуговая сварка деталей из ковкого чугуна?
Электродуговая сварка деталей из КЧ ведется в основном без подогрева электродами на основе меди и никеля, а также стальными электродами ЦЧ-4 (с ванадием в обмазке) и механизированной сваркой проволокой ПАНЧ-1 1 (см. Сварку серого чугуна.). Результаты удовлетворительные. Если от отремонтированного изделия требуется высокая герметичность, сварной шов сверху покрывают герметикой, а во внутренней полости создают небольшой вакуум. В этом случае герметик впитывается в поры.
- Как получают углерод отжига деталей из ковкого чугуна?
Детали получают отливкой в земляные формы, затем — многочасовой (20-40 ч.) двухступенчатый (t1=920...970°C, t2:=720...7600C) отжиг. В результате отжига происходит разложение Fe3C с образованием гнезд углерода отжига.
- Какие детали изготавливают из силумина?
Из алюминиевых сплавов изготавливаются такие детали, как блок и головка блока цилиндров, картер, крышка картера и удлинитель коробки передач, картер рулевого механизма, впускные трубопроводы двигателя, крышка распределительных шестерен, корпус водяного насоса.
- Какие свойства окисла Al2O3 снижают качество сварки деталей из силумина?
1) AL легко окисляется. На поверхности сварочной ванны образуется тугоплавкая окисная пленка Аl2Оз с температурой плавления 2050°С (AL- 659 С) и плотностью в 1,5 раза большей, чем у алюминия (3,85 и 2,7 т/м3), к тому же химически очень стойкая. Пленка окисла не дает возможности вступить расплавочному присадочному материалу в контакт с основным. Расплавленный присадочный материал, тоже имеющий окисную пленку, свертывается в шарик и скатывается. Поэтому при сварке AL сплавов не обходимо, прежде всего, удалить окисную пленку на поверхностях, соединяемых кромок и присадочной проволоки.
- Почему при сварке деталей из силумина могут появится трещины по шву и в околошовной зоне?
Склонность металла шва к возникновению трещин в связи с грубой столбчатой структурой металла шва и выделением по границам зерен легкоплавких эвтектик (577°С при концентрации кремния до 0,5%). При содержании кремния 4...5% образующаяся эвтектика "залечивает" трещину. Склонность металла шва к возникновению трещин в связи с грубой столбчатой структурой металла шва и выделением по границам зерен легкоплавких эвтектик (577°С при концентрации кремния до 0,5%). При содержании кремния 4...5% образующаяся эвтектика "залечивает" трещину. Поэтому стержни электродов, присадочные прутки при сварке автомобильных деталей изготавливают из высококремнистого силумина (Св-АК5, Св-АК10 и др.). Иногда в транспортных предприятиях сварщики изготавливают прутки из алюминиевых поршней. Отрицательное значение имеет и большая усадка расплавленного металла (7%), приводящая к возникновению внутренних напряжений и, следовательно, к значительному короблению ремонтируемого сваркой изделия.
- Почему перед сваркой детали из силумина подогревают до 200-250С?
Предварительный и сопутствующий нагрев, особенно корпусных деталей, до температуры 150...250°С замедляет кристаллизацию металла сварочной ванны, в результате чего выделение растворенного газа происходит более полно и пористость снижается .5) Применение мощных источников тепла для сварки, поскольку алюминиевые сплавы имеют для сварки большую теплопроводность и поэтому трудно создать сосредоточенный нагрев для плавления металла. И с этой точки зрения целесообразным является применение предварительного и сосредоточенного нагрева до t°150...250°C.
- Причина образования пористости в сварочном шве при сварке деталей из силумина?
Свариваемые кромки изделия и присадочный материал следует тщательно очистить от грязи, жиров, влаги и т. д. Так как неочищенная поверхность может служить источником насыщения алюминиевых сплавов газом. При повышении температуры растворимость газов, особенно водорода, резко повышается; при, охлаждении дегазация, металла шва идет очень медленно (препятствует окисная пленка). В результате в металле возникает интенсивная пористость, снижающая его пластичность.
- Флюсы для газовой сварки деталей из силумина?
Основу флюсов и покрытий составляют легкоплавкие смеси хлористых солей Na, К, Li. К этим солям добавляют до 10…15 % фтористых солей (более активные, но и более токсичные). При газовой сварке применяют флюс АФ-4А (КС1 - 50 %, NaCl - 25 %, LiF - 14 %, NaF – 8.
- Как флюсы (АФ-4А и др.) взаимодействуют с окислами Al2O3?
Флюс взаимодействуют с окислами следующим образом. Во время сварки вследствие большой разницы в коэффициентах линейного расширения основного металла и окислов в окислах образуются трещины, куда затекает расплавленный флюс, образуя под пленкой окислов соль А1С13. Под действием этих солей окислы в виде чешуек отрываются от основного металла, всплывают на поверхность и смываются флюсами, частично растворяясь в нем. Так как основным источником появления в сварочной ванне водорода является влага, то перед сваркой рекомендуется прогревать деталь и прокаливать флюсом.
- Подготовка деталей из силумина к сварке?
Перед сваркой кромки трещины разделывают под углом 60...90°. Загрязнения удаляют различными растворителями, а окислы - механической зачисткой или химическим травлением 0,5...! мин (NaOH - 45....55 г/л; NaF - 40...50 г/л; промывка в горячей воде, нейтрализация 25...30 % HNO3 в течение 1 ...2 мин; промывка холодной и горячей водой). Подготовленные таким образом детали до сварки нужно хранить не более 2.. .4 часов.
- Присадочные прутки для ацетиленокислородной сварки деталей из силумина?
Газовую сварку деталей из алюминиевых сплавов можно вести с использованием ацетилена или пропан-бутановой смеси нормальным или слегка ацетиленистым пламенем использованием флюса АФ-4А. В качестве присадочного материала используются также проволоки, которые применяются при аргонно-дуговой сварке (Св-АК5, Св-АК10, Св-АК12), или проволока того же состава, что и свариваемый металл. Диаметр присадочной проволоки устанавливают по толщине свариваемого металла. Толщина металла, мм 3...5 6...8 9...12. Диаметр проволоки, мм 4...5, 5...7 6...8 Режимы сварки также зависят от толщины металла. При сварке деталей, толщина стенки которых больше 5 мм, рекомендуется применять правый способ, если меньше, то левый ведения горелки.
- Как удаляют остатки флюса после сварки деталей из силумина?
Флюсы и электродные покрытия вызывают коррозию сварного шва, поэтому после сварки сразу же следует остатки флюса удалить. Для этого поверхность шва и околошовной зоны протирают ветошью, смоченной теплой водой, и прочищают стальной щеткой до блеска поверхности.
- Электродуговая сварка деталей из силумина плавящимся электродом?
Дуговая сварка алюминиевых сплавов производиться электродами ОЗА-2 и ОЗА-1. Сердечник электродов изготавливается из проволоки Св-АК5 или Св-АК10. Покрытие электрода ОЗА-2 обладает большей способностью к влагопоглащению. Отсыревшие электроды перед употреблением прокаливают при 200...300°С в течение 1,0... 1,5 ч. Режимы электродуговой сварки зависят в основном от толщины свариваемого металла. Режимы ручной дуговой сварки алюминиевых сплавов электродами ОЗА-2 и ОЗА-1. В ряде случаев для улучшения качества шва дуговую сварку алюминиевых сплавов ведут с применением флюса АФ-4А. Электродуговую сварку плавящимся электродом ведут на постоянном токе обратной полярности. Электрод рекомендуется держать перпендикулярно к поверхности, вести без поперечных колебаний (для повышения устойчивости дуги). Скорость сварки обычно 4...6 мм/мин.
- Электродуговая сварка деталей из силумина не плавящимся электродом?
Наиболее надежный способ восстановления алюминиевых сплавов применение аргонно-дуговой сварки. Соединяемые кромки детали и присадочный материал нагреваются теплом электрической дуги, образующейся между неплавящимся (вольфрамовым) электродом и деталью. При этом из сопла наконечника горелки непрерывно подается аргон, который, окружая дугу, создает сосредоточенный нагрев, а также предохраняет расплавленный металл шва от вредного влияния кислорода и азота воздуха, распыляет окисную пленку. В результате этого условия плавление металла улучшаются, качество шва получается высоким, коробление почти отсутствует, отпадает необходимость применения" электродных покрытий и флюсом.
- Как повышается устойчивость дуги при сварки деталей из силумина переменным током?
- ГОСТ на газ аргон для сварки? Какие газы могут добавляться к аргону?
Для сварки применяется аргон марок: А, Б, В (ГОСТ 10157-73) и технический (ТУ). Объемное
содержание аргона: А - 99,99 %, Б - 99,96 %, В - 99,90 %, технический - 83,3 % (12... 16 % азот). При
сварке и наплавке некоторых деталей к аргону добавляется дешевый газ: например, при наплавке
впускного клапана и сварке малоуглеродистой стали - Аг + 10 % СО2. Аргон поставляется (на Алтай
из Новокузнецка) в баллонах под давлением 150±5 кгс/см2; для А, Б, В - черного цвета с белым вер
хом и черной надписью "Аргон чистый", а для технического - черного цвета с белой горизонтальной
полос.
- Положительные стороны сварки деталей постоянным током?
Положительные стороны сварки на постоянном токе: высокая устойчивость дуги; возможно применять сварку по методу Бенароса (угольным электродам. Сваривают низко плавкие металлы, например, свинцовые перемычки аккумуляторных батарей); имеется возможность регулирования режима сварки путем изменения полярности (если к деталям подключается "+", выделяется на детали 43 % тепла; если "-" (обратная полярность) 36 % тепла); независимость сварочного поста от электросети, если у сварочного агрегата ДВС; возможно вести сварку не обмазочным (с меховой обмазкой) электродом.)
- Отрицфтельные стороны сварки деталей переменным током?
Отрицательные стороны сварки на постоянном токе: низкий КПД сварочного агрегата; высокий расход электроэнергии: 3,5 .. кВт/ч на 1 кг. Расплавленного металла; переменным током, 4,6 кВт/ч - постоянным током; дорогое обслуживание и ремонт агрегата; большой вес и габариты.
- Источники тока для сварки деталей постоянным током?
Источники питания сварочной дуги:
Сварочные преобразователи постоянного тока (состоят из генератора и приводного электродвигателя или двигателя внутреннего сгорания); Выпрямители; Трансформаторы переменного тока, j. Применяются генераторы нескольких типов. С независимым возбуждением с размагничивающей последовательной обмоткой, самовозбуждение с размагничивающей последовательной обмоткой и расцепленными полюсами. Для автоматической и полуавтоматической сварки в защитных газах необходимы генераторы с жесткой или возрастающей внешней характеристикой. Для этой цели выпускаются генераторы ГСГ-350 и ГСГ-500, входящие в состав преобразователей ПСГ-350 и ПСГ-500-1 (в генераторах предусмотрены две обмотки возбуждения: одна независимая, другая последовательная, подмагничивающая).
- Источники тока для сварки деталей переменным током?
Оборудование для сварки переменным током. Каждый сварочный аппарат состоит из понижающего трансформатора и устройства для создания падающей внешней характеристики - дросселя (регулятора тока), подвижного магнитного шунта или подвижной обмотки. Трансформатор обеспечивает питание дуги переменным током напряжением 60...70В?
- Вольтамперная характеристика источника тока для сварки?
Вместо сварочных преобразователей нередко для сварки используют выпрямители тока, состоящие из понижающего трансформатора и блока селеновых или кремниевых выпрямителей. Крутопадающая внешняя характеристика выпрямителя и регулирование сварочного тока обеспечиваются дросселем насыщения, включенным между трансформатором и выпрямительным блоком. В зависимости от внешних характеристик сварочные выпрямители бывают с крутопадающими характеристиками (BCС-300-3, ВСС-120-4 и др.), жесткими пологопадающими характеристиками (ВС-200, ВС-300, ВС-600 и др.) и универсальные (ВСУ-300, ВСУ-500).Универсальные выпрямители позволяют получение как жестких, так и падающих внешних характеристик.
- Осцилляторы и их назначения?
Осцилляторы. Используются для повышения устойчивости дуги при сварки дугой малой мощности, при аргонодуговой сварке, при падении напряжения в сети. Подключаются параллельно сварочному трансформатору. Параметры: N=100...250 Вт, и=2000...3000 В, v=l 50000...260000.
- Назначение балластных сопротивлений при сварке?
- Классификация электродов (ГОСТ9466-75).
В соответствии с ГОСТ 9466-75 электроды предназначены для сварки: углеродистых и конструктивных легированных сталей; легированных теплоустойчивых стилей; для высоколегированных сталей с особыми свойствами; для наплавки.
- Электроды для сварки конструкционных сталей?
Для сварки конструкционных сталей выпускается 15 типов электродов: Э-34, Э-42, Э-42А, Э-46, Э-46А - для низкоуглеродистых сталей; Э - 50, Э - 50А, Э-55 - для среднеуглеродистых и низколегированных сталей; Э-60, Э-60А, Э-70, Э-85, Э-100, Э-120, Э-145 - для легированных сталей повышенной прочности. цифра означает % ктс/мм2. Для сварки теплоустойчивых сталей - 7 типов (Э-М; Э-МХ, Э-ХМ, Э-ХМФ, Э-ХМФБ, Э-Х2МФБ и Э-Х5МФ). Буквы обозначают легирующие химические элементы (хром, молибден, ванадий, бор). Каждому типу электрода соответствует несколько марок, например: Э-42 (ОММ-5, СМ-5, ЦМ-7, КПЗ-32Р, УНЛ-1, АНО-6, АНО-5, АНО-1, ОМА-2, ВСП-1, ВСЦ-2). Всего отечественная промышленность выпускает 330 марок электродов.
- Назовите основные параметры электрода Э46А-УОНИ-13/45-3.0-УД2/Е432(5)-Б10.
Пример полного обозначения электродов (ГОСТ 9466-75):
Э46А - УОНИ-13/45 - 3.0 - УД2
Е432(5)-Б10
Э46А - тип электрода по ГОСТ 9467-75; Э - электрод для дуговой сварки;46 - тт гарантируемый предел прочности металла шва в кгс/мм2 - 460 МПа; А - гарантируется получение повышенных пластичных свойств металла шва; УОНИ-13/45 - марка лектрода;3,0 - диаметр, мм; У - электроды для сварки углеродистых и низкоуглеродистых сталей, \ Д2 – с толстым покрытием второй группы, Е – электрод.
- Кислые покрытия (А) электродов; назначения, положительные стороны?
A - кислые покрытия имеют окислительный характер; не рекомендуются для сварки легированных сталей и углеродистых (С>0,30 %), закаливающихся (образуются горячие трещины из-за не водораживания металла). Металл СВ 08, СВ Q8A + "А" - состава соответствует кипящей стали. Металл при сварке электродом с покрытием "А" разбрызгивается. /Покрытия "А" токсичны (много выделяется марганцовистых соединений). Преимущества малая чувствительность к образованию пор при наличии на поверхности детали ржавчины, окалина; стабильное горение дуги при сварке переменным током во всех пространственных положениях; высокая производительность.
- Кислые покрытия (А) электродов; отрицательные стороны стороны?
Металл при сварке электродом с покрытием "А" разбрызгивается. Покрытия "А" токсичны (много выделяется марганцовистых соединений).
- Рутиловые (Р) покрытия электродов?
Р - рутиловые покрытия Окислительная способность меньше, чем у покрытий "А". Состав накопленного металла (СВ 08, 08А + "Р"-полуспокойная сталь. Преимущества: малое разбрызгивание; небольшая токсичность; металл шва обладает малой чувствительностью к образованию пор при колебаниях длины дуги при сварке по окисленным поверхностям.
- Электроды с основным покрытием (Б); применение, положительные стороны?
Б - основные покрытия. Очень малая окислительная способность, чем обеспечивается высокий коэффициент перехода легирующих элементов в наплавленный металл. Существенное преимущество при сварке высоколегированных сталей. Металл мало насыщается водородом, что важно при сварке закаливающихся сталей. Высокая ударная вязкость.
- Электроды с основным покрытием (Б); недостатки?
Недостатки образование пор при сварке ржавого металла, при увлажнении, при удлинении дуги; стабильность дуги хуже. Сварку ведут короткой дугой на постоянном токе обратной полярности.
- Электроды с целлюлозным покрытием (Ц)?
Ц-целлюлозные покрытия. Образуют много защитных газов. При сварке шов наводораживается и склонен к образованию трещин. Сваривают металл малой толщины; широко применяют в монтажных условиях. Достоинства:
стабильность дуги; сварка переменным током в любых пространственных положениях.
Выбор режима сварки (ручной электродуговой)?
При сварке стыковых швов низколегированных сталей в нижнем положении режим рассчитывают в такой последовательности:
1) подбирают диаметр электрода в зависимости от толщины свариваемого металла, мм:
толщина | 1,5 | 2,0 | 3,0 | 4...S | 6...3 | 9...12 | 13...15 | 16...20 |
диаметр | 1,6 | 2,0 | 3,0 | 3...4 | 4,0 | 4...S | 5,0 | S...6 |
2) подбирают допустимую силу сварочного тока. Обычно пользуются эмпирическими зависимостями:
диаметр электрода - 4 и 5 мм: JCB= (40...60)d3; для диаметров <4 мм и >5 мм: JCB=d3(20 + 6d3).
При сварке вертикальных швов силу сварочного тока уменьшают на 10... 15 %, а при сварке поточных - на 15...20 %.
При сварке угловых швов из низкоуглеродистой стали:
катет шва, мм: | 2 | 3 | 4 | 5 | 6...S |
диаметр, мм: | 1,6...2,0 | 2.5...3.0 | 3...4 | 4,0 | 4. ..5 |
За один проход свариваются швы катетам не более 8 мм. При необходимости сваривать швы с большим катетом - за два или несколько подходов.
Дата добавления: 2018-02-28; просмотров: 639; Мы поможем в написании вашей работы! |
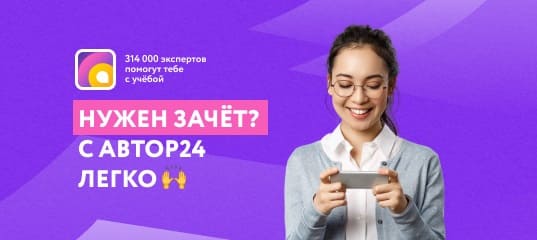
Мы поможем в написании ваших работ!