Підприємства виробів на основі вапна
Використання вапна для одержання міцних і водостійких штучних кам'яних виробів тривалий час не знаходило застосування, тому що в природних умовах вапно твердіє дуже повільно, вироби на його основі мають невелику міцність (1-2 МПа) і легко розмокають при дії води.
Однак у 1880 році було встановлено, що при автоклавному обробленні вапняно-піщаних сумішей при тиску пари 0,8 МПа і температурі вище170°С можуть бути отримані дуже міцні, водостійкі й довговічні вироби. Сьогодні силікатна промисловість - одна з найбільш розвинутих галузей промисловості будівельних матеріалів [65].
Суть перетворення вапняно-піщаної суміші із легкорозмокаючого і неміцного матеріалу в міцний і водостійкий камінь полягає у наступному. У природних умовах пісок у вапняно-піщаних сумішах інертний і не здатний хімічно взаємодіяти з вапном. У результаті цього набуття міцності вапняно-піщаними розчинами в природних умовах досягається головним чином за рахунок твердіння вапна. Однак, у середовищі насиченої пари (100% вологості) при температурі 170°С і вище кремнезем набуває хімічної активності та починає швидко взаємодіяти з вапном за таким рівнянням
Са(ОН)2+SiО2+(n-1)Н2О = СаО-SiО2*nН2О,
утворюючи гідросилікати кальцію - міцну й водостійку речовину [81].
З вапняно-піщаних сумішей виготовляють великорозмірні вироби для збірного будівництва: блоки і панелі для стін та перекриттів, а також штучні вироби - силікатну цеглу і камені для стін.
|
|
Виготовлення силікатних блоків і панелей не відрізняється від виробництва залізобетонних виробів.
Силікатна цегла за своєю формою, розмірами й основним призначенням не відрізняється від глиняної цегли.
Матеріалом для виготовлення силікатної цегли є повітряне вапно і кварцовий пісок. Вапно застосовують у вигляді меленої негашеної, частково загашеної або гашеної гідратної. Вапно має характеризуватися швидким гасінням та не повинно містити більше 5% Мg. Перевитрати сповільнюють швидкість гасіння вапна і навіть викликають появу у виробах тріщин, спучувань та інших дефектів, тому для виробництва автоклавних силікатних виробів вапно не повинно містити перепалу. Кварцовий пісок у виробництві силікатних виробів застосовують немеленим або у вигляді суміші немеленого і тонкомеленого, а також грубомеленого із вмістом кремнезему не менше 70%. Наявність домішок у піску негативно впливає на якість виробів: слюда знижує міцність і її вміст у піску не повинен перевищувати 0,5%; органічні домішки викликають спучування й також знижують міцність; обмежується вміст у піску сернистих домішок до 1% у перерахуванні на SО3. Рівномірно розподілені глинисті домішки допускаються в кількості не більше 10%; при такому вмісті вони навіть трохи підвищують зручновкладуваність суміші. Великі добавки глини в піску не допускаються, оскільки знижують якість виробів.
|
|
Склад вапняно-піщаної суміші для виготовлення силікатної цегли такий: 92-95% чистого кварцового піску, 5-8% повітряного вапна і приблизно 7% води.
Виробництво силікатної цегли відбувається двома способами: барабанним і силосним, які відрізняються приготуванням вапняно-піщаної суміші.
При барабанному способі (рис. 8.1) пісок і тонкомолоте негашене вапно, яке можна одержати подрібнюванням у кульовому млині комового вапна, надходять в окремі бункери над гасильним барабаном.
З бункерів пісок, який дозується за обсягом, а вапно - за масою, періодично завантажуються в гасильний барабан. Останній герметично закривають і протягом 3-5 хв перемішують сухі матеріали. Потім, при подаванні перегрітої пари під тиском 0,15-0,2 МПа відбувається гасіння вапна при барабані, який неперервно обертається. Процес гасіння вапна триває до 40 хв.
При силосному способі попередньо перемішану і зволожену масу направляють для гасіння в силоси. Гасіння в силосах відбувається 7-12 год, тобто в 10-15 разів більше, ніж у барабанах, що є істотним недоліком силосного способу. Добре загашену в барабані чи силосі вапняно-піщану масу подають у лопатеву мішалку або на бігуни для додаткового зволоження і перемішування, й далі - на пресування.
|
|
Пресування цегли здійснюють на механічних пресах під тиском до 15-20 МПа, що забезпечує одержання щільної та міцної цегли. Відформований сирець укладають на вагонетку, яку направляють в автоклав для твердіння.
Рис. 8.1.Технологічна схема виробництва силікатної цегли за барабанним способом:
1 — барабанний грохот для сортування піску; 2 — гасильний барабан; 3 — склад вапна;
4 — дробарка; 5 — млин; 6 — сепаратор; 7 — бункер меленого вапна; 8 — ваговий дозатор;
9 — шнек; 10 — перемішування і подрібнення маси на бігунах;
11 — пресування цегли; 12 - твердіння цегли в автоклаві
Автоклав становить собою сталевий циліндр діаметром 2см і більше, довжиною до 20м, з торців герметично закривається кришками (рис. 8.2) [18].
З підвищенням температури прискорюється реакція між вапном і піском, а при температурі 174°С вона протікає протягом 8-10 годин. Швидке твердіння відбувається не тільки при високій температурі, але й високій вологості, для цього в автоклав напускають пару тиском до 0,8 МПа і цей тиск витримують 6-8 годин. Тиск пари піднімають і знижують протягом 1,5 години. Цикл запарювання продовжується 10-14 годин [27].
|
|
Рис. 8.2. Автоклав:
1 — кронштейн; 2 — візок; 3 - стійка; 4 — манометр; 5 — запобіжний клапан;
6 — металевий циліндр; 7 — штуцер із краном; 8 — кришка; 9 — лебідка;
10 — рейковий місток; 11 — паропровід; 12 — рейки
Під дією високої температури й вологості відбувається хімічна реакція між вапном і кремнеземом піску. Гідросилікати, які утворюються в результаті реакції, зростаються з зернами піску в міцний камінь. Однак твердіння силікатної цегли на цьому не припиняється. Міцність силікатної цегли продовжує підвищуватися після запарювання. Частина вапна, що вступила в хімічну взаємодію з кремнеземом піску, реагує з вуглекислотою повітря, утворюючи міцний вуглекислий кальцій за таким рівнянням
Са (ОН)2 + СО2 = СаСО3 + Н2О.
Силікатну цеглу випускають розміром 250x120x65 мм; марок - М75, 100 і 125, 150 і 200; водопоглиненням - 8-16%; коефіцієнтом теплопровідності - 0,70-0,75Вт/м°С; об'ємною масою - 1800-1900 кг/м3, тобто дещо вище, ніж глиняної цегли; морозостійкістю Мрз 15. Теплоізоляційні якості стін із силікатної цегли і глиняної практично рівні.
Застосовують силікатну цеглу там же, де й звичайну глиняну цеглу, але з деякими обмеженнями. Не можна застосовувати силікатну цеглу для укладання фундаментів і цоколів, тому що вона менш водостійка, ніж глиняна, а також для укладання печей і димарів, оскільки при тривалому впливі високої температури відбувається дегідратація гідросилікату кальцію і гідрату окису кальцію, які зв'язують зерна піску, і цегла руйнується.
За техніко-економічними показниками силікатна цегла перевершує цеглу глиняну. На її виробництво потрібно вдвічі менше палива, утричі менше електроенергії, у 2,5 рази менше трудомісткості виробництва; в остаточному підсумку собівартість силікатної цегли виявляється на 25-35% нижчою за глиняну.
Питання для повторення
1. Технологія отримання виробів на основі вапна.
2. Застосування виробів на основі вапна у будівництві.
3. Назвіть вироби, які найчастіше використовуються у будівництві.
4. Технологія отримання силікатної цегли.
5. Операції технологічного процесу отримання силікатної цегли.
6. Компоненти силікатної маси для отримання цегли.
7. Що таке автоклав?
8. При якій температурі відбувається затвердіння силікатної цегли?
9. Цикл затвердіння силікатної маси при номінальній температурі.
10. За рахунок чого створюється температура в автоклаві?
11. Який створюється тиск в автоклаві при затвердінні силікатної цегли?
12. Цикл підйому і зниження тиску пари в автоклаві.
13. Цикл витримки максимального тиску пари в автоклаві при затвердінні
силікатної цегли.
14. У яких будівельних конструкціях категорично заборонено застосовувати силікатну цеглу?
Підприємства асфальтобетону
Асфальтовим або дьогтьовим бетоном називають штучний матеріал, що утворюється в результаті ущільнення спеціально підібраної суміші, яка складається з щебеню (або гравію), піску, мінерального порошку, бітуму або дьогтю і пеку. Застосовують його, головним чином, у дорожньому будівництві [30].
Асфальтові бетони. Залежно від температури, при якій укладають і ущільнюють суміш у покритті, і в'язкості застосовуваного бітуму розрізняють такі різновиди асфальтових бетонів: гарячі, які готуються на в'язких бітумах при температурі 140-180°С і вкладаються у покриття при температурі не нижче 130°С, формування структури бетону в основному закінчується в період ущільнення; гарячі дьогтьобетони при укладанні повинні мати температуру 80-110°С; теплі - готуються на бітумах зниженої в'язкості при температурі 90-160°С і вкладаються у покриття при температурі 30-100°С, формування структури також в основному закінчується у період ущільнення; холодні, які готуються на рідких бітумах при температурі 80-120°С і вкладаються в покриття після повного їх остигання, формування їх структури продовжується протягом 20-30 діб. До холодних належать також асфальтобетонні суміші на бітумних емульсіях, які вкладаються при нормальній температурі.
За максимальною крупністю зерен мінерального матеріалу асфальтовий бетон поділяють на: крупнозернистий з найбільшим розміром зерен 40 мм, середньозернистий – 25 мм, дрібнозернистий – 15 мм та піщаний – 5 мм.
За структурними ознаками (щільністю) асфальтовий бетон може бути щільний, тобто мати сумарну пористість 3-5% об'єму, і великопористий - з пористістю 5-10% об'єму.
Асфальтобетонну суміш готують за такою технологічною схемою (рис. 9.1): мінеральні матеріали (щебінь і пісок) з відкритих складів і мінеральний порошок із закритого складу подають у дозатори, після чого відважений на один заміс (масою 3-3,5т) матеріал транспортером подають у бункер, звідки при відкритті затвору він самопливом надходить у барабан змішувача, який обертається.
Рис. 9.1. Технологічна схема приготування асфальтобетонної суміші:
1 – дробарка для каменю; 2 - елеватор; 3 - сортування на фракції; 4 – бункери щебеню;
5 - бункер піску; 6 - живильник; 7 - елеватор для холодної суміші; 8 – сушильний барабан;
9- полиця; 10 - подача нафти; 11 - елеватор для гарячої суміші;
12 – бункери гарячої суміші;13 — елеватор для наповнювача; 14 – дозатори;
15 — змішувач; 16 - самоскид;17 - приймач для наповнювача
Останній поділений на два відділення - сушильне для просушування і підігрівання мінеральних матеріалів до 170-190°С та змішувальне - для об'єднання мінеральних матеріалів і розплавленого бітуму, який надходить через дозатор по трубах з бітумоплавильних казанів. На один цикл роботи витрачається 12-15хв. Продуктивність змішувача Д-138 (Г-1) при приготуванні грубозернистої асфальтобетонної суміші складає 90-110т за зміну.
Готову асфальтобетонну суміш транспортують в автосамоскидах і у місцях укладання завантажують в асфальтоукладач, який рівним за товщиною шаром розподіляє її по підготовленій основі. Розподілену по дорожній основі суміш ущільнюють катками масою 5-14т або вібраційними моторними катками масою 0,5-4,5т.
У будівництві найчастіше застосовують асфальтобетон, тому що він довговічніший за дьогтьобетон. Великозернистий асфальтобетон використовують для нижнього шару дорожнього покриття; середньозернистий - для одношарових покриттів і верхнього шару двошарових покриттів; дрібнозернистий, який має досить високу опірність механічним та атмосферним впливам, для покриття з інтенсивним рухом і для верхнього шару двошарових покриттів; піщаний, який має підвищену пластичність - для покриття підлог у цехах промислових будівель, тротуарів і покриттів доріг із легким рухом.
Для покриття на дорогах полегшеного типу використовують дрібнозернисті асфальтобетонні суміші холодного типу. Грубозернисті холодні бетони застосовують для основ і нижнього шару двошарового покриття. Холодні бетони простіші та дешевші при виготовленні й зручніші при укладанні, особливо в сиру і холодну погоду, аніж звичайні асфальтові бетони.
У будівельній практиці поряд із гарячим, теплим і холодним асфальтовими бетонами застосовують також литий асфальтобетон. Ущільнюють його в гарячому стані прасками або легкими (0,5-1,5т) катками. Литий асфальт використовують у несприятливих умовах, де не можна використовувати важкі катки і вібратори, або при малих обсягах робіт (для пристрою покриттів на тротуарах, плоских покрівлях, підлогах у складських і виробничих приміщеннях, а також для гідроізоляції).
Питання для повторення
1. Що собою становить асфальтобетон?
2. Назвіть компоненти, які входять до асфальтобетону.
3. Структурні ознаки асфальтобетону.
4. Технологічний процес виготовлення асфальтобетону.
5. Температура варіння асфальтобетону.
6. Погодні умови, при яких забороняється укладати асфальтобетон у шляхове полотно.
7. Температура асфальту, при якій заборонено укладати бетон у шляхове полотно.
Дата добавления: 2018-02-18; просмотров: 790; Мы поможем в написании вашей работы! |
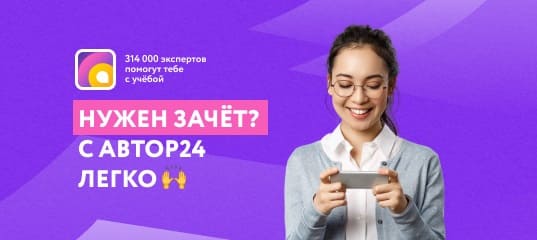
Мы поможем в написании ваших работ!