Приготовление прядильной массы;
Формование волокна;
Отделка.
Для получения исходного материала используют традиционные методы синтеза высокомолекулярных смол. Применяются очень чистые смолы, способные растворяться в растворителях или плавиться. Для очистки исходное сырье подвергается фильтрованию.
Приготовление прядильной массы состоит в растворении полимера в растворителе или его расплавлении. На этой стадии добавляются красители для получения нужного цвета.
Формование волокна производится на специальном оборудовании путем продавливания прядильной массы через фильеры - мельчайшие отверстия диаметром 0,04 мм. Образующиеся тонкие струйки раствора или расплава отверждают путем охлаждения или химическим способом с использованием специальных отвердителей. Образующиеся нити сматывают на приемные катушки. Отделка волокна состоит в его обработке различными реагентами, сушке, кручении, отбелке, вытягивании, термообработке, перемотке, сортировке.
Каучук - характерный представитель высокомолекулярных (полимерных) соединений. Он является основной составной частью резины, бывает растительного происхождения (натуральный) и синтетический. Наиболее широкое применение в промышленности получил синтетический каучук. Его химический состав и строение, а также физические свойства могут быть весьма разнообразны, и сильно отличаться от свойств натурального каучука, в чем и заключается преимущество синтетических каучуков.
|
|
Основным сырьем для производства синтетических каучуков являются попутные газы нефтепереработки, этиловый спирт и ацетилен. Основные методы получения - полимеризация и поликонденсация. При переработке каучуки превращают в резину. Она характеризуется высокой эластичностью, сопротивлением к истиранию, изгибам, обладает газо- и водонепроницаемостью, высокими электроизоляционными свойствами, стойкостью к агрессивным средам.
Резину получают добавлением к каучуку ряда компонентов (ингредиентов) и полученную смесь подвергают вулканизации. Вулканизация заключается в образовании мостиков между линейными молекулами каучука и получении трехмерной пространственной молекулярной структуры. Такая структура приводит к повышению термической стойкости и прочности материала, к уменьшению его растворимости и увеличению химической стойкости. Наиболее распространенным вулканизатором является сера, она же определяет и твердость резины. Также вводятся различные наполнители как для улучшения свойств (сажа, цинковые белила, каолин, противостарители), так и для удешевления (мел, тальк).
Резиновые изделия изготавливают: методом шприцевания, штамповкой, литьем под давлением, окунанием моделей в латекс и др. Разделяют резиновые изделия по назначению и условиям эксплуатации.
|
|
В химической промышленности наибольшие расходы приходятся на сырье и составляют в среднем 60-70 % себестоимости, а на топливо и энергию - около 10 %. Амортизационные отчисления составляют 3-4 %, заработная плата основных производственных рабочих колеблется от 3 до 20 % себестоимости продукции и зависит от типа производства.
8.6. Основные направления технологического прогресса в химической промышленности
1. Увеличение масштабов аппаратов. Обеспечит повышение производительности процессов.
2. Интенсификация работы аппаратов. Необходима для совершенствования и улучшения режимов работы аппаратов. Связана с модернизацией и реконструкцией.
3. Механизация трудоемких процессов.
4. Автоматизация и дистанционное управление процессами.
5. Замена периодических процессов непрерывными. Это аналогично применению конвейеров в механической технологии. Переход к непрерывным процессам повышает производительность труда, улучшает качество продукции и условий труда,
6. Использование, теплоты реакции.
|
|
7. Создание безотходных производств. Решает комплексно-экологическую проблему и обеспечивает снижение себестоимости продукции благодаря полному использованию всех компонентов сырья.
8. Применение прогрессивных химико-технологических процессов. К ним относятся плазмохимические процессы, фотохимические реакции, радиационно-химические процессы и биотехнологии. Особое место занимает биохимическая технология, поскольку живая клетка обладает высокоактивными, тонкоселективными биологическими катализаторами, по своей эффективности при низких (нормальных природных) температурах несравненно превышающими катализаторы, используемые в химических производствах.
ЛЕКЦИЯ 9. ОСНОВЫ ТЕХНОЛОГИИ ПРОИЗВОДСТВА СТРОИТЕЛЬНЫХ МАТЕРИАЛОВ И СТРОИТЕЛЬНОГО ПРОИЗВОДСТВА
9.1. Общие сведения о технологии производства строительных материалов и строительного производства
В технологии производства строительных материалов и строительного производства реализуются знания о классификации и свойствах строительных материалов для получения из них изделий необходимого качества и технологических характеристик. Из основных строительных технологий складываются факторы, определяющие структуру систем технологий производства строительных материалов и изделий, капитального строительства.
|
|
Основы технологии производства важнейших строительных материалов и изделий дают представления о особенностях производства керамики, стекла, минеральных вяжущих веществ, бетона и железобетона, используемых в строительном производстве. Анализируя их можно дать технико-экономическую и экологическую оценку их производства. На данном этапе развития строительных технологий развивается множество методов организации строительных работ, происходит индустриализация строительства. Основным направлением технологического прогресса в производстве строительных материалов в капитальном строительстве на данном этапе развития общественного производства является реализация технологий безотходного производства, сборочного производства, производства новых малодефицитных и экологически чистых строительных материалов, обладающих новыми свойствами.
9.2. Основные свойства строительных материалов
Свойства строительных материалов определяют области их применения. Только при правильной оценке качества материалов, т.е. их важнейших свойств, могут быть получены прочные и долговечные строительные конструкции зданий и сооружений высокой технико-экономической эффективности.
Все свойства строительных материалов по совокупности признаков подразделяют на физические, химические, механические и технологические. К физическим относятся весовые характеристики материала, его плотность, проницаемость для жидкостей, газов, тепла, радиоактивных излучений, а также способность материала сопротивляться агрессивному действию внешней эксплуатационной среды. Последнее характеризует стойкость материала, обусловливающую в конечном итоге сохранность строительных конструкций. Химические свойства по существу своему также оцениваются показателями стойкости материала при действии кислот, щелочей, растворов солей, вызывающих обменные реакции в материале и разрушение его. Механические свойства характеризуются способностью материала сопротивляться сжатию, растяжению, удару, вдавливанию в него постороннего тела и другими видами воздействий на материал с приложением силы. Технологические свойства — способность материала подвергаться обработке при изготовлении из него изделий. Эти свойства материалов рассматриваются в соответствующих разделах курса применительно к конкретному материалу.
Свойства строительного материала определяются его структурой. Для получения материала заданных свойств следует создать его внутреннюю структуру, обеспечивающую необходимые технические характеристики. В конечном итоге знание свойств материалов необходимо для наиболее эффективного его использования в конкретных условиях эксплуатации.
Структуру строительного материала изучают на трех уровнях:
- макроструктура — строение материала, видимое невооруженным глазом;
- микроструктура — строение, видимое через микроскоп; внутреннее строение вещества, изучаемое на молекулярно-ионном уровне (физико-химические методы исследования — электронная микроскопия, термография, рентгеноструктурный анализ и др.).
Макроструктуру твердых строительных материалов (исключая горные породы, имеющие свою геологическую классификацию) делят на следующие группы: конгломератная, ячеистая, мелкопористая, волокнистая, слоистая и рыхлозернистая (порошкообразная). Искусственные конгломераты представляют собой большую группу; это различного вида бетоны, керамические и другие материалы. Ячеистая структура материала отличается наличием макропор; она свойственна газо- и пенобетонам, газосиликатам и др. Мелкопористая структура характерна, например, для керамических материалов, получаемых в результате выгорания введенных органических веществ. Волокнистая структура присуща древесине, изделиям из минеральной ваты и др. Слоистая структура характерна для листовых, плитных и рулонных материалов. Рыхлозернистые материалы — это заполнители для бетонов, растворов, различного вида засыпка для теплозвукоизоляции и др.
Микроструктура строительных материалов может быть кристаллическая и аморфная. Эти формы нередко являются лишь различными состояниями одного и того же вещества, например кварц и различные формы кремнезема. Кристаллическая форма всегда более устойчива. Чтобы вызвать химическое взаимодействие между кварцевым песком и известью в производстве силикатного кирпича, применяют автоклавную обработку сырца насыщенным водяным паром с температурой 175°С и давлением 0,8 МПа, в то же время трепел (аморфная форма двуокиси кремнезема) с известью при затворении водой образует гидросиликат кальция при нормальной температуре 15-25°С. Аморфная форма вещества может перейти в более устойчивую кристаллическую.
Для каменных материалов практическое значение имеет явление полиморфизма, когда одно и то же вещество способно существовать в различных кристаллических формах, называемых модификациями. Полиморфные превращения кварца сопровождаются изменением объема. Для кристаллического вещества характерна определенная температура плавления и геометрическая форма кристаллов каждой модификации.
Свойства монокристаллов в разных направлениях неодинаковы. Теплопроводность, прочность, электропроводность, скорость растворения и явления анизотропии являются следствием особенностей внутреннего строения кристаллов.
В строительстве применяют поликристаллические каменные материалы, в которых разные кристаллы ориентированы хаотично. Эти материалы по своим свойствам относятся к изотропным, исключение составляют слоистые каменные материалы (гнейсы, сланцы и др.).
Внутренняя структура материала определяет его механическую прочность, твердость, теплопроводность и другие важные свойства.
Кристаллические вещества, входящие в состав строительного материала различают по характеру связи между частицами, образующими кристаллическую решетку. Она может быть образована: нейтральными атомами (одного и того же элемента, как в алмазе, или разных элементов, как в SiO2); ионами (разноименно заряженными, как в кальците СаСО3, или одноименными, как в металлах); целыми молекулами (кристаллы льда).
Ковалентная связь, обычно осуществляемая электронной парой, образуется в кристаллах простых веществ (алмазе, графите) или в кристаллах, состоящих из двух элементов (кварце, карборунде). Такие материалы отличаются высокой прочностью и твердостью, они весьма тугоплавки.
Ионные связи образуются в кристаллах материалов, где связь имеет в основном ионный характер, например гипс, ангидрид. Они имеют невысокую прочность, не водостойки.
В относительно сложных кристаллах (кальците, полевых шпатах) имеют место и ковалентная и ионная связи.
Молекулярные связи образуются в кристаллах тех веществ, в молекулах которых связи являются ковалентными, кристалл этих веществ построен из целых молекул, которые удерживаются друг около друга относительно слабыми ван-дер-ваальсовыми силами межмолекулярного притяжения (кристаллы льда), имеющими низкую температуру плавления.
Силикаты имеют сложную структуру. Так, волокнистые минералы (асбест) состоят из параллельных силикатных цепей, связанных между собой положительными ионами, расположенными между цепями. Ионные силы слабее ковалентных связей внутри каждой цепи, поэтому механические силы, недостаточные для разрыва цепей, расчленяют такой материал на волокна.
Пластинчатые минералы (слюда, каолинит) состоят из силикатных групп, связанных в плоские сетки. Сложные силикатные структуры построены из тетраэдров, связанных между собой общими вершинами (атомами кислорода) и образующих объемную решетку, поэтому их рассматривают как неорганические полимеры.
Состав. Строительный материал характеризуется химическим, минеральным и фазовым составом. Химический состав строительных материалов позволяет судить о ряде свойств материала — механических, огнестойкости, биостойкости, а также других технических характеристиках. Химический состав неорганических вяжущих материалов (извести, цемента и др.) и естественных каменных материалов удобно выражать содержанием в них окислов (в %). Основные и кислотные окислы химически связаны и образуют минералы, которые характеризуют многие свойства материала. Минеральный состав показывает, каких минералов и в каком количестве содержится в данном материале, например в портландцементе содержание трехкальциевого силиката составляет 45—60%, причем при большем содержании этого минерала ускоряется процесс твердения и повышается прочность. Фазовый состав и фазовые переходы воды, находящейся в его порах, оказывает большое влияние на свойства материала. В материале выделяют твердые вещества, образующие стенки пор, т.е. каркас и поры, наполненные воздухом или водой. Изменение содержания воды и ее состояния меняет свойства материала.
9.3. Свойства и основы производства керамических материалов и изделий
Керамические материалы получают из глиняных масс путем формования и последующего обжига. При этом часто имеет место промежуточная технологическая операция — сушка свежесформованных изделий, называемых «сырцом».
Универсальность свойств, широкий ассортимент, высокая прочность и долговечность керамических изделий позволяют широко использовать их в самых разнообразных конструкциях зданий и сооружений: для стен, тепловых агрегатов, в качестве облицовочного материала для полов и стен, в виде труб для сетей канализации, для облицовки аппаратов химической промышленности, в качестве легких пористых заполнителей для сборных железобетонных изделий.
Сырьем для изготовления керамических материалов служат различные глинистые горные породы. Для улучшения технологических свойств глин, а также придания изделиям определенных и более высоких физико-механических свойств к глинам добавляют кварцевый песок, шамот (дробленая обожженная при температуре 1000-1400°С огнеупорная или тугоплавкая глина), шлак, древесные опилки, угольную пыль.
Глиняные материалы образовались в результате выветривания изверженных полевошпатовых горных пород. Процесс выветривания горной породы заключается в механическом разрушении и химическом разложении. Механическое разрушение происходит в результате воздействия переменной температуры и воды. Химическое разложение происходит, например, при воздействии на полевой шпат воды и углекислоты, в результате чего образуется минерал каолинит.
Глиной называют землистые минеральные массы или обломочные горные породы, способные с водой образовывать пластичное тесто, по высыхании сохраняющее приданную ему форму, а после обжига приобретающее твердость камня.
На многих керамических заводах отсутствует сырье, пригодное в естественном виде для изготовления соответствующих изделий. Такое сырье требует введения добавок. Так, добавляя к пластичным глинам добавки до 6—10% (песок, шлак, шамот и др.), можно уменьшить усадку глины при сушке и обжиге. Большое влияние на связующую способность глин и их усадку оказывают фракции меньше 0,001 мм.
Чем больше содержание глинистых частиц, тем выше пластичность. Пластичность можно повысить добавлением высокопластичных глин, а также введением поверхностно-активных веществ — сульфитно-дрожжевой бражки (СДБ) и др. Понизить пластичность можно добавлением непластичных материалов, — кварцевого песка, шамота, шлака, древесных опилок, крошки угля.
Усадкой называют уменьшение линейных размеров и объема при сушке образца (воздушная усадка) и обжиге (огневая усадка). Воздушная усадка происходит при испарении воды из сырца в процессе его сушки. Для различных глин линейная воздушная усадка колеблется от 2—3 до 10—12% в зависимости от содержания тонких фракций. Огневая усадка происходит из-за того, что в процессе обжига легкоплавкие составляющие глины расплавляются, и частицы глины в местах их контакта сближаются. Огневая усадка в зависимости от состава глин бывает от 2 до 8%. Полная усадка равна алгебраической сумме воздушной и огневой усадок, она колеблется в пределах 5—18%. Это свойство глин учитывают при изготовлении изделий необходимых размеров.
Характерным свойством глин является их способность превращаться при обжиге в камневидную массу. В начальный период повышения температуры начинает испаряться механически примешанная вода, затем выгорают органические примеси, а при нагревании до 550—800°С происходит дегидратация глинистых минералов и глина утрачивает свою пластичность.
При дальнейшем повышении температуры осуществляется обжиг — начинает расплавляться некоторая легкоплавкая составная часть глины, которая, растекаясь, обволакивает нерасплавившиеся частицы глины, при охлаждении затвердевает и цементирует их. Так происходит процесс превращения глины в камневидное состояние. Частичное плавление глины и действие сил поверхностного натяжения расплавленной массы вызывают сближение ее частиц, происходит сокращение объема — огневая усадка. Совокупность процессов усадки, уплотнения и упрочнения глины при обжиге называют спеканием глины. При дальнейшем повышении температуры масса размягчается — наступает плавление глины.
На цвет обожженных глин оказывает влияние главным образом содержание окислов железа, которые окрашивают керамические изделия в красный цвет при наличии избытка в печи кислорода или в темно-коричневый и даже черный при недостатке кислорода. Окислы титана вызывают синеватую окраску черепка.
Для получения белого кирпича обжиг ведут в восстановительной среде (при наличии свободных СО и Н2 в газах) и при определенных температурах, чтобы окись железа перевести в закись.
Несмотря на обширный ассортимент керамических изделий, разнообразие их форм, физико-механических свойств и видов сырьевого материала, основные этапы производства керамических изделий являются общими и состоят из следующих операций:
- добычи сырьевых материалов,
-подготовки сырьевой массы,
-формования изделий (сырца),
-сушки сырца, обжига изделий,
-обработки изделий (обрезки, глазурования и пр.) и упаковки.
Добыча сырья. Заводы по производству керамических материалов, как правило, строят вблизи месторождения глины, и карьер является составной частью завода. Разработку (добычу) сырья осуществляют на карьерах открытым способом — экскаваторами. Транспортировку сырья от карьера к заводу производят автосамосвалами, вагонетками или транспортерами при небольшой удаленности карьера от цеха формовки.
Подготовка сырьевых материалов состоит из разрушения природной структуры глины, удаления или измельчения крупных включений, смешения глины с добавками и увлажнения до получения удобоформуемой глиняной массы.
Формование. Подготовку керамической массы в зависимости от свойств исходного сырья и вида изготовляемой продукции осуществляют полусухим, пластическим и шликерным (мокрым) способами. При полусухом способе производства глину вначале дробят и подсушивают, затем измельчают и с влажностью 8—12% подают на формование. При пластическом способе формования глину дробят, затем направляют в глиносмеситель, где она перемешивается с обогощающими добавками до получения однородной пластичной массы влажностью 20—25%. Формование керамических изделий при пластическом способе осуществляют преимущественно на ленточных прессах. При полусухом способе глиняную массу формуют на гидравлических или механических прессах под давлением до 15 МПа и более. По шликерному способу исходные материалы измельчают и смешивают с большим количеством воды (до 60%) до получения однородной массы — шликера. В зависимости от способа формования шликер используют как непосредственно для изделий, получаемых способом литья, так и после его сушки в распылительных сушилках.
Сушка. Современный период развития производства строительной керамики характеризуется интенсификацией технологических процессов, комплексной механизацией, конвейеризацией и автоматизацией производства. В этой связи важную роль отводят разработке новой технологии получения пресспорошка в распылительных сушилах, сущность которой заключается в совмещении процессов обезвоживания, дробления и сепарации.
Обязательной промежуточной операцией технологического процесса производства керамических изделий по пластическому способу является сушка. Если же сырец, имеющий высокую влажность, сразу после формования подвергнуть обжигу, то он растрескивается. При сушке сырца искусственным способом в качестве теплоносителя используют дымовые газы обжигательных печей, а также специальных топок. При изготовлении изделий тонкой керамики применяют горячий воздух, образуемый в калориферах. Искусственную сушку производят в камерных сушилах периодического действия или туннельных сушилах непрерывного действия.
Процесс сушки представляет собой комплекс явлений, связанных с тепло- и массообменом между материалом и окружающей средой. В результате происходит перемещение влаги из внутренней части изделий на поверхность и испарение ее. Одновременно с удалением влаги частицы материала сближаются, и происходит усадка. Уменьшение объема глиняных изделий при сушке происходит до определенного предела, несмотря на то, что вода к этому моменту полностью еще не испарилась.
В целях, получения высококачественных керамических изделий процессы сушки и обжига должны осуществляться в строгих режимах. Обжиг является завершающей стадией технологического процесса. В печь сырец поступает с влажностью 8-12%, где в начальный период происходит его досушивание.
В результате обжига изделие приобретает камневидное состояние, высокие водостойкость, прочность, морозостойкость и другие ценные строительные качества.
9.4. Свойства и основы производства минеральных вяжущих веществ
Минеральными вяжущими веществами называют тонкоизмельченные порошки, образующие при смешивании с водой пластичное тесто, под влиянием физико-химических процессов переходящее в камневидное состояние. Это свойство вяжущих веществ используют для приготовления на их основе растворов, бетонов, безобжиговых искусственных каменных материалов и изделий.
Различают минеральные вяжущие вещества воздушные и гидравлические. Воздушные вяжущие вещества твердеют, долго сохраняют и повышают свою прочность только на воздухе. К воздушным вяжущимвеществам относятся гипсовые и магнезиальные вяжущие, воздушная известь и кислотоупорный цемент. Гидравлические вяжущие вещества способны твердеть и длительно сохранять свою прочность не только на воздухе, но и в воде. В группу гидравлических вяжущих входят портландцемент и его разновидности, пуццолановые и шлаковые вяжущие, глиноземистый и расширяющиеся цементы, гидравлическая известь. Их используют как в надземных, так и в подземных и подводных конструкциях. Наряду с этим различают вяжущие вещества, эффективно твердеющие только приавтоклавной обработке — давлении насыщенного пара 0,8—1,2 МПа и температуре 170—200°С. В группу вяжущих веществ автоклавного твердения входят известково-кремнеземистые и известково-нефелиновые вяжущие, а также смеси тонкомолотого песка с портландцементом, которые хотя и могут твердеть в других условиях, но дают значительно более высокий прирост прочности при автоклавном режиме твердения.
Гипсовые вяжущие вещества делят на две группы - низкообжиговые и высокообжиговые. Низкообжиговые гипсовые вяжущие вещества получают при нагревании двуводного гипса CaSO4•2Н2О до температуры 150— 16О°С с частичной дегидратацией двуводного гипса и переводом его в полуводный гипс CaSO4•0,5Н2О. Высокообжиговые (ангидритовые) вяжущие получают обжигом двуводного гипса при более высокой температуре до 700—1000°С с полной потерей химически связанной воды и образованием безводного сульфата кальция - ангидрита CaSO4. К низкообжиговым относится строительный, формовочный и высокопрочный гипс, а к высокообжиговым — ангидритовый цемент и эстригипс.
Сырьем для производства гипсовых вяжущих служат природный гипсовый камень и природный ангидрид CaSO4, а также отходы химической промышленности, содержащие двуводный или безводный сернокислый кальций, например фосфогипс. Возможно применение гипсосодержащего природного сырья в виде сажи и глиногипса.
Производство гипса складывается из дробления, помола и тепловой обработки (дегидратации) гипсового камня. Имеется несколько технологических схем производства гипсового вяжущего: в одних помол предшествует обжигу, в других помол производится после обжига, а в третьих помол и обжиг совмещаются в одном аппарате. Последний способ получил название обжига гипса во взвешенном состоянии. Тепловую обработку гипсового камня производят в варочных котлах, сушильных барабанах, шахтных или других мельницах. Наиболее распространена схема производства гипсового вяжущего с применением варочных котлов (рисунок 9.1).
Рис. 9.1. Технологическая схема производства строительного гипса с применением варочных котлов:
1 - мостовой грейферный кран; 2 - бункер гипсового камня; 3 - лотковый питатель; 4 - щековая дробилка; 5 - ленточные транспортеры; 6 - бункер гипсового щебня; 7 - тарельчатый питатель; 8 - шахтная мельница; 9 - сдвоенный циклон; 10 - батарея циклонов; 11 - вентилятор; 12 - рукавные фильтры; 13 - пылеосадительная камера; 14 - шнеки; 15 - бункер сырого молотого гипса; 16 - камера томления; 17 - гипсоварочный котел; 18 - элеватор; 19 - бункер готового гипса; 20 - скребковый транспортер
Гипсовый камень, поступающий на завод в крупных кусках, сначала дробят, затем измельчают в мельнице, одновременно подсушивая его. В порошкообразном виде камень направляют в варочный котел периодического или в установку непрерывного действия. Последняя имеет в 2-3 раза выше производительность, но еще находится в стадии практического освоения.
Варочный котел периодического действия (рисунок 9.2) представляет собой обмурованный кирпичом стальной котел 1 со сферическим днищем 2, обращенным выпуклой стороной внутрь цилиндра. Для перемешивания гипса в котле имеется мешалка 3, приводимая в движение электродвигателем 4. Раскаленные топочные газы обогревают днище и стенки котла, а также проходят через жаровые трубы 5 внутри котла и в охлажденном состоянии удаляются по дымовой трубе. Продолжительность варки — 90—180 мин. При варке в котле гипс не соприкасается с топочными газами, что позволяет получать чистую продукцию, не загрязненную золой топлива.
Рис. 9.2. Варочный котел для изготовления строительного гипса: 1 - днище; 2 - мешалка; 3 - электродвигатель; 4 - котел; 5 – жаровые трубы; 6 - выгрузочный желоб
Гипсовое вяжущее в сушильных барабанах получают путем обжига гипсового камня в виде щебня размером до 20 мм. Обжиговой частью сушильного барабана служит наклонный стальной цилиндр диаметром до 2,5 м и длиной до 20 м, установленный на роликовых опорах и непрерывно вращающийся. Гипсовый щебень подается в барабан с приподнятой стороны и в результате вращения наклонного барабана перемещается в сторону наклона. Из топки в барабан поступают раскаленные дымовые газы, которые при движении вдоль барабана обжигают гипсовый камень, а с противоположной стороны удаляются вентилятором. Далее гипсовый камень измельчают в мельницах.
Применяется гипсовое вяжущее для производства гипсовых и гипсобетонных строительных изделий для внутренних частей зданий (перегородочных плит, панелей, сухой штукатурки, приготовления гипсовых и смешанных растворов, производства декоративных и отделочных материалов, например искусственного мрамора), а также для производства гипсоцементно-пуццолановых вяжущих.
Высокопрочный гипс является разновидностью полуводного гипса. Высокопрочный гипс выпускают пока в небольшом количестве и применяют в основном в металлургической промышленности для изготовления форм. Однако он успешно может заменить обыкновенное гипсовое вяжущее, обеспечив изделиям высокую прочность.
Формовочный гипс состоит в основном из кристаллов /3-модификации и незначительного количества примесей. Он обладает повышенной водопотребностью, а будучи затвердевшим, имеет высокую пористость. Это свойство формовочного гипса успешно используется в керамической и фарфорофаянсовой промышленности для изготовления форм.
Ангидритовое вяжущее получают обжигом природного двуводного гипса при температуре 600—700°С с последующим его измельчением с добавками — катализаторами твердения (известью, смесью сульфата натрия с медным или железным купоросом, обожженным доломитом, основным доменным гранулированным шлаком и др.). Ангидритовое вяжущее можно получить также путем помола природного ангидрида с указанными выше добавками.
Ангидритовый цемент — это медленно схватывающееся вяжущее вещество с началом схватывания не ранее 30 мин, концом — не позднее 24 ч.
Применяют ангидритовые цементы для приготовления кладочных и отделочных растворов, бетонов, производства теплоизоляционных материалов, искусственного мрамора и других декоративных изделий.
Высокообжиговый гипс (эстрих-гипс) является разновидностью ангидритовых цементов. Высокообжиговый гипс медленно схватывается и твердеет, но водостойкость и прочность при сжатии (10—20 МПа) позволяют успешно использовать его при устройстве мозаичных полов, изготовлении искусственного мрамора и др. Изделия из высокообжигового гипса мало-, тепло- и звукопроводны, они обладают по сравнению с изделиями из гипсового вяжущего более высокой морозостойкостью, повышенной водостойкостью и меньшей склонностью к пластическим деформациям.
Строительную известь получают путем обжига (до удаления углекислоты) из кальциево-магниевых горных пород — мела, известняка, доломи-тизированных и мергелистых известняков, доломитов.
Для производства тонкодисперсной строительной извести гасят водой или размалывают негашеную известь, вводя при этом минеральные добавки в виде гранулированных доменных или электротермофосфатных шлаков, активные минеральные добавки или кварцевые пески. Строительную известь применяют для приготовления строительных растворов и бетонов, вяжущих материалов и в производстве искусственных камней, блоков и строительных деталей.
В зависимости от условий твердения различают строительную известь воздушную, обеспечивающую твердение строительных растворов и бетонов и сохранение ими прочности в воздушно-сухих условиях, и гидравлическую, обеспечивающую твердение растворов и бетонов и сохранение ими прочности в воздушно-влажных условиях
Портландцемент является важнейшим вяжущим веществом. По производству и применению он занимает первое место среди всех других вяжущих веществ..
Портландцемент — гидравлическое вяжущее вещество, твердеющее в воде и на воздухе. Оно получается тонким измельчением обожженной до спекания сырьевой смеси известняка и глины, обеспечивающей преобладание в клинкере силикатов кальция. Спекшаяся сырьевая смесь в виде зерен размером до 40 мм называется клинкером; от качества его зависят важнейшие свойства цемента: прочность и скорость ее нарастания, долговечность, стойкость в различных эксплуатационных условиях.
Портландцемент, получаемый на заводах из различных видов природного сырья и с неодинаковой технологией производства, отличается как по химико-минералогическому составу, так и по свойствам.
Технологический процесс производства портландцемента состоит из следующих основных операций: добычи известняка и глины, подготовления сырьевых материалов и корректирующих добавок, приготовления из них однородной смеси заданного состава, обжига смеси и измельчения клинкера в тонкий порошок совместно с гипсом, а иногда с добавками.
В зависимости от приготовления сырьевой смеси различают два основных способа производства портландцемента: мокрый и сухой. При мокром способе сырьевые материалы измельчают и смешивают в присутствии воды, и смесь в виде жидкого шлама обжигают во вращающихся печах; при сухом способе материалы измельчают, смешивают и обжигают в сухом виде. В последнее время все шире начинает применяться комбинированный способ приготовления сырьевой смеси, по которому сырьевую смесь подготовляют по мокрому способу, затем шлам обезвоживают и из него приготовляют гранулы, которые обжигают по сухому способу.
9.5. Свойства и основы производства бетона и железобетона
Бетон — искусственный камень, получаемый в результате формования и твердения рационально подобранной смеси вяжущего вещества, воды и заполнителей (песка и щебня или гравия). Смесь этих материалов до затвердения называют бетонной смесью.
Зерна песка и щебня составляют каменный остов в бетоне. Цементное тесто, образующееся после затвердения бетонной смеси водой, обволакивает зерна песка и щебня, заполняет промежутки между ними и играет роль смазки заполнителей, придающей бетонной смеси подвижность (текучесть). Цементное тесто, затвердевая, связывает зерна заполнителей, образуя искусственный камень — бетон.
Бетон в сочетании со стальной арматурой называют железобетоном.
Получение смеси и бетона хорошего качества возможно только при глубоком знании их технологии; умелом подборе составляющих материалов надлежащего качества и в оптимальных соотношениях; режимах приготовления бетонной смеси, методах ее укладки, уплотнения в условиях твердения, обеспечивающих получение бетонных конструкций высокой прочности, долговечности и низкой стоимости.
Бетон является одним из важнейших строительных материалов во всех областях современного строительства. Это объясняется изменением свойств бетона в широком диапазоне путем использования компонентов соответствующего качества, применения специальных методов механической и физико-химической обработки, возможностью изготовления самых разнообразных по форме и размерам долговечных строительных конструкций, возможностью полной механизации бетонных работ, экономичностью бетона, так как до 80-85% объема его составляют заполнители из местных каменных материалов.
Бетоны классифицируют по следующим ведущим признакам: плотности, прочности, долговечности, виду вяжущего вещества и заполнителя и по назначению.
Основной считается классификация бетона по плотности, в результате чего бетон делят на особо тяжелый плотностью более 2500 кг/м3 тяжелый - 2200 - 2500 кг/м3, облегченный - 1800 - 2200 кг/м3 и легкий — 500 — 1800 кг/м3, особо легкий (теплоизоляционный) — менее 500 кг/м3.
В зависимости от крупности применяемого заполнителя бетоны бывают на мелкозернистом заполнителе (до 10 мм) и крупнозернистом (10-150 мм).
Важнейшими показателями качества бетона являются его прочность и долговечность. По показателям прочности при сжатии бетоны имеют следующие марки: тяжелые бетоны - М50 - 800, легкие - М25 - 400.
Бетоны, предназначенные для зданий и сооружений, делят на 19 классов (В1; В 1,5; В2;...;В60, а также С0,8; С 1,2; С 1,6; С2;...;С55), основной контролируемой характеристикой которых является прочность при сжатии кубов размером 150х150х х150 мм и соответственно цилиндров размером 150x300 мм. Кроме того, контролируемыми характеристиками являются прочность на растяжение, морозостойкость и водонепроницаемость.
Долговечность бетона оценивают степенью морозостойкости. По этому показателю бетоны делят на марки: для тяжелых бетонов Мрз50—500 и легких бетонов— Мрз 15—500.
По виду вяжущего вещества бетоны бывают: цементные, изготовленные на гидравлических вяжущих веществах — портландцементные и его разновидностях; силикатные — на известковых вяжущих в сочетании с силикатными или алюминатными компонентами; гипсовые — с применением гипсоангидритовых вяжущих; бетоны на неорганических и органических вяжущих материалах. В настоящей главе рассмотрены бетоны на минеральных вяжущих веществах. Тяжелые бетоны изготовляют на цементе и обычных плотных заполнителях, а легкие — на цементе с применением естественных или искусственных пористых заполнителей. Разновидностью легкого бетона является ячеистый бетон, представляющий собой отвердевшую смесь вяжущего вещества, воды и тонкодисперсного кремнеземистого компонента. Он отличается высокой пористостью до 80 — 90% с равномерно распределенными порами размером 3 мм. Силикатные бетоны получают из смеси извести и кварцевого песка с последующим твердением сформованных изделий в автоклаве при давлении 0,8 — 1,2 МПа и температуре 170-200°С.
По виду заполнителя различают бетоны: на плотных заполнителях, пористых, специальных, удовлетворяющих специальным требованиям (защиты от излучений, жаростойкости, химической стойкости и т.п.).
По назначению бетон бывает следующих видов: обычный — для бетонных и железобетонных несущих конструкций зданий и сооружений (колонны, балки, плиты); гидротехнический — для плотин, шлюзов, облицовки каналов и др.; для стен зданий и легких перекрытий; для полов и дорожных покрытий и оснований; специальный — кислотоупорный, жароупорный, особо тяжелый для биологической защиты; особо тяжелый на цементе с применением специальных видов заполнителей высокой плотности.
Приготовление бетонной смеси включает две основные технологические операции — дозировку исходных материалов и их перемешивание.
Важнейшим условием приготовления бетонной смеси с заданными показателями свойств, а также обеспечения постоянства эти показателей от замеса к замесу является точность дозировки составляющих материалов в соответствии с рабочим составом бетона. Дозирование материалов производят дозаторами (мерниками) периодического или непрерывного действия. Первые могут иметь ручное, полуавтоматическое или автоматическое управление.
Перемешивание бетонной смеси производят в бетоносмесителях периодического и непрерывного действия. В бетоносмесителях периодического действия рабочие циклы машины протекают с перерывами, т.е. в них периоически загружаются отвешенные порции материалов, перемешивают и далее бетонная смесь выгружается. В бетоносмесителях непрерывного действия все три операции производятся непрерывно.
Продолжительность перемешивания бетонной смеси зависит от подвижности бетонной смеси и емкости бетоносмесителя. Чем меньше подвижность бетонной смеси и чем больше рабочая емкость бетоносмесителя, тем больше оптимальное время перемешивания. На автоматизированных бетонных заводах применяют бетоносмесители непрерывного действия, в которых бетонная смесь принудительно перемешивается и одновременно перемещается от загрузочного отверстия к другому концу, где происходит ее выгрузка.
Для приготовления жестких и особо жестких бетонных смесей созданы так называемые вибросмесители, в которых перемешивание составляющих материалов осуществляется в сочетании с вибрацией, а в некоторых конструкциях — только вибрацией.
В технологию приготовления бетонной смеси начинает внедряться перемешивание с нагреванием смеси. Суть этого метода состоит в том, что разогрев бетонной смеси до 60—65°С производят паром, подаваемым в смеситель в процессе ее перемешивания. Такое нагревание происходит равномерно, проще и во много раз быстрее, чем при предварительном нагреве воды и заполнителей, а также электроразогреве смеси.
Транспортирование бетонной смеси к месту укладки должно обеспечить сохранение ее однородности и степени подвижности. При длительной перевозке бетонная смесь загустевает вследствие гидратации цемента, поглощения воды заполнителями и испарения, однако подвижность смеси к моменту укладки ее должна быть не меньше проектной.
При выборе способа транспортирования необходимо учитывать дальность и скорость перевозки, подвижность смеси и экономичность способа. На заводах бетонные смеси транспортируют бетонораздатчиками, самоходными тележками, ленточными транспортерами; в цехах малой и средней мощности — электротельферами и электрокарами. Подвижные смеси можно транспортировать на большие расстояния по трубам с помощью пневматических установок. На строительные площадки, где ведутся бетонные работы, бетонную смесь доставляют на автосамосвалах или автобетоносмесителях, в которых бетонную смесь перемешивают примерно за 5 мин до прибытия на место.
Железобетонные изделия для сборного строительства - относительно новый вид конструктивных элементов. Начало практического применения их относят к концу прошлого столетия. В 20-х и 30-х годах текущего столетия появились первые здания, выполненные в основном из сборных железобетонных изделий. Однако широкому и всестороннему применению сборного железобетона в то время препятствовал низкий уровень механизации строительства, отсутствие мощных монтажных кранов и оборудования для производства железобетонных изделий.
За прошедшие годы в СНГ создана самая крупная в мире индустриальная промышленность сборного железобетона. Если в 1954 г. было выпущено около 2 млн;м3 сборных железобетонных изделий, то в 1980 г. общий выпуск сборного железобетона составил 122 млн. м3. Наряду с увеличением выпуска расширяется номенклатура железобетонных изделий, увеличиваются их размеры. Накоплен некоторый опыт строительства зданий с применением объемных элементов.
Основные факторы, обеспечивающие столь быстрый подъем производства сборного железобетона следующие:
1) максимальная степень заводской готовности, что дает определенный технико-экономический эффект;
2) универсальность свойств железобетонных изделий; путем определенных технологических приемов изготовления и соответствующего выбора материалов железобетонные изделия могут быть получены с различными механическими и физическими свойствами — высокопрочные, водонепроницаемые, жаростойкие, с низкой теплопроводностью и т.д.;
3) долговечность;
4) возможность значительно сократить расход стали в строительстве.
Наряду с достоинствами железобетонные конструкции обладают и недостатками:
1) большая плотность;
2) высокая себестоимость изделий;
3) значительные транспортные расходы.
Все это снижает общую технико-экономическую эффективность строительства из сборных железобетонных изделий.
Первостепенной задачей производственников и конструкторов является уменьшение массы сборных железобетонных конструкций путем применения материалов высокого качества и более рациональных форм изделий, совершенствование организации технологического процесса, более полная его механизация с широким использованием автоматического управления.
Железобетон представляет собой строительный материал, в котором выгодно сочетается совместная работа бетона и стали.
В различных конструкциях, в зависимости от местных условий, фактора цен и т.д., эффективность взаимозаменяемых материалов проявляется по-разному. Расчеты показывают, что в тех случаях, когда строительство ведется в труднодоступных районах, стальные конструкции оказываются, как правило, эффективнее железобетонных. При наличии сред агрессивных и повышенной влажности во многих случаях более целесообразно использовать железобетон.
Экономичность металлических конструкций определяется их конструктивной формой, возможностью индустриального изготовления, степенью совершенствования монтажа зданий и сооружений.
Отечественная и зарубежная практика строительства свидетельствует об экономической целесообразности более широкого использования легких алюминиевых сплавов в различных строительных конструкциях. Интересно, что около 1/5 всего вырабатываемого в мире алюминия сегодня используется для нужд строительства. Алюминиевые сплавы желательно использовать в ряде несущих и ограждающих конструкций, для заполнения оконных проемов и устройства витражей, при сооружении мостов, емкостей для хранения различных материалов и продуктов, для отражательной теплоизоляции и в других целях. Эффективность применения алюминиевых сплавов в строительстве также зависит от района его использования. Так, наибольший экономический эффект применения алюминия получен в районах Крайнего Севера, а также в труднодоступных и сейсмических районах.
Наиболее целесообразно применять железобетон для строительных элементов, подверженных изгибу. При работе таких элементов возникают напряжения двух видов — растягивающие и сжимающие. При этом сталь воспринимает первые напряжения, а бетон вторые, и железобетонный элемент в целом успешно противостоит изгибающим нагрузкам. Таким образом сочетается работа бетона и стали в одном материале — железобетоне.
Возможность совместной работы в железобетоне двух резко различных по своим свойствам материалов определяется следующими важнейшими факторами: прочным сцеплением бетона со стальной арматурой, вследствие этого при возникновении напряжения в железобетонной конструкции оба материала работают совместно; почти одинаковым коэффициентом температурного расширения для стали и бетона, чем обеспечивается полная монолитность железобетона; бетон не только не оказывает разрушающего влияния на заключенную в нем сталь, но и предохраняет ее от коррозии.
В зависимости от способа армирования и состояния арматуры различают железобетонные изделия с обычным армированием и с предварительно напряженным. Армирование бетона стальными стержнями, сетками или каркасами не предохраняет изделия, работающие на изгиб, от образования трещин в растянутой зоне бетона, так как последний обладает незначительной растяжимостью (1—2 мм на 1 м), тогда как сталь выдерживает без разрушения в 5—6 раз большие растягивающие напряжения, чем бетон. Появление трещин отрицательно влияет на работу железобетонного элемента: увеличиваются прогибы, в трещины проникают влага и газы, отчего создается опасность коррозии стальной арматуры.
Избежать образования трещин в железобетонной конструкции можно предварительным сжатием бетона в местах, подверженных растяжению. В предварительно сжатом бетоне трещины появляются только в том случае, если растягивающие напряжения перерастут напряжения предварительного сжатия. Сжатие бетона достигается предварительным (растяжением) арматуры.
Различают два вида предварительного напряжения арматуры — до затвердения бетона и после приобретения бетоном определенной прочности. Бели напряжение арматуры производится до бетонирования, то уложенная в форму арматура растягивается и в таком состоянии закрепляется в форме. После заполнения формы бетонной смесью и затвердения бетона арматура освобождается от натяжения, сокращается и увлекает за собой окружающий ее бетон, обжимая железобетонный элемент в целом. Если же напряжение арматуры производится после затвердения бетона, то в этом случае арматуру располагают в специально оставленном в бетоне канале. После затвердения бетона арматуру натягивают и закрепляют на концах конструкции анкерными устройствами. Затем заполняют канал раствором, который после затвердения сцепляется с арматурой и с бетоном конструкции, обеспечивая монолитность железобетона.
По виду армирования железобетонные изделия делят на предварительно напряженные и. с обычным армированием.
В зависимости от назначения сборные железобетонные изделия делят на основные группы: для жилых, общественных, промышленных зданий, для сооружений сельскохозяйственного строительства и изделий общего назначения.
Железобетонные изделия должны отвечать требованиям действующих государственных стандартов, а также требованиям рабочих чертежей и технических условий на них. Изделия массового производства должны быть типовыми и унифицированными для возможности применения их в зданиях и сооружениях различного назначения.
Изделия должны иметь максимальную степень заводской готовности.
Составные или комплексные изделия поставляют потребителю, как правило, в законченном, собранном и полностью укомплектованном деталями виде. Железобетонные изделия с проемами поставляют со вставленными оконными или дверными блоками, проолифленными или загрунтованными. Качество поверхности изделий должно быть таким, чтобы на месте строительства (если это не предусмотрено проектом) не требовалось дополнительной их отделки.
Технологический процесс производства железобетонных изделий складывается из следующих последовательно выполняемых операций: приготовления бетонной смеси; армирования железобетонных изделий; формования; тепловлажностной обработки, обеспечивающей получение необходимой прочности бетона изделий к заданному сроку; отделки лицевой поверхности изделий.
Организация выполнения этого комплекса основных технологических операций и их техническое оформление в современной технологии сборного железобетона осуществляются по трем принципиальным схемам:
1. Изготовление изделий в неперемещаемых формах; в этом случае все технологические операции от подготовки форм до распалубки готовых отвердевших изделий осуществляются на одном месте. К этому способу относится формование изделий на плоских стендах или матрицах, в кассетах.
2. Изготовление изделий в перемещаемых формах, в этом случае отдельные технологические операции формования или отдельный комплекс их производится на специализированных постах. Форма, а затем изделие вместе с формой перемещаются от поста к посту по мере выполнения отдельных операций. В зависимости от степени расчлененности общего технологического процесса формования по отдельным постам различают конвейерный, имеющий наибольшую расчлененность, и поточно-агрегатный.способы. Последний отличается тем, что ряд операций — укладка арматуры и бетонной смеси, уплотнение — выполняются на одном посту, т.е. сагрегированы между собой. При конвейерном способе большинство операций выполняется на соответствующих постах, образующих в совокупности технологическую линию.
3. Непрерывное формование — способ, возникший сравнительно недавно, но хорошо зарекомендовавший себя. Он отличается металлоемкостью и несравнимо высоким объемом продукции с единицы производственной площади предприятия. Способ непрерывного формования изделий осуществляется на вибропрокатном стане.
9.6. Общая характеристика применяемых в строительных технологиях конструкций из древесины
Конструкции из древесины и индустриальные строительные детали изготовляют на специальных строительных заводах.
Комплекты деревянных изделийи деталей для домов заводского изготовления делят на следующие группы: комплекты для брусчатых домов; для каркасных домов со стенами несущего деревянного или железобетонного каркаса с различными заполнителями; для панельных домов со стенами из несущих панелей - деревянных (щитов), железобетонных или других материалов; для домов со стенами из местных каменных и других строительных материалов. Комплекты деревянных изделий и деталей изготовляют из древесины хвойных (сосны, ели, лиственницы, кедра, пихты) и лиственных пород (бука, березы, тополя, ольхи, осины, липы).
Изделия и детали поставляют на стройку в готовом виде, исключающем мх подгонку; детали и изделия, соприкасающиеся с землей, антисептируют.
Клееные конструкции применяют в покрытиях, перекрытиях, мостах в качестве балок прямоугольного и двутаврового сечения, а также в виде арок и частей металлодеревянных ферм в виде криволинейных и прямолинейных блоков верхних поясов ферм и элементов решетки, рам и стоек, свай и шпунта, мостовых брусьев, шпал, клеефанерных щитов (покрытий' стен и перекрытий), а также инвентарной опалубки. Клееные конструкции изготовляют путем склейки из досок (брусков) или из досок (брусков) и фанеры. Для изготовления прямолинейных клееных конструкций применяют доски и бруски толщиной не более 50 мм и шириной не более 100 мм для досок, склеиваемых под углом 90°, и не более 150 мм для досок, склеиваемых под углом 45°. В зависимости от вида работы элементы деревянных клееных несущих конструкций делят на пять категорий.
Влажность древесины для изготовления клееных конструкций не должна превышать 12%. Элементы конструкций, подвергающиеся увлажнению, изготовляют на водостойких клеях типа фенолоформальдегидного.
9.7. Основы технологии получения строительных пластмасс, полимеров и изделий из них
Пластмассами называют обширную группу органических материалов, основу которых составляют искусственные или природные высокомолекулярные соединения — полимеры, способные при нагревании и давлении формоваться и устойчиво сохранять приданную им форму. Главными компонентами пластмасс являются: связующее вещество — полимер; наполнители в виде органических или минеральных порошков, волокон, нитей, тканей, листов; пластификаторы; стабилизаторы, отвердители и красители.
В основу классификации пластмасс положены их физико-механические свойства, структура и отношение к нагреванию.
По физико-механическим свойствам все пластмассы разделяют на пластики и эластики.
Пластики бывают жесткие, полужесткие и мягкие. Жесткие пластики — твердые упругие материалы, аморфной структуры с высоким модулем упругости (свыше 1000 МПа) и малым удлинением при разрыве, сохраняющие свою форму при внешних напряжениях в условиях нормальной или повышенной температуры. Полужесткие пластики — твердые упругие материалы кристаллической структуры со средним модулем упругости (выше 400 МПа), высоким относительным и остаточным удлинением при разрыве, причем остаточное удлинение обратимо и полностью исчезает при температуре плавления кристаллов. Мягкие пластики — мягкие и эластичные материалы с низким модулем упругости (не выше 20 МПа), высоким относительным удлинением и малым остаточным удлинением, причем обратимая деформация исчезает при нормальной температуре с замедленной скоростью.
Эластики — мягкие и эластичные материалы с низким модулем упругости (ниже 20 МПа), поддающиеся значительным деформациям при растяжении, причем вся деформация или большая ее часть исчезает при нормальной температуре с большой скоростью (практически мгновенно).
По строению полимерной цепи различают пластмассы карбоцепные (цепь состоит только из атомов углерода) и гетероцепные (в состав цепи кроме углерода входят кислород, азот и другие элементы).
По структуре пластмассы делят на гомогенные (однородные) и гетерогенные (неоднородные). Структура пластмасс зависит от введения в нее наряду с полимером других компонентов. Последнее позволяет делить пластмассы на ненаполненные, газонаполненные, наполненные и составные.
В технологии производства строительных пластмасс полимеры, получаемые синтезом из простейших веществ (мономеров), по способу производства подразделяются на два класса:
класс А — полимеры, получаемые цепной полимеризацией,
класс Б — полимеры, получаемые поликонденсацией и ступенчатой полимеризацией.
Наиболее распространенными полимерами, применяемыми в производстве строительных материалов, являются:
по классу А — полиэтилен, полипропилен, поливинилхлорид, полиизобутилен полистирол, поливинилацетат, полиарилаты и кумароноинденовые полимеры;
по классу Б — фенолоальдегидные, фенолоформальдегидные и резорцинформальдегидные полимеры, полимеры на основе амидо- и аминоформальдегидной поликонденсации, глифталевый полимер, полиуретаны, полиэфирмалеинатные и полиэфиракрилатные полимеры, а также кремнийорганические и эпоксидные полимеры.
Строительные материалы и изделия, изготовляемые на основе полимеров, дефицитны и дороги. Это объясняется недостаточным объемом производства полимеров и их относительно высокой стоимостью. Основное требование к пластмассам — минимальный расход полимера на единицу готовой продукции. Это требование выявило основные области их использования в строительстве, к ним следует отнести: материалы для покрытия полов; внутренней отделки стен, потолков и встроенной мебели; для строительных конструкций; синтетические клеи и мастики; тепло- и звукоизоляционные материалы; кровельно-гидроизоляционные и герметизирующие материалы; санитарно-техническое оборудование, трубопроводы и арматура; синтетические лакокрасочные материалы.
ЛЕКЦИЯ 10. ОСНОВЫ ТЕХНОЛОГИИ ЛЕГКОЙ ПРОМЫШЛЕННОСТИ
10.1. Общая характеристика легкой промышленности
Двадцатый век вошел в историю как столетие революционных изменений в развитии технологических процессов в различных сферах деятельности человека, а также как время социальных перемен. Развитые страны переходят от индустриального общества к информационному, изменяется облик науки, техники, человека и общества. Благодаря научно-технической революции произошли коренные изменения в области, пищевой и легкой промышленности. Новые технологические процессы используемые в легкой промышленности становятся основным фактором экономических и социальных преобразований, благодаря которым человек изменяет все сферы своей жизни и меняется сам.
Экспансия новых технологий в легкой промышленности породила ряд проблем, являющихся как сугубо технологическими, так и социальными (политическими, культурологическими, психологическими, экологическими, медицинскими и т. д.). Например, современная экологическая ситуация такова, что вероятность технологических катастроф ставит под угрозу существования на огромных территориях животных и человека. На фоне захватывающих человечество технологических новаций прослеживается конфликтная ситуация между человеком, обществом и природой, разрешение которой является одной из актуальных проблем нашего времени. А легкая промышленность оказывает на экологическую ситуацию большое влияние.
Основными направлениями развития легкой промышленности является применение прогрессивных технологических процессов, что в свою очередь расширяет возможности автоматизации выполняемых работ и повышает их качественный уровень, оптимизирует и стабилизирует параметры техпроцесса, уменьшает расход ресурсов (сырья, материалов, энергии, инструмента, трудозатрат и т. д.), приводит к экологической и экономической эффективности. Приоритет отдается тому технологическому направлению, который обеспечивает достаточно высокий уровень производства. На протяжении всей истории развития легкой промышленности позитивные изменения происходили под влиянием технологических и технических новаций.
Технологическая структура легкой промышленности многообразна и имеет сложные технологические связи. В легкую промышленность входят такие технологии, как технологии текстильного производства, технологии прядения и ткачества, технологии обувного производства, и др.
10.2. Основы технологии легкой промышленности на примере текстильного производства. Основные направления развития текстильной промышленности
Текстильная отрасль промышленности является частью легкой промышленности.
На современном этане большое внимание уделяется развитию производства предметов потребления.
Легкая индустрия включает текстильную швейную обувную кожевенную и другие отрасли промышленности. Текстильная промышленность выпускает примерно пятую часть всей промышленной продукции в СНГ и дает часть всех доходов поступающих в бюджет.
Текстильная промышленность с ее хлопчатобумажной льняной шерстяной и трикотажной отраслями является важнейшей комплексной отраслью легкой индустрии.
В текстильной промышленности имеется ряд научно исследовательских и проектных институтов конструкторских бюро.
Текстильная пpoмышлeннocть производит продукцию групп A и Б. Выработки бытовых и технических тканей и ткани идущие на швейные предприятия для производства одежды относятся к группе А. Ткани, нити, вата, ватин, трикотаж и другие изделия реализуемые в торговле относятся к группе Б.
Текстильная промышленность обеспечивает тканями оборонную, химическую, машиностроительную, электромеханическую, автомобильную, авиационную и другие отрасли промышленности, строительство транспорт сельское хозяйство Большая доля прироста продукции в текстильной промышленности будет достигнута в процессе внедрении достижении науки.
С ростом производства тканей будет расти и сырьевая база.
Научно-исследовательскими институтами синтетических волокон (ВНИИСВ) созданы новые виды полиэфирных нитей, текстурированные с фасонным эффектом и с креповым эффектом. Нити комбинированные и с фасонным эффектом состоят из двух нитей, одну из которых получают классическим способом, а вторую высокоскоростным способом формования. Эти нити используются для производства трикотажных изделий.
Разработана также технология получения модифицированных полиамидных волокон повышенной гидрофильности и пониженной электризуемости, обладающих хлопко- и шерстоподобным грифом. Из новых волокон в смеси с другими химическими волокнами производят чулочно-носочные изделия и одеяла.
Ведутся работы по широкому использованию крученой, эффектной, высокообъемной, стержневой пряжи, пряжи с разным направлением крутки и других новых видов пряжи к нитей. Таким образом, применение натуральных и новых химических волокон и пряжи новых структур обеспечит увеличение объема тканей и изделий из них, расширение, улучшение ассортимента и повышение их качества.
Это способ позволяет сократить технологический процесс производства пряжи из химических волокон и их смесей с натуральными волокнами. В шерстяной, шелковой и льняной отраслях промышленности отечественные машины полностью заменили импортные. Внедрение одной такой машины дает возможность получить экономию в размере до 30 тыс. руб. в год за счет сокращения числа технологических переходов и повышения производительности труда. Внедрение новых машин позволяет использовать жгутовые химические волокна большой линейной плотности в чистом виде и в смеси с хлопком в хлопкопрядении.
В настоящее время Отраслевая научно-исследовательская лаборатория по разработке новых высокопроизводительных технологических процессов безверетенных способов прядения проводит комплекс научно-исследовательских работ по созданию новых отечественных пневмопрядильных машин, в том числе машины для производства гребенной шерстяной пряжи, новой однопереходной пневмомеханической прядильной машины для производства пряжи из малоразвесного жгутового химического волокна.
Дата добавления: 2016-01-04; просмотров: 13; Мы поможем в написании вашей работы! |
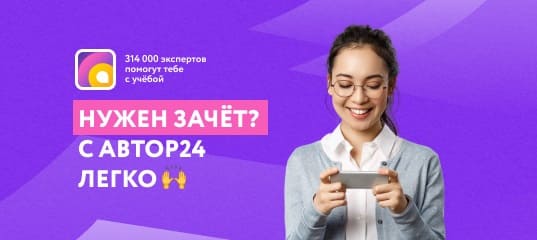
Мы поможем в написании ваших работ!