ОЦЕНКА ПРОЧНОСТИ ДОРОЖНОЙ ОДЕЖДЫ И СОСТОЯНИЯ ДОРОЖНОГО ПОКРЫТИТЯ.
Важной характеристикой транспортного состояния автомобильной дороги является прочность дорожной одежды. В зависимости от прочности одежды решается вопрос организации грузовых перевозок. Внимательное изучение прочности дорожной одежды является основой разработки мероприятий по поддержанию высокой несущей способности дорожной одежды.
Работы по обследованию состояния дорожных одежд состоят из трех этапов: подготовительного, полевого и камерального.
Во время подготовительного периода собирают данные, характеризующие земляное полотно, интенсивность и состав движения во взаимной увязке с конструктивными особенностями дорожной одежды для всего маршрута. При этом используют: проектные материалы по обследуемой дороге; данные о грунтах земляного полотна, конструкции дорожной одежды; принятые при расчете дорожной одежды модули упругости грунтов земляного полотна и отдельных конструктивных слоев дорожной одежды, а также эквивалентные проектные модули упругости всей дорожной одежды разрезы дорожной одежды; материалы, освещающие историю, время постройки дороги и времяпроведения ремонтных работ; данные об участках подверженных пучинам, результаты обследования земляного полотна.
На основе материалов, полученных в подготовительный период, организуют рекогносцировочный проезд вдоль дороги, намечают места бурения и испытания прочности одежды, частоту проведения измерений и выбор методов оценки прочности.
|
|
Наиболее трудоемкий этап - полевой период, когда выполняют работы по бурению и измерению прочности дорожной одежды.
Основой для выбора места бурения служат дефектные ведомости, составленные при детальном обследовании состояния дорожного покрытия. При этом важнейшими критериями являются: виды дефектов покрытия и степень его разрушенности; условия работы дорожной одежды (толщина, тип основания, тип местности по характеру увлажнения, грунты земляного полотна, расположение в плане4 и профиле). Бурение осуществляют на глубину м.о 1,0 м с целью установления фактической толщины каждого слоя дорожной одежды. Образцы материалов отдельных слоев дорожной одежды направляют в лабораторию для детального анализа.
По результатам бурения в зависимости от гранулометрического состава, качества и состояния материала в отдельных слоях дорожной одежды оценивают модуль упругости. Полученные в процессепромера скважин толщины конструктивных слоеви вычисленные модули упругости каждого слоя позволяют определить по формулам теории прочности нежестких дорожных одежд фактический эквивалентный модуль деформации всей дорожнойодежды на рассматриваемом поперечнике. Полученный расчетом модуль упругости может бытьпринят ориентировочно за показатель фактической прочности дорожной одежды.
|
|
Более точное значение прочности дорожной одежды получают путем непосредственных измерений на дороге в полевых условиях разными методами (см. п. 2.3).
Определенный по данным измерения модуль упругости записывают в линейный график дорожной одежды. Затем вычисляют коэффициент запаса прочности дорожной одежды
kз = Еф / Етр , (7.6)
где Еф- фактический эквивалентный модуль упругости, показывающий фактическую прочность дорожной одежды;
Етр - требуемый эквивалентный модуль упругости, характеризующий требуемую по фактическому составу и интенсивности движении прочность дорожной одежды.
По значению kзрассчитывают необходимое усиление дорожной одежды. При этом анализируют изменение коэффициента k3по длине дороги, выделяя участки с k3>l; k3=l и k3<l. Для каждого участка проверяют уменьшение коэффициента запаса прочности дорожной одежды, определяя изменение грузонапряженности дороги по сравнению с предусмотренной по проекту.
Наряду с прочностью дорожной одежды большое влияние на транспортные качества дороги оказывает состояние дорожного покрытия. При обследованиях дорог состояние дорожного покрытия оценивают по его ровности, сцепным качествам и шероховатости.
|
|
Ровность дорожного покрытияизмеряют толчкомером, прибором типа ПКРС, рейками различных типов, акселераторами или акселерографами (см. п. 3.2). Наиболее широкое применение для оценки ровности находит толчкомер.
Перед выездом на дорогу подбирают необходимую документацию, проверяют исправность толчкомера, предварительно тарируют толчкомер на специальном тарировочном участке с заранее известной ровностью, проверяют правильность работы спидометра. Вес автомобиля должен сохраняться постоянным в продолжении всех измерений. Необходимо внимательно проверить состояние шин и давление в них, которое должно быть 0,2 МПа.
Полевые измерения выполняют во время проезда автомобиля с установленным на нем толчкомером при определенной и равномерной скорости движения по обследуемому участку дороги. По каждой полосе движения делают не менее двух проездов, а при наличии расхождения в полученных данных и третий проезд - выборочно по участкам, для которых показания толчкомера после двух проездов имеют расхождение :более 10%.
|
|
В состав бригады по измерению ровности входят водители автомобиля и два оператора. Один оператор наблюдает за счетчиком спидометра, своевременно берет отсчет при проезде створа километрового столба и сообщает второму оператору цифры отпечатанного на ленте отсчета. В обязанность второго оператора входит контроль скорости движения по секундомеру, вычисление разности последовательных отсчетов с занесением ее в ведомость и регистрация в ведомости случаев отступления от равномерного движения с постоянной скоростью (обгон, торможение, вынужденная остановка и т. п.), а также запись на основании визуальной оценки состояния покрытия. В связи с трудностью ведения записи в движущемся с большой скоростью автомобиле рекомендуется использование портативного магнитофона или диктофона, на который продиктовывают всю необходимую информацию.
Ровность измеряют в период наименьшей интенсивности движения на дороге при скорости 60 км/ч. По результатам измерений строят линейный график показателя ровности покрытия (рис. 7.3). Этот график является основой для выбора мероприятий по улучшению ровности. На графике дается качественная оценка ровности дорожного покрытия в соответствии с рекомендациями (табл. 7.1), составленными для скорости 60 км/ч.
Таблица 7.1
Покрытие | Показания толчкомера, см/км, соответствующие оценке рованости | ||
отлично | хорошо | удовлетв. | |
Цементобетьонные, асфальтобе- тонные, щебеночные, обработан- ные органическими вяжущими…. Щебеночные и грвийные ……….. Булыжная мостовая ……………... | ![]() ![]() ![]() | ![]() ![]() ![]() | ![]() ![]() ![]() |
Примечание: В числителе – значения для случаев измерений с бескамерными шинами; в знаменателе – с камерными шинами. |
Металлические или деревянные рейки целесообразно применять только при оценке ровности участков дорог незначительного протяжения (участки с выбоинами, пучинами, просадками над водопропускными сооружениями, колейностью и т. п.). При использовании реек ровность покрытия оценивают по зазору между нижней кромкой рейки и поверхностью покрытия. Допускаемые отклонения по ровности покрытия при измерениях трехметровыми рейками должны соответствовать требованиям табл. 7.2.
Таблица 7.2
Оценка ровности | Количество просветов не более 3 мм, % | Допустимое количество просветов свыше 5 мм,% | Максимальный допустимый просвет, мм |
Отлично Хорошо Удовлетворительно | 95 90 80 | 1 2 5 | 7 8 10 |
Основной характеристикой степени скользкости дорожных покрытий является коэффициент сцепления. Косвенной оценкой скользкости служит шероховатость поверхности покрытия.
Коэффициент сцепления определяют с помощью динамометрических тележек или портативных приборов (см. п. 3.3), а также по длине тормозного пути. Наиболее точные значения получают при использовании динамометрических прицепов. Измерения динамометрическими прицепами выполняют, как правило, на участках дорог большого протяжения при скорости 60 км/ч.
При отсутствии динамометрических прицепов степень скользкости дорожных покрытий оценивают методом торможения автомобиля (обычно ГАЗ-24 «Волга») на мокрых покрытиях. В этом случае коэффициент сцепления вычисляют подлине тормозного пути
, (7.7)
где V - начальная скорость торможения, км/ч;
Sт -длина тормозного пути, м.
Для ускорения определения коэффициента сцепления пользуются также данными, приведенными в табл. 7.3.
Таблица 7.3
Суммарная длина тормоз- ного пути,м | ![]() | Суммарная длина тормоз- ного пути,м | ![]() | Суммарная длина тормоз- ного пути,м | ![]() | ||
5,8 6,1 6,9 7,9 | 0,76 0,72 0,64 0,64 | 8,5 9,2 10,0 11,0 | 0,52 0,48 0,44 0,40 | 12,2 13,0 14,7 16,9 20,0 | 0,36 0,34 0,30 0,26 0,20 |
Измерения тормозного пути выполняют на прямых горизонтальных участках дороги при отсутствии сильного ветра и закрытии движения на участке измерений. Автомобиль должен иметь шины с поизношенным рисунком протектора и отрегулированную тормозную систему, обеспечивающую одновременное и полное затормаживание всех колес.
Спидометр должен быть оттарирован и обеспечивать определение скорости движения с точностью до ±5,0 км/ч. Автомобиль на участке торможения разгоняют до скорости 40 км/ч и резко тормозят.
Длину тормозного пути измеряют рулеткой по следу на поверхности покрытия. Большую точность измерений обеспечивает автомобиль, оборудованный пистолетом - ракетницей, который заряжается краской или порошком (сухой краской). Пистолет-ракетница связан с педалью тормоза, нажатие на педаль вызывает выстрел и отметку на проезжей
части, положение которой фиксирует начало тормозного пути.
При использовании децелерометра коэффициент сцепления вычисляют по замеренному отрицательному ускорению а(замедлению) автомобиля при резком торможении в течение 1 с:
, (7.8)
где g - ускорение свободного падения, м/с2.
Измерения проводят на мокром покрытии. Значение замедления принимают средним из 4 - 5 торможений.
Итоговым документом оценки скользкости дорожного покрытия является линейный график коэффициентов сцепления.
Шероховатость поверхности дорожных покрытийизмеряют методом песчаного пятна или портативными микропрофилографами. В первом случае отпадает необходимость в применении какого-либо специального оборудования.
Метод «песчаного пятна» заключается в распределении на поверхности покрытия определенного объема песка (обычно 10 - 30 см3) с размером частиц 0,15 - 0,30 мм. Песок распределяют вровень с поверхностью отдельных выступов покрытия, придавая песчаному пятну форму правильного круга. По измеренному диаметру пятна Dи объему песка Vвычисляют среднюю глубину шероховатости:
(7.9)
Если вычисленная средняя глубина шероховатости на участках дорог с продольными уклонами до 30% о на покрытиях с применением органических вяжущих материалов составляет менее 0,7 мм, а на цементобетонных покрытиях менее 0,5 мм, то шероховатость считается неудовлетворительной, при средней глубине шероховатости соответственно от 0,7 до 1,5 и от 0,5 до 0,6 мм - удовлетворительной, от 1,5 до 2,0 и от 0,6 до 0,8 мм - хорошей и при средней глубине более 2,0 и 0,8 мм - очень хорошей.
Для безопасного движения на участках дорог с большими уклонами средняя глубина шероховатости должна быть не менее следующих значений:
Уклон, %...................... ………………… 40 50 60 70 80
Средняя глубина шероховатости, мм. 3,5 4 4,5 5 5
Более полная характеристика шероховатости покрытия может быть получена с помощью микропрофилографов. Кроме средней глубины, по записанному профилю можно определить среднее расстояние между выступами и углы при вершине выступов.
Измерения шероховатости на одном и том же месте выполняют не менее 3 раз и в случае расхождений не более 10% вычисляют среднее арифметическое. Места измерений выбирают в пределах полос наката и лишь для сопоставления на середине проезжей части и на участках между полосами наката.
Целесообразно все линейные графики, характеризующие состояние дорожного покрытия, располагать один под другим. В этом случае облегчаются анализ состояния покрытия и планирование необходимых мероприятий.
Как правило, мероприятия по улучшению ровности покрытия одновременно повышают коэффициент сцепления и степень шероховатости поверхности покрытия.
Для дорог высших категорий может создаваться банк данных состояния дорожного покрытия с применением ЭВМ. В этом случае на магнитную ленту или диски ЭВМ фиксируют значения измеренных коэффициентов сцепления и показателей ровности. Покрытие наиболее важных маршрутов фотографируют сверху на пленку, просматривая которую, принимают решение о проведении необходимых мероприятий по его улучшению. Такой метод накопления информации используется в СНГ и во Франции.
Для комплексной оценки состояния дорожного покрытияв ряде стран используют специальный прицепной прибор (рис. 7.4). Характерной особенностью конструкции прибора является наличие большого количества измерительных колес. Такой прибор позволяет одновременно оценивать поперечный уклон проезжей части, наличие выбоин, глубину колей и т. п.
Комплексная оценка состояния дорожного покрытия в ряде стран осуществляется с помощью показателя службы.
В Японии используют следующую формулу для расчета показателя службы (РSI):
РSI = 4,53 - 0,518 а - 0,37
- 0,174 D2,
где а - среднее квадратическое отклонение неровностей поверхности дорожного покрытия;
С - показатель трещиноватости;
D - средняя глубина колеи, см.
При РSI = 2,1 – 3 рекомендуется поверхностная обработка, при
РSI = 1,1 - 2 - укладка нового слоя покрытия, при РSI = 1 - реконструкция участка дороги.
Дата добавления: 2018-02-18; просмотров: 657; Мы поможем в написании вашей работы! |
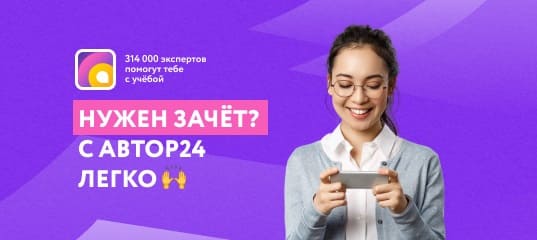
Мы поможем в написании ваших работ!