Деформация - изменение формы и размеров твердого тела под воздействием приложенных к нему нагрузок. Различают деформацию упругую (обратимую) и пластическую (необратимую).
Упругой деформацией называют такую, которая исчезает после снятия нагрузок, т.е. тело восстанавливает свою первоначальную форму.
Пластическая деформация остается после снятия внешней нагрузки, т.е. тело не восстанавливает первоначальную геометрическую форму и размеры. Пластическая деформация сопровождается смещением одной части кристалла относительно другой на расстояния, значительно превышающие расстояния между атомами в кристаллической решетке металлов и сплавов.
Способность металлов и сплавов к пластической деформации имеет важное практическое значение, так как все процессы обработки металлов давлением основаны на пластическом деформировании заготовок.
Пластичность - способность твердого тела сохранять целостность без видимых (макроскопических) нарушений в процессе деформирования. Она зависит от химического состава, строения кристаллической решетки металла, температуры, скорости деформации и ряда других факторов.
Приближенно пластичность может быть оценена относительным удлинением и относительным сужением образцов при испытании на растяжение. При пластической деформации изменяется не только форма, но и существенно изменяются свойства деформируемого металла. В реальном поликристаллическом металле происходит изменение формы зерен (кристаллитов), дробление отдельных зерен, а также их механических магнитных и электрических свойств В общем случае анизотропия свойств металла отрицательно сказывается при последующей его обработке и эксплуатации изделий. Общее изменение механических и физико-химических свойств металла при пластической деформации принято называть упрочнением наклепом - явление упрочнения проявляется в том, что по мере перемещения инструмента относительно деформируемой заготовки и увеличения степени деформации сопротивление металла деформированию повышается. При упрочнении снижается пластичность, ударная вязкость, увеличивается предел текучести и твердость, что может вовлечь за собой развитие микро- и макротрещин в деформируемом металле.
|
|
Степень упрочнения металла зависит от многих факторов, важнейшие из которых: исходные свойства металла, температура, степень и скорость деформации. Чем выше степень деформации и ниже температура процесса, тем больше упрочнение.
Степень деформации (важнейший фактор, определяющий производительность процессов обработки металлов давлением) - абсолютное или относительное изменение размеров заготовки при деформировании. Так, при прокатке степень деформации характеризуется линейным (абсолютным) обжатием, т. е. разностью высот полосы до и после обжатия. Относительное обжатие - отношение абсолютного обжатия к первоначальной высоте полосы, выраженное в процентах.
|
|
Для восстановления пластичности холоднодеформированного упрочненного металла его подвергают рекристаллизационному отжигу, Процесс рекристаллизации протекает с определенной скоростью, зависящей от температуры и степени предшествующей деформации: чем выше температура и степень деформации, тем больше скорость рекристаллизации. Для каждого металла экспериментально устанавливается связь между размером зерна, степенью деформаций и температурой рекристаллизации в виде диаграмм, которые используются также при назначении термомеханических режимов горячей обработки давлением.
Горячая обработка металлов давлением обычно производится при температурах, значительно превышающих температуру их рекристаллизации, когда скорость процесса разупрочнения, вызванного рекристаллизацией, обычно превышает скорость процесса упрочнения. Зерна в металле получаются тем мельче, чем больше степень деформации.
Перед горячей обработкой давлением (прокаткой, ковкой, штамповкой) металлы и сплавы нагревают до определенной температуры (начала горячей обработки давлением) для повышения их пластичности и уменьшения сопротивления деформированию. Однако в процессе обработки температура металла понижается. Минимальная температура, при которой можно производить обработку, называется температурой окончания обработки давлением. Область температур между началом и окончанием обработки, в которой металл или сплав обладает наилучшей пластичностью, наименьшей склонностью к росту зерна и минимальным сопротивлением деформированию, называют температурным интервалом горячей обработки давлением.
|
|
Оптимальный режим нагрева металла характеризуется быстрым равномерным его прогревом до температуры, обеспечивающей высокую пластичность металла, с наименьшими затратами энергия и потерями на окалину. При неправильно назначенном режиме нагрева (по температуре, времени выдержки, скорости нагрева) имеют место большие потери металла на окалину (до 4...5 %), обезуглероживание поверхностных слоев, перегрев, ведущий к образованию крупнозернистой структуры, а также неисправимый брак — пережог и горячие трещины в заготовках. При пережоге происходит окисление металла на границах зерен, металл становится хрупким и при ударе разрушается. Горячие трещины образуются, когда скорость нагрева слишком велика и создается большой перепад температур поверхности и сердцевины заготовки.
|
|
При недостаточном нагреве повышается сопротивление металла деформации, ухудшается его обрабатываемость давлением, а иногда этот процесс становится невозможным вследствие повышения хрупкости металла. Для стали наиболее опасным с точки зрения повышения хрупкости (синеломкости) является интервал температур 300...500 °С. Правильный выбор температуры начала и конца горячей обработки давлением имеет исключительно важное технико-экономическое значение.
Нагрев заготовок перед обработкой давлением может осуществляться в различных печах и нагревательных устройствах. Нагревательные печи делятся на пламенные, в которых теплота образуется при сжигании топлива (твердого, жидкого или газообразного), и электрические. Выбор способа нагрева заготовок определяется технико-экономическими соображениями.
Нагрев крупных заготовок чаще всего осуществляется в пламенных печах. Средние и мелкие заготовки можно нагревать как в пламенных, так и в электрических печах и устройствах.
К основным способам обработки металлов давлением относятся процессы прокатки (рисунок 7.4, а), волочения (рисунок 7.4, б), прессования (рисунок 7.4, в), свободной ковки (рисунок 7.4, г), горячей и холодной объемной штамповки (рисунок 7.4, д), а также листовой или холодной штамповки (рисунок 7.4, е).
Рис. 7.4. Схемы обработки металлов давлением:
а – прокатка, б – волочение, в - прессование, г - свободная ковка, д - горячая и холодная объемная штамповка, е - листовая или холодная штамповка
Большинство процессов обработки давлением отличаются высокой производительностью при небольших отходах металлов, сопутствующих улучшению механических свойств.
Высокая производительность процессов обработки металлов давлением обеспечивается за счет одновременного или последовательного деформирования всего или значительной части объема обрабатываемого металла при высоких скоростях машин-орудий и простоте рабочих и вспомогательных движений.
Сущность процесса прокатки,(рисунок 7.4, а) заключается в деформировании (обжатии) металла между вращающимися валками, зазор между которыми меньше толщины обжимаемой заготовки. В результате обжатия толщина заготовки уменьшается, а длина и ширина увеличиваются (см. рисунок. 7.4, а). Обычно относительное обжатие заготовки за один проход не превышает даже для горячего металла 70...80 %, поэтому окончательный профиль продукта получается многократным повторением процесса обработки заготовки при постепенном уменьшении зазора между валками. При каждом пропуске заготовки площадь ее поперечного сечения уменьшается, а форма и размеры постепенно приближаются к требуемым.
Современный прокатный стан, (см. рисунок 7.5) - сложное оборудование, оснащенное всевозможными механизмами и приборами, которые позволяют полностью механизировать, а в ряде случаев и автоматизировать.
Рис. 7.5. Схема устройства прокатного стана:
1 – электродвигатель, 2 - редуктор, 3 - шестеренная клеть, 4 – передаточные механизмы, 5 – рабочие валки
Рабочая машина состоит из одной или нескольких рабочих клетей, в которых расположены прокатные валки 5. Валки бывают гладкие для прокатки листов и лент и сортовые для прокатки различных профилей (круглых, квадратных, угловых, рельсов и т.п.).
Для передачи движения от электродвигателя 1 к рабочим валкам 5 стана служит шестеренная клеть 3. Между шестеренной клетью и электродвигателем помещается обычно редуктор 2, служащий для изменения частоты вращения рабочих валков. К прокатному стану относятся также вспомогательные машины, выполняющие подсобные операции по резке, правке, отделке и транспортировке готовой продукции. Прокатные станы классифицируются по трем основным признакам: назначению (характеру выпускаемой продукции), числу и расположению рабочих валков и направлению их движения, числу и расположению рабочих клетей.
Технологический процесс современного прокатного производствa, независимо от вида получаемой продукции, состоит из нескольких этапов: заготовки исходного материала, нагрева его (в случае горячей прокатки), прокатки и отделки. Кроме того, на всех стадиях прокатки осуществляется контроль за ходом процесса и состоянием оборудования.
Первичными заготовками в прокатном производстве являются слитки различного сечения и массы. Перед прокаткой слитки проверяют для обнаружения трещин, шлаковых включений, которые удаляют зачисткой, заваркой. Затем слитки нагревают до температуры прокатки в нагревательных колодцах. Из слитков на обжимных станах получают полуфабрикат: блюмы, слябы и заготовки круглого сечения диаметром до 200мм, которые после раскатки на требуемый размер разрезаются на заготовки определенной длины и подаются на заготовочный стан для дальнейшей обработки. Обычно обжимные и заготовочные станы располагаются близко друг к другу, что дает возможность вести прокатку с однократным нагревом металла. На заготовочных станах продукция первичной прокатки подвергается обжатию для получения заготовки меньшего сечений и большей длину, служащей полуфабрикатом для станов окончательной прокатки (листовых, сортопрокатных и т.п.).
Перед окончательной прокаткой заготовку разрезают на мерные части, устраняют поверхностные дефекты (закаты, трещины) и вновь нагревают в методических или индукционных печах.
На станах окончательной прокатки получают либо законченные изделия (рельсы), либо изделия и материалы, нуждающиеся в последующей обработке (балки, трубы, периодический прокат, листовой и прутковый материал). Вся продукция прокатного производства подвергается отделочным операциям (разрезанию, правке), удаляются поверхностные дефекты. Затем производится контроль качества и маркировка продукции. Иногда при ее окончательной отделке ведут термическую обработку (отжиг или нормализацию) и травление для обеспечения заданных механических свойств материала и качества поверхности.
7.6.2. Основные виды проката
Продукция прокатного производства называется прокатом. Он различается по размерам и форме сечения - профилю.
Из слитков массой до 25 т на обжимных прокатных станах получают заготовки квадратного профиля - блюмы, используемые для изготовления сортового проката, и слябы - заготовки прямоугольного профиля, из которых получают лист и полосы.
Совокупность профилей с различными формой и размерами сечений называется сортаментом проката: сортовой прокат, листовой прокат, трубы, периодический прокат и специальный прокат (в том числе гнутые профили).
Сортовой прокат разделяется на простой и фасонный (сложного профиля). К простому прокату относят профили с простой геометрической формой сечения - круг, квадрат, шестигранник, овал и т. д. (рисунок 7.6, а).
К сортовому прокату фасонного профиля относится угловая сталь, швеллер, двутавр, тавр, рельс, зетовая, колонная и ромбовидная сталь (рисунок 7.6, б).
К специальным видам проката относят продукцию законченной формы, изготовленную по заказам отдельных министерств (рисунок 7.6 в). Такой продукцией могут быть накладки (24) и подкладки (25) для рельсов, обод автомобильного колеса (29), бортовое кольцо (34), башмак гусеницы трактора (31) и т.д.
Рис. 7.6. Сортамент проката:
а – простой сортовой прокат, б - фасонный сортовой прокат, в - специальные виды проката, г – прокат периодического профиля
Прокат периодического профиля (рис. 7.6, г) представляет собой полосу или пруток, поперечное сечение которых изменяется по длине проката, воспроизводя форму будущей детали. Этот вид проката может с успехом применяться в качестве фасонных заготовок в кузнечном производстве и заготовок под окончательную механическую обработку. При этом значительно снижается объем работ и отходы металла в стружку.
Листовой прокат разделяют на толстолистовой, тонколистовой и фольгу. К толстолистовому прокату относится броневая, котельная, резервуарная сталь; к тонколистовому - кровельная, трансформаторная, электротехническая сталь, жесть и др.
В последнее время большое развитие получило производство гнутых профилей из холодно- и горячекатаных полос и лент. Гнутые профили сложной конфигурации применяются в автотракторной, авиационной промышленности и в строительстве. Они изготовляются на специальных ролико-гибочных машинах и поставляются в виде отдельных заготовок или бухт ленты определенного профиля. Сортамент гнутых профилей превышает 400 разновидностей.
7.6.3. Особенности производства листового и трубного проката
Листовой прокат по способу производства делят на горяче- и холоднокатаный. Горячекатаную толстолистовую сталь получают из слябов, прокатанных в многоклетеных листопрокатных станах. Готовый прокат проходит правку, обрезку на заданные размеры, очистку и термообработку. Горячекатаный тонкий лист (толщиной менее 4 мм) получают из сутунки—заготовки прямоугольного сечения толщиной 6...12 мм, из слябов на станах полунепрерывной и непрерывной прокатки. Тонкая лента на выходе из последней клети стана непрерывной прокатки скатывается в рулоны. Рулонный метод прокатки обеспечивает повышение выхода годной продукции, производительности процесса и механических свойств металла. Лист в рулонах либо поступает на дальнейшую обработку в цех холодной прокатки, либо подвергается отделочным операциям.
Холодной прокаткой получают только тонкую листовую сталь и стальную ленту с высокими качеством поверхности и точностью по толщине. Прокатку ведут листовым или рулонным способом на четырехвалковых многоклетевых станах. Применение смазки валков способствует их охлаждению и получению высококачественной поверхности изделий.
Сварные трубы изготовляют из плоской заготовки - ленты (рисунок 7.7, а), получаемой из штрипсов - листов, ширина которых соответствует длине окружности трубы. Нагретый до высокой температуры (1300... 1350 °С) штрипс протягивают через воронку, в которой он сворачивается в трубу 3 и одновременно под давлением сваривается встык. После этого сварная труба поступает на стан горячей калибровки для доведения до точного диаметра. Из штрипсов изготовляют сравнительно короткие трубы диаметром до 400 мм. Трубы большого диаметра до 1500 мм с толщиной стенки до 12 мм получают из свернутой по сдирали полосы с последующей дуговой сваркой спирального шва под слоем флюса.
Бесшовные трубы изготовляют из сплошной заготовки. Технологический процесс производства бесшовных труб делится на два основных этапа: получение пустотелой гильзы из слитка или круглого проката (рисунок 7.7, б) и готовой трубы из гильзы (рис. 7.7, в).
Заготовку 1 (см. рисунок 7.7, б) перемещают между валками 2 и 4, оси которых пересекаются в пространстве. Навстречу заготовке движется оправка 5, прошивающая гильзу 3. Благодаря расположению валков под углом по отношению к заготовке она одновременно совершает вращательное и поступательное движения. Конусные валки при вращении заготовки разрыхляют ее сердцевину, а оправка образует полость, расширяет и выглаживает ее. Необходимый внутренний диаметр трубы обеспечивается оправкой, а наружный ее диаметр - соответствующей настройкой валков 2 переменного сечения (рисунок 7.7, в).
Рис. 7.7. Изготовление труб:
а – изготовление сварных труб, б – изготовление пустотелой гильзы при получении бесшовных труб, в – изготовление трубы из гильзы
Использование полых трубных заготовок, полученных методом непрерывного литья, позволяет устранить наиболее трудоемкую операцию - прошивку заготовки и обеспечивает экономию до 50 кг металла на 1 т труб.
После раскатки трубы обрабатываются на специальной машине для устранения овальности и разностенности и затем калибруются на окончательный размер. Отделочные операции при производстве труб могут включать отжиг для получения заданной структуры металла, правку, отрезание концов трубы, зачистку заусенцев, смазку и др.
Значительная экономия металла достигается за счет обработки проката (в частности, труб), называемой в черной металлургии четвертым переделом (термическое и термомеханическое упрочнение, дополнительное холодное деформирование, в том числе гнутие из полосы профилей, нанесение антикоррозионных и других покрытий).
7.6.4. Волочение и прессование
Волочение (см. рисунок 7.4. б), - процесс обжатия металла при протаскивании заготовки через волоку - инструмент с отверстием, сечение которого меньше исходного сечения заготовки. В результате волочения поперечное сечение заготовки уменьшается, а длина увеличивается.
Процесс волочения осуществляется в холодном состоянии и используется для получения тонкой проволоки (от 0,002 мм до 5 мм), калиброванных прутков различного профиля и тонкостенных труб, при этом получают изделия точных размеров, заданной геометрической формы, с чистой и гладкой поверхностью. Заготовками могут служить прокат (катаная проволока, прутки, трубы), а также прессованные профили (прутки, трубы). Окончательные размеры изделий обеспечиваются протягиванием (волочением заготовки) через несколько последовательно расположенных волок (фильер) - представляющих собой кольца, изготовленные из инструментальной стали, металлокерамических сплавов или технического алмаза.
Различают волочильные станы двух основных типов: с прямо-линейным движением протягиваемых изделий и с круговым. К первому типу относятся станы с механическим (цепные и реечные), гидравлическим и пневматическим приводами, для волочения прутков и труб. На станах второго типа (барабанных) осуществляется непрерывное волочение проволоки, которая наматывается на вращающийся барабан или катушку.
Технологический процесс волочения состоит из трех основных стадий: подготовки металла (очистка от окалины, смазывание, заделка концов), волочения по определенному режиму и отделки (удаление дефектов, правка, разрезание на мерные длины, марки-
Прессование (см. рисунок 7.4, в) - процесс выдавливания металла, заключенного в замкнутой полости контейнера, через отверстие матрицы, сечение которого меньше площади сечения контейнера, а форма соответствует форме готового изделия.
Процесс прессования осуществляется при температурах горячей обработки металлов давлением, т.е. при их высокой пластичности. Прессованию подвергают алюминий, медь и сплавы на их основе, цинк, олово, свинец.
Прессованием получают разнообразные профили (рисунок 7.8) из специальных сталей, титановых сплавов и других малопластичных металлов; профили сложной формы, которые не могут быть получены другим способом; обычные профили небольших размеров (например, трубы из цветных металлов).
Исходной заготовкой для прессования служит либо слиток, либо прокат круглого сечения. Прессование производится, на горизонтальных или вертикальных гидравлических прессах
Процесс прессования высокопроизводителен, обеспечивает высокую точность профиля получаемых изделий. Простая замена инструмента - матрицы позволяет легко переходить к изготовлению изделия другого вида.
Особые требования при прессовании предъявляются к инструменту (матрицам, пресс-шайбам, пуансонам), работающему в условиях высоких температур и больших нагрузок. Обычно этот инструмент изготовляют из высоколегированных сталей и сплавов, содержащих вольфрам, ванадий, молибден, хром и другие элементы.
Рис. 7.8. Профили, полученные прессованием
Метод прессования в силу сложности оборудования и высокой стоимости инструмента применяется главным образом в условиях массового производства сложных профилей.
7.6.5. Свободная ковка
Свободная ковка (см. рисунок 7.4, г), - способ горячей обработки металлов давлением, при котором заготовке придается заданная форма при ударах бойка молота или нажатии бойка пресса. Исходными заготовками при свободной ковке могут быть слитки или прокат (круглый, квадратный, прямоугольный), получаемые изделия называются поковками. В большинстве случаев поковка служит заготовкой для дальнейшей механической обработки.
Различают ручную и машинную свободную ковку. Ручная ковка для получения мелких штучных поковок производится на наковальне с помощью кувалды и различного вспомогательного инструмента и применяется при ремонтных работах.
Машинная ковка, осуществляемая на кузнечно-прессовых машинах с помощью бойков, обжимок и других инструментов, позволяет получать поковки массой до 250 т. Основным оборудованием при свободной ковке являются ковочные молоты с массой падающих частей от 0,5 до 16 т и ковочные прессы с усилием 5...150 МН. Мелкие и средние поковки (до 2 т) обычно получают на молотах, а тяжелые на прессах. Поковки, изготовляемые на прессах, отличаются большей точностью размеров и более высокими механическими свойствами. Режимы работы прессов более спокойны, чем молотов: снижается шум, вибрации и т. д. Замена молотов прессами - одно из направлений технического прогресса в кузнечном производстве.
Технологический процесс свободной ковки (см. рисунок 7.9) разрабатывают в следующей последовательности: по чертежу детали составляют чертеж поковки, выбирают последовательность и режимы кузнечных операции и нагревов заготовки, необходимое оборудование и оснастку, определяют состав бригады рабочих и норм их выработки.
Размеры поковки должны быть больше размеров получаемой из нее детали, что предусматривают в чертеже поковки путем назначения припусков и допусков ее размеров.
Рис. 7.9. Основные формообразующие операции свободной копки
а – осадка, б – высадка, в – вытяжка, г, д – раскатка, е - гибка, ж – кручение, з – рубка, и, к – прошивка
Свободная ковка включает ряд операций по предварительной обработке заготовки, формообразованию и окончательной отделке изделия
К предварительным операциям относится разрезание проката или слитков на заготовки соответственно массе и объему будущей поковки с учетом потерь металла на угар, обсечку и т. п., а также нагрев заготовок по установленному режиму.
К основным формообразующим операциям относятся: осадка (рисунок 7.9, а), высадка (рисунок 7.9, б), вытяжка (рисунок 7.9, в), раскатка (рисунок 7.9, г, д), гибка (рисунок 7.9, е), кручение (рисунок 7.9, ж), рубка (рисунок 7.9, з). прошивка (рисунок 7.9, и, к). Выбор кузнечных формообразующих операций и их последовательность производится в зависимости от необходимой формы поковки.
Окончательными операциями являются охлаждение поковок, очистка их от окалины, термическая обработка (если необходимо).
Свободной ковкой изготовляют поковки разнообразной формы и размеров. Но точность размеров и чистота поверхности поковок невысока, что усложняет и удорожает последующую механическую обработку. Кроме того, сам процесс свободной ковки трудоемок и малопроизводителен. Несмотря на недостатки, он является пока единственным способом изготовления крупногабаритных поковок для ответственных деталей гидрогенераторов, турбин, шагающих экскаваторов, прокатного оборудования и других изделий тяжелого машиностроения, к которым предъявляются требования повышенной прочности. Основными путями повышения производительности труда при свободной ковке является механизация трудоемких работ - использование кантователей, манипуляторов и других специальных машин, многобойковых прессов с инструментом, движущимся во взаимно перпендикулярных направлениях, совершенствование методов нагрева заготовок.
7.6.6. Горячая объемная штамповка
Горячая объемная штамповка (см. рисунок 7.4, д), - способ обработки металлов давлением, при котором изделию (поковке) придается необходимая форма при помощи специального инструмента - штампа. При объемной штамповке металл деформируется одновременно по всему объему, а течение его происходит в полости штампа, очертания и размеры которой соответствуют будущей детали Этот способ получения поковок отличается от свободной ковки более высокой производительностью, обеспечивает повышение механических свойств поковок, значительно меньший расход металла и широко применяется в крупносерийном и массовом производстве. Штамповкой можно изготовлять поковки массой от нескольких граммов до 200...350 кг, в отдельных случаях до 2 т. Наиболее экономически целесообразна штамповка поковок до 20 кг, так как при большей их массе резко возрастают расходы на изготовление и эксплуатацию штампов.
Штампы - массивные стальные формы, состоящие из двух частей, в которых имеются полости (ручьи), Верхняя часть штампа закрепляется на подвижной части кузнечной машины, нижняя на неподвижной. При смыкании обеих частей штампа образуется ручей, формы и размеры которого соответствуют изготовляемому изделию. В зависимости от степени сложности изделия используют штампы одноручьевые или многоручьевые. Штамповка поковок сложной конфигурации производится в многоручьевых штампах, ручьи которого подразделяются на заготовительные и штамповочные (черные и чистовые). В заготовительных ручьях происходит предварительное, а в штамповочных окончательное формоизменение заготовки. Различают штамповку в открытых и закрытых штампах.
С целью снижения отходов металла применяется безоблойная штамповка в закрытых штампах. Ее внедрение стало возможным благодаря разработке методов получения заготовок точных массы и объема и их безокислительному нагреву. Применение проката периодического профиля в качестве заготовок для штамповки также способствует экономии металла, при этом сокращается технологический процесс штамповки и упрощается конструкция штампов, так как отпадает необходимость в заготовительных операциях. Особенно эффективно применение указанного проката при изготовлении таких типовых деталей, как шатуны двигателей внутреннего сгорания, всевозможные автомобильные тяги, рычаги, шарики и ролики подшипников и т. о.
Штампы изготовляют из высококачественных сталей, что сопряжено со значительными затратами как на материалы, так и на их механическую обработку, поэтому штамповка рентабельна только в условиях массового и крупносерийного производства.
Разработка технологического процесса штамповки включает конструирование штампов, а в остальном производится в такой же последовательности, как и для свободной ковки.
Горячую штамповку производят на паровоздушных фрикционных молотах, кривошипных, фрикционных и гидравлических прессах, горизонтально-ковочных машинах, ковочных вальцах и других машинах.
Штамповочное оборудование отличается от ковочного большими точностью координации движения соударяющихся частей, скоростями их рабочих движений и меньшей мощностью. Основными характеристиками молотов являются: масса падающих частей (общая масса штока, бабы и штампа), число ударов в минуту и коэффициент полезного действия (КПД). Штамповочные прессы характеризуют по развиваемому усилию, числу ходов ползуна в минуту и КПД.
Выбор оборудования определяется конкретными условиями производства: характером исходной заготовки, габаритами и степенью сложности поковки, требуемой точностью изделия, производительностью и т. п. В общем случае штамповка на прессах имеет ряд преимуществ перед штамповкой на молотах.
Прессовые поковки отличаются более высокой точностью формы и размеров, так как на прессах обеспечивается точное совмещение верхней и нижней частей штампа, а наличие выталкивателей позволяет уменьшить штамповочные уклоны. При этом нормы расхода металла снижаются на 10…20% по деталям типа тел вращения и на 2...20 % по деталям сложной конфигурации.
Прессовая штамповка легко поддается механизации и автоматизации, и оборудование для нее может быть встроено в комплексную автоматическую линию. В настоящее время применяется поточный метод штамповки на специализированных агрегатных линиях.
После штамповки изделий производят ряд завершающих операций: обрезку облоя, прошивку отверстий, правку, термическую обработку (отжиг или нормализацию), очистку от окалины и контроль качества поковок.
7.6.7. Листовая штамповка
Листовaя штамповка (см. рисунок 7.4, е), - процесс получения изделий или заготовок из листового материала путем деформирования его на прессах с помощью штампов. Листовой штамповкой можно получать изделия не только из металла, но и из кожи, картона, пластмасс. Ниже будет рассмотрена только листовая штамповка из металлов.
В зависимости от толщины обрабатываемого листового металла листовую штамповку делят на толстолистовую (толщина листа более 10 мм) и тонколистовую (холодную). Толстолистовую штамповку обычно осуществляют в горячем состоянии. Тонкостенные изделия разнообразной формы получают из листа, ленты или полосы в холодном состоянии.
Холодная листовая штамповка является одним из наиболее прогрессивных и экономичных методов изготовления деталей. Объем металла, перерабатываемого этим способом, больше, чем холодной объемной штамповкой. Детали, полученные листовой штамповкой, отличаются точностью размеров, взаимозаменяемостью и в большинстве случаев не требуют дальнейшей механической обработки.
Высокая производительность процесса обеспечивается за счет большой скорости рабочего хода штамповочных прессов и применения штампов, позволяющих совмещать несколько операций таким образом, что в большинстве случаев готовая деталь получается за один ход пресса. Экономичность листовой штамповки обусловлена как высокой ее производительностью, так и высоким коэффициентом использования металла, достигающим 85,..90 %. Чем выше удельная доля листа в сортаменте проката, перерабатываемого в машиностроении, тем выше общий коэффициент использования металла.
Листовой холодной штамповкой изготовляют детали обшивки вагонов и самолетов, кузова автомобилей и кабины тракторов. Особенно широко применяется листовая штамповка в электротехнической, приборостроительной промышленности, производстве бытовой техники и др.
Различают два вида операций технологического процесса листовой штамповки: разделительные и формообразующие. К разделительным операциям относятся отрезание, вырубка, пробивка, обрезка, надрезка кромки; к формообразующим - вытяжка, формовка, отбортовка, закатка и гибка.
Штампы для листовой штамповки могут быть простыми, предназначенными для выполнения одной операции (гибочные, вырубные, вытяжные), и сложными последовательного и совмещенного действия, в которых последовательно или одновременно выполняется несколько операций.
Для листовой штамповки применяются гидравлические и механические прессы (кривошипные, эксцентриковые, фрикционные). Работа на холодноштамповочных прессах предполагает повторяющиеся однообразные движения рабочего, что приводит к быстрому его утомлению. Механизация и автоматизация штамповочных работ позволяет повысить производительность труда и обеспечить его безопасность.
7.6.8. Прогрессивные способы штамповки
Высокоэкономичным и эффективным способом получения деталей из низкопластичных и труднодеформируемых металлов и сплавов является штамповка взрывом с применением тротила, аммонала и других взрывчатых веществ. При взрыве развиваются кратковременные высокие давления, под действием которых заготовка принимает форму штампа. Штамповкой взрывом получают обычно крупногабаритные детали из толстолистовых заготовок, но из-за повышенной опасности она имеет ограниченное применение.
Более широкое распространение получила относительно безопасная электрогидравлическая штамповка. В жидкой среде создается за счёт кратковременного электрического разряда мощная ударная волна, давление которой на штамп достигает нескольких сот мегапаскалей. Изделия, получаемые в условиях всестороннего давления, отличаются высокой точностью размеров и не требуют дополнительной обработки. Установки электрогидравлической штамповки малогабаритны, легко перемещаются. Рассматриваемым методом производят легкие объемные детали для самолетов, автомобилей, тракторов, детали из листового малопластичного материала.
Для обработки сталей и сплавов с узким температурным интервалом обработки используют изотермическую штамповку. При такой обработке штамп, изготовленный из жаропрочного сплава, устанавливают в индукционный нагреватель. Штамповку производят при одинаковой и постоянной температуре заготовок и штамповых вставок. Полученные поковки обладают улучшенными структурой и свойствами. Повышение пластичности металла и снижение усилий деформирования может быть достигнуто также при вибрационных способах горячей объемной и холодной листовой штамповки.
7.6.9. Технико-экономические показатели процессов обработки металлов давлением
Оценка технико-экономической эффективности процессов обработки металлов давлением производится по следующим основным показателям: объему выпускаемой продукции (в тоннах, по номенклатуре и в стоимостных показателях) за определенный календарный период (месяц, год), съему продукции с 1 м2 производственной площади, выходу годного, расходу энергии и себестоимости.
Технико-экономические показатели технологического процесса зависят от правильности его построения и степени механизации и автоматизации, соблюдения технологической дисциплины, организации производства.
Объем выпускаемой продукции можно увеличить за счет уменьшения простоя оборудования, связанного с его ремонтом, сменой рабочего инструмента (прокатных валков, штампов), за счет механизации трудоемких работ, сокращения продолжительности нагрева заготовок, организации непрерывных процессов обработки.
Своевременный ремонт оборудования, применение высокопрочных износостойких материалов для изготовления валков прокатных станов и штампов, применение смазочно-охлаждающих средств и безокислительных методов нагрева позволяют повысить объем выпуска изделий.
Выход годного характеризует использование металла в процессе производства и исчисляется как отношение расчетной массы готовой продукции (поковки, проката) к массе исходной заготовки. Так как в себестоимости получения проката, поковок, штамповок основную долю составляют затраты на материалы, главной задачей является уменьшение отходов металла и приближение заготовок по форме, размерам и качеству поверхности к готовым изделиям.
В прокатном производстве повышение выхода годного достигается за счет рационального раскроя слитков, использования слитков непрерывной разливки, получения прокатных профилей с минусовыми допусками.
В кузнечно-прессовом производстве увеличение выхода годного может быть достигнуто применением электронагрева, заготовок рациональной формы (проката периодического профиля), безоблойной штамповки, сочетанием ковки и штамповки со сваркой (при изготовлении крупных и сложных по форме поковок), оптимизацией раскроя листового материала с помощью математических методов и т. д.
7.7. Основы технологии обработки материалов резанием
7.7.1. Назначение и сущность технологического процесса обработки материалов резанием
Резание металлов - обработка их снятием стружки для получения изделий заданных формы, размеров и обеспечения определенного технологией качества поверхности.
На большинстве машиностроительных предприятий резание, является преобладающим способом обработки металлов: до 40...60 % деталей машин получают в результате обработки заготовок на металлорежущих станках. Совершенствование технологии резания, модернизация металлорежущего оборудования, разработка и внедрение новых методов резания металлов являются поэтому актуальными проблемами.
Истории возникновения металлообработки в России мало исследована, однако известно, что уже в X в. русские мастера пользовались достаточно сложными приспособлениями при изготовлении оружия, предметов домашнего обихода и т. п.
Относительно быстрое и последовательное развитие металлообработка в России получила в XVII—XVIII вв. в результате значительного развития производительных сил - объединения мелких производств, превращения их в ремесленные мастерские и далее в фабрики, оборудованные машинами.
Совершенствование конструкций станков и инструментов создало предпосылки для разработки теории резания металлов.
Основоположником отечественных исследований в области процессов резания металлов является И. А. Тиме, впервые сформулировавший в 1867—1880 гг. основные законы резания, сделавший важные выводы о причинах вибрации при резании и т. д.
Работы И. А. Тиме были продолжены и дополнены П. А. Афанасьевым, исследовавшим процесс стружкообразования с учетом сил трения между резцом и деталью, К. А. Зворыкиным и А. Н. Челюсткиным, которые в результате экспериментальных и теоретических изысканий получили основные расчетные зависимости, выявившие их влияние на стойкость инструмента, и др.
Теоретические разработки И. А. Тиме и его последователей получили дальнейшее развитие в трудах советских ученых: А. П. Соколовского, предложившего идею типизации технологических процессов и исследовавшего вопросы точности механической обработки, В, М. Кована по теории расчета припусков на обработку, Г. А. Шаумяна по определению характеристик и режимов резания при обработке на автоматах и автоматических линиях и др. Были созданы предпосылки для развития учения о резании металлов и превращения его в науку, для установления основных закономерностей эффективных и экономичных процессов изготовления деталей машин.
Технологический процесс механической обработки резанием - это часть производственного процесса, связанная с последовательным изменением размеров и формы заготовки до превращения ее в готовую деталь. Этот процесс состоит из ряда операций, которые могут выполняться при одной или нескольких установках детали.
Часть технологического процесса по обработке одной или нескольких деталей, выполняемого на одном рабочем месте непрерывно до перехода к обработке следующей детали, называется операцией, а часть операции, выполняемой при одном закреплении ной детали относительно станка и режущего инструмента называется позицией. Технологическая операции механической обработки выполняется за один или несколько переходов, под которыми понимают часть операции, выполняемой на одной обрабатываемой поверхности одним и тем же режущим инструментом при данном режиме резания (например, обточка цилиндра - один переход, подрезка торца - другой и т. д.).
Различают последовательное и параллельное выполнение переходов и операций технологического процесса.
Организация работы по последовательной схеме присуща серийному производству. Параллельная схема технологического процесса обеспечивает более высокую производительность, так как обработка деталей осуществляется с одновременным выполнением ряда переходов в одной операции на многорезцовых и многошпиндельных станках, применение которых целесообразно при значительных программах выпуска изделий.
Технологический процесс механической обработки зависит от ряда факторов: формы и размеров детали, требуемой точности обработки; вида заготовок и способа их получения, программы выпуска деталей, наличного парка оборудования и др. Во всех случаях следует стремиться к нахождению оптимального варианта технологического процесса, обеспечивающего наибольшую производительность при наименьшей себестоимости обработки.
При механической обработке резанием вначале проводят черновую или обдирочную обработку, затем чистовую и в заключение - отделочную обработку, обеспечивающую нужную точность и степень шероховатости поверхности детали.
Повышение производительности при механической обработке резанием может быть достигнуто совершенствованием конструкции типовых металлорежущих станков, режущего инструмента и приспособлений, а также технологического процесса обработки на типовых металлорежущих станках.
При совмещении операций (черновой и чистовой обработки одной поверхности) или видов обработки резанием (сверления и зенкерован ия с развертыванием, резьбонарезанием, фрезерованием и др.), выполняемых комбинированным инструментом па одной рабочей позиции станка, производительность процесса значительно выше, чем при последовательной обработке несколькими типовыми инструментами.
Совершенствование технологического процесса механической обработки на типовых металлорежущих станках может быть достигнуто за счет правильного выбора станка, режущего, мерительного инструмента и приспособлений; применения интенсивных режимов резания; улучшения конструкции режущего инструмента; модернизации станков и усовершенствования приспособлений; одновременной обработки несколькими инструментами; увеличения числа одновременно обрабатываемых деталей и др.
7.7.2. Качество и точность обработки резанием в машиностроении
Механизмы современных мощных и быстроходных машин работают в сложных условиях при значительных нагрузках. Это требует улучшения комплекса качественных показателей выпускаемых изделий и прежде всего технологического процесса их производства, обеспечивающего решающее условие качества - обработку деталей машин. Улучшение качества обработанных поверхностей и точности обработки создает реальные предпосылки для повышения эксплуатационных свойств машин, увеличения скоростей и удельных нагрузок. Известно, что окончательная обработка деталей машин достигается в большинстве случаев обработкой при помощи резания, поэтому влияние инструмента и режима резания является решающим при формировании качества обработанной поверхности.
Пути достижения требуемой точности должны решаться комплексно с учетом всех стадий технологического процесса.
Во всех случаях при решении вопросов точности в машиностроении следует учитывать сроки службы машины, затраты на ее изготовление и эксплуатацию.
В современном машиностроении для обеспечения высокого качества продукции используется взаимозаменяемость.
Взаимозаменяемость - свойство одних и тех же деталей, сборочных единиц или агрегатов машин, механизмов и других конструкций, позволяющее устанавливать или заменять их без дополнительной подгонки при сохранении всех требований, предъявляемых к работе сборочной единицы, агрегата и конструкции в целом. Взаимозаменяемость может быть обеспечена только при соответствующей точности геометрических параметров деталей.
Функциональная взаимозаменяемость предполагает, что основные эксплуатационные показатели деталей и сборочных единиц согласуются с назначением и условиями работу машин, в которые они входят.
Взаимозаменяемость может быть полной или неполной (частичной).
Полная взаимозаменяемость распространяется на все изделия, входящие в состав машины. Тот или иной уровень взаимозаменяемости определяется эксплуатационными требованиями и условиями рационального производства.
Взаимозаменяемость деталей и сборочных единиц в машиностроении имеет большое народнохозяйственное значение, что объясняется соответствием ее принципов современным условиям производства. За счет нее упрощается и ускоряется сборка изделий, облегчается автоматизация технологических процессов, внедрение в производство высокоэффективных станков и приспособлений, обеспечивается значительное снижение себестоимости и повышение качества продукции- основное и необходимое условие современного массового и серийного производства.
Даже современными, достаточно совершенными методами изготовления деталей обеспечить абсолютно точные их размеры нельзя. Основными причинами погрешностей деталей являются: неточность изготовления станков и оснастки, деформации деталей в процессе резания, неоднородность свойств обрабатываемых заготовок и колебания припусков на их размеры, неточность измерений и др. С учетом этого в существующей практике машиностроения взаимозаменяемость однотипных деталей достигается установлением допустимых отклонений (допусков) размеров деталей от номинальных. Номинальный размер служит началом отсчета отклонений и относительно него определяются предельные размеры детали.
Предельные размеры детали - это два предельных значения размера, между которыми должен находиться действительный размер годной детали. Различают наибольший и наименьший предельные размеры детали (соответственно для отверстия и вала). Разность между наибольшим и наименьшим предельными размерами называется допуском размера.
Следовательно, допуск размера определяет степень точности, с которой должна быть обработана деталь. Сравнение действительного размера с предельным дает возможность судить о годности детали.
Отклонением размера называется алгебраическая разность между размером (действительным, предельным и т. д.) и соответствующим номинальным размером. Отклонение может быть положительным (со знаком плюс), если действительный размер больше номинального, и отрицательным, если он меньше номинального. Если размер равен номинальному, его отклонение равно нулю.
Предельным отклонением называется алгебраическая разность между предельными и номинальными размерами. Различают верхнее и нижнее предельные отклонения. Верхнее предельное отклонение — алгебраическая разность между наибольшим предельным и номинальным размерами. Нижнее предельное отклонение - алгебраическая разность между наименьшим предельным и номинальным размерами. Допуск размера также может быть определен через предельные отклонения как алгебраическая разность между верхним и нижним отклонениями.
В Республике Беларусь используется общепринятая единая система допусков и посадок (ЕСДП).
Классы (степень) точности в ЕСДП названы квалитетами. Всего предусмотрело 17 квалитетов, обозначаемых порядковым номером, возрастающим с увеличением допуска: 01; 0; 1; 2; 3-..17 (номера 01 и 0 соответствуют двум наиболее точным квалитетам). Допуск выражается определенным, постоянным для данного квалитета числом единиц допуска.
Следует отметить особенности допусков по ЕСДП. При данном квалитете и интервале номинальных размеров значение допуска постоянно для размеров любых элементов (валов, отверстий, уступов и др.) и в любых полях допусков. Начиная с 5-го квалитета, допуски при переходе к следующему, более грубому квалитету увеличиваются на 60 %. Через каждые пять квалитетов допуски увеличиваются в 10 раз.
Поле допуска образуется сочетанием основного отклонения (характеристика расположения) и квалитета (характеристика допуска). Соответственно условное обозначение поля допуска состоит из буквы основного отклонения и числа - номера квалитета
Машины и механизмы состоят из деталей, которые в процессе работы совершают относительные движения или находятся в относительном покое. Две детали, элементы которых входят друг в друга, образуют соединение. Такие детали называются сопрягаемыми, а поверхности соединяемых элементов сопрягаемыми поверхностями. Поверхности тех элементов деталей, которые не входят в соединение с другими деталями, называются несопрягаемыми. Соединения подразделяются в зависимости от геометрической формы сопрягаемых поверхностей. Соединение деталей, имеющих сопрягаемые цилиндрические поверхности с круглым поперечным сечением, называются гладкими цилиндрическими. Если сопрягаемыми поверхностями каждого элемента соединения являются две параллельные плоскости, соединение называется плоским.
В соединении элементов двух деталей один из них является внутренним (охватывающим), другой — наружным (охватываемым). В системе допусков и посадок гладких соединений любой наружный элемент условно называется валом, любой внутренний — отверстием.
Разность размеров отверстия и вала до сборки определяет характер соединения деталей, или посадку. Разность размеров отверстия и вала, если размер отверстия больше размера вала, называется зазором. Он характеризует большую или меньшую свободу относительного перемещения деталей. Разность размеров вала и отверстия до сборки, если размер вала больше размера отверстия, называется натягом. Натяг характеризует степень сопротивления относительному смещению деталей в соединении.
В зависимости от относительного расположения полей допусков отверстия и вала различают посадки трех типов: с зазором, натягом и переходные.
Различные посадки могут быть осуществлены в системе отверстия или в системе вала. Система отверстия применяется чаще по технологическим и другим причинам. Основной из них является уменьшение потребностей производства в размерном (нерегулируемом) режущем инструменте для обработки отверстий (зенкерах, развертках, протяжках и др.) и другой аналогичной технологической оснастке.
Система вала применяется в конструкциях машин и механизмов, детали которых могут быть изготовлены из пруткового калиброванного материала без обработки резанием сопрягаемых поверхностей; при наличии длинных валов, когда на отдельных участках вала одного номинального размера необходимо поместить несколько деталей с различными посадками, и в некоторых других случаях.
Качествообработанных поверхностей в значительной степени определяет качество деталей машин и механизмов и в первую очередь долговечность, стойкость к коррозии, сопротивление усталости и другие их эксплуатационные свойства. От качества обработки поверхностей зависит также износостойкость деталей, их триботехнические характеристики. Необходимо отметить, что иногда неправильно отождествляются два понятия: качество и шероховатость поверхности.
Качество поверхности детали определяется совокупностью всех служебных ее свойств, определяемой твердостью, шероховатостью, микроструктурой и другими физико-механическими свойствами поверхностного слоя металла.
Шероховатость поверхности определяется совокупностью неровностей с относительно малыми шагами, образующих рельеф поверхности на базовой длине исследуемого участка профиля (рисунок 7.10).
Рис. 7.10. Параметра шероховатости поверхности детали
Оценка шероховатости поверхности производится по двум основным параметрам: среднему арифметическому отклонению профиля Ra и по высоте неровностей профиля по десяти точкам Rz.
Параметр Rmax — наибольшая высота профиля - расстояние между линией выступов профиля и линией впадин профиля в пределах базовой длины; S - среднее значение шага местных выступов профиля, a Sm - среднее значение шага неровностей профиля в пределах базовой длины. Шаговые параметры характеризуют относительное расположение неровностей - вершин выступов профиля и точек пересечения профиля со средней линией Т. Их значения указываются на чертежах деталей.
Базой для отсчета отклонений профиля является средняя линия профиля, имеющая форму номинального профиля и проведенная так, что в пределах базовой длины среднее квадратическое отклонение измеренного профили до этой линии минимально.
Нормирование параметров шероховатости должно производиться с учетом назначения и эксплуатационных свойств поверхности. Основным во всех случаях является нормирование высотных параметров. Предпочтительно, в том числе и для самых грубых поверхностей, нормировать параметр Ra, поскольку он определяется по всем точкам (или достаточно большому числу точек) профиля. Параметром Ra нормируется шероховатость образцов сравнения.
Шероховатость поверхности оценивается с помощью специальных приборов - профилометров. В производственных условиях обычно применяются стандартные наборы образцов сравнения с различной шероховатостью поверхности.
Разные виды механической обработки - точение, сверление, развертывание и другие обеспечивают различную шероховатость поверхности.
Шероховатость поверхностей обозначают на чертеже изделия соответствующим знаком с указанием ее параметров, вида обработки поверхности, базовой длины и условного обозначения направления неровностей.
7.7.3. Способы обработки металлов резанием и элементы режима резания
B процессе обработки исходная заготовка и режущий инструмент получают рабочее движение от механизмов металлорежущих станков и перемещаются относительно друг друга. Для осуществления обработки резанием необходимо сочетание двух видов движения: главного движения резания и движения подачи.
Главное движение резания - прямолинейное поступательное происходящее с наибольшей скоростью V в процессе резания.
Движение подачи - прямолинейное поступательное или вращательное движение режущего инструмента или заготовки, скорость Vs которого меньше скорости главного движения резания, предназначенное для того, чтобы распространить отделение слоя материала на всю обработанную поверхность. В зависимости от направления движения подачи различают продольное, поперечное и другие движения подачи.
Наиболее распространенными способами обработки металлов резанием являются точение, сверление, фрезерование, строгание, шлифование (на рисунке 7.11 стрелками указаны направления главного движения резания и движения подачи).
Рис. 7.11. Способы обработки металлов резанием:
а – точение, б –сверление, в – фрезерование, г – строгание, д – шлифование.
При точении (рисунок 7.11, а) заготовке сообщается главное движение резания, а инструменту - движение подачи; при сверлении (рисунок 7.11, б) оба движения, как правило, сообщаются сверлу; при фрезеровании (рисунок 7.11, в) главное движение резания осуществляет фреза, а движение подачи - заготовка; при строгании на поперечно-строгальных станках (рисунок 7.11, г) главное движение резания совершает резец, движение подачи - заготовка, а на продольно-строгальных станках наоборот; при шлифовании (рисунок 7.11, д) главное движение резания осуществляет шлифовальный круг. Продольная подача при плоском шлифовании сообщается обычно заготовке, а поперечная - заготовке или шлифовальному кругу.
В общем случае процесс резания характеризуется элементами режима резания, скоростями главного движения резания и движения подачи; подачей; толщиной, шириной, а также площадью срезаемого слоя; машинным и штучным временем (см. рисунок 7.12).
Рис. 7.12. Элементы режима резания
Скорость главного движения резания - скорость рассматриваемой точки режущей кромки или заготовки в главном движении резания:
V = πDn*60/1000 (7.1)
где V — скорость главного движения резания, м/мин; D - диаметр поверхности обрабатываемой заготовки, мм; n - частота вращения заготовки, об/мин.
Скорость движения подачи - скорость рассматриваемой точки режущей кромки в движении подачи.
Подача S - отношение расстояния, пройденного рассматриваемой точкой режущей кромки или заготовки вдоль траектории этой точки в движении подачи, к соответствующему числу циклов или определенных долей цикла другого движении во время резании или к числу определенных долей цикла этого другого движения.
Под циклом движения понимают полный оборот, ход или двойной ход режущего инструмента или заготовки. Долей цикла является часть оборота, соответствующая угловому шагу зубьев режущего инструмента. Под ходом понимают движение в одну сторону при возвратно-поступательном движении. Различают подачу на оборот Sn, на зуб Sz, на ход Sx, на двойной ход Sдв.х.
Подача Sn - поступательное перемещение режущей кромки резца за один оборот заготовки.
Толщина срезаемого слоя а - длина нормали к поверхности резания, проведенной через рассматриваемую точку режущей кромки, ограниченная сечением срезаемого слоя. Ширина срезаемого слоя b —длина стороны сечения срезаемого слоя, образованной поверхностью резания. Площадь среза - это площадь сечения срезаемого слоя f=ab. Время, затрачиваемое непосредственно на процесс отделения стружки, называют основным технологическим временем. По основному технологическому времени рассчитываются нормы выработки на данном виде оборудования.
7.7.4. Характеристика используемого режущего инструмента и оборудования
Обработку металлов резанием производят на металлорежущих станках при помощи режущего инструмента, который подразделяется на две группы: однолезвийный (например, резцы) и многолезвийный с двумя и более режущими кромками (сверла, зенкеры, развертки и др.).
Инструменты, изготовленные из абразивных материалов (например, шлифовальные круги), обеспечивают высокую точность обработки и относятся к многолезвийным, т.е. имеющим множество острых режущих кромок.
Производительность режущего инструмента в основном зависит от материала, из которого он изготовлен, способности продолжительное время сохранять режущие свойства. Следовательно, инструментальные материалы должны иметь такие свойства, как красностойкость, теплопроводность, износостойкость, высокое сопротивление изгибу и удару, а также твердость. Для изготовления резцов и других режущих инструментов применяются углеродистые инструментальные стали, легированные инструментальные стали, быстрорежущие стали, металлокерамические твердые сплавы, а также естественные и синтетические алмазы, кубический нитрид бора, эльбор и др. Последние характеризуются высоким модулем упругости, теплопроводностью (в 2,5...9 раз большей, чем твердые сплавы). Инструменты из них имеют наилучшую износостойкость. Известен случай, когда алмазный резец до полного использования затачивался 105 раз, прослужив в общей сложности 16 лет.
Область применения алмазного инструмента весьма обширна: шлифование, заточка и доводка твердосплавных режущих инструентов и штампов; правка шлифовальных кругов алмазно-металлическими карандашами и алмазов в оправке; разрезание высокопрочных материалов алмазными дисками и пилами и др.
Толщина срезаемого слоя и качество обработанной поверхности при использовании абразивного инструмента зависят, в частности, от зернистости материала инструмента, т. е. степени измельчения его зерен, а также физико-механических свойств, как самих зерен, так и цементирующей их связки,
В СНГ абразивные инструменты изготовляют с электрокорундовыми зернами, с белым электрокорундом, с карбидом кремния, а также с синтетическими алмазными зернами (СА) и кубическим нитридом бора (КНБ).
В качестве цементирующих веществ при изготовлении абразивных инструментов применяются неорганическая {керамическая, силикатная, магнезиальная), органическая (бакелитовая, глифталевая, вулканитовая) и различные металлические связки. Алмазный абразивный круг - это металлический (часто алюминиевый) или пластмассовый корпус с нанесенным алмазным слоем толщиной 1.5...3 мм с металлической или бакелитовой связкой и содержанием алмазных зерен обычно 50% (реже 25 и 100%). Основные характеристики абразивного инструмента указываются в марке на его поверхности. Например, ЧАЗ Э9А40СМ2К6 ПП300х20х127 35 м/с означает: ЧАЗ - завод-изготовитель; Э9А - эльбор повышенного качества, используемый в качестве абразива; 40 - номер зернистости; СМ2 - твердость инструмента; К6 - содержание эльбора 60%. Дальше обозначены форма круга (ПП - плоский прямого профиля); размеры круга в миллиметрах (наружный диаметр, толщина, диаметр посадочного отверстия) и допустимая скорость вращения.
Надежность режущего инструмента определяется его стойкостью, т. е. способностью сохранять режущую кромку достаточно острой в течение определенного времени работы. Затупление резца происходит в результате молекулярно-термических процессов и механического изнашивания его граней и режущей кромки. Скорость изнашивания режущего клина (лезвия) в значительной степени зависит от количества теплоты, выделяющейся при резании за счет работы, затрачиваемой на деформацию срезаемого слоя, трение стружки о переднюю поверхность резца и трение задней главной его поверхности о поверхность резания. В результате в резец отводится 10...40% общего количества теплоты, выделяющейся в процессе резания, и температура лезвия может достигать 800...100 °С. Это обусловливает ускорение изнашивания режущего инструмента - истирания и удаления микрочастиц с его поверхности и образования микросколов (выкрашивания) режущей кромки. Сопротивление изнашиванию - важнейшая характеристика инструмента.
Дата добавления: 2016-01-04; просмотров: 12; Мы поможем в написании вашей работы! |
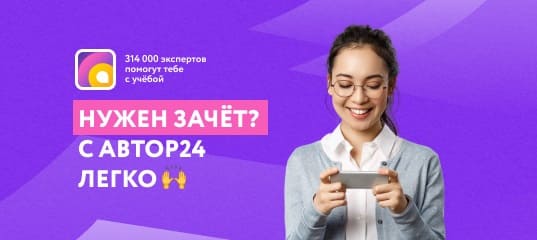
Мы поможем в написании ваших работ!