Особенности вибродуговой наплавки, деталей, обеспечивающих безопасность движения?
Пример: наплавка шеек распредвала ЗИЛ.
Режимы: напряжение - 13 В., индуктивность 5 витков, частота вращения 3,5 мин"1, шаг наплавки 3,0 мм/об, расход жидкость 0,5 л/мин, HRC - 45...50. Проволока: марка ОВС, диаметр 1,6 мм, скорость подачи 1,3м/мин. t
Наплавка деталей ОБД (обеспечивающих безопасность движения) - поворотные цапфы, рулевые тяги, рычаги поворотных цапф, рулевые валы и др. Эти детали работают при больших знакопеременных нагрузках. Чтобы не снизить усталостную прочность, при изготовлении детали ОВД не закаливают до высокой твердости (подвергают нормализации или улучшению), НВ=169...440. Учитывая это, вибродуговую наплавку этих деталей ведут в защитной среде углекислого газа. Наплавкой в углекислом газе или в атмосфере можно восстанавливать детали малых диаметров с резьбой, используя проволоку ОВС диаметром 1,6 мм. Поврежденную резьбу предварительно срезают для обеспечения устойчивости сварочной дуги.
Особенности вибродуговой наплавки деталей из сч и кч?
Наплавка чугунных деталей Удовлетворительные результаты по структуре и твердости наплавленного металла получаются при наплавке деталей из серого и ковкого чугуна малоуглеродистой проволокой (Св08 и др.). отбеливание ковкого чугуна не происходит, наплавленный металл не науглераживается и не закаливается. После такой наплавки деталь из ковкого чугуна можно обрабатывать
обычным режущим инструментом. Пример наплавка отверстия под наружный подшипник ступицы переднего колеей ЗИЛ. Электродная проволока: Марка Св-08, диаметр 1,6 мм, скорость подачи 1,4 м/мин. Режим: напряжение 17 В., индуктивность - 12 витков, шаг наплавки - 2,4 мм/об, частота вращения 2 мин1, расход жидкости 0,02 л/мин (значительно меньше, чем при наплавке стальных деталей).
|
|
Детали из серого чугуна рекомендуется наплавлять малоуглеродистой проволокой в два слоя. В сером чугуне много пор, в которые при эксплуатации автомобиля проникает машинное масло (при наплавке образуется много газов). Первый слой тонкий (0,8 мм), как бы изолирует чугун. При наплавке второго слоя («1<6 мм) он частично расплавляется и отпускается, в нем "ликвидируются поры.
Для какой цели обеспечивается вибрация электрода при вибродуговой наплавке деталей?
Вибродуговая наплавка отличается тем, что возбуждение дуги происходит вибрирующим (50Гц) электродом под струей охлаждающей жидкости или защитного газа, флюса. Наплавке могут подвергаться детали из стали, ковкого и серого чугуна по наружным и внутренним цилиндрическим поверхностям, резьбе и шлицам. При коротком замыкании основное количество тепла практически аккумулируется в вылете электрода и небольшом микрообъеме поверхностного слоя детали. При этом температура жидкой ванны достигает 1450...1500°С, т.е. не превышает температуры плавления металла. Это не только смягчает тепловой режим наплавки, но и предотвращает возможность выгорания и испарения химических компонентов металла.
|
|
Преимущества электродуговой сварки в среде защитных газов в сравнении со шлаковой зашитой?
Автоматическая наплавка в среде СО2 по сравнению с наплавкой под флюсом имеет следующие преимущества; меньший нагрев детали; возможность наплавлять детали 010мм и более.
Основные затруднения при сварке деталей в среде СО2?
В процессе сварки углекислый газ, попавший в зону горения дуги, диссоциирует:2СО2 = 2СО+О2 Поэтому сварка уже происходит не в чистом углекислом газе, а в равновесной смеси газов СО2, СО и О2. Содержание кислорода в продуктах диссоциации углекислого газа только несколько меньше, чем в атмосфере воздуха. Следовательно, при сварке в среде СО2 обеспечивается практически полная защита расплавленного металла, от азота воздуха, но окислительный характер газовой смеси почти такой, же, как при сварке электродной проволокой в атмосфере воздуха. Таким образом, при сварке в среде СО2 необходимо предусматривать меры по раскислению наплавленного металла. В основном в качестве раскислителей используют кремний (0,6...1,0 %) и марганец (1...2 %), включаемые в состав электродной проволоки. Раскисление окислов железа идет по реакциям: FeO+Mn->MnO+Fe, 2FeO+Si->SiO2+2Fe. Образующиеся в процессе раскисления окислы кремния и марганца всплывают и скапливаются на поверхности сварочной ванны в виде шлака.
|
|
Недостатки сварки среде СО2?
Недостатки:1) необходимость применения легированной проволоки;2) необходимость защиты сварщика от излучаемой дуги.
Дата добавления: 2018-02-28; просмотров: 561; Мы поможем в написании вашей работы! |
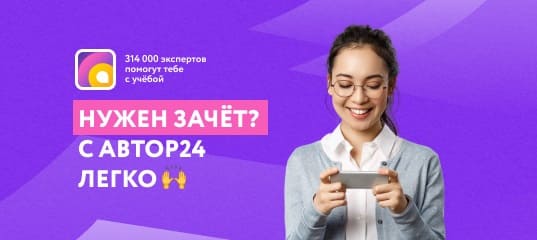
Мы поможем в написании ваших работ!